橡胶硫化工艺
橡胶硫化工艺流程
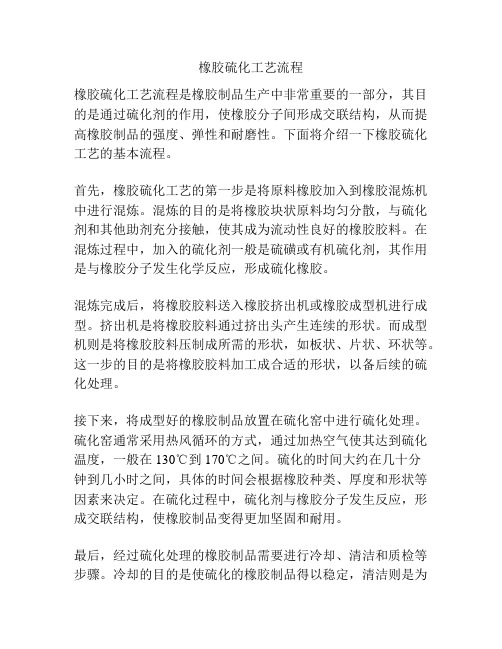
橡胶硫化工艺流程橡胶硫化工艺流程是橡胶制品生产中非常重要的一部分,其目的是通过硫化剂的作用,使橡胶分子间形成交联结构,从而提高橡胶制品的强度、弹性和耐磨性。
下面将介绍一下橡胶硫化工艺的基本流程。
首先,橡胶硫化工艺的第一步是将原料橡胶加入到橡胶混炼机中进行混炼。
混炼的目的是将橡胶块状原料均匀分散,与硫化剂和其他助剂充分接触,使其成为流动性良好的橡胶胶料。
在混炼过程中,加入的硫化剂一般是硫磺或有机硫化剂,其作用是与橡胶分子发生化学反应,形成硫化橡胶。
混炼完成后,将橡胶胶料送入橡胶挤出机或橡胶成型机进行成型。
挤出机是将橡胶胶料通过挤出头产生连续的形状。
而成型机则是将橡胶胶料压制成所需的形状,如板状、片状、环状等。
这一步的目的是将橡胶胶料加工成合适的形状,以备后续的硫化处理。
接下来,将成型好的橡胶制品放置在硫化窑中进行硫化处理。
硫化窑通常采用热风循环的方式,通过加热空气使其达到硫化温度,一般在130℃到170℃之间。
硫化的时间大约在几十分钟到几小时之间,具体的时间会根据橡胶种类、厚度和形状等因素来决定。
在硫化过程中,硫化剂与橡胶分子发生反应,形成交联结构,使橡胶制品变得更加坚固和耐用。
最后,经过硫化处理的橡胶制品需要进行冷却、清洁和质检等步骤。
冷却的目的是使硫化的橡胶制品得以稳定,清洁则是为了去除表面的杂质和污染物,保证产品的质量。
质检是为了确保橡胶制品的尺寸、力学性能和外观等符合标准要求。
总之,橡胶硫化工艺流程是一个复杂而关键的过程,其中包括混炼、成型、硫化、冷却、清洁和质检等环节。
通过这些步骤的协同作用,可以使橡胶制品达到所需的机械性能和物理性能。
橡胶工艺----硫化篇
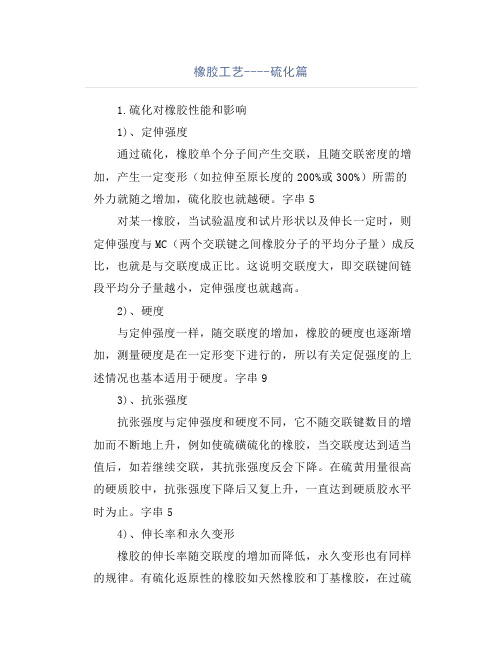
橡胶工艺----硫化篇1.硫化对橡胶性能和影响1)、定伸强度通过硫化,橡胶单个分子间产生交联,且随交联密度的增加,产生一定变形(如拉伸至原长度的200%或300%)所需的外力就随之增加,硫化胶也就越硬。
字串5对某一橡胶,当试验温度和试片形状以及伸长一定时,则定伸强度与MC(两个交联键之间橡胶分子的平均分子量)成反比,也就是与交联度成正比。
这说明交联度大,即交联键间链段平均分子量越小,定伸强度也就越高。
2)、硬度与定伸强度一样,随交联度的增加,橡胶的硬度也逐渐增加,测量硬度是在一定形变下进行的,所以有关定促强度的上述情况也基本适用于硬度。
字串93)、抗张强度抗张强度与定伸强度和硬度不同,它不随交联键数目的增加而不断地上升,例如使硫磺硫化的橡胶,当交联度达到适当值后,如若继续交联,其抗张强度反会下降。
在硫黄用量很高的硬质胶中,抗张强度下降后又复上升,一直达到硬质胶水平时为止。
字串54)、伸长率和永久变形橡胶的伸长率随交联度的增加而降低,永久变形也有同样的规律。
有硫化返原性的橡胶如天然橡胶和丁基橡胶,在过硫化以后由于交联度不断降低,其伸长率和永久变形又会逐渐增大。
5)、弹性未硫化胶受到较长时间的外力作用时,主要发生塑性流动,橡胶分子基本上没有回到原来的位置的倾向。
橡胶硫化后,交联使分子或链段固定,形变受到网络的约束,外力作用消除后,分子或链段力图回复原来构象和位置,所以硫化后橡胶表现出很大的弹性。
交联度的适当增加,这种可逆的弹性回复表现得更为显著。
2.硫化过程的四个阶段胶料在硫化时,其性能随硫化时间变化而变化的曲线,称为硫化曲线。
从硫化时间影响胶料定伸强度的过程来看,可以将整个硫化时间分为四个阶段:硫化起步阶段、欠硫阶段、正硫阶段和过硫阶段。
1)、硫化起步阶段(又称焦烧期或硫化诱导期)硫化起步的意思是指硫化时间胶料开始变硬而后不能进行热塑性流动那一点的时间。
硫起步阶段即此点以前的硫化时间。
在这一阶段内,交联尚未开始,胶料在模型内有良好的流动性。
橡胶硫化工艺
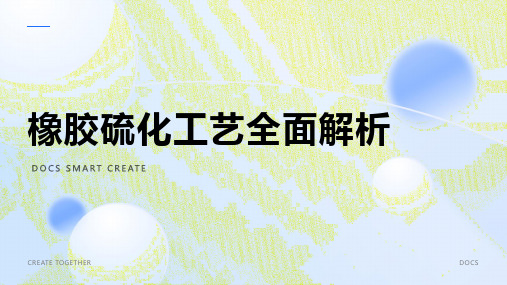
橡胶硫化工艺的未来发展趋势
智能化硫化工艺
• 利用物联网和大数据技术进行硫化工艺的监控和优化 • 提高硫化工艺的生产效率和产品质量
绿色硫化工艺
• 降低硫化工艺的能耗和污染排放 • 提高橡胶制品的环保性能
橡06胶硫化工艺在典型橡胶制品中的应用
实例
橡胶轮胎的硫化工艺与应用实例
橡胶轮胎的硫化工艺
• 热硫化工艺 • 压力硫化工艺
橡胶轮胎的应用实例
• 汽车轮胎 • 摩托车轮胎 • 飞机轮胎
橡胶密封件的硫化工艺与应用实例
橡胶密封件的硫化工艺
• 冷硫化工艺 • 压力硫化工艺
橡胶密封件的应用实例
• 汽车密封件 • 建筑密封件 • 航空航天密封件
橡胶输送带的硫化工艺与应用实例
• 热硫化工艺:加热橡胶材料进行硫化 • 冷硫化工艺:不加热橡胶材料进行硫化 • 压力硫化工艺:在压力条件下进行硫化
橡胶硫化工艺的特点
• 热硫化工艺:硫化效果好,生产效率较高 • 冷硫化工艺:适用于特殊场合,生产效率较低 • 压力硫化工艺:适用于大型橡胶制品,能提高制品的致密性
02
橡胶硫化工艺的主要方法及其原理
热硫化工艺及其原理
热硫化工艺
• 将橡胶材料加热至一定温度,加入硫化剂进行硫化 • 适用于大多数橡胶制品的硫化
热硫化工艺的原理
• 橡胶材料在加热过程中,分子链运动加剧,有利于硫化 剂的渗透 • 硫化剂与橡胶分子发生化学反应,形成交联结构,提高 橡胶制品的性能
冷硫化工艺及其原理
冷硫化工艺
• 在室温条件下,使用催化剂和硫化剂对橡胶材料进行硫 化 • 适用于特殊场合,如低温、高温或无法加热的场合
硫化工艺和注胶工艺的区别

硫化工艺和注胶工艺的区别硫化工艺和注胶工艺是两种常见的工业生产过程,主要应用于不同类型的产品制造中。
硫化工艺,又称为橡胶硫化,是一种将橡胶加热处理,使其在加热和加硫剂的作用下发生交联反应,从而使橡胶得到硬化的工艺方法。
硫化过程中,橡胶分子链之间的亲和力增强,分子链之间形成交联结构,增加了橡胶的硬度、耐磨性和机械强度。
硫化工艺可以提高橡胶材料的耐热性、耐磨性、耐油性以及机械性能,广泛应用于橡胶制品的生产中,如轮胎、密封件等。
注胶工艺,是一种将液态胶注射到模具中,通过固化反应形成所需产品的工艺方法。
注胶工艺适用于塑料、橡胶、树脂等材料的制品生产,在电子、汽车、医疗、食品包装等多个领域有广泛的应用。
注胶工艺具有生产效率高、产品精度高、成本低等优势,可以生产出形状复杂、结构丰富的产品,如手机外壳、汽车零件、塑料瓶等。
两种工艺的主要区别如下:1. 工艺原理不同:硫化工艺主要依靠加热和硫化剂使橡胶发生交联反应,从而实现橡胶的硬化;而注胶工艺通过液态胶注射进模具,并在固化反应中形成产品。
2. 适用材料不同:硫化工艺主要应用于橡胶材料的制品生产,如橡胶密封件、橡胶管、轮胎等;注胶工艺适用于塑料、橡胶、树脂等材料的产品生产。
3. 设备和工艺要求不同:硫化工艺通常需要橡胶硫化机、硫化模具等设备,以及硫化时间较长;注胶工艺涉及到注射机、模具等设备,通常需要控制注胶时间、注胶温度等参数。
4. 加工效率不同:硫化工艺相对注胶工艺来说,加工效率低,需要较长的硫化时间,因此生产周期相对较长;注胶工艺生产效率高,通过流水线生产可以实现大规模生产,缩短生产周期。
5. 产品特性和用途不同:硫化工艺生产的橡胶制品通常具有耐磨、耐油、耐高温等特性,广泛应用于汽车、机械、电器等领域;注胶工艺生产的产品通常具有良好的密封性能、外观精美等特点,广泛应用于电子、医疗、食品包装等领域。
总而言之,硫化工艺主要应用于橡胶制品生产,通过加热和硫化剂使橡胶硬化;注胶工艺主要应用于塑料、橡胶、树脂等材料的产品生产,通过注射和固化反应形成所需产品。
橡胶硫化工艺流程
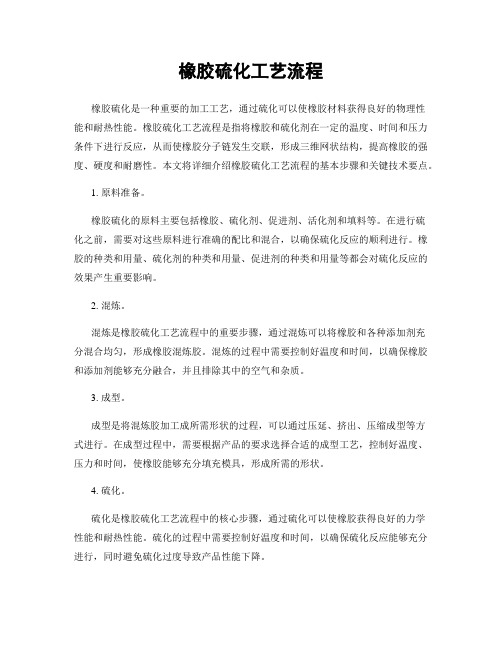
橡胶硫化工艺流程橡胶硫化是一种重要的加工工艺,通过硫化可以使橡胶材料获得良好的物理性能和耐热性能。
橡胶硫化工艺流程是指将橡胶和硫化剂在一定的温度、时间和压力条件下进行反应,从而使橡胶分子链发生交联,形成三维网状结构,提高橡胶的强度、硬度和耐磨性。
本文将详细介绍橡胶硫化工艺流程的基本步骤和关键技术要点。
1. 原料准备。
橡胶硫化的原料主要包括橡胶、硫化剂、促进剂、活化剂和填料等。
在进行硫化之前,需要对这些原料进行准确的配比和混合,以确保硫化反应的顺利进行。
橡胶的种类和用量、硫化剂的种类和用量、促进剂的种类和用量等都会对硫化反应的效果产生重要影响。
2. 混炼。
混炼是橡胶硫化工艺流程中的重要步骤,通过混炼可以将橡胶和各种添加剂充分混合均匀,形成橡胶混炼胶。
混炼的过程中需要控制好温度和时间,以确保橡胶和添加剂能够充分融合,并且排除其中的空气和杂质。
3. 成型。
成型是将混炼胶加工成所需形状的过程,可以通过压延、挤出、压缩成型等方式进行。
在成型过程中,需要根据产品的要求选择合适的成型工艺,控制好温度、压力和时间,使橡胶能够充分填充模具,形成所需的形状。
4. 硫化。
硫化是橡胶硫化工艺流程中的核心步骤,通过硫化可以使橡胶获得良好的力学性能和耐热性能。
硫化的过程中需要控制好温度和时间,以确保硫化反应能够充分进行,同时避免硫化过度导致产品性能下降。
5. 后处理。
硫化完成后,还需要进行后处理工艺,如冷却、清洗、修整等,以确保产品的质量和外观。
同时还需要进行产品的检验和包装,最终将产品送往市场。
总之,橡胶硫化工艺流程是一个复杂而精细的加工过程,需要严格控制各个环节,以确保产品的质量和性能。
只有在每个步骤中严格执行工艺要求,才能生产出符合要求的橡胶制品。
希望本文对橡胶硫化工艺流程有所帮助,谢谢阅读。
橡胶硫化处理

橡胶硫化处理
橡胶硫化处理是一种常用的橡胶加工工艺,通过加入硫化剂和硫化促进剂,将橡胶中的双键与硫化剂反应,形成交联结构,使橡胶具有弹性和耐热性。
橡胶硫化处理的步骤如下:
1. 预处理:将橡胶进行粉碎、除尘等处理,去除杂质,提高橡胶的流动性和加工性能。
2. 配方调制:根据橡胶产品的要求,制定合适的配方,包括橡胶种类、硫化剂、硫化促进剂、填料和增塑剂等。
3. 混炼:将橡胶和配方中的其他原料进行混合研磨,通过机械剪切和摩擦产生热量,使配方中的硫化剂和硫化促进剂溶解在橡胶中。
4. 成型:将混炼后的橡胶转移到模具中,经压力和温度作用下,使橡胶成型为所需形状。
5. 硫化:将成型后的橡胶制品放入硫化箱中,控制温度和时间,使硫化剂与橡胶发生反应,形成交联结构。
硫化过程中,还可通过加入加速剂、防老剂等,控制硫化速度和增强橡胶的性能。
6. 后处理:经过硫化处理的橡胶制品进行洗涤和擦拭,去除表面的灰尘和杂质,使其达到最终的外观和品质要求。
橡胶硫化处理可以提高橡胶制品的硬度、强度、弹性和耐热性,改善橡胶制品的耐磨性和耐老化性能,使其适用于各种工业和日常用品的制造。
橡胶制品的硫化工艺
橡胶制品的硫化工艺橡胶制品的硫化工艺是指将橡胶原料通过加入硫化剂,经过一系列的加热和加压处理,使其发生化学反应,从而获得具有弹性和耐磨性的橡胶制品的过程。
硫化是橡胶工业中最重要的工艺之一,能够赋予橡胶制品优异的性能,提高其耐磨性、耐老化性等。
硫化剂是橡胶制品硫化过程中不可或缺的重要成分。
常用的硫化剂有硫磺、硫醇类、过氧化物等。
硫磺是最常用的硫化剂,它能与橡胶中的双键反应形成交联结构,使橡胶分子间产生交联,从而提高橡胶的强度和弹性。
而硫醇类和过氧化物则能通过产生自由基来引发橡胶的交联反应。
选择合适的硫化剂是确保橡胶制品质量的关键。
在硫化工艺中,温度和时间是两个重要的参数。
温度的选择应根据不同类型的橡胶和硫化剂来确定。
一般来说,硫磺硫化需要较高的温度,而硫醇类和过氧化物则可以在相对较低的温度下进行硫化反应。
同时,硫化时间也需要根据橡胶制品的尺寸和厚度来确定,以保证橡胶材料能够充分反应交联。
硫化过程中,还需要一定的压力来促进橡胶分子间的交联反应。
压力的大小也会影响硫化的速率和效果。
通常,在硫化开始时,会施加较高的压力以确保橡胶材料的形状和尺寸,随着硫化的进行,压力逐渐降低。
压力的选择应根据橡胶制品的用途和要求来确定。
硫化工艺中还有一项重要的工序是硫化后的后处理。
在硫化完成后,橡胶制品需要经过一定的处理来去除硫化剂残留和改善其性能。
常见的后处理方法包括水洗、热风处理、热水处理等。
水洗可以有效去除硫化剂残留,热风和热水处理则可以改善橡胶制品的表面光洁度和性能。
在橡胶制品的硫化工艺中,除了硫化剂、温度、时间和压力等因素外,还需要考虑到橡胶原料的选择和橡胶配方的优化。
不同类型的橡胶具有不同的硫化特性,需要选择适合的硫化剂和工艺条件。
橡胶配方的优化则可以通过调整橡胶中的添加剂和填充剂等成分来改善橡胶制品的性能。
橡胶制品的硫化工艺是一个复杂而关键的生产过程,它直接影响着橡胶制品的质量和性能。
通过合理选择硫化剂、控制温度和时间、施加适当的压力以及进行后处理,可以获得优异的橡胶制品。
橡胶制品的硫化工艺
橡胶制品的硫化工艺橡胶制品的硫化工艺是指将橡胶原料与硫化剂在一定条件下进行反应,使橡胶分子间形成交联结构,从而提高橡胶的物理性能和耐热性能的过程。
硫化是橡胶加工中的重要工艺,对于提高橡胶制品的强度、耐磨性和耐老化性能具有重要作用。
一、硫化剂的选择硫化剂是橡胶制品硫化反应的催化剂,常用的硫化剂有硫磺、过氧化物、硫醇等。
选择合适的硫化剂要考虑橡胶种类、硫化温度、硫化速度以及橡胶制品的要求等因素。
二、硫化温度和时间硫化温度和时间是橡胶制品硫化工艺中非常重要的参数。
硫化温度过低会导致反应速度慢,硫化不完全;而硫化温度过高则会导致橡胶热老化、焦化等问题。
硫化时间过短会导致硫化不完全,物理性能不达标;而硫化时间过长则会浪费时间和能源。
三、硫化促进剂的添加硫化促进剂是一种能够加快橡胶硫化反应速度的物质。
常用的硫化促进剂有促进剂M和促进剂DM等。
硫化促进剂的添加可以提高硫化速度,缩短硫化时间,同时还能提高橡胶制品的物理性能和耐热性能。
四、硫化工艺条件控制硫化工艺条件的控制对于橡胶制品的质量起着至关重要的作用。
首先是硫化温度的控制,要根据橡胶种类和硫化剂的要求确定合适的硫化温度。
其次是硫化时间的控制,要根据硫化剂的种类和硫化速度确定合适的硫化时间。
此外,还需要对硫化压力、硫化介质等进行合理控制,以确保橡胶制品硫化过程的顺利进行。
五、硫化反应机理橡胶硫化反应是一个复杂的化学反应过程,其机理主要包括链断裂、硫醇与橡胶分子的反应、交联等。
硫化反应的机理研究对于优化硫化工艺、提高橡胶制品性能具有重要意义。
六、硫化后的橡胶制品处理硫化后的橡胶制品需要进行后处理,包括清洗、修整、检验等。
清洗可以去除硫化剩余物和杂质,使橡胶制品表面干净整洁;修整可以修剪橡胶制品的边缘,使其外观更加美观;检验则是对橡胶制品进行物理性能和外观质量的检测,以确保橡胶制品符合规定的标准和要求。
橡胶制品的硫化工艺是一个非常重要的工艺环节,对于提高橡胶制品的性能和质量至关重要。
橡胶硫化工艺
橡胶硫化工艺橡胶硫化工艺是将天然橡胶或合成橡胶通过硫化反应,使其具备强度、耐磨性、耐老化性等特性的一种工艺。
本文将从橡胶硫化的原理、硫化剂的选择、硫化工艺流程以及硫化后橡胶的性能等方面展开阐述。
一、橡胶硫化的原理橡胶硫化是指通过将橡胶与硫化剂在一定温度下反应,使橡胶中的双键与硫原子发生加成反应,形成交联结构的过程。
在硫化过程中,硫化剂中的硫原子会与橡胶中的双键发生反应,形成硫化橡胶。
硫化反应可以使橡胶具备耐高温、耐溶剂、耐老化等优异性能。
二、硫化剂的选择硫化剂是橡胶硫化过程中的重要组成部分,常用的硫化剂有硫、过氧化氮、过氧化物等。
硫是一种常用的硫化剂,其硫化反应速度较慢,但可以获得较好的硫化效果。
过氧化氮是一种加速剂,可以提高硫化反应速度和效果。
过氧化物则是一种高温硫化剂,适用于高温硫化橡胶。
三、硫化工艺流程橡胶硫化一般包括预硫化和硫化两个阶段。
预硫化是指在较低温度下对橡胶进行预处理,使其具备一定的硫化程度,提高硫化效果。
硫化是指在较高温度下对橡胶进行硫化反应,形成交联结构。
硫化温度一般在120℃-180℃之间,硫化时间根据橡胶种类和硫化剂的不同而定。
四、硫化后橡胶的性能橡胶经过硫化后,其性能得到显著改善。
硫化可以提高橡胶的强度、硬度、耐磨性、耐油性、耐老化性等。
硫化后的橡胶具有较好的弹性和可塑性,广泛应用于橡胶制品、轮胎、密封材料等领域。
总结:橡胶硫化工艺是将橡胶经过硫化反应,使其具备优异性能的一种工艺。
硫化剂的选择和硫化工艺流程对于硫化效果具有重要影响。
硫化后的橡胶具有较好的强度、耐磨性、耐老化性等性能,广泛应用于各个领域。
橡胶硫化工艺的研究和应用对于提高橡胶制品的品质和性能具有重要意义。
橡胶的硫化工艺
橡胶的硫化工艺
橡胶的硫化工艺是一种使橡胶制品获得优良性能的过程,主要通过在一定的温度和压力下,将橡胶分子交联成为网状结构来实现。
这个过程包括以下步骤:
1. 混炼:将生胶和配合剂混合在一起,在炼胶机上加工成具有可塑性的混炼胶。
2. 塑炼:通过物理方法降低生胶的弹性,增加其可塑性。
3. 压延:将塑炼胶压延成一定形状的薄片。
4. 压出:将塑炼胶通过口型压出成一定形状的橡胶半成品。
5. 硫化:在一定的温度和压力下,经过一定的时间进行化学和某些物理变化,使橡胶分子由线型结构变成网状结构的交联过程。
硫化后的橡胶制品不仅能提高强度,还获得了优良的使用性能。
同时,硫化过程中应经常注意检查压力表、安全阀等安全装置,看其是否灵敏可靠。
此外,使用的脱模剂也是易燃物质,应妥善保管和使用,以防发生火灾。
- 1、下载文档前请自行甄别文档内容的完整性,平台不提供额外的编辑、内容补充、找答案等附加服务。
- 2、"仅部分预览"的文档,不可在线预览部分如存在完整性等问题,可反馈申请退款(可完整预览的文档不适用该条件!)。
- 3、如文档侵犯您的权益,请联系客服反馈,我们会尽快为您处理(人工客服工作时间:9:00-18:30)。
PPT文档演模板
橡胶硫化工艺
3、平坦硫化阶段
➢cd段,相当于网络形成的前期,这时交联反应已 基本完成,继而发生交联键的重排、裂解等反应。
➢交联、裂解同时存在,达到平衡,出现平坦区,对 应平坦硫化时间,其长短取决于胶料配方,主要是促 进剂和防老剂。
➢胶料具有最佳综合性能,在该区选取正硫化时间
PPT文档演模板
橡胶硫化工艺
PPT文档演模板
2020/11/22
橡胶硫化工艺
硫化是指橡胶的线性大分子通过化学交联
而构成三维网状结构的化学变化过程。
未硫化:线性,链间可自由移动,受到外力时,分子 链重心产生相对位移,表现出较大的变形与塑性流动; 具有可溶性。
硫化后:链间产生化学交联成网状结构,使相对运动 受到了限制,外力作用下,链重心不发生位移,即失 去了流动性;不能溶解,只能溶胀。
PPT文档演模板
橡胶硫化工艺
(三)硫化曲线及其参数
ML-最小转矩 ; MH-最大转矩; ΔM-最大与最小转矩差; M10= ML +10% ΔM M 90= ML +90% ΔM ;
TH-理论正硫化时间; T10-焦烧时间,M10对应的时间; T90- 工艺正硫化时间,M90对应的时间
PPT文档演模板
橡胶硫化工艺
(四)、理想硫化曲线
➢硫化诱导期足够大,充分保证生产加工的安 全性; ➢硫化速度要快,提高生产效率,降低成本; ➢硫化平坦期要长。
达到上述要求,必须正确选择硫化条件和硫化 体系。
PPT文档演模板
橡胶硫化工艺
三、正硫化及其测定方法
1、正硫化及正硫化时间
➢正硫化,又称最宜硫化,通常是指橡胶制品 性能达最佳值时的硫化状态。
诱 导 期 阶 段
交联 反应 阶段
促进剂
活化剂
硫磺
促进剂多硫化合物 橡胶
橡胶分子链的多硫化合物
分解 自由基(或离子)
橡胶
交联反应
网络 形成 阶段
交联重排、裂解、主链改性 硫化胶
第一阶段:诱导阶段
先是硫磺、活化剂、促进 剂相互作用,使活化剂在 胶料中溶解度增加,活化 促进剂,使促进剂与硫磺 之间反应生成一种活性更 大的中间产物;然后进一 步引发橡胶分子链产生可 交联的橡胶大分子自由基。
橡胶硫化工艺
4、过硫化阶段
曲线继续上升,结构化作
用所致,通常非硫磺硫化
的SBR、NBR、CR、 E保PM持等较都长可平能坦出期现,这通种常现 象用硫磺硫化的SBR、
NBR、EPDM等都会出
d以后部分,相当于硫化反 现这一现象。
应中网络形成的后期,存在 曲线下降,网络裂解所 交联键的重排、交联键和链 致,NR的普通硫磺硫化 段的热裂解反应。不同的胶 是最典型的例子。 料,表现不同。
二、橡胶硫化历程
(一)橡胶硫化反应过程 硫化反应是一个由多元组份参与的复杂的化 学反应过程,它包含橡胶分子与硫化剂及其 它配合剂之间发生的一系列化学反应。
在形成网状结构时伴随着发生各种副反应。 其中橡胶与硫化剂的反应占主导地位,它是 形成空间网络的基本反应。
PPT文档演模板
橡胶硫化工艺
含促进剂、硫磺的橡胶硫化历程:
➢正硫化时间是指达到正硫化状态所需时间。 ➢实际上正硫化时间是一个范围,不是一个点,
一般在平坦硫化阶段选取。 ➢处于正硫化前期(欠硫)或后期(过硫)状
态,硫化胶物性都较差。
PPT文档演模板
橡胶硫化工艺
由于理论与实际的差别,在实际生产中所采用 的正硫化时间与理论上的正硫化时间并不一致, 通常正硫化时间包括理论正硫化时间、工艺正 硫化时间和工程正硫化时间三个概念。
PPT文档演模板
橡胶硫化工艺
硫化是橡胶制品加工的主要工艺过程之一,也 是橡胶制品生产中的最后一个加工工序。
橡胶经历了一系列复杂的化学变化,由塑性的 混炼胶变为高弹性的或硬质的交联橡胶,从而 获得更完善的物理机械性能和化学性能,提高 和拓宽了橡胶材料的使用价值和应用范围。。
PPT文档演模板
橡胶硫化工艺
PPT文档演模板
橡胶硫化工艺
Ø 理论正硫化时间:指硫化曲线上达到 最大转矩时所对应的硫化时间;
Ø 工艺正硫化时间:指硫化曲线上M90 所对应的硫化时间,即T90;
Ø 二者都是有硫化曲线得到的。
PPT文档演模板
橡胶硫化工艺
Ø 胶料各项性能在某一时间不可能都处于最佳 值,必须综合考虑,生产上根据某些主要指 标来选择正硫化时间,具有工程实际意义, 称为工程正硫化时间。
PPT文档演模板
橡胶硫化工艺
诱
促进剂
活化剂
导
硫磺
第二阶段:交联反应阶段
期 阶 段
交联 反应 阶段
促进剂多硫化合物 橡胶
橡胶分子链的多硫化合物 分解
自由基(或离子) 橡胶
交联反应
可交联的自由基或 离子与橡胶分子链 产生反应,生成交 联键。
网络 交联重排、裂解、主链改性 形成
阶段
硫化胶
PPT文档演模板橡胶硫化工艺 导促进剂活化剂
硫磺 第三阶段:网络形成阶段
期 阶
促进剂多硫化合物 橡胶
此阶段的前期交联反应
段 橡胶分子链的多硫化合物 已趋完成,初始形成的
交联 反应
分解
自由基(或离子) 交联键发生短化、重排 橡胶
阶段
交联反应
和裂解反应,最后网络
网络 交联重排、裂解、主链改性 趋于稳定,获得性能稳
形成 阶段
硫化胶
定的硫化胶。
PPT文档演模板
橡胶硫化工艺
(二)、硫化历程图
在硫化过程中橡胶的各种性能都随 着时间增加而发生变化,若将橡胶 的某一项性能的变化与对应的硫化 时间作图,则可得到一个曲线图形, 从这种曲线图形中可显示出胶料的 硫化历程,称为硫化历程图,也称 硫化曲线。 反映的是胶料在一定硫化温度下, 转矩(模量)随硫化时间的变化。
PPT文档演模板
橡胶硫化工艺
工业上从硫化工艺控制角度考虑将硫化曲线分为四 个阶段,即焦烧阶段、热硫化阶段、平坦硫化阶段 和过硫化阶段。
PPT文档演模板
橡胶硫化工艺
1、焦烧阶段
ab段,相当于硫化反应中的诱导期,对应焦烧时 间。焦烧时间的长短是由胶料配方所决定的,其中 主要受促进剂的影响,胶料在操作过程中的受热历 程也是一个重要影响因素。
PPT文档演模板
橡胶硫化工艺
2、热硫化阶段
bc段,相当于硫化反应中 的交联反应阶段,胶料发生 交联反应,逐渐生成网状结 构,胶料的转矩或强度等性 能急剧上升。
➢斜率大小代表硫化反应速率的快慢,斜率越大,硫 化反应速度越快,生产效率越高。 ➢热硫化时间的长短取决于硫化温度和胶料配方,通 常温度越高,促进剂用量越多,硫化速度越快。