Aspen精馏过程模拟
应用AspenPlus软件模拟二异丙苯精馏过程
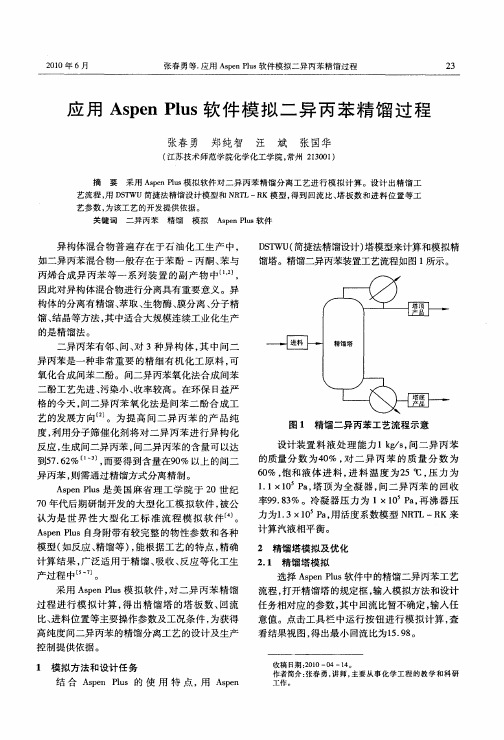
丙烯合成异丙苯等一系列装 置的副产物 中¨ 】 ., 2
因此对 异构 体混合 物进 行分 离具有 重 要意 义 。异
构 体 的分离 有精馏 、 取 、 物酶 、 萃 生 膜分 离 、 分子 精 馏 、 晶等 方法 , 中适合 大 规模连 续工 业 化生 产 结 其 的是 精馏 法 。
二异 丙 苯有邻 、 、 3种 异 构 体 , 中 间 二 间 对 其 异丙 苯是 一种 非 常 重 要 的精 细 有 机 化工 原 料 , 可
2 3 模拟 结果 .
2 2 1 回流 比与塔 板数 ..
使用 ApnPu 软 件 中灵 敏 度 分 析工 具 , se ls 进 行灵 敏度分 析 , 考查 回流 比和塔板数 之间 的关 系 , 计算 结果见 图 2 。
选择合适 的 回流 比为2 .8 间二异丙 苯 的 回 O7 、 收率 为 9 .3 , 算 出 的 模 拟 结 果 见 表 1和 9 8% 计
关键词 二异 丙 苯 精馏 模拟 A pnPu 软 件 se ls
异 构体 混合 物 普 遍 存在 于石 油 化 工 生 产 中 , 如二异 丙苯 混合 物 一 般存 在 于 苯 酚 一丙 酮 、 与 苯
DT ( SWU 简捷法精 馏设计 ) 塔模 型来计 算和模 拟精
馏塔 。精馏二异丙 苯装 置工艺流 程如图 1 所示 。
反应 , 成 间二 异丙 苯 , 生 间二异 丙苯 的含 量 可 以达
图 1 精 馏二 异丙 苯工艺 流程 示意
设计装 置 料 液 处 理 能 力 1k / , 二 异 丙 苯 gs间 的质 量 分 数 为4 % , 二 异 丙 苯 的质 量 分 数 为 0 对
到5 . 2 ¨ , 要得 到含 量在9 % 以上 的间二 76 % 而 0
ASPENPLUS模拟计算乙烯精馏生产工艺

ASPENPLUS模拟计算乙烯精馏生产工艺乙烯是一种重要的基础化工原料,被广泛用于塑料、橡胶、纺织、化肥等行业。
乙烯的生产通常通过乙烷的裂解来实现,然后对产物进行精馏分离。
在ASPENPLUS软件中,我们可以使用模拟计算来研究乙烯精馏的生产工艺。
以下是一个关于乙烯精馏的工艺流程模拟计算的示例。
首先,我们需要建立一个乙烯精馏塔的模型。
我们可以选择合适的塔模型,例如McCabe-Thiele模型。
然后,我们需要输入原料的物性数据,例如乙烯和乙烷的物理属性,以及裂解过程中形成的其他组分的数据。
接下来,我们需要定义裂解的反应过程。
乙烷经过裂解反应产生乙烯和其他副产物。
我们可以选择合适的反应模型,例如矿物油裂解反应模型。
然后,我们需要指定反应的条件,例如温度和压力。
在模拟计算中,我们还需要考虑其他的操作条件,例如塔顶和塔底的温度和压力,以及塔内的塔板数目和塔板的设计参数。
这些参数的选择将直接影响到乙烯的分离效果和产品纯度。
在进行模拟计算之前,我们还需要制定一个目标函数。
例如,我们可以设定乙烯的纯度和回收率作为优化目标。
然后,我们可以根据目标函数进行优化计算,以确定最佳操作条件和设计参数。
在模拟计算完成后,我们可以通过查看计算结果和对比不同操作条件下的性能指标来评估乙烯生产工艺的优劣。
例如,我们可以比较不同温度和压力条件下的乙烯回收率和纯度,以确定最佳操作条件。
此外,我们还可以通过敏感性分析来评估不同因素对乙烯生产工艺的影响。
例如,我们可以分析温度、压力、反应物料比例等因素对乙烯纯度的影响,并找到优化方案。
总之,ASPENPLUS软件是一种实用的工具,可以用于乙烯精馏生产工艺的模拟计算。
通过合理设置模拟计算的参数和目标函数,我们可以研究不同操作条件和设计参数对乙烯生产的影响,并找到最佳的操作条件和设计方案。
ASPENPLUS模拟计算乙烯精馏生产工艺

ASPENPLUS模拟计算乙烯精馏生产工艺乙烯是一种重要的有机化工原料,广泛应用于塑料、合成纤维、橡胶等领域。
精细的乙烯精馏生产工艺对于获得高纯度的乙烯产品至关重要。
在本文中,将使用ASPENPLUS软件进行乙烯精馏生产工艺的模拟计算。
首先,需要建立物料平衡模型。
假设进料为乙烯和杂质物料,出料为乙烯和杂质物料的混合物。
首先,可以使用MESH分离块对进料进行塔板线性分离,并定义进料进口的操作条件。
然后,可以选择塔板压降模型,然后设置相平衡模型,例如使用UNIFAC-RK模型。
接下来,需要定义塔板的结构和操作参数。
在塔顶设置乙烯的回收器,并在塔底设置乙烯的热循环回收,以提高乙烯的回收率和纯度。
然后,需要选择合适的塔板类型和厚度。
请注意,在乙烯精馏塔中,常用的塔板类型有Sieve Tray、Valve Tray、Bubble Cap Tray等。
我们可以选择其中一种适合的塔板类型。
在进行塔板设计时,需要选择适当的塔心直径、液体停留时间和气体速度,以确保塔板的正常运行。
同时,还需要通过指定冷冻器、热交换器等设备,控制塔顶和塔底的温度。
完成了物料平衡和塔板设计后,接下来需要进行乙烯的精馏过程的热力学计算。
在ASPENPLUS中,可以选择适当的热力学模型,如NRTL或UNIFAC模型,以模拟乙烯的汽液相平衡行为。
此外,还可以通过设置温度、压力和摩尔流量等操作参数,优化乙烯的回收率和纯度。
最后,可以进行仿真计算和结果分析。
在ASPENPLUS中,可以使用数据回归方法,通过各个操作参数的变化,建立乙烯精馏过程的模拟模型。
通过模拟计算,可以得到乙烯的纯度、回收率以及杂质物料的分离效果。
然后,可以根据需求进行调整,以优化乙烯精馏生产工艺。
研究结果显示,通过ASPENPLUS的模拟计算,可以实时监测乙烯精馏过程的各项参数,包括温度、压力、流量等,并通过调整操作参数,实现乙烯的高回收率和高纯度。
同时,模拟计算还可以预测乙烯精馏过程中可能出现的问题,并提供相应的解决方案。
aspen 精馏模拟详细过程及探讨疑问

精馏塔设计初步介绍1.设计计算◆输入参数:●利用DSTWU模型,进行设计计算●此时输入参数为:塔板数(或回流比以及最小回流比的倍数)、冷凝器与再沸器的工作压强、轻组分与重组分的回收率(可以从产品组成估计)、冷凝器的形式◆输出参数(得到用于详细计算的数据):●实际回流比●实际塔板数(实际回流比和实际塔板数可以从Reflux Ratio Profile 中做图得到)●加料板位置(当加料浓度和此时塔板上液体浓度相当时的塔板)●蒸馏液(馏分)的流量●其他注:以上数据全部是估计得初值,需要按一定的要求进行优化(包括灵敏度以及设计规定的运用),优化主要在RadFrac模型中进行。
2.详细计算◆输入参数:●输入参数主要来自DSTWU中理论计算的数据◆输出参数:●输出的主要是设计板式塔所需要的水力学数据,尺寸数据等其他数据(主要是通过灵敏度分析以及设计规定来实现)3.疑问●在简捷计算中:回收率有时是估计值,它对得到详细计算所需的数据可靠性的影响是不是很大?●在简捷计算中:有多少个变量,又有多少个约束条件?●在简捷计算中:为什么回流比和塔板数有一定的关系?简捷计算(对塔)1.输入数据:●Reflux ratio :-1.5(估计值,一般实际回流比是最小回流比的1.2—2倍)●冷凝器与再沸器的压强:1.013 ,1.123 (压降为0.11bar)●冷凝器的形式:全冷凝(题目要求)、●轻重组分的回收率(塔顶馏出液):0.997 ,0.002 (如果没有给出,可以根据产品组成估计)●分析时,注意Calculation Option 中的设置,来确定最佳回流比以及加料板位置2.输出数据:●Reflux Ratio Profile中得到最佳的回流比与塔板数为:塔板数在45—50中选择,回流比在:0.547 —0.542●选定塔板数为:48,回流比为:0.544●把所选的塔板数回代计算,得到下列用于RadFrac模型计算的数据(见下图):●●从图中可得:实际回流比为:0.545(摩尔比);实际塔板数为:48;加料板位置:33;Distillate to feed fraction :0.578(自己认为是摩尔比,有疑问??);馏出液的流量:11673.5kg/h疑问:进料的流量是怎么确定的,肯定是大于11574kg/h,通过设计规定得到甲醇产量为:11574kg/h(分离要求),求出流量为:16584.0378kg/h。
用AspenPlus对反应精馏的模拟计算

摘要以甲醇和醋酸的酯化反应为例,介绍了用AspenPlus软件模拟计算反应精馏过程的方法。
计算过程包括:(1)对反应精馏塔模型进行合理的简化;(2)选取合适的数学模型和热力学模型;(3)选取合适的参数。
计算初步确定了最佳回流比,合理的甲醇过量程度,并通过灵敏度分析得出灵敏板的大概位置。
本计算结果可作为反应精馏实验的基础。
关键词酯化反应AspenPlus反应精馏中图分类号TQ018作者简介:樊艳良女1973年生工程师主要从事工艺设计和项目设计管理工作Vol.32No.5May2007上海化工ShanghaiChemicalIndustry14・・第5期樊艳良:用AspenPlus对反应精馏的模拟计算HOAc+MeOH←→MeOAc+H2O上述反应具有如下特点:(1)为液相可逆反应,转化率受化学平衡的限制。
若通过提高反应温度增加反应速率,则逆反应-水解反应的速率也会随之加快。
(2)反应体系存在复杂的共沸物,难以制备高纯度的MeOAc。
MeOAc/H2O、MeOAc/MeOH能够形成共沸物(见表1),且共沸物与产品MeOAc的沸点非常接近,所以常规精馏难以直接制备纯度大于95%的MeOAc。
表1常压下酯化系统的共沸物性质(3)需要采用强酸性催化剂(如浓硫酸、对甲苯磺酸、强酸型阳离子交换树脂、杂多酸、固体超强酸、分子筛等),以提高反应速率。
对于传统的酯化工艺,由于反应物和产物同时存在于反应体系中,受化学平衡的限制,原料转化率不高,未转化的原料必须循环利用,增加了能耗。
同时,需要设置一系列萃取精馏塔及相关设备,以打破共沸物,得到高纯度的MeOAc。
显而易见,传统的酯化工艺流程繁琐、能耗高、投资大。
反应精馏技术的出现,成功解决了这一问题。
2.2反应精馏酯化工艺介绍反应精馏塔是酯化工艺的核心设备,自下而上分为四段:气提段、反应段、萃取段和精馏段。
原料醋酸从塔上部的萃取段进入塔内,浓硫酸催化剂从萃取段底部进入塔内,而原料甲醇从反应段的中下部加入,见图1。
aspen精馏过程模拟
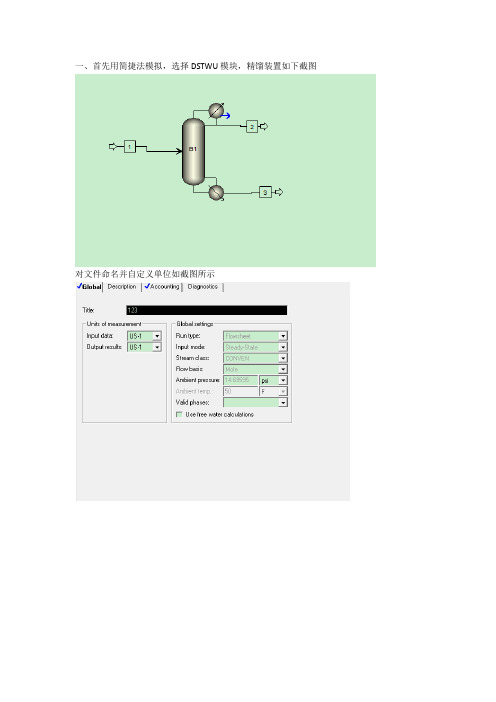
一、首先用简捷法模拟,选择DSTWU模块,精馏装置如下截图对文件命名并自定义单位如截图所示然后在计算机上输入物料的组成,如下截图所示选择一个热力学方法为SRK方法如下截图所示对1号进料物流管进行参数设定,为泡点进料,进料压力为16.5Kg/cm2,进料流量为100kmol/h。
还有物料组成及比例如下截图所示对精馏塔进行参数的设定,回流比为最小回流比的1.2倍,塔顶轻组分丙烷的含量为0.999,重组分含量丁烷为0.001,参数设定值如下截图所示参数设定完成运行软件并查看结果,计算结果如下图所示从结果可知实际的回流比为1.198,实际塔板数为38块,实际的进料板为第17块板,冷凝器的温度为44.25℃,塔釜的温度为116.88℃。
二、进行严格法计算根据简化法得到的条件进行模拟选择Radfrac模块,模拟装置图如下截图对文件命名并自定义单位如截图所示在计算机上输入物料的组成,如下截图所示选择一个热力学方法为SRK方法如下截图所示对1号进料物流管进行参数设定,为泡点进料,进料压力为16.5Kg/cm2,进料流量为100kmol/h。
还有物料组成及比例如下截图所示对塔进行参数设置,根据简化法的计算结果知,塔板数为38,实际回流比为1.198。
再根据题目设计的要求冷凝器为全回流,塔顶的采出率为80。
参数如下截图所示:根据简化法结果进料板为第十七块板进料,截图如下设置塔顶压力为16kg/cm2,冷凝器压力为15.8kg/cm2,全塔的压降为0.2kg/cm2。
设置如下截图所示参数设置完成并运行软件,查看结果不满足分离的目的,则进行自定义设定,目标值设定为0.001选择丙烷选择3号物流设置回流比的可变范围为1到100,增量为0.1运行软件查看结果满足分离的要求。
接下来进行灵敏度分析以确定最佳的进料位置参数设置完成并运行软件查看灵敏度分析的结果如下截图从结果的表中可以看出第22块板的回流比,冷凝器的热负荷,再沸器的热负荷都是最小的,从而可以知道最佳的进料位置为第22块板并对数据在plot里作出X-Y的曲线图如下截图所示从图中也可以明显的看出最佳的进料板为第22块塔板。
反应精馏过程模拟_ASPENPLUS应用范例
( 上接第 56 页) 图 6 可以看出, 环氧丙烷在 2、6 板上摩尔分率较高, 从而这就造成在这两块板上反 应量较大。这样, 我们可以看出, 该反应的主反应区在第二块板和第六块板, 三、四、五块板反应量很少, 加料板( 第六块版) 以下反应量几乎为零。 5 结论
件下是很难做到在短时间内混合均匀的。 水 合反应生成的一水碱( N a2CO3 ·H 2O ) 呈
松散的颗粒状态, 内含游离水 5- 7% 左右, 密度 约 1250K g/ T 。根据查定, 在水合机反应区内一水 碱与热纯碱的体积比大于 2. 0∶1( 我厂水合机满 负荷生产时此体积比是 2. 2∶1) 。由上述分析可 知, 若采取将水合水先加入到一水碱中, 利用一水 碱分散性能好和在反应区内的体积大于热纯碱的 条件, 使吸水后的一水碱与热纯碱混合, 就可使热 纯碱很容易地迅速分散到一水碱中, 吸收一水碱 中含有的水分进行水合反应。即是将一水碱做为 水合水的载体和两相混合中的连续相, 热纯碱做 为两相混合中的分散相, 消除了热纯碱与水合机 内壁的接触机会, 从而避免水合机内壁粘碱结疤。 3 异径水合机的防结疤技术
分散到一水碱中。随着机体的旋转, 机内采用的大 抄板技术使一水碱与热纯碱迅速而均匀地得到了 混合。
异径水合机长度为 4775mm , 一水 碱在机内 的停留时间是 10 分钟, 仅是直筒式水合机停留时 间的一半。由于出料端亦采用了异径技术, 消除了 出料死角, 加之较短的停留时间使机内物料在温 度尚未降低时导出, 避免了因温度降低而发生的 机尾结疤。
通过模拟计算与优化处理, 我们得到反应的工艺条件如表 1 所示, 我们发现计算结果与实际情况非 常接近。 3. 2 计算结果及分析
ASPEN共沸精馏模拟例39丁醇和水的非均相共沸精馏
ASPEN共沸精馏模拟例39丁醇和水的非均相共沸精馏(1) 分离任务课本例题3-9进料F=5000kmol/h,原料组成为水28%,丁醇72%,气液混合进料,气相分率为30%。
分离要求:丁醇产品中含水不大于0.04(摩尔分数),废水中含正丁醇不大于0.005(摩尔分数)。
(2) 流程的确定建立如图所示的流程图。
流程的描述:原料在合适的位置进入丁醇塔TOWER1,塔顶无冷凝器,出共沸组成,塔底为丁醇出口;塔顶共沸物经冷凝后分相,醇相回流至TOWER1作为回流液,水相作为水塔TOWER2的进料和回流液;TOWER2塔底为废水,塔顶为共沸物,经冷凝和分相后循环。
分析:f<Xα<Xβ,应在A( 根据题中可知, Xα=0.573,Xβ=0.975,故X丁醇塔进料。
B( 利用三相闪蒸模型,直接模拟冷凝器和分相器。
规定气相分率为0,饱和液体回流。
(3) 物性方法的选择丁醇和水是二元极性体系,所以NRTL方程能够很好的描述这一平衡过程。
根据文献介绍,用ASPEN物性数据库中的NRTL模型计算得出的丁醇-水共沸物的汽液平衡数据和实际值基本一致,故选用NRTL模型为本次模拟的物性方法。
(4) 流程的模拟根据物料衡算,计算出丁醇塔B1=3743.5kmol/h,水塔B2=1256.5kmol/h.同时由于,如果两塔同时给定塔顶采出率或者塔底采出率时,很难收敛。
故选择TOWER1给定塔底采出率,TOWER2给定塔顶采出率。
最终初次收敛时的参数如下图所示:TOWER1的初始参数如下图所示:TOWER2初始参数如下图所示:(5) 流程的优化根据变压精馏的原理用design限定TOWER1的塔底采出率。
(1) 经分析可得,TOWER2的塔顶采出率影响循环量。
故在全流程中,对其做灵敏度分析。
Q1为冷凝器能耗,Q2为TOWER1能耗,Q3为TOWER2能耗。
(2)满足design的条件下,塔板数的优化。
TOWER1S-2塔板数灵敏度分析当塔板数继续减小时,收敛有点困难,采用手动调节。
乙苯与苯乙烯精馏过程的Aspen Plus模拟
本科毕业设计(论文)本科毕业设计乙苯与苯乙烯精馏过程的Aspen Plus模拟目录1前言 (1)1.1精馏原理及发展 (2)1.1.1精馏塔设备的介绍 (2)1.1.2塔板的类型及性能评价 (2)1.1.3精馏过程进行计算机模拟 (3)1.1.4精馏传质动力学研究更加深入 (3)1.1.5精馏节能技术研究势在必行 (3)1.2 精馏特点 (4)1.3 精馏问题描述 (4)1.4 化工过程模拟 (5)1.4.1化工过程模拟系统的发展 (5)1.5流程模拟技术 (5)1.6精馏模拟软件——Aspen Plus简介 (5)1.7模拟计算 (6)1.7.1 物性计算 (6)1.7.2 操作模型与计算方法 (6)1.8 本文研究的主要内容 (6)2 流程简介 (7)2.1分离物质的起始条件 (7)2.2模拟流程图 (7)3 Aspen Plus模拟计算 (8)3.1模拟流程 (8)3.1.1建立流程 (8)3.1.2进料组分 (8)3.1.3设置物性方法 (9)3.1.4流量参数设置 (10)3.1.5精馏塔的参数设置 (10)3.1.6输出模拟结果 (11)4 灵敏度分析 (15)4.1灵敏度分析 (15)4.2模型分析工具设置 (15)4.2.1创建分析单元S-1 (15)4.2.2创建分析变量与设置被控变量 (16)4.2.3设置操作变量 (17)4.3计算结果及其分析 (18)4.3.2数据分析 (19)5 CupTower对塔的设计计算及校核 (20)5.1 精馏段的塔板设计 (20)5.1.1 基本参数的设置 (20)5.1.2 塔板计算结果 (21)5.1.3 校核 (22)5.2 提馏段塔板工艺设计 (24)5.2.1 基本参数的设置 (24)5.2.2 塔板计算结果 (25)5.2.3 校核 (26)结论 (29)参考文献 (30)附录一:TPFQ结果数据 (31)附录二:气相组成分布 (33)附录三:精馏段塔板工艺设计数据 (35)附录四:提馏段工艺设计结果数据 (37)致谢 (39)乙苯与苯乙烯精馏过程的Aspen Plus模拟摘要本文主要论述利用Aspen Plus模拟乙苯、苯乙烯两组分在精馏塔的分离情况,在DSTWU模拟操作计算得出结果的基础上,然后再重新选取数据,用RadFrac模块进行精确计算,再根据浓度分布剖形的结果选取最佳进料位置,重新进行校核计算,为了达到预期的分离效果,通过改变操作条件:如进料位置等,对结果进行比较,通过比较分析,对操作条件进行分析,进而完成本次对精馏塔分离的模拟任务,之后利用CUPTOWER软件对塔板进行设计,得出塔板结构参数和工艺参数。
Aspen反应精馏的模拟和设计
注意选择Kinetic
输入正反应的方式
输入逆反应的方式
在动力学表单中为每一个化学反应输入发 生反应的相态、动力学参数以及浓度基准。 幂律型:反应动力学因子(Kinetic factor)即反应 速率常数 k’,它与温度的关系用修正的 Arrhenius方程表示:
E 1 1 T k ' k exp R T T0 T0
Reactive Distillation Simulation by Aspen Plus
Aspen Plus 反应精馏设计
华东理工大学
凌昊
中国化工学会培训中心 中国石油和化学工业协会培训中心
稳态模拟选择Steady-State即可,若选 择dynamic将来可以转成动态模拟.
输入系统所需的物质
同tray sizing holdup的设计
超过0.1524则压力需要自己给定
分相槽及冷凝器操作方法
Decanter之操作压 力及温度
因为水为第一液 相,所以酯为第 二液相
冷凝器操作状态
有效相
收敛方法设定
收敛设定的相对误差
全局收敛的设定
选择收敛的方法
每个设计规定和撕裂流都有一个相关联的收敛模块。 收敛模块确定撕裂流或设计规定的操作变量的推测值 在迭代过程中的更新方法。 Aspen Plus定义的收敛模块的名字以字符“$.”开头。
创建化学反应对象时,需赋予对象ID和 选择对象类型。对于小分子反应,常用的类 型有三种: 1、LHHW 型 (Langmuir-Hinshelwood-Hougen-Watson) 2、幂律型 (Power Law 反应级数) 3、反应精馏型 (Reac-Dist)
- 1、下载文档前请自行甄别文档内容的完整性,平台不提供额外的编辑、内容补充、找答案等附加服务。
- 2、"仅部分预览"的文档,不可在线预览部分如存在完整性等问题,可反馈申请退款(可完整预览的文档不适用该条件!)。
- 3、如文档侵犯您的权益,请联系客服反馈,我们会尽快为您处理(人工客服工作时间:9:00-18:30)。
SCFrac
第4页
4.1 单元操作模型 -- 塔-严格塔
模型
RadFrac
说明 严格分馏
目的 单个塔的严格核算和设 计
用法 蒸馏, 吸收, 汽提, 萃取和恒沸蒸馏, 反应蒸馏 热集成塔, 空气分离器, 吸收塔/汽 提塔 结合, 乙烯主分馏塔/急冷塔 组合, 石油炼制 预闪蒸塔, 常压原油单元, 减压单元 , 催化裂解塔 或焦碳分馏塔, 减压 润滑油分馏塔, 乙烯分馏塔和急冷 塔 一般恒沸蒸馏, 3-相, 和反应间歇蒸 馏
模型 说明 目的 确定最小回流比, 最小 理论板数, 和用 WinnUnderwood-Gilliland 方 法得到的实际回流比或 实际塔板数 用途 带有一个进料物流和两个 产品物流的塔
DSTWU 简蒸馏 核算 石油馏分的 简捷法蒸馏
用 Edmister 方法在回流 带有一个进料物流和两个 比、理论板数和D:F比 产品物流的塔 的基础上确定分离 用分离指数确定产品的 复杂塔, 例如原油加工装 组成和流量, 每段的塔 置和减压塔 板数,负荷
2)指定第一调整变量 --- Specifications 调整distillate rate 在0.2-0.6kmol/sec之间变化
第35页
例4.2 使用“DESIGN SPEC-VARY”功能
3) 运行模拟 --- Control Pannel
第36页
例4.2 使用“DESIGN SPEC-VARY”功能
4) 查 看 结 果
第37页
例4.2 使用“DESIGN SPEC-VARY”功能
5)指定第二控制变量--- Specifications 第二控制变量为塔底中c3的浓度值为0.01
第38页
例4.2 使用“DESIGN SPEC-VARY”功能
5)指定第二控制变量--- Components
第39页
9)查看计算结果
分离要求:xD,IC4≤2 mol% xB,C3≤1 mol%
可通过增加回流比或增加塔 的理论板数提高分离效果
第28页
例4.1 丙烷、异丁烷的分离过程模拟
10) 增大回流比为3
分离要求:xD,IC4≤2 mol% xB,C3≤1 mol%
第29页
例4.2 使用“DESIGN SPEC-VARY”功能
第5页
*
Requires separate license
4.2 RadFrac --严格多级分离模块
教学目标
• 讨论RadFrac模型的最小输入条件 • 学习RadFrac内嵌的变量规定
第6页
4.2 RadFrac---严格多级分离模块
可对下述过程做两相或三相模拟:
• 普通蒸馏
• 吸收, 再沸吸收 • 汽提, 再沸汽提 • 恒沸蒸馏 • 反应蒸馏
MultiFrac
复杂塔严格 多级塔和复杂塔的严格 分馏 核算和设计
PetroFrac
石油炼制分 石油炼制应用的严格核 馏 算和设计 严格间歇蒸 单个间歇塔的严格核算 馏
BatchFrac*
RateFrac* Extract
单个和多级塔的严格核 蒸馏塔, 吸收塔, 汽提塔, 反应系统, 基于速率的 算和设计. 建立在非平衡 蒸馏 热集成单元, 石油应用 计算基础上 液-液萃取 液-液萃取塔的严格核算 液-液萃取
VFLOW
H2IN
VAP FEED-MIX RXIN
T = 150C P = 23 bar
REACT HP-SEP RXOUT
T = 200 C Pdrop = 1 bar Benzene conv = 0.998 T = 50 C Pdrop = 0.5 bar
LTENDS
Stages = 12 Reflux ratio = 1.2 Bottoms rate = 99 kmol/hr 只有气体馏出物 的部分冷凝器 P = 15 bar Feed stage = 8
第32页
例4.2 使用“DESIGN SPEC-VARY”功能
1)指定第一控制变量--- Components
第33页
例4.2 使用“DESIGN SPEC-VARY”功能
1)指定第一控制变量--- Feed/Product Sreams
第34页
例4.2 使用“DESIGN SPEC-VARY”功能
不同的物性计算模型
第20页
例4.1 丙烷、异丁烷的分离过程模拟
6)输入流股信息
第21页
例4.1 丙烷、异丁烷的分离过程模拟
7)输入设备参数 - C1- Configuration
第22页
例4.1 丙烷、异丁烷的分离过程模拟
7)输入设备参数 - C1- Streams
第23页
例4.1 丙烷、异丁烷的分离过程模拟
精馏过程模拟
第1页
例题-环己烷生产
•目的:创建一个流程来模拟环己烷生产过程 •环己烷可以用苯加氢反应得到,反应如下: • C6H6 苯 + 氢气 3 H2 = 环己烷 C6H12
•在进入固定床反应器前,苯和氢气进料与循环氢气和环 己烷混合。 假设苯转化率为 99.8%。
•反应器出料被冷却,轻气体从产品物流中分离出去。 部 分轻气体作为循环氢气返回反应器。 •从分离器出来的液体产品物流进入蒸馏塔进一步脱除溶 解的轻气体,使最终产品稳定。部分环己烷产品循环进入 第2页 反应器,辅助控制温度。
回流 L1 + LW
热 (可选) 液体蒸馏物 (DL) 水 (DW) (可选) D=DL+DV DV:D=DV/D RR=L1/D RW=LW/DW 产品 (任何数量) 倾析器
上升蒸汽 (VN) N级
返回 热 (可选) 塔底 (B) BR=VN/B
产品
第9页
4.3 RadFrac---结构设置
规定: • 理论板数 • 冷却器和再沸器结构 • 两塔操作规定 • 有效相态 • 收敛
第7页
4.2 RadFrac---严格多级分离模块
结构选项:
• 任何数量的进料
• 任何数量的侧线采出 • 总液体采出和循环回流 • 任何数量的换热器 • 任何数量的倾析器
第8页
4.2 RadFrac---拓扑结构
气体蒸馏物 (DV) 1
顶级或冷凝器热负荷 (Q1) 物料 (任何数量) 热 循环回流 热 热 (任何数量) 底级或再沸器热负荷 (QN)
第10页
4.4 RadFrac---流股设置
规定:
进料板位置 进料物流规则 (见帮助) ABOVE-STAGE:
从进料物流来的气体进入 进料板上一层塔板,液体进 入进料板位置 ON-STAGE: 来自进料的气体和液体都 进入进料板位置
第11页
4.5 RadFrac---压力设置
规定下列项之一:
泵和控制阀的命名以易于 与精馏塔C1关联为宗旨
选择液相馏出物
第17页
例4.1 丙烷、异丁烷的分离过程模拟
3)设定全局特性
工程概述、工程 单位、报告输出 形式等
第18页
例4.1 丙烷、异丁烷的分离过程模拟
4)指定化学组分并重命名
第19页
例4.1 丙烷、异丁烷的分离过程模拟
5)选择物性计算模型
注意:不同单元操作可选择
BZIN
T = 40 C P = 1 bar Benzene flow = 100 kmol/hr
CHRCY LFLOW
COLFD
去物流 CHRCY的流量为30%
PRODUCT
用 RK-SOAVE 物性方法
COLUMN
完成后另存为: 文件名: CYCLOHEX.BKP 第3页
4.1 单元操作模型 -- 塔-简捷塔
数32,第16块板处进料。回流比为2。冷凝器为全 凝器。泵的压力提升为5atm, 阀的压力降为3atm。 热力学方法为chao-sea.
第13页
例4.1 丙烷、异丁烷的分离过程模拟
• 流程图
第14页
例4.1建立稳态模拟流程
1 启动新的模拟过程 2 指定化学组分及物性模型
3 输入流股信息
4 输入设备参数
7)输入设备参数 - C1- Pressure
第24页
例4.1 丙烷、异丁烷的分离过程模拟
7)输入设备参数 - P11&P12
第25页
例4.1 丙烷、异丁烷的分离过程模拟
7)输入设备参数 - V1
第26页
例4.1 丙烷、异丁烷的分离过程模拟
8)运行模拟计算
第27页
例4.1 丙烷、异丁烷的分离过程模拟
• 塔压力分布
• 塔顶/塔底压力
• 塔段压降
第12页
例4.1丙烷、异丁烷的分离过程模拟
【例4.1】 采用Radfrac模块,对于丙烷、异丁烷的 分离过程进行模拟。进料中丙烷的摩尔含量为40% 。分离要求塔顶流出物中异丁烷的含量为2%,塔 底产品中丙烷的含量为1%。流程图如下图所示。
进料温度为322K, 精馏塔操作压力为14atm,塔板
例4.2 使用“DESIGN SPEC-VARY”功能
5)指定第二控制变量--- Feed/Product Sreams
第40页
例4.2 使用“DESIGN SPEC-VARY”功能
6 )指定第二调整变量 --- Specifications Reflux Ratio在 1-5之间调整
第41页
例4.2 使用“DESIGN SPEC-VARY”功能
7) 再次运行模拟 --- Control Pannel
第42页
例4.2 使用“DESIGN SPEC-VARY”功能
8) 查 看 结 果
第43页
例4.2 使用“DESIGN SPEC-VARY”功能
查看结果 --- 操作回流比