玻璃钢拉挤成型中在脱模剂的使用
玻璃钢拉挤成型工艺以及玻璃钢拉挤成型工艺产品的应用

玻璃钢拉挤成型工艺以及玻璃钢拉挤成型工艺产品的应用玱璃钢拉挤成型工艺以及玱璃钢拉挤成型工艺产品的应用玱璃钢拉挤成型工艺目前已经成为新型产业群,产品具有耐腐蚀性强,能耐各种稀酸、碱、盐介质的腐蚀等特点,阻燃性好,潍坊科林环保已经经国家与业测试机构检测,材料的氧指数可达到28%以上。
可放心选购。
一、工艺及控制1、拉挤工艺拉挤成型工艺过程是由送纱、浸胶、预成型、固化定型、牵引、切断等工序组成。
无捻粗纱从纱架引出后,经过导纱装置进入树脂槽浸透树脂胶液,然后进入预成型模,将多余树脂和气泡排出,再进入成型模凝胶、固化。
固化后的制品由牵引机连续不断地从模具拉出,最后由切断机定长切断。
拉挤成型工艺中除立式和卧式机组外,尚有弯曲形制品拉挤成型工艺,反应注射拉挤工艺等。
增强热塑性塑料拉挤工艺在最近几年也取得了一定的突破。
最近美国道化学公司采用聚氨酯不玱纤经过拉挤制成强度、韧性、抗损伤性能均很优良的型材。
其拉挤速度可达到热固性塑料拉挤速度的10倍。
2、工艺控制拉挤成型工艺控制的参数主要包括成型温度、固化时间、牵引张力及牵引速度等。
(1)成型温度在拉挤成型过程中,材料在穿越模具时发生的变化是最关键的。
玱璃纤维浸胶后通过加热的金属模具,一般将连续拉挤过程分为预热区、胶凝区和固化区。
在模具上使用加热板戒加热套来加热。
树脂在加热过程中,温度逐渐升高,粘度降低。
通过预热区后,树脂体系开始胶凝、固化,在固化区内产品受热继续固化,以保证出模时有足够的固化度。
模具的加热条件是根据树脂体系来确定的。
以聚酯树脂配方为例,一般来讲,模具温度应大于树脂的放热峰值,温度上限为树脂的降解温度。
温度、胶凝时间、拉速应当匹配。
预热区温度可以较低,胶凝区不固化区温度相似。
温度分布应使产品固化放热峰出现在模具中部靠前,胶凝固化分离点应控制在模具中部。
温度梯度不宜过大。
(2)拉挤速度的确定拉挤模具的长度一般为0.6-1.2m。
在一定的温度条件下,树脂体系的胶凝时间对工艺参数速度的确定是非常重要的。
脱模剂的使用方法
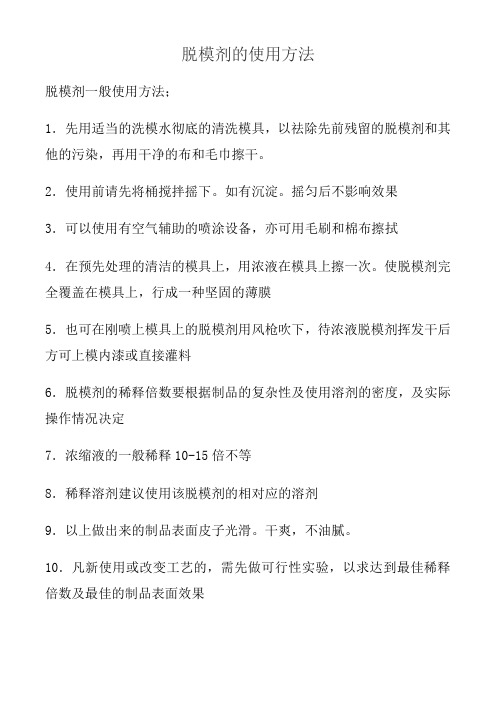
脱模剂的使用方法
脱模剂一般使用方法;
1.先用适当的洗模水彻底的清洗模具,以祛除先前残留的脱模剂和其他的污染,再用干净的布和毛巾擦干。
2.使用前请先将桶搅拌摇下。
如有沉淀。
摇匀后不影响效果
3.可以使用有空气辅助的喷涂设备,亦可用毛刷和棉布擦拭
4.在预先处理的清洁的模具上,用浓液在模具上擦一次。
使脱模剂完全覆盖在模具上,行成一种坚固的薄膜
5.也可在刚喷上模具上的脱模剂用风枪吹下,待浓液脱模剂挥发干后方可上模内漆或直接灌料
6.脱模剂的稀释倍数要根据制品的复杂性及使用溶剂的密度,及实际操作情况决定
7.浓缩液的一般稀释10-15倍不等
8.稀释溶剂建议使用该脱模剂的相对应的溶剂
9.以上做出来的制品表面皮子光滑。
干爽,不油腻。
10.凡新使用或改变工艺的,需先做可行性实验,以求达到最佳稀释倍数及最佳的制品表面效果。
我国玻璃钢拉挤成型工艺、产品应用及(精)

我国玻璃钢拉挤成型工艺、产品应用及现状一、概述拉挤成型工艺是将浸透胶液的连续无捻粗纱、毡、带或布等增强材料,在牵引力的作用下,通过模具加热挤拉成型、固化,连续不断地生产长度不限的玻璃钢型材。
2008年,拉挤成型工艺用不饱和聚酯树脂消费量4万吨,过氧化物消费量约为600吨。
拉挤成型工艺是玻璃钢成型工艺中的一种特殊工艺,适于生产各种断面形状的玻璃钢型材,如棒、管、实体型材(工字形、槽形、方形型材)和空腹型材等。
其优点是:1、生产过程连续进行,制品质量稳定,重复性好;2、增强材料含量可根据要求进行调整,产品强度高;3、能够调整制品的纵向强度和横向强度,满足不同的使用要求;4、能够生产截面形状复杂的制品,满足特殊场合使用的要求;5、制品具有良好的整体性,原材料的利用率高;6、设备的投资费用低。
二、拉挤工艺用原材料1、树脂基体在拉挤工艺中,应用最多的是不饱和聚酯树脂,还有环氧树脂、乙烯基树脂、热固性甲基丙烯酸树脂、改性酚醛树脂、阻燃性树脂等。
(1不饱和聚酯树脂用作拉挤的基本上是邻苯和间苯型。
间苯型树脂有较好的力学性能、坚韧性、耐热性和耐腐蚀性能。
目前国内使用的较多的是邻苯型,因其价格较间苯型有优势,但质量因生产厂家不同差距较大,使用时要根据不同的产品慎重选择。
(2乙烯基树脂乙烯基树脂具有较好的综合性能,可提高耐化学性能和耐水解稳定性。
(3环氧树脂环氧树脂和不饱和聚酯树脂、酚醛树脂相比,具有优良的力学性能、高介电性能、耐表面漏电、耐电弧,是优良绝缘材料。
(4酚醛树脂它是最早的一类热固性树脂。
具有突出的瞬时耐高温烧蚀性能,目前酚醛树脂已成功应用在拉挤成型工艺中。
2、增强材料拉挤工艺用的增强材料主要是玻璃纤维及其制品,如无捻粗纱、玻璃纤维毡等。
为了满足制品的特殊性能要求,可用芳纶纤维、碳纤维、超高分子量聚乙烯纤维及玄武岩纤维等。
(1玻璃纤维用于拉挤工艺的玻璃纤维主要有无碱、中碱和高强玻璃纤维。
玻璃纤维制品的品种有:①无捻粗纱无捻粗纱有并股纱和直接纱,线密度为1100(1200)号到4400(4800)号。
复合材料-拉挤成型工艺-(综合版改)

复合材料拉挤成型工艺——纺硕1205班柴寅芳、丁倩、刘冰、刘小梅、戎佳琦、王卷1 拉挤成型定义拉挤成型是指玻璃纤维粗纱或其织物在外力牵引(外力拉拔和挤压模塑)下,经过浸胶、挤压成型、加热固化、定长切割,连续生产长度不限的玻璃钢线型制品的一种方法。
这种工艺最适于生产各种断面形状的型材,如棒、管、实体型(工字形、槽形、方形型材)和空腹型材(门窗型材、叶片)等。
2 拉挤成型的特点2.1优点:1)典型拉挤速度0.5-2m/min,效率高,适于批量生产,制造长尺寸制品;2)树脂含量可精确控制;3)主要用无捻粗纱增强,原材料成本低,多种增强材料组合使用,可调节制品力学性能;4)拉挤制品中纤维含量可高达80%,浸胶在张力下进行,能充分发挥连续纤维的力学性能,产品强度高;5)原材料利用率在95%以上,废品率低;6)制品纵、横向强度可任意调整,可以满足不同力学性能制品的使用要求。
2.2缺点:1)不能利用非连续增强材料;2)产品形状单调,只能生产线形型材(非变截面制品),横向强度不高;3)模具费用较高;4)一般限于生产恒定横截面的制品。
3 拉挤成型所需的材料拉挤成型工艺中使用的材料包括树脂、增强材料、辅助材料等。
3.1拉挤成型工艺所用树脂拉挤成型工艺要求所用的树脂黏度低,主要使用不饱和聚酯树脂和环氧树脂或改性环氧树脂。
不饱和聚酯树脂用作拉挤的基本上是邻苯和间苯型。
间苯型树脂有较好的力学性能、坚韧性、耐热性和耐腐蚀性能。
目前国内使用的较多的是邻苯型,因其价格较间苯型有优势。
环氧树脂和不饱和聚酯树脂相比,具有优良的力学性能、高介电性能、耐表面漏电、耐电弧,是优良绝缘材料。
常用拉挤工艺用树脂如表1所示,树脂生产配方如表2和表3。
表1拉挤工艺用树脂表2典型拉挤用不饱和聚酯树脂配方树脂 196 100份填料(轻质碳酸钙)脱模剂(硬脂酸锌)固化剂(过氧化物)低收缩剂(PVC树脂)颜料5~15份3~5份1~3份5~15份0.1~1份表 3环氧树脂配方环氧树脂 E-55脱模剂(硬脂酸锌)固化剂(590#)增韧剂100份3~5份15~20份10~15份适量稀释剂3.2拉挤成型工艺所用增强材料拉挤成型玻璃钢所用的纤维增强材料,主要是 E 玻璃纤维无捻粗纱居多,其优点是不产生悬垂现象,集束性好,易被树脂浸透,力学性能较高。
脱模剂的种类及使用方法

脱模剂的种类及使用方法无论是新配制的模板,还是已用并清除了污、锈待用的模板,在使用前必须涂刷脱模剂。
因此,脱模剂是混凝土模板不可缺少的辅助材料。
1脱模剂的种类和配制混凝土模板所用脱模剂大致可分为油类、水类和树脂类三种。
1.油类脱模剂(1)机柴油用机油和柴油按3:7(体积比)配制而成。
(2)乳化机油先将乳化机油加热至50~60℃,将磷质酸压碎倒入已加热的乳化机油中搅拌使其溶解,再将60~80℃的水倒入,继续搅拌至乳白色为止,然后加入磷酸和苛性钾溶液,继续搅拌均匀。
(3)妥尔油用妥尔油:煤油:锭子油=1:7.5:1.5配制(体积比)。
(4)机油皂化油用机油:皂化油:水=1:1:6(体积比)混合,用蒸汽拌成乳化剂。
2.水性脱模剂主要是海藻酸钠。
其配制方法是:海藻酸钠:滑石粉:洗衣粉:水=1:13.3:1:53.3(重量比)配合而成。
先将海藻酸钠浸泡2~3d,再加滑石粉、洗衣粉和水搅拌均匀即可使用,刷涂、喷涂均可。
3.树脂类脱模剂为长效脱模剂,刷一次可用6次,如成膜好可用到10次。
甲基硅树脂用乙醇按作固化剂,重量配合比为1000:3~5。
气温低或涂刷速度快时,可以多掺一些乙醇钱;反之,要少掺。
2使用注意事项1.油类脱模剂虽涂刷方便,脱模效果也好,但对结构构件表面有一定污染,影响装饰装修,因此应慎用。
其中乳化机油,使用时按乳化机油:水=1:5调配(体积比),搅拌均匀后涂刷,效果较好。
2.油类脱模剂可以在低温和负温时使用。
3.甲基硅树脂成膜固化后,透明、坚硬、耐磨、耐热和耐水性能都很好。
涂在钢模面上,不仅起隔离作用,也能起防锈、保护作用。
该材料无毒,喷、刷均可。
配制时容器工具要干净,无锈蚀,不得混入杂质。
工具用毕后,应用酒精洗刷干净晾干。
由于加入了乙醇钱易固化,不宜多配。
故应根据用量配制,用多少配多少。
当出现变稠或结胶现象时,应停止使用。
甲基硅树脂与光、热、空气等物质接触都会加速聚合,应贮存在避光、阴凉的地方,每次用过后,必须将盖子盖严,防止潮气进入,贮存期不宜超过三个月。
模具脱模剂使用方法
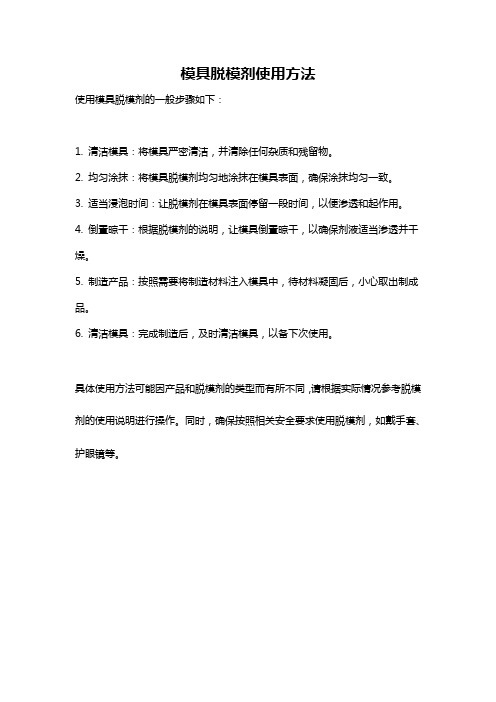
模具脱模剂使用方法
使用模具脱模剂的一般步骤如下:
1. 清洁模具:将模具严密清洁,并清除任何杂质和残留物。
2. 均匀涂抹:将模具脱模剂均匀地涂抹在模具表面,确保涂抹均匀一致。
3. 适当浸泡时间:让脱模剂在模具表面停留一段时间,以便渗透和起作用。
4. 倒置晾干:根据脱模剂的说明,让模具倒置晾干,以确保剂液适当渗透并干燥。
5. 制造产品:按照需要将制造材料注入模具中,待材料凝固后,小心取出制成品。
6. 清洁模具:完成制造后,及时清洁模具,以备下次使用。
具体使用方法可能因产品和脱模剂的类型而有所不同,请根据实际情况参考脱模剂的使用说明进行操作。
同时,确保按照相关安全要求使用脱模剂,如戴手套、护眼镜等。
玻璃钢制作工艺简介
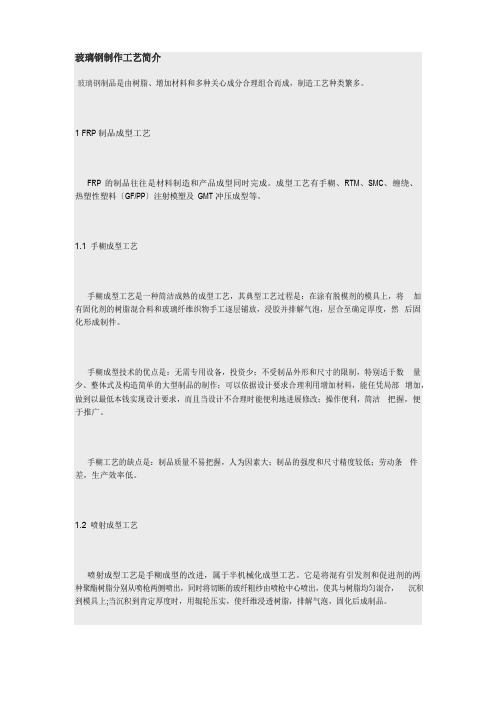
玻璃钢制作工艺简介玻璃钢制品是由树脂、增加材料和多种关心成分合理组合而成,制造工艺种类繁多。
1FRP 制品成型工艺FRP 的制品往往是材料制造和产品成型同时完成。
成型工艺有手糊、RTM、SMC、缠绕、热塑性塑料〔GF/PP〕注射模塑及GMT 冲压成型等。
1.1手糊成型工艺手糊成型工艺是一种简洁成熟的成型工艺,其典型工艺过程是:在涂有脱模剂的模具上,将加有固化剂的树脂混合料和玻璃纤维织物手工逐层铺放,浸胶并排解气泡,层合至确定厚度,然后固化形成制件。
手糊成型技术的优点是:无需专用设备,投资少;不受制品外形和尺寸的限制,特别适于数量少、整体式及构造简单的大型制品的制作;可以依据设计要求合理利用增加材料,能任凭局部增加,做到以最低本钱实现设计要求,而且当设计不合理时能便利地进展修改;操作便利,简洁把握,便于推广。
手糊工艺的缺点是:制品质量不易把握,人为因素大;制品的强度和尺寸精度较低;劳动条件差,生产效率低。
1.2喷射成型工艺喷射成型工艺是手糊成型的改进,属于半机械化成型工艺。
它是将混有引发剂和促进剂的两种聚酯树脂分别从喷枪两侧喷出,同时将切断的玻纤粗纱由喷枪中心喷出,使其与树脂均匀混合,沉积到模具上;当沉积到肯定厚度时,用辊轮压实,使纤维浸透树脂,排解气泡,固化后成制品。
喷射成型的优点是:用玻纤粗纱代替织物,可降低材料本钱;生产效率比手糊的高2~4倍;产品整体性好,无接缝,层间剪切强度高,树脂含量高,耐腐蚀、耐渗漏性好;产品尺寸、外形不受限制。
喷射成型的缺点是:树脂含量高,制品强度低;产品只能做到单面光滑;污染环境,有害工人安康。
1.3SMC 及BMC 成型工艺片状模塑料〔Sheet Molding Comp,SMC〕和团状模塑料〔Bulk Molding Compoun,BMC〕是由树脂糊浸渍纤维或短切纤维毡,两边掩盖聚乙烯薄膜而制成的一类片状模压料,属于预浸毡料范围。
使用时,将两面的薄膜撕去,按制品的尺寸裁剪、叠层,放入金属模具中加温加压,即得所需要的制品。
拉挤成型玻璃钢脱模剂的应用
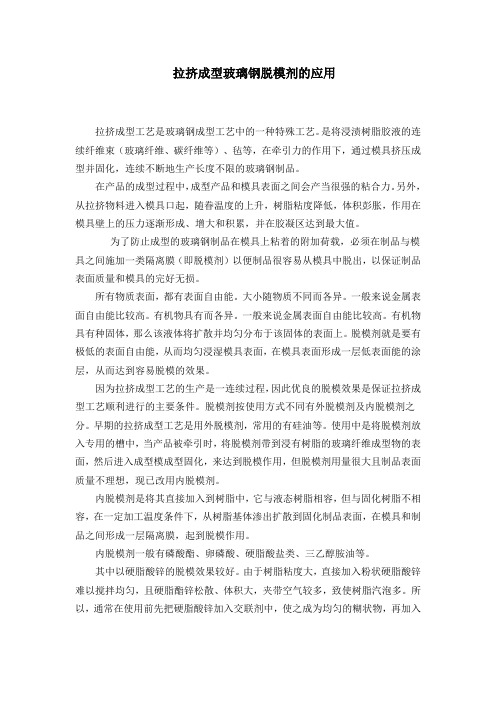
拉挤成型玻璃钢脱模剂的应用拉挤成型工艺是玻璃钢成型工艺中的一种特殊工艺。
是将浸渍树脂胶液的连续纤维束(玻璃纤维、碳纤维等)、毡等,在牵引力的作用下,通过模具挤压成型并固化,连续不断地生产长度不限的玻璃钢制品。
在产品的成型过程中,成型产品和模具表面之间会产当很强的粘合力。
另外,从拉挤物料进入模具口起,随眷温度的上升,树脂粘度降低,体积彭胀,作用在模具壁上的压力逐渐形成、增大和积累,并在胶凝区达到最大值。
为了防止成型的玻璃钢制品在模具上粘着的附加荷载,必须在制品与模具之间施加一类隔离膜(即脱模剂)以便制品很容易从模具中脱出,以保证制品表面质量和模具的完好无损。
所有物质表面,都有表面自由能。
大小随物质不同而各异。
一般来说金属表面自由能比较高。
有机物具有而各异。
一般来说金属表面自由能比较高。
有机物具有种固体,那么该液体将扩散并均匀分布于该固体的表面上。
脱模剂就是要有极低的表面自由能,从而均匀浸湿模具表面,在模具表面形成一层低表面能的涂层,从而达到容易脱模的效果。
因为拉挤成型工艺的生产是一连续过程,因此优良的脱模效果是保证拉挤成型工艺顺利进行的主要条件。
脱模剂按使用方式不同有外脱模剂及内脱模剂之分。
早期的拉挤成型工艺是用外脱模剂,常用的有硅油等。
使用中是将脱模剂放入专用的槽中,当产品被牵引时,将脱模剂带到浸有树脂的玻璃纤维成型物的表面,然后进入成型模成型固化,来达到脱模作用,但脱模剂用量很大且制品表面质量不理想,现已改用内脱模剂。
内脱模剂是将其直接加入到树脂中,它与液态树脂相容,但与固化树脂不相容,在一定加工温度条件下,从树脂基体渗出扩散到固化制品表面,在模具和制品之间形成一层隔离膜,起到脱模作用。
内脱模剂一般有磷酸酯、卵磷酸、硬脂酸盐类、三乙醇胺油等。
其中以硬脂酸锌的脱模效果较好。
由于树脂粘度大,直接加入粉状硬脂酸锌难以搅拌均匀,且硬脂酯锌松散、体积大,夹带空气较多,致使树脂汽泡多。
所以,通常在使用前先把硬脂酸锌加入交联剂中,使之成为均匀的糊状物,再加入到树脂之中。
- 1、下载文档前请自行甄别文档内容的完整性,平台不提供额外的编辑、内容补充、找答案等附加服务。
- 2、"仅部分预览"的文档,不可在线预览部分如存在完整性等问题,可反馈申请退款(可完整预览的文档不适用该条件!)。
- 3、如文档侵犯您的权益,请联系客服反馈,我们会尽快为您处理(人工客服工作时间:9:00-18:30)。
玻璃钢拉挤成型中在脱模剂的使用
在产品的成型过程中,成型产品和模具表面之间会产当很强的粘合力。
另外,从拉挤物料进入模具口起,随着温度的上升,树脂粘度降低,体积彭胀,作用在模具壁上的压力逐渐形成、增大和积累,并在胶凝区达到最大值。
为了防止成型的玻璃钢制品在模具上粘着的附加荷载,必须在制品与模具之间施加一类隔离膜(即脱模剂)以便制品很容易从模具中脱出,以保证制品表面质量和模具的完好无损。
所有物质表面,都有表面自由能。
大小随物质不同而各异。
一般来说金属表面自由能比较高。
有机物也是一种固体,那么该液体将扩散并均匀分布于该固体的表面上。
脱模剂就是要有极低的表面自由能,从而均匀浸湿模具表面,在模具表面形成一层低表面能的涂层,从而达到容易脱模的效果。
因为拉挤成型工艺的生产是一连续过程,因此优良的脱模效果是保证拉挤成型工艺顺利进行的主要条件。
脱模剂按使用方式不同有外脱模剂及内脱模剂之分。
早期的拉挤成型工艺是用外脱模剂,常用的有硅油等。
使用中是将脱模剂放入专用的槽中,当产品被牵引时,将脱模剂带到浸有树脂的玻璃纤维成型物的表面,然后进入成型模成型固化,来达到脱模作用,但脱模剂用量很大且制品表面质量不理想,现已改用内脱模剂。
内脱模剂的选择内脱模剂是将其直接加入到树脂中,它与液态树脂相容,但与固化树脂不相容,在一定加工温度条件下,从树脂基体渗出扩散到固化制品表面,在模具和制品之间形成一层隔离膜,起到脱模作用。
内脱模剂一般有磷酸酯、卵磷酸、硬脂酸
盐类、三乙醇胺油等。
其中以硬脂酸锌的脱模效果较好。
由于树脂粘度大,直接加入粉状硬脂酸锌难以搅拌均匀,且硬脂酯锌松散、体积大,夹带空气较多,致使树脂汽泡多。
所以,通常在使用前先把硬脂酸锌加入交联剂中,使之成为均匀的糊状物,再加入到树脂之中。
使用硬脂酸锌作内脱模剂对制品的颜色、固化速度及树脂粘度均无显著影响。
在拉挤生产中,通常更愿意使用在常温下为液体状的内脱模剂。
目前市售的内脱模剂多为伯胺、仲胺和有机磷酸与脂肪酯共聚体的混合物。
液体状内脱模剂在拉挤工艺上有许多优点:1、很容易在树脂中分散;2、有清洁模具的作用;3、能保护金属模具使其免受腐蚀;4、在降低拉挤阻力、减少模具损耗的同时提高生产效率;5、能降低树脂混合物的表面张力,降低树脂粘度,改善树脂对增强材料、填料的浸润性,改善树脂的流动性;6、辅助消泡及改进部件的表面质量,使制品表面光洁;7、不影响树脂的固化特性,不改变混合树脂的适用期,不影响制品的物理力学性能,不影响制品的耐候性等。
脱模剂使用中注意的问题由于大多数液体状内脱模剂都是酸性的,所以在使用中要注意以下问题:1、在使用对酸敏感的颜料时会导致颜色变化;2、在使用碱性填料时,如碳酸钙,酸性脱模剂会与之起反应,引起混合料的粘度增加,但不会影响脱模效果;3、如果填料为氢氧化铝,酸性脱模剂除了会使混合料的粘度增加外,还会在混合料固化过程中放出水份,导致气泡、裂纹等问题。
通常,内脱模剂的起始用量为树脂量的1%,有效添加范围是基于树脂重量的0.75-2%。
应根据实际情况适当调
整。
1、薄壁的简单型材,用量可以适当少些,比如0.8%或更少;2、厚壁或形状复杂的型材需要多加一些。
3、在高填料体系内,应提高内脱模剂的添加量,但内脱模剂添加量过多,会延迟固化。
4、在拉挤生产中,如果阻力过大又找不到原因时,就需要适当增加脱模剂用量。
在使用时应注意加料顺序,在混合时应在加入固化剂、填料和其它树脂添加剂之前,将内脱模剂加树脂体系中并混合均匀。
这样可以达到最佳的脱模效果。