机械制造企业中安全生产事故原因分析与对策措施正式样本
起重机事故原因分析及对策
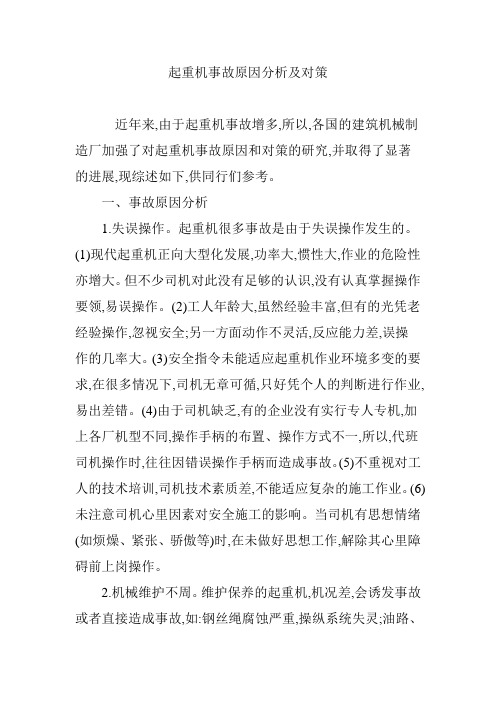
起重机事故原因分析及对策近年来,由于起重机事故增多,所以,各国的建筑机械制造厂加强了对起重机事故原因和对策的研究,并取得了显著的进展,现综述如下,供同行们参考。
一、事故原因分析1.失误操作。
起重机很多事故是由于失误操作发生的。
(1)现代起重机正向大型化发展,功率大,惯性大,作业的危险性亦增大。
但不少司机对此没有足够的认识,没有认真掌握操作要领,易误操作。
(2)工人年龄大,虽然经验丰富,但有的光凭老经验操作,忽视安全;另一方面动作不灵活,反应能力差,误操作的几率大。
(3)安全指令未能适应起重机作业环境多变的要求,在很多情况下,司机无章可循,只好凭个人的判断进行作业,易出差错。
(4)由于司机缺乏,有的企业没有实行专人专机,加上各厂机型不同,操作手柄的布置、操作方式不一,所以,代班司机操作时,往往因错误操作手柄而造成事故。
(5)不重视对工人的技术培训,司机技术素质差,不能适应复杂的施工作业。
(6)未注意司机心里因素对安全施工的影响。
当司机有思想情绪(如烦燥、紧张、骄傲等)时,在未做好思想工作,解除其心里障碍前上岗操作。
2.机械维护不周。
维护保养的起重机,机况差,会诱发事故或者直接造成事故,如:钢丝绳腐蚀严重,操纵系统失灵;油路、汽路不畅通或泄漏;电路接触不良或短路、断路、滑轮、轴承缺油(脂)、转动不灵或卡住不转动等。
3.缺乏安全装置。
有的起重机,没有安装防超载防碰撞等安全装置,当出现事故预兆时,不能报警或停机,从而酿成了事故。
4.环境因素。
在下列环境中作业,起重机易发生事故:在回填土方或泥泞场地吊装;在坡地吊装;有几台吊车在狭窄地段内同时作业,与土建施工交叉作业,在雨后路滑的地段吊装;在输电线路禁区附近吊装。
5.部件质量差。
起重机吊杆、支腿等部件质量差,如材质不合格,有裂纹等,会成为导致起重机发生事故的重要原因。
6.综合原因。
由上述两种或两种以上因素综合作用,更易发生事故。
二、防止事故发生的对策1.改进设计和制造工艺。
机械制造过程中发生伤害的原因分析和预防对策

机械制造过程中发生伤害的原因分析和预防对策机械制造过程中发生伤害的原因分析和预防对策机械制造是工业的基础,适用于各种生产领域,但是在机械制造过程中,由于各种原因,可能会发生伤害事故,严重影响操作者的安全和健康。
为此,需要对机械制造过程中发生伤害的原因进行分析,并采取一定的预防措施,以确保机械制造过程中的安全和健康。
一、原因分析1. 设备安全性低:机床、机器人和其他设备在使用和检修时,由于制造过程不符合标准或使用不当,容易出现安全性问题。
2. 机械操作者对操作规程和安全标准的不了解:有些工人不了解机械制造设备的操作规程和安全标准,或者不按规程操作,容易出现安全问题。
3. 设备老化和损坏:机械制造设备在生产过程中经常使用,容易出现设备磨损、老化或损坏,这些问题不及时得到维修或更换,会严重影响设备安全性。
4. 人为错误:操作者在操作过程中因疏忽大意或不注意安全,操作过程中出现人为错误,如操作中兴起的纱线、工具刀具上的铁屑、工具上的油脂等可能导致伤害。
5. 自然因素:例如受外界气温和湿度等自然因素影响,会导致设备零部件的膨胀或收缩,由此产生的误差和偏差,影响机械操作的安全性。
二、预防措施1. 加强设备安全:检查设备是否规范、合格以及是否需要定期维修、更换设备备件等。
2. 操作者要了解机械制造设备的操作规程和安全标准,并且在使用机械制造设备时,要按照标准操作,如正确穿着劳保用具、使用机器防护设备、杜绝非规定用途的操作等。
3. 加强设备维护和检查:定期走访和检查机械设备,发现问题及时维护和更换损坏部分。
4. 增强操作者的安全意识:对操作者进行安全教育,加强操作者的安全意识,让他们更加重视安全问题。
5. 加强管理:建立完善的管理机制,健全事故应急预案,加强事故预防、处置和搜救救援等工作。
存在安全问题及时通报,确保机械制造过程的安全性。
综上所述,在机械制造过程中,要注意对设备的维护以及操作人员对设备的了解,对相关工作外的操作应加强管理,提高操作者的安全意识,预防事故发生,确保机械操作过程的安全和健康。
安全工程师案例分析汽车制造工厂机械安全事故调查及改进措施

安全工程师案例分析汽车制造工厂机械安全事故调查及改进措施安全工程师案例分析:汽车制造工厂机械安全事故调查及改进措施作为一名安全工程师,我将以一个真实的案例来分析汽车制造工厂中发生的一起机械安全事故,并提出相应的改进措施。
本文的目的是为了帮助读者更好地了解机械安全事故的原因以及预防措施,以保障员工的安全和健康。
一、事故概况在某汽车制造工厂,最近发生了一起机械安全事故。
事故的起因是一名工人在操作机械设备时,由于操作不当,导致手指被机器夹住并受伤。
经过初步调查,事故原因主要有两个方面:设备操作不规范和缺乏必要的安全保护措施。
二、事故原因分析1. 设备操作不规范在车辆生产线上,机械设备的操作是非常频繁的。
然而,由于工人对设备操作规范的理解不足,操作时存在盲目性和随意性。
此次事故中,工人未按照标准程序进行机器操作,未戴好防护手套,也未采取确认安全状态的步骤,因而导致了手指受伤的事故。
2. 缺乏必要的安全保护措施该汽车制造工厂在机械设备的安全保护方面存在明显的缺陷。
首先,机械设备的触发机制设计不合理,容易将手指夹住。
其次,工作区域缺乏警示标识和安全防护栏,无法提醒工人注意危险,并保护工人免受伤害。
三、改进措施为了避免类似的机械安全事故再次发生,我提出以下改进措施:1. 建立操作规范制定详细的设备操作规程,明确操作程序,包括正确佩戴防护手套、操作前检查设备状态等。
同时,培训员工,提高他们对操作规范的理解和重视程度。
2. 设备安全改进对机械设备进行安全评估,重新设计机械的触发机制,避免将手指夹住。
增设安全防护装置,如安全防护栏和警示标识,以确保工人在作业过程中能够更加明确地认识到潜在的危险。
3. 安全培训与警示定期组织安全培训,加强员工的安全意识,培养他们对机械安全的重视。
为工作区域配备警示标识,提醒员工注意安全,同时在设备附近设置便于取得的急救设备。
4. 审查设备维护计划确保设备经常性维护,并定期审查维护计划的有效性。
机械制造产业工作者安全事故报告
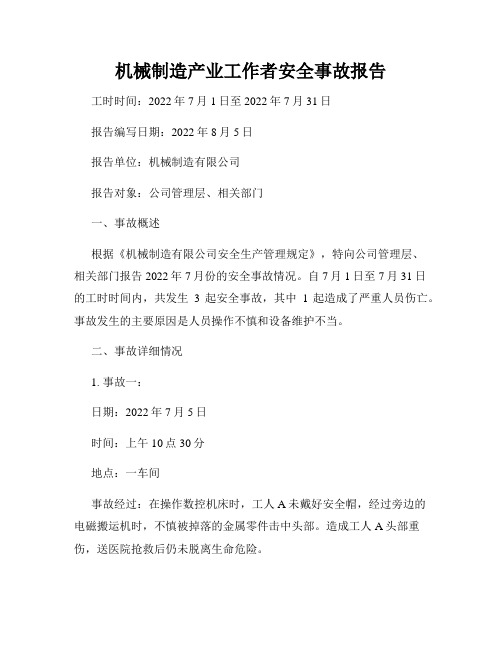
机械制造产业工作者安全事故报告工时时间:2022年7月1日至2022年7月31日报告编写日期:2022年8月5日报告单位:机械制造有限公司报告对象:公司管理层、相关部门一、事故概述根据《机械制造有限公司安全生产管理规定》,特向公司管理层、相关部门报告2022年7月份的安全事故情况。
自7月1日至7月31日的工时时间内,共发生3起安全事故,其中1起造成了严重人员伤亡。
事故发生的主要原因是人员操作不慎和设备维护不当。
二、事故详细情况1. 事故一:日期:2022年7月5日时间:上午10点30分地点:一车间事故经过:在操作数控机床时,工人A未戴好安全帽,经过旁边的电磁搬运机时,不慎被掉落的金属零件击中头部。
造成工人A头部重伤,送医院抢救后仍未脱离生命危险。
事故责任:操作人员未按规定使用个人防护装备,且未掌握安全操作流程。
2. 事故二:日期:2022年7月15日时间:下午2点15分地点:二车间事故经过:在维护机械设备时,工人B未断电就进行了清理工作,意外接触到高压电源。
工人B被电击后当场昏迷,及时送医院抢救后生命体征稳定。
事故责任:操作人员未按规定进行设备维护前的断电操作,并未掌握设备维护的安全程序。
3. 事故三:日期:2022年7月21日时间:下午3点40分地点:三车间事故经过:在操作起重设备时,工人C未正确固定货物,导致货物从高处坠落,砸中旁边工人D的腿部。
工人D受伤后被紧急送往医院,经检查无生命危险。
事故责任:操作人员未严格按照操作规程操作起重设备,未进行正确的货物固定。
三、事故原因分析1. 缺乏安全意识:造成事故的主要原因是相关工作人员缺乏安全意识,对安全操作规程和个人防护措施不重视。
2. 不合规操作:部分工人对设备的操作规程和维护程序不熟悉或敷衍了事,导致操作不当,引发事故。
3. 缺乏培训:在员工培训方面,公司还存在一定的不足,应加强对员工的安全操作培训以及定期的安全知识培训。
四、事故处理与改进措施1. 对事故责任人进行严肃处理,依法追究相应责任,并开展安全教育,提高安全意识。
机械安全事故案例分析

机械安全事故案例分析机械安全事故是生产过程中经常发生的问题,对企业和员工的安全带来极大的威胁。
本篇文章通过对一些典型的机械安全事故案例进行分析,以提高大家对机械安全问题的认识,并找出防止类似事故发生的措施。
案例一:机械伤害某工厂的一名工人在操作一台冲压机时,不慎将手卷入机器中,造成严重伤害。
经过调查分析,事故发生的原因有以下几点:1.工人未按照操作规程操作,伸手进入危险区域。
2.冲压机缺少必要的防护装置,如防护栏、警示标志等。
3.工厂对员工的安全培训不足,导致员工对安全风险认识不足。
案例二:物体打击在某建筑工地上,一名工人在操作塔吊时,吊装的货物突然脱落,将地面上的一名工人击中,导致重伤。
事故原因分析如下:1.工人操作塔吊时,未对货物进行稳固,导致货物脱落。
2.塔吊的监控系统不完备,无法实时监控货物状态。
3.现场安全管理不到位,缺乏对作业现场的安全监督。
案例三:触电事故一家电器生产厂家的员工在维修一台电动机时,未切断电源,直接进行维修,导致触电事故发生。
事故原因分析如下:1.员工在进行设备维修时,未按照操作规程切断电源。
2.企业对设备维修的安全管理不严格,未对员工进行充分的安全教育。
3.设备本身存在缺陷,如缺乏漏电保护装置等。
通过对以上三个案例的分析,我们可以总结出一些防止机械安全事故发生的措施:1.加强员工的安全培训,提高员工的安全意识,使员工熟练掌握安全操作规程。
2.企业应完善设备的安全防护设施,如防护栏、警示标志、漏电保护装置等。
3.企业应建立健全的安全管理制度,加强对作业现场的安全监督,确保各项安全措施得到有效执行。
4.加强设备的日常维护和检修,确保设备处于良好的工作状态。
以上是本文对机械安全事故案例的分析,希望对大家有所启示。
在今后的生产过程中,我们要时刻警惕机械安全风险,确保企业和员工的安全。
案例四:火灾爆炸在某化工厂,由于操作人员未严格遵守操作规程,在搬运易燃物品时引发了火灾,火势蔓延导致爆炸事故。
机械制造安全因素及控制措施.doc

机械制造安全因素及控制措施1.1人为因素产生安全事故的原因很多,比如违规操作、管理松懈及忽视安全生产等究其原因主要是由于不安全行为和理念造成的,比如领导层安全意识缺乏,在一定程度上不只是难以保证安全投入,导致劳保用品不足,普及安全生产知识不够等。
因安全管理松懈,对违章指挥监管不力,违规操作纠正不及时而产生安全隐患,而引发机械制造安全事故。
1.2机械运行风险机械在运行过程中因自身不安全状态也容易引发一些风险,加工机械产品通常需要设施运行过程中产生的能力,若接触这些就易对人体产生伤害,严重情况还将导致死亡。
所以,加强企业安全生产管理,才能降低机械运行中的风险,不只是需要对机械设备合理设计,综合考虑设备类型、参数进行选择。
1.3环境因素直接、间接和设备运行状态等三种方式是引发安全事故的环境因素。
员工患有职业病是对环境直接作用的主要表现,因长期工作于不健康环境中,易导致员工的一些职业病。
诸如粉尘、噪音及采用具有放射性或有毒材料等在机械制造中都会对员工身心健康产生不同程度的危害。
环境的间接影响主要是指因环境因素对员工产生的间接性伤害,因不合理的照明设计,员工在机械制造过程中产生籡昏、呕吐感,精神状态不佳而易于引起安全事故。
影响设备运行状态主要是指温湿度等对机械设备质量标准产生影响,在运行中易发生故障,而导致一些安全隐患。
2机械制造中控制安全事故的措施2.1控制人为因素的措施意识由物质所决定并对其产生能动的反作用,这要求对企业管理者与员工加强安全教育,提高对安全生产重要性的认识,进而树立安全生产理念。
企业领导层的安全意识与安全工作的落实具有密切关系,培训企业管理者使其深入了解安全生产流程及监管方法,加强培训沟通技巧,以确保安全监管的顺利实施。
而对于企业员工也要加强安全培训,在机械生产中严格遵循操作规程要求掌握安全生产技术。
此外,建立安全生产的企业文化,并将安全生产管理体系不断健全。
2.2控制机械运行的措施机械运行中通常都具有一定的安全风险,但可采取规避安全隐患的措施,在机械运行中减少风险。
机械伤害事故的原因与预防措施正式版

In the schedule of the activity, the time and the progress of the completion of the project content are described in detail to make the progress consistent with the plan.机械伤害事故的原因与预防措施正式版机械伤害事故的原因与预防措施正式版下载提示:此解决方案资料适用于工作或活动的进度安排中,详细说明各阶段的时间和项目内容完成的进度,而完成上述需要实施方案的人员对整体有全方位的认识和评估能力,尽力让实施的时间进度与方案所计划的时间吻合。
文档可以直接使用,也可根据实际需要修订后使用。
机械伤害事故的原因:1、机械设备在设计制造上存在缺陷;2、设备设施、工具、附件有缺陷;3、是设备日常维护、保养不到位、机械设备带病作业;4、从业人员个人操作错误、人为造成安全装置失效、机械运转时加油、维修、清扫,或者操作者进入危险区域进行检查、安装、调试;5、生产作业环境缺陷,操作空间不符合安全要求。
机械伤害事故的预防措施:1、在选择机械设备时,一定要选择有资质的正规厂商生产的机械设备,防护罩、保险、限位、信号等装置齐全,设备本身质量达到安全状态;2、专用设备必须配备专用的工具,设备设施上的安全附件有缺陷时,一定应及时处理,处理不了的要及时更换设备;3、加强对设备的使用、维护、保养、检查等工作,建立完善点巡检工作制,及早发现设备隐患并迅速处理,使机械设备不带病作业;4、以制度为切入点,规范员工操作行为,进一步完善规章制度和安全技术操作规程,杜绝违章指挥和违章操作的行为。
狠抓安全生产知识和安全操作技能培训工作,提高员工的自我保护意识;5、积极改善员工的生产作业环境,设备的改造应充分考虑到操作空间与周围环境,必须能够保证员工安全操作的需要。
——此位置可填写公司或团队名字——。
机械伤害事故处置方案
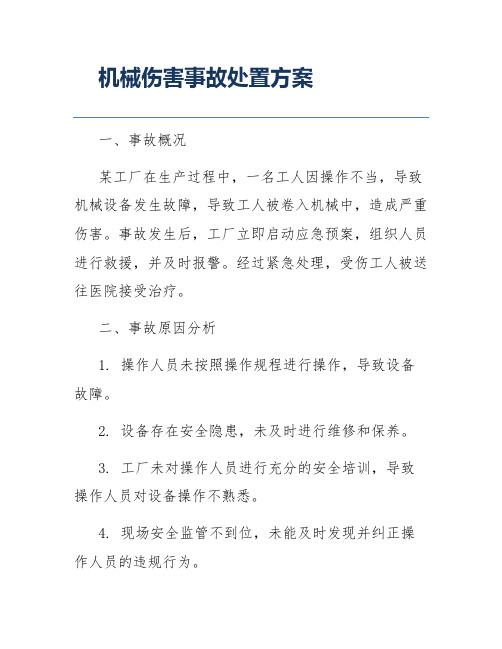
机械伤害事故处置方案一、事故概况某工厂在生产过程中,一名工人因操作不当,导致机械设备发生故障,导致工人被卷入机械中,造成严重伤害。
事故发生后,工厂立即启动应急预案,组织人员进行救援,并及时报警。
经过紧急处理,受伤工人被送往医院接受治疗。
二、事故原因分析1. 操作人员未按照操作规程进行操作,导致设备故障。
2. 设备存在安全隐患,未及时进行维修和保养。
3. 工厂未对操作人员进行充分的安全培训,导致操作人员对设备操作不熟悉。
4. 现场安全监管不到位,未能及时发现并纠正操作人员的违规行为。
三、事故处置方案1. 成立事故调查组,对事故原因进行全面调查,查明事故责任,提出整改措施。
2. 对受伤工人进行及时救治,并做好家属安抚工作。
3. 组织对事故现场进行清理,确保生产安全。
4. 对事故责任人员进行严肃处理,按照相关规定进行处罚。
5. 对全厂员工进行安全培训,提高员工的安全意识和操作技能。
6. 对工厂设备进行全面检查,消除安全隐患,确保设备安全运行。
7. 加强现场安全监管,严格执行操作规程,防止类似事故再次发生。
8. 定期组织安全演练,提高员工应对突发事故的能力。
9. 加强与医院等相关部门的联系,确保事故发生后能及时得到救援。
10. 对事故处理情况进行总结,及时向上级部门报告。
四、预防措施1. 加强员工安全培训,确保员工熟悉操作规程,提高员工安全意识。
2. 定期对设备进行维修和保养,确保设备安全运行。
3. 加强现场安全监管,严格执行操作规程,防止违规操作。
4. 定期开展安全检查,及时发现并消除安全隐患。
5. 建立健全事故应急预案,提高应对突发事故的能力。
6. 加强与相关部门的联系,确保事故发生后能及时得到救援。
7. 定期对事故处理情况进行总结,不断完善安全管理体系。
通过以上措施,确保工厂生产安全,防止类似事故再次发生。
同时,工厂将积极配合相关部门进行事故调查,严肃处理事故责任人员,切实保障员工生命安全和身体健康。
- 1、下载文档前请自行甄别文档内容的完整性,平台不提供额外的编辑、内容补充、找答案等附加服务。
- 2、"仅部分预览"的文档,不可在线预览部分如存在完整性等问题,可反馈申请退款(可完整预览的文档不适用该条件!)。
- 3、如文档侵犯您的权益,请联系客服反馈,我们会尽快为您处理(人工客服工作时间:9:00-18:30)。
文件编号:TP-AR-L5707In Terms Of Organization Management, It Is Necessary To Form A Certain Guiding And Planning Executable Plan, So As To Help Decision-Makers To Carry Out Better Production And Management From Multiple Perspectives.(示范文本)编制:_______________审核:_______________单位:_______________机械制造企业中安全生产事故原因分析与对策措施正式样本机械制造企业中安全生产事故原因分析与对策措施正式样本使用注意:该解决方案资料可用在组织/机构/单位管理上,形成一定的具有指导性,规划性的可执行计划,从而实现多角度地帮助决策人员进行更好的生产与管理。
材料内容可根据实际情况作相应修改,请在使用时认真阅读。
随着我国社会生产力的发展,机械制造企业逐年增多,安全生产事故频频发生。
在机械制造企业中,如何对安全生产事故进行有效预防,保持良好的安全生产秩序,对维护安全生产稳定起着极其重要的作用。
一、问题的提出据统计机械制造企业的安全生产事故在所有安全生产事故中所占比例是相当大的,它不仅影响企业的声誉与效益,而且严重伤害员工的身心健康,甚至生命。
在机械制造企业有秩序的生产活动和过程中发生的不测事件,不仅造成生产的中断或干扰,而且造成生产设施和材料的损坏,直接延误了生产,给员工和企业造成的伤害和损失是不言而喻的。
所以开展安全与事故研究是机械制造企业的重要工作。
本文将对机械制造企业中安全生产事故的原因进行分析与研究,并提出对策措施。
二、事故原因分析一)事故的直接原因分析(一)物的不安全状态机械设备的质量、技术、性能上的缺陷以及在制造、维护、保养、使用、管理等诸多环节上存在的不足,是导致机械伤害事故的直接原因之一。
具体表现为:一是机械设备在设计制造上就存在缺陷,如有的设备机械传动部位没有防护罩;有的设备没有安全保险措施;有的设备运动部件没有限位装置;有的设备没有工作运行提示信号装置;有的设备没有处理好人机工程学问题,使得机器的可操作性太差,容易引起操作者的误操作;二是设备设施、工具、附件有缺陷,加之有的企业擅自拆装、改装、拼装和使用自制非标设备,设备安全性能得不到保障;三是设备日常维护、保养不到位、机械设备带病运转、运行,对设备的使用、维护、保养、安全性能的测试缺乏有效的日常管理机制;四是从业人员个人劳动防护用品、生产工具缺少或缺陷,导致工人在操作中将身体直接置身于机械运转的危险区域之中;五是生产作业环境有缺陷,有的企业设备安装布局不合理,机械设备之间的安全间距不足,工人操作空间不符合要求,更有少数企业现场管理混乱,产成品乱堆乱放、无定置、无通道。
(二)人的不安全行为人的不安全行为是造成机械伤害事故的又一直接原因,集中表现为:一是操作失误,忽视安全,忽视警告。
操作者缺乏应有的安全知识和自我防护意识,思想麻痹,有的违章指挥,违章作业,违反操作规程,这个原因在企业新进职工身上体现得尤为明显。
二是操作人员野蛮操作,导致机器设备安全装置失效或失灵,造成设备本身处于不安全状态;三是手工代替工具操作或无意识冒险进入危险场所、区域,有的职工为多出产量,用工具操作麻烦,直接徒手操作,有的职工为图省事,走捷径,擅自跨越机械传动部位或危险区域;四是机械运转时加油、清扫,或者操作者进入危险区域进行检查、安装、维修、调试,虽然关停了设备,但未能开启限位、保险装置或在现场设置安全警示提示牌,或未及时通知生产现场调度人员,在无他人现场监护的情况下,将身体置身于他人可以启动设备的危险之中;五是操作者忽视使用或佩戴劳保用品,在操作中嫌麻烦。
二)事故的间接原因分析一是安全机构网络不健全,有的企业没有专职安全员或安全员配备不足,有的安全员身兼多职,职责不明;二是安全生产制度、操作规程不健全,即使有制度也流于形式,执行不到位,监管不到位;三是安全宣传教育、安全培训不到位,有的企业新工人未经培训就直接上岗作业,有的上岗职工缺乏必要的安全生产常识,特别是特种作业人员未经相关部门培训,缺乏安全操作技术知识,存在边学边干的现象;四是对事故隐患整改不力,有的企业虽然定期进行安全检查,但对发现的问题和隐患,往往一查了之,不能跟踪督查整改到位。
三、预防机械伤害事故的对策措施通过事故原因分析,为控制和避免机械安全生产事故应采取以下应对措施:第一、严把设备采购关。
机械制造企业在采购生产设备时,应当充分考虑生产设备的安全性能,认真地研究、分析生产设备潜在危险之处,对可能发生的各种危险进行预测,从源头上保证生产设备的本质安全度。
第二,以制度为抓手,规范职工操作行为。
对于机械企业来说,必须进一步完善规章制度和安全操作规程,落实相关职能部门的工作安全责任,提高制度的执行能力和可操作性,对一些特殊的专用设备的操作规程必须针对加工产品的特点及使用规定作深入细致的研究,制定更为细致和规范的操作规程,督促操作者掌握该设备的危险源(点)及防范措施。
通过建立健全安全生产规章制度,实行严格检查督促,落实各级各类人员的安全生产责任制,杜绝违章指挥和违章操作的行为。
第三,严格科学设置机械设备的安全规定和要求。
机械设备包括所有的金属切削设备,各种类型的锻压压力设备、木工机械、热加工设备、砂轮机以及机械传动装置等。
那么企业对所有机械加工设备的布局、设备与设备之间的间距、设备本身的安全操作空间必须符合《工厂安全卫生规程》,做到统一布局、科学安装。
同时对所有机械设备的危险部位都必须安装防护装置,保护机床区域内的操作者和其他人不受机械设备工作点、卷入挤压点、回转零件、飞出的碎屑和火花造成伤害,对防护网、防护罩、栏杆、防护档板等,必要时应增加安全连锁装置,这些装置必须与机械设备同时设计、同时施工、同时投入使用。
另外根据机械设备的维护保养的要求和规定进行日常的维护保养、定期维护保养及定期检修,以便及时发现和排除设备安全隐患,将事故隐患遏制在萌芽状态。
第四、应加强定置化管理工作。
单位要严格按照设计规范和单位内部管理规定,实行设备、工量具定置化管理。
一是机械设备间距要符合设计要求;二是要设置工具箱,工、量具或其它物品要存放在工具箱内,禁止放在车床床头、小刀架、床面、滑道面上;三是设置不同区域分区线、定位线,不同物料分区域、分类定置存放;四是确保安全通道畅通,禁止临时性设备、物料占压安全通道;五是生产成品不得长期存放在生产车间,应及时将成品转运仓库存放。
第五、应加强安全用电治理。
一是电工必须持证上岗;二是用电用具的外壳、开关、尽缘、接地线有破损、失灵等情况时,应及时修理,未经修复不得使用;三是严禁将电线架设在机械设备及钢架上;四是不准在机床运转时离开工作岗位,因故离开时必须停车并切断电源;五是严格落实停送电制度,维修机械设备时,控制开关处应悬挂“正在维修、禁止合闸”的警示标志,并有专人监控。
第六,狠抓培训教育,全力提高从业人员的自我保护意识。
强化生产经营单位和从业人员安全培训教育工作是贯彻安全生产方针,实现安全生产,提高管理者和从业人员安全意识和安全素质的重要途径,提高产品质量,加快推进现代工业化进程,对从业人员提出越来越高的要求,每个劳动者不但需要熟练掌握生产技术,而且还要求具备安全生产知识和安全操作技能,因此,应加强对职工安全培训工作。
企业要严格按照《生产经营单位安全培训规定》(国家安监总局第3号令)及地方有关安全培训的规定,强化对全体职工的安全培训工作。
一是健全安全培训档案,包括年度培训计划、时间、内容、考核、总结等资料;二是培训内容要全面,除对安全生产法律法规、规章制度、操纵规程培训外,还有涉及最新颁布的法律法规和有关规定;三是确保培训时间,一年内对职工的培训时间累计应不少于有关规定;四是确保全员培训,安全培训包括班组长、兼职安全员、各岗位正式工、临时工、外来承包商全员培训;五是培训形式要全面,新职工进行“三级”安全培训,调岗或离岗一年以上重新上岗时要安全培训,实施新工艺、新技术或者使用新设备、新材料时,应对有关从业职员重新进行有针对性的安全培训;六是企业对特种作业人员必须按照国家有关规定经专门的安全教育培训,取得特种作业安全操作资格证书,方可上岗作业,按照时限规定及时复审换证。
,第七、严格执行劳动保护要求。
强制执行劳动防护用品的使用与佩戴,为保护劳动者在劳动过程中的安全和健康,企业必须为劳动者配备必要的预防性装备,同时相关职能部门还必须加大检查力度,通过正确配备和使用劳动防护用品来改善劳动条件,防止伤亡事故,预防职业危害的发生。
一方面用人单位应正确采购和选用劳动防护用品;另一方面,督促从业人员正确佩戴和使用劳动防护用品,同时建立健全劳动防护用品的购买、验收、保管、发放、使用、更换和报废等管理制度,保障劳动者的安全与健康。
第八,建立健全安全生产检查和隐患排查制度,落实隐患整改。
安全生产检查和隐患排查是一项综合性的安全生产管理措施,是建立良好的安全生产环境,做好安全生产工作的重要手段,也是预防事故、消除隐患、减少职业危害的有效办法。
各机械制造企业必须建立健全安全检查和隐患排查制度,从查制度、查培训、查管理、查违章指挥和违章操作、查隐患、查安全设施等六个方面进行定期不定期的安全检查和排查,对一时难以整改到位的问题和隐患,限期整改,并明确专人负责跟踪督查、督办,确保隐患得到控制和消除。
第九、应加强对职工遵守安全操作规程的日常督查。
一是督查职工正确穿着劳动防护用品情况,操作旋转机械设备的职工要扎好袖口、系好纽扣,不准戴围巾、戴手套,女工发辫应挽在帽子内,高速切削时要戴好防护眼镜等;二是督查职工按规程操作情况,调整机床速度、装夹工件、刀具以及擦拭机床时都要停车进行,禁止隔着机床转动部分跨跃、传递拿取工具等物品,切大料时应留有足够余量以免切断时料掉伤人,小料切断时不准用手接,机床开动后要站在安全位置以避开机床运动部位和铁屑飞溅,清除铁屑不准用手应使用专门工具等。
第十、改造老式、陈旧设备,购买自动化设备。
一是对未淘汰的老式设备,除职工要严格执行操作规程外,要对未加防护装置的机械转动部位加设防护罩或防护栅栏,把危险区隔离保护起来,避免操作职员的身体触及危险区。
二是购买自动化设备,减少职工中间环节的操作,实现自动化作业,避免发生工伤事故。
此处输入对应的公司或组织名字Enter The Corresponding Company Or Organization Name Here。