凸凹模(落料拉深)尺寸计算
冲模冲裁件凸凹模尺寸计算
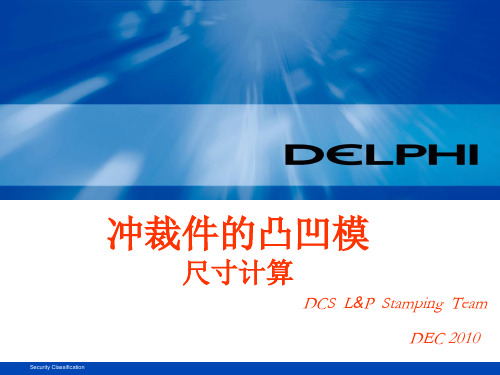
Security Classification
Date6ຫໍສະໝຸດ 经验公式如下: PX=KX*P(N) PT=nKX*P(N) PD=Kd *P(N) 式中, PX 、PT 、PD------分別为卸料力,推件力和頂件力系数 P------冲裁力 n------同时卡在凹模洞口內的落料件数.n=H/t,H为凹模刃壁垂直 部分高度,t为料厚.当采用锥形洞口时,因无落料件卡在洞口 內,故可不计推件力.
冲压力是指冲裁时,压力机应给出的最小压力。冲 压力是冲裁力,卸料力,推件力和顶出力的总称。 冲裁力的计算公式: P=KLtτ (N) P----冲裁力(N) L----冲裁件周边长度(MM) τ ----材料的抗剪程度(MPA) t----料的厚度(MM) k----系数通常k=1.3
Security Classification
Security Classification Date 8
如有不同意见敬请赐教! 让我们共同进步!
Thanks!
DCS L&P Stamping Team
DEC 2010
Security Classification
Date
9
Date
3
2、降低冲裁力的方法
(1) 斜刃口及波形刃口冲裁法
Security Classification
Date
4
(2) 阶梯凸模冲裁法
Security Classification
Date
5
3、卸料力,推件力,頂件力的計算
卸料力是将箍在凸模上的板料卸下时所需要的力;推料力是 将落料件顺着冲裁凹模洞口推出时所需的力;頂件力是将落料件 逆着冲裁方向顶出凹模刃口时所需的力。
2. 凸、凹模分开加工
凸、凹模刃口尺寸的计算
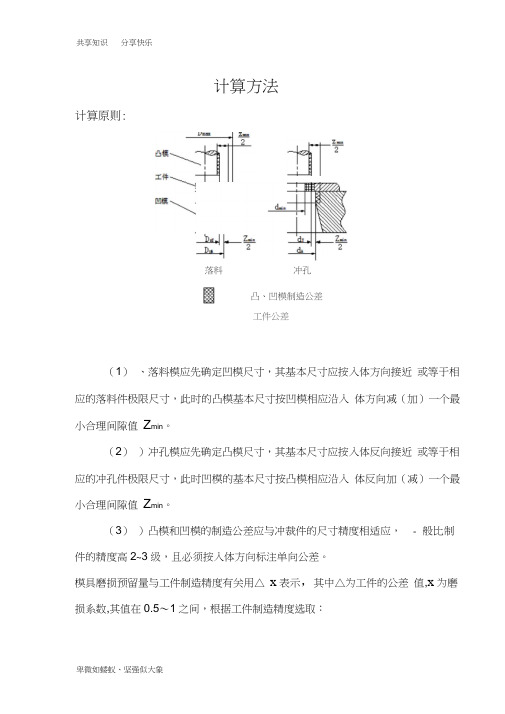
工件公差(1) 、落料模应先确定凹模尺寸,其基本尺寸应按入体方向接近 或等于相应的落料件极限尺寸,此时的凸模基本尺寸按凹模相应沿入 体方向减(加)一个最小合理间隙值 Z min 。
(2) )冲孔模应先确定凸模尺寸,其基本尺寸应按入体反向接近 或等于相应的冲孔件极限尺寸,此时凹模的基本尺寸按凸模相应沿入 体反向加(减)一个最小合理间隙值 Z min 。
(3) )凸模和凹模的制造公差应与冲裁件的尺寸精度相适应, - 般比制件的精度高2~3级,且必须按入体方向标注单向公差。
模具磨损预留量与工件制造精度有关用△ x 表示,其中△为工件的公差 值,x 为磨损系数,其值在0.5〜1之间,根据工件制造精度选取:计算原则:计算方法落料 冲孔凸、凹模制造公差工件精度IT10级以上X =1.0工件精度IT11〜13X =0.75工件精度IT14X =0.5规则形状冲裁模凸模、凹模制造偏差51、分别加工法§凸+ §凹W Z max- Z min落料D凹=(D max - X △0D凸=(D凹-Z min )二凸=(D max - X △Z min )」凸冲孔d凸=(d min + X △) 1凸d凹=(d凸+ Z min ) 0 = ( d min + X△Z min ) 0孔心距孔心距属于磨损后基本不变的尺寸,在同一工步中,在工件上冲出的孔距为L±2/2两个孔时,其凹模型孔心距L d可按下式确定。
L d =L+ —■-8:凸、「•凹一一凸、凹模制造公差,可按IT6〜IT7级来选取,或取、•凸W0.4 ( Z max- Z min ) , '•凹W0.6 ( Z max" Z min )2、单配加工法单配加工法是用凸模和凹模相互单配的方法来保证合理间隙的一种方法。
此方法只需计算基准件(冲孔时为凸模,落料时为凹模)基本尺寸及公差,另一件不需标注尺寸,仅注明“相应尺寸按凸模(或凹模)配做,保证双面间隙在Z max〜Z min之间”即可。
凸凹模尺寸计算4
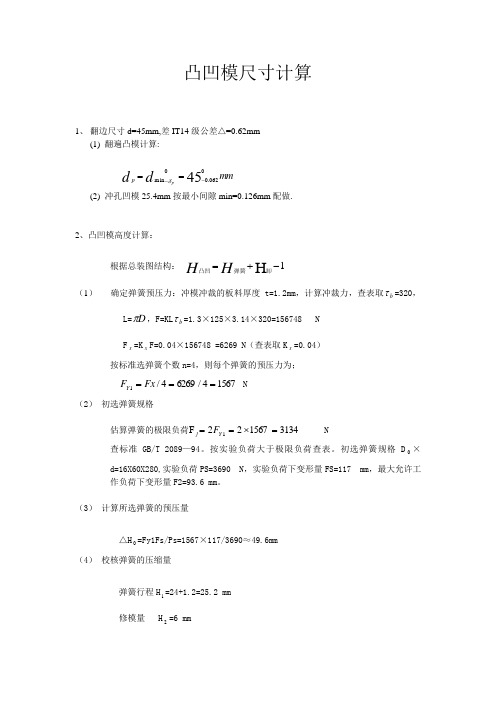
1、翻边尺寸d=45mm,差IT14级公差△=Biblioteka .62mm(1)翻遍凸模计算:
(2)冲孔凹模25.4mm按最小间隙min=0.126mm配做.
2、凸凹模高度计算:
根据总装图结构:
(1)确定弹簧预压力:冲模冲裁的板料厚度t=1.2mm,计算冲裁力,查表取 =320,L= ,F=KL =1.3×125×3.14×320=156748 N
故H +H =280+20=300 mm
取凹凸模高H=299 mm
(3) 计算所选弹簧的预压量
△H =Fy1Fs/Ps=1567×117/3690≈49.6mm
(4) 校核弹簧的压缩量
弹簧行程H =24+1.2=25.2 mm
修模量 H =6 mm
故 H = 25.2 + 6 + 49.6 =81.2mm<93.6mm
因此所选的弹簧满足要求。规格为10X60X280
F =K F=0.04×156748 =6269 N(查表取K =0.04)
按标准选弹簧个数n=4,则每个弹簧的预压力为;
N
(2) 初选弹簧规格
估算弹簧的极限负荷N
查标准GB/T 2089—94。按实验负荷大于极限负荷查表。初选弹簧规格D ×d=16X60X280,实验负荷PS=3690 N,实验负荷下变形量FS=117 mm,最大允许工作负荷下变形量F2=93.6 mm。
凸凹模(落料、拉深)尺寸计算
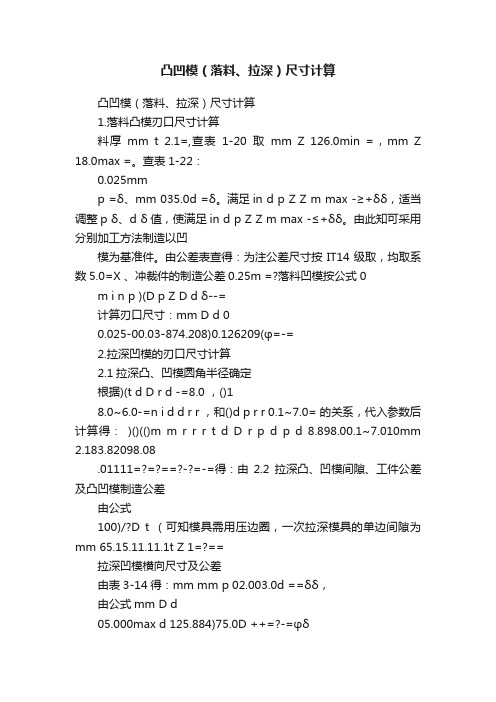
凸凹模(落料、拉深)尺寸计算凸凹模(落料、拉深)尺寸计算1.落料凸模刃口尺寸计算料厚mm t 2.1=,查表1-20取mm Z 126.0min =,mm Z 18.0max =。
查表1-22:0.025mmp =δ、mm 035.0d =δ。
满足in d p Z Z m max -≥+δδ,适当调整p δ、d δ值,使满足in d p Z Z m max -≤+δδ。
由此知可采用分别加工方法制造以凹模为基准件。
由公差表查得:为注公差尺寸按IT14级取,均取系数5.0=X 、冲裁件的制造公差0.25m =?落料凹模按公式0 m i n p )(D p Z D d δ--=计算刃口尺寸:mm D d 00.025-00.03-874.208)0.126209(φ=-=2.拉深凹模的刃口尺寸计算2.1拉深凸、凹模圆角半径确定根据)(t d D r d -=8.0 ,()18.0~6.0-=n i d d r r ,和()d p r r 0.1~7.0= 的关系,代入参数后计算得:)()(()m m r r r t d D r p d p d 8.898.00.1~7.010mm 2.183.82098.08.01111=?=?==?-?=-=得:由2.2拉深凸、凹模间隙、工件公差及凸凹模制造公差由公式100)/?D t (可知模具需用压边圈,一次拉深模具的单边间隙为mm 65.15.11.11.1t Z 1=?==拉深凹模横向尺寸及公差由表3-14得:mm mm p 02.003.0d ==δδ,由公式mm D d05.000max d 125.884)75.0D ++=?-=φδ3.1计算弹簧的预压力冲模冲裁的板料厚度t=1.2mm ,由表1-7得MPa b 350=σ,由表1-8得45.00=X K ,冲裁力:N Lt F b .22756293502.16.2656=??==σ ,所以卸料力:N F X .31124035.236211445.00=?=按标准选弹簧个数n=4,则每个弹簧的预压力为;N F F Y Y 5.731004/1.3124034/1===3.2初选弹簧规格估算弹簧的极限负荷.5N 62015.73100221=?==r j F F查标准GB/T 2089—94。
冲裁模凸凹模尺寸计算

第四章 冲裁
一、冲裁件的工艺性分析
3.冲裁件尺寸标注 冲裁件尺寸的基准应尽可能 与其冲压时定位 基准重合 ,并选 择在冲裁过程中基本上下 不变动
的面或线上。
第四章 冲裁
二、冲裁工艺方案的确定
1.冲裁工序的组合 (1)根据生产批量来确定 (2)根据冲裁件尺寸和精度等级来确定 (3)根据对冲裁件尺寸形状的适应性来确定 (4)根据模具制造安装调整的难易和成本的高低来确定 (5)根据操作是否方便与安全来确定
第四章 冲裁
一、凸、凹模刃口尺寸计算原则(续)
计算原则: 1.设计落料模先确定凹模刃口尺寸。以凹模为基准,间隙取 在凸模上,即冲裁间隙通过减小凸模刃口尺寸来取得。 设计冲孔模先确定凸模刃口尺寸。以凸模为基准,间隙取 在凹模上,冲裁间隙通过增大凹模刃口尺寸来取得。 2.根据冲模在使用过程中的磨损规律,设计落料模时,凹模 基本尺寸应取接近或等于工件的最小极限尺寸; 设计冲孔模时,凸模基本尺寸则取接近或等于工件孔的最 大极限尺寸。 模具磨损预留量与工件制造精度有关。
第四章 冲裁
二、冲裁工艺方案的确定
2、冲裁顺序的安排 (1)级进冲裁顺序的安排 1)先冲孔或冲缺口,最后落料或切断,将冲裁件与条料分离。 2)采用定距侧刃时,定距侧刃切边工序安排与首次冲孔同时进 行,以便控制送料进距。 (2)多工序冲裁件用单工序冲裁时的顺序安排 1)先落料使坯料与条料分离,再冲孔或冲缺口。 2)冲裁大小不同、相距较近的孔时,为减少孔的变形,应先冲 大孔后冲小孔。
+δ A
0 0
DT = (D A − Z min )−δ T = (Dmax − x∆ − Z min )−δ T
(2)冲孔 0 d T = (d min + x∆ )−δ T
二、落料、首次拉深复合(复合模)的主要工作部分尺寸计算1:

模具的落料凹模,凸凹模,冲孔凸模的工作关系。
对工件未注公差可按IT14计算,也可由书附录1D 查得各尺寸的未注公差。
根据表1—20(见冲压模具设计与制造)查得冲裁模刃口双间隙040.0min=Zmm , 060.0max=Zmm 。
1 工作部分尺寸的计算(1)、落料刃口尺寸计算:087.096-φ的凸凹模的制造公差由表1—22(见冲压模具设计与制造)查得mm035.0=凹δ, mm025.0=凸δ。
由于minmax06.0ZZ->=+凸凹δδ=0.060-0.040=0.02mm , 故采用凸模与凹模配合加工方法,该冲裁件属落料件,选凹模为设计基准件,采用配合加工,只需要计算落料凹模刃口尺寸及制造公差,凸模刃口尺寸根据凹模实际尺寸按间隙要求配作。
因数由表 1—23(见冲压模具设计与制造)因为冲裁件精度IT14级,查得X=0.5 ,则落料凹模的基本尺寸计算如下:mmX D D218.0087.0410410max 565.9587.05.096+⨯+∆+=⨯-=∆-=)()(凹凸D 按凹模尺寸配制,根据表1—20(见冲压模具设计与制造)查得其双面间隙为0.040~0.060mm ,该零件,5.152.0100)/( =⨯D t 所以需采用压边圈,第一次拉深凸模与凹模的单边间隙可按表3—13(见冲压模具设计与制造)中式Z=1.2t 计算得Z=0.6mm ,由于拉深工件的公差可采用IT10级精度,拉深凸模,凹模制造公差查表3—14(见冲压模具设计与制造)03.0=凸δmm 凹δ=0.02mm ,因为零件尺寸标注在外形,所以按以下公式可求拉深凸、凹模尺寸及公差如下:工件尺寸:074.04.62-φmmmmD D 02.0002.00max 845.61)74.075.04.62(75.0+++=⨯-=∆-=凹)(凹δmmZ D D 003.00max 645.60)6.0274.075.04.62()275.0(--=⨯-⨯-=-∆-=凸凸δ计算拉深凸,凹模的圆角半径 首次拉伸凹模圆角半径可按td D r )(8.01-=凹和凹凸)(r r0.1~7.0=的关系;计算首次拉深凹模与凸模的圆角半径,分别算得为:mmr28.31=凹mmr 28.31=凸其工作部分结构尺寸如图所示:二模具的总体设计及装配该工件的模具结构如图(冲压模具设计与制造见253页)主要由上下模座、上下固定板、落料凹模、凸凹模、拉深凸模、上顶件块、下推件块、压边圈卸料板、橡胶等零件组成。
各种冲压模具结构形式与设计
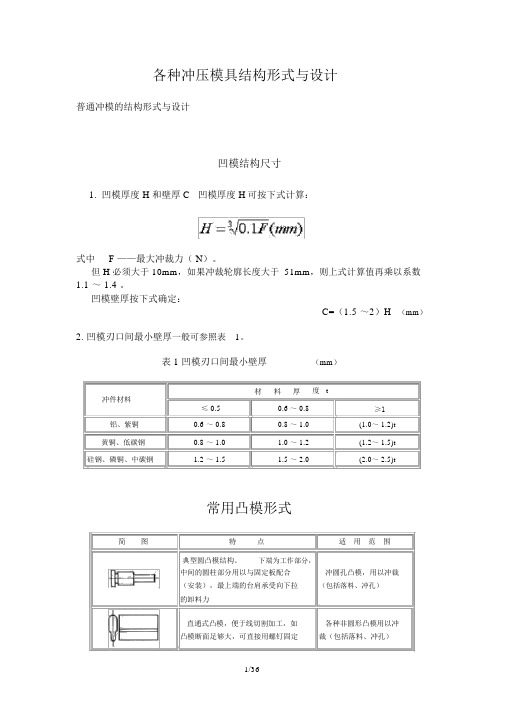
各种冲压模具结构形式与设计普通冲模的结构形式与设计凹模结构尺寸1.凹模厚度 H 和壁厚 C 凹模厚度 H可按下式计算:式中 F ——最大冲裁力( N)。
但 H 必须大于 10mm,如果冲裁轮廓长度大于 51mm,则上式计算值再乘以系数1.1 ~ 1.4 。
凹模壁厚按下式确定:C=(1.5 ~2)H(mm)2.凹模刃口间最小壁厚一般可参照表1。
表 1 凹模刃口间最小壁厚(mm)材料厚度 t冲件材料≤ 0.50.6 ~ 0.8≥1铝、紫铜0.6 ~ 0.80.8 ~ 1.0(1.0~ 1.2)t 黄铜、低碳钢0.8 ~ 1.0 1.0 ~ 1.2(1.2~ 1.5)t 硅钢、磷铜、中碳钢 1.2 ~ 1.5 1.5 ~ 2.0(2.0~ 2.5)t常用凸模形式简图特点适用范围典型圆凸模结构。
下端为工作部分,中间的圆柱部分用以与固定板配合冲圆孔凸模,用以冲裁(安装),最上端的台肩承受向下拉(包括落料、冲孔)的卸料力直通式凸模,便于线切割加工,如各种非圆形凸模用以冲凸模断面足够大,可直接用螺钉固定裁(包括落料、冲孔)断面细弱的凸模,为了增加强度和凸模受力大,而凸模相刚度,上部放大对来说强度、刚度薄弱凸模一端放长,在冲裁前,先伸入单面冲压的凸模凹模支承,能承受侧向力整体的凸模结构上部断面大,可直单面冲压的凸模接与模座固定节省贵重的工具钢或硬凸模工作部分组合式质合金组合式凸模,工作部分轮廓完整,圆凸模。
节省工作部分与基体套接定位的贵重材料冲裁凹模的刃壁形式简特点适用范围图刃壁带有斜度,冲件或废料不易滞留在刃孔内,因而减轻对刃壁的磨适用于冲件为任何形状、各损,一次刃磨量较少。
刃口尺寸随刃种板厚的冲裁模(但料太薄不磨变化宜采用)凹模工作部分强度好α一般取5′~ 30 ′刃壁带有斜度,漏料畅通,但由于适用于材料厚度小于3mm 刃壁与漏料孔用台肩过渡,因此凹模的冲裁模工作部分强度较差凹模厚度即有效刃壁高度。
刃壁带有斜度,冲件或废料不易滞留在刃孔内,因而刃壁磨损小,一次刃磨量少。
第2章冲裁模设计-4_凹模尺寸计算

(2)凹模外形尺寸(外形及紧固孔布置)1. 外形尺寸(1) 厚度尺寸)(=理mm LP H 6225.0值)修磨量(表=理实h H H 52−+小型 H 实际=10~25mm大型 H 实际≤50mm ,时加固理mm H 50>(2) 长宽尺寸(图2-28),,,理理理H W H W H W 0.25.12.1321≥≥≥两形孔之间最小壁厚不得小于5mm 。
注:W1平滑曲线到凹模边界距离,W2直线到凹模边界距离,W3复杂情况或尖端到凹模边界距离。
2. 紧固件(螺钉、圆柱销)尺寸(1) 直径与配合长度1)直径d 表2-2,通常取理H 31 2)配合长度 通常取d 5.1≥(2) 位置尺寸1)孔心-外部边距离,一般可取1.5d2)孔心-(光滑)孔边距离,一般可取1.5d 。
3)螺孔间距 一般约等于10d例题一已知某冲件如图,求凹模结构尺寸解:求外廓尺寸1. 冲裁周长L =20+20+20+10π=91.4162. 冲裁力P =1.3×91.416×1×200=23768.160(P =1.3lt τ)3. 厚度H(取整数进一位)===理1626.1525.062LP H 考虑刃磨量,据表2-5,刃口厚度h =5,21516==实+H4. 长宽尺寸(1) 边宽 W 1=1.2×16=19.2,W 2=1.5×16=24(2) 压力中心 X 0=0,Y 0=-6.6(压力中心6.656.6432144332211−≈−=++++++=l l l l y l y l y l y l y c ) (3) 长度尺寸20-6.6+W 2=37.4,10+6.6+W 1=35.8压力中心定为凹模几何中心,则凹模长度为2×37.4=74.8=75(进一位取整数)(4) 宽度尺寸20+2W 2 =68∴凹模外形尺寸为75×68×21注:通常凹模板外廓尺寸应按标准选取,可加大取为:80×80×22求紧固孔尺寸 料厚=1抗剪强度20016=5.3进一位取61. 紧固件直径:由d≈H理/3=3如内六角螺钉GB70-85 M6×L圆柱销GB119-86 A6×L A表示过度配合B表示间隙2. 紧固件长度L 紧固件配合长度L’应大于1.5d3. 紧固件位置及数量(1)距边尺寸,取1.5d=9(2)螺孔间距75-2×9=5768-2×9=50(3)销孔位置:销孔边距螺孔中心≥1.5d=9销孔中心距螺孔中心≥2d=12销孔中心距57-2×12=33。
- 1、下载文档前请自行甄别文档内容的完整性,平台不提供额外的编辑、内容补充、找答案等附加服务。
- 2、"仅部分预览"的文档,不可在线预览部分如存在完整性等问题,可反馈申请退款(可完整预览的文档不适用该条件!)。
- 3、如文档侵犯您的权益,请联系客服反馈,我们会尽快为您处理(人工客服工作时间:9:00-18:30)。
凸凹模(落料、拉深)尺寸计算
1.落料凸模刃口尺寸计算
料厚mm t 2.1=,查表1-20取mm Z 126.0min =,mm Z 18.0max =。
查表1-22:
0.025mm
p =δ、mm 035.0d =δ。
满足in d p Z Z m max -≥+δδ,适当调整p δ、d δ值,使满足in d p Z Z m max -≤+δδ。
由此知可采用分别加工方法制造以凹
模为基准件。
由公差表查得:为注公差尺寸按IT14级取,均取系数5.0=X 、冲裁件的制造公差0.25m =∆落料凹模按公式0
m i n p )(D p Z D d δ--=
计算刃口尺寸:mm D d 0
0.025-00.03-874.208)0.126209(φ=-=
2.拉深凹模的刃口尺寸计算
2.1拉深凸、凹模圆角半径确定
根据)(t d D r d -=8.0 ,()1
8.0~6.0-=n i d d r r ,和()d p r r 0.1~7.0= 的关系,代入参数后计算得: )()(()m m r r r t d D r p d p d 8.898.00.1~7.010mm 2.183.82098.08
.01111=⨯=⨯==⨯-⨯=-=得:由 2.2拉深凸、凹模间隙、工件公差及凸凹模制造公差
由公式
100)/⨯D t (可知模具需用压边圈,一次拉深模具的单边间隙为mm 65.15.11.11.1t Z 1=⨯==
拉深凹模横向尺寸及公差
由表3-14得:mm mm p 02.003.0d ==δδ,
由公式mm D d
05.000max d 125.884)75.0D ++=∆-=φδ
3.1计算弹簧的预压力
冲模冲裁的板料厚度t=1.2mm ,由表1-7得MPa b 350=σ,由表1-8得45.00=X K ,
冲裁力:N Lt F b .22756293502.16.2656=⨯⨯==σ ,所以
卸料力:N F X .31124035.236211445.00=⨯=
按标准选弹簧个数n=4,则每个弹簧的预压力为;
N F F Y Y 5.731004/1.3124034/1===
3.2初选弹簧规格
估算弹簧的极限负荷.5N 62015.73100221=⨯==r j F F
查标准GB/T 2089—94。
按实验负荷大于极限负荷查表。
初选弹簧规格2807012⨯⨯=⨯⨯O H D d ,实验负荷Ps=7170N ,实验负荷下变形量Fs=128mm ,最大允许工作负荷下变形量F2=202mm 。
3.3计算所选弹簧的预压量
mm P F F H S S Y Y 55.367170/1285.73100/1=⨯==
3.4校核弹簧的压缩量
卸料板的工作行程hx=t+h1+1=1.2+26.5+1=28.7mm 取凸模刃口修模量hm=6mm ,则弹簧工作时的总压缩量为
h=hy+hx+hm=55.36+28.7+6=90.06mm ,因为h<F2=202mm ,故所选弹簧合适。
弹簧标记为:YA 2807012⨯⨯ GB/T2089-94
3.5弹簧的安装高度
Ha=H0-hY=280-55.36=224.64mm ,取225mm
查国标GB2873.3-81得:上固定板厚度为28mm、弹簧安装高度为225mm、卸料板厚度为22mm。
凸凹模高度:
1-=
+
+
=
225
=
22
mm
1-
H
H
H246
弹
卸。