车螺纹的方法
数控车如何加工螺纹【共18张PPT】
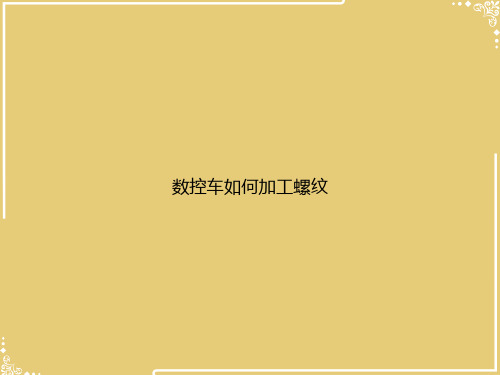
30
1 .5 O
70
3 Z
程序如下: O0308; N020 G00 U-62.0;
N021 G32 W-74.5 F4.0 ;
N022 G00 U62.0;
N023 W74.5; N024 U-64.0;
N025 G32 W-74.5; N026 G00 U64.0; N027 W74.5;
例:如下图所示圆锥螺纹,螺纹导程为1.5 mm。δ1=2 mm , δ2=1mm。 试编写螺纹加工程序
0.6
0.6
0.6
0.6
0.6
用G32加工螺纹时,由于机床伺服系统本身具有滞后特性,会在起始段和停止段发生螺纹的螺距不规则现象,故应考虑刀具的引入长度和超越长度,整个被加工螺纹的长度应该是引入长度、超越长度和
量 4 次 螺纹长度之和。
G32 W.
0.16
0.4
0.4
0.4
0.6
0.6
及 5 次 该指令的循环路线与前述的G90指令基本相同,只是F后面的进给量改为螺纹导程即可。
δ1=2 mm , δ2=1mm。
0.1
0.4
0.4
0.4
0.4
三、等螺距螺纹切削指令G32
四、简单螺纹切切削循6环指次令G92
0.15
0.4
0.4
0.4
削 7 次 D为第一次循环时的切削深度;
三、等螺距螺纹切削指令G32
N026 G00 U64.
次8次
0.2
0.2
0.4
0.15
0.3
数9次
0.2
例:如图所示是圆柱螺纹加工实例,螺距为4 mm,第一次 和第二次单边切削量均为1 mm,引入长度 为3 mm,超越长度为1.5 mm。
车螺纹的方法

车螺纹简介(图)将工件表面车削成螺纹的方法称为车螺纹。
螺纹按牙型分有三角螺纹、梯形螺纹、方牙螺纹等(图1)。
其中普通公制三角螺纹应用最广。
图1 螺纹的种类1. 普通三角螺纹的基本牙型普通三角螺纹的基本牙型如图2所示,各基本尺寸的名称如下:图2 普通三角螺纹基本牙型D—内螺纹大径(公称直径);d—外螺纹大径(公称直径);D2 —内螺纹中径;d2—外螺纹中径;D1 —内螺纹小径;d1—外螺纹小径;P—螺距;H-原始三角形高度。
决定螺纹的基本要素有三个:牙型角α 螺纹轴向剖面内螺纹两侧面的夹角.公制螺纹α=60o,英制螺纹α=55o。
螺距P 它是沿轴线方向上相邻两牙间对应点的距离.螺纹中径D2(d2)它是平螺纹理论高度H的一个假想圆柱体的直径。
在中径处的螺纹牙厚和槽宽相等。
只有内外螺纹中径都一致时,两者才能很好地配合.从图上可以看出:车削外螺纹时,应该将外径车削为:车削外螺纹外径=公称直径-2*H/8其中H为螺纹原始三角形高度,计算公式为H=0.866*P(P为螺距,根据手册可以查出)车削内螺纹时,孔径应为:车削内螺纹孔径=公称直径-2*5/8H *5/8=0。
625 1/8=0。
125以车削方式制作M20X2.5的粗牙螺纹为例:螺栓坯料外径=20—2*((0。
866*2.5)/8)=19.46螺母坯料内径=20-2*((0。
866*2.5)*5/8)=17。
29这样车制出来的螺纹仅仅是牙面配合,不会出现牙顶与牙底干涉的情况。
使用板牙、丝锥做作螺纹时,由于加工时的挤压作用,因此上述公式不能适合(根据材料不同而选择另外的公式2. 车削外螺纹的方法与步骤(1)准备工作1)安装螺纹车刀时,车刀的刀尖角等于螺纹牙型角α=60o,其前角γo=0o才能保证工件螺纹的牙型角,否则牙型角将产生误差。
只有粗加工时或螺纹精度要求不高时,其前角可取γo=5o~20o。
安装螺纹车刀时刀尖对准工件中心,并用样板对刀,以保证刀尖角的角平分线与工件的轴线相垂直,车出的牙型角才不会偏斜。
螺纹加工方法详细讲解
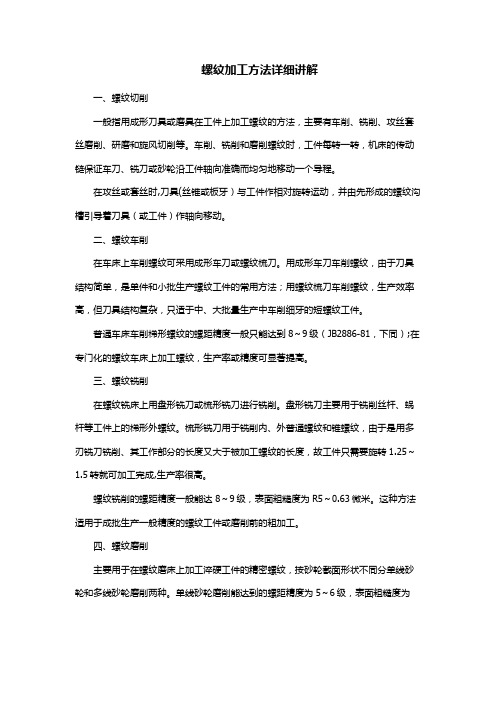
螺纹加工方法详细讲解一、螺纹切削一般指用成形刀具或磨具在工件上加工螺纹的方法,主要有车削、铣削、攻丝套丝磨削、研磨和旋风切削等。
车削、铣削和磨削螺纹时,工件每转一转,机床的传动链保证车刀、铣刀或砂轮沿工件轴向准确而均匀地移动一个导程。
在攻丝或套丝时,刀具(丝锥或板牙)与工件作相对旋转运动,并由先形成的螺纹沟槽引导着刀具(或工件)作轴向移动。
二、螺纹车削在车床上车削螺纹可采用成形车刀或螺纹梳刀。
用成形车刀车削螺纹,由于刀具结构简单,是单件和小批生产螺纹工件的常用方法;用螺纹梳刀车削螺纹,生产效率高,但刀具结构复杂,只适于中、大批量生产中车削细牙的短螺纹工件。
普通车床车削梯形螺纹的螺距精度一般只能达到8~9级(JB2886-81,下同);在专门化的螺纹车床上加工螺纹,生产率或精度可显著提高。
三、螺纹铣削在螺纹铣床上用盘形铣刀或梳形铣刀进行铣削。
盘形铣刀主要用于铣削丝杆、蜗杆等工件上的梯形外螺纹。
梳形铣刀用于铣削内、外普通螺纹和锥螺纹,由于是用多刃铣刀铣削、其工作部分的长度又大于被加工螺纹的长度,故工件只需要旋转1.25~1.5转就可加工完成,生产率很高。
螺纹铣削的螺距精度一般能达 8~9级,表面粗糙度为R5~0.63微米。
这种方法适用于成批生产一般精度的螺纹工件或磨削前的粗加工。
四、螺纹磨削主要用于在螺纹磨床上加工淬硬工件的精密螺纹,按砂轮截面形状不同分单线砂轮和多线砂轮磨削两种。
单线砂轮磨削能达到的螺距精度为5~6级,表面粗糙度为R1.25~0.08微米,砂轮修整较方便。
这种方法适于磨削精密丝杠、螺纹量规、蜗杆、小批量的螺纹工件和铲磨精密滚刀。
多线砂轮磨削又分纵磨法和切入磨法两种。
纵磨法的砂轮宽度小于被磨螺纹长度,砂轮纵向移动一次或数次行程即可把螺纹磨到最后尺寸。
切入磨法的砂轮宽度大于被磨螺纹长度,砂轮径向切入工件表面,工件约转1.25转就可磨好,生产率较高,但精度稍低,砂轮修整比较复杂。
切入磨法适于铲磨批量较大的丝锥和磨削某些紧固用的螺纹。
车螺纹的技巧

3.为什么螺纹车削要求如此之高螺纹车削的要求要高于普通车削操作。
切削力一般较高,螺纹刀片的切削端部半径较小,比较薄弱。
在螺纹加工中,进给速度必须与螺纹的节距精确对应。
对于节距为8螺纹/英寸(tpi)的情况,刀具必须以8转/英寸或者0.125英寸/转的进给速度前进。
与普通车削应用(其中典型的进给速度大约为0.012ipr)相比,螺纹车削的进给速度要高出10倍。
螺纹加工刀片刀尖处的作用力可能要高100~1,000倍。
图2:多齿刀片,在一个系列中带有多个齿,螺纹加工效率可能会提高,但切削力较高。
承受这种作用力的端部半径一般为0.015英寸,而常规车削刀片的半径为0.032英寸。
对于螺纹加工刀片,该半径受许可的螺纹形状根部半径(其大小由相关螺纹标准规定)的严格限制。
它还受所需要的切削动作限制,因为材料无法经受普通车削中的剪切过程,否则会发生螺纹变形。
切削力较高和作用力聚集范围较窄导致的结果是:螺纹加工刀片要承受比一般车刀高得多的应力。
部分与全轮廓刀片的比较部分轮廓刀片,有时候被称作“非加支持式”刀片,它在不给螺纹加支持或装牙支持的情况下切削螺纹沟槽。
(参见图1)一把刀片可以产生一系列螺纹,直至最粗的节距-即每英寸螺纹数最少处为止-这是刀片端部半径强度许可的。
这种端部半径设计得足够小,刀片可以加工各种节距。
对于小节距,端部半径会显得尺寸过小。
这意味着刀片必须穿透得深一些。
例如,用一把部分轮廓刀片加工一个8tpi的螺纹需要螺纹深度为0.108英寸,而用完全轮廓刀片产生的相同螺纹则只需要0.81英寸的指定深度。
因此,全轮廓刀片可以产生强度更高的螺纹。
此外,全轮廓刀片加工出螺纹的操作可以少4道。
多齿刀片多齿刀片连续地带有系列齿,任何齿在螺纹沟槽中切削的深度都要比它前面的一个齿更深。
(参见图2)借助这些刀片,加工一个螺纹所需要的操作道数可以减少80%。
刀具寿命要远远长于单支持尖刀片,因为最终的齿只加工某个给定螺纹一半或三分之一的金属。
车螺纹
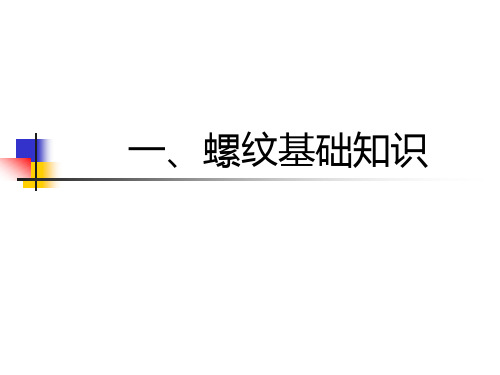
例:
T0202;(退刀槽加工) S400; G00 X22.0 Z-19.0; G75 R0.5; G75 X16.0 Z-20.0 P1000 Q1000
F20.0; G00 X100.0 Z50.0; T0303;(螺纹加工) G00 X22.0 Z2.0; G76 P020060 Q100 R300; G76 X16.75 Z-18.0 P1624 Q500 F2.5; G00 X100.0 Z50.0; T0202;(工件切断) S200; G00 X40.0 Z-53.0; G01 X2.0 F20.0; X40.0; G00 X100.0 Z50.0; M05; M30;
Z-30; N20 X35; G70 P10 Q20; G00 G40 X100 Z50;
T0202 S300;(退刀槽加工) G00 X35 Z-30; G01 X26 F30; G04 X4; G01 X35; G00 X100 Z50;
T0303; M03 S400; G00 X29.1 Z5 ; G32 Z-28 F2; G00 X31;
试用G32指令编写螺纹加工程序。
2、螺纹切削循环 G92
格式:
G92 X(U)_Z(W)_R_F_;
锥螺纹起点半径与 终点半径的差值
用G92进行圆柱螺纹加工
45°
X
Z
W
4(R)
3(F) 2(F)
R
1(R)
O
XU 22
R<0
Z
用G92进行圆锥螺纹加工
例:
T0303; M03 S400; G00 X29.1 Z5 ; G32 Z-28 F2; G00 X31;
公制螺纹 2.0
1.299 0.9 0.6 0.6
普车螺纹操作方法
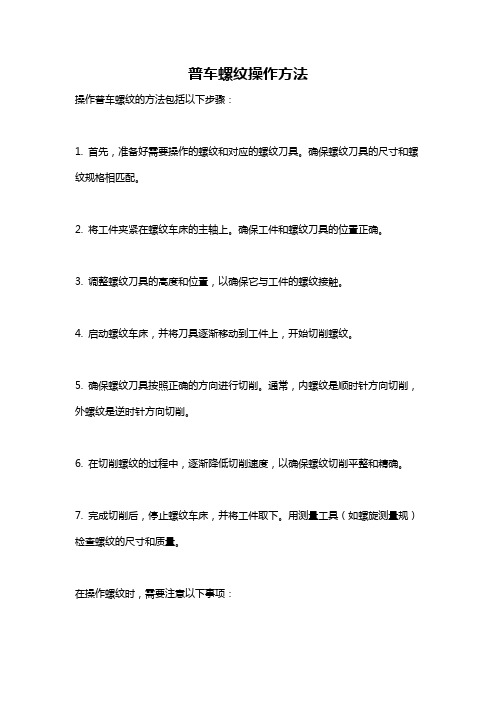
普车螺纹操作方法
操作普车螺纹的方法包括以下步骤:
1. 首先,准备好需要操作的螺纹和对应的螺纹刀具。
确保螺纹刀具的尺寸和螺纹规格相匹配。
2. 将工件夹紧在螺纹车床的主轴上。
确保工件和螺纹刀具的位置正确。
3. 调整螺纹刀具的高度和位置,以确保它与工件的螺纹接触。
4. 启动螺纹车床,并将刀具逐渐移动到工件上,开始切削螺纹。
5. 确保螺纹刀具按照正确的方向进行切削。
通常,内螺纹是顺时针方向切削,外螺纹是逆时针方向切削。
6. 在切削螺纹的过程中,逐渐降低切削速度,以确保螺纹切削平整和精确。
7. 完成切削后,停止螺纹车床,并将工件取下。
用测量工具(如螺旋测量规)检查螺纹的尺寸和质量。
在操作螺纹时,需要注意以下事项:
1. 确保使用合适的刀具和工件夹具,以防止刀具断裂或工件脱离夹具。
2. 切削过程中,保持螺纹刀具和工件之间的冷却润滑,以提高切削效率和延长刀具寿命。
3. 调整螺纹刀具的位置和切削力,以确保切削过程平稳和均匀。
4. 定期检查螺纹刀具的磨损情况,及时更换磨损严重的刀具。
5. 在操作过程中,遵循安全规范,保持工作环境整洁有序,以确保操作人员的安全。
车螺纹的步骤与方法
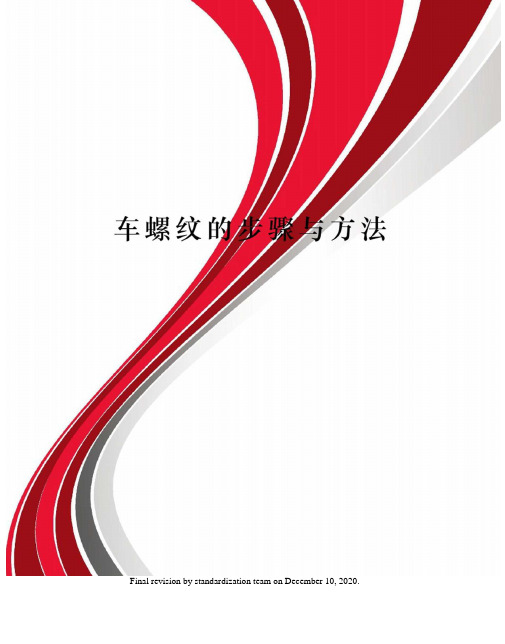
Final revision by standardization team on December 10, 2020.车螺纹的步骤与方法:(低速车削三角形螺纹V < 5米/分)1、车螺纹前对工件的要求:1)螺纹大径:理论上大径等于公称直径,但根据与螺母的配合它存在有下偏差(一),上偏差为0;因此在加工中,按照螺纹三级精度要求。
螺纹外径比公称直径小。
螺纹外径D二公称直径一2)退刀槽:车螺纹前在螺纹的终端应有退刀槽,以便车刀及时退出。
3)倒角:车螺纹前在螺纹的起始部位和终端应有倒角,且倒角的小端直径C螺纹底径。
4)牙深高度(切削深度):hl二2、调整车床:先转动手柄接通丝杠,根据工件的螺距或导程调整进给箱外手柄所示位置。
调整到各手柄到位。
3、开车、对刀记下刻度盘读数,向右退出车刀。
4、合上开合螺母,在工件表面上车出一条螺旋线,横向退出车刀,并开反车把车刀退到右端,停车检查螺距是否正确(钢尺)。
5、开始切削,利用刻度盘调整切深(逐渐减小切深)。
注意操作中,车刀将终了时应做好退刀、停车准备,先快速退出车刀,然后开反车退回刀架。
吃刀深度控制,粗车时t「,精车时t < O六、螺纹的测量:1、单向测量法:1)顶径的测量:螺纹顶径的尺寸,一般都允许有较大的误差,外螺纹顶径可用游标卡尺或千分尺测量,内螺纹顶径可用游标卡尺测量。
2)螺距的测量:螺距一般可用钢尺测量,3)中径的测量:(1)用螺纹千分尺测量螺纹中径。
(2)用三针法测量螺纹中径。
三针法测量螺纹中径是一种比较精密的测量方法。
2、综合测量法:综合测量法就是对螺纹的各项尺寸用螺纹量规进行综合性的测量七、安全生产:1)车螺纹前检查车床正反车操纵机构及开合螺母等,以防操作失灵。
2)在吃刀时注意不要多摇进一圈,否则会发生车刀撞坏,工件顶弯或飞出等事故。
3)不能用手模螺纹表面,更不能用棉纱去擦正在旋转的螺纹工件,以防发生事故。
车螺纹的步骤与方法:(低速车削三角形螺纹V C 5米/分)1、车螺纹前对工件的要求:1)螺纹大径:理论上大径等于公称直径,但根据与螺母的配合它存在有下偏差(一),上偏差为0;因此在加工中,按照螺纹三级精度要求。
车螺纹方法
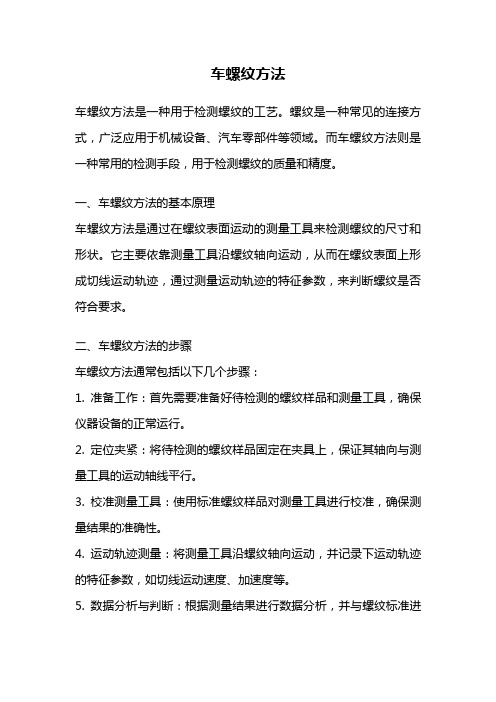
车螺纹方法车螺纹方法是一种用于检测螺纹的工艺。
螺纹是一种常见的连接方式,广泛应用于机械设备、汽车零部件等领域。
而车螺纹方法则是一种常用的检测手段,用于检测螺纹的质量和精度。
一、车螺纹方法的基本原理车螺纹方法是通过在螺纹表面运动的测量工具来检测螺纹的尺寸和形状。
它主要依靠测量工具沿螺纹轴向运动,从而在螺纹表面上形成切线运动轨迹,通过测量运动轨迹的特征参数,来判断螺纹是否符合要求。
二、车螺纹方法的步骤车螺纹方法通常包括以下几个步骤:1. 准备工作:首先需要准备好待检测的螺纹样品和测量工具,确保仪器设备的正常运行。
2. 定位夹紧:将待检测的螺纹样品固定在夹具上,保证其轴向与测量工具的运动轴线平行。
3. 校准测量工具:使用标准螺纹样品对测量工具进行校准,确保测量结果的准确性。
4. 运动轨迹测量:将测量工具沿螺纹轴向运动,并记录下运动轨迹的特征参数,如切线运动速度、加速度等。
5. 数据分析与判断:根据测量结果进行数据分析,并与螺纹标准进行比较,判断螺纹是否符合要求。
6. 结果记录:将测量结果记录下来,包括测量数据、判断结果等。
三、车螺纹方法的应用领域车螺纹方法广泛应用于机械制造、汽车零部件等领域。
在机械制造中,螺纹是一种重要的连接方式,螺纹的质量和精度直接影响到机械设备的性能和可靠性。
因此,通过车螺纹方法对螺纹进行检测,可以确保产品质量,提高生产效率。
在汽车零部件制造中,车螺纹方法也扮演着重要的角色,用于检测发动机、底盘、传动系统等零部件的螺纹质量。
四、车螺纹方法的优势和局限性车螺纹方法具有以下优势:1. 非接触式测量:车螺纹方法采用非接触式测量,不会对螺纹表面造成损伤。
2. 高精度测量:车螺纹方法可以实现对螺纹尺寸和形状的高精度测量,确保产品质量。
3. 高效率:车螺纹方法可以实现对大批量产品的快速检测,提高生产效率。
然而,车螺纹方法也存在一定的局限性:1. 对设备要求高:车螺纹方法需要使用专门的测量设备,对设备的要求较高。
- 1、下载文档前请自行甄别文档内容的完整性,平台不提供额外的编辑、内容补充、找答案等附加服务。
- 2、"仅部分预览"的文档,不可在线预览部分如存在完整性等问题,可反馈申请退款(可完整预览的文档不适用该条件!)。
- 3、如文档侵犯您的权益,请联系客服反馈,我们会尽快为您处理(人工客服工作时间:9:00-18:30)。
抬闸法
利用开合螺母的压下和抬起来车削螺纹。
正反车车削法
抬闸法
退刀方式
利用丝杆的反转纵向返回起点
手动纵向返回起点
适用范围
适用于任何螺距的加工
只适用于丝杆螺距是工件螺距整数倍时
螺纹车削进刀方式:
加工方法
加工示意
加工特点
适用范围
直进法
垂直进刀,两刀பைடு நூலகம்同时车削
适用于小螺距螺纹的加工
左右车削法
垂直进刀+小刀架左右移动,只有一条刀刃切削
2、防止“扎刀”
【加工余量分配不合理,或一次车削的余合理分多,而使螺纹两侧面粗糙严重甚至崩刃。】
工件、刀具装夹合理分配余量,选择合适的进刀方法及时退刀。
车螺纹的方法
常用的切削加工方法:
车螺纹
铣螺纹
工艺流程:
车端面一车螺纹大径(d<公称直径)一车退刀槽(<螺纹小径)→倒角→车螺纹(多刀车削)
安装技巧:
安装工件
选择合适的夹紧位置。
有足够的夹紧力。
安装刀具:
安装要点:刀尖分角线垂直于工件轴线。
机床调整:
针对螺纹车削
调整主轴转速
调整螺距
螺纹车削操作方法与步骤:
适用于所有螺距螺纹的加工
斜进法
垂直进刀+小刀架向一个方向移动
适用于较大螺距螺纹的粗加工
注意事项:
1、避免“乱扣”
【如果后一刀未能准确的落在前一刀已车出的反车的方法螺纹槽中,造成工件报废。】
若丝杠螺距不是工件螺距的整数位,须用正反车的方法采取倒顺车进行车削.
工件与主轴之间的相对位置不能变动。
如果换刀或磨刀,则应重新对刀。