橡胶硫化工艺方法
橡胶硫化工艺流程

橡胶硫化工艺流程橡胶硫化是指将橡胶中的双键或多键化合物与硫或其它硫化剂反应生成交联结构的化学反应过程。
硫化是橡胶制品加工中必不可少的一道工艺,它可以提高橡胶制品的耐磨性、耐老化性和强度,使橡胶制品具有更好的物理性能。
橡胶硫化工艺流程是指橡胶硫化过程中所涉及到的各个环节和步骤,下面将详细介绍橡胶硫化工艺流程。
首先,橡胶硫化的原料准备。
在橡胶硫化工艺流程中,首先需要准备好橡胶和硫化剂。
橡胶可以是天然橡胶、合成橡胶或再生橡胶,而硫化剂主要是硫磺。
在一般情况下,还需要添加一些促进剂、活化剂和防老化剂等辅助原料,以提高硫化效果和橡胶制品的性能。
其次,橡胶混炼。
橡胶混炼是指将橡胶和各种硫化剂、促进剂等原料混合均匀的过程。
混炼的目的是使各种原料充分分散,以便硫化剂能够均匀地和橡胶发生化学反应。
混炼过程中需要控制好温度、时间和机械作用,以确保橡胶和各种原料充分混合。
然后,硫化成型。
混炼后的橡胶料需要进行硫化成型,即将橡胶料放入硫化模具中,加热使其发生硫化反应,并得到所需形状的橡胶制品。
硫化成型的温度、时间和压力等参数需要根据具体橡胶制品的要求来进行控制,以确保橡胶制品的质量。
最后,橡胶制品的后处理。
硫化成型后的橡胶制品需要进行后处理,包括去除模具、修整边角、清洗等工序。
有些橡胶制品还需要进行硫化后的热处理或冷却处理,以进一步提高其性能。
总之,橡胶硫化工艺流程是一个复杂的过程,需要严格控制各个环节和步骤,以确保橡胶制品的质量和性能。
只有在整个硫化工艺流程中严格执行标准操作规程,才能生产出优质的橡胶制品,满足不同行业的需求。
橡胶硫化工艺流程
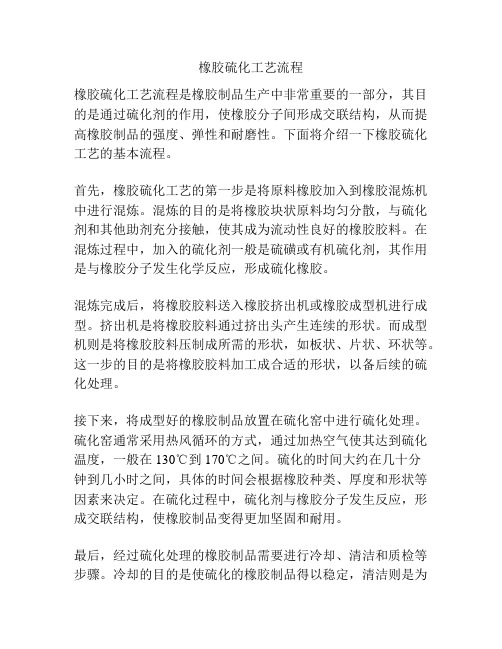
橡胶硫化工艺流程橡胶硫化工艺流程是橡胶制品生产中非常重要的一部分,其目的是通过硫化剂的作用,使橡胶分子间形成交联结构,从而提高橡胶制品的强度、弹性和耐磨性。
下面将介绍一下橡胶硫化工艺的基本流程。
首先,橡胶硫化工艺的第一步是将原料橡胶加入到橡胶混炼机中进行混炼。
混炼的目的是将橡胶块状原料均匀分散,与硫化剂和其他助剂充分接触,使其成为流动性良好的橡胶胶料。
在混炼过程中,加入的硫化剂一般是硫磺或有机硫化剂,其作用是与橡胶分子发生化学反应,形成硫化橡胶。
混炼完成后,将橡胶胶料送入橡胶挤出机或橡胶成型机进行成型。
挤出机是将橡胶胶料通过挤出头产生连续的形状。
而成型机则是将橡胶胶料压制成所需的形状,如板状、片状、环状等。
这一步的目的是将橡胶胶料加工成合适的形状,以备后续的硫化处理。
接下来,将成型好的橡胶制品放置在硫化窑中进行硫化处理。
硫化窑通常采用热风循环的方式,通过加热空气使其达到硫化温度,一般在130℃到170℃之间。
硫化的时间大约在几十分钟到几小时之间,具体的时间会根据橡胶种类、厚度和形状等因素来决定。
在硫化过程中,硫化剂与橡胶分子发生反应,形成交联结构,使橡胶制品变得更加坚固和耐用。
最后,经过硫化处理的橡胶制品需要进行冷却、清洁和质检等步骤。
冷却的目的是使硫化的橡胶制品得以稳定,清洁则是为了去除表面的杂质和污染物,保证产品的质量。
质检是为了确保橡胶制品的尺寸、力学性能和外观等符合标准要求。
总之,橡胶硫化工艺流程是一个复杂而关键的过程,其中包括混炼、成型、硫化、冷却、清洁和质检等环节。
通过这些步骤的协同作用,可以使橡胶制品达到所需的机械性能和物理性能。
橡胶硫化工艺流程
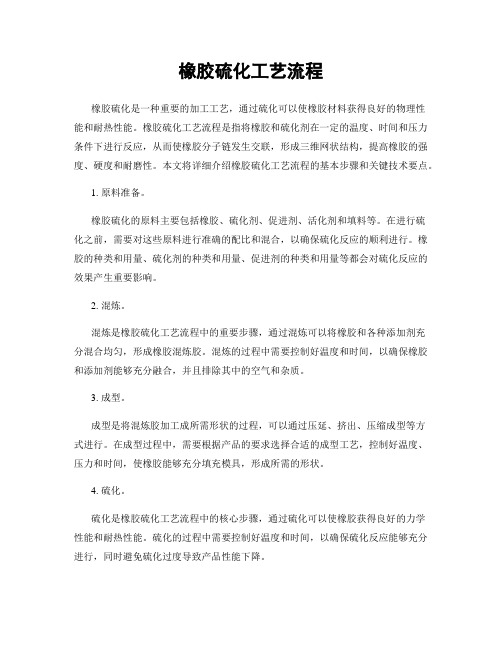
橡胶硫化工艺流程橡胶硫化是一种重要的加工工艺,通过硫化可以使橡胶材料获得良好的物理性能和耐热性能。
橡胶硫化工艺流程是指将橡胶和硫化剂在一定的温度、时间和压力条件下进行反应,从而使橡胶分子链发生交联,形成三维网状结构,提高橡胶的强度、硬度和耐磨性。
本文将详细介绍橡胶硫化工艺流程的基本步骤和关键技术要点。
1. 原料准备。
橡胶硫化的原料主要包括橡胶、硫化剂、促进剂、活化剂和填料等。
在进行硫化之前,需要对这些原料进行准确的配比和混合,以确保硫化反应的顺利进行。
橡胶的种类和用量、硫化剂的种类和用量、促进剂的种类和用量等都会对硫化反应的效果产生重要影响。
2. 混炼。
混炼是橡胶硫化工艺流程中的重要步骤,通过混炼可以将橡胶和各种添加剂充分混合均匀,形成橡胶混炼胶。
混炼的过程中需要控制好温度和时间,以确保橡胶和添加剂能够充分融合,并且排除其中的空气和杂质。
3. 成型。
成型是将混炼胶加工成所需形状的过程,可以通过压延、挤出、压缩成型等方式进行。
在成型过程中,需要根据产品的要求选择合适的成型工艺,控制好温度、压力和时间,使橡胶能够充分填充模具,形成所需的形状。
4. 硫化。
硫化是橡胶硫化工艺流程中的核心步骤,通过硫化可以使橡胶获得良好的力学性能和耐热性能。
硫化的过程中需要控制好温度和时间,以确保硫化反应能够充分进行,同时避免硫化过度导致产品性能下降。
5. 后处理。
硫化完成后,还需要进行后处理工艺,如冷却、清洗、修整等,以确保产品的质量和外观。
同时还需要进行产品的检验和包装,最终将产品送往市场。
总之,橡胶硫化工艺流程是一个复杂而精细的加工过程,需要严格控制各个环节,以确保产品的质量和性能。
只有在每个步骤中严格执行工艺要求,才能生产出符合要求的橡胶制品。
希望本文对橡胶硫化工艺流程有所帮助,谢谢阅读。
橡胶硫化工艺 -回复

橡胶硫化工艺 -回复
橡胶硫化工艺是指将橡胶加热和加硫化剂混合,在一定时间内使橡胶分子链发生交联反应,形成强度和弹性的产品。
硫化是橡胶加工中重要的工艺步骤,它可以提高橡胶的耐磨性、耐热性、耐老化性和弹性等性能。
具体的硫化工艺步骤包括:
1. 橡胶的混炼:将橡胶与其他添加剂(如填充剂、增塑剂、防老剂等)混合,形成胶料。
2. 准备硫化剂:根据橡胶种类和要求,选择合适的硫化剂。
3. 在混炼机或橡胶硫化机中加入硫化剂:将硫化剂均匀地混合到胶料中。
4. 调整温度和时间:根据橡胶种类、硫化剂和产品要求,确定硫化温度和硫化时间。
5. 进行硫化反应:将经过混炼后的胶料放入硫化机中,进行硫化反应。
6. 冷却、脱模:经过硫化反应的橡胶制品进行冷却,并脱模成型。
7. 进行后处理:可以进行修整、检验、包装等工艺步骤。
以上是一般橡胶硫化工艺的基本步骤,具体的操作要根据不同的橡胶种类、产品要求和硫化机的具体情况进行调整和改善。
橡胶制品的硫化工艺
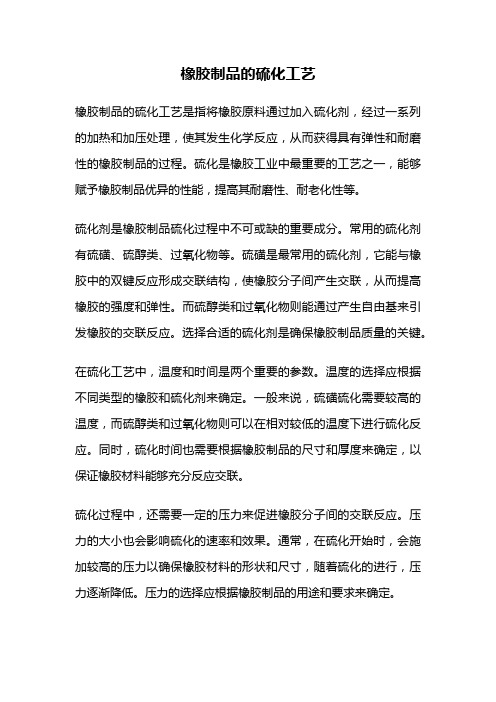
橡胶制品的硫化工艺橡胶制品的硫化工艺是指将橡胶原料通过加入硫化剂,经过一系列的加热和加压处理,使其发生化学反应,从而获得具有弹性和耐磨性的橡胶制品的过程。
硫化是橡胶工业中最重要的工艺之一,能够赋予橡胶制品优异的性能,提高其耐磨性、耐老化性等。
硫化剂是橡胶制品硫化过程中不可或缺的重要成分。
常用的硫化剂有硫磺、硫醇类、过氧化物等。
硫磺是最常用的硫化剂,它能与橡胶中的双键反应形成交联结构,使橡胶分子间产生交联,从而提高橡胶的强度和弹性。
而硫醇类和过氧化物则能通过产生自由基来引发橡胶的交联反应。
选择合适的硫化剂是确保橡胶制品质量的关键。
在硫化工艺中,温度和时间是两个重要的参数。
温度的选择应根据不同类型的橡胶和硫化剂来确定。
一般来说,硫磺硫化需要较高的温度,而硫醇类和过氧化物则可以在相对较低的温度下进行硫化反应。
同时,硫化时间也需要根据橡胶制品的尺寸和厚度来确定,以保证橡胶材料能够充分反应交联。
硫化过程中,还需要一定的压力来促进橡胶分子间的交联反应。
压力的大小也会影响硫化的速率和效果。
通常,在硫化开始时,会施加较高的压力以确保橡胶材料的形状和尺寸,随着硫化的进行,压力逐渐降低。
压力的选择应根据橡胶制品的用途和要求来确定。
硫化工艺中还有一项重要的工序是硫化后的后处理。
在硫化完成后,橡胶制品需要经过一定的处理来去除硫化剂残留和改善其性能。
常见的后处理方法包括水洗、热风处理、热水处理等。
水洗可以有效去除硫化剂残留,热风和热水处理则可以改善橡胶制品的表面光洁度和性能。
在橡胶制品的硫化工艺中,除了硫化剂、温度、时间和压力等因素外,还需要考虑到橡胶原料的选择和橡胶配方的优化。
不同类型的橡胶具有不同的硫化特性,需要选择适合的硫化剂和工艺条件。
橡胶配方的优化则可以通过调整橡胶中的添加剂和填充剂等成分来改善橡胶制品的性能。
橡胶制品的硫化工艺是一个复杂而关键的生产过程,它直接影响着橡胶制品的质量和性能。
通过合理选择硫化剂、控制温度和时间、施加适当的压力以及进行后处理,可以获得优异的橡胶制品。
橡胶用硫磺硫化的工艺流程
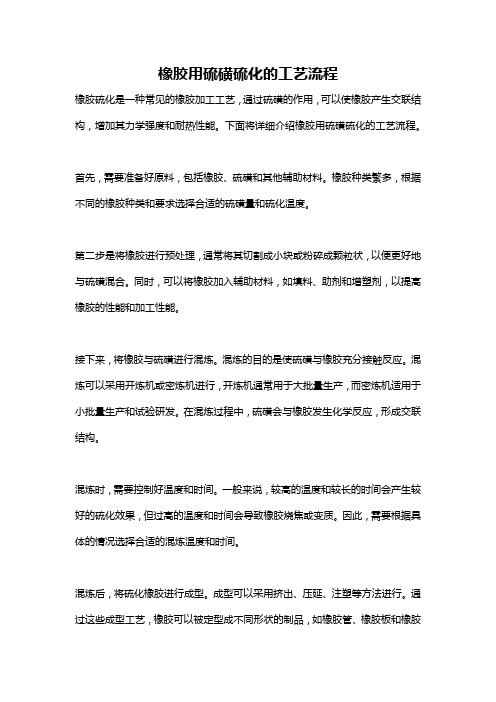
橡胶用硫磺硫化的工艺流程橡胶硫化是一种常见的橡胶加工工艺,通过硫磺的作用,可以使橡胶产生交联结构,增加其力学强度和耐热性能。
下面将详细介绍橡胶用硫磺硫化的工艺流程。
首先,需要准备好原料,包括橡胶、硫磺和其他辅助材料。
橡胶种类繁多,根据不同的橡胶种类和要求选择合适的硫磺量和硫化温度。
第二步是将橡胶进行预处理,通常将其切割成小块或粉碎成颗粒状,以便更好地与硫磺混合。
同时,可以将橡胶加入辅助材料,如填料、助剂和增塑剂,以提高橡胶的性能和加工性能。
接下来,将橡胶与硫磺进行混炼。
混炼的目的是使硫磺与橡胶充分接触反应。
混炼可以采用开炼机或密炼机进行,开炼机通常用于大批量生产,而密炼机适用于小批量生产和试验研发。
在混炼过程中,硫磺会与橡胶发生化学反应,形成交联结构。
混炼时,需要控制好温度和时间。
一般来说,较高的温度和较长的时间会产生较好的硫化效果,但过高的温度和时间会导致橡胶烧焦或变质。
因此,需要根据具体的情况选择合适的混炼温度和时间。
混炼后,将硫化橡胶进行成型。
成型可以采用挤出、压延、注塑等方法进行。
通过这些成型工艺,橡胶可以被定型成不同形状的制品,如橡胶管、橡胶板和橡胶密封件等。
最后,将成型的橡胶制品进行硫化处理。
硫化可以采用加热硫化和热压硫化两种方法。
在加热硫化中,将制品放入硫化箱或硫化室中,加热到一定温度,使硫磺与橡胶发生硫化反应。
热压硫化是在加热的同时施加压力,以加快硫化反应速度和提高硫化效果。
硫化温度和时间是硫化过程中的重要参数,需要根据橡胶种类和制品要求进行调整。
过低的温度和时间会导致硫化不完全,影响橡胶的性能;而过高的温度和时间会导致橡胶过硫化,出现老化和变质现象。
总结来说,橡胶用硫磺硫化的工艺流程包括原料准备、橡胶预处理、混炼、成型和硫化处理。
每个步骤都需要根据橡胶种类和制品要求进行操作,以保证橡胶硫化的效果和质量。
橡胶硫化工艺(2021精选文档)
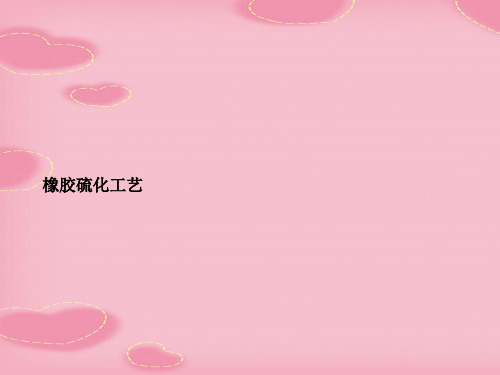
硫化是橡胶制品加工的主要工艺过程之一,也 是橡胶制品生产中的最后一个加工工序。
橡胶经历了一系列复杂的化学变化,由塑性的 混炼胶变为高弹性的或硬质的交联橡胶,从而 获得更完善的物理机械性能和化学性能,提高 和拓宽了橡胶材料的使用价值和应用范围。。
二、橡胶硫化历程
(一)橡胶硫化反应过程 硫化反应是一个由多元组份参与的复杂的化 学反应过程,它包含橡胶分子与硫化剂及其 它配合剂之间发生的一系列化学反应。
TH-理论正硫化时间; T10-焦烧时间,M10对应的时间; T90- 工艺正硫化时间,M90对应的时间
(四)、理想硫化曲线
➢硫化诱导期足够大,充分保证生产加工的安 全性; ➢硫化速度要快,提高生产效率,降低成本; ➢硫化平坦期要长。
达到上述要求,必须正确选择硫化条件和硫化 体系。
三、正硫化及其测定方法
1、正硫化及正硫化时间
➢正硫化,又称最宜硫化,通常是指橡胶制品 性能达最佳值时的硫化状态。
➢正硫化时间是指达到正硫化状态所需时间。 ➢实际上正硫化时间是一个范围,不是一个点,
一般在平坦硫化阶段选取。 ➢处于正硫化前期(欠硫)或后期(过硫)状
态,硫化胶物性都较差。
由于理论与实际的差别,在实际生产中所采用 的正硫化时间与理论上的正硫化时间并不一致, 通常正硫化时间包括理论正硫化时间、工艺正 硫化时间和工程正硫化时间三个概念。
第一阶段:诱导阶段
先是硫磺、活化剂、促进 剂相互作用,使活化剂在 胶料中溶解度增加,活化 促进剂,使促进剂与硫磺 之间反应生成一种活性更 大的中间产物;然后进一 步引发橡胶分子链产生可 交联的橡胶大分子自由基。
橡胶制品连续硫化方法简介

橡胶制品连续硫化方法简介连续硫化法是一种动态硫化方法。
其优点是产品不受长度限制,无重复硫化,能实现连续化、自动化、提高生产效率。
常见的连续硫化工艺如下:(1)热空气连续硫化室硫化法这是一种常压硫化方法,主要应用于硫化胶布、海绵胶条和胶乳制品。
制品连续通过硫化室进行加热硫化。
硫化室可分为三段,第一段为预热、升温,将制品加热到硫化温度;第二段为恒温硫化,制品于该段内的停留时间可以通过调节制品运动速度的方法加以调节;第三段为降温冷却,以便于制品的收卷。
硫化室可采用间接蒸汽、电、红外线等方式加热。
(2)蒸汽管道连续硫化法此工艺的特点是使制品连续地通过密封的硫化管道进行硫化。
硫化管道与压出机相连,制品经压出后直接进入硫化管道,管道中通入1~2.5MPa的高压蒸汽,管道尾部有高压冷却水进行冷却。
硫化管道的两端都安装防止高压蒸汽泄露的密封装置,一般采用迷宫式垫圈或水封法密封。
这种硫化方法主要用于硫化胶管、电缆、电线等两端易于密封的制品。
(3)液体介质连续硫化法(盐浴连续硫化法)硫化介质为熔融合金(锡42%、铋58%),熔点150℃;或者熔盐(硝酸钾53%、亚硝酸钠40%、硝酸钠7%),其熔点142℃,沸点500℃。
硫化时先将硫化介质以电加热至180~250℃,然后将半成品通过(通过时间依胶料的硫化条件而定),便可进行连续硫化。
由于熔融合金或熔融盐密度很大(1926kg/m3),因而必须用钢带将半成品型材压住使其浸入熔融液中。
由于熔融液传热很快,能使半成品迅速受热硫化,在180~250℃下以10~15m/min的速度硫化制品,但存在易使薄制品和空心制品变形的缺陷。
此法常用于胶管、胶条、电缆以及其他型材的硫化。
(4)沸腾床连续硫化法沸腾床是指在热空气流中悬浮直径为0.15~0.25mm的玻璃珠或粒径为0.2~0.3mm的石英砂为硫化介质的装置。
在受热空气流的吹动下,固体粒子悬浮于气体翻动,形成沸腾状态的加热床。
沸腾床可用电热或者过热蒸汽等加热,使之达到200~250℃的温度。
- 1、下载文档前请自行甄别文档内容的完整性,平台不提供额外的编辑、内容补充、找答案等附加服务。
- 2、"仅部分预览"的文档,不可在线预览部分如存在完整性等问题,可反馈申请退款(可完整预览的文档不适用该条件!)。
- 3、如文档侵犯您的权益,请联系客服反馈,我们会尽快为您处理(人工客服工作时间:9:00-18:30)。
橡胶硫化工艺方法
一、传统橡胶硫化工艺
1、影响硫化工艺过程的主要因素:
硫磺用量。
其用量越大,硫化速度越快,可以达到的硫化程度也越高。
硫磺在橡胶中的溶解度是有限的,过量的硫磺会由胶料表面析出,俗称“喷硫”。
为了减少喷硫现象,要求在尽可能低的温度下,或者至少在硫磺的熔点以下加硫。
根据橡胶制品的使用要求,硫磺在软质橡胶中的用量一般不超过3%,在半硬质胶中用量一般为20%左右,在硬质胶中的用量可高达40%以上。
硫化温度。
若温度高10℃,硫化时间约缩短一半。
由于橡胶是不良导热体,制品的硫化进程由于其各部位温度的差异而不同。
为了保证比较均匀的硫化程度,厚橡胶制品一般采用逐步升温、低温长时间硫化。
2、硫化时间:这是硫化工艺的重要环节,时间过短,硫化程度不足(亦称欠硫)。
时间过长,硫化程度过高(俗称过硫)。
只有适宜的硫化程度(俗称正硫化),才能保证最佳的综合性能
二、橡胶硫化工艺方法
按硫化条件可分为冷硫化、室温硫化和热硫化三类。
1、冷硫化可用于薄膜制品的硫化,制品在含有2%~5%氯化硫的二硫化碳溶液中浸渍,然后洗净干燥即可。
2、室温硫化时,硫化过程在室温和常压下进行,如使用室温硫化胶浆(混炼胶溶液)进行自行车内胎接头、修补等。
3、热硫化是橡胶制品硫化的主要方法。
根据硫化介质及硫化方式的不同,热硫化又可分为直接硫化、间接硫化和混气硫化三种方法。
①直接硫化,将制品直接置入热水或蒸汽介质中硫化。
②间接硫化,制品置于热空气中硫化,此法一般用于某些外观要求严格的制品,如胶鞋等。
③混气硫化,先采用空气硫化,而后再改用直接蒸汽硫化。
此法既可以克服蒸汽硫化影响制品外观的缺点,也可以克服由于热空气传热慢,而硫化时间长和易老化的缺点。
三、橡胶硫化工艺:
橡胶在未硫化之前,分子之间没有产生交联,因此缺乏良好的物理机械性能,实用价值不大。
当橡胶加入硫化剂以后,经热处理或其他方式能使橡胶分子之间产生交联,形成三维网状结构,从而使其性能大大改善,尤其是橡胶的定伸应力、弹性、硬度、拉伸强度等一系列物理机械性能都会大大提高。
橡胶大分子在加热下与交联剂硫磺发生化学反应,交联成为立体网状结构的过程。
经过硫化后的橡胶称硫化胶。
硫化是橡胶加工中的最后一个工序,可以得到定型的具有实用价值的橡胶制品。
四、注压成型硫化工艺:
普通模压与注压最明显的区别在于前者胶料是以冷的状态充入模腔的,而后者则是将胶料加热混合,并在接近硫化温度下注入模腔。
因而,在注压过程中,加热模板所提供的热量仅仅只用于维持硫化,它能很快将胶料加热到190℃-220℃。
在模压过程中,由加热模板所提供的热量首先要用于预热胶料,由于橡胶的导热性能差,如果制品很厚,热量要传导到制品中心需要较长的时间。
采用高温硫化也可在一定程度上缩短操作时间,但往往导致靠近热板的制品边缘出现焦烧。
采
用注压法硫化,可以缩短成型周期,实现自动化操作,这对大批量生产最为有利。
注压还具有以下优点:可以省去半成品准备、起模和制品修边等工序;可以生产出尺寸稳定、物理机械性能优异的高质量产品;减少硫化时间,提高生产效率,减少胶料用量,降低成本,减少废品,提高企业经济效益。
五、注压成型硫化工艺注意事项:
采用合理的螺杆转速、背压,控制适当的注射机温度。
一般地,应保持出料口胶温和控制循环温度之差不大于30度为宜。
注射机螺杆的用途是在选定的和均匀的温度下为每一循环制备足够量的胶料;它明显地影响着注射机的产量。
背压是通过放慢注射缸中出油口的流量而产生的,并对注射机所射出胶料,对注射油缸的推挤作用进行限制。
实践中,背压只会稍微增加对胶料的剪切,而不会引起硫化制品物理性能的降低。
喷嘴的设计:
喷嘴连接注射机头和模具,同时对热平衡有一定作用。
经过喷嘴的压力损失会经由注射而转换成为热量。
胶料绝不允许在这个部位硫化。
因此,选择合适的喷嘴直径非常重要,它影响着喷嘴部位的摩擦生热、胶料注射时所需要的压力和充模时间。
合适的模具温度,最佳的硫化条件。
在选择好胶料的最佳配合之后,重要的就是注射成型条件与硫化条件的相互配合。
注压成型与模压成型相比,由于模具表面、内部温度分布不同,要实现良好的硫化就必须对温度进行高精度控制,使模具表面、内部同时达到最佳硫化条件。
高温会增大橡胶的收缩率,但二者关系是线性的,在生产前应有充分的估计。
此外,就成型压力而言,高压成型是极为有利的,因为压力与收缩成反比关系。
安全合理的胶料配方设计。
对于进行注压硫化成型的胶料,要求其具有以下特性:胶料的门尼焦烧时间应当尽可能的长,以获得最大的安全性。
通常,门尼焦烧时间应比胶料在机筒中的停留时间长2倍。
硫化速度快,通过对不同胶料硫化体系的合理选择,添加合适的促进剂,使胶料在注压硫化时有令人满意的效率。
流动性良好,良好的流动性能减少胶料的停留时间,减少注压时间,并提高防焦烧能力。
六、氮气硫化工艺
采用充氮气硫化的主要优点是节能和延长胶囊寿命,可节省蒸汽80%,胶囊使用寿命可延长1倍。
轮胎在硫化过程中要消耗大量热能和电能,因此开发和推广节能硫化工艺意义重大。
由于氮气分子量小、热容很小,氮气充入轮胎胶囊内腔时,不会吸热而引起温度降低,也不易造成胶囊氧化裂解破坏。
七、氮气硫化的工艺特点
先通高温高压蒸汽,若干分钟后切换通入氮气,利用充氮硫化的“保压变温”工艺硫化至结束。
因为最初通入几分钟蒸汽的热量足够保持硫化一条轮胎,理论上只要在完成硫化之前温度不降到150℃以下即可。
但是,采用氮气硫化时,首先通入的是高温高压蒸汽,会造成上下胎侧的温差,要消除上下胎侧的硫化温差,必须合理布置硫化介质喷射的位置,改进密封和热工管路系统。
硫化用氮气的纯度要求达99.99%,最好达到99.999%,并建议企业自配制氮系统,以降低使用成本。
氮气纯度不够,会影响胶囊的使用寿命。
将氮气硫化的“保压变温”硫化原理应用于传统循环过热水硫化工艺的改造,人们又开发出了用高温高压蒸汽加过热水的硫化工艺取代常规的循环过热水硫化工艺。
硫化时,先通入高温高压蒸汽,若干分钟后切换通入循环过热水,再过若干分钟后关闭回水阀停止循环,直
到利用潜热硫化至结束。
采用这种新的加热硫化方法,据理论计算,其能耗仅是传统硫化工艺方法的1/2。
八、变温硫化工艺
变温硫化工艺过程的关键因素
根据成品物理性能试验和生产经验,缩短硫化时间。
这在一定程度上减轻了过硫化程度。
采用高温硫化。
近年来小型轮胎硫化工艺逐渐向高温硫化方向发展,且考虑后硫化效应,硫化时间短,对减轻过硫和提高硫化程度的均匀性有一定作用。
进行硫化测温,找到制品中的最慢硫化点,以该点为依据来确定硫化时间,效果较前两种好。
利用该法可不同程度地提高硫化效率,改善硫化程度的均匀性。
但由于实际生产中只考察外温,轮胎各部位的实际温度并不确知,加上并不是每次温度固定不变,因此根据测温计算出的结果与实际硫化的结果有较大误差。
橡胶厚制品硫化过程温度场模拟仿真与预测表明,温度不均匀是造成轮胎外胎硫化程度不均匀的主要因素。
橡胶工业普遍认为外温恒定是保证质量的重要条件,从设备上要千方百计地实现恒温。
这对非厚橡胶制品来说是正确的,而对轮胎外胎等厚橡胶制品则不然。
轮胎在模型中加热硫化,热经由模型传到外胎各部位。
橡胶是热的不良导体,温升慢,加热早期外胎各部位存在明显的温度梯度,经过较长时间才能达到平衡。
上一篇:橡胶拉力试验机测试项目。