几种铸造工艺在汽车零件上应用研究
汽车缸体铸造工艺

汽车缸体铸造工艺一、缸体材料车用发动机缸体缸盖的材质主要有灰铸铁,铝合金,蠕墨铸铁等。
传统的发动机无论是缸体还是缸盖都是采用铸铁的,但是铸铁有着许多先天的不足,例如重量大、散热性差、摩擦系数高等等。
所以,许多发动机厂商都在寻找更适合的材料制造发动机的构成部件,比如密度小的铝。
铝的比重轻,单位体积的铝结构强度要小于铸铁,所以铝缸体通常体积反而大些。
但铝容易和燃烧时产生的水发生化学作用,耐腐蚀性不及铸铁缸体,尤其对温度压强都更高的增压引擎更是如此。
铸铁缸体和铝缸体各有其优缺点,所以所以高增压的引擎很多都采用铸铁缸体,小型车的缸体则更多向铝缸体发展。
金属中的元素组成会对金属材料的性能产生较大的影响,就钢铁而言,钢中含碳量增加,屈服点和抗拉强度升高,但塑性和冲击性降低,当碳量0.23%超过时,钢的焊接性能变坏,因此用于焊接的低合金结构钢,含碳量一般不超过0.20%。
碳量高还会降低钢的耐大气腐蚀能力,在露天料场的高碳钢就易锈蚀;此外,碳能增加钢的冷脆性和时效敏感性。
不同的缸体元素配比也是有差别的。
合肥江淮铸造有限责任公司缸体化学成分要求化学成分(%)C Si Mn P S Cr Cu Ti Sn Pb下限 3.25 1.95 0.60 0.00 0.06 0.25 0.30 0.00 0.06 0.00 0上限 3.40 2.10 0.90 0.06 0.10 0.35 0.50 0.03 0.09 0.00 4二、原材料熔炼熔炼设备选用:中频感应保温电炉:生产效率10t/h,外水冷长炉龄大排距冲天炉:生产效率7t/h。
1、原材料原材料一般为回炉料,废钢和生铁。
回炉料是厂家的常备材料,在使用时必须注意其本身的干净程度。
回炉料的加入量必须严格按一定比例,否则会导致铁水的Si、S含量不易控制。
江淮生产的缸体铸件回炉料使用量一般不超过20%。
在江淮的缸体生产中,废钢的使用量超过50%。
这是由于生铁本身含有粗大石墨,而石墨熔点较高,在2000℃以上,在熔炼中不能熔尽,使得结晶过程中石墨变得粗大。
铸造铝合金技术在汽车中的应用
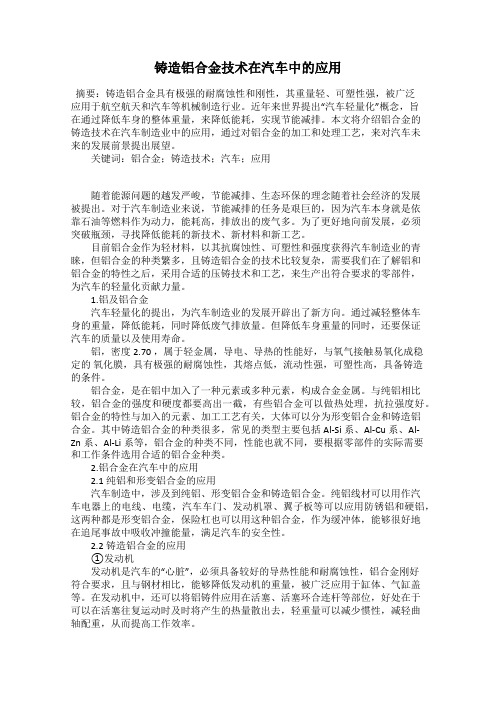
铸造铝合金技术在汽车中的应用摘要:铸造铝合金具有极强的耐腐蚀性和刚性,其重量轻、可塑性强,被广泛应用于航空航天和汽车等机械制造行业。
近年来世界提出“汽车轻量化”概念,旨在通过降低车身的整体重量,来降低能耗,实现节能减排。
本文将介绍铝合金的铸造技术在汽车制造业中的应用,通过对铝合金的加工和处理工艺,来对汽车未来的发展前景提出展望。
关键词:铝合金;铸造技术;汽车;应用随着能源问题的越发严峻,节能减排、生态环保的理念随着社会经济的发展被提出。
对于汽车制造业来说,节能减排的任务是艰巨的,因为汽车本身就是依靠石油等燃料作为动力,能耗高,排放出的废气多。
为了更好地向前发展,必须突破瓶颈,寻找降低能耗的新技术、新材料和新工艺。
目前铝合金作为轻材料,以其抗腐蚀性、可塑性和强度获得汽车制造业的青睐,但铝合金的种类繁多,且铸造铝合金的技术比较复杂,需要我们在了解铝和铝合金的特性之后,采用合适的压铸技术和工艺,来生产出符合要求的零部件,为汽车的轻量化贡献力量。
1.铝及铝合金汽车轻量化的提出,为汽车制造业的发展开辟出了新方向。
通过减轻整体车身的重量,降低能耗,同时降低废气排放量。
但降低车身重量的同时,还要保证汽车的质量以及使用寿命。
铝,密度2.70 ,属于轻金属,导电、导热的性能好,与氧气接触易氧化成稳定的氧化膜,具有极强的耐腐蚀性,其熔点低,流动性强,可塑性高,具备铸造的条件。
铝合金,是在铝中加入了一种元素或多种元素,构成合金金属。
与纯铝相比较,铝合金的强度和硬度都要高出一截,有些铝合金可以做热处理,抗拉强度好。
铝合金的特性与加入的元素、加工工艺有关,大体可以分为形变铝合金和铸造铝合金。
其中铸造铝合金的种类很多,常见的类型主要包括Al-Si系、Al-Cu系、Al-Zn系、Al-Li系等,铝合金的种类不同,性能也就不同,要根据零部件的实际需要和工作条件选用合适的铝合金种类。
2.铝合金在汽车中的应用2.1纯铝和形变铝合金的应用汽车制造中,涉及到纯铝、形变铝合金和铸造铝合金。
探究熔模精密铸造技术在汽车工业的发展及应用

探究熔模精密铸造技术在汽车工业的发展及应用据统计,2014 年,中国汽车年产销已达2400 万辆,已成为世界第一汽车生产大国。
因此,精铸件的市场需求量也在不断快速增长和发展, 这也给国内从事汽车企业熔模精密铸造工艺带来了巨大的发展机遇,竞争优势很明显。
其特点是很高的尺寸精度和表面光洁度,加工余量少,适合复杂的合金铸件,已广泛应用于国内外精铸行业。
1 熔模精密铸造技术在汽车工业的应用1.1 熔模铸造技术特点与工艺流程熔模铸造最早起源于2500 年前的春秋时期,1978 年在湖北随州出土的曾侯乙墓的尊和盘是早期熔模铸造的代表作。
我国精铸行业在20 世纪50年代中期已经建立,逐渐得到推广应用。
现在它在航空、船舶、汽车、仪表、军工等行业得到了广泛的应用,并向日常化、民用化发展。
精铸工艺流程多且较为复杂,影响因素比较多,不易控制。
1.2 国外熔模精密铸造技术在汽车工业的应用现状在20 世纪,国外熔模铸造技术发展很快。
1965年,通用汽车公司的Henzel 和Keverian 等利用有限差分法对发动机缸体铸件进行了凝固模拟, 结果与实验情况吻合。
前苏联高尔基汽车精铸熔模铸造车间从制蜡、制壳、焙烧、浇注完全自动化,由于精铸可以生产少切削或无切削的复杂合金件, 故前苏联把这种工艺作为90 年代的重点发展工艺。
在90 年代,又出现了SUP 法的一种工艺,该工艺是用水溶性尿素树脂代替蜡料作模料, 采用低压注射成型的精铸法,最大优点是成本低,适用于批量生产,产品表面光洁度好、尺寸精度高。
近年来,随着新材料和新技术的不断发现,产生了很多新工艺、新技术、新设备。
目前,在日本、英国、德国等已成功地把精铸工艺采用流水线来生产低成本的汽车零件。
1.3 国内熔模精密铸造技术在汽车工业的应用现状随着我国汽车发动机机盖、支架、齿轮、铰链、摇臂等精铸零件的研制, 我国精铸工业化进程也加速发展。
在20 世纪50 年代,中科院研究所开发了水玻璃制壳工艺,成功用于汽车领域。
铸造工艺技术方法

铸造工艺技术方法铸造工艺技术方法是一门将熔化的金属材料注入模具中并冷却凝固的工艺,被广泛应用于制造各类金属制品的行业。
铸造工艺技术方法的选择和运用对于产品质量和生产效率具有重要的影响。
下面将介绍几种常见的铸造工艺技术方法。
一、砂型铸造工艺技术方法砂型铸造是铸造工艺中最常见的一种方法。
它的工艺流程是:制作砂型,熔化金属,填充砂型,冷却固化,分离模具,修整和后处理。
砂型铸造方法具有成本低、可制造复杂形状、适用于大批量生产等优点,广泛应用于汽车零部件、机械设备等行业。
二、压铸工艺技术方法压铸是一种将熔化的金属通过高压注入模腔中的工艺。
它的工艺流程是:熔化金属,注入模腔,冷却凝固,开模取出。
压铸工艺技术方法适用于制造复杂形状、高精度要求的制品,如电子设备外壳、汽车发动机零部件等。
三、失重铸造工艺技术方法失重铸造是一种利用熔化金属在失重条件下凝固的铸造方法,主要有真空吸铸和气体动力喷射铸造两种方法。
失重铸造工艺技术方法适用于制造高温合金、钛合金等难以进行传统铸造的材料和复杂形状的制品。
四、连续铸造工艺技术方法连续铸造是一种将熔化金属连续注入模具中,通过连续冷却凝固得到长条状的产品的工艺。
它的工艺流程是:熔化金属,连续注入模具,连续冷却凝固,切割产品。
连续铸造方法适用于制造长条状的金属制品,如钢铁、铝合金等材料。
五、低压铸造工艺技术方法低压铸造是一种利用压力将熔化金属从底部注入模腔中的铸造方法。
它的工艺流程是:熔化金属,模具旋转,底部注入,冷却凝固,开模取出。
低压铸造方法适用于制造厚壁、大尺寸的金属制品,如管道、容器等。
六、精密铸造工艺技术方法精密铸造是一种制造高精度、复杂形状的金属制品的铸造方法。
它的工艺流程是:制作精密模具,熔化金属,注入模腔,冷却凝固,开模取出。
精密铸造方法具有高精度、表面质量好的优点,广泛应用于光学、仪器仪表等行业。
综上所述,铸造工艺技术方法在金属制品的生产中起到了至关重要的作用。
不同的产品和材料需要选择合适的铸造工艺技术方法,以提高产品质量和生产效率。
壳型铸造轿车发动机曲轴的研究与应用

间震实 ,每箱5 个壳 型 ,1 件 曲轴 。 0
应 电炉 熔化 铁 水 并浇 注 成 铸 件 的 工 曲轴 轮廓 尺 寸 为4 0 mmX 8 16 发热 保温 冒口的试 验开 发 8 1 2 mm .
艺 方法 ,其主要 工艺流程见 图1 。
X 6 1 0 mm ;上 海 华 普 曲 轴 单 重 为
壳型 曲轴 采用立 浇底 注式 浇注系 进 .从 提 高 曲轴质 量 和 降 低 生产 成 育 剂 含 钡 孕 育 剂 、含 锆 孕 育剂 ,
统 .过 滤 网放 置 及 过 滤 网 的种 类 、
一
直 到 现 在 ,曲轴 都 使 用 发热 块 作
为冒 口补缩辅 助工艺 。
1 浇 口杯 的选择 _ 7
浇 E杯 的作用主要 有三方面 。第 l
一
.
要 有利 于 浇 注 ,在 浇 注 过 程 中
要 有 一定 的容 量 ,不能 使 铁 水 溢 出
图1 壳型铸造 工艺流程
壳 外 第 二 ,曲轴采 用 立 浇 底 注式
工 艺 ,整个 浇 注 系统 为封 闭 式 浇注
2 汽车T艺与材料 AS ̄ 6 I TV d
20年 5 07 第 期
维普资讯
.
生 产 碗 场
抗拉 强度 / ・nn N li- e
发 气量/ g mL・。
<l 5
熔点/ ℃
9 ~10 4 0
造工艺 。
15 曲轴装箱 工艺 .
采 用 壳 型 外 侧 充 填 铁 丸
( ̄ - d 2 4 mm ) ,要 经 过 1 - 0 s 5 3 时
壳型铸造 是采用覆 膜砂制壳 ,两 轮廓 尺 寸 为4 6 mmX 4 4 1 2 mmX 3 10
新型铸造技术的研究及应用

新型铸造技术的研究及应用随着工业化的不断发展,铸造技术作为制造行业的重要基石,在技术的持续改进和创新中也得到了长足的发展。
近年来,新型铸造技术的研究和应用,为铸造行业带来了新的发展机遇。
一、新型铸造技术的研究1.1 数字化铸造技术数字化铸造技术是一种集成了数字化设计、数字化模拟、数控加工等多种先进技术的铸造生产方式。
主要通过对铸造工艺进行数字化仿真,优化铸造参数设置,提高生产效率和产品质量。
其中,CAD/CAM技术和虚拟样机技术是数字化铸造技术的核心。
1.2 新材料铸造技术新材料铸造技术是指应用新材料和新工艺技术进行铸造。
这种技术能够满足特定材料的需求,如高性能合金、超导材料等,同时还可以降低能耗和环境污染。
1.3 先进成形技术先进成形技术是一种通过快速成形技术制造金属原型的铸造技术。
它采用了激光喷粉和激光熔化成形、电子束烧结和光敏树脂快速成型等多种技术手段,可以实现一次成形,并且工艺稳定可靠,能够有效改善金属成形的精度和质量。
二、新型铸造技术的应用2.1 轻量化汽车零部件铸造随着汽车工业和环保意识的不断提高,轻量化汽车零部件的需求也越来越大,而新型铸造技术的应用,则可以有效地解决这一问题。
比如,采用先进的高强度铝材料,或采用热成型、注压成型等先进技术生产部件,可以将汽车的重量减轻15%-20%。
2.2 航空航天领域铸造航空航天领域对铸造技术的要求尤为高。
而数字化铸造技术和新材料铸造技术则可以为航空航天领域带来更高的科技含量。
比如,使用高强度合金材料,采用虚拟样机技术进行设计和仿真,可以有效的提高飞机的安全性和性能。
2.3 家电产品铸造家电产品作为大众化产品,对铸造的要求较高。
而先进成型技术的应用,则可以大幅提高产品的生产效率和质量。
比如,使用激光喷粉和激光熔化成形技术代替传统的生产方式,可以有效地提高家电产品的质量和生产效率。
三、新型铸造技术未来的发展趋势随着科技的不断推进,新型铸造技术也在不断的发展和创新。
镁合金半固态压铸汽车产品实例

镁合金半固态压铸汽车产品实例1.引言1.1 概述镁合金半固态压铸技术是一种新兴的铸造工艺,能够制造出高强度、轻量化的汽车零部件。
随着汽车工业的发展和对轻量化材料需求的增加,镁合金半固态压铸技术得到了广泛关注和应用。
本文将通过介绍镁合金半固态压铸技术的原理和特点,以及汽车产品中的应用实例,来探讨这一技术在汽车制造领域中的潜力和前景。
镁合金半固态压铸技术是将镁合金加热到半固态状态,通过压铸成型得到所需的零部件。
相比传统的压铸工艺,镁合金半固态压铸技术具有以下几个显著的优势。
首先,半固态状态下的镁合金具有较低的黏度和较高的塑性,使得其在压铸过程中更容易充填模腔,提高了产品的成形质量和尺寸精度。
其次,半固态压铸过程中的镁合金具有较低的热应力,可有效降低零部件的变形和缩松现象。
此外,由于镁合金具有良好的可再生性和循环利用性,采用半固态压铸技术制造汽车零部件有助于环境保护和可持续发展。
在汽车产品中,镁合金半固态压铸技术已得到广泛应用。
一方面,由于镁合金具有优异的强度和刚度,采用半固态压铸技术可以制造出更轻量化、更节能的汽车零部件。
例如,采用半固态压铸技术制造的发动机缸体和传动壳体重量可以减轻20以上,同时提高了产品的耐久性和可靠性。
另一方面,由于镁合金具有良好的导热性能,采用半固态压铸技术可以制造出具有良好散热效果的汽车零部件。
例如,采用半固态压铸技术制造的发动机散热器可以有效降低发动机的温度,提升整车的燃油经济性和动力性能。
综上所述,镁合金半固态压铸技术是一种有潜力的汽车零部件制造技术,具有轻量化、节能和环保等优势。
随着该技术的不断发展和完善,相信在未来的汽车制造领域中将得到更广泛的应用。
1.2 文章结构文章结构部分的内容可以描述文章的组织方式和结构设计,以便读者能够更好地理解和阅读文章。
具体内容如下:文章结构:本文主要分为三个部分,分别是引言、正文和结论。
1. 引言部分:引言部分首先对镁合金半固态压铸技术进行概述,介绍其在汽车制造领域中的重要性和应用背景。
铝合金挤压铸造的研究进展及其在汽车轻量化上的应用

铝合金挤压铸造的研究进展及其在汽车轻量化上的应用挤压铸造是一种集铸造、锻造为一体的先进铸造成型技术,与传统的重力铸造相比,液态金属在压力作用下强制进行补缩,从而可获得连续致密组织、晶粒细小、性能优异的精密铸件[1-3]。
由于挤压铸造具有诸多优点,挤压铸造技术已经在航空航天、汽车、机械制造及船舶工业得到了应用。
挤压铸造按照压力传递形式,可分为直接挤压铸造(Direct squeeze casting)和间接挤压铸造(Indirect squeeze casting)两种[2]。
直接挤压铸造是冲头直接作用在液态金属上,无浇注系统,压力直接作用在铸件上使金属液凝固成型,直接挤压铸造适合生产形状简单的挤压铸件。
间接挤压铸造是冲头通过浇道将压力传递给铸件,使金属液在模具型腔内受压力作用凝固成型,这种成型方式可生产壁厚不均、形状复杂的零件,随着装备制造业的不断发展,对零件的质量及力学性能也逐渐地提高,间接挤压铸造作为一种新工艺将得到更广泛的应用。
1 间接挤压铸造的理论研究进展间接挤压铸造理论的研究对于指导生产实践有一定的积极意义,无论是直接挤压铸造还是间接挤压铸造,其核心工艺参数都是压力,都是将压力作用在金属液上而引起的一系列组织性能的变化,所以现在关于挤压铸造的理论研究都是以压力为切入点进行的,然后再进一步探究压力对金属凝固结晶、成分偏析、凝固传热以及相图变化等方面的影响。
1.1 压力对显微组织的影响目前关于挤压铸造压力下晶粒细化的理论主要有两种说法。
Frank等认为[4],液态金属在较高压力作用下,使凝固时的过冷度增加,从而提高形核率,最终使晶粒细化。
Chadwick等认为[5],压力只是使合金凝固时,凝壳与模壁之间的热交换系数增加,使凝壳与模壁之间的有效接触面积增加而导致合金的凝固速度增大,从而细化了晶粒。
图1为ADC12铝合金间接挤压铸造和金属型铸造的显微组织。
由图1可以看出,间接挤压铸造组织更加细小,金属型铸造中存在较多树枝晶。
- 1、下载文档前请自行甄别文档内容的完整性,平台不提供额外的编辑、内容补充、找答案等附加服务。
- 2、"仅部分预览"的文档,不可在线预览部分如存在完整性等问题,可反馈申请退款(可完整预览的文档不适用该条件!)。
- 3、如文档侵犯您的权益,请联系客服反馈,我们会尽快为您处理(人工客服工作时间:9:00-18:30)。
第一章概论1.1课题的来源、背景及意义现代汽车的发展不仅是朝着品种的多样化方向进行,而更是以汽车的性能为重点,结合人们生活发展的需要,做到价廉、质轻、省油、环保。
本课题来源于汽车系电动汽车开发项目,如下图1.1是该次试验所要研究的产品。
图1.1 产品该产品是铝合金铸件。
根据图1.1,可以看出该产品特点是结构紧凑而复杂,并且生产中对该产品的要求是精度高。
经分析研究,结合实际情况,我们可采用消失模铸造、精密复合铸造、石膏型铸造对该产品进行研究和探讨。
但是这三种方法都是建立在消失模的基础上的。
因此,我们需要对消失模技术进行比较系统的认识和了解。
进入八十年代以来,采用干砂消失模铸造法(EPC技术)生产铝合金汽车铸件在欧美得以迅速发展。
干砂消失模铸造是一项完全不同于传统湿砂型铸造的全新技术。
采用该技术代替传统湿砂型进行生产,具有铸件质量高、生产成本低、结构设计自由度大、易于实现自动化生产、应用范围广等许多优点。
该铸造技术可实现铸件的轻量化和精密化,铸件的尺寸精度可达CT6-8级,表面粗糙度Ra6.3-12.5um,与传统砂型铸造相比,可减少加工量10~30%,降低投资成本15~40%,并显著提高生产效率,改善工作环境,实现清洁生产。
该技术是铸造工艺的一个重要发展方向,被誉为二十一世纪的铸造技术[1]。
1.2消失模的国内外现状及其发展1.2.1国外的发展1962年美国人M.C.Flemings开始用干砂和EPS模生产铸件[2]。
80年代初,干砂消失模铸造专利的失效以及试验研究取得的进展,为这一新工艺的工业应用提供了极好的机遇。
福特汽车公司率先在加拿Essex工厂建立了生产100万只铝进气歧管的高度自动化消失模铸造生产线,揭开了这一新技术在先进工业国家飞速发展的序幕。
在不改变原设计及结构的前提下,采用干砂消失模铸造法生产的铝进气管铸件比普通砂型铸造法生产的重量轻20%左右,成本约下降20%,而发动机功率可提高4%左右。
1990年通用汽车公司在Saturn建成占地面积10万m2年产铸件5.5万吨的新铸造厂,全自动的EPC生产线有三条,其中一线生产319A1四缸体,二线生产两种型号的319A1汽缸盖,三线生产珠光体球铁曲轴和两种型号的传动差动壳体。
Fiat和Fata公司在意大利建造了两个车间,用该法专门生产汽车发动机进气管,其中一个车间在生产率为50型/小时的自动线上生产铝进气管,一个铸型可生产四个管件。
英国Perry Bar Mefal公司已将金属型浇注法生产铝合金铸件改为气化模铸造法生产。
目前,该公司向市场提供发动机进气管、水泵和压气机壳体及其它零件。
90年代,德国大众投资2000万美元建造了四缸铝合金缸体生产线。
宝马汽车公司建成了年产20万件的六缸铝合金缸盖生产线。
日本、荷兰等国也在稳步发展EPC技术,使之在铸造生产中发挥其特有的优势。
可见,EPC技术己经在工业发达国家稳定地发展起来,发达国家投入了相当的人力和财力研究和开发干砂消失模铸造技术,并取得了巨大成功。
对于复杂消失模铸件,其公差可达到石膏型铸件的水平。
1.2.2国内的发展90年代以来,我国消失模铸造技术得到了较大发展。
但我国消失模铸造工厂生产铸件的品种基本为铸铁和铸钢件。
目前,我国采用消失模铸造正式大批量生产铸铝件的厂家仅第一汽车厂一家。
第一汽车集团轻型发动机厂从美国VULCAN公司引进了制模成套设备及振动台,与国内其它设备配套组成生产线,用于大批量生产CA488发动机铝合金进气管,已于1993年正式投产。
当前我国EPC技术水平与工业发达国家相比,无论在零件的品种、复杂程度和铸件质量、在机械化、自动化程度、生产效率方面,或者在基础研究方面,都有着较大的差距。
工业发达国家己将先进的气化模铸造工艺应用于铝合金缸体、缸盖、进气歧管、曲轴箱、复合功能部件等。
零件复杂程度高、铸件尺寸精度高、表面粗糙度小。
而我国目前生产的铸件品种还少,复杂程度和质量比国外还差一个档次。
工业发达国家在EPC技术的成套问题上解决得比较好,分工合作,使EPC 技术总体水平迅速提高。
我国EPC技术的成套化工作还比较差,尚停留在单枪匹马、小而全的阶段,新建的一些生产线生产规模及机械化程度比较低,还没有自动化的生产线。
在基础研究方面,工业发达国家对于EPC法的几个关键技术(如气化模材料及制模技术、涂料技术、EPC 法充填特性的研究、干砂紧实特性的研究、工艺设计及废品分析)己经作了比较深入的研究,进行了比较长期的技术积累,为工业应用打下了较好的基础。
譬如气化模材料及制模技术方面,制定了EPS的标准。
研究了气化模的尺寸变化及影响因素,因而能获得比重小、表面光洁、尺寸精确、复杂程度高的气化模。
对于EPC法充填特性的研究,不仅限于多触点法等工程测试方法,而且开始进行计算机数值摸拟,深入掌握特定条件下金属充填的规律,并注意它的实际应用,为解决相关的铸造缺陷提供了依据。
而我国的EPC基础研究还很薄弱,有待加强这方面的研究。
目前,我国对铝合金消失模铸造的某些关键技术尚未掌握,如某厂使用进口EPS原始珠粒,且使用美国Ashland化学公司专用涂料,在实际生产中还是发现当浇注温度较低时铸件成形不良,易产生冷隔和浇不足等铸造缺陷。
当前,针孔严重、气密性差,铸件渗漏率甚至高达30%左右,不得不采用浸渗工艺进行补救,从而增加了工艺的复杂性,提高了生产成本。
另有一个厂花费4000万元巨资从国外引进了成套设备与工艺技术,至今己经五年尚未投入生产。
其中,技术上就是铝铸件气密性的问题未能得到解决,给国家造成了巨大经济损失。
综上所述,我国与发达国家在消失模铸造技术方面存在很大的差距,国外消失模铸造技术对外极为保密,我国尚未完全掌握国外采用干砂消失模铸造生产铝合金铸件的诀窍,以致铸件针孔严重,气密性差。
其技术关键主要体现在涂料研究、铝液高温(760-800o C)处理、铸造工艺的优化设计以及各工艺参数的正确选取。
因此,有必要结合我国的生产实际围绕减少铝铸件的针孔开展干砂消失模铸造铝合金的研究。
1.3 铝合金消失模铸造研究现状1.3.1 充型特性充型特性的研究主要包括铝液流动前沿的流动形态、铝液的流动性、充型速度和影响充型的因素(包括模样材料、涂料、浇注温度、真空度、浇注系统设计等) 三个方面。
许多研究者采用各种方法, 如冷淬法、高速摄影法、电极触点法等对不同形状的铝合金铸件的流动形态进行了观察。
研究结果表明,铝合金消失模铸造的充型与空腔铸造的充型的流动形态有明显的不同。
空腔铸造时,金属液的流动受重力的影响比较大,先从下部充填, 然后逐步向上推进,最后充填部分在顶部。
而消失模铸造时,金属液流动前沿的流动形态总是以内浇道为中心呈放射弧状依次向前推进,逐层对泡沫模样进行置换,最后充填的部位为离内浇道最远处。
负压的引入可能产生附壁效应,即在负压作用下,金属液先沿铸型壁流动。
严重的附壁效应会导致厚壁铸件产生夹杂及气孔缺陷。
S. Shivkumar[3]采用热分析法和高速摄影法研究了铝合金充填条形试样时的流动性,结果表明提高静压头、增加试样尺寸均可提高铝液的流动速度以及流动长度。
文献[4]的研究表明,铝液充型前沿热解产物主要为液态,气态产物较少。
铝液充型速度主要受模样材料的液态热解产物渗出涂层的速度所控制。
施加负压, 提高浇注温度均使流速增加。
研究还表明,铝合金消失模铸造充型速度比空腔铸造慢得多的主要原因是EPS 模样热解消耗大量的铝液热量,使铝液充型前沿温度下降, 同时热解产物在铝液与EPS 模样界面上起阻挡作用。
而有人却指出,浇注铝合金时存在一个临界温度,在临界温度以下时,液态分解产物较多,提高浇注温度有利于充型速度的提高;而在临界温度以上时,浇注温度的提高促使更多的气体产生,会降低充型速度[5]。
S. Sh ivkumar认为浇注系统性质显著影响着金属液的充填形态; 并指出, 水平浇注时充填速度先快后慢, 而垂直浇注则先慢后快再慢。
有的学者认为, 在阶梯式浇注方式中, 若采用实型直浇道, 则金属液从上内浇道开始流入型腔; 而采用空心直浇道,金属液则从下内浇道开始流入型腔。
H. S. Lee[6]的研究结果表明, 采用顶注、侧注、底注方式均可, 但底注充型平稳, 有利于气体排放, 应优先选用。
魏尊杰[7]研究了干砂消失模铸造铝液停止流动机理。
在试验基础上建立了铝合金液停止流动物理模型, 并建立了铝液停止流动的统一判据。
研究表明, 降低聚苯乙烯密度与气化潜热可以减少金属液流端部凝固壳层厚度或固液两相区的宽度, 而降低聚苯乙烯发气性, 提高涂料层透气性或减少涂料层厚度则可以减少金属液前端的气隙压力, 从而降低金属液充型时的流动阻力, 提高金属液的充型能力。
杨军生[4]的研究表明, 当铝液充型前沿达共晶温度时仍有显著的充型能力。
认为: 随着铝液的充型,模样的激冷作用使铝液前沿出现凝固壳层, 铝液不断熔化和冲破此壳层而流动。
当温度降至共晶温度时, 铝液靠其较大的潜热和较低的固相体仍然流动相当长的一段距离, 只有当前沿的固相率增大到临界固相率时, 流动才停止。
1.3.2 模样热分解、传热传质特性模样的热分解方式以及生成的气相、液相和固相产物数量取决于金属液的浇注温度, 浇注速度以及聚苯乙烯材料的物理化学性能。
文献[8]采用DTA , TGA ,LO I 等技术研究了模样加热过程中的热破坏, 并给出了聚苯乙烯破坏的热谱图。
研究表明, 在铝合金液浇注温度范围内(700~800℃) , 模样基本上只分解成蒸汽状的液体馏分和一定量的气体, 燃烧只是有限地进行。
J. Brenner认为聚苯乙烯是以缓慢的裂解方式形成二聚物、三聚物、单体很少。
将一定量金属液滴过模样块, 测得模样分解的液相产物比气相产物多一个数量级。
进一步研究指出, 在660~900℃范围内, 模样发气量基本没有变化, 约为(205±25)cm3/g。
在消失模铸造充型过程中, 金属液与模样、涂料和干砂之间发生传导、对流、辐射等热量传递过程。
S.Shivkum r 借助于计算机采用计算的办法计算了充型过程中铝合金的前沿温度。
有人把模样消失归纳为一个有潜热的相变过程,确定了热解相变过程的数学模型。
上述研究表明铝合金前沿存在较大的温度梯度。
干砂消失模铸造的传质现象是指热解产物的型腔中的行为及通过涂层向干砂传输而排出的过程。
在铝合金干砂消失模铸造中, 模样的热解产物是气液混合物, 且以液态为主。
铝合金干砂消失模铸造时, EPS 热解产物在涂料中的传输是靠液态热解产物的润湿和渗透。
有人实测了干砂中不同区域热解产物的灼烧减量。
文献[4]对液态热解产物通过涂层向干砂中的传输特性进行了研究, 应用LOI法对铸铝件铸型中的EPS 热分解产物残留量进行了分析, 研究表明, 液态热解产物通过润湿和渗透以及铝液的压力作用能迅速进入涂层及相邻干砂中。