4 晶粒长大
晶粒生长
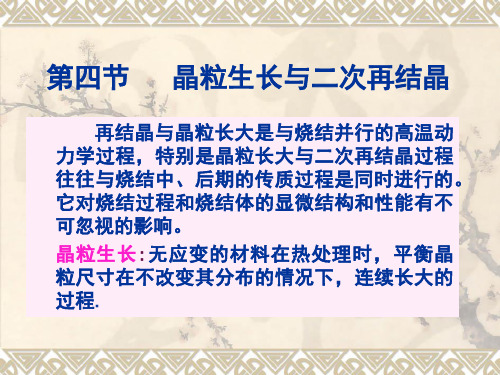
再结晶与晶粒长大是与烧结并行的高温动 力学过程,特别是晶粒长大与二次再结晶过程 往往与烧结中、后期的传质过程是同时进行的。 它对烧结过程和烧结体的显微结构和性能有不 可忽视的影响。 晶粒生长:无应变的材料在热处理时,平衡晶 粒尺寸在不改变其分布的情况下,连续长大的 过程.
坯体继续致密化
❖晶界越过气孔或杂质,产生二次再结晶,把气 孔包入晶体内部
⑵有少量液相出现在晶界上—少量液相抑制晶粒 长大
5.极限晶粒直径:
DL—晶粒正常生长时的极限尺寸
DL d f
d—夹杂物或气孔的平均直径 f—夹杂物或气孔的体积分数
讨论:
①当f愈大时则DL愈小 ②当f一定时,d愈大则晶界移动时与夹杂
物相遇的机会就越少,于是DL愈大
三. 二次再结晶
(或称异常长大和晶粒不连续长大)
1.定义:二次再结晶是少数巨大晶粒在细晶消耗时 成核长大的过程(当正常的晶粒长大过程停止后, 个别具有多边界的大晶粒以自身为核心不断吞并 周围小晶粒而异常长大的过程为二次再结晶)
2.推动力:大晶粒界面与邻近高表面能和小曲率半 径的晶面相比有较低的表面能
1
❖logD—t作图为一直线,其斜率为 2
4.影响晶粒生长的因素:
图示1 图示2
⑴第二相夹杂物(杂质、气孔)影响—阻碍作用
当气孔汇集在晶界上时,晶界移动可能出现的 三种情况:
❖晶界移动被气孔或杂质所阻挡,使正常的晶粒 长大终止
❖晶界带动气孔或杂质以正常速度移动,使气孔 保持在晶界上,并可利用晶界的快速通道排除,
⑴ 原始粒度不均匀,存在个别大晶粒 ⑵ 烧结温度偏高或烧结速率太快 ⑶ 成型压力不均,局部有不均匀液相
5.避免二次再结晶采取的措施:
材料科学基础重点总结4 材料形变和再结晶
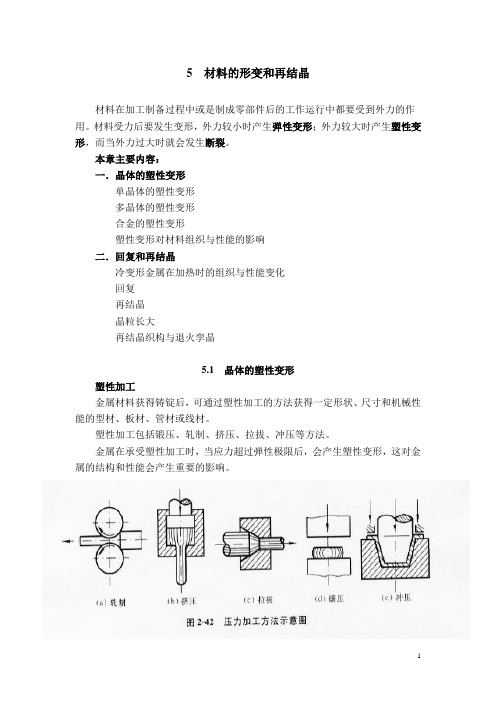
5 材料的形变和再结晶材料在加工制备过程中或是制成零部件后的工作运行中都要受到外力的作用。
材料受力后要发生变形,外力较小时产生弹性变形;外力较大时产生塑性变形,而当外力过大时就会发生断裂。
本章主要内容:一.晶体的塑性变形单晶体的塑性变形多晶体的塑性变形合金的塑性变形塑性变形对材料组织与性能的影响二.回复和再结晶冷变形金属在加热时的组织与性能变化回复再结晶晶粒长大再结晶织构与退火孪晶5.1 晶体的塑性变形塑性加工金属材料获得铸锭后,可通过塑性加工的方法获得一定形状、尺寸和机械性能的型材、板材、管材或线材。
塑性加工包括锻压、轧制、挤压、拉拔、冲压等方法。
金属在承受塑性加工时,当应力超过弹性极限后,会产生塑性变形,这对金属的结构和性能会产生重要的影响。
5.1.1 单晶体的塑性变形单晶体塑性变形的两种方式:滑移孪生滑移:滑移是晶体在切应力的作用下,晶体的一部分相对于另一部分沿着某些晶面和晶向发生相对滑动。
滑移线:为了观察滑移现象,可将经良好抛光的单晶体金属棒试样进行适当拉伸,使之产生一定的塑性变形,即可在金属棒表面见到一条条的细线,通常称为滑移线.滑移带:在宏观及金相观察中看到的滑移带并不是单一条线,而是由一系列相互平行的更细的线所组成的,称为滑移带。
滑移系:塑性变形时位错只沿着一定的晶面和晶向运动,这些晶面和晶向分别称为“滑移面”和“滑移方向”。
一个滑移面和此面上的一个滑移方向结合起来组成一个滑移系。
滑移的临界分切应力τk晶体的滑移是在切应力作用下进行的,但其中许多滑移系并非同时参与滑移,而只有当外力在某一滑移系中的分切应力达到一定临界值时,该滑移系方可以首先发生滑移,该分切应力称为滑移的临界分切应力。
滑移的特点晶体的滑移并不是晶体的一部分相对于另一部分同时做整体的刚性的移动,而是通过位错在切应力作用下沿着滑移面逐步移动的结果,因此实际滑移的临界分切应力τk 比理论计算的低得多。
(滑移面为原子排列最密的面)单晶体滑移时,除滑移面发生相对位移外,往往伴随着晶面的转动。
第7章 回复、再结晶-2
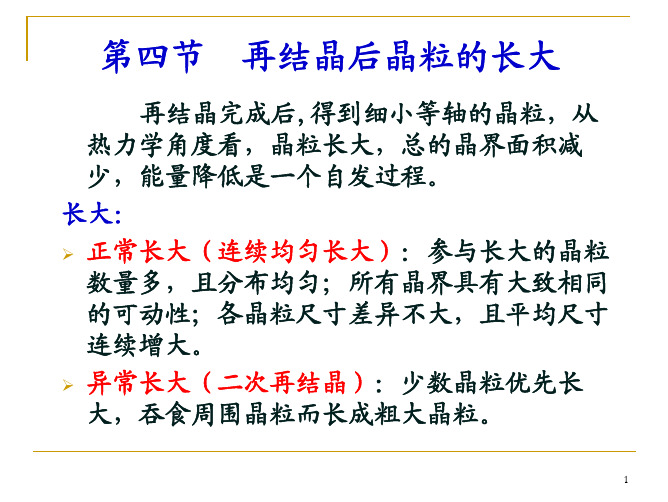
再结晶后晶粒的长大
再结晶完成后,得到细小等轴的晶粒,从 热力学角度看,晶粒长大,总的晶界面积减 少,能量降低是一个自发过程。 长大: ¾ 正常长大(连续均匀长大):参与长大的晶粒 数量多,且分布均匀;所有晶界具有大致相同 的可动性;各晶粒尺寸差异不大,且平均尺寸 连续增大。 ¾ 异常长大(二次再结晶):少数晶粒优先长 大,吞食周围晶粒而长成粗大晶粒。
式中:m 为比例常数,称为晶界的平均迁移率(即单位驱 动力作用下的晶界平均迁移速度);r 为晶界的平均曲率 半径,正常长大时r≈D。 m和σ对各种金属在一定温度均可视为常数,则:
近似有: 上式表明:在恒温下,晶粒发生正常长大时,平均直径与 保温时间的平方根成线性关系。 上述关系适用:高纯度金属在高温加热保温时。在一般情 况下,时间的指数小于1/2。
1
一、正常长大 长大方式: 依靠界面移动“大吃小、凹吃 凸”,长大中界面向曲率中心方向移 动,大晶粒吞食了小晶粒,直到晶界平 直化。
2
1、晶粒长大时的晶界迁移方向和驱动力 晶界迁移:晶界在其法线方向上的迁移。 晶界迁移的驱动力:界面能的减少,与曲率有关。(界面
向曲率中心方向移动将引起晶界面积减小,降低界面能。但这 种驱动力与储存能相比是较小的,所以晶粒长大时晶界迁移速 度比再结晶时慢。)
26
3、动态回复组织特点 在伸长的晶粒内部存在许多动态回复亚晶。 动态回复亚晶粒:胞壁位错密度小,胞内位错密度也 小。 当达到稳衡态时,动态回复亚晶有如下特征: 等轴状;胞状亚晶之间的取向差保持不变;胞壁之 间距离(亚晶尺寸)保持不变;胞壁之间的位错密度 保持不变。 注意:热加工过程中的动态回复不能看成是冷加工与 静态回复的叠加。应变与回复同时出现就避免了冷加 工效果的累积,所以,形变金属不能发展成高位错密 度,而且亚晶较细。 动态回复亚晶平均尺寸d与形变温度T和变形速率ε的 关系: d∝T/ε
铸件晶粒粗大的原因及防治措施

针对常州永青铸件晶粒粗大,中挖研究院与华强研究院一直在进行研究分析,主要原因有以下几方面造成:1)化学成份不合理;2)浇注系统设计不合理;3)热处理工艺不不合理;针对不同原因,我们主要做了如下工作;1)调整化学成份,严格控制化学成份,提高合金元素Ni含量(含量由0.2调整至0.4以上),改善晶粒大小,提高铸件冲击韧性;已于常州永青与12年4月批量实施;2)改善浇注系统,局部增加冷铁,改善冷却速度,以细化晶粒;已于常州永青与12年4月批量实施;4)改善热处理方式,延长保温时间和改善冷却方式以细化晶粒;已于常州永青与12年5月批量实施;5)改善热处理方式,热处理工艺有正火调整至正火加调质,使晶粒更细化;湖州运河从产品试制一致采用;6)7)在铸钢的熔化和脱氧操作中,加入合金元素的元素,因此和锻钢相比,铸钢不太容易形成品粒粗大。
因成分而引起品粒粗大的铸钢件,可通过退火或正火处理得到细化。
是指经过机械工或进行断口检验时,显示出晶粒组织过分粗大而不适合应用的缺陷,这种晶粒粗大的组织,可能是遍布于铸件整体,也可能发生于铸件的局部。
从本质上讲,晶粒粗大缺陷是一种冶金缺陷。
笔者根据多年的生产实践并参阅有关资料,谈谈铸件晶粒粗大缺陷产生的原因及防止措施。
1.铸件结构和工艺设计(1)铸件截面差异过,会因为较厚的截面冷却缓慢而造成该处晶粒粗大。
灰铸铁等对截面变化十分敏感的金属,更容易产生此类缺陷。
防止产生这类缺陷的有效方法是避免铸件截面尺寸过分悬殊,但这种途径有时是铸造工作者所无能为力的。
因而就铸造本身言,可通过采取设置冷铁、控制浇注温度或通过选择合适的浇汁系统来减少这类问题的发生,降低这类缺陷的严重程度。
采用冷铁可加快铸件较厚截面的冷却速度;浇注温度过高,会使这类问题更为严重,应予以避免;通过调节、修正浇注系统设计,使温度低的金属熔液位于铸件截面较厚的部位,并在铸件的厚截面处设计最有效的冒口,以尽可能减小冒口的尺寸。
4-晶粒长大
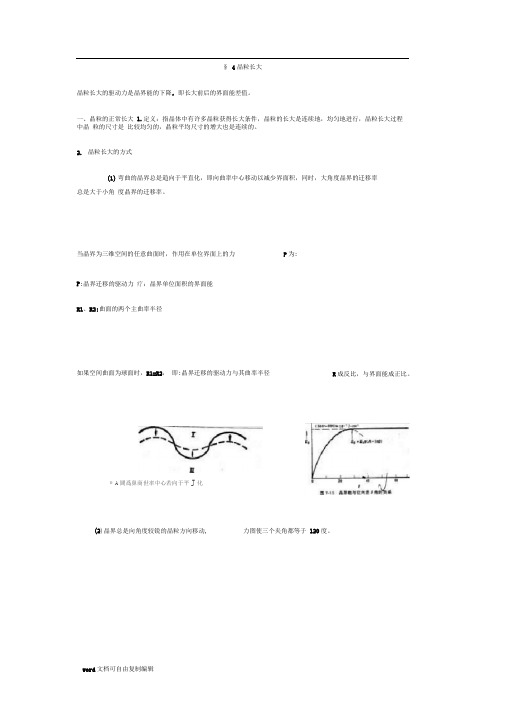
§ 4晶粒长大晶粒长大的驱动力是晶界能的下降,即长大前后的界面能差值。
一、晶粒的正常长大1.定义:指晶体中有许多晶粒获得长大条件,晶粒的长大是连续地,均匀地进行,晶粒长大过程中晶粒的尺寸是比较均匀的,晶粒平均尺寸的增大也是连续的。
2.晶粒长大的方式(1)弯曲的晶界总是趋向于平直化,即向曲率中心移动以减少界面积,同时,大角度晶界的迁移率总是大于小角度晶界的迁移率。
当晶界为三维空间的任意曲面时,作用在单位界面上的力P:晶界迁移的驱动力疗:晶界单位面积的界面能R1、R2:曲面的两个主曲率半径如果空间曲面为球面时,R1=R2,即:晶界迁移的驱动力与其曲率半径P为:R成反比,与界面能成正比。
(2)晶界总是向角度较锐的晶粒方向移动, 力图使三个夹角都等于120度。
® A闘爲鼻商世率中心若向于平J化在三维坐标中,晶粒长大最后稳定的形状是正十四面体。
3 .影响晶粒长大(即晶界迁移率)的因素(1)温度 温度越高,晶粒长大速度越快,晶粒越粗大RT}G:晶界迁移速度G0:常数QG 晶界迁移的激活能(2) 第二相晶粒长大的极限半径K :常数 r :第二相质点半径 f :第二相的体积分数当界面张力平衡时: 因为大角度晶界 在二维坐标中,晶界边数少于数大于6的晶粒,晶界 向内凹进,逐渐长大,当晶粒的边数为TA=TB=TC 而 A+B+C=360度 /• A=B=C=120度6的晶粒,其晶界向外凸出,必然逐渐缩小,甚至消失,而边6时,处于稳定状态。
1■兀■兀Sin B sm C7,• •第二相质点的数量越多,颗粒越小,则阻碍晶粒长大的能力越强。
设第二相颗粒为球形,对晶界的阻力为 F ,与驱动力平衡F = Z TT cos(^-<7-cospO°-/J)6C0妙—妙 (1) a 角只取决于第二相颗粒与晶粒间的表面张力,可看作恒定值,现将( 竺0令却 ,可得: 盂+ (2)F 住=叫TP (1 + COE 氐) (3) 设单位体积中有NV 个质点,其体积分数为f4=一曲3 (5)的正方体,所有中心位于这个 1 X 1 X 2r 体积内半径为r 的第二相颗分晶界交截,单位面积晶界将与1 X 1X 2r X NV 个晶粒交截。
06 金属材料热处理 第六章 变形金属及合金的回复与再结晶

第六章 变形金属与合金的回复与再结晶本章教学目的:1 揭示形变金属在加热过程中组织和性能变化的规律;2 揭示再结晶的实质3 说明热加工与冷加工的本质区别以及热加工的特点。
教学内容:(1)变形金属在退火过程中(回复,再结晶以及晶粒长大)过程的组织与性能变化;(2)影响再结晶的因素;(3)再结晶晶粒大小及控制;(4)热加工与冷加工重点:(1)回复与再结晶的概念和应用;(2)临界变形度的概念;(3)再结晶晶粒度的控制;(4)热加工与冷加工的区别。
难点:(1)再结晶形核机制与再结晶动力学;(2)再结晶晶粒的二次长大机理§6-1变形金属与合金在退火过程中的变化金属经冷塑性变形后,内部组织和各项性能均发生相应变化,而且由于位错等结构缺陷密度的增加以及畸变能的升高,使其处于热力学不稳定状态。
当变形金属加热时,通过原子扩散能力的增加,有助于促进向低能量状态的转变。
一、显微组织的变化第一阶段:显微组织基本上未发生变化,其晶粒仍保持纤维状或扁平状变形组织,称回复阶段。
第二阶段:以新的无畸变等轴小晶粒逐渐取代变形组织,称为再结晶阶段。
第三阶段:上述小晶粒通过互相吞并方式而长大,直至形成较为稳定的尺寸,称为晶粒长大阶段。
二、储存能及内应力的变化当变形金属加热到足以引起应力松弛的温度时,其中的储存能将释放出来。
回复阶段释放的储存能很小三、机械性能的变化规律回复阶段硬度变化很小,约占总变化的1/5,再结晶阶段下降较多,强度与硬度有相似的变化规律。
因为回复阶段仍保持很高的位错密度。
在再结晶阶段,硬度与强度显著下降,塑性大大提高。
四、其它性能的变化1、电阻的变化电阻的回复阶段已表现出明显的下降趋势。
点缺陷对电阻的贡献远大于位错,而回复阶段点缺陷的密度发生显著的减小。
2、密度的变化再结晶阶段密度急剧增高。
五、亚晶粒尺寸在回复阶段前期,亚晶粒尺寸变化不大,但在后期,尤其在接近再结晶温度时,晶粒尺寸显著增大。
§6-2 回复一、退火温度和时间对回复过程的影响回复是指冷塑性变形的金属在加热时,在光学显微组织发生改变之前所产生的某些亚结构和性能的变化过程。
6回复与再结晶

•
黄铜冷加工变形量达到C 38% (a)黄铜冷加工变形量达到CW=38%后的组织 580ºC保温3 (b)经580 C保温3秒后的组织
(a)可见粗大晶粒内的滑移线 ) (b)试样上开始出现白色小的颗粒,即再结晶出的新的晶粒 )试样上开始出现白色小的颗粒,
580ºC保温4 (c)580 C保温4秒后的金相组织 580ºC保温8 (d)580 C保温8秒后的金相组织
加热时冷变形金属显微组织发生变化
黄铜再结晶和晶粒长大各个阶段的照片
•
退火时,由于温度升高原子的能动性增加, 退火时,由于温度升高原子的能动性增加,即原子的 扩散能力提高, 回复阶段只是消除了由由于冷加工应变 扩散能力提高,而回复阶段只是消除了由由于冷加工应变 能产生的残余内应力,大部分应变能仍然存在, 能产生的残余内应力,大部分应变能仍然存在,变形的晶 粒仍未恢复原状。所以,随着保温时间加长, 粒仍未恢复原状。所以,随着保温时间加长,新的晶粒核 心便开始形成并长大成小的等轴晶粒,这就是再结晶 再结晶的开 心便开始形成并长大成小的等轴晶粒,这就是再结晶的开 随着保温时间的加长或温度的升高, 始。随着保温时间的加长或温度的升高,再结晶部分愈来 愈多,直到原来的晶粒全部被新的小晶粒所代替。 愈多,直到原来的晶粒全部被新的小晶粒所代替。进一步 晶粒长大现象。 保温或升温,新晶粒尺寸开始增大,这就是晶粒长大现象 保温或升温,新晶粒尺寸开始增大,这就是晶粒长大现象。 可用下图为黄铜再结晶和晶粒长大各个阶段的照片来 说明退火过程中的这种变化本照片。 说明退火过程中的这种变化本照片。
(c)显示有更多新的晶粒出现 ) (d)粗大的带有滑移线的晶粒已完全被细小的新晶粒所取代,即完成了再结晶 )粗大的带有滑移线的晶粒已完全被细小的新晶粒所取代,
第七章 回复与再结晶(新)
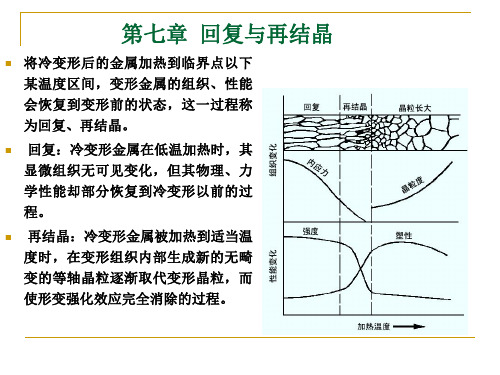
过程:
亚晶蚕食机制示意图
① ρ很大的小区域位错攀移重分布,使位错运动到相邻晶粒, 形成一个ρ低的小区域。 ②ρ低的区域逐渐扩大,其与周围区域的位向角增大。 ③当小区域扩大到一定体积,与周围晶粒之晶界变为大角晶界。 ④大角晶界弓出形成核心。
三种形核机制都是大角度晶界的突然迁移,所不同的是获得大角度晶界的途径不同。
超塑性
超塑性:某些材料在特定变形条件下呈现的特别大的延伸率。 条 件 : 晶 粒 细 小 、 温 度 范 围 ( 0.5~0.65Tm ) 、 应 变 速 率 小 ( 1 ~ 0.01%/s)。 本质:多数观点认为是由晶界的滑动和晶粒的转动所致。 应用:复杂零件的精密成形;难于热变形材料的加工。
晶粒的异常长大
1 异常长大: 少数再结晶晶粒的急剧长大现象 (二次再结晶) 2 基本条件:正常晶粒长大过程被(第二分散相微粒、织构)强烈阻碍。 3 驱动力:界面能变化(不是重新形核) 4 原因:晶粒内部肯定存在大量的阻止晶粒长大的因素。 1)合金元素附集晶界,阻碍晶界迁移。 2)第二相粒子阻碍晶界运动。
第七章 回复与再结晶
将冷变形后的金属加热到临界点以下 某温度区间,变形金属的组织、性能 会恢复到变形前的状态,这一过程称 为回复、再结晶。 回复:冷变形金属在低温加热时,其 显微组织无可见变化,但其物理、力 学性能却部分恢复到冷变形以前的过 程。 再结晶:冷变形金属被加热到适当温 度时,在变形组织内部生成新的无畸 变的等轴晶粒逐渐取代变形晶粒,而 使形变强化效应完全消除的过程。
动态再结晶
热加工后的组织与性能
(1)改善铸锭组织。气泡焊合、破碎碳化物、细化晶粒、降低偏析。提 高强度、塑性、韧性。 (2)形成纤维组织(流线)。 组织:枝晶、偏析、夹杂物沿变形方向呈纤维状分布。 性能:各向异性。沿流线方向塑性和韧性提高明显。 (3)形成带状组织 形成:两相合金变形或带状偏析被拉长。 影响:各向异性。类似于流线组织。 消除:避免在两相区变形、减少夹杂元素含量、采用高温扩散退火或 正火。
- 1、下载文档前请自行甄别文档内容的完整性,平台不提供额外的编辑、内容补充、找答案等附加服务。
- 2、"仅部分预览"的文档,不可在线预览部分如存在完整性等问题,可反馈申请退款(可完整预览的文档不适用该条件!)。
- 3、如文档侵犯您的权益,请联系客服反馈,我们会尽快为您处理(人工客服工作时间:9:00-18:30)。
§4 晶粒长大
晶粒长大的驱动力是晶界能的下降,即长大前后的界面能差值。
一、晶粒的正常长大
1.定义:指晶体中有许多晶粒获得长大条件,晶粒的长大是连续地,均匀地进行,晶粒长大过程中晶粒的尺寸是
比较均匀的,晶粒平均尺寸的增大也是连续的。
2.晶粒长大的方式
(1)弯曲的晶界总是趋向于平直化,即向曲率中心移动以减少界面积,同时,大角度晶界的迁移率总是大于小角
度晶界的迁移率。
当晶界为三维空间的任意曲面时,作用在单位界面上的力P为:
P:晶界迁移的驱动力
:晶界单位面积的界面能
R1、R2:曲面的两个主曲率半径
如果空间曲面为球面时,R1=R2 ,即:晶界迁移的驱动力与其曲率半径R成反比,与界面能成正比。
(2)晶界总是向角度较锐的晶粒方向移动,力图使三个夹角都等于120度。
,
当界面张力平衡时:因为大角度晶界TA=TB=TC,而 A+B+C=360度∴A=B=C=120度
在二维坐标中,晶界边数少于6的晶粒,其晶界向外凸出,必然逐渐缩小,甚至消失,而边数大于6的晶粒,晶界
向内凹进,逐渐长大,当晶粒的边数为6时,处于稳定状态。
在三维坐标中,晶粒长大最后稳定的形状是正十四面体。
3.影响晶粒长大(即晶界迁移率)的因素
(1)温度温度越高,晶粒长大速度越快,晶粒越粗大
G:晶界迁移速度
G0:常数
QG:晶界迁移的激活能
(2)第二相晶粒长大的极限半径
K:常数
r:第二相质点半径
f:第二相的体积分数
∴第二相质点的数量越多,颗粒越小,则阻碍晶粒长大的能力越强。
设第二相颗粒为球形,对晶界的阻力为F,与驱动力平衡
(1)
α角只取决于第二相颗粒与晶粒间的表面张力,可看作恒定值,现将(1)式对φ求极大值,
令,可得:(2)
假设在单位面积的晶界面上有NS个第二相颗粒,其半径都为r,则总阻力
(3)
设单位体积中有NV个质点,其体积分数为f
(4)
(5)
取单位晶界面积两侧厚度皆为r的正方体,所有中心位于这个1×1×2r体积内半径为r的第二相颗粒,都将与这部
分晶界交截,单位面积晶界将与1×1×2r×NV个晶粒交截。
将(4)、(5)式代入(3)式
(6)
这个总阻力与晶界驱动力平衡
∴
整理得:(7)
可看作常数,令
∴(8)
(3)可溶解的杂质或合金元素阻碍晶界迁移,特别是晶界偏聚现象显著的元素,其阻碍作用更大。
但当温度很高
时,晶界偏聚可能消失,其阻碍作用减弱甚至消失。
二、晶粒的异常长大(二次再结晶)
1.定义:将再结晶完成后的金属继续加热至某一温度以上,或更长时间的保温,会有少数几个晶粒优先长大,成
为特别粗大的晶粒,而其周围较细的晶粒则逐渐被吞食掉,整个金属由少数比再结晶后晶粒要大几十倍甚至几百
倍的特大晶粒组成。
2.驱动力:同正常晶粒长大一样,是长大前后的界面能差
3.产生条件:正常晶粒长大过程被弥散的第二相质点或杂质、织构等所强烈阻碍。
4. 对性能的影响:得到粗大组织,降低材料的室温机械性能,大多数情况下应当避免。