制粉工艺流程
制粉工艺流程
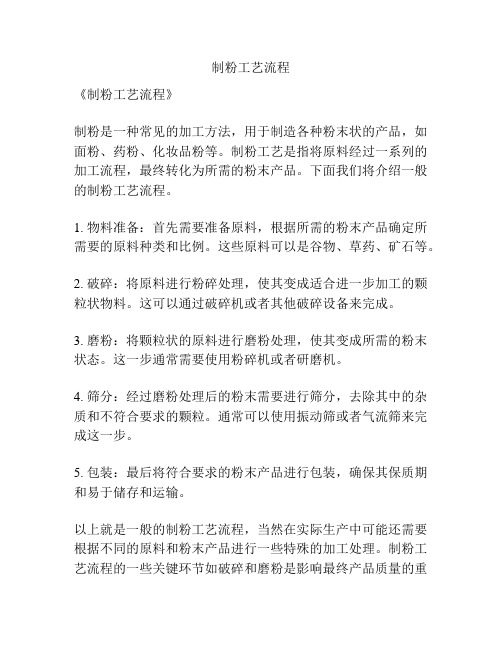
制粉工艺流程
《制粉工艺流程》
制粉是一种常见的加工方法,用于制造各种粉末状的产品,如面粉、药粉、化妆品粉等。
制粉工艺是指将原料经过一系列的加工流程,最终转化为所需的粉末产品。
下面我们将介绍一般的制粉工艺流程。
1. 物料准备:首先需要准备原料,根据所需的粉末产品确定所需要的原料种类和比例。
这些原料可以是谷物、草药、矿石等。
2. 破碎:将原料进行粉碎处理,使其变成适合进一步加工的颗粒状物料。
这可以通过破碎机或者其他破碎设备来完成。
3. 磨粉:将颗粒状的原料进行磨粉处理,使其变成所需的粉末状态。
这一步通常需要使用粉碎机或者研磨机。
4. 筛分:经过磨粉处理后的粉末需要进行筛分,去除其中的杂质和不符合要求的颗粒。
通常可以使用振动筛或者气流筛来完成这一步。
5. 包装:最后将符合要求的粉末产品进行包装,确保其保质期和易于储存和运输。
以上就是一般的制粉工艺流程,当然在实际生产中可能还需要根据不同的原料和粉末产品进行一些特殊的加工处理。
制粉工艺流程的一些关键环节如破碎和磨粉是影响最终产品质量的重
要因素,需要特别注意和精心设计。
希望对大家了解制粉工艺流程有所帮助。
小麦制粉的工艺流程

小麦制粉的工艺流程
小麦制粉是将小麦经过一系列的工艺处理,将其加工成粉状物的过程。
下面是一个典型的小麦制粉的工艺流程:
首先是清洁:将原料小麦经过风选、石选和磁选等清洁方法,去除杂质和异物,保证小麦的纯度和质量。
接下来是浸泡:将清洁过的小麦浸泡在水中,促进小麦中蛋白质的溶解和水分的吸收。
浸泡时间一般为8-10小时,浸泡后的小麦含水量增加,准备进入下一步。
然后是蒸煮:浸泡过的小麦经过蒸煮,一方面能使小麦胚芽获得适当的热量发芽,另一方面能软化小麦内胚乳,使其易于研磨。
常见的蒸煮时间为30-60分钟。
接下来是研磨:经过蒸煮的小麦进入研磨机,研磨机利用摩擦力将小麦研磨成粉末。
经过多道研磨,确保小麦粉质细腻,没有颗粒状物质。
然后是筛分:研磨后的小麦粉通过筛网进行筛分,去除大颗粒的异物和未研磨干净的小麦,确保粉末状小麦的纯度和质量。
接下来是浸泡漂白:为了提高小麦粉的白度,可以进行浸泡漂白处理。
将小麦粉浸泡在一定浓度的次氯酸钠溶液中,再用清水漂洗,可去除小麦粉中的色素和杂质。
然后是烘干:精制后的小麦粉含水量较高,需要经过烘干将其
含水量控制在一定范围内,一般为14-16%。
最后是包装:经过烘干后的小麦粉经过称重、包装机包装,以方便贮藏、运输和销售。
以上是小麦制粉的典型工艺流程。
当然,不同地区、品种的小麦以及不同的制粉工厂可能会有一些差异和特殊的处理方法。
但总的来说,清洁、浸泡、蒸煮、研磨、筛分、浸泡漂白、烘干和包装是制粉的基本步骤,通过这些步骤可以获得高品质的小麦粉。
小麦制粉工艺流程解析

小麦制粉工艺流程解析
小麦制粉是将小麦磨成面粉的过程,是面包、面点等食品加工的基础
工艺之一、下面将对小麦制粉的工艺流程进行详细解析。
1.清洗:将采收的小麦进行清洗,去除杂质、石块等,以保障面粉的
质量和卫生。
2.浸泡:将清洗过的小麦进行浸泡,使其吸水膨胀,方便后续的加工
处理。
浸泡时间一般为8-12小时。
3.蒸煮:浸泡后的小麦经过蒸煮,一方面可以使小麦糊化,有利于面
粉的提取,另一方面也可以杀灭小麦中的细菌和酵母。
蒸煮温度通常为
80-90摄氏度,时间为10-20分钟。
4.烘干:蒸煮后的小麦需要进行烘干,去除多余的水分,提高小麦的
贮存稳定性。
常用的烘干方法有阳光曝晒、机械烘干等。
5.粉碾:将烘干后的小麦经过粉碾机进行磨粉处理。
粉碾机利用碾盘
的反复摩擦实现对小麦的破碎和碾磨,将小麦磨成粉末状。
6.筛分:粉碾后的面粉需要进行筛分,去掉较粗的颗粒,以提高面粉
的质量和细腻度。
常用的筛分设备包括振动筛、气流筛等。
7.磨光:筛分后的面粉通常还需要进行磨光处理,以去除表面的粗糙
颗粒,使面粉细腻光滑。
常用的磨光设备有光面机、圆筒磨光机等。
8.包装:磨光后的面粉经过包装,通常使用密封包装袋,以防止面粉
受潮、虫蛀等。
上述是小麦制粉的一般工艺流程,具体情况还会根据不同的制粉目的、工艺特点和设备条件等因素进行调整。
需要注意的是,在整个小麦制粉过程中,卫生和食品安全十分重要。
因此,在小麦制粉车间中要做好清洁、消毒等工作,严格控制生产环境的卫生状况,确保面粉的质量和安全性。
制粉工艺流程
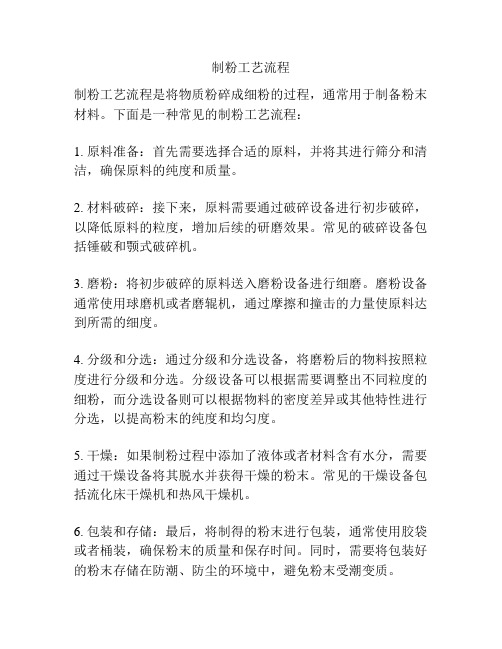
制粉工艺流程
制粉工艺流程是将物质粉碎成细粉的过程,通常用于制备粉末材料。
下面是一种常见的制粉工艺流程:
1. 原料准备:首先需要选择合适的原料,并将其进行筛分和清洁,确保原料的纯度和质量。
2. 材料破碎:接下来,原料需要通过破碎设备进行初步破碎,以降低原料的粒度,增加后续的研磨效果。
常见的破碎设备包括锤破和颚式破碎机。
3. 磨粉:将初步破碎的原料送入磨粉设备进行细磨。
磨粉设备通常使用球磨机或者磨辊机,通过摩擦和撞击的力量使原料达到所需的细度。
4. 分级和分选:通过分级和分选设备,将磨粉后的物料按照粒度进行分级和分选。
分级设备可以根据需要调整出不同粒度的细粉,而分选设备则可以根据物料的密度差异或其他特性进行分选,以提高粉末的纯度和均匀度。
5. 干燥:如果制粉过程中添加了液体或者材料含有水分,需要通过干燥设备将其脱水并获得干燥的粉末。
常见的干燥设备包括流化床干燥机和热风干燥机。
6. 包装和存储:最后,将制得的粉末进行包装,通常使用胶袋或者桶装,确保粉末的质量和保存时间。
同时,需要将包装好的粉末存储在防潮、防尘的环境中,避免粉末受潮变质。
以上是一种常见的制粉工艺流程,不同的物料和要求可能会有所不同。
在制粉过程中需要注意物料的纯度和质量,设备的选择和操作也对制粉效果有着重要的影响。
此外,在制粉过程中还需要遵守相关的安全规范和操作规程,确保工作环境的安全和人员的健康。
第十节 小麦制粉工艺流程
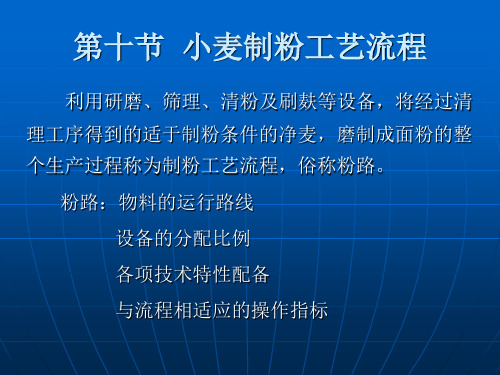
四、渣磨系统
(一)渣磨系统的任务、道数、设备比例: 任务是将皮磨系统及清粉机提出的带皮的粗粒(称麦渣),经较轻的剥 刮作用,刮去连附在麸皮上的胚乳,提出质量好的胚乳颗粒(麦心),同时 磨出部分质量较好的面粉。 渣磨道数:①生产标准粉或以标准粉为主:1~2道; ②生产优质粉:3~5道。 设备:一般占粉间设备的5~15%。 (二)渣磨系统的流程: ①若设一道渣磨(一般称1S),则设粗渣磨,来料为前路皮磨及经清粉机 清粉的大粗粒或大中粗粒。 ②若设二道,则设粗渣和细渣(一般称2S),来料为前路皮磨及经过清粉 的中、小粗粒。 ③若设三道,则设粗渣、细渣和尾渣磨(一般称3S),来料为清粉机及粗 细渣磨的粗筛筛上物或中路皮磨提出的较次的麦渣。 ④若设四道,设粗渣二道,细渣和尾渣各一道。 ⑤若设五道,设粗渣二道,细渣二道,尾渣一道。 (三)渣磨系统的磨辊技术特性和筛网配备: (四)渣磨系统的操作指标:
(二)皮磨系统的流程:(麸渣混、麸渣分磨、粗细麸分磨)
(三)皮磨系统的磨辊技术特性(设备比例:50~75%) (四)皮磨系统的筛路及筛网配备
(五)皮磨系统的操作指标
三、清粉系统
(一)清粉系统的任务:将皮、渣及其他系提出的麦渣、麦心 及粗粉按质量分成麦皮、麦渣和纯净的麦心。 1、皮磨系统中一等品质的粗粒和硬粗粉 2、经过渣磨处理后仍含有麸屑的中、小粗粒。 3、从皮磨和尾渣系统出来的二等品质的粗粒。 4、清粉机的吸出物: (清粉设备不多时:皮磨大粗粒→中粗粒→渣磨中小粗粒→二 等品质的粗粒→清粉机的吸出物) (二)清粉系统的流程 1、皮磨大粗粒的清粉流程: 2、皮磨及渣磨中小粗粒的清粉流程: 3、二等品质粗粒的清粉流程: 4、清粉机吸出物的重复清粉流程: (三)清粉机的技术设备
方便粉丝生产工艺

方便粉丝生产工艺
1.工艺流程:
原辅料→和浆→制粉→老化→冷冻→松丝→抓粉计量→烘干→粉饼
2.工艺要求:
2.1原辅料
2.2和浆
2.3制粉
将和好的浆液转进自熟式粉丝机挤压熟化,要求粉丝充分熟化,无生粉或过度熟化粉。
2.4老化
熟化后的粉丝先经输送线输送自然老化,然后剪粉,剪粉长度控制在30-31cm。
将剪切的粉丝挂在老化架上进行自然老化,老化时间夏季6-8小时,冬季4-6小时。
2.5冷冻
老化好的粉丝进冻库冷冻,在0-4℃预冷4-5小时,再快速冷冻到-5℃以下至粉丝表面有冰晶析出,冷冻时间合计为10-12小时。
2.6松丝
冷冻好的粉丝经解冻后用松丝机松丝,松丝时间5-10分钟,要求松后的粉丝基本无并条和断条。
2.7抓粉计量
将松后的粉丝根据产品克重工艺要求进行人工抓粉计量,要求抓粉计量克重必须在规定范围内。
2. 8烘干
烘干温度60-65℃,约1.5小时,烘干后粉饼要求规则成型,无湿心饼、不脆断。
制粉工艺流程
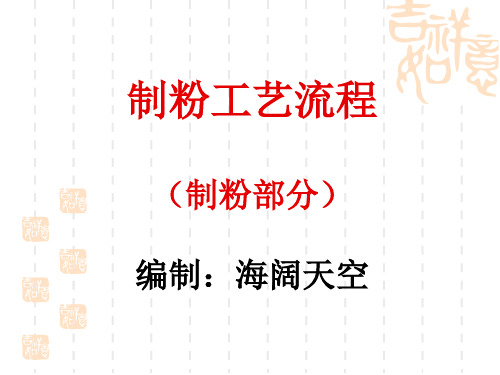
料的流量以及各设备间流量平衡状态的表
格,是设计、管理粉路的重要依据。
(一) 流量平衡表的内容 在流量平衡表中,应体现粉路的各个系统设置、 各道名称、各道占1B的流量、各道的出粉比例、出粉 等级以及副产品的类别和占1B的比例等;在流量平衡 表中还应体现各系统和各道物料的来源和去向;反应 皮磨的剥刮率和出粉率、心磨和其它系统的出粉率; 反应各系统和各道的流量平衡状态和质量平衡状态。 流量平衡表中的质量平衡状态,是以灰分作为评价的, 常以分式表示,分子为流量值(流量百分比),分母 为质量值(灰分百分比)。流量和质量平衡表一般是 测定所得。
(四)流量平衡表的作用 流量平衡表的作用是系统设计流量平衡的依据; 是磨粉机、高方平筛及其它设备配置的依据;是气力 输送设计的依据;是对磨粉机操作和工艺效果评价的 依据;是工艺测定最终反应工艺效果综合性图表。
粉路的设计
在新建、扩建或改造制粉厂时,均应进行粉
路设计。在粉路设计之前,应根据设计的要求, 认真进行调查研究,收集使用的资料,以提高粉
制粉工艺流程
(制粉部分)
编制:海阔天空
制粉工艺流程即将净麦加工成面粉 的全部工艺过程,也称粉路。将其粉路 按照图形符号反应在图纸中,并标注相 应的参数,称为粉路图。包括研磨、筛 理、清粉、打(刷)麸、松粉等工序, 粉路组合的合理性是制粉厂取得良好生 产效果的重要环节。
粉路组合的原则
粉路组合的原则是: 保证质量、均衡负荷、循序后推、同
(二)流量平衡表的格式 表的第一行与第一列为粉路中各道设备的名称, 按皮磨系统、清粉系统、渣磨系统、心磨系统分别循 环填写;每行数据表示对应设备的处理流量及所分出 物料的比例及去向,每列数据表示去向相同的物料各 自的流量。右边最后几列填写成品和副产品流量,最
玉米制糁制粉工艺流程

玉米制糁制粉工艺流程1. 玉米的选择和处理在玉米制糁制粉的工艺流程中,我们需要选择优质的玉米原料。
优质的玉米应该具有以下特点:颗粒饱满、色泽金黄、无霉变和虫蛀现象。
还需要对玉米进行处理,包括去杂、去皮、洗净等步骤。
步骤:1.将玉米原料进行筛选,去掉受损和不符合要求的颗粒。
2.使用清水将玉米浸泡2-4小时,使其充分吸水。
3.将浸泡后的玉米进行漂洗,去除表面污物。
4.去皮:将浸泡和漂洗后的玉米进行脱皮处理,可以使用专业设备或手工操作。
2. 玉米破碎经过处理后的玉米需要进行破碎处理,将其破碎成较小颗粒,为后续工艺步骤提供条件。
常见的破碎设备有碾磨机、颚式破碎机等。
步骤:1.将处理好的玉米送入破碎设备中。
2.调整破碎设备的参数,使得玉米颗粒能够被破碎成所需大小。
3.运行破碎设备,将玉米破碎成较小颗粒。
3. 玉米浸泡将破碎后的玉米颗粒进行浸泡处理,目的是使其吸水膨胀,便于后续工艺步骤的进行。
步骤:1.将破碎后的玉米颗粒放入浸泡槽中。
2.加入适量清水,使其能够完全覆盖住玉米颗粒。
3.控制浸泡时间,通常为6-12小时,具体时间根据实际情况而定。
4. 玉米脱水经过浸泡后的玉米颗粒含有较多水分,需要进行脱水处理。
步骤:1.将浸泡后的玉米放入脱水设备中。
2.调整脱水设备的参数,使得玉米颗粒能够被充分脱水。
3.运行脱水设备,去除玉米颗粒中多余的水分。
5. 玉米烘干脱水后的玉米颗粒还含有一定的水分,需要进行烘干处理,使其水分含量达到要求。
步骤:1.将脱水后的玉米颗粒放入烘干设备中。
2.调整烘干设备的参数,使得玉米颗粒能够受到适当的热风和热量。
3.运行烘干设备,将玉米颗粒中多余的水分蒸发掉。
6. 玉米碾磨经过烘干处理后的玉米颗粒需要进行碾磨,将其制成细小的颗粒或粉末。
步骤:1.将烘干后的玉米颗粒送入碾磨设备中。
2.调整碾磨设备的参数,使得玉米颗粒能够被充分碾磨成所需大小。
3.运行碾磨设备,将玉米颗粒制成细小的颗粒或粉末。
- 1、下载文档前请自行甄别文档内容的完整性,平台不提供额外的编辑、内容补充、找答案等附加服务。
- 2、"仅部分预览"的文档,不可在线预览部分如存在完整性等问题,可反馈申请退款(可完整预览的文档不适用该条件!)。
- 3、如文档侵犯您的权益,请联系客服反馈,我们会尽快为您处理(人工客服工作时间:9:00-18:30)。
比较适合加工软麦,充分发挥了渣磨系统的作用 ,清粉范围稍窄,清粉机使用数量较少,适合加工 硬度低的小麦。缺点是渣磨物料的质量不均匀,研
• (一)皮磨系统的流程 • 采用心磨出粉法时,前路皮磨提取种类较
多的在制品,需配置重筛;中、后路皮磨 分级较少,根据要求也可设置重筛。
(二)渣磨系统流程 渣磨系统的设置通常有三种工艺形式:
一、是先清粉后入渣的工艺; 二、是先入渣后清粉的工艺;
三、是先清粉后入渣再清粉的工艺。
1、先清粉后入渣的工艺,该流程的主要特点是: 比较适合加工硬质小麦,清粉范围较宽、一等品
是测定所得。
(二)流量平衡表的格式 表的第一行与第一列为粉路中各道设备的名称,
按皮磨系统、清粉系统、渣磨系统、心磨系统分别循 环填写;每行数据表示对应设备的处理流量及所分出 物料的比例及去向,每列数据表示去向相同的物料各 自的流量。右边最后几列填写成品和副产品流量,最 下一行为合数。表中数据均以入磨净麦流量为计算基 准,即1B的流量为100%,其它各道的流量以其占1B 流量的百分比表示。
第四、在制品的处理要循序后推,要保证研磨 次数,但一般不应有回路。
第五、为节省投资降低动耗,保证生产的稳定 性,应尽量减少物料的提升次数。
第六、工艺流程中如净麦段、吸风粉、成品打 包段等应设一定容量的缓冲仓,设备配置和选用 应考虑原料、气候、产品的变化。整个工艺根据 原料的变化要有一定的适应性和灵活性。
备注: ①各系统先后顺序用阿拉伯数字1、2、3……表示。 如1B、2M; ②各道磨粉机分粗细时,分别在系统代号右下角用小 写的c、f表示。如2Bc、1Mf; ③不同品种面粉,在代号前用阿拉伯数字区别。 如1F、2F; ④设备顺序,在相应代号前或后用阿拉伯数字区别。
如1BrF、2D 、DF1。
制粉工艺流程的内容
不适应加工软质小麦。
(三)清粉系统 1、清粉机的组合原则及清粉机的配置
根据物料的性质和前路磨粉机和高方平筛设备的配 置情况,对进入清粉机的物料要求必需先经过分级并 尽可能筛净面粉,物料粒度均匀一致,同时物料组合 还应遵守以下原则 :
(1)各道皮磨提取的麦渣应单独处理; (2)1B、2B的粗、细麦心或粗粉可同类合并处理, 但不能将麦心和粗粉合并清粉; (3)中后路提出的物料不能和前路物料合并,即使是 粒度相同也应单独处理;
表中每行第二列数据为该道设备的处理流量,其 值应与同行其它所有数据之和相等;从第二列开始, 每列的数值之和应与接收该列物料的设备的处理流量 值相等;成品(面粉)及副产品(麸皮等)的数据总 和应等于100%。
第二列的最下一项,表示包括1B在内的各道研磨 设备的流量总和,称为研磨物料周转率,较长的粉路 该数值较大,且其中不包括清粉机、辅助筛理设备的 处理流量。
采用前路均衡出粉法时,皮磨系统单位接触长度为 :3~4.5%mm·[100kg(麦)·24h]-1,占全部辊总长的 40~55%。
(二)渣磨系统的道数和磨辊接触长度 根据粉路类型、生产规模、产品种类及原料等条
件,渣磨一般设1~3道。 磨辊接触长度为0.8~1.2mm·[100kg(麦)·24h] -1,占
由于圆筛的工作机构是立式或卧式的工作圆筒, 内部有打板转子,工作圆筒配置粉筛筛网,并有强烈 的振动。与平筛相比,圆筛在处理比较粘腻的物料时 ,对筛下物具有一定的强迫过筛作用,且筛筒的高频 振动,使筛孔不易堵塞。
在制粉间气力输送系统由袋式除尘器收集的“吸 风粉”也是比较粘腻的物料,用圆筛筛理的效果比平 筛好。
其它吸风粉合并处理。
(四)心磨系统的流程 前、中路心磨平筛中应配置20%~35%的分级筛,
分出麸屑和麦心,以确保后续心磨的入机物料品质。 分级筛的设置视物料性质而定,如前路粗心磨物料含 麸屑和麦心较多时,可先用分级筛提出麸屑(含麸屑 较多的胚乳可进入细渣磨或一尾磨处理),再筛粉, 后用下分级筛将麦心分级,可减少对粉筛的磨损。
(三)流量平衡表的设计 设计粉路流量平衡表时,为便于计算,一般数据
精确道占1B流量的1%,少数流量较小的物料可精确至 0.5%。对吸风粉和面粉检查筛筛上物等流量较小的物 料,设计时可不考虑,但在粉路中应标明该物料去向
,并注意其对有关设备的影响。
(四)流量平衡表的作用 流量平衡表的作用是系统设计流量平衡的依据;
是磨粉机、高方平筛及其它设备配置的依据;是气力 输送设计的依据;是对磨粉机操作和工艺效果评价的
依据;是工艺测定最终反应工艺效果综合性图表。
粉路的设计
• 在新建、扩建或改造制粉厂时,均应进行 粉路设计。在粉路设计之前,应根据设计的要 求,认真进行调查研究,收集使用的资料,以 提高粉路设计的可靠性;在设计中应认真参考 资料,按照粉路组合的规律,根据适当的操作 指标,制订粉路工艺流程,选用制粉工艺设备 ,配置适用的工艺参数。
(一)粉路设计的依据 1、设计规模
日处理小麦的数量(t/d)、每天生产班次(三班8 小时、二班12小时)等。 2、原料情况
小麦的来源、品种、含杂、水分、质量、等级等。 3、成品要求
成品和副产品的种类、等级、质量要求、包装要求 、发放形式等。
4、设备情况 现有设备及拟够设备、设备的数量、设备的型号、
磨周转率高,一等品质的粗粒提取率稍低。
3、先清粉后入渣再清粉的工艺,该流程的主要特点是 :
比较适合加工硬度较高的小麦,不仅充分发挥了 清粉系统的作用,而且充分挖掘渣磨(甚至粗心磨)系 统的潜力,尽可能多提取出一等品质的粗粒、粗粉, 本工艺有能力提取数量较多的高精度面粉。缺点是清 粉机使用台数较多,操作管理要求及动力消耗稍高。
品。
制粉工艺流程的系统设置
(一)皮磨系统的道数和磨辊接触长度 皮磨系统包括4~5道研磨、筛理设备以及打麸
设备。皮磨系统的道数一般设4~5道。硬麦皮层 胚乳的结合较弱,较易剥刮,后路可少设一道, 整个系统为4道。软麦的皮层较厚,皮层与胚乳 结合力较强,为刮净皮层,一般设置5道。
心磨出粉法皮磨系统所需要磨辊接触长度为: 4~5.5mm·[100kg(麦)·24h]-1,占全部磨辊总长的 35%~40%。
总接触长度的5%~15%。 前路均衡出粉法设渣磨0~2道,占总接触长度的
0~10%左右。
(三)心磨系统的道数和磨辊接触长度 心磨系统的道数主要根据制粉方法来确定,同时
考虑设备条件、成品要求、原料等因素的影响。在心 磨出粉法中一般心磨设置7~10道;前路均衡出粉法设 置3-5道。当厂型大、成品要求高、加工硬麦时,应配 备较多的心磨道数。
制粉工艺流程
(制粉部分) 编制:海阔天空
• 制粉工艺流程即将净麦加工成面粉 的全部工艺过程,也称粉路。将其粉路 按照图形符号反应在图纸中,并标注相 应的参数,称为粉路图。包括研磨、筛 理、清粉、打(刷)麸、松粉等工序, 粉路组合的合理性是制粉厂取得良好生 产效果的重要环节。
粉路组合的原则
• 粉路组合的原则是: • 保证质量、均衡负荷、循序后推、同
(4)渣磨提出的物料宜单独清粉。
当清粉机数量较少时,应首先考虑精选前 路皮磨提取的麦渣和粗细麦心,其次是前路渣 磨物料和中路皮磨的渣心。若清粉机数量足够 ,应对送往前路心磨的所有物料均进行清粉或
采取二次清粉工艺。
2、清粉系统流程 清粉机吸出物中有部分吸风粉,若直接送往
磨粉机,则会影响磨粉机粉的喂料和研磨效果 。因此,可将该物料送入后续细皮磨平筛或与
设备的质量和设备的生产厂家。 5、采用技术
工艺类型及新技术新设备的选用,物料的输送形式 ,面粉后处理技术的选择等。 6、其它条件
如地理位置、周围环境、水电暖供应情况、气候条 件、生产发展的可能性、厂房结构等。
制粉工艺流程的流量平衡表
流量平衡表是反映粉路中各道进出物 料的流量以及各设备间流量平衡状态的 表格,是设计、管理粉路的重要依据。
(一) 流量平衡表的内容 在流量平衡表中,应体现粉路的各个系统设置、
各道名称、各道占1B的流量、各道的出粉比例、出粉 等级以及副产品的类别和占1B的比例等;在流量平衡 表中还应体现各系统和各道物料的来源和去向;反应 皮磨的剥刮率和出粉率、心磨和其它系统的出粉率; 反应各系统和各道的流量平衡状态和质量平衡状态。 流量平衡表中的质量平衡状态,是以灰分作为评价的 ,常以分式表示,分子为流量值(流量百分比),分 母为质量值(灰分百分比)。流量和质量平衡表一般
质合并、连续稳定、安全合理。
粉路组合的要求
• 第一、粉路中系统和道数的设置应根据产 品的等级、产量和原料品质的情况合理。 第二、粉路中各道设备的配备应根据物料 性质、数量和加工要求设置,应使各系统的工 作负荷均衡合理。
第三、各类在制品的走向,应遵循“同质合并 ”的原则,将品质相近的物料合并处理,既保证 产品质量,又简化流程、方便操作。
对前路细心磨不再分级,因含麸屑和麦心较少且 粒度差别较小,一般采取先筛粉后分级的方式。中路 心磨研磨的麦心经松粉后再筛理,提出二等品质的面 粉,分出的含麸屑胚乳进入二尾磨,麦心进入下道心 磨处理。后路心磨不再分级,全部为粉筛。末道心磨 的粉筛筛上物可直接作为饲料。
尾磨因麸屑含量多,麦心和面粉数量较少,所 以其平筛配备50%~60%的分级筛,采取分级—筛粉 —分级的流程。若对尾磨有提胚要求时,尾磨后的 松粉机可去掉或降低打击作用,以免将压成片状的 麦胚打碎。
1尾筛通常采用16W~18W的钢丝筛网提胚,用 40W~46W的筛网提出细麸屑送入后路细皮磨,用 60GG~72GG的筛网提出细小麸屑送入下续尾磨处理 ,麦心送入中路心磨处理,即采用提胚—分级—筛
粉—分级的形式。
2尾研磨后经松粉机打击再筛理,40GG~52GG的 筛网提取细麸皮(末道尾磨直接打包),筛下物筛粉 后再经一次分级,筛下物分别送入后路心磨处理。即 尾磨上分级的物料,根据工艺设置情况和物料状态, 送往中后路细皮磨或下道尾磨;末道尾磨上分级物料 也可送往打麸机,下分级筛的筛上物可直接作为副产