次氯酸钙生产工艺优化
氯气氧化分解草酸钴沉淀母液中的草酸

氯气氧化分解草酸钴沉淀母液中的草酸田庆华;易宇;郭学益【摘要】为有效去除草酸沉钴母液中残留的大量草酸,采用氯气作为氧化剂探索氧化分解母液中草酸的可行性.考察反应温度、反应时间、氯气用量、搅拌速度和钴离子浓度等因素对氧化效果的影响.确定了优化工艺条件:反应温度50℃,搅拌速度700 r/min,次氯酸钙150 g,6 mol/L盐酸550 mL,反应时间3h.在此条件下,草酸的氧化率可达97.9%,母液中残留的草酸质量浓度仅为0.42 g/L,处理后的母液可直接返回含钴物料的浸出,实现了工艺流程的闭路循环.%In order to remove the oxalic acid left in the mother-liquor originated from the precipitation of cobalt by oxalic acid, a novel method of using chlorine as the oxidant to decompose the oxalic acid was proposed. The main factors affecting the oxidation rate such as the solution temperature, reaction time, quantity of chlorine, stirring speed and Co2* concentration were investigated. The optimal conditions are as follows: 700 r/min of stirring speed, 150 g calcium hypochlorite, 550 mL of hydrochloric acid with concentration of 6 mol/L and 5 h of reaction time at 70 °C. Under these conditions, the oxidation rate of oxalic acid is 97.9% and the concentration of residual oxalic acid in mother liquor is only 0.42 g/L. The treated mother liquor can be returned directly for leaching cobalt. There is a closed circulation in the whole process.【期刊名称】《中南大学学报(自然科学版)》【年(卷),期】2011(042)009【总页数】5页(P2558-2562)【关键词】氯气;氧化;草酸;草酸钴【作者】田庆华;易宇;郭学益【作者单位】中南大学冶金科学与工程学院,湖南长沙,410083;中南大学冶金工程博士后流动站,湖南长沙,410083;中南大学冶金科学与工程学院,湖南长沙,410083;中南大学冶金科学与工程学院,湖南长沙,410083【正文语种】中文【中图分类】TF803.22目前,国内外草酸钴的生产主要采用草酸铵沉钴法,即在氯化钴溶液体系中,加入沉淀剂草酸铵,生成草酸钴沉淀,经过滤干燥得到产品[1]。
氯碱生产中淡盐水脱氯及氯回收工艺的改进

氯碱生产中淡盐水脱氯及氯回收工艺的改进发布时间:2023-03-08T03:32:57.643Z 来源:《福光技术》2023年3期作者:韩百胜[导读] 氯碱企业排出或泄漏的氯气是造成大气环境污染的重要污染物。
新疆圣雄氯碱有限公司新疆吐鲁番 838100摘要:氯碱企业排出或泄漏的氯气是造成大气环境污染的重要污染物。
青海电化厂原来的淡盐水脱氯流程,虽然脱出的氯气用碱液吸收,但由于吸收过程中冷却效果较差,次氯酸钠产品易受热分解,造成质量不合格,因而生产中往往将淡盐水脱出的氯气不经碱液吸收而通过放空管直接排入大气。
一般情况下,排入大气的氯气量为6~ 10kg /h。
当淡盐水质量不好时,排氯量甚至可达18kg /h。
为了根治氯气污染,我们对原有淡盐水脱氯及氯回收工艺进行了技术改造。
改造后氯气的回收率达到了99.87%。
关键词:淡盐水;氯回收;应用方法随着科技的进步,氯碱厂对烧碱生产中产生的氯水的处理也经历了直接排放—处理后排放—闭路循环—节能闭路循环的过程,不但避免了对环境的污染,而且使能源和资源得到了回收利用。
但目前国内某些氯碱厂还存在处理氯水方法不当的问题,而且经常有些厂家向“全国氯碱工业信息站”问起氯水处理方法的新进展情况。
应厂家的要求,笔者查阅了相关资料,现将有关氯水处理与利用的文献总结如下,希望对厂家能有所帮助。
1脱氯机理将淡盐水通入板框式平板膜一侧,作为吸收液的碱性溶液在膜的另一侧循环流动,氯便从水溶液中挥发出来,气态氯迅速地在膜孔内气体介质中扩散通过膜,与膜另一侧的碱性溶液进行反应,生成不可逆扩散的氯离子和次氧酸根离子。
水及非挥发性离子(cl-、K+、H+)被截留。
氯自膜一侧的水溶液中扩散至膜的界面层;在膜孔与溶液界面层处氯挥发成气态氯;气态氯在膜孔气体介质中迅速地从膜一侧向另一侧扩散;气态氯溶于碱性溶液。
2新、旧两种流程的比较2.1原有流程从电解工序返回化盐工序的含0. 2~0.5g /L游离氯的淡盐水流入淡盐水吹除槽(1)中,在进入吹除槽前往淡盐水中加入盐酸,使淡盐水中的游离氯均以氯分子状态存在。
84消毒液生产工艺

84消毒液生产工艺
生产84消毒液的工艺步骤包括以下几个方面:
1. 配料准备:准备所需的原料,包括次氯酸钙、钠水化物和水。
2. 清洁设备:确保生产设备干净,以防止污染。
3. 加水混合:将一定比例的水注入混合槽或容器中。
4. 加入次氯酸钙:将正确比例的次氯酸钙加入混合槽中。
5. 搅拌混合:使用混合设备将水和次氯酸钙均匀混合,并确保溶解彻底。
6. 筛选澄清:将混合液通过过滤器或沉淀槽进行澄清,去除杂质和固体颗粒。
7. 加入钠水化物:加入适量的钠水化物,使混合液中的次氯酸钙中和降低酸度。
8. 混合搅拌:再次使用混合设备将混合液均匀混合,确保反应充分。
9. 测试质量:取样并进行相关质量测试,确保产品符合标准。
10. 包装和储存:将成品84消毒液进行包装,并进行标签贴附。
存放在干燥、阴凉的库房中。
需要注意的是,在整个生产工艺中,应严格遵循操作规程和安全操作规范,保证员工的安全和产品的质量。
化纤生产过程优化降低成本提高效率的关键策略

化纤生产过程优化降低成本提高效率的关键策略化纤生产过程优化降低成本、提高效率,是每个化纤企业追求的目标。
在竞争激烈的市场环境下,寻找关键策略成为了必然选择。
本文将探讨化纤生产过程中的关键策略,并提出一些可行的方案。
一、优化生产工艺1. 工艺流程改进:针对化纤生产的每个环节,进行详细的流程分析和评估。
优化原材料的选择、配比比例、温度控制、反应时间等,确定最佳的生产方案和操作方法。
2. 设备更新升级:及时跟进行业技术的发展,引进新型设备和机械,提高生产效率和产品质量。
同时,对老旧设备进行改造,提升其性能和可靠性。
3. 节能降耗:通过节能降耗的措施,减少资源的浪费,降低能源消耗,例如优化工艺参数,减少废水排放,实施循环利用等等,从而降低成本。
二、质量控制与品质提升1. 强化质检环节:建立完善的质量检验体系,严格把控原材料的质量,确保生产过程中符合规定的技术指标,减少次品率,提高产品的合格率。
2. 进行产品创新:根据市场需求和潮流变化,进行产品创新和改良。
开发具有竞争力的新产品,提高市场份额,增加收益。
3. 建立质量管理体系:制定标准化的质量管理制度,加强对生产过程的监控和管理,建立追溯制度,及时纠正和改进不足,确保产品质量的稳定性和可靠性。
三、供应链管理优化1. 供应商合作:与优质的原材料供应商建立稳定的合作关系,加强沟通和协作,共同优化供应链流程,减少延迟和损耗。
2. 库存管理:合理制定库存策略,通过精确的需求预测和订单管理,降低库存压力和资金占用,提高资金周转率。
3. 运输物流优化:优化运输物流手段,减少运输时间和成本。
采用智能调度系统,合理安排运输路线,提高配送效率。
四、人力资源优化1. 培训提升:加强员工培训与技能提升,确保操作人员具备专业技能和良好的工作素养,提高工作效率和产品质量。
2. 激励机制:建立科学的绩效考核和激励机制,激发员工的积极性和创造力,鼓励团队合作,共同推动生产过程的优化。
次氯酸钙生产

次氯酸钙生产1次氯酸钙制备反应原理1.1次氯酸钙结晶种类在氯化反应器中装入浓石灰,然后通入氯气进行氯化反应,反应后生成次氯酸钙和氯化钙。
氯化钙在水中的溶解度较高而次氯酸钙的溶解度较低,所以氯化钙能够完全溶解在水中,次氯酸钙只能部分溶解,大部分以结晶形式析出。
这样就得到了次氯酸钙产品,将次氯酸钙结晶过滤分离后得到的固相进行干燥,制成了漂粉精。
其有效氯为60-70%,稳定性较好,非溶解性残渣较少。
基本反应式。
根据反应条件的不同,次氯酸钙结晶产物不同,具体分为以下几种,如表1所示。
表1漂粉精生产中析出的结晶(1)Ca(C1O)2,酸碱性质表现为中性,不含有结晶水的无定型结构,总体结晶度较低,颗粒粒度较小导致比表面积过大。
综合考虑宏观过滤性质发现该次氯酸盐过滤困难。
(2)Ca(C1O)2·2Hz0,酸碱性质表现为中性,含有两个结晶水的板状晶体结构,通常反应温度在20-30℃时会生成该物质。
反应开始时为较薄的具有四角的板状结构,随着反应时间的增加,该晶体会长大,形成50-200um大的“书页”状(糕点馅饼状)薄层重合着的晶体。
该物质的理论有效氯含量在99%左右,是组成漂粉精的重要成分。
(3)Ca(C1O)2 1/2Ca(OH)2,该物质被称为半碱式次氯酸钙,初始形成温度在50℃左右,形成片状结晶,直径在100-200um左右;随着反应温度的升高,晶体会继续生长,长径比变大,成为约500um的细长的竹叶形结晶体。
该物质结晶度较高,比表面积较小,所以过滤效果好,理论有效氯含量在79%左右,而且稳定性好,不易分解。
有效氯含量为60%的漂粉精以这种结晶为主要成分。
(4)Ca(C1O)22Ca(OH)2,酸碱性质表现为碱性,含有两个氢氧化钙的板状晶体结构。
较多情况下以100-200um的较大六角板形结晶析出,有时会以500-1000um的结晶析出。
该物质结晶度高,所以过滤分离容易,分离之后母液中的残余氯化钙经进一步氯化后可以得到高纯度的二碱式次氯酸钙,降低了原料的损失率。
次氯酸钙生产

次氯酸钙生产1次氯酸钙制备反应原理1.1次氯酸钙结晶种类在氯化反应器中装入浓石灰,然后通入氯气进行氯化反应,反应后生成次氯酸钙和氯化钙。
氯化钙在水中的溶解度较高而次氯酸钙的溶解度较低,所以氯化钙能够完全溶解在水中,次氯酸钙只能部分溶解,大部分以结晶形式析出。
这样就得到了次氯酸钙产品,将次氯酸钙结晶过滤分离后得到的固相进行干燥,制成了漂粉精。
其有效氯为60-70%,稳定性较好,非溶解性残渣较少。
基本反应式。
根据反应条件的不同,次氯酸钙结晶产物不同,具体分为以下几种,如表1所示。
表1漂粉精生产中析出的结晶(1)Ca(C1O)2,酸碱性质表现为中性,不含有结晶水的无定型结构,总体结晶度较低,颗粒粒度较小导致比表面积过大。
综合考虑宏观过滤性质发现该次氯酸盐过滤困难。
(2)Ca(C1O)2·2Hz0,酸碱性质表现为中性,含有两个结晶水的板状晶体结构,通常反应温度在20-30℃时会生成该物质。
反应开始时为较薄的具有四角的板状结构,随着反应时间的增加,该晶体会长大,形成50-200um大的“书页”状(糕点馅饼状)薄层重合着的晶体。
该物质的理论有效氯含量在99%左右,是组成漂粉精的重要成分。
(3)Ca(C1O)2 1/2Ca(OH)2,该物质被称为半碱式次氯酸钙,初始形成温度在50℃左右,形成片状结晶,直径在100-200um左右;随着反应温度的升高,晶体会继续生长,长径比变大,成为约500um的细长的竹叶形结晶体。
该物质结晶度较高,比表面积较小,所以过滤效果好,理论有效氯含量在79%左右,而且稳定性好,不易分解。
有效氯含量为60%的漂粉精以这种结晶为主要成分。
(4)Ca(C1O)22Ca(OH)2,酸碱性质表现为碱性,含有两个氢氧化钙的板状晶体结构。
较多情况下以100-200um的较大六角板形结晶析出,有时会以500-1000um的结晶析出。
该物质结晶度高,所以过滤分离容易,分离之后母液中的残余氯化钙经进一步氯化后可以得到高纯度的二碱式次氯酸钙,降低了原料的损失率。
优化次氯酸钙生产工艺

次氯酸钙生产工艺优化1 消石灰品质作为制备灰浆的原料,消石灰的品质即石灰石中Ca(OH)₂ 的含量对漂粉精有效氯含量有较大影响。
原料氢氧化钙的纯度是漂粉精的有效氯含量的重要影响原因,一般来讲,两者成正比关系。
氢氧化钙带入的杂质重要有Mg(OH)₂、SiO₂、 Al₂O₃ 和Fe₂O₃。
Mg(OH)z 也会与氯气反应生成Mg(C1O)₂, 但Mg(C1O)₂不稳定,在加热干燥的过程中极易分解,从而导致有效氯的损失;其他杂质首先阻碍Ca(C10)₂的晶体生长,另首先在漂粉精中占据一定的含量,这些都使漂粉精的有效氯含量下降。
因此在灰浆制备前,先测量消石灰中Ca(OH)₂的含量,从而计算需要放入混灰罐中消石灰的质量。
通过试验得到G=3.5008g 、V=50mL,V=12.75m1,M=0.025mol/L。
Ca(OH): 含量按下式计算:按照上述数据计算,Ca(OH): 的含量为98.5%。
符合试验规定。
1.2氯化反应在氯化反应过程中,石灰浆中会析出小六角棱形晶体,该晶体会持续成长。
伴随搅拌的进行。
大晶体会被破碎,开始出现针型晶体。
在针型晶体出现时加入母液,使反应中的氢氧化钙含量保持为300g/L。
最终会生成破板状大针形结晶,待所有的晶体均为大针形结晶时即为氯化反应终点,此时停止通入氯气。
依次套用母液进行试验,套用次数不得少于6次。
对6批制得的次氯酸钙产品进行有效氯和水分分析,成果如表1和表2所示。
由表1和表2中可以得到,在正常的生产条件下,使用钙法工艺分析纯原料,在试验室产品有效氯可到达63.5%,含水量可到达2.5%左右。
批量化生产中产中,产品有效氯可到达58.0%,含水量可到达2.4%左右。
由于批量生产过程中原料的品质下降,杂质较多,在反应过程中,杂质会引起较多的副反应的发生从而增进己生成的次氯酸钙产品的分解,导致产品的有效率含量比分析纯原料得到的产品的有效氯含量低。
并且在批量生产过程中,温度、压力等条件不易及时进行调控,这也是导致产品有效率含量减少的重要原因。
次氯酸钙生产工艺
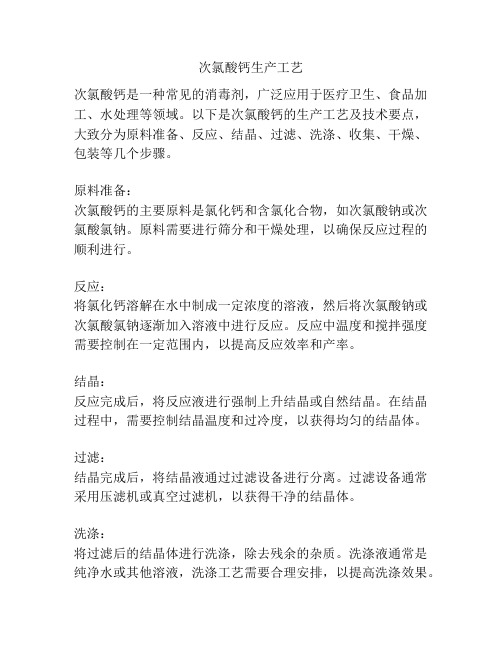
次氯酸钙生产工艺次氯酸钙是一种常见的消毒剂,广泛应用于医疗卫生、食品加工、水处理等领域。
以下是次氯酸钙的生产工艺及技术要点,大致分为原料准备、反应、结晶、过滤、洗涤、收集、干燥、包装等几个步骤。
原料准备:次氯酸钙的主要原料是氯化钙和含氯化合物,如次氯酸钠或次氯酸氯钠。
原料需要进行筛分和干燥处理,以确保反应过程的顺利进行。
反应:将氯化钙溶解在水中制成一定浓度的溶液,然后将次氯酸钠或次氯酸氯钠逐渐加入溶液中进行反应。
反应中温度和搅拌强度需要控制在一定范围内,以提高反应效率和产率。
结晶:反应完成后,将反应液进行强制上升结晶或自然结晶。
在结晶过程中,需要控制结晶温度和过冷度,以获得均匀的结晶体。
过滤:结晶完成后,将结晶液通过过滤设备进行分离。
过滤设备通常采用压滤机或真空过滤机,以获得干净的结晶体。
洗涤:将过滤后的结晶体进行洗涤,除去残余的杂质。
洗涤液通常是纯净水或其他溶液,洗涤工艺需要合理安排,以提高洗涤效果。
收集:洗涤完成后,将洗涤液进行收集,以便进一步处理或回收利用。
收集过程需要注意防止污染和杂质混入。
干燥:洗涤液收集完成后,将其放置在通风干燥的环境中,使其逐渐脱水和干燥。
同时需要控制干燥温度和时间,以保证产品质量。
包装:干燥完成后,将次氯酸钙产品进行包装。
通常采用塑料袋、纸箱或其他包装材料,以保护产品免受外界环境的影响。
以上是次氯酸钙的生产工艺和技术要点。
每个步骤都需要进行严格的控制和操作,以确保产品的质量和效果。
同时,安全生产和环保要求也是生产过程中需要重点考虑的因素。
- 1、下载文档前请自行甄别文档内容的完整性,平台不提供额外的编辑、内容补充、找答案等附加服务。
- 2、"仅部分预览"的文档,不可在线预览部分如存在完整性等问题,可反馈申请退款(可完整预览的文档不适用该条件!)。
- 3、如文档侵犯您的权益,请联系客服反馈,我们会尽快为您处理(人工客服工作时间:9:00-18:30)。
次氯酸钙生产工艺优化1消石灰品质作为制备灰浆的原料,消石灰的品质即石灰石中Ca(OH)2的含量对漂粉精有效氯含量有较大影响。
原料氢氧化钙的纯度是漂粉精的有效氯含量的重要影响因素,一般来讲,二者成正比关系。
氢氧化钙带入的杂质主要有也会与氯气反应生成Mg(C1O)2,但Mg(C1O)2不稳定,在加热干燥的过程中极易分解,从而造成有效氯的损失;其他杂质一方面阻碍Ca(C10)2的晶体生长,另一方面在漂粉精中占据一定的含量,这些都使漂粉精的有效氯含量下降。
所以在灰浆制备前,先测量消石灰中Ca(OH)2的含量,从而计算需要放入混灰罐中消石灰的质量。
通过实验得到G=3.5008g、V总=50mL,V=12.75m1,M=0.025mo1/L。
Ca(OH):含量按下式计算:按照上述数据计算,Ca(OH):的含量为98.5%。
符合实验要求。
1.2氯化反应在氯化反应过程中,石灰浆中会析出小六角棱形晶体,该晶体会持续成长。
随着搅拌的进行。
大晶体会被破碎,开始出现针型晶体。
在针型晶体出现时加入母液,使反应中的氢氧化钙含量保持为300g/L。
最终会生成破板状大针形结晶,待所有的晶体均为大针形结晶时即为氯化反应终点,此时停止通入氯气。
依次套用母液进行实验,套用次数不得少于6次。
对6批制得的次氯酸钙产品进行有效氯和水分分析,结果如表1和表2所示。
由表1和表2中可以得到,在正常的生产条件下,使用钙法工艺分析纯原料,在实验室产品有效氯可达到63.5%,含水量可达到2.5%左右。
批量化生产中产中,产品有效氯可达到58.0%,含水量可达到2.4%左右。
因为批量生产过程中原料的品质下降,杂质较多,在反应过程中,杂质会引起较多的副反应的发生从而促进己生成的次氯酸钙产品的分解,造成产品的有效率含量比分析纯原料得到的产品的有效氯含量低。
而且在批量生产过程中,温度、压力等条件不易及时进行调控,这也是造成产品有效率含量降低的主要原因。
表1钙法工艺生产产品的有效氯含量表2钙法工艺生产产品的水分含量2实验室钠法生产工艺实验结果与分析2.1纯品原料实验结果2.1.1氯化温度的确定氯化反应温度是影响漂粉精产品的有效氯含量的重要因素,氯化反应温度存在最优值,即该温度下,产品的有效氯含量最高。
而氯化温度过高或过低时,产品的有效氯含量均会明显降低。
原因是当氯化反应温度较低时,产品容易生成,一种六棱柱形三重盐,导致漂粉精的有效氯含量降低;当氯化温度较高时,容易导致漂粉精主要成分次氯酸钙分解,进而导致漂粉精的有效氯含量降低。
实验先初步确定液体烧碱的浓度为30%,然后对氯化温度进行分析,得到最优的氯化温度。
在选取的四组氯化反应温度下,漂粉精有效氯含量和水分含量的分析结果见图1所示。
图1氯化反应温度对分析纯级原料制备的漂粉精有效氯含量和水分含量的影响。
分析上述实验结果可以看出,漂粉精的有效氯含量随着氯化温度的增加而增加,水分含量随着温度的增加而降低。
当氯化温度达到40℃时,平均有效氯含量为69.9%,水分含量为5.1%。
根据以上实验结果,得到最佳反应温度为40℃。
不同的生产温度得到的产品的晶型不同,通常反应温度在20-30℃时会生成Ca(C10)2 2H2O,反应开始时为较薄的具有四角的板状结构,随着反应时间的增加,该晶体会长大,形成50-200um大的“书页”状(糕点馅饼状)薄层重合着的晶体。
该物质的理论有效氯含量在99%左右,所以40℃时生成的Ca(C1O)2 2H2O含量最高,产品的有效率含量也最高。
2.1.2烧碱浓度的确定烧碱浓度是影响漂粉精产品的有效氯含量的另一个重要因素,在选定的反应温度即40℃的情况下,进行不同浓度烧碱的实验,以确定最佳浓度烧碱浓度存在最佳值,即烧碱在该浓度下,产品的有效氯含量最高。
当烧碱浓度较低或者较高时,所得产品的有效氯含量都不够高。
当烧碱浓度较低时,造成次氯酸钙的过饱和度较小,易出现非均相成核,即在次氯酸钙的晶体中,有可能包有氢氧化钙的粒子,导致漂粉精的有效氯含量降低。
当烧碱浓度较高时,一方面由于悬浮液过于粘稠,导致氯化反应不够均匀,局部参加氯化反应,即与通氯管口距离近的悬浮液参与反应,而与通氯管口距离远的悬浮液却没有参与反应;另一方面由于悬浮液浓度较大,析出的副产物氯化钠也会比较多,上述原因都会使漂粉精的有效氯含量下降。
故确定烧碱的浓度尤为重要。
图2显示的是烧碱浓度对于分析纯级原料制备的漂粉精有效氯含量和水分含量的影响。
对比实验结果可得到,最佳反应温度为40℃,NaOH的浓度为30%,此条件下得到的产品有效氯含量及含水量最佳,有效氯含量可达到69.9%,水分含量在5%左右。
图4-2烧碱浓度对分析纯级原料制备的漂粉精有效氯含量和水分含量的影响2.2工业级原料实验结果2.2.1氯化温度的确定按照实验室级原料的研究步骤对工业级原料进行实验分析,在选取的四组氯化温度下,漂粉精有效氯含量和水分含量的分析结果见图3所示。
图4-3氯化温度对工业级原料漂粉精有效氯含量和水分含量的影响分析上述实验结果可以看出,漂粉精的有效氯含量随着氯化温度的增加而增加,水分含量随着温度的增加而降低。
当氯化温度达到40℃时,平均有效氯含量为65.9%,水分含量为7.05%。
根据以上实验结果,得到最佳反应温度为40℃。
总体来看,工业级生产产品品质略低于实验室级原料生产的产品品质,因为工业级原料纯度低于实验室级原料,易于引进杂质。
2.2.2烧碱浓度的确定在得到最优的氯化温度40℃下,对选取的四组烧碱浓度进行分析,漂粉精有效氯含量和水分含量的分析结果见图4。
通过使用工业级原料进行实验,得到最佳反应温度为40℃,NaOH的浓度为30%,此条件下得到的产品有效氯含量及含水量最优,与纯品级原料得到结果一致。
产品有效氯含量可达到65%以上,水分含量可达到7%左右。
得到的次氯酸钙产品的外观形貌如图5所示。
从图可以看出,次氯酸钙产品为白色粉末,粒度较为均一。
测量后得到次氯酸钙微粒粒径在0.5-1.4mm之间,占据了总量的85-90%,有少部分大颗粒。
图4烧碱浓度对工业级原料漂粉精有效氯含量和水分含量的影响图5工业生产次氯酸钙外观形貌3放大试验结果分析按照批产量2.5kg漂粉精计算,进行放大试验。
试验结果见表34母液回收利用实验结果初次氯化反应在无回收母液的情况下,取30%氢氧化钠溶液和氢氧化钙配成混合液,采取一步氯化工艺。
氯化后产生成品,经过测量约含有10%的次氯酸钙,即需要的成品,考虑成本及环保要求,需进行回收实验。
表4-3工业放大试验产品性能分析4.1实验室母液回收实验结果对于实验室级实验,母液与30%氢氧化钠溶液混合,按照凯密迪工艺流程进行回收实验。
实验至少要进行6次循环,结果见表4 表4分析纯级实验产品性能分析通过分析可以看出,6次循环实验得到的成品次氯酸钙的质量较稳定,平均得到约100g成品次氯酸钙。
次氯酸钙的有效氯含量在65%左右,低于使用消石灰原料制备的次氯酸钙产品的有效氯含量。
这是因为回收母液中的Ca(OH)2含量较低,且含有大量杂质,所以得到的产品的品质降低,但是总体来看对于回收母液而言Ca(OH)2仍有效且具有重要作用。
4.2放大试验母液回收结果对于工业级扩大化试验,原料为1.8t的30%氢氧化钠溶液,1.4t 氢氧化钙和液氯。
采用一步氯化得到产品,干燥后得到产品0.97t,母液2.5t。
将得到的母液混合2.5t的30%氢氧化钠溶液,进行氯化反应等工序,最终得到干燥成品0.95t,母液约2.5t,继续回收。
重复第2步继续进行母液回收实验,得到干燥产品约0.95t。
共计重复5次回收母液实验,得到的产品质量数据如表5所示。
进行干燥包装。
产生的母液中,实验序号产品质量(t)表5工业级实验产品性能分析产品有效氯含量显著提高,杂质含量显著降低,形成颗粒状结晶成品,三废排放大大减少,同时采用母液回收工艺,将母液中的次氯酸钙成品回收,用以进行下次氯化反应,经粗略估算生产成本可降低约5%。
5工业化试生产通过上述的一系列试验,初步得出在漂粉精制备工艺中,钠法漂粉精生产工艺克服钙法工艺所存在的一定劣势。
依托天津市某次氯酸钙生产企业,进行工艺改造。
其原有工艺为钙法工艺,现新建钠法生产工艺,进行工艺调试和中试生产。
5.1主要建设内容天津市西青区某次氯酸钙生产企业新建2万吨/年漂粉精(钠法次氯酸钙)技术改造项目。
在厂区的西侧新建一套生产装置,项目占地面积10400m2,由油炉房、液氯库(包括汽化器站房)、氯化车间(包括压缩机房)、离心干燥车间、石灰库、成品库、冷冻站、变配电室等组成。
新建钠法漂粉精生产工艺西青区某次氯酸钙生产企业主要建设内容见表6表6主要建设内容5.2产品和原料产品是次氯酸钙((2万吨/年),及副产品次氯酸钠(作为产品销售)。
原料见表7。
表7工业放大试验生产原料表5.3主要设备主要设备见表8表8主要设备5.4改进后的生产工艺流程图6是改造后的工艺流程图。
①配浆:首先在配浆池内加入定量的水,开启搅拌。
将购进的氢氧化钙(含量>95%)用天车移至绞龙上方,开启绞龙,通过绞龙将氢氧化钙粉末送至配浆池,充分搅拌20分钟,化验浓度达到36%-38%即为合格,供氯化工序使用。
粉碎筛分图6 改后工艺流程图②氯化:关键控制点有以下几点:a.将回收的母液投入反应釜,然后开启搅拌将购进的液碱通过离心泵流量计打入反应釜,通入定量氯气观察终点,经检测合格后进入配料工序。
b.将回收的母液投入反应釜,然后开启搅拌将配置好的石灰乳通过离心泵打入计量称,当数量达到时停止离心泵,把计重好的石灰乳投入到反应釜内。
开启热水阀门给物料升温。
当温度上升到40℃时,停止供热阀门,保温30min。
保温完毕后通知氯气房按规定供氯速度进行通氯,当通氯量达到要时通知氯化操作工关闭阀门。
通氯过程中温度63℃.完毕后供配料供需使用。
c.将a,b两步配置好的反应液通过离心泵打入反应釜,启动盐水泵进行降温,同时启动搅拌,充分搅拌5-10分钟。
当温度降至20℃时,开始通知氯气岗位通氯气,当用显微镜观察时,发现反应液中,一个视时野中仅有3-4个圆晶片时,将通氯速度降至10-5kg/min,同时将pH 计插入反应釜中,进行pH在线检测,当pH值降至11时,停止通氯。
即为终点。
在通氯反应过程中,随时调节盐水阀门的开启度,来控制反应温度。
在反应过程中严禁超温,且有晶形转换前不要温度太低。
在通氯过程中,除停电或其它不可抗力等因素外,严禁中断氯气(中间不能换瓶等),否则会影响晶体的形成。
导致反应液发粘等现象的发生。
到终点后,通知化验室取样检测,当检测合格后,方可放料,打入反应液储料池。
③配料:先将第一步氯化反应的次钠溶液经过离心机分离出化第二步经过离心机分离出的湿饼进入配料池与第一步的次氯酸钠液体进行混合。