第7章_物料需求计划(MRP)的编制
物料需求计划mrp

100
002 4-抽 屉 文 件 柜
60
60 120
60
007 桌 子
150
150
90
产品结构清单
(Bill of Material,BOM)
BOM是产品结构的明细单,表示产品是 如何组成的。
– 所需零部件数目 – 制造提前期
3-抽屉文件柜的产品结构
3-抽屉文件柜
级别 0
铁皮外壳组装 (1)
1周
库存的精确性
1. 保持整齐有序的仓库 2. 控制进入仓库的通道 3. 建立和执行有效的库
存的取货制度 4. 保证及时和准确的仓
库进货的记录 5. 对物质库存定期进行点数 6. 及时纠正库存差错 (使用
循环点数的方法)
订制批量: LT: 总需求量 已在途的订货 计划库存 净需求量 计划应收到的订货 计划应发出的订货
制造资源计划
Manufacturing Resource Planning (MRP II)
MRP的延伸 对经营一个企业的所有资源进行计划 MRP II 的不同形式:
– Service Requirements Planning (SRP) – Business Requirements Planning (BRP) – Distribution Requirements Planning (DRP)
MRP 输出表
PD
1 2 3 4 5 6 7 8 9 10
项目 – 物品名称或编号
LLC – low-level-code; 项目在产品结构中出现的最 低层编码
MRP 输出表的组成
批量(Lot size) – 可多次重复发出的订货数量
提前期 (lead time,LT)
第7章物料需求计划

(四)其他信息:低位码、损耗系数(组装废品系数、零 件废品系数、材料利用率)
(五)能力需求计划(后述) (六)生产计划:生产什么、生产多少、何时开始、何时
结束 (七)采购计划:采购什么、采购多少、何时开始、何时
B×2 LT=1
D×2 LT=2
Enterprise Resource Planning
1. 根据产品A的MPS计划、提前期和期初库存量计算产品A 的毛需求量、净需求量和下达订单的数量、时间
物料 MRP
计划周期
项目 项目指标 1 2 3 4 5 6 7 8
MPS计划量
200
毛需求量
200
A
净需求量
Y
0层
1层
F
D
G
D
E
H
K
2层
对应物料D的LLC=2 其他如物料X的LLC=0;物料A的LLC=1;物料H的LLC=2
物料需求计划
Enterprise Resource Planning
(五)损耗系数:说明在生产或采购过程中的损 耗情况
1. 组装废品系数:用于估计在组装过程中损耗的 系数,主要对部件的毛需求量进行调整
A的毛需求量2 (相关需求)
80 30 60
物料需求计划
Enterprise Resource Planning 3. 根据物料A的MPS计划量(独立需求)和相对于产品X和Y
的相关毛需求量计算物料A的毛需求总量
MRP 项目 X的MPS量 X的订单量
计划周期
1 2 3 4 5 6 7 8 9 10 11 12 13
MRP——精选推荐

物料需求计划(MRP)的编制物料需求计划(Material Requirements Planning,MRP)是ERP管理层的计划,MRP计划的运行是由ERP决策层的主生产计划(MPS)驱动的。
1MRP的概念1.1物料需求计划物料需求计划(MRP)是ERP的核心,是一种物料管理和生产方式,它建立在MPS的基础上。
根据产品的BOM、工艺路线、批量政策和提前期等技术和管理特征,生成原材料、毛坯、外购件的采购作业计划和零部件生产、装配计划,从而达到有效管理和控制企业物料流动的微观计划。
1.2物料需求计划(MRP)的作用MRP的作用就是利用有关书录信息,实现各计划时间段(计划周期)的采购计划(采购订单)和制造计划(生产订单)。
MRP主要解决以下5个问题:1)要生产(含采购或制造)什么?(这些数据从MPS获得)2)要用到什么?(这些数据根据BOM表展开获得。
)3)已经有了什么(包括已分配量和以订货量)?(这些数据根据物料库存信息获得。
)4)还缺什么?(这些数据根据MRP计算结果获得)。
5)何时安排(包括何时开始采购制造、何时完成采购制造)?(这些数据依据物料的提前期获得)。
1.3物料需求计划(MRP)在ERP中的层次关系对于ERP共有5个层次的计划中,物料需求计划处于第四层,属于管理层计划,它与其它计划间的关系详如下图所示。
注:BOM:分解各种物料的工具。
物料编码:识别、使用的依据。
工艺路线和工序:安排生产作业顺序的基础。
工作中心:把MRP与能力需求计划关联起来。
制造日历:有助于明确安排时间。
2.1 MRP的输入数据项主生产计划主生产计划说明一个企业在一个时期内(计划展望期内)计划生产的产品名称、数量和日期。
主生产计划作为MRP的输入数据项、主要解决“生产(含采购和制造)什么”,亦即“生产(含采购和制造)多少”问题。
这里的主生产计划的计划(或排产)对象是指企业的最种产品。
主生产计划是MRP最重要和最基本的数据,开始编制物料需求计划时,必须首先得到一个有效的主生产计划。
MRP的制定全过程
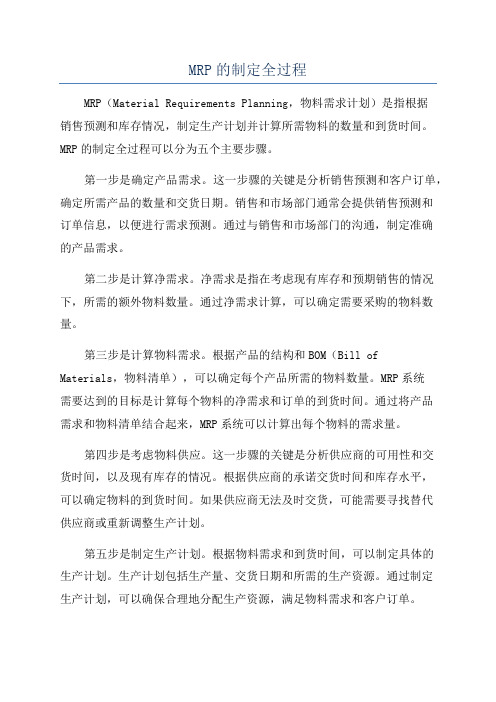
MRP的制定全过程MRP(Material Requirements Planning,物料需求计划)是指根据销售预测和库存情况,制定生产计划并计算所需物料的数量和到货时间。
MRP的制定全过程可以分为五个主要步骤。
第一步是确定产品需求。
这一步骤的关键是分析销售预测和客户订单,确定所需产品的数量和交货日期。
销售和市场部门通常会提供销售预测和订单信息,以便进行需求预测。
通过与销售和市场部门的沟通,制定准确的产品需求。
第二步是计算净需求。
净需求是指在考虑现有库存和预期销售的情况下,所需的额外物料数量。
通过净需求计算,可以确定需要采购的物料数量。
第三步是计算物料需求。
根据产品的结构和BOM(Bill of Materials,物料清单),可以确定每个产品所需的物料数量。
MRP系统需要达到的目标是计算每个物料的净需求和订单的到货时间。
通过将产品需求和物料清单结合起来,MRP系统可以计算出每个物料的需求量。
第四步是考虑物料供应。
这一步骤的关键是分析供应商的可用性和交货时间,以及现有库存的情况。
根据供应商的承诺交货时间和库存水平,可以确定物料的到货时间。
如果供应商无法及时交货,可能需要寻找替代供应商或重新调整生产计划。
第五步是制定生产计划。
根据物料需求和到货时间,可以制定具体的生产计划。
生产计划包括生产量、交货日期和所需的生产资源。
通过制定生产计划,可以确保合理地分配生产资源,满足物料需求和客户订单。
在整个MRP制定的过程中,还需要不断地监控和调整。
MRP系统应该能够及时反馈物料到货时间和库存水平的变化,以便及时采取行动。
此外,还需要与销售、采购、生产和库存部门等相关部门进行紧密合作,确保准确的需求信息和物料信息。
总结起来,MRP的制定全过程包括确定产品需求、计算净需求、计算物料需求、考虑物料供应和制定生产计划。
通过这个过程,可以实现合理的生产计划和物料需求,确保生产和供应链的顺利运转。
同时,MRP系统的有效运用还需要与相关部门的紧密合作和持续的监控与调整。
物料需求计划

物料需求计划物料需求计划(MRP)是一种用于计划生产所需原材料和零部件的方法。
通过物料需求计划,生产企业可以确保在生产过程中有足够的物料供应,从而避免生产线停工和生产延误。
本文将讨论物料需求计划的基本原理和流程,以及如何有效地实施物料需求计划。
物料需求计划的定义和作用物料需求计划是一种基于生产计划和销售订单的方法,用于确定制造企业需要什么类型和数量的原材料和零部件,以及需要何时购买或生产这些物料。
物料需求计划的主要作用包括:•确保生产过程中有足够的物料供应,避免生产线停工•优化库存管理,减少库存积压和库存过多•提高生产计划的准确性和可靠性•减少物料采购和库存管理成本物料需求计划的流程物料需求计划通常包括以下几个步骤:1.制定生产计划和销售预测:根据市场需求和销售预测,制定生产计划,确定需要生产的产品数量和日期。
2.识别物料需求:根据生产计划,确定每种产品所需的原材料和零部件的种类和数量。
3.检查现有库存:检查当前库存,确定哪些物料需要订购或生产。
4.编制需求计划:根据物料清单和生产计划,编制物料需求计划,确定每种物料的采购或生产日期和数量。
5.执行需求计划:根据物料需求计划,及时采购或生产所需的物料。
物料需求计划的实施策略为了有效地实施物料需求计划,企业可以采取以下策略:1.建立完善的物料清单:建立详细的物料清单,明确每种产品所需的原材料和零部件。
2.优化库存管理:根据需求预测和库存水平,优化库存管理,避免库存积压和库存不足。
3.建立供应链合作关系:与供应商建立紧密的合作关系,确保及时供应物料。
4.使用物料需求计划软件:利用物料需求计划软件,自动化物料需求计划的制定和执行过程,提高效率和准确性。
5.持续改进:定期评估物料需求计划的执行效果,根据反馈信息不断改进物料需求计划的流程和策略。
结语物料需求计划是制造企业保持生产运作顺畅和高效的重要工具。
通过合理制定和执行物料需求计划,企业可以实现生产过程的优化和成本的降低,提高竞争力。
第七章 MRP

§7.1 MRP概述
一、传统订货点方法的缺点与MRP的提出
(一)订货点方法主要缺点 1.盲目性
2.高库存与低服务水平 3.“块状”需求,增加了库存。
(二)MRP的提出
MRP:是在定货点法(order point system)计划基 础上发展形成的一种新的库存计划与控制方法,是建立 在计算机基础上的生产计划与库存控制系统。
二、MRP采购实施的基础条件
1.企业实施了MRP管理系统 2.企业有良好的供应商管理
三、MRP采购的特点
(一)需求的相关性 (二)需求的确定性 (三)计划的精细性 (四)计算的复杂性
四、MRP采购的优缺点
§7.3 MRP发展历程
一、 时段式MRP阶段 二、闭环MRP(closee-loop MRP)
资源需求计划、能力需求计划 、控制计划
三、MRPⅡ(Manufacturing Resource Planning)
这种把生产、财务、销售、采购、工程技术等各个子系 统结合为一个一体化的系统,称为制造资源计划 (MRPⅡ)。
四、ERP
ERP是在MRPⅡ基础上发展起来的,以供应链管理 思想为基础,以先进计算机及网络通信技术为运行 平台,能将供应链上合作伙伴之间的物流、资金流、 信息流进行全面集成的管理信息系统。
§7.2 MRP的原理
一、MRP基本原理
需求预测
主生产计划
客户订单
产品信息 (物料清单文件 ---产品结构图)
MRP计算处理 (物料需要的 时间和数量)
库存信息 (现有剩余库存、 已下的订单、订 货提前期)
采购计划
加工计划
(一)MRP的输入
MRP的编制教程

产品结构图
A
0层
B(1)
C(2)
D(2)
1层
C(2)
E(3) D (3) E(1) G(3千克)
2层
D (3) E(1) H(2.5) H(2.5) H(2.5)
3层
A
B(1)
C(2)
C(2)
D (3) E(1) E(3) D (3) E(1)
D(2)
H(2.5) H(2.5) H(2.5) G(3千克)
5 6 7 8 9 10 11
40
50
15
S
B
C
Lead time = 6 for S
Master schedule for S
8 9 10 11 12 13
40
20
30
Master schedule for S sold directly
12 3 10 10
Periods
Gross requirements: B
• MRP是一种存货控制方法,也是一 种时间进度安排方法。
14
MRP概述-2
• MRP始于最终商品的时间进度安排 ,再由它转换为特定时间生产产成品 所需的部件、组件及原材料的时间进 度安排,它主要回答三各问题:
需要什么? 需要多少? 何时需要?
15
2.3 MRP的基本原理-1
• 基本思想:围绕非独立需求的物料, 按需准时生产。
1. Facility utilization 2. Personnel needs
Intermediate-term
3. Subcontracting
中期计划
Master Schedule 主生产计划
1. MRP
第七章 MRP、MRPⅡ与ERP(生产与运作)
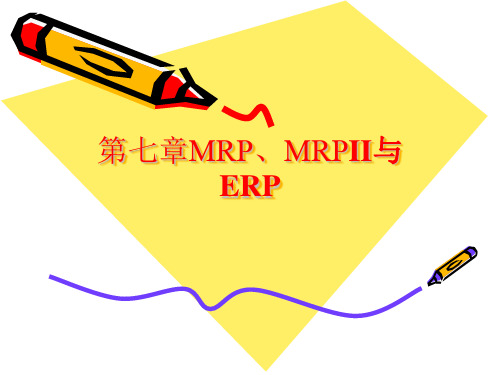
第一节 MRP概述
部件P 第0层 部件A 部件B 部件C 第1层
部件A1
部件A2
部件B1
部件B2
部件B3
部件C1
部件C2
第2层
A1
A2
A3
第3层
图7—1 产品结构或物料清单
第一节 MRP概述
(二)MRP的原理和逻辑 1.MRP的原理 (1)根据主生产计划(Master Production Schedule MPS)确定 独立需求产品或备件备品的需求数量和日期。 (2)依据物料清单自动推导出构成独立需求物料的所有相 关需求物料的需求,即毛需求。 (4)由毛需求以及现有库存量和计划接收量得到每种相关 需求的净需求量。 (4)根据每种相关需求物料的各自提前期(采购或制造)推 导出每种相关需求物料开始采购或制造的日期。如图7- 2为MRP的处理过程图。 净需求量=毛需求量-计划接收量-现货量(现有库存量)
(三)能力需求计划
工作中 心文件
工厂 日历
工艺路 线文件
车间在 制任务 文件
零部件 作业 计划
A
零件工序进度计算编制 工作中心可用 能力计算
工序进 度计划 文件
工序进度维护
工作中心负荷计算
负荷与能力的分析
负荷与能力的直方图
负荷分布报告
工作中心可用 能力计算
人工进行 负荷调平
决定加班或替换 工作中心 任务提前或拖期 零部件作业 计划修改
B计划投入量
C 总需求量 可用库存量40 净需求量 计划交货量 计划投入量 D 总需求量 可用库存量30 净需求量 计划交货量 计划投入量 1530 30 30 1560 1560 0 1530 1530 1200 40 40 40
- 1、下载文档前请自行甄别文档内容的完整性,平台不提供额外的编辑、内容补充、找答案等附加服务。
- 2、"仅部分预览"的文档,不可在线预览部分如存在完整性等问题,可反馈申请退款(可完整预览的文档不适用该条件!)。
- 3、如文档侵犯您的权益,请联系客服反馈,我们会尽快为您处理(人工客服工作时间:9:00-18:30)。
是对主生产计划的各个项目所需的全部制造件和全部采购件
的需求计划。
它是根据主生产计划对最终产品的需求数量和交货期,推导 出构成产品的零部件及材料的需求数量和需求日期,直至导 出自制零部件的制造订单下达日期和采购件的采购订单发放 日期,并进行需求资源和可用能力之间的进一步平衡。
第7章 物料需求计划(MRP)的编制
本章内容:
7.1 MRP的概念 7.2 MRP的工作原理
7.3 MRP处理过程
7.4 MRP的编制案例 7.5 MRP的更新方法
ቤተ መጻሕፍቲ ባይዱ
7.1 MRP的概念
7.1.1 什么是物料需求计划 7.1.2 物料需求计划的作用 7.1.3 MRP在ERP中的层次关系
7.1.1 什么是物料需求计划
还处理其 它项目? 否
逐 层 处 理 各 个 项 目
是
结束
7.3 MRP处理过程
7.3.1 MRP处理过程系统流程图 7.3.2 每一个项目的处理步骤
7.3.2 每一个项目的处理步骤
(1)计算毛需求 物料毛需求=物料独立需求+父项的相关需求 父项的相关需求=父项的计划订单数量×项目用 量因子
ï Ï è ï Æ ® Î À Ð Ç » º ¨ © £ MRP£
É ¹ ¨¤ ² ¸ ¶ µ Æ ì ¨¤ Ö Ô ¶ µ
7.2 MRP的工作原理
7.2.1 MRP工作原理图 7.2.2 MRP结构图的有关说明
7.2.2 MRP结构图的有关说明
一、MRP的输入数据项
1.主生产计划
主生产计划说明一个企业在一个时期内(即计划展望 期内)计划生产的产品名称、数量和日期。 主生产计划为 MRP提供基本的数据,开始编制物料
7.1 MRP的概念
7.1.1 什么是物料需求计划 7.1.2 物料需求计划的作用 7.1.3 MRP在ERP中的层次关系
7.1.2 物料需求计划的作用
物料需求计划MRP的基本作用是:利用有关输入信息,实现
各计划时间段(即计划周期)的采购计划(即采购订单)
和制造计划(即生产订单)。
MRP是生产管理的核心,它将主生产计划排产的产品分解成
(5)何时安排(包括何时开始采购制造、何时完成采购
制造)?(这些数据依据物料的提前期获得)
7.1 MRP的概念
7.1.1 什么是物料需求计划 7.1.2 物料需求计划的作用 7.1.3 MRP在ERP中的层次关系
7.1.3 MRP在ERP中的层次关系
对于ERP共有五个层次的计划中,物料需求计划处于 第四层,属于管理层,它与其它计划间的关系可由下图描 述。
占用流动资金减少,但增加了加工或采购的费用,
考虑批量的主要原因是:降低订货成本、降低准备成本、降低运输成本、 降低在制品成本。
目前,物料需求批量的计算方法主要有:直接批量法(Lot for Lot)、 固定批量法(Fixed Quantity)、 固定周期法(Fixed Time)、 经济 批量法(Economic Order Quantity)
各自制零部件的生产计划和采购件的采购计划。
MRP主要解决以下五个问题:
(1)要生产(含采购或制造)什么?生产(含采购或制
造)多少?(这些数据从MPS获得)
(2)要用到什么?(这些数据根据BOM表展开获得) (3)已经有了什么?(这些数据根据物料库存信息) (4)还缺什么?(这些数据根据MRP计算结果获得)
ï µ ª Æ ® Æ Ò ½ Ó » º ½ ö ² ß ² ã
ú ú Æ ® ï Ù ¨ © É ² » º ´ · £ PP£
ðú ú Æ ® ¨ Ö É ² » º £ MPS£ © Ü í ã ¸ ¿ ²
ï Ï è Ç Æ ® ¨ Î À Ð ï » º £ MRP£ ©
第7章 物料需求计划(MRP)的编制
3.物料清单
物料清单是为装配或生产一种产品所需要的零部件、 配料或原材料的清单。物料清单说明产品是由什么组 成的,各需要多少。
MRP从物料清单中得到有关主生产计划项目的零部件、
原材料的数据。
4.库存信息
库存信息说明物料清单中列出的每个项目的如下数据: 物料可用数据和编制订单数据. (1)物料可用数据 ①现有库存量:指仓库中实际存放的可用库存量。
本章内容:
7.1 MRP的概念 7.2 MRP的工作原理 7.3 MRP处理过程 7.4 MRP的编制案例 7.5 MRP的更新方法
7.2 MRP的工作原理
7.2.1 MRP工作原理图 7.2.2 MRP结构图的有关说明
7.2.1 MRP工作原理图
ðú ú Æ ® Ö É ² » º ¿ ¢ è ï ¶ À Ð Ç ï Ï å ¤ Î À Ç µ â æ Å ¢ ¾ ´ Ð Ï ä ü î Ø Æ Ë Ò Ë
右图示的产品BOM结 构树中的零件C分别 处于产品结构树的l 层和2层,于是零件C 的低位码就是2,而 其他零件的低位码数 与它们位于产品结构 树的层次相同。
A LT=1 B(2) LT£ 2 ¼ D(1) LT=1 C(2) LT=3 C(2) LT=3
(2)损耗系数 在生产各个环节中,有各种各样的损耗,因此在MRP的 计算过程中,要考虑有关损耗系数,包括:组装废品系数、 零件废品系数、材料利用率等。 ①组装废品系数 组装废品系数是对部件毛需求的调整。当一个零部件在 装配它的父项时,能估计到零部件的损失或毁坏时,考虑 组装废品系数,它以百分数表示,存放在物料清单中。 例如,在装配产品A时,估计有5%的玻璃管毁坏,因此 在生产A所需的玻璃管的毛需求时要增加组装时的损耗部分。 如装配100件A的订单,当考虑其组装废品系数5%时,要有 105 (100+100×5%=105)个玻璃管部件的需求。
②零件废品系数
零件废品系数是对订单数量的调整。零件废品系数是 对项目本身在采购或生产过程中出现的损耗而考虑的。
例如,产品A的零件废品系数为2%,在组装时的组装 废品系数为5%,针对该需求制定MRP时,首先考虑2%的 废品系数,计算产品A的计划订单数,计划订单数量要比 计算的需要多2%,如A需求为100时,订单应为100+ 100×2%=102,然后根据计划订单数量再考虑组装A时的 组装废品系数,在这种情况下,A项目102的订单对玻璃管 的毛需求量应为108(102+102×5%)。
④批量规则(批量政策)
实际计划生产或采购的交付数量和订货数量并非等于净需求量,这是由 于在实际生产或订货中,准备加工、订货、运输、包装等都必须是按照
一定的数量来进行的,这一定的数量称为生产或订货的批量。批量规则
是库存管理人员根据库存管理的要求和目标权衡利弊后选择的。
批量过大,占用的流动资金过多,但加工或采购的费用减少;批量过小,
二、MRP的输出项
MRP的输出项主要有两项:采购订单和制造订单。
1、采购订单
采购订单主要包括四项内容:采购什么、采购多少、 何时开始采购、何时完成采购
2、制造订单
同样,制造订单主要包括四项内容:制造什么、制造 多少、何时开始制造、何时完成制造
注意:上述MRP输出的采购订单和制造订单,必须经 过企业的计划人员检查确认后,才能下达到采购部门 和车间去执行。
③材料利用率
材料利用率是有效产出与总输入的比率,即:材料利
用率=有效产出/总投入。 材料利用率,同零件废品系数一样,均说明预计的生 产损耗情况,只是表述方法(术语)不同而已。 例如:某装配件的材料利用率是95%,那么为了要100
件的产成品就要有106(注:10095%=105.3)个装配件才
能保证零件废品系数与材料利用率。
7.3 MRP处理过程
7.4 MRP的编制案例 7.5 MRP的更新方法
(6) 考虑损耗因子和提前期下达订单计划(又称计划订单下 达),包括计划投入量和投入的时间。
计划投入量=计划产出量÷损耗系数
计划投入时间=计划产出时间-提前期
(7) 利用计划订单数量计算同一周期内更低一层相关项目的毛 需求,进入下一个循环。
第7章 物料需求计划(MRP)的编制
本章内容:
7.1 MRP的概念 7.2 MRP的工作原理
例1 推算毛需求量 (当独立需求与相关需求同时存在时)
已知:物料A既是产品X的组件又是产品Y的组件,BOM图 见下图。所以,A的需求为相关需求;此外,A作为配件 又有独立需求。已知MPS计划为:在第6、8、11个计划周 期时产出的产品X分别为25、30、15件;第9、11、13个 计划周期时产出产品Y分别为40、15、30件;在第1、2周 期产出A产品均为15件。因此,物料A的总的毛需求应为 其独立需求和相关需求之和。其算例见下表。
X(LT=4)
Y(LT=6)
A(1)
B(1)
A(1)
C(1)
产品X、Y的BOM图(物料X的需求关系〕
物料A的毛需求计算表 周 X(lt=4) Y(LT=6) 相关需求X-A 相关需求Y-A 独立需求A A的毛需求 15 15 15 40 40 30 15 45 25 40 30 15 15 30 1 2 3 4 5 6 25 7 8 30 40 9 10 11 12 13 15 15 30
需求计划时,必须首先得到一个有效的主生产计划。
2.独立需求
当一个项目的需求不能直接从另一个项目的需求计划得 到时,这种需求称为独立需求;否则,为相关需求。 独立需求与相关需求的概念是相对的。例如,若生产圆 珠笔,则笔的需求是独立需求,其需求数量是由预测得 到的,而对构成笔的笔芯和弹簧之类的项目而言便是相 关需求。其需求数量是通过计划得到的。但是,若想单 独销售笔芯,则笔芯又是独立需求。 在编制物料需求计划时,必须认真地分析与收集独立需 求与相关需求。