双加压法生产硝酸工艺流程(精)
双加压法硝酸生产装置的主要工序
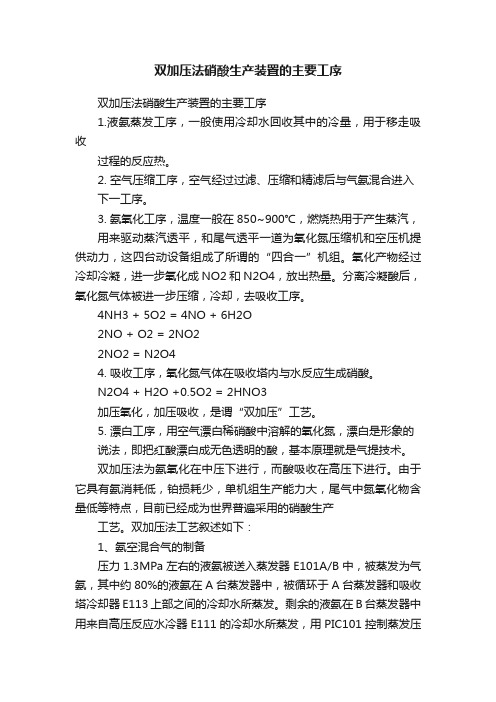
双加压法硝酸生产装置的主要工序双加压法硝酸生产装置的主要工序1.液氨蒸发工序,一般使用冷却水回收其中的冷量,用于移走吸收过程的反应热。
2. 空气压缩工序,空气经过过滤、压缩和精滤后与气氨混合进入下一工序。
3. 氨氧化工序,温度一般在850~900℃,燃烧热用于产生蒸汽,用来驱动蒸汽透平,和尾气透平一道为氧化氮压缩机和空压机提供动力,这四台动设备组成了所谓的“四合一”机组。
氧化产物经过冷却冷凝,进一步氧化成NO2和N2O4,放出热量。
分离冷凝酸后,氧化氮气体被进一步压缩,冷却,去吸收工序。
4NH3 + 5O2 = 4NO + 6H2O2NO + O2 = 2NO22NO2 = N2O44. 吸收工序,氧化氮气体在吸收塔内与水反应生成硝酸。
N2O4 + H2O +0.5O2 = 2HNO3加压氧化,加压吸收,是谓“双加压”工艺。
5. 漂白工序,用空气漂白稀硝酸中溶解的氧化氮,漂白是形象的说法,即把红酸漂白成无色透明的酸,基本原理就是气提技术。
双加压法为氨氧化在中压下进行,而酸吸收在高压下进行。
由于它具有氨消耗低,铂损耗少,单机组生产能力大,尾气中氮氧化物含量低等特点,目前已经成为世界普遍采用的硝酸生产工艺。
双加压法工艺叙述如下:1、氨空混合气的制备压力1.3MPa左右的液氨被送入蒸发器E101A/B中,被蒸发为气氨,其中约80%的液氨在A台蒸发器中,被循环于A台蒸发器和吸收塔冷却器E113上部之间的冷却水所蒸发。
剩余的液氨在B台蒸发器中用来自高压反应水冷器E111的冷却水所蒸发,用PIC101控制蒸发压力在0.5MPa。
约0.9m3/h的液体连续地用控制阀HC101控制,从E101A引至E101B,并通过就地调节将积存在E101B的水份排至辅助蒸发器E102中,用低压蒸汽蒸发,回收气氨。
残留物则间断排至排油罐R109中,E101A/B出口气氨经预过滤器R114过滤后,送入氨过热器E103中,用低压蒸汽加热,气氨温度由TRCA101控制。
双加压法硝酸生产工艺技术分析与探讨
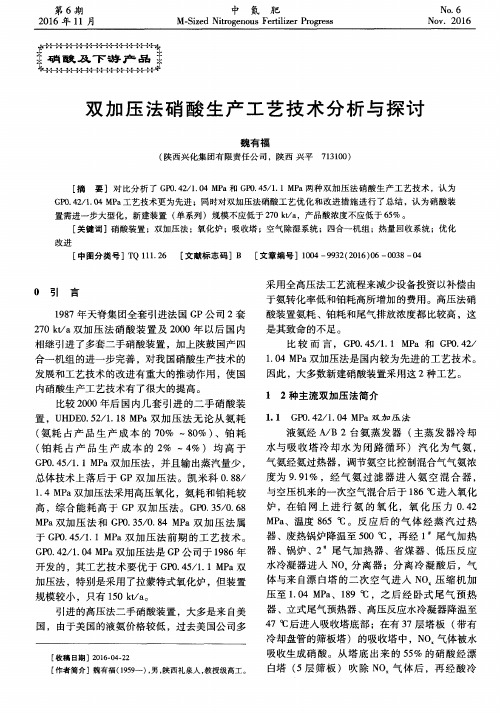
[ 中图分类号 ]T Q 1 1 1 . 2 6 [ 文献标 志码 ]B [ 文章编号 ]1 0 0 4—9 9 3 2 ( 2 0 1 6 ) 0 6— 0 0 3 8— 0 4
0 引 言
采用 全高 压法 工艺 流程来 减少 设 备投 资 以补 偿 由 于氨 转化 率低 和铂 耗高 所增加 的费用 。高压 法硝
1 9 8 7年天 脊集 团全 套引 进法 国 G P公 司 2套 2 7 0 k t / a双加 压 法 硝 酸装 置及 2 0 0 0年 以后 国 内 相 继 引进 了多套 二 手硝 酸装 置 ,加上 陕鼓 国产 四 合 一 机组 的进 一步完 善 ,对 我 国硝酸生 产技 术 的
酸装置氨耗、铂耗和尾气排放浓度都 比较高,这 是其 致命 的不 足 。 比 较 而 言 ,G P O . 4 5 / 1 . 1 M P a和 G P 0 . 4 2 /
魏 有福
( 陕西兴化集 团有 限责任公 司 ,陕西 兴平 7 1 3 1 0 0 )
[ 摘
要 】对 比分析 了 G P 0 . 4 2 / 1 . 0 4 MP a和 G P 0 . 4 5 / 1 . 1 MP a两种 双加压 法硝酸 生产工艺 技术 ,认 为
G P 0 . 4 2 / 1 . 4 0 M P a工艺技术更为先进 ;同时对双加压法硝酸工艺 优化 和改进措 施进行 了总结 ,认 为硝酸 装 置需进一 步大型化 ,新建装 置 ( 单 系列)规模不应低 于 2 7 0 k t / a ,产 品酸浓度 不应低 于 6 5 %。 [ 关键词]硝酸装置 ;双加压法 ;氧化炉 ;吸收塔 ;空气 除湿 系统 ;四合 一机组 ;热量 回收系统 ;优 化
器 、立式尾气预热器 、高压反应水冷凝器 降温至
双加压法硝酸生产工艺流程

双加压法硝酸生产工艺流程1.该工艺流程首先需要将硝酸铵溶解在水中。
The process begins by dissolving ammonium nitrate in water.2.溶液随后被加入到浓硫酸中。
The solution is then added to concentrated sulfuric acid.3.这一步会产生硝酸铵和硫酸的反应。
This step results in a reaction between ammonium nitrate and sulfuric acid.4.产生的硝酸铵溶液经过加热。
The resulting ammoniumnitrate solution is heated.5.随后,溶液经过脱水,使得硝酸浓度增加。
The solution is then dehydrated to increase the concentration of nitric acid.6.然后,再次加入浓硫酸进行反应。
Next, concentrated sulfuric acid is added for another reaction.7.反应产生的硝酸再次被加热。
The resulting nitric acid is heated once again.8.经过脱水处理后,硝酸的浓度进一步提高。
After dehydration, the concentration of nitric acid is further increased.9.这种双加压法的生产工艺流程可以生产高纯度的硝酸。
Thisdual-pressure production process can produce high-puritynitric acid.10.工艺流程需要精确的控制温度和压力。
The process requires precise control of temperature and pressure.11.硫酸和硝酸的反应是放热反应。
双加压法硝酸

一. 主要原料及规格 氮气 99.2%
二. 工艺原理 氨氧化法制稀硝酸分以下两步: 1.氨的氧化 4NH3 + 5O2 = 4NO +6H2O 2.氮氧化合物的氧化及吸收 2NO + O2 = NO2 + 热量 3NO2 + H2O = 2HNO3 + NO +热量
三. 工艺流程 .氨的氧化及热能的回收 来自界区的液氨经蒸发器及过热器后成气态氨气,再经过滤器除去氨气中的杂质,然后与压缩 后的空气按一定比例(氨气占9.5%体积比)经氨-空混合器后进入氨氧化器.在氨氧化器中经与铂铑 网充分接触,96%至97%的氨气被氧化成NO,氨的氧化使气体温度上升至860oC,此气体经氨氧化器下部 的蒸气过热器和废热锅炉回收热量后温度降至400oC。 .NO的氧化及吸收 NO气体离开废热锅炉后,经高温气―气换热器,以及省煤气后,气体的温度冷却至156oC, 在温度降低的过程中,混合气体中的NO被氧化成NO22进入低压反应水冷却器被进一步冷却至40oC, 在该处NO2气体与冷凝水反就生成34%的稀硝酸。酸-气混合物经氧化氮分离器分离出稀硝酸送入吸 收塔塔板。同时由低压把就水冷却器来自氧化氮气体与来自漂白塔的十次空气混合,经氧化氮分离 器后送入NOX压缩机压缩至10,0~13.0bar。被压缩后的气体经尾气预热器被冷却至126oC,再经低压水冷 却器冷却至40oC,冷却后的氧化氮气体与冷凝酸一并送入吸收塔底部的氧化器继续氧化,在塔板上NO4 气体被水及收生成硝酸。当塔内的液体逐板流下时,和NO2气体充分接触,硝酸的浓度不断提高, 当硝酸到达塔底时,其浓度约为65%~67%。 自吸收塔来的65%~67%的硝酸是至漂白塔的顶部塔板,用二次空气提出溶解气体,完成漂白过程, 而由吸收塔顶部排陋的尾气经尾气分离器,以及究气过热器后,再经过尾气预热器、高温气-气换热 器后,温度升至360oC,加热后的气体进入尾气透平回收60%左右的总压缩功。
27万吨年双加压硝酸装置操作规程(最终)

27万吨年双加压硝酸装置操作规程(最终) 270kt/a双加压硝酸装臵岗位操作法Q/NH00:C.22—11分发号:270kt/a双加压硝酸装臵岗位操作法,试行,- 1 -270kt/a双加压硝酸装臵岗位操作法目录第一章中控岗位操作法一、装臵简介、岗位任务及管辖范围二、生产原理及工艺规程三、工艺正常生产指标及联锁指标一览表四、开车六、停车七、正常操作八、日常维护九、事故原因及处理十、主要设备一览表十一、主要参数一览表第二章巡检岗位操作法一、岗位任务及管辖范围二、工艺流程及原理三、工艺参数一览表四、开车五、正常生产操作六、停车七、事故分析及处理九、附录泵的操作法第三章第四章三废处理第五章各设备简图稀硝酸工艺流程说明:因“四合一”机组等设备资料未到齐,少量数据未最终确认。
- 2 -270kt/a双加压硝酸装臵岗位操作法第一章中控岗位操作法一、装置简介1、装臵简介本装臵为双加压法生产稀硝酸的装臵~由空气中的氧和氨反应生成氧化氮~然后在吸收塔内由水吸收生成60%的稀硝酸~供浓硝及硝铵等下游装臵使用~稀硝酸生产能力为折百270kt/a。
2、岗位任务和管辖范围:对整个装臵界区内的安全和生产负责。
“四合一”机组室内操作。
凡中控室表盘上的仪表及室内的全部设施均由中控操作工使用、维护和保管。
在工长的领导下~负责指挥巡检岗位进行操作。
1,把空气经空压机加压后~分两路送出~一路送至氧化炉~用于氧化~另一路送至漂白塔~用于酸的漂白~还有一少部分用于密封系统。
2,将氨氧化后生产的NOx气体经氧化氮压缩机加压后~送至吸收塔供吸收用。
3,利用氨氧化反应热在废热锅炉中产生出一定压力的过热蒸汽~驱动蒸汽透平作功~为压缩机提供驱动动力。
4,被加热的高温尾气送至尾气透平回收能量~为尾气透平提供驱动动力。
二、生产原理及工艺流程1、生产原理:本装臵生产硝酸是采用氨接触氧化法进行的~生产硝酸的过程可用下列三个化学反应方程式表示:,1,氨和空气中的氧气~在铂催化剂的作用下生成NO~此反应实在氧化炉中进行的~化学反应方程式为:4NH + 5O = 4NO + 6HO +Q 322,2,NO继续氧化成NO~此反应是在一系列换热设备、吸收塔及管道中进行2 的~化学反应方程式为:2NO + O = 2NO +Q 22,3,用脱盐水,工艺水,吸收NO生成硝酸~此反应是在吸收塔内进行的~化2 - 3 -270kt/a双加压硝酸装臵岗位操作法学反应方程式为:3NO + HO = 2HNO + NO +Q 223通过上述三步反应~可制得58~60%的硝酸。
年产30万吨双压法稀硝酸工艺设计.doc

年产30万吨稀硝酸工艺设计一、稀硝酸生产的主要原理解氨接触氧化法制硝酸的总反应式为:NH3+2O2===HNO3+H2O,反应可分三步进行:氨的接触氧化过程:在催化剂的作用下,将氨氧化为一氧化氮,其反应式为:4NH3+5O2====4NO+6H2O (1)一氧化氮氧化过程:将前一过程中生成的NO进一步氧化成NO2,其反应式为:2NO+O2====2NO2 (2)氮氧化物的吸收过程:用水吸收二氧化氮,从而得到产品硝酸,其反应式为:3NO2+H2O====2HNO3+NO (3)用此工艺可生产浓度为45%~60%的稀硝酸。
60年代后,硝酸生产的技术特点是,采用大型化组,适当的提高操作压力。
采用高效设备,降低原料及能量消耗,决尾气中氮氧化物的污染问题。
二、工艺条件的确定催化剂:铂系催化剂氨氧化工艺条件1.温度在不同温度下,氨氧化后的反应生成物也不同。
低温时,主要生成的是氮气。
650℃时,氧化反应速率加快,氨氧化率达90%;700~1000℃时,氨氧化率为95%~98%。
温度高于1000℃时,由于一氧化氮分解,氨氧化率反而下降。
在650~1000℃范围内,温度升高,反应速率加快,氨氧化率也提高。
但是温度太高,铂损失增大,同时对氧化炉材料要求也更高。
因此一般常压下,氧化温度取750~850℃,加压氧化取870~900℃为宜。
2.压力氨氧化反应实际上可视为不可逆反应,压力对于NO产率影响不大,但加压反有助于反应速度的提高。
在工业生产条件下,加压时氧化率比常压时氧化率低1%~2%。
尽管加压可导致氨氧化率降低,但由于反应速度的提高可使催化剂的生产强度增大。
尤其是压力提高可大大节省NO氧化和NO2吸收所用的昂贵不锈钢设备。
生产中究竟采用常压还是加压操作,应视具体条件而定。
一般加压氧化采用0.3~0.5MPa压力,国外有采用1.0MPa。
由于本设计选用全中压法,操作压力选为0.45MPa。
3.接触时间混合气体在铂网区的停留时间称为接触时间。
硝酸生产工艺

摘要:简要介绍了国内外硝酸工业的技术及发展趋势,同时对双加压法的特点进行阐述,并提出了其发展前景及需关注的问题。
关键词:硝酸生产双加压法问题发展趋势前言硝酸工业的发展已有一百多年的历史,自从硝酸实现工业化生产以来,人们就把装置产量的提高,经济技术指标的优化和运行安全可靠作为追求的目标。
伴随着金属材料技术、设备机械制造技术、催化剂技术和控制技术的发展,硝酸生产的大型化、经济技术指标的先进化、控制手段的自动化成为可能。
1 硝酸生产方法简介稀硝酸的生产过程根据氧化压力和吸收压力设置的不同,主要有常压法(N)、综合法(N+M)、中压法(M+M)、高压法(H+H)和双加压法(M+H)五种方法。
表1给出了各种生产方法的特征。
表1 各种生产方法的特征从表1可以看出:氨和铂的消耗综合法为最低,中压法和双加压法次之,高压法最高;相对投资费用高压法最低,双加压法次之;在生产规模上双加压法、高压法最宜实现大型化。
尾气排放双加压法最优。
1.1常压法、综合法[1]我国已将此两种生产方法列入落后和淘汰行列,除个别老厂在运行外,新建装置已不许选用上述两种方法。
1.2全中压法[2]氨的氧化和氮氧化物的吸收均在0.35~0.6MPa压力下进行,此法的特点是:设备较为紧凑,生产强度较高,不需要NO x压缩机,流程比综合法简单,投资较少,酸浓度为53%,能量可以部分回收。
缺点是生产强度低,吸收容积较大,尾气中NO x含量较高为2 000×10-6,需处理才能达标排放,并且系统设备腐蚀严重。
1.3高压法氨氧化和氮氧化物吸收均在0.71~1.2MPa的压力下进行。
此法的特点是全过程压力均由空气压缩机供给,不需NO x压缩机,流程简单,设备布置紧凑,基建投资少,特种钢材用量少,生产强度大,吸收率高达99%,产品浓度高(55%~70%),尾气中氮氧化物含量低,能实现清洁生产,能量回收率高。
缺点是氨氧化率低,氨耗高,铂催化剂装填量大,使用周期短,损耗亦大,生产成本较高。
硝酸工艺流程简介

中压蒸
92
11 Βιβλιοθήκη 34582液氨 6
1
1 2
1
1 1
2 尾气
空气
7
2
1
1
1
至漂白
1
1、2—液氨蒸发器, 3—辅助蒸发器, 4—氨过热器, 5—氨过滤器, 6—空气
过滤室, 7—空压机, 8—混合器, 9—氧化炉、过热器、废热锅炉, 10—高温
氨和空气在氨─空混合器中混合以后,进入氧化炉,经过铂网催化剂氧 化生成 NO等混合气体,铂网氧化温度为 860 ℃,然后经过蒸汽过热器、废热 锅炉,再经高温气─气换热器、省煤器、低压反应水冷器,再进入氧化氮分 离器,在此将稀酸分离下来,气体则与漂白塔来的二次空气混合后进入氧化 氮压缩机,进气温度为 60 ℃,压力为 Mpa;出口温度为 200 ℃,压力为 Mpa。 再经尾气预热器、高压反应水冷却器进入吸收塔,进入吸收塔时的氮氧化物 气体温度为 40℃,氮氧化物气体从吸收塔底部进入,工艺水从吸收塔顶部喷 淋而下,二者逆流接触,生成 58 %—60 %的硝酸,塔底酸温度为 40 ℃,从 吸收塔出来的硝酸进入漂白塔,用来自二次空气冷却器的约 120 ℃的二次空 气在漂白塔中逆流接触,以提出溶解在稀酸中的低价氮氧化物气体,完成漂 白过程,漂白后的成品酸经酸冷却器冷却到 40 ℃,进入成品酸贮罐,再用成 品酸泵送往硝铵和间硝装置。
后进入碱吸收塔,经碱吸收后排入大气,排放的尾气中 400ppm。
NOX 的含量最低约
3.常压法稀硝酸生产工艺流程: 空气通过过滤器除去机械杂质和粉尘后经过鼓风机,进入混合器与过滤
后的氨气混合,然后进入氧化炉,反应生成高温的氧化氮工艺气体,工艺气 体经过锅炉、冷却器降温至 40℃,进入吸收塔底部,在常压下经过多个酸吸 收塔吸收,从吸收塔顶部出来的尾气进入多个碱吸收塔,经碱吸收后排入大 气,排放的尾气中 NOX 的含量最低约 2000ppm。