日本钢铁厂炼焦工序的余热回收技术
近年日本炼铁工序的节能环保技术简介汇总

近年日本炼铁工序的节能环保技术简介日本在钢铁发展达到顶峰的上世纪70年代,曾拥有高炉~70座,年炼铁能力~1.1亿t。
石油危机以后从节能的角度出发,对小型落后的高炉采取了大幅度关停的措施,到1995年仅保留高炉31台。
最为突出的是新日铁釜山厂,由钢铁联合企业变为只剩1个线材工厂并依靠外部供坯生产的钢铁厂;广烟厂和堺厂由于高炉关停后只有靠转炉吹氧喷煤熔化废钢铁炼钢。
对保留生产的高炉也全面实施了节能环保技术,如高炉顶压发电、热风炉利用余热提高风温、烧结机利用余热发电以及用喷煤粉全部代替了喷油,并达到了100kg/t以上的水平,这些措施均对能耗达到国际先进水平作出了很大的贡献。
同时在含铁粉尘用于烧结机配料和高炉渣用于水泥等方面也进步很快,1995年的利用率已达到96%左右。
1995年以后为了贯彻“世界21世纪议程”中提出的可持续发展方针以及以减排CO2为中心的节能环保企业2010年志愿计划,除了开展高炉喷吹废塑料代煤和开发直接还原铁技术以合理利用资源和能源外,还利用90年代后期钢铁需求疲软导致高炉低利用系数生产的有利时机,大力开发扩大喷吹煤粉以代焦炭而降低成本的技术,部分高炉月度喷煤比高达254~266kg/t铁,具体情况如表1所示。
表1 日本喷煤比较高的高炉各项指标由此,在1998年和1999年,日本全国喷煤比也创造了129.5kg/t和132.9kg/t的历史新纪录。
2000年以后随着钢产量和生铁产量的上升而高炉又减少了3座(中山制钢关停2×850m3高炉和JFE钢铁千叶分厂关停2000m3高炉),由于利用系数的提高,喷煤比开始略有下降,具体见表2。
表2 近年日本高炉产量和燃比指标的变化由于高炉开工座数由2001年之前的31座和平均炉容3800m3,减少为2005年的28座,加上不少高炉大修扩容,2005年平均单炉容积为4004m3,最大炉容为5775m3。
2005年全国的平均利用系数为2.03。
日本低成本和环境友好型炼焦新技术的进展(上)

日本低成本和环境友好型炼焦新技术的进展(上)近年来,钢铁企业为降低生产成本,以及应对环保要求日益严格的形势,纷纷把研发的重点集中在原燃料新技术的开发方面。
焦炭质量好坏对高炉炼铁生产起着至关重要的作用,同时炼焦工序是钢铁企业控制污染物排放的关键环节之一。
因此,低成本和环境友好型炼焦新技术的开发成为人们关注的重点。
本文对日本新近研发的新一代SCOPE 21炼焦技术,全部使用弱、非黏结煤生产焦炭技术,以及高反应性焦炭生产技术进行了阐述,重点介绍了这3种技术的研发背景、特点和目前的研究状况以及工业化应用情况。
这3种技术的开发对于提高弱、非黏结煤的用量,降低生产成本都具有十分重大的意义。
日本在开发低成本和环境友好型炼焦新技术方面一直走在世界前列,其炼焦新技术的研发主要集中在两个方面:一是在保证焦炭质情况下,加大廉价煤的使用量,主要是扩大非黏结煤或者弱黏结煤的用量;二是减少污染物排放。
1 日本典型的低成本和环境友好型炼焦新技术日本近年来一直致力于进行大量使用弱黏结煤技术的开发。
弱黏结煤有以下特征:由于煤在软化温度区域的熔融性指数比黏结煤低,如果单独使用,煤颗粒间的黏着会不充分;大量使用弱黏结煤时,焦炭强度会下降,无法获得优质焦炭。
因此,为了能够大量使用弱黏结煤,必须对煤进行一些预处理。
为此,日本开发了煤的新型预处理技术,其中包括煤预热技术。
一般认为焦炭是一种多孔质材料,其强度主要受以下因素的支配:基质强度、气孔率、焦炭内的龟裂和缺陷。
因此,在配加弱黏结煤的情况下,只有改善这些影响因素,才能大量配加。
煤预热炼焦技术是利用热的惰性气体将配合煤快速加热到150℃-250℃后热煤装炉的一种炼焦技术。
煤料装入炭化室后,其堆密度比湿煤高10%-15%,由于装炉煤的升温速度加快,塑性温度间隔增宽,改善了煤料的塑性,同时装炉煤的膨胀压力也增大。
该项技术适用于膨胀压力较小的高挥发分弱黏结煤。
与常规的湿煤炼焦相比,结焦时间缩短了20%-30%,散密度增大了10%-15%,焦炉生产能力提高了30%-50%。
焦炉余热回收系统及实用性分析
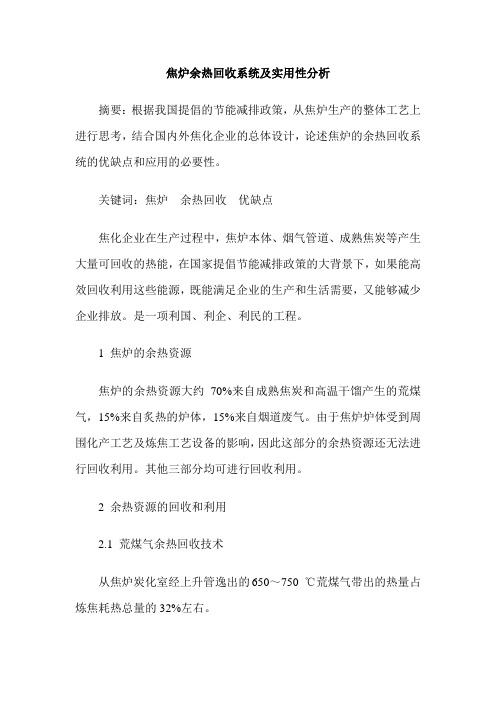
焦炉余热回收系统及实用性分析摘要:根据我国提倡的节能减排政策,从焦炉生产的整体工艺上进行思考,结合国内外焦化企业的总体设计,论述焦炉的余热回收系统的优缺点和应用的必要性。
关键词:焦炉余热回收优缺点焦化企业在生产过程中,焦炉本体、烟气管道、成熟焦炭等产生大量可回收的热能,在国家提倡节能减排政策的大背景下,如果能高效回收利用这些能源,既能满足企业的生产和生活需要,又能够减少企业排放。
是一项利国、利企、利民的工程。
1 焦炉的余热资源焦炉的余热资源大约70%来自成熟焦炭和高温干馏产生的荒煤气,15%来自炙热的炉体,15%来自烟道废气。
由于焦炉炉体受到周围化产工艺及炼焦工艺设备的影响,因此这部分的余热资源还无法进行回收利用。
其他三部分均可进行回收利用。
2 余热资源的回收和利用2.1 荒煤气余热回收技术从焦炉炭化室经上升管逸出的650~750 ℃荒煤气带出的热量占炼焦耗热总量的32%左右。
2.1.1 上升管汽化冷却技术上升管汽化冷却技术(简称JSQ),为中国首创技术,于20世纪70年代初首先在首钢、太钢等企业的单集气管焦炉上使用。
但是有些企业不知道什么原因就放弃了这项技术,不再使用。
技术优点:投资少,使用过程中所消耗的费用低。
技术缺点:(1)回收的热量仅为荒煤气部分余热,且在上升管根部由于煤气聚冷易造成焦油析出,最终引起结石墨严重。
(2)虽然他的技术不断完善,但是其本身的管理风险还是很大的,易发生如上升管夹套内压过大或漏水等突发情况,均会对焦炉造成很大的危害。
(3)若不采用新的工艺技术匹配,回收热量产生的低压饱和蒸汽利用途径受到极大限制。
2.1.2 导热油夹套技术日本新日铁公司于1982年开发了利用导热油回收焦炉荒煤气余热的技术,并将回收的热量用于炼焦煤的干燥,形成了第一代炼焦煤调湿技术。
技术优点:安全性高,回收热量可在一定范围内精确调整,上升管结石墨现象比汽化冷却方式少。
技术缺点:(1)导热油在使用过程中难免会发生热变质现象,这样工作就无法正常运行。
荒煤气带出热的回收和利用技术
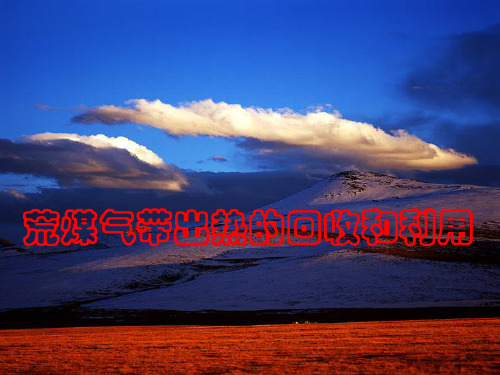
焦炉输出热量的充分利用
高效回收利用在炼焦过程中产生的余热资源是资 高效回收利用在炼焦过程中产生的余热资源是资 源节约、环境友好的绿色焦化厂节能的主要方向和潜 源节约、环境友好的绿色焦化厂节能的主要方向和潜 力所在, 效率的主要途径之一。 力所在,也是提高 效率的主要途径之一。通过对炼 焦过程输入端和输出端能量流分析得出: 焦过程输入端和输出端能量流分析得出: □出炉红焦显热约占焦炉输出热的37%——CDQ 出炉红焦显热约占焦炉输出热的37% 焦炉输出热 CDQ
日本煤炭能源中心(简称JCOAL) 日本煤炭能源中心(简称JCOAL)在焦炉旁安装 JCOAL 一个COG重整装置, 1200~1250℃高温下对COG进 一个COG重整装置,在1200~1250℃高温下对COG进 COG重整装置 高温下 行重整,生成合成气。目前已在日本三井矿山焦化 行重整,生成合成气。 厂的焦炉间台进行了一孔炭化室无催化转化技术实 厂的焦炉间台进行了一孔炭化室无催化转化技术实 验,正在建设三孔炭化室试验装置。 正在建设三孔炭化室试验装置。
上 升 管
热管换热器
750℃ 锅炉给水
用锅炉回收荒煤气热量
750℃荒煤气 750℃荒煤气
xMPa
锅
300~ 300~500℃ 荒煤气去净化车间
上 升 管
锅炉给水
用半导体温差发电回收荒煤气热量
荒煤气去净化车间 温 差 发 电 机 发 电 模 块 热 发电
焦 炉
过去用水套管回收荒煤气热量
上升管 荒煤气去净化车间 冷水 水夹 套式 上升管
1.1 回收焦炉荒煤气带出热 出热占焦炉总热量36% 出热占焦炉总热量36%。 36 为了冷却高温的荒煤气必须喷洒大量70℃~ 为了冷却高温的荒煤气必须喷洒大量70℃~75℃ 70℃ 循环氨水, 循环氨水,高温荒煤气因循环氨水的大量蒸发而被冷 却至82℃~85℃,再经初冷器冷却至22℃~35℃, 却至82℃~85℃,再经初冷器冷却至22℃~35℃,荒 82℃ 22℃ 煤气带出热量被白白浪费。 煤气带出热量被白白浪费。 煤气在集气管冷却时所放出的热量中约有75~ 煤气在集气管冷却时所放出的热量中约有75~80 75 用于蒸发氨水、10~15%使氨水升温, %用于蒸发氨水、10~15%使氨水升温,而集气管的 散热损失约占10% 散热损失约占10%。 10
钢铁工业余热余能资源利用途径及回收潜力探索

钢铁工业余热余能资源利用途径及回收潜力探索1、前言钢铁工业余热余能资源是指钢铁生产过程中某一工艺系统未被利用的能量,包括余热和余压。
其中余热指工艺过程中未被利用而排放到周围环境中的热能,按载热体形态的不同分为固态载体余热(如焦炭、炉渣、烧结矿、球团矿、连铸坯等)、液态载体余热(如冷却水、冷凝水等)以及气态载体余热(如高、焦、转炉煤气、废烟气、蒸汽等)三种;余压指由工艺设备排出的有一定压力的流体,按载体形态的不同分为气态余压(如高炉炉顶余压)和液态余压(如循环冷却水余压等)。
由于钢铁工业在消耗能源推动物料转变的同时会产生大量的余热余能,因此各类余热余能的有效回收利用,是钢铁工业节能降耗的重要途径。
国内钢铁工业相关研究早在20世纪80年代就已开始,最初技术人员计算了1986年我国钢铁工业的余热资源量及回收利用率,提出了余热回收利用的潜力。
随后,宝钢、本钢等钢铁企业也对余热余能回收利用进行了调查分析。
近年来,钢铁工业余热余能资源回收利用水平快速提高,为中国钢铁工业节能降耗做出巨大贡献。
2、余热余能资源及利用途径2.1 焦化工序焦化工序现阶段已回收利用的余热余能资源包括焦炭显热、焦炉煤气潜热、烟道气显热和初冷水显热。
焦炭显热主要是采用干熄焦技术回收利用产生蒸汽用于发电,目前干熄焦发电技术在国内钢铁联合企业的应用普及率已很高。
焦炉煤气热值高,是一种优质燃料,目前已得到充分利用,放散率很低,主要利用途径是供各生产用户使用,富余资源用于驱动锅炉发电。
同时,由于焦炉煤气富含氢气和甲烷,提升利用品位,将其作为化工原料生产甲醇、合成氨等化工产品及天然气资源的利用方式近年来得到了更多的关注。
烟道气显热的温度一般在250~300℃,目前主要采用余热回收设备回收蒸汽供生产、生活用户或作为煤调湿热源。
焦化初冷水显热温度一般在60~70℃,主要采用换热器回收热量用于北方地区冬季采暖。
2.2 烧结工序烧结工序现阶段已回收利用的余热余能资源包括烧结矿显热及烧结烟气显热。
钢铁工业余热回收的主要环节介绍
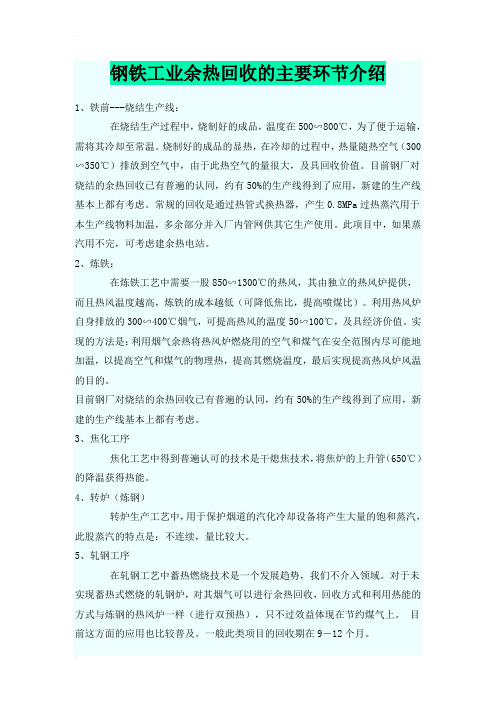
钢铁工业余热回收的主要环节介绍1、铁前---烧结生产线:在烧结生产过程中,烧制好的成品,温度在500∽800℃,为了便于运输,需将其冷却至常温。
烧制好的成品的显热,在冷却的过程中,热量随热空气(300∽350℃)排放到空气中,由于此热空气的量很大,及具回收价值。
目前钢厂对烧结的余热回收已有普遍的认同,约有50%的生产线得到了应用,新建的生产线基本上都有考虑。
常规的回收是通过热管式换热器,产生0.8MPa过热蒸汽用于本生产线物料加温,多余部分并入厂内管网供其它生产使用。
此项目中,如果蒸汽用不完,可考虑建余热电站。
2、炼铁:在炼铁工艺中需要一股850∽1300℃的热风,其由独立的热风炉提供,而且热风温度越高,炼铁的成本越低(可降低焦比,提高喷煤比)。
利用热风炉自身排放的300∽400℃烟气,可提高热风的温度50∽100℃,及具经济价值。
实现的方法是:利用烟气余热将热风炉燃烧用的空气和煤气在安全范围内尽可能地加温,以提高空气和煤气的物理热,提高其燃烧温度,最后实现提高热风炉风温的目的。
目前钢厂对烧结的余热回收已有普遍的认同,约有50%的生产线得到了应用,新建的生产线基本上都有考虑。
3、焦化工序焦化工艺中得到普遍认可的技术是干熄焦技术,将焦炉的上升管(650℃)的降温获得热能。
4、转炉(炼钢)转炉生产工艺中,用于保护烟道的汽化冷却设备将产生大量的饱和蒸汽,此股蒸汽的特点是:不连续,量比较大。
5、轧钢工序在轧钢工艺中蓄热燃烧技术是一个发展趋势,我们不介入领域。
对于未实现蓄热式燃烧的轧钢炉,对其烟气可以进行余热回收,回收方式和利用热能的方式与炼钢的热风炉一样(进行双预热),只不过效益体现在节约煤气上。
目前这方面的应用也比较普及。
一般此类项目的回收期在9-12个月。
1、铁前---烧结生产线:在烧结生产过程中,烧制好的成品,温度在500∽800℃,为了便于运输,需将其冷却至常温。
烧制好的成品的显热,在冷却的过程中,热量随热空气(300∽350℃)排放到空气中,由于此热空气的量很大,及具回收价值。
钢铁厂炼焦炉上升管余热回收技术发展及应用

钢铁厂炼焦炉上升管余热回收技术发展及应用摘要传统荒煤气冷却工艺造成大量显热流失浪费,同时消耗淡水资源带来环境压力。
在技术人员的多年努力下,上升管余热回收技术及装置已日臻成熟并得到了推广应用,创造了良好的经济和环保效益。
一、钢铁联合企业炼焦工序余热资源长流程钢铁生产工艺,高炉炼铁工序中作为还原剂的主要原料是焦炭。
用于还原铁矿石中的铁元素,生产出的生铁供给后续炼钢车间炼钢。
高炉内的化学方程式为:Fe0+C=Fe+CO。
钢铁联合企业一般自备炼焦炉系统生产焦炭满足生产需求。
焦炭由炼焦煤在炼焦炉碳化室中,隔绝空气高温干馏去除有机质、挥发分生成。
炼焦生产过程中有三种余热资源产生:红焦显热、烟道废气显热、荒煤气显热。
各自在焦炉总体热量消耗中所占比例分别为:37%、17%、36%本文讨论荒煤气显热的回收----上升管余热回收技术:二、炼焦炉上升管余热(荒煤气显热)回收的必要性红焦炭带出的显热及烟道废气显热,通过采用成熟可靠的干熄焦发电装置和烟道余热锅炉已实现有效回收利用。
但荒煤气的显热由于种种因素一直没有好的办法来回收。
传统工艺为便于后工序的煤气净化与处理,普遍的做法是:先在桥管和集气管喷洒循环氨水与荒煤气直接接触,靠循环氨水大量气化,使荒煤气急剧降温至80~85℃;降温后荒煤气在初冷器中再用冷却水间接冷却至常温。
所得到的效果是:荒煤气被冷却,其中所夹带的粉尘被清洗除去,绝大部分焦油蒸汽冷凝、萘凝华(并溶于焦油)而被脱除,为煤气的输送、深度净化和化学产品回收创造了较好的条件。
上述过程对荒煤气的冷却和初步净化而言是高效的,但在热力学上却是不完善的。
第一、该回收的能量未回收。
荒煤气在桥管和集气管内急剧降温─增湿过程是高度不可逆过程,其物理显热损失达90%以上.第二、冷却水耗量大。
荒煤气从650~850℃降温至常温所放出的热量绝大部分是在初冷器中靠冷却水移除的(以两段循环水一段深冷水的横管初冷器为例,冷却水总比用量约43t/km3)。
日本钢铁业研究的减排CO_2炼铁新技术

和神 户钢 铁等研 究 了焦炭 反 应性 对 高 炉 操作 的
影 响并 发现 , 焦炭 反应 性 提 高 可 以 降 低 炉 子 上部
的温度 ; 随焦 炭反 应性 的提高 , 炭在 储 热 区内溶损 焦
反 应 的模 式 中 由在焦炭 颗粒各 处 均匀 发 生变 为 只发 生 在焦 炭颗 粒表 面 。也 就是说 , 随焦 炭反应 性 提 高 , 焦 炭颗 粒 内部 的溶损反 应受 到 了抑制 。这 样 就抑 制 了焦炭 进一 步粉 化 , 而 阻止焦炭 颗 粒进 一 步变小 , 从
NE RoNM AK I W I NG TECH NoLoG Y oF RED UCI NG Co
oF J APANES TEEL I ES NDUS TRY
Hu J n e W a g Zay Ch n Ya Z o e to Gu n i g u g n ii e n h u W na o Ya ln
求 。 因此 , 日本在 减少 钢 铁业 排 放 C 的炼 铁 新 技 O
1 近 期 开 发 的 减 排 C 炼 铁 新 技 术 O
近 年来 ,3 钢 铁 企业 由 于大 量使 用廉 价 铁矿 1本
作 者 简 介 : 俊 鸽 (9 6一) 女 , 级 工 程 师 , 士 研 究 生 ,9 0年 毕业 于 东北 工 学 院 胡 16 , 高 硕 19
炉料 , 以保持在当前高炉设施 和产能不 变情况下 , 以 可 进一步降低高炉还原剂 比( 生产 1 铁所需要 的还原剂 t 量, 比如焦炭、 煤等 )从而实现减排 的 C 目的。长期 , O
则通 过开发 革命性 的、 以氢气还 原铁 矿石 的高 炉炼铁
控制技术和与之相配套 的使用 新型粘结剂 的炼焦技术