精益生产五大指标
精益生产衡量指标计算方法

库存周转期和周转率
原材料的库存周转期(天)=30天/原材料的库存周 转率; 原材料的库存周转率=2×当月原材料的出库金额 总和/(月期初原材料库存金额总和+月期末原材料 库存金额总和);
成品的库存周转期(天)=30天/成品的库存周转率; 成品的库存周转率=2×当月成品的出库金额总和/ (月期初成品库存金额总和+月期末成品库存金额 总和);
BTS计算方法
Volume%产量性能用于监控生产计划完成情况 Volume%=实际生产数量/计划生产数量; 混线性能Mix%用于测量在厂内制造的产品系/ 型号/类型等在适当的生产日的完成比率。 Mix%=实际生产品种数/计划生产品种数;
顺序性能Sequence%用于测量在适当的生产日 按照正确的生产顺序完成生产任务的比率 Sequence%=按计划顺序生产品种数/计划生产品 种数;
A B
90
100-10 (補修+報廢) /100 = .90 一次合格產出
6
100
100-16 (補修+報廢) /17 5
90-12 (補修+報廢) /90 = .86 一次合格產出
R
K
報廢 2
D
87-7 (補修+報廢) /87 = .91 一次合格產出
報廢品
生产周期
计算一批(1000件)产品需要的生产时间;
设备总效率OEE
OEE = 设备利用率 x 作业效率 x 良品率 對象: 瓶颈工程/產能較不足之工程
设备利用率
稼动率=设备实际作业时间/设备可用时间 可用时间:指设备可以利用的时间, 设备可用时间=(设备计划运行时间-固定 的休息/停机时间)设备实际作业时间=每天 设备实际工作时间之和 举例:甲班全天出勤时间为8小时,中途休息时 间为20分钟,设备故障停机修理时间为40分钟 设备稼动率=(8x60-20-40)/(8x60-20)
精益生产五大指标

5、 DTD:Dock to Dock有效生产周期
• 定义:指从原材料到发运 产品之间的总运转时间间 隔;用于测量原材料转化 成成品发运的速度,也就 是通过工厂的速度,而不 是加工工艺的速度。
Ó ¶ Ð Á È µ ò º
1、BTS:Build To Schedule生产计划完成率
定义:BTS是在指定的生产日按照正确的生产 顺序完成生产计划的比例情况。 是三个(总的数量是否满足符合性、品种是否 满足符合性、顺序是否满足符合性)不同的计 算值的乘积;
作用:用来显示工厂、生产线 以正确顺序、在正确时间、产出 正确产品的执行程度 。
每天客户需求数量
例子:
节拍时间 = (60 x 17.0) - ((15+15+30+20)x2) 258 件 860 分钟 x 60 秒/分 258 件 = = 860 分钟 258 件
ABC 装配线 节拍时间
=
200 秒/件
争取使每一工位每3分20秒生产一件合格品
需要多少操作工?
• The number of operator is calculated by dividing the sum of the operator work ( value added + non value added )by the Module Takt Time • 操作工的数量等于总的单件产品的人工工 作量除以单条生产线之节拍时间
精益生产五大指标
1、BTS:Build To Schedule 生产计划完成率 2、FTT:First Time Through 首次通过率 (一次交验合格率) 3、OEE:Overall Equipment Effectiveness 设备综合利用率 4、TT:TAKT Time 节拍时间 5、DTD:Dock to Dock 有效生产周期
精益生产基础知识

精益基础知识1、精益生产:仅在最少可能的时间内,以最小可能的资源,生产最少的必要单位,为客户创造价值2、精益生产追求的7个“零”目标是什么?(1)“零”转产工时浪费(Products•多品种混流生产)(2)“零”库存(Inventory•消减库存)(3)“零”浪费(Cost•全面成本控制)(4)“零”不良(Quality•高品质)(5)“零”故障(Maintenance•提高运转率)(6)“零”停滞(Delivery•快速反应、短交期)(7)“零”灾害(Safety•安全第一)3、精益生产的五大原则1)价值:精确地确定客户愿为之付钱的产品价值点。
2)价值流:识别产品生产过程中价值的流动过程。
3)流动:使价值不间断的流动。
4)拉动:从客户一直到生产者形成需求拉动。
5)完美:永远追求尽善尽美4、精益生产与传统的大量生产方式对比具有哪些优点?对比项目单件生产方式大量生产方式精益生产方式产品特点完全按顾客要求标准化,品种单一品种多样化、系列化设备和工装通用、灵活、便宜专用、高效、昂贵柔性高、效率高作业分工粗略、丰富细致、简单、重复较粗略、多技能、丰富操作工要求较高操作技能不需要专业技能多技能库存水平高高低制造成本高低更低产品质量低高更高市场需求极少量需求物资缺乏、供不买方市场应求5、精益生产中的“5S”指的是什么?并指出它们之间的特点?整理:把物品区分要与不要,不要的东西坚决丢弃整顿:把整理好的物品明确规划定位并加以标识清扫:经常清洁打扫保持干净明亮的环境清洁:维持前3S成果使其规范化标准化素养:养成良好习惯,提高整体素质关系:●只有整理没有整顿,物品真难找得到;●只有整顿没有整理,无法取舍乱糟糟;●只有整理、整顿没清扫,物品使用不可靠;●3S之效果怎保证,清洁出来献一招;标准作业练修养,公司管理水平高6、精益生产中的七大浪费分别指什么?请列举您日常工作中所见的七大浪费具体表现各一条。
七大浪费:库存,过度加工,缺陷,多余动作,过量生产,等待,搬运●七大浪费1:库存的浪费表现:•准备过多的物料•不良品等待返工或更换•生产能力不足所造成的安全库存•生产计划临时变更造成物流停滞●七大浪费2:过量生产表现:•物流阻塞•库存、在制品增加•产品积压造成不良发生•材料、零件过早取得●七大浪费3:等待的浪费表现:•自动机器操作中,人员的“闲视”等待•作业充实度不够的等待•设备故障、材料不良的等待•生产安排不当的人员等待•上下工序间未衔接好造成的等待●七大浪费4:搬运的浪费表现:•搬运距离很远•主副线中的搬运•出入库次数多的搬运•破损、刮痕的发生●七大浪费5:多余动作的浪费表现:•步行、转身、弯腰;•动作停顿、幅度太大;•两手空闲、单手空闲、左右手交换;•动作重复。
通用汽车精益生产主要指标介绍

通用汽车精益生产主要指标介绍1. 引言•精益生产是一种通过优化生产流程和减少浪费来提高生产效率的方法论。
在汽车制造业中,精益生产被广泛应用,其积极影响了通用汽车(General Motors)的生产和经营。
•本文将介绍通用汽车精益生产中的三个主要指标,包括制造周期时间、首次通过率和责任分配的指标。
通过深入了解这些指标,我们可以了解通用汽车在精益生产方面的实践和取得的成果。
2. 制造周期时间•制造周期时间是指完成一个产品生产所需的总时间,包括原料采购、生产、装配、质量检验和物流等各个环节。
通用汽车通过优化供应链和生产过程,不断缩短制造周期时间来提高生产效率和客户满意度。
•通用汽车引入了精益生产的概念和方法,通过减少浪费、优化流程和提高生产柔性,使制造周期时间得以大幅减少。
通过实施精益生产,通用汽车在制造周期时间方面取得了显著的成就。
3. 首次通过率•首次通过率是指在生产过程中,产品在第一次质量检验中通过的比例。
通用汽车非常注重产品质量,通过提高首次通过率来降低质量问题的出现,从而减少返工和废品率,提高生产效率和降低成本。
•通用汽车实施了一系列措施,包括严格的质量控制标准、员工培训和自动化技术的应用等,以提高首次通过率。
通过不断改进和优化生产流程,通用汽车的首次通过率得到了显著提高,为客户提供了高质量的汽车产品。
4. 责任分配•在精益生产中,责任分配是指将任务和责任分配给适当的人员,以确保生产过程的高效运行。
通用汽车注重团队合作和员工参与,通过清晰的责任分配来提高生产效率和质量。
•通用汽车实施了一套完善的责任分配机制,包括明确的岗位职责、流程标准化和培训计划等。
通过将责任分配给具备相应技能和经验的员工,通用汽车确保了生产过程的顺利进行,并提高了生产效率和质量水平。
5. 总结•通用汽车在精益生产方面取得了显著的成就,得益于制造周期时间的缩短、首次通过率的提高和责任分配的优化。
这些主要指标的改善不仅提高了生产效率和质量水平,还使通用汽车更加具有市场竞争力。
某某汽车精益生产主要指标介绍
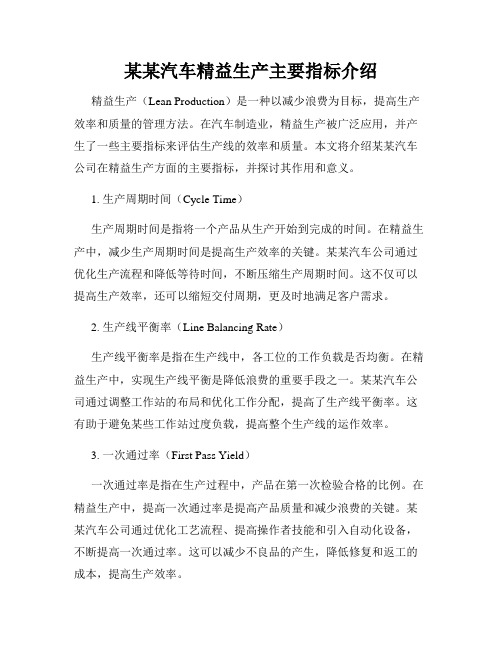
某某汽车精益生产主要指标介绍精益生产(Lean Production)是一种以减少浪费为目标,提高生产效率和质量的管理方法。
在汽车制造业,精益生产被广泛应用,并产生了一些主要指标来评估生产线的效率和质量。
本文将介绍某某汽车公司在精益生产方面的主要指标,并探讨其作用和意义。
1. 生产周期时间(Cycle Time)生产周期时间是指将一个产品从生产开始到完成的时间。
在精益生产中,减少生产周期时间是提高生产效率的关键。
某某汽车公司通过优化生产流程和降低等待时间,不断压缩生产周期时间。
这不仅可以提高生产效率,还可以缩短交付周期,更及时地满足客户需求。
2. 生产线平衡率(Line Balancing Rate)生产线平衡率是指在生产线中,各工位的工作负载是否均衡。
在精益生产中,实现生产线平衡是降低浪费的重要手段之一。
某某汽车公司通过调整工作站的布局和优化工作分配,提高了生产线平衡率。
这有助于避免某些工作站过度负载,提高整个生产线的运作效率。
3. 一次通过率(First Pass Yield)一次通过率是指在生产过程中,产品在第一次检验合格的比例。
在精益生产中,提高一次通过率是提高产品质量和减少浪费的关键。
某某汽车公司通过优化工艺流程、提高操作者技能和引入自动化设备,不断提高一次通过率。
这可以减少不良品的产生,降低修复和返工的成本,提高生产效率。
4. 库存周转率(Inventory Turnover)库存周转率是指在一定时间内,公司的库存发生的次数。
在精益生产中,降低库存周转率是减少库存占用成本和减少不必要的物流活动的关键。
某某汽车公司通过精确预测和规划需求,灵活调整供应链,优化库存管理,实现了库存周转率的提高。
这不仅能够减少库存积压,还能够降低资金占用成本,提高企业盈利能力。
5. 损失时间(Downtime)损失时间是指生产线因故障、维修和调整等原因而停工的时间。
在精益生产中,减少损失时间是提高生产效率的关键。
精益生产衡量指标知识

精益生产衡量指标的相关知识精益生产之七个“零”的目标﹕零不良零库存零切换零停滞零故障零伤害零浪费用于业绩度量的三大类指标:基于合格/不合格(计数型数据)的FTY/RTY度量指标;基于缺陷数据(计点型数据)的DPU/DPMO度量指标;基于平均值/标准差(连续型数据)的Z(西格玛水平)。
它们基本覆盖了对产品、服务、商务、管理等所有类型过程的度量。
FPY:First Pass Yield定义为:一次通过率。
(FPY是第一次通过率,一般针对一个工位)(与FTY是一个意思)FTY First Time Yield 首次通过率,就是一次通过检验的合格率,就是第一次就把事情做对,由没有经返工返修就通过的过程输出单位数而计算出的合格率。
生产过程投产1000个单位,第一个子过程产生废品40个单位,返工40个单位,即第一个子过程只有920个单位一次合格。
得到FTY=92%.FTT:First Time Throghut,指首次通过率是指一次性完成一个生产过程并且满足质量要求的零件的百分率,不包括报废,返工,再测试,下线修理或返回。
FTT 用于衡量制造过程的质量。
PFY(process final yield)定义为:最终合格率。
就是过程的最后合格率(不区分是否经过返工)过程最终的合格率通常是指通过检验的合格单位数占过程投产全部单位数的比例。
但是这种质量计算方法不能计算该过程的输出在通过最终检验前发生的返工、返修的损失.(也就是说:将返工后合格的产品也算进合格品率里面去了。
):RTY:Rolled Throughput Yield 当然是全过程通过率了(直通率)。
对一个串行生产过程,假定各过程彼此独立,则其流通合格率等于每个子过程FTY的乘积,表明由这些子过程串联构成的大过程的一次合格率。
一次交验合格率就只看一个环节,而直通率应该把前面环节都考虑。
比如说:一个产品有三个工序来完成,各个环节的合格率都是90%,那么交验合格率应该是90%,而直通率应该是90%*90%*90%=72.9%一般来说交验合格率是指最后一个环节。
精益生产的五大原理包括
精益生产的五大原理包括精益生产是一种管理和生产理念,旨在通过消除浪费并持续提高生产效率和质量,实现生产过程的精益化。
精益生产的五大原理包括价值、价值流、流动、生产拉动和追求卓越。
下面将对每个原则进行详细解释。
1. 价值(Value):精益生产的第一原理是确定和了解客户价值。
价值是指客户愿意为其付费的产品或服务的特征。
在精益生产中,价值是通过消除不必要的活动和步骤来实现的。
如果一个步骤不增加产品或服务的价值,那么它就被认为是浪费的,并应该被消除或减少。
2. 价值流(Value Stream):价值流是指整个产品或服务的物质和信息流动路径,从原材料采购到最终交付给客户的过程。
价值流图是分析产品或服务流程并识别浪费的有效工具。
通过减少在价值流中的浪费,可以提高产品或服务的交付时间和质量。
3. 流动(Flow):流动是指在生产过程中物料和信息的持续和顺畅传递。
在传统的批量生产中,产品在各个生产环节会积压和堆积,导致产能低下、生产周期长和库存堆积。
而精益生产通过优化价值流,实现了物料和信息的流动,减少了等待时间和浪费。
4. 生产拉动(Pull):生产拉动是指根据实际需求生产,避免过度生产和库存积压。
传统生产方式中,有大量的库存和预测式生产,这样很容易导致过剩的库存和浪费。
而精益生产通过建立由客户需求驱动的生产系统,根据订单及时生产,避免了超额生产和库存积压。
5. 追求卓越(Perfection):追求卓越的原则意味着精益生产是一个持续改进的过程。
在精益生产中,通过精益工具和方法,如持续改进、标准化工作、员工参与等,不断改进和提高生产效率和质量。
以此为基础,为了更好地满足客户需求,实现更高水平的效率和质量。
综上所述,精益生产的五大原则包括价值、价值流、流动、生产拉动和追求卓越。
这些原则帮助企业识别和消除浪费,优化生产过程,提高生产效率和质量。
通过执行这些原则,企业可以实现持续改进和创造更大的价值。
精益生产的五大原则和七大浪费
精益生产的五大原则和七大浪费简介精益生产是一种由日本丰田汽车公司引入的生产管理方法,旨在提高生产效率、降低成本,同时满足客户需求。
精益生产的核心理念是通过消除浪费,并着重于价值创造的过程,从而提高生产效率和质量。
本文将介绍精益生产的五大原则和七大浪费。
五大原则1.价值观念(Value)价值观念是精益生产的核心。
它强调只有为客户创造价值的活动才是有意义的。
所有的活动和决策都应围绕价值创造展开,同时减少或消除对于客户价值无意义的活动。
2.价值流(Value Stream)价值流包括产品或服务的所有步骤和流程,从原材料采购直到产品交付给客户。
精益生产强调识别和优化价值流的各个环节,以最大程度地提高价值创造效率和质量。
3.流程改善(Flow)流程改善是确保产品或服务在价值流中流动顺畅的关键。
通过优化和简化流程,减少等待时间和物料的运输,可以加快生产时间并降低成本。
4.拉动生产(Pull)拉动生产是一种以需求为驱动的生产方式。
它意味着只在真正需要时才开始生产产品,以防止过度生产和库存积压。
拉动生产可以通过实施Just-in-Time(JIT)生产和有效的供应链管理来实现。
5.追求完美(Perfection)精益生产提倡不断追求完美和持续改进的精神。
它鼓励员工参与到问题解决和改进过程中,通过学习和实践来不断提高生产效率和质量。
七大浪费1.运输浪费运输浪费是指物料、产品或信息在生产过程中被频繁搬运、转移或传输的现象。
它会导致生产周期延长、运营成本增加,并容易造成损坏或丢失。
2.库存浪费库存浪费是指过多的库存造成的资源浪费。
过多的库存会占用资金,增加仓储成本,而且容易导致过期、损坏或过时的产品。
3.动作浪费动作浪费是指生产过程中不必要的动作或额外的劳动。
例如,多次处理、重复操作、不必要的检查等,都会增加成本和生产时间。
4.等待浪费等待浪费是指生产过程中由于前一道工序的延迟导致的等待时间。
等待时间会降低生产效率,增加生产周期和成本。
精益生产5大指标
实际 生产
率
Байду номын сангаас
OEE
24
97.87%
465
455
97.85% 1.3 350 80.29% 76.89%
实际运行时间=生产计划时间-停 工时间
OEE=可动率×实际生产率×首次通过率
停工时间=工具更换、调整、故障停 止、上下流等待、质量维持、确认
、工件不良、操作失误、作业缓滞
停止等时间
4. 实际节拍时间 5.生产周 (分钟/件)TT 期DTD
精
1.生产计划完成率BTS
产品
日期
日计 划产
量
实际 生产
产量 绩效
依照计 划品种 生产量
品种绩 效
按照计 划顺序 生产量
顺序 绩效
BTS
A
实例 281 281 100.00% 271 96.44% 261 96.31% 92.88%
BTS = 产量绩效 × 品种绩效 × 顺序绩效
= 实际生产量 × 依照计划品种的生产量
TAKT=实际运行时间/生 A产品从原材到成品
产计划运行时间
各个过程时间之和
1.619217082
首次通过率
计划生产量
实际生产量
× 实际依照顺序生产的数量 依照计划品种生产的数量
停工时间 止、上下流等 、工件不良、
精益生产五大指标
2.首次通过 率FTT
3.设备综合利用率OEE
报 废
返 修
FTT=返修 率*报废率
生产计划运 行时间(分
钟)
实际运行 时间(分
钟)
可动 率
理论加 工周期 (分钟 /件)
理论 生产 总量
通用汽车精益生产主要指标介绍
2024/6/30
27
例子
方案A:
过程#1 = P1 ;过程#2 = P2 ;……过程#= Pn 第一季度91天的可利用时间小时数是2184; n = 过程数; 直接时间能力利用 可用时间 = 2184 × n 91天的总直接时间小时数 = S.T.P1 + S.T.P2 ……+ S.T.Pn 直接时间能力利用 = 总的直接时间小时数/可用小时数 计划维修,加班时间和闲置时间能力利用来的计算方法重 复即可。
应用/信息
• 设备能力利用的计算应考虑在每个要汇报的工厂 中所有的生产过程/设备,可以考虑加权,以 更 真实地反应设备的利用状况。
• 当总计几个工厂或部门时,有必要考虑根据预计 更换价值对每个工厂和部门进行加权。不应使用 所有的其它加权方法(例如:使用直接劳力方 法)。把资金密集的单一的过程与多个低成本过 程简单相加,将曲解其真实的设备能力利用率, 这种状况更显加权的重要。
2024/6/30
29
通用汽车精益生产 DMS--主要指标6
生产率
2024义: 是指在一段时间内发出产品的总工时数与这段时间内总工 作小时数的比值.
• 目的:在工厂,部门,小组的水平上,用作判断一段时间内生产率 提高速率的工具,是年度值。
• 公式: 生产率 = 总发货工时数 (到客户) /总工作小时数(薪金人员和直 接人员)(包括加班工时)
100点/小时 或 • 标准工时/件=时间/件(小时)=0.03945 小 时/件.(例) • 总发货工时 = (36,370 件/月*0.03945小时 /件)= 1434运送小时/月.
×100 – 闲置时间比率%=(停工时间小时数/可利用时间)×100 – 总的比率 = 100%
- 1、下载文档前请自行甄别文档内容的完整性,平台不提供额外的编辑、内容补充、找答案等附加服务。
- 2、"仅部分预览"的文档,不可在线预览部分如存在完整性等问题,可反馈申请退款(可完整预览的文档不适用该条件!)。
- 3、如文档侵犯您的权益,请联系客服反馈,我们会尽快为您处理(人工客服工作时间:9:00-18:30)。
定义:指从原材料到发运产 品之间的总运转时间间隔; 用于测量原材料转化成成品 发运的速度,也就是通过工 厂的速度,而不是加工工艺 的速度。
Ó Ð È ò ¶ Á µ º
â æ ¿ ´
ý ¿ ú ú ¹ Á É ² ö Ó Û µ Ô ¼ ¼ Ö
ì é ¼ Ñ
·¤ µ ¹
5-2
â æ ¿ ´
日产量 = 200 (2 班/16小时)(顾客日需求量)
节拍时间是流动线的节奏或拍子
1-2生产线速率/节拍时间(TAKT)
Takt 节拍时间 = 可用工作时间
客户需求数量
Takt节拍时间 =
(60 X 工作小时/天) - 休息 & 午餐& 其它停顿时间
每天客户需求数量
例子:
节拍时间 = (60 x 17.0) - ((15+15+30+20)x2) 258 件 860 分钟 x 60 秒/分 258 件 = = 860 分钟 258 件
操作工数量 =
43+38+36+45+35 生产线节拍时间(40S)
2、FTT首次通过率
ቤተ መጻሕፍቲ ባይዱ
定义:指一次性完成一个生产过程并且满足质量要求的零件的百分率 ,包括报废、返工、再测试、剖检和下线修理或返回数。 首次通过率FTT%=每道工序的合格率数值相乘。 4、桑塔纳燃油箱FTT%案例 工序: 1)挤吹成型——2)冷却定型——3)打孔焊接——4)装配— —5)水下测漏/电性能——6)装配2 假设:1)挤吹成型为180只,报废2只;FTT1=〔180-2/180〕 *100%=98.88 2)冷却定型为178只, 报废1只;FTT2=〔178-1/178〕*100%=99.43 3)打孔焊接为177只, 报废1只,返工2只;FTT3=〔177-3/177〕 *100%=98.30 4)装配1为176只,报废1只,返工2只;FTT4=〔176-3/176〕 *100%=98.27 5)水下测漏/电性能为175只,报废1只,返工2只或重复做了两次; FTT5= 〔175-3/175〕*100%=98.24 6)装配2为174只,报废1只,返工1只;FTT6=〔174-2/174〕 *100%=98.80 FTT%=FTT1*FTT2*FTT3*FTT4*FTT5*FTT6 =98.88*99.43*98.30*98.27*98.24*98.88=92.25%。
1-1、节拍时间(TAKT)
TAKT Time determines the rate at which work must
be accomplished at each operation (Operational Cycle Time) based on the line rate.
节拍时间确定了每一工位必须完成工作的速率(操作周 期时间) TAKT is the rhythm or beat of the flow line.
= 0.85%
BTS= (9/10)*(3+1+3/10)*(6/10)*100%=90%*70%*60%=37.8% 产量性能用于监控生产计划完成情况 混线性能用于测量在厂内制造的产品系/型号/类型在适当的生产日的完成 比率 顺序性能用于测量在适当的生产日按照正确的生产顺序完成生产任务的 比率
5-1、有效生产周期(DTD)
3-3、OEE示例1-2
装配的 OEE4=(实际工作时间/理论工作时间)*(理 想循环时间*总生产数量/实际工作时间)*(总生产数 量—总缺陷/总生产数量)*100%。 水检的 OEE5=(实际工作时间/理论工作时间)*(理 想循环时间*总生产数量/实际工作时间)*(总生产数 量—总缺陷/总生产数量)*100%。 OEE总= OEE1*OEE2*OEE3*OEE4*OEE5
3-2、OEE示例1-1
B5生产线案例: 工序为:挤吹及冷却定型—打孔焊接—氟化—装配—水检 挤吹及冷却定型的OEE1=(实际工作时间/理论工作时间)*( 理想循环时间*总生产数量/实际工作时间)*(总生产数量—总 缺陷/总生产数量)*100%。 打孔焊接的OEE2=(实际工作时间/理论工作时间)*(理想循 环时间*总生产数量/实际工作时间)*(总生产数量—总缺陷/总 生产数量)*100%。 氟化的OEE3=(实际工作时间/理论工作时间)*(理想循环时 间*总生产数量/实际工作时间)*(总生产数量—总缺陷/总生产 数量)*100%。
ABC 装配线 节拍时间
=
200 秒/件
争取使每一工位每3分20秒生产一件合格品
1-3Operator Balance Chart 操作工负荷平衡表
Operator Balance Chart
Project: L-6 PCM Header Assembly Date:
9/29 - 9/30/98
1 2 3 4 3
3-1、OEE计算(实际50-60%/OK)/整个流水线
定义:OEE是三个不同的计算值的乘积,用于 测量指定设备的利用率,性能效率(节拍)和 质量率(FTT)。 OEE总= 各道工序的OEE相乘的乘积。 各工序的OEE=[(实际工作时间/理论工作时 间)*(理想循环时间*总生产数量/实际工作时 间)*(总生产数量—总缺陷/总生产数量)]* 100%。 OEE数据可以帮助识别由设备/过程不足引起 的不同的浪费
TYPE 2 NON VALUE 5.0 5.0 10.0 SECONDS / PIECE
WAIT FOR CYCLE
OPERATOR TOTAL 41.0 39.0 34.0 35.0 0.0
TAKT 36.2 36.2 36.2 36.2 36.2
数据输入区
SEC / PC 50.0 45.0 40.0 35.0 30.0 25.0 20.0 15.0 10.0 5.0 0.0 Retainers & Electrical
Time - to - Takt
1-4How Many Operators Needed? 需要多少操作工?
The
number of operator is calculated by dividing the sum of the operator work ( value added + non value added )by the Module Takt Time 操作工的数量等于总的单件产品的人工工作量除以单 条生产线之节拍时间=5.1人
OPERATOR BALANCE CHART
WAIT FOR CYCLE TYPE 2 NON VALUE TYPE 1 NON VALUE VALUE ADDED TAKT
Takt 节拍时间线 负荷时间图
Filters & Leak Test
Pin Insertion
Ferrite, Sealant, DIPG
4、BTS(生产计划的符合率)(60-70/OK)
定义:BTS是指在指定的生产日按照正确的生产顺序完成生产计划的比例 情况。BTS反映了工厂能够按照客户的要求完成生产的能力,客户需何种 产品,何时需要和客户使用产品的顺序。 是三个(总的数量是否满足符合性、品种是否满足符合性、顺序是否满 足符合性)不同的计算值的乘积; 计划:A1A2A3 B1B2B3B4 C1C2C3 总生产10个品种件 实际;A1A2A 3 A1A2B3X B1C2C3
OPERATION NAME Retainers & Electrical Filters & Leak Test Pin Insertion Ferrite, Sealant, DIPG
VALUE ADDED 26.0 24.0 34.0 10.0
TYPE 1 NON VALUE 10.0 10.0 15.0
ý ¿ ú ú ¹ Á É ² ö Ó Û µ Ô ¼ ¼ Ö
原材料库存折算为仓库中的零件数 1000 等待检验的零件数 400 各工序生产移动的零件数 400 正在检验的零件数 200 返工的零件数 200
生产时间提前1.5小时
ì é ¼ Ñ
·¤ µ ¹
生产周期时间 = 2200/200 = 11 天(是否满足顾客周期时间的要求) 增加价值 = 1.5/(11*16)