电泳漆涂装应用工艺
电泳漆工艺流程

电泳漆工艺流程电泳漆是一种涂装工艺,通过将电泳液中的颜料和树脂粉末以电场作用下沉到工件表面,形成均匀、致密的涂膜,以达到涂装保护和美化的目的。
下面是一个关于电泳漆工艺流程的简要描述。
首先,准备工作。
工件要进行电泳涂装前需要进行一系列的准备工作。
例如,对表面进行除锈、除油等处理,确保表面干净无尘。
其次,准备电泳槽。
电泳槽是用来装电泳液的容器,它分为阳极槽和阴极槽。
阳极槽里装有电泳液,而阴极槽则是放置待涂工件的区域。
槽体需要坚固耐用,以承受电流和电泳工艺的要求。
然后,调制电泳液。
电泳液是整个电泳涂装工艺的核心,它主要由颜料和树脂粉末组成。
调制电泳液需要根据不同工件的要求和涂装效果进行配比。
通常情况下,会进行多次试配,确保电泳液的稳定性和涂层质量。
接着,进行电泳漆。
将经过准备的工件放置在阴极槽中。
工件与电极相连,与阳极槽中的电泳液形成电场。
在电场的作用下,电泳液中的颜料和树脂粉末被吸附到工件表面,形成均匀、致密的涂膜。
此外,进行电泳漆效果检验。
对涂装后的工件进行目测检验和实验室测试。
目测检验可以通过观察涂层的颜色、亮度、平整度等指标来判断涂装效果;实验室测试则需要对涂层进行一系列的物理性能和耐候性能测试,以确保涂膜质量符合要求。
最后,进行涂后处理。
当电泳漆干燥后,需要进行涂后处理。
这包括涂层的固化、烤炉烘烤、表面光洁处理等。
涂后处理的目的是提高涂层的硬度、耐候性和外观效果。
总之,电泳漆是一种先进的涂装工艺,具有涂层均匀、精细、致密、耐候性好等优点。
在实际应用中可以广泛用于汽车、摩托车、家具、电器等领域。
电泳漆工艺流程的每一步都需要进行精确控制,以确保涂装效果和涂层质量达到要求。
电泳漆工艺
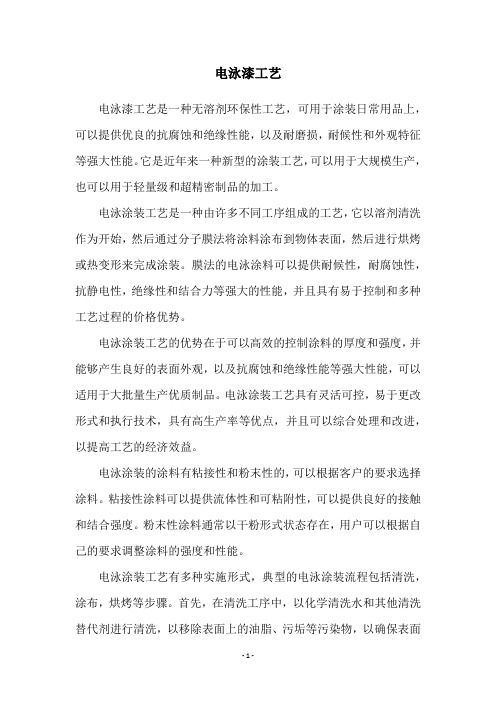
电泳漆工艺电泳漆工艺是一种无溶剂环保性工艺,可用于涂装日常用品上,可以提供优良的抗腐蚀和绝缘性能,以及耐磨损,耐候性和外观特征等强大性能。
它是近年来一种新型的涂装工艺,可以用于大规模生产,也可以用于轻量级和超精密制品的加工。
电泳涂装工艺是一种由许多不同工序组成的工艺,它以溶剂清洗作为开始,然后通过分子膜法将涂料涂布到物体表面,然后进行烘烤或热变形来完成涂装。
膜法的电泳涂料可以提供耐候性,耐腐蚀性,抗静电性,绝缘性和结合力等强大的性能,并且具有易于控制和多种工艺过程的价格优势。
电泳涂装工艺的优势在于可以高效的控制涂料的厚度和强度,并能够产生良好的表面外观,以及抗腐蚀和绝缘性能等强大性能,可以适用于大批量生产优质制品。
电泳涂装工艺具有灵活可控,易于更改形式和执行技术,具有高生产率等优点,并且可以综合处理和改进,以提高工艺的经济效益。
电泳涂装的涂料有粘接性和粉末性的,可以根据客户的要求选择涂料。
粘接性涂料可以提供流体性和可粘附性,可以提供良好的接触和结合强度。
粉末性涂料通常以干粉形式状态存在,用户可以根据自己的要求调整涂料的强度和性能。
电泳涂装工艺有多种实施形式,典型的电泳涂装流程包括清洗,涂布,烘烤等步骤。
首先,在清洗工序中,以化学清洗水和其他清洗替代剂进行清洗,以移除表面上的油脂、污垢等污染物,以确保表面的洁净度和涂料的防腐蚀性能。
接着,在涂布步骤中,利用电泳方法在物体表面形成膜层,然后进入烘烤步骤,以确保涂层完整,表面光滑和强度足够。
电泳涂装工艺是一种技术新兴的,采用节能,环保,涂料用量少等特点,目前被广泛应用于电子产品,汽车,航空航天,医疗器械等各个行业。
这种工艺在生产过程中消耗低,性能稳定,可靠,使产品尺寸精确,外观和抗腐蚀性能更加优秀,具有良好的市场前景。
综上所述,电泳漆工艺是一种可以提供优良的抗腐蚀和绝缘性能,以及耐磨损,耐候性和外观特征等强大性能的环保涂装工艺。
电泳涂装工艺具有高效控制,多种工艺过程优势,以及节能,环保,质量可靠等优势,可以充分满足大规模生产以及轻量级和超精密制品的加工的需求。
汽车电泳涂装工艺要求

汽车电泳涂装工艺要求
汽车电泳漆涂装工艺技术要求
一、涂装工艺概述
电泳漆是一种在金属表面形成原子层的新型涂装工艺,它是一种将电
泳漆浆料和基底金属发生化学反应、原子层和金属基底介面完全结合在一
起的技术,广泛应用于汽车表面装饰和防护上。
电泳漆涂装表面有极高的
抗腐蚀能力和极强的抗冲击性,坚固耐用,具有漆膜光泽美观、透明耐刮、抗氧化、耐腐蚀、发光等性能优势,是目前汽车表面装饰和防护的最佳涂
装工艺。
二、涂装工艺流程
(1)静电喷涂:静电喷涂是将应用电泳漆浆料制成涂料,用喷枪以
恒定的压力和喷嘴的喷口,将涂料通过气流的推动使涂料分层涂在工件表面,用于汽车面部装饰的表面处理方法,它能够有效地控制漆膜厚度和颜色,使它们更加完美和美观。
(2)表面处理:在涂装过程之前,表面工具的表面必须进行清洁和
处理,以便能够增强涂层的附着力,确保最终涂装质量。
表面清洁的处理,包括抛光、铬电镀、清洗、水处理和清洁。
(3)涂装:电泳漆涂装是在清洁处理后用电泳漆浆料制成涂料,用
喷枪以恒定的压力和喷口将涂料均匀喷涂到表面,形成原子层,考虑到涂
料的活性特。
电泳涂装线工艺

电泳涂装线工艺
电泳涂装工艺一般由漆前表面处理、电泳涂装、电泳后清洗、电泳漆膜的烘干等四道主要工艺(或工序)组成。
一般的工艺是:
上挂→除油→水洗→除锈→水洗→表调→磷化→水洗→去离子水洗→电泳→水洗→去离水洗→压缩空气吹气→烘干→下挂
①漆前表面处理工艺:为得优质的、防腐蚀性好的电泳漆涂层,电泳前被涂物必须进行表面处理,首先清洗掉各种污物(如油污、锈、氧化皮、焊渣、金属屑等),随后应进行化学处理(磷化、钝化处理),并应进行充分的水洗,洗掉前处理药品、磷化沉渣等,最后用去离于水洗.所用新鲜的去离子水水质要好,电导不应大于25us/cm.确保被涂物的滴水电导不大于30us/cm。
如果油污不洗净带入电泳槽内.影响电泳质量,易产生缩孔、针孔;锈不除掉,磷化不上,易产生电泳涂膜的异状附着,且在涂膜下继续扩蚀;氧化皮不除掉.不导电,泳涂不上;焊渣、金属屑、前处理药品、磷化沉渣不除净,带入电泳槽,污染槽液影响涂装质量.
②电泳涂装工序:是将被涂物浸入电泳槽中按规定的泳涂条件通电一定时间,使槽液中的成膜物质泳涂至被涂物表面上,随后取出送去冲洗.
③电泳后清洗工艺:为提高电泳涂膜外观质量.防止产生再溶解、二次流痕等漆膜弊病;电泳涂装的被涂物需用超滤液清洗。
最后用离子水清洗
④电泳涂膜的烘干:在规定的烘干温度下保持一定时间达到涂膜完全固化。
电泳涂装工艺特点及与油漆喷涂比较

电泳涂装工艺特点及与油漆喷涂比较电泳又名电着,泳漆,电沉积。
创始于二十世纪六十年月,由福特汽车公司最先应用于汽车底漆。
由于其精彩的防腐、防锈功能,很快在军工行业得到广泛应用。
近几年由汽车行业引申到自行车、摩托车及家电、轻工饰品德业。
如:空调、彩电、洗衣机、摩托车、眼镜、锁具、灯具及饰品、发夹、领带夹等各个金属行业及铝材外表防锈行业。
由于其优良的质素和高度环保,正在逐步替代传统油漆喷涂。
工艺原理:电泳漆以离子状态分散于水中,在直流电场作用下,定向集结五金工件外表上,形成致密外表膜。
电泳特点:1.附着力强,漆膜不易脱落,连续弯折不爆皮。
2.均匀致密,工件内处任何部位漆膜厚薄皆均匀全都。
即使在很凹的部位,即可形成均匀的保护膜。
并可利用调整不同的操作电压,即可掌握镀层的厚度。
到达极高的防腐性。
消退了喷漆中会消灭的结皮,泪痕等不良故障。
3.耐蚀性佳,其他任何涂装方式的耐腐蚀性均不行与之相比较。
4.合符环保,水性涂料,无毒、无污染、无有害物质残留。
比较工程油漆喷涂电泳涂装附着力不强,易脱落强,很难脱落防府性不耐腐蚀耐腐蚀装饰性外表粗糙,平滑度低平展光滑环保性污染严峻合符环保要求电泳与喷涂的比较与区分比较工程油漆喷涂电泳涂装附着力不强,易脱落强,很难脱落防府性不耐腐蚀耐腐蚀装饰性外表粗糙,平滑度低平展光滑环保性污染严峻合符环保要求主题:电泳〔电著〕涂装进展及应用A、概述电泳涂装技术争论起于一百多年前,基于人们对金属外表防腐防锈要求的不断提高而相关表面处理工艺技术又不能较好地解决这种需求的压力下,而被渐渐研制开发。
直到60 年月才由George Brewer 博士及福特汽车公司研制开发成功阳极电泳漆。
其最早应用于福特汽车公司的涂装线,随着阳极电泳漆生产使用,日渐暴露其漆膜中包含有金属离子造成抗蚀性差的缺陷,因而,高抗蚀性的阴极电泳漆于七十年月被开发成功,并被人们等认可并大力推广应用。
之后,电泳技术进展日月异,产品品种由环氧型树脂型进展到丙烯酸型及聚氨脂型。
电泳漆工艺流程

电泳漆工艺流程电泳漆工艺流程通常包括以下几个步骤:预处理、电泳涂装、烘烤和后处理。
预处理阶段是整个工艺流程的第一步,目的是去除表面的油污和氧化物,提供一个干净的基材表面,以便良好的粘附涂料。
此阶段的处理包括清洗、脱脂、水洗和磷化等。
首先,将待处理的工件放入清洗槽中,利用化学清洗剂去除表面的油污。
然后,将工件放入脱脂槽中,使用溶剂溶解油脂。
接下来是水洗步骤,通过水洗去除清洗剂和溶剂的残余物。
最后,将工件放入磷化槽中,利用磷酸盐溶液形成一层磷酸盐转化膜,增加涂层的附着力。
接下来是电泳涂装阶段,即给工件表面涂上电泳漆。
首先,将工件装在漆槽中,然后注入电泳漆溶液,相应的工艺参数根据不同的涂料和工艺进行调整。
然后,通过施加恒定的直流电压,形成均匀的电场,使电泳漆离子在阳极上产生,并沉积在阴极上。
在电泳涂装阶段,涂料的选择、工件的悬挂和电泳涂装参数的调整都会影响涂层的质量。
接下来是烘烤阶段,即将涂上电泳漆的工件放入烘烤室中进行加热,以使涂层干燥和固化。
这一步骤旨在去除溶剂、挥发性成分和水分,使涂层形成均匀、致密的膜层。
工艺参数如烘烤温度、时间和湿度需要根据涂料的特性和工件的尺寸进行调整。
最后是后处理阶段,主要是对涂层进行检查和修复。
检查涂层的质量,包括涂层的附着力、厚度和外观等方面。
同时,对涂层进行必要的修复,如修补划痕、抛光和调整颜色等。
后处理的目的是确保涂层符合客户的需求和要求。
总的来说,电泳漆工艺流程包括预处理、电泳涂装、烘烤和后处理四个主要阶段。
通过这些步骤,可以实现对工件表面的清洁和涂层的均匀、致密和耐用的成膜。
不同的涂料和工件需要调整相应的工艺参数,以获得高质量的涂层。
这种工艺流程在汽车和家电等行业得到广泛应用,为产品提供了美观、保护和耐用的涂装效果。
电泳漆工艺流程详解
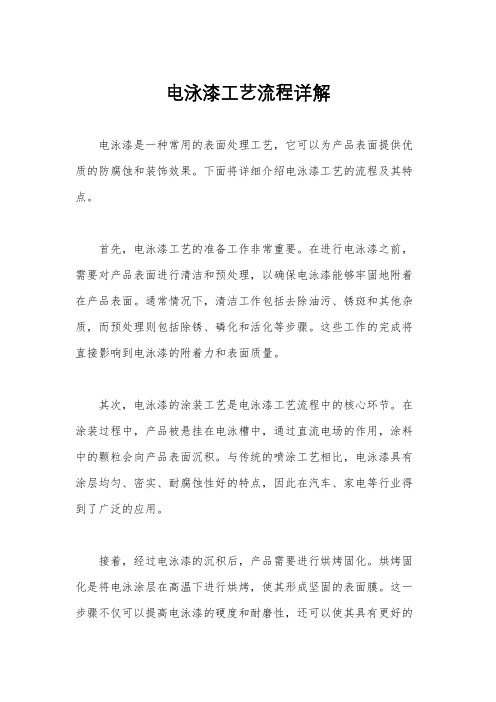
电泳漆工艺流程详解
电泳漆是一种常用的表面处理工艺,它可以为产品表面提供优质的防腐蚀和装饰效果。
下面将详细介绍电泳漆工艺的流程及其特点。
首先,电泳漆工艺的准备工作非常重要。
在进行电泳漆之前,需要对产品表面进行清洁和预处理,以确保电泳漆能够牢固地附着在产品表面。
通常情况下,清洁工作包括去除油污、锈斑和其他杂质,而预处理则包括除锈、磷化和活化等步骤。
这些工作的完成将直接影响到电泳漆的附着力和表面质量。
其次,电泳漆的涂装工艺是电泳漆工艺流程中的核心环节。
在涂装过程中,产品被悬挂在电泳槽中,通过直流电场的作用,涂料中的颗粒会向产品表面沉积。
与传统的喷涂工艺相比,电泳漆具有涂层均匀、密实、耐腐蚀性好的特点,因此在汽车、家电等行业得到了广泛的应用。
接着,经过电泳漆的沉积后,产品需要进行烘烤固化。
烘烤固化是将电泳涂层在高温下进行烘烤,使其形成坚固的表面膜。
这一步骤不仅可以提高电泳漆的硬度和耐磨性,还可以使其具有更好的
光泽和色彩稳定性。
最后,经过烘烤固化的产品需要进行检验和包装。
检验工作主要包括对电泳漆涂层厚度、附着力、耐腐蚀性等性能进行检测,以确保产品质量符合要求。
而包装工作则是为了保护产品表面不受损坏,并便于运输和存储。
总的来说,电泳漆工艺流程包括准备工作、涂装、烘烤固化、检验和包装等环节。
它具有涂层均匀、耐腐蚀性好、环保等优点,适用于各种金属制品的表面处理。
希望本文的介绍能够帮助大家更好地了解电泳漆工艺流程,并在实际生产中加以应用。
浅谈电泳涂装漆膜的工艺和若干问题

浅谈电泳涂装漆膜的工艺和若干问题1前言金属表面电泳涂装工艺在我国涂装行业中已经得到普遍采用,尤其在汽车行业中应用最为广泛。
电泳涂装是利用外加电场使悬浮于电泳液中的颜料和树脂等微粒定向迁移并沉积于电极之一的基底表面的涂装方法,是对水性涂料最具有实际意义的施工工艺,其主要功能是防腐蚀性。
2电泳涂装的工艺流程和工艺特点2.1电泳涂装的工艺流程汽车金属表面的电泳涂装,其工艺流程为:预清理→上线→除油→水洗→除锈→水洗→中和→水洗→磷化→水洗→钝化→电泳涂装→槽上清洗→超滤水洗→烘干→下线等。
2.2电泳涂装的工艺特点电泳漆膜具有涂层丰满、均匀、平整、光滑的优点,电泳漆膜的硬度、附着力、耐腐蚀、冲击性能、渗透性能明显优于其它涂装工艺。
主要有以下特点:①电沉积涂漆获得的漆膜质量与通电量成正比,所以可借助增减通电量来调整涂膜沉积量。
②工件各部位都可获得比较均匀的漆膜,如内层、凹陷、焊缝、箱形体的内外表面等,解决了其它涂装方法对复杂形状工件的涂装难题,防腐性能获得显著改善。
③电沉积漆膜含水率低,它不溶于水,不流动,不易产生垂滴、流痕、滞痕等漆膜缺陷,也不会在烘干过程中产生像浸涂漆膜烘干时经常发生的溶剂气洗现象。
④由于带负电的高分子粒子在电场作用下定向沉积,因而电沉积漆膜的耐水性能很好,附着力也比其它施工方法高。
⑤电沉积涂漆所用漆液浓度低、粘度小,因而浸渍作用粘附于被涂物而带出的漆较少,特别是超滤技术应用于电沉积涂漆后,涂料的利用率可达95%以上。
⑥采用水溶性涂料,以水为溶解介质,节省了大量有机溶剂,大大降低了大气污染和环境危害,安全卫生,同时避免了火灾的隐患。
⑦生产效率高,施工可实现自动化连续生产或间歇生产,大大提高劳动效率。
3电泳涂装漆膜中出现的问题、原因及其解决措施电泳涂装与其它涂装方法相比有着明显的优越性,但是因为电泳涂装方法的独特性,故也有其独特的缺陷。
常见的电泳涂装漆膜缺陷及其产生原因和解决措施。
3.1漆膜粗糙或颗粒电泳槽液有沉淀物、凝聚物或其它异物,槽液过滤不良;电泳后冲洗液不干净或冲洗水中含漆浓度过高;进入电泳槽的被涂工件不洁;磷化后的水洗不净;涂装生产区域周围环境差和烘干过程中烘房内污物较多。
- 1、下载文档前请自行甄别文档内容的完整性,平台不提供额外的编辑、内容补充、找答案等附加服务。
- 2、"仅部分预览"的文档,不可在线预览部分如存在完整性等问题,可反馈申请退款(可完整预览的文档不适用该条件!)。
- 3、如文档侵犯您的权益,请联系客服反馈,我们会尽快为您处理(人工客服工作时间:9:00-18:30)。
电泳漆涂装应用工艺
在采用电泳漆涂装时,应在涂装线的设计、制造及调试上保证能满足电泳漆的应用参数要求,以获得最佳的电泳漆膜。
一、电泳漆的涂装工艺
将前处理合格的干燥工件浸入电泳槽液中,在最佳涂装电压下通直流电,槽液中的成膜物质在电场作用下沉积到工件上,120~180sec后从槽中取出涂好的工件,并送往进行后冲洗工序,最后烘干。
调稀电泳漆和清洗所用的去离子水的技术指标:
PH:5.5~6.8 电导率:小于10μs/cm(25℃)
如果电导率高于25μs/cm,就会对槽液造成污染。
由于电泳槽液是有机物的水溶液,所以槽液需不断更新才能保持稳定,一般更新期不超过三个月,更新期超过六个月则需要特殊护理。
二、新建电泳涂装线设备的清洗
在完成设备验收调试及一般清洗后,应按标准连续清洗下列设备:
1.电沉积槽及槽内外的配管和相关设备。
2.备用槽及槽内外的配管。
3.水洗槽,水洗室及有关设备。
4.UF装置及有关设备。
5.极液系统及有关设备。
6.搅漆装置及配管。
7.调温设备及纯水供给设备。
8.运输设备及烘干室。
推荐清洗工艺:
1.自来水冲洗后,除去垃圾异物,需要时用稀料擦洗油份。
2.安装好过滤器,将自来水加到够循环的水位,循环两小时。
3.加入配置好的专用清洗溶剂105%,循环16小时后,排放用于清洗备用槽和水洗槽(备用槽、水洗槽清洗工艺同电泳主槽)
4.自来水循环清洗两次,每次两小时。
5.加满自来水,并加入0.5%氨水(25%)和105%专用清洗溶剂循环8小时,排放用于清洗被用槽,水洗槽及相关设备。
6.用高压水冲洗两遍后,注满自来水循环两小时。
7.加入1%乳酸,使其PH值为5~6,充分循环清洗16小时,排放用于清洗备用槽和水洗槽。
8.用高压水冲洗两遍后,加满自来水循环2小时。
9.用去离子水冲洗两遍后,加满去离子水,至少循环12小时(去离子水的电导率小于
20μs/cm)
10.检测各设备中去离子水的电导率,最高电导率应小于50μs/cm,否则应再换去离子水进行循环清洗。
11.取槽中去离子水配漆做缩孔试验,并测试各项参数,若合格则认为清洗符合要求,否则应重复前述清洗过程直至合格。
12.在1~9各项中,个阀门应多次开阀,搅漆设备和极液循环系统也同时清洗。
13.前处理设备及烘干室也应按设备制造厂商的要求进行清洗,以保证产品涂装质量。
三、缩孔试验方法
方法1:预先配置好无缩孔的电泳漆槽液(用合格的去离子水配制),并在相同条件下涂装6块样板,冲洗干净后,三块浸于合格的去离子水,三块浸于待检的去离子水中各一分钟,然后一块烘干,并比较外观,无缩孔或与标准板相同(个数及大小)则认为合格。
方法2:用待检的去离子水配漆,泳涂样板,这是最可靠的方法。
方法3:取待检的去离子水,加入到预先配置好的电泳槽液中,加入10%量后再行测试各项参数,合格既符合要求(主要检测PH值、电导率、电压、厚度、板面状态、温升等)。
清洗合格后,做以下点检:
1.全部阀门的开、闭状态。
2.安置过滤网。
3.设置电极隔膜,投入极液。
4.槽内有无遗忘物及二次污染。
四、初次投槽方法
1.在完成涂装线调试,彻底清晰后,进行初次投槽前的准备,应先确认以下各项:
A、足够的合格的电泳投槽漆。
B、足够的去离子水,并检测去离子水的水质。
C、涂装线各设备的各功能进行全面检查。
D、连续初次投槽的时刻表及应急方案。
E、人员安排。
F、处次投槽时用户,设备制造厂,涂料供应厂均应参加。
2.投槽工艺
①关闭通往UF系统的全部阀门。
②在电泳槽内加入足够量的去离子水,使其能维持最起码的循环。
③每10吨电沉积槽及相关设备的容积加入0.5Kg电泳漆中和剂及10升的电泳漆专用溶剂。
④把去离子水或槽液抽入到搅漆罐中,开启搅拌并用隔膜泵将电泳投槽漆打入到搅漆罐中,充分搅拌15分钟,检查溶解度。
⑤将稀释好的漆液,打入到电泳槽中,并维持电泳槽中的循环。
⑥根据配置量不断重复上述过程,直至槽液固体份符合要求为止。
配槽原则
在初次配置电泳漆槽液中,槽液的固体含量是由0逐渐变化到规定值,这是一个渐变分
散过程。
为了使大槽内的漆液分散良好,在搅漆罐内调制的漆液固体含量应维持在25~30%。
第一次使用去离子水配制,以后各次则使用含有一定固体含量的槽液。
为了使搅漆罐中的漆液固体含量维持在25~30%,保证漆液进入大槽内分散良好,必须分阶段的调整原漆与兑稀槽液的比例。
配槽使用的去离子水量应按槽体及相关设备的容积来计算,但不是一次性的加入槽内,而是根据大槽内漆液固体含量的变化分阶段加入。
配槽总则是:既要使大槽中漆液固体含量低于5%的时间愈短愈好,又要使配漆罐的漆液固体含量维持在25~30%范围内,以保证漆液进入大槽内分散良好。
3.试涂装
①在完成投槽后,将槽液温度调整到规定的工艺温度。
②循环2~3小时后检查以下项目:
A.涂料特性值:PH值、固体份、MEO值、灰份
B.涂面状态:有无缩孔等重大弊病(低电压泳涂样板检查)
③配槽24小时后按UF装置的说明书、启动UF装置,开始运转过滤系统,并超滤出10~25%的UF液至UF冲洗槽及UF贮槽,以调整槽液进入工作状态。
④调整极液,并开始循环,确认极液循环正常。
⑤调整电泳后的水洗系统。
⑥试涂装:熟化48小时进行工件的涂装,根据实验市的实验结果来设定试涂装的条件(温度、电压、时间),电压要比实验室电压高50V左右。
试涂装工件烘干后可以进行以下检查:膜厚、漆膜表面状态和干燥性。
⑦在投槽初期,涂状电压会天天变化,应分析前日膜厚分布来修正涂装条件。
五、电泳漆的日常管理检测频次
1.生产检测频次:
为了减少生产中的不正常现象的发生,每次应控制以下各项参数。
A.电泳槽液:槽液温度、浸入时间、通电时间、运输链速度、涂装电压、最大电流密度、去离子水消耗量及水质情况、液面流速、液面落差和泡沫情况
B.被涂工件:表面质量、膜厚
C.超滤液:流量及进出口的压差
D.补加系统:补加漆分散状态
E.极液系统:极液流量,去离子水补加量
F.循环冲洗液:冲洗液液面高度
G.循环泵密封体系:密封液液面位置
H.烘干室:烘干条件
2.实验室检测频次。
(附后表)注:所有检测数据、加入补槽漆量、添加各种补槽漆、助剂
电泳漆液参数的调整及涂膜缺陷的排除。