制动器制动力矩的改善措施
汽车制动性能的评价及改进措施
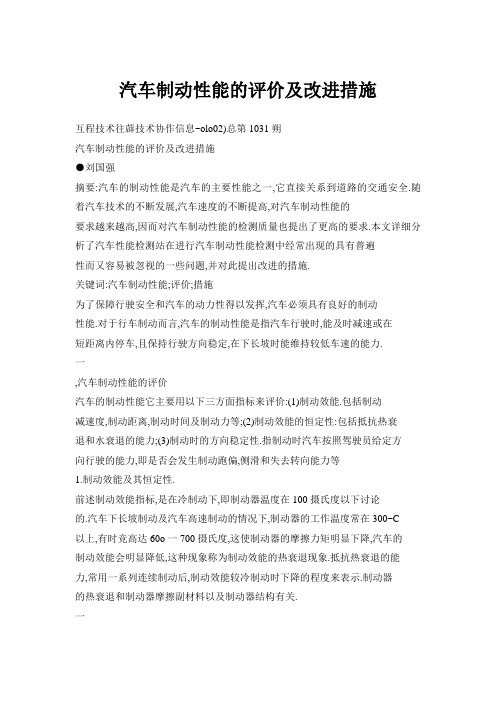
汽车制动性能的评价及改进措施互程技术往薜技术协作信息~olo02)总第1031朔汽车制动性能的评价及改进措施●刘国强摘要:汽车的制动性能是汽车的主要性能之一,它直接关系到道路的交通安全.随着汽车技术的不断发展,汽车速度的不断提高,对汽车制动性能的要求越来越高,因而对汽车制动性能的检测质量也提出了更高的要求.本文详细分析了汽车性能检测站在进行汽车制动性能检测中经常出现的具有普遍性而又容易被忽视的一些问题,并对此提出改进的措施.关键词:汽车制动性能;评价;措施为了保障行驶安全和汽车的动力性得以发挥,汽车必须具有良好的制动性能.对于行车制动而言,汽车的制动性能是指汽车行驶时,能及时减速或在短距离内停车,且保持行驶方向稳定,在下长坡时能维持较低车速的能力.一,汽车制动性能的评价汽车的制动性能它主要用以下三方面指标来评价:(1)制动效能.包括制动减速度,制动距离,制动时间及制动力等;(2)制动效能的恒定性:包括抵抗热衰退和水衰退的能力;(3)制动时的方向稳定性.指制动时汽车按照驾驶员给定方向行驶的能力,即是否会发生制动跑偏,侧滑和失去转向能力等1.制动效能及其恒定性.前述制动效能指标,是在冷制动下,即制动器温度在100摄氏度以下讨论的.汽车下长坡制动及汽车高速制动的情况下,制动器的工作温度常在300~C以上,有时竞高达60o一700摄氏度,这使制动器的摩擦力矩明显下降,汽车的制动效能会明显降低,这种现象称为制动效能的热衰退现象.抵抗热衰退的能力,常用一系列连续制动后,制动效能较冷制动时下降的程度来表示.制动器的热衰退和制动器摩擦副材料以及制动器结构有关.一般制动器是以铸铁作制动鼓,石棉摩擦材料作摩擦片组成的.制动鼓的合金成分,金属组织,硬度,工艺等要求合格的条件下,摩擦片对摩擦性能起决定作用.在一般情况下制动时,石棉摩擦片与制动鼓的摩擦系数为O.3—O.4.此时摩擦系数是稳定的.在连续强烈制动及高速制动的情况下,摩擦片温度过高,其内含的有机物发生分解,产生了一些气体和液体.它们在两接触面间形成有润滑作用的薄膜,使摩擦系数下降,而出现了热衰退制动器的结构形式对抗热衰退的能力有较大的影响.常用制动器效能因数与摩擦系数的曲线来说明各种制动器的效能及其稳定程度.双向自动增力蹄及双增力蹄式制动器,由于结构上的几何力学关系产生增力作用,具有较大的制动效能因数.摩擦系数变大时,制动效能按非线性关系迅速增加.故摩擦系数的微小变化,能引起制动效能的大幅度改变,即制动器工作的稳定性差.双减力蹄式制动器因为有减力作用,制动效能因数低,但制动效能因数随摩擦系数变化而改变的量很小, 即稳定性较好.增减力蹄式介于两者之间.这里特别要指出的是盘式制动器.盘式制动器的制动效能没有鼓式的大,但其稳定性最好.高强度制动时摩擦系数虽因热衰退而有所下降,但对制动效能的影响却不大.汽车涉水后,由于制动器被水浸湿,制动效能也会降低,为缓解这种现象,汽车涉水后,应踩几脚制动踏板,使制动蹄与制动鼓间因摩擦而产生热量,使制动器迅速干燥,制动效能恢复正常.制动过程中有时会出现制动跑偏,侧滑, 使汽车失去控制而离开规定行驶方向.汽车在制动过程中维持直线行驶能力, 或按预定弯道行驶的能力,制动时原期望汽车按直线方向减速停车,但有时汽车却自动向左或向右偏驶,这种现象称为"制动跑偏".跑偏现象多数是由于技术状况不正常造成的,经过维修调整是可以消除的.产生制动跑偏的主要原因是在制动过程中,左,右轮地面制动力增大的快慢不一致,左,右轮地面制动力不等.特别是前轴左,右轮制动力不等,是产生制动跑偏的主要原因,侧滑是指汽车制动时,某一轴的车轮或两铀的车轮发生横向滑动的现象:最危险的情况是在高速制动时,后轴发生侧滑,这时汽车常发生不规则的急剧回转运动,使之部分地或完全失去操纵.侧滑产生的原因是在制动过程中,地面制动力达到附着极限后,继续增加制动力,车轮将处于抱死拖滑状态.此时,侧向附着系数为零,即该轮抵抗侧向干扰的能力为零,这时,即使车轮受到任何一点侧向力, 都会引起沿侧向力方向的滑动.在紧急制动过程中,常出现一根轴的侧滑.实践证明,后论侧滑具有很大的危险性,可以使汽车掉头;前轴侧滑对汽车行驶方向改变不大,但是已不能用转向盘来控制汽车的行驶方向.2.以汽车前轮抱死拖滑和后轮抱死拖滑两种运动情况进行分析.图1汽车侧滑时的运动状况(a)前轴侧滑;(b)后轴侧滑图1(b)是前轴滚动,后轴制动到抱死拖滑,如有侧向力作用,后轴将发生侧滑,u8与汽车纵轴线夹角为a,uA的方向仍按汽车纵轴线方向.此时汽车也发生回转运动,作用于重心c的圆周运动惯性力Fi,此时却与后轴侧滑方向一致.惯性力Fi加剧后轴侧滑;后轴侧滑又加剧惯性力,汽车将急剧转动.因此后轴侧滑是一种不稳定状态.二,提高制动性能的措施如何更有效地利用汽车前后轴制动器制动力,即提高汽车制动系的制动效率,以及如何保证汽车制动时有较好的方向稳定性,这是涉及总制动器制动力在前后轴间的分配的一个问题.1.制动力的调节.汽车制动时,为了防止后轮抱死而发生危险的侧滑.在汽车制动系中装有各种压力调节装置,以改变后轮制动油压,从而控制后轮制动器制动力,实现制动的平顺性和稳定性.常用的压力调节装置有限压阀,比例阀,载荷控制比例阀,载荷控制限压阀等组成.2.车轮的防抱死控制系统.前轮在制动过程中出现抱死,从而使汽车失去转向能力性,轿车和部分客车采用了制动防抱系统(ARS).制动防抱系统(ABs)由三部分组成:传感器,电子控制单元和制动压力调节器.汽车制动时,制动主缸中的调压活塞被一个较大的弹簧力推至左端,活塞顶端有一推杆顶开单向阀,使制动主缸与制动轮缸之间的管路接通.此时系统处于常规制动状态,主缸直接控制制动器制动压力的增减.制动过程中,控制器不断分析传感器测出的车轮运动参数.在汽车制动过程中,若ECU判断出车轮即将出现抱死时,立即给制动压力调节器发出减低分泵油压信号,以减少制动器制动力.由控制器发出的电脉冲信号,使电磁线圈产生吸力,电磁阀内的柱塞移到右边,蓄能器中储存的高压液体,通过管路作用在调压活塞的左侧,产生一个与弹簧力方向相反的作用力,使调压活塞右移,单向阀关闭,主缸和轮缸间通路被切断.因调压活塞右移而使轮缸侧容积增加,制动压力减小.制动解除后,车轮转速增加,控制器又下令再制动,柱塞回到最左端位置,作用在调压活塞左侧的高压被解除,调压活塞左移,调压活塞左侧制动掖进入储液器,同时制动主缸和制动轮缸的管路相通.轮缸侧容积增加量在此期间减小,制动压力增加至初始值,重新制动,这种压力升降循环的频率应足够高,以适应路面不断的变化,每秒可达l0~l2次.参考文献【1】朱灵安;前桥制动装置效能及检测系统研究【Dl;浙江大学;2007年【2】李冰;汽车制动性能仿真与动态检测技术研究【D】;东北林业大学;2005年【3】肖洪涛;汽车安全性能检测系统的研究『D】;吉林大学;2006年(作者单位:黑龙江省宝泉岭交通局)154。
电磁制动器的调整方法和要求

电磁制动器的调整方法和要求电磁制动器是一种常见的制动器件,广泛应用于各种机械设备中。
为了保证电磁制动器的正常运行和性能发挥,需要进行调整和维护。
本文将介绍电磁制动器的调整方法和要求。
一、调整方法1. 调整螺栓松紧度:电磁制动器通常通过螺栓固定在机械设备上。
在使用过程中,螺栓可能会松动,影响制动器的工作效果。
因此,需要定期检查螺栓的松紧度,并进行调整。
调整时,应使用扳手适度拧紧螺栓,确保制动器与机械设备之间的连接牢固可靠。
2. 调整制动力矩:电磁制动器的制动力矩需要根据具体使用需求进行调整。
一般来说,制动力矩应满足机械设备的制动要求,既要能够快速停止设备运动,又要避免过大的制动力矩对设备造成损伤。
调整制动力矩时,可以通过增加或减小电磁制动器的电流来实现。
3. 调整制动间隙:制动间隙是指电磁制动器在脱离电源后,制动摩擦片与制动盘之间的距离。
制动间隙的大小直接影响电磁制动器的制动灵敏度和制动效果。
调整制动间隙时,可以通过调整制动器上的调整螺栓或刀片来实现。
一般来说,制动间隙应尽量小,但不能太小,以免制动器长期接触制动盘而损坏。
二、调整要求1. 定期检查:电磁制动器应定期进行检查和调整,以确保其正常工作。
检查时,应注意制动器的固定件、电源连接、制动片和制动盘的磨损情况等。
2. 维护清洁:电磁制动器在使用过程中,会因为灰尘、油污等物质的积累而影响其工作效果。
因此,应定期清洁电磁制动器,保持其表面干净。
3. 防止过热:电磁制动器在长时间工作时,会产生较大的热量。
为了避免过热对制动器的损坏,应注意制动器的散热性能。
可以通过增加散热片或安装风扇等方式来提高制动器的散热效果。
4. 注意安装位置:电磁制动器的安装位置也会影响其工作效果。
应选择通风良好、温度适宜的位置进行安装,避免受到外界环境的干扰。
5. 注意电源电压:电磁制动器的工作效果与电源电压密切相关。
应确保电源电压稳定,并符合电磁制动器的额定电压要求。
电磁制动器的调整方法和要求是保证其正常工作和性能发挥的重要保证。
气压盘式制动器制动力矩的改进设计

5结束语
5 l 嘻4 两 2 0 . 2 _ 刍 0 65 i
维普资讯
技 术 与 研 究
2影 响因素分析
2 1制动输 入力的影响 . 从公式 ( )分析 可知 , 1 增大 制
动输入力就可 以直接增加制动力矩 , 但要根据情况具体分析 。
图1
( )摩擦 系数 。 4 供 的制动力 矩在 16 N ・ 以下 , 率 ;r一制动器制动半径 。 .万 m 其 中气 室推 力和增力 比两项的 不能满足 1 t 以上 载重车辆的制动 3 从 图上可 以看 出, B整体传 AD 制动力传递效率高 。 影 影响性质相 同 , 即增加制动输入力 , 需求。目前国外适用于 2 . 英寸车 递机构简单 , 25 轮较先进的产品制动力矩一般都在 响制动力矩的因素主要有以下几点 : 制动器 制动半 径是设 计尺寸 ,受轮 辋尺 寸和制动 器 外形尺寸 的约束 , ( )气室推力 F; 1 22 N ・ .万 m左右 , 我公 司受 国内制 摩 擦系数与选 择的摩擦材料 的特性 ( )增力 比i 2 ; 动厂家委托 ,对 ADB产 品进行改
进 ,以期增大其制动力矩 。
( )制动器制动半径 r 3 ;
有关。
融资、物业开发 、外部协调及运营 确保设计工作 的成果 达到优质 、高 设计企业之 间要有能力互补与组合、 效 、经济及合理 的 目标 。 管理方面的工作 ,适应 当今工程建 结 盟、合作 ,在分工与协作 中求生 设 “ 小业主 ,大社会”的发展 方向。 存与发展 ,这是适应市场需求的虚 设计总承包单位是全面 负责整个建 设项 目设计工作 的管理 和控 制 ,其 拟组织成员之 间为达到 同一 目标的 社会越发展 ,劳动分 工就越细 经济合作组织 ,同时存在着为实现 成立的设计总承包管理组负责对参 化 ,设 计单位逐 步走向专业化 。而 业主和虚拟组织的双 目标 ,业主通 与项 目设计工作 的各单位 的设计 进 在 我国经济大发展 的时期 ,建设工 过设计招投标确定各工点设计单位 , 度、 质量 和工程投 资实施全面调控 ; 程趋 势为 大规模 、综合性 强 、技术 并 以合 同的形式组合成 以设计总包 设计总体组负责对参 与项 目设 计工 含量 高 ,一家设 计单位独立承揽一 总体单位为牵头单位 的虚拟组织模 作的各单位设计成果实施 技术上 的 项大型建设项 目的可能性 日见减少 , 式 。包括大 的顾 问公司,也应该能 全面管理与协调 ,从而最大 限度地 为求 得社会 的发展 和企 业的生 存 , 与小专业 公司合作 。
刹车制动力不足的原因和修复方法

刹车制动力不足的原因和修复方法刹车是车辆行驶中非常重要的系统之一,它们保证了我们的安全。
然而,有时候我们可能会遇到刹车制动力不足的情况,这给驾驶带来了很大的风险。
本文将探讨刹车制动力不足的原因,并提供一些修复方法。
一、刹车制动力不足的原因1. 刹车片和刹车盘磨损:刹车片和刹车盘是刹车系统中最关键的部件。
长时间的使用会导致它们的磨损,从而减少制动力。
刹车片磨损严重或刹车盘倾斜可能导致接触面积减少,从而降低制动力。
2. 刹车液不足:刹车液不仅传递制动力,还负责将刹车踏板的力量转化为刹车片的力量。
刹车液不足会导致刹车系统失去效力,从而降低制动力。
3. 刹车系统泄漏:刹车系统的泄漏也会导致刹车制动力不足。
无论是泄漏的刹车液还是空气从系统中进入,都会减少刹车液的压力,降低制动力。
4. 刹车系统堵塞:刹车系统中的管道或喇叭口可能会被杂物阻塞,这样刹车液无法正常流动,从而导致制动力不足。
二、修复方法1. 更换磨损的刹车片和刹车盘:当刹车片和刹车盘磨损严重时,最有效的解决方法就是更换它们。
请确保选择适合您车型的刹车片和刹车盘,并请专业技师进行更换。
2. 检查并补充刹车液:定期检查刹车液的液面,并确保它处于正确的水平。
如果液面过低,用适当的刹车液补充。
3. 修复刹车系统泄漏:如果发现刹车系统泄漏,必须尽快修复。
检查刹车系统的管道和接头,更换泄漏的部件,并确保刹车系统没有空气。
4. 清洁刹车系统:定期清洁刹车系统可以防止杂物阻塞刹车管道和喇叭口。
使用专业的刹车系统清洁剂进行清洁,并确保通风孔和排水孔畅通。
5. 调整刹车片的位置:刹车片磨损不均匀会导致制动力不足。
调整刹车片的位置,使其均匀磨损,可以提高制动力。
请注意,在处理刹车问题时,建议您寻求专业技师的帮助。
他们拥有经验丰富的技能和适当的工具,可以确保您的刹车系统运行正常。
结论刹车制动力不足是一种常见的问题,但它可以通过采取适当的维护和修复措施来解决。
定期检查刹车片、刹车盘和刹车液的状况,并及时修复刹车系统的泄漏问题,都是保持刹车制动力的关键。
如何提升车辆制动效率方案
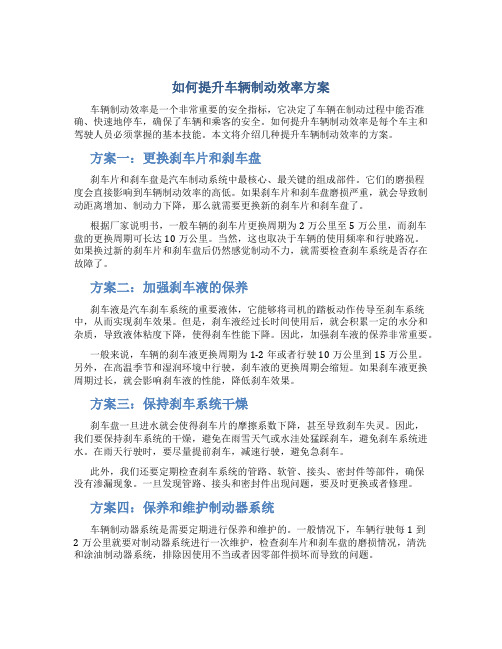
如何提升车辆制动效率方案车辆制动效率是一个非常重要的安全指标,它决定了车辆在制动过程中能否准确、快速地停车,确保了车辆和乘客的安全。
如何提升车辆制动效率是每个车主和驾驶人员必须掌握的基本技能。
本文将介绍几种提升车辆制动效率的方案。
方案一:更换刹车片和刹车盘刹车片和刹车盘是汽车制动系统中最核心、最关键的组成部件。
它们的磨损程度会直接影响到车辆制动效率的高低。
如果刹车片和刹车盘磨损严重,就会导致制动距离增加、制动力下降,那么就需要更换新的刹车片和刹车盘了。
根据厂家说明书,一般车辆的刹车片更换周期为2万公里至5万公里,而刹车盘的更换周期可长达10万公里。
当然,这也取决于车辆的使用频率和行驶路况。
如果换过新的刹车片和刹车盘后仍然感觉制动不力,就需要检查刹车系统是否存在故障了。
方案二:加强刹车液的保养刹车液是汽车刹车系统的重要液体,它能够将司机的踏板动作传导至刹车系统中,从而实现刹车效果。
但是,刹车液经过长时间使用后,就会积累一定的水分和杂质,导致液体粘度下降,使得刹车性能下降。
因此,加强刹车液的保养非常重要。
一般来说,车辆的刹车液更换周期为1-2年或者行驶10万公里到15万公里。
另外,在高温季节和湿润环境中行驶,刹车液的更换周期会缩短。
如果刹车液更换周期过长,就会影响刹车液的性能,降低刹车效果。
方案三:保持刹车系统干燥刹车盘一旦进水就会使得刹车片的摩擦系数下降,甚至导致刹车失灵。
因此,我们要保持刹车系统的干燥,避免在雨雪天气或水洼处猛踩刹车,避免刹车系统进水。
在雨天行驶时,要尽量提前刹车,减速行驶,避免急刹车。
此外,我们还要定期检查刹车系统的管路、软管、接头、密封件等部件,确保没有渗漏现象。
一旦发现管路、接头和密封件出现问题,要及时更换或者修理。
方案四:保养和维护制动器系统车辆制动器系统是需要定期进行保养和维护的。
一般情况下,车辆行驶每1到2万公里就要对制动器系统进行一次维护,检查刹车片和刹车盘的磨损情况,清洗和涂油制动器系统,排除因使用不当或者因零部件损坏而导致的问题。
制动器的调整方法

制动器的调整方法制动器的调整方法主要是为了确保车辆制动系统的性能和安全性。
制动器的不良调整会导致制动性能下降、制动间隙过大或过小、制动失灵等问题,严重危害行车安全。
因此,定期对制动器进行调整是很有必要的。
下面,我们来看一下制动器的调整方法。
1. 调整制动踩踏高度:制动踩踏高度是指踩下制动踏板后,制动器实际开始作用的距离。
过大或过小的制动踩踏高度都会影响车辆的制动性能。
调整制动踩踏高度时,首先需要松开制动踏板底座上的调节螺钉,在踏板底座上找到踩踏高度调节螺栓,根据需要调整踏板高度,然后拧紧调节螺钉,确保制动踩踏高度符合要求。
2. 调整制动器间隙:制动器间隙是指踏板和制动器工作部件之间的间隙。
合适的制动器间隙可以保证制动性能,避免制动器持续摩擦导致过度发热。
调整制动器间隙时,需要先将制动踏板放到最高位置,然后松开制动器间隙调节螺栓,根据需要调整间隙大小,最后拧紧调节螺栓。
3. 调整制动片间隙:制动片间隙是指制动片与制动盘之间的间隙,过大或过小的间隙都会影响制动性能。
调整制动片间隙时,需要先将车辆抬起,轮子卸下,然后松开制动器固定螺栓,调整制动片间隙,最后固定螺栓。
4. 调整制动力矩:制动力矩是指制动器在工作时对轮子的制动力。
适当的制动力矩可以确保制动效果,并避免过度制动产生的损伤。
调整制动力矩时,需要先调整制动踏板的高度和间隙,然后进行试车,观察制动效果,根据需要调整制动力矩大小。
5. 替换制动片:如果制动片磨损严重,影响制动效果,就需要更换新的制动片。
更换制动片时,需要将车辆抬起,轮子卸下,拆卸制动器,取下旧制动片,清洁制动器工作部件,然后安装新的制动片,拧紧螺栓,最后进行试车,确保制动效果良好。
总的来说,调整制动器必须谨慎细致,不能马虎从事。
制动系统是车辆的安全保障,所以一定要确保制动器的调整完全符合要求,避免制动失灵或制动性能不佳的情况发生。
另外,尽量选择正规的汽车维修店或者专业技师来调整制动器,以确保调整的准确性和安全性。
汽车制动力矩范围
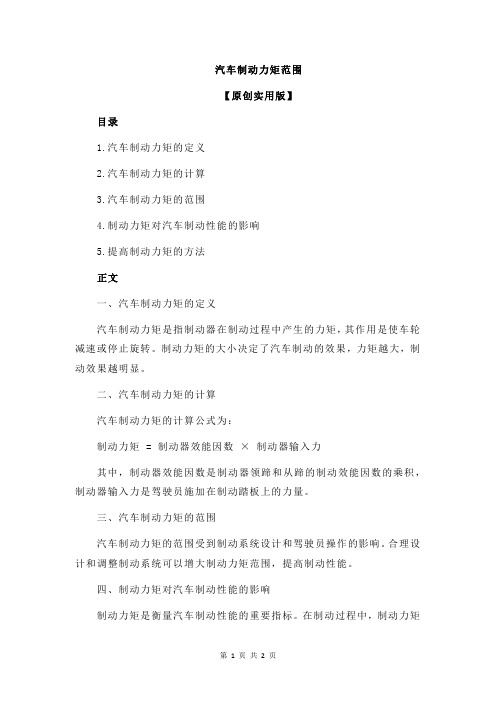
汽车制动力矩范围
【原创实用版】
目录
1.汽车制动力矩的定义
2.汽车制动力矩的计算
3.汽车制动力矩的范围
4.制动力矩对汽车制动性能的影响
5.提高制动力矩的方法
正文
一、汽车制动力矩的定义
汽车制动力矩是指制动器在制动过程中产生的力矩,其作用是使车轮减速或停止旋转。
制动力矩的大小决定了汽车制动的效果,力矩越大,制动效果越明显。
二、汽车制动力矩的计算
汽车制动力矩的计算公式为:
制动力矩 = 制动器效能因数×制动器输入力
其中,制动器效能因数是制动器领蹄和从蹄的制动效能因数的乘积,制动器输入力是驾驶员施加在制动踏板上的力量。
三、汽车制动力矩的范围
汽车制动力矩的范围受到制动系统设计和驾驶员操作的影响。
合理设计和调整制动系统可以增大制动力矩范围,提高制动性能。
四、制动力矩对汽车制动性能的影响
制动力矩是衡量汽车制动性能的重要指标。
在制动过程中,制动力矩
越大,制动距离越短,制动效果越好。
因此,提高制动力矩对提高汽车制动性能具有重要意义。
五、提高制动力矩的方法
1.增大制动器效能因数:通过选用高性能的制动材料和优化制动器结构设计,可以提高制动器效能因数,从而增大制动力矩。
2.增大制动器输入力:驾驶员在制动过程中,合理操作可以增大制动器输入力,从而提高制动力矩。
制动力矩调整说明

制动力矩调整说明
一:调整好制动臂的位置,注意:
1. 顶杆螺栓2与制动器的顶杆应对正无偏斜。
2. 抱闸臂与箱体的两侧间隙应均匀不相碰。
二:将锁紧螺母4锁紧,再将压紧螺母5顺时针转动压紧弹簧使距离L= 30/45mm (MCG200 为30mm ;MCG150 为45mm );
三:预调抱闸间隙:用手按住制动器的顶杆, 再用另一只手旋转顶杆螺栓2使其与制动器的顶杆的间隙在1-1.5mm之间;同样的方法调整另一边;
四:按要求(DC110的制动器为DC88-90V;AC220的制动器为AC220V)接入电源打开抱闸,使抱闸轮能自由转动;
五:使曳引机分别正向、反向转动,然后点动制动器的开关,观察变频器的电流值在制动瞬间时,其制动电流是否为额定电流的2倍,再根据实际值的大小相应调整压紧螺母5;
六:调整好力矩后锁紧两边的锁紧螺母6;
七:在抱闸打开曳引机运转的情况下,逆时针慢慢旋转顶杆螺栓2,同时仔细听辨,直到抱闸皮与抱闸轮正好轻微相碰时,再顺时针慢慢旋转顶杆螺栓2约90-120度,然后锁紧顶杆锁紧螺母3;
八:用同样的方法调好另一边的间隙并锁紧螺母;
九:观察两制动臂开闸闭合时的快慢统一性,当开闸时一侧慢另一侧快时,在保证制动力矩足够的情况下,慢的一侧应减小压力;反之,快的一侧应增加压力。
边调整边观察,直到同步。
合闸时,一侧快另一侧慢,慢的一侧应增加压力,快的一侧应减小压力,直到同步;
十:在抱闸打开曳引机运转的情况下,最终确认制动力矩和抱闸间隙适当及开合闸同步性。
永磁同步曳引机制动系统结构示意图。
- 1、下载文档前请自行甄别文档内容的完整性,平台不提供额外的编辑、内容补充、找答案等附加服务。
- 2、"仅部分预览"的文档,不可在线预览部分如存在完整性等问题,可反馈申请退款(可完整预览的文档不适用该条件!)。
- 3、如文档侵犯您的权益,请联系客服反馈,我们会尽快为您处理(人工客服工作时间:9:00-18:30)。
制动器制动力矩的改善措施
汽车制动力矩不足会出现滑坡现象,还会降低行车制动效能,直接影响车辆行驶的安全性。
所以对于制动力矩不足的问题必须采取有效的改进措施。
某越野车辆在路面良好的规定坡度坡道上停驻时,由于制动力矩不足出现车辆滑坡(向下方滑移)现象。
根据驻车坡度和整车参数计算,要求单个后轮驻车制动力矩不小于10 034.5N·m,而实测后轮最大驻车制动力矩为5400N·m,与要求相差甚远。
本文通过对某越野车辆后轮制动器驻车制动力矩不足的原因分析得出,除了制动器的主要结构参数选择不合理是制动力矩不足的主要原因之外,制动蹄强度不足也是制动力矩达不达标的主要原因之一。
采取增加制动气室输出推杆的推力和制动调整臂长度、减小渐开线凸轮基圆半径、增加制动蹄强度等改进措施后,能使制动力矩达到要求值。
制动器结构
该越野车的后轮制动器见图1,是定心渐开线凸轮促动领从蹄鼓式制动器,气压驱动,制动气室是行车制动与驻车制动兼用的复合式储能弹簧制动气室。
制动器制动时,凸轮机构保证了两蹄的位移相等,因此,作用于两蹄上的法向反力和由此产生的制动力矩也分别相等,领从蹄的张开力与其效能因数成反比。
图1 后轮制动器结构
1.制动鼓
2.制动蹄及滚轮
3.凸轮轴
4.制动底板
5.凸轮轴支座
6.制动调整臂
7.制动气室
原因分析
1.实物复检
将此制动器拆开,对各零部件进行复检,结果发现各零部件均满足资料要求,由此可排除制造缺陷因素。
2.制动力矩的计算
单个制动器产生的制动力矩M计算如下:
式中 Q——弹簧制动气室输出推杆的推力,N;
L——制动调整臂长度,mm;
η——凸轮支承的传动效率;
rb——渐开线凸轮基圆半径,mm;
f′——凸轮与滚轮接触点处的摩擦系数;
m——切向力(摩擦力)的力臂,mm;
K1、K2——领蹄、从蹄的效能因数;
R——制动鼓半径,mm。
此制动器的主要结构参数为:Q=7500N,L=132mm,η=0.6~0.8,计算时取η=0.7;rb=13mm,f′=0.15,m=13.62mm,R=190mm,K1=1.01,K2=0.45。
经计算得出单个制动器产生的制动力矩M=5449.58N·m,与实测值(5400N·m)相符。
因此确定制动力矩不足的主要原因是设计不合理,应进行改进。
3.试验及分析
(1)方案一将原20/24型制动气室改为20/30型制动气室,增大制动气室输出推杆的推力Q,并减小凸轮基圆半径(rb=10mm)。
经计算得出单个制动器产生的制动力矩
M=9055.28N·m。
而实测此状态的后轮最大驻车制动力矩仅为6800N·m,测量值与计算值相差很多。
图2 制动蹄结构
1.支承座
2.腹板
3.翼缘
4.连接板
5.筋
6.加强板
(2)方案二为了进一步查找原因,再次减小凸轮基圆半径(rb=8mm)。
经计算得出单个制动器产生的制动力矩M=10 958.86N·m。
此时制动力矩理论上已能满足要求,但实测此状态的后轮最大驻车制动力矩仍然为6800N·m,与试验方案一的实测值相同。
(3)制动蹄的受力分析理论计算所依据的制动蹄摩擦面上的压力分布规律是在制动蹄为绝对刚性的假设上得出的。
分析认为:此时制动蹄局部应力已达到屈服极限,产生塑性变形,制动力矩不再按理论对应关系相应增大,导致实测值与计算值不相符。
制动蹄用Q345钢板焊接而成,其结构如图2所示。
以领蹄作为分离体进行受力分析,它受到等效法向合力N1与等效切向合力fN1的合力F1、张开力P1和支反力S1,按三力平衡汇交定理计算后:张开力P1=27 465.82N,支反力S1=62 210.30N。
由计算得出的P1和S1,使用有限元法对领蹄进行强度分析,得到详细的应力分布(见图3)和塑性变形区域(见图4)。
图3 领蹄的应力分布
图4 领蹄的塑性变形区域
有部分区域的应力已超过Q345钢的屈服极限(345MPa),理论最大应力为884.9MPa。
当局部发生屈服时,应力不再增加,屈服区域向外延伸而扩大,实际上的塑性变形区域比图4所示范围更大。
所以制动蹄的强度不足是制动力矩实测值与计算值不符的原因。
(4)制动力矩不足的主要原因直接原因是制动器的主要结构参数(如制动气室输出推杆的推力、制动调整臂长度和凸轮基圆半径等)选择不合理;间接原因是制动蹄的强度不足。
改进措施
通过上述试验分析,针对制动力矩不足,得出如下改进措施:将20/24型制动气室改为20/30型制动气室,增大弹簧制动气室输出推杆的推力;减小凸轮基圆半径(rb=8mm);增大制动调整臂长度(L=165mm);制动蹄用Q345钢板焊接而成,并针对图3所示的薄弱部位进行加强:增加了制动蹄腹板和翼缘的厚度,增加支座壁厚,增加外加强板的长度,增加筋和连接板的数量,新增内加强板和两种弧形板,腹板和内、外加强板间增加塞焊缝,腹板和翼缘间采用连续角焊缝,提高制动蹄的强度和刚度,改进的制动蹄如图5所示。
图5 改进的制动蹄结构
1.支承座 2、8.弧形板Ⅰ、Ⅱ 3.内加强板 4.翼缘 5.连接板 6.筋 7.腹板 9.外加强板
1.改进的制动蹄受力分析
经计算:领蹄的张开力P1=34 332.27N,支反力S1=77 762.86N。
由求出的P1和S1,利用有限元法对领蹄进行强度分析,应力分布情况如图6所示。
改进制动蹄的最大应力为277.1MPa,安全系数为1.25,强度满足要求。
图6 改进领蹄的应力分布
2.改进后制动力矩计算
单个制动器产生的制动力矩M=13 698.58N·m,其理论值是要求值10 034.5N·m的1.37倍,满足要求。
3.驻车制动力矩实测值
实测改进的后轮最大驻车制动力矩为14 500N·m,与计算值基本相符。
4.驻车试验
将改进的制动器安装在该越野车辆上,在路面良好的规定坡度的坡道上停驻时,能可靠平稳地驻车,制动器的制动力矩完全能满足驻车能力的要求。
结语
增大渐开线凸轮促动鼓式制动器制动力矩的措施,除了可以增加制动气室输出推杆的推力和制动调整臂长度以外,还可以减小渐开线凸轮基圆半径,增加制动蹄强度等措施。
制动蹄强度或刚度不足会使制动力矩减小,在实际设计工作中容易忽视此因素。
进行结构设计时,制动蹄的结构尺寸和断面形状应保证其有足够的强度和刚度。