炼钢精炼工艺和设备
炼铁炼钢工艺流程

炼铁炼钢工艺流程炼铁炼钢是冶金工艺中的重要环节,通过对铁矿石的提炼和精炼,最终获得高质量的钢铁产品。
下面将详细介绍炼铁炼钢的工艺流程。
一、炼铁工艺流程1. 副矿材料预处理:将收集的副矿材料经过破碎、筛分、磁选等工序处理,去除杂质,得到纯净的副矿材料。
2. 铁矿石处理:将铁矿石破碎、浸泡于水中,去除表面的杂质,然后经过磁力分离、重力选矿等工序,将铁矿石中的有用成分提取出来。
3. 炼铁炉炼炉:将提取的铁矿石与焦炭、石灰石等原料混合,投入高炉中进行炼制。
高炉内温度达到1500℃以上,矿石中的铁含量经过还原反应被提取出来,形成生铁。
4. 生铁处理:将炼出的生铁经过浇铸或炼钢炉炉处理,去除其中的硫、磷等杂质,得到优质的铁合金。
二、炼钢工艺流程1. 炼钢炉前处理:将铁合金破碎、筛分,去除其中的杂质,得到纯净的铁合金。
2. 炼钢炉炼炉:将铁合金与适量的废钢、废铁加入炼钢炉中,进行炼制。
炼钢炉内温度高达1600℃以上,通过氧气吹吹炼,使废钢等物质被氧化,产生大量热,达到熔化的目的。
3. 炼钢炉后处理:炼钢完成后,钢水需要进行过滤、脱硫等处理,以去除其中的杂质。
此外,还需要根据不同的需求,添加适量的合金等元素,调整钢的成分和性能。
4. 连铸成型:将经过处理的钢水注入到连铸机中,通过涡轮旋转或摇摆,使钢水冷却凝固,形成钢坯。
钢坯可进一步进行轧制、锻造等加工,制成不同形状的钢材。
以上就是炼铁炼钢的工艺流程。
通过这个过程,铁矿石和副矿材料得到了有效的利用,矿石中的铁成分被提取出来,并经过加工得到高质量的钢材。
这个工艺流程不仅具有广泛的应用价值,还在很大程度上推动了工业化的进程。
钢包精炼炉设备规格书及说明

钢包精炼炉设备规格书及说明一、设备概况钢包精炼炉是钢铁冶炼工艺的重要设备,用于去除钢水中的氧化物、硫化物、氮化物和其他杂质,从而提高钢水的质量。
该设备主要包括钢包本体、倾转装置、电加热设备、倾炉机构、底吹氩气设备等部分。
二、设备规格1. 钢包本体- 采用优质碳素钢板制造,内壁使用耐高温耐磨材料覆盖,提高耐磨性和耐火性。
- 直径:根据生产要求确定- 高度:根据生产要求确定- 底部配有倾炉孔和底吹氩气孔2. 电加热设备- 采用高温合金发热丝,加热效率高,耐高温性能好- 电加热功率:根据钢包大小和设计要求确定- 温度控制系统:可实现精确的温度控制,自动调节加热功率3. 倾转装置- 采用液压或机械倾转装置,可实现任意角度的倾转- 倾转速度可调,倾转平稳可靠4. 底吹氩气设备- 用于通过底部孔向钢水中喷吹氩气,去除氧化物等杂质- 氩气流量可调,可实现不同生产工艺要求三、操作说明1. 在使用前,需要进行设备检查和维护保养,确保设备运行正常2. 启动加热设备,设定加热温度和保温时间3. 将炼钢炉钢水倾入精炼炉内,启动底吹氩气设备4. 在适当的时机,使用倾转装置倾倒钢水,并进行精炼处理5. 精炼完成后,停止加热设备,并将精炼后的钢水倾出6. 定期对设备进行维护保养,保证设备长期稳定运行以上为钢包精炼炉设备的规格书及使用说明。
希望使用人员按照相关操作规范进行使用和维护,确保设备的安全运行和生产效率。
很高兴能够给您提供更多相关内容。
让我们继续讨论钢包精炼炉设备的使用细节及相关重要信息。
四、使用注意事项1. 安全操作:在使用钢包精炼炉设备时,操作人员必须严格遵守相关安全操作规程,穿戴好劳动防护用具,确保人身安全。
2. 设备维护:定期对电加热设备、倾转装置和底吹氩气设备进行维护保养,保证设备的正常运行和稳定效率。
3. 加热控制:在加热过程中,需要根据钢水温度和生产工艺要求,精确控制加热功率和保温时间,确保钢水温度达到要求。
LF精炼炉主要设备及技术特点
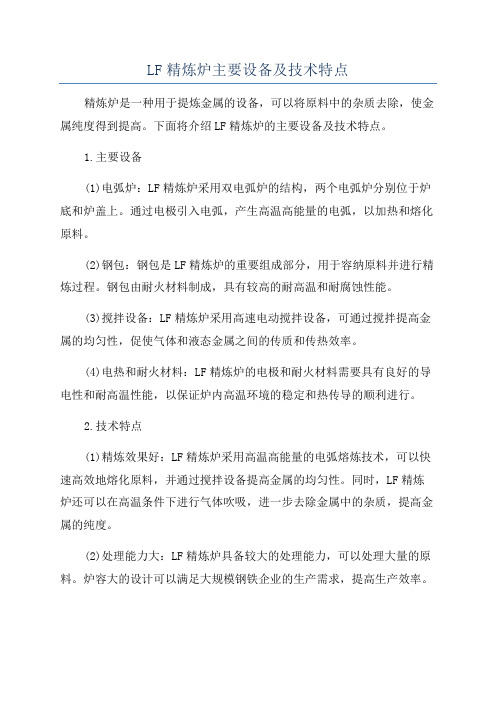
LF精炼炉主要设备及技术特点精炼炉是一种用于提炼金属的设备,可以将原料中的杂质去除,使金属纯度得到提高。
下面将介绍LF精炼炉的主要设备及技术特点。
1.主要设备(1)电弧炉:LF精炼炉采用双电弧炉的结构,两个电弧炉分别位于炉底和炉盖上。
通过电极引入电弧,产生高温高能量的电弧,以加热和熔化原料。
(2)钢包:钢包是LF精炼炉的重要组成部分,用于容纳原料并进行精炼过程。
钢包由耐火材料制成,具有较高的耐高温和耐腐蚀性能。
(3)搅拌设备:LF精炼炉采用高速电动搅拌设备,可通过搅拌提高金属的均匀性,促使气体和液态金属之间的传质和传热效率。
(4)电热和耐火材料:LF精炼炉的电极和耐火材料需要具有良好的导电性和耐高温性能,以保证炉内高温环境的稳定和热传导的顺利进行。
2.技术特点(1)精炼效果好:LF精炼炉采用高温高能量的电弧熔炼技术,可以快速高效地熔化原料,并通过搅拌设备提高金属的均匀性。
同时,LF精炼炉还可以在高温条件下进行气体吹吸,进一步去除金属中的杂质,提高金属的纯度。
(2)处理能力大:LF精炼炉具备较大的处理能力,可以处理大量的原料。
炉容大的设计可以满足大规模钢铁企业的生产需求,提高生产效率。
(3)过程控制精确:LF精炼炉采用先进的自动化控制系统,可以实时监测和控制炉内温度、压力等参数,保证精炼过程的稳定性和精确性。
同时,还可以根据不同的原料和工艺要求进行灵活的调整和控制。
(4)能源消耗低:LF精炼炉采用高效的电弧熔炼技术,其能源消耗相对传统炼钢方法更低。
此外,精炼过程中的气体吹吸也能够有效利用高温和高压气体的能量,降低能源浪费。
(5)环保节能:LF精炼炉在炼钢过程中产生的废气可通过尾气处理系统进行净化处理,达到环保排放标准。
同时,由于能源消耗低,可以降低对自然资源的需求,具有良好的节能效果。
综上所述,LF精炼炉作为一种重要的炼钢设备,具备精炼效果好、处理能力大、过程控制精确、能源消耗低和环保节能等技术特点,能够满足现代化钢铁生产的需求,推动钢铁行业的发展。
精炼炉炼钢原理与工艺

精炼炉炼钢原理与工艺引言:钢铁工业是现代工业的基础和重要支撑,而钢铁的生产中,精炼炉是不可或缺的重要设备之一。
本文将介绍精炼炉炼钢的原理与工艺,让读者对精炼炉的作用和工作过程有更深入的了解。
一、精炼炉的原理精炼炉是在炼钢过程中用于进一步减少钢液中杂质含量、提高钢液质量的设备。
其主要原理是利用物理、化学和冶金学的知识,通过各种操作手段,将钢液中的非金属夹杂物和气体溶解物质排除,以达到提高钢液纯度和质量的目的。
二、精炼炉的工艺1. 加入炉料精炼炉的第一步是将炉料加入炉内。
炉料通常由钢液和精炼剂组成。
其中,钢液是需要进行精炼的主要物料,而精炼剂则是用来吸附和吸收钢液中的杂质的物质。
2. 提升温度在精炼炉中,钢液需要保持一定的温度。
通常情况下,钢液的温度会通过加热设备进行升温,以满足后续的精炼工艺需要。
温度的控制对于精炼炉的工艺效果至关重要。
3. 氧气吹炼精炼炉中常采用氧气吹炼技术,通过向钢液中吹入氧气,使钢液中的杂质被氧化并排除。
氧气吹炼能够有效地去除钢液中的硫、磷等杂质,提高钢液的纯度。
4. 加入精炼剂在精炼炉的过程中,加入精炼剂是必不可少的一步。
精炼剂能够与钢液中的杂质发生反应,形成易于排除的化合物或气体。
常见的精炼剂包括石灰、氧化钙等。
5. 搅拌为了加快杂质与精炼剂的反应速度和提高反应效果,精炼炉内通常会设置搅拌装置,对钢液进行搅拌。
搅拌可以使钢液中的杂质更加均匀地与精炼剂接触,促进反应的进行。
6. 渣化处理在精炼炉中,产生的渣是需要处理的。
渣是由精炼剂和钢液中的杂质组成的固体物质。
通过合理的渣化处理工艺,将渣排出,以保证钢液的纯净度。
7. 出钢精炼炉中的工艺完成后,即可进行出钢操作。
出钢是将经过精炼的钢液从精炼炉中排出,并送往下一道工序进行后续加工。
出钢的操作需要注意保持钢液的温度和纯净度,以确保钢液质量的稳定。
结语:精炼炉炼钢原理与工艺是钢铁生产过程中至关重要的环节。
通过精炼炉的操作,可以有效地提高钢液的纯度和质量,满足不同行业对钢材的需求。
炼钢工艺流程图

炼钢厂工艺流程与设备规格性能一、炼钢厂工艺流程图二、炼钢厂示意图1、转炉示意图及工艺参数工艺参数转炉炉体1.1炉体总高(包括炉壳支撑板):7050mm1.2炉壳高度:6820mm1.3炉壳外径:Φ4370mm1.4高宽比: H/D=1.561.5炉壳内径:Φ4290mm1.6公称容量:50t1.7有效容积:39.5m31.8熔池直径: Φ3160mm1.9炉口内径:Φ1400mm1.10出钢口直径:140mm1.11出钢口倾角(与水平):20°1.12炉膛内径:Φ3160mm1.13炉容比:0.79m3 /t.s1.14熔池深度:1133mm1.15炉衬厚度:熔池:500mm 炉身:500mm 炉底:465mm 炉帽:550mm 1.16炉壳总重:77.6t1.17炉衬重量:120t1.18炉口结构:水冷炉口1.19炉帽结构:水冷炉帽1.20挡渣板结构:双层钢板焊接式1.21托圈结构:箱式结构(水冷耳轴)倾动装置型式:四点啮合全悬挂扭力杆式(交流变频器调速)最大工作倾动力矩:100t*m最大事故倾动力矩:300t*m倾动角度:±360°倾动速度:0.2~1r/min二、方坯连铸示意图大包中包方坯弧形连铸机铸机基本参数:机型:全弧形铸机弧型半径:R6000/12000mm;机~流:5~5流间距:1250mm弯曲:连续弯曲矫直:连续矫直铸坯规格:120mm × 120mm;150mm × 150mm;100mm × 173mm;130mm × 173mm;拉速:120mm × 120mm 3.2~3.76 m/min;150mm × 150mm 2.0~3.0 m/min;100mm × 173mm; 2.8~3.4 m/min;130mm × 173mm; 2.0~3.0 m/min;冶金长度: 14.69 m(全凝固矫直);17.27 m(带液芯矫直)铸机长度:16.16m(铸机外弧基准线至固定挡板)定尺长度:3~6m铸机有效作业率:85%钢水收得率:96.8%设计年产量:80万吨/年三、板坯连铸大包中包结晶器板坯连铸机示意图铸机基本参数:机型:立弯式连铸机铸机弧型半径:6000mm;机~流:2~2流间距:4700mm弯曲:8点弯曲,R65000mm、R30600mm、R19300mm、R14000mm、R11000mm、R9000mm、R7200mm、R6000mm矫直:6点矫直,R6000mm、R7200mm、R9000mm、R11700mm、R16700mm、R31600mm 铸坯规格:150mm × 350~680mm;180mm × 350~680mm;200mm × 350~680mm;拉速:150mm × 350~680mm; V max:1.6 m/min; 180mm × 350~680mm; V max:1.5 m/min;200mm × 350~680mm; V max:1.2 m/min;冶金长度:17.43 m铸机长度:17.43 m定尺长度:6500m铸机有效作业率:82%钢水收得率:97%设计年产量:60万吨/年。
炼钢-精炼工艺介绍
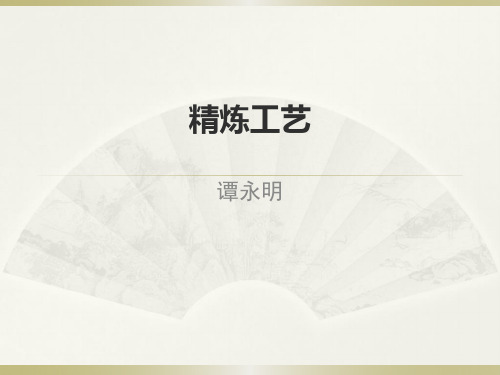
CAS底吹排渣工艺
4、CAS工艺
排渣效果(裸露钢液面面积)主要与渣层厚度、渣粘度和底吹氩 能力等有关。在底吹排渣过程中,随着底吹氩气流量增大,排渣 面积增大,但当底吹氩气流量达到一定值后,进一步增大底吹氩 气流量,其排渣效果变化不大。应选择较佳的底吹氩排渣流量, 防止钢水散热过多和减少氩气消耗量。
1.3增碳剂 袋装20Kg/包,要求固定碳含量≥94%,S≤0.5%,H2O≤0.5% 粒度3-8mm。
1、精炼过程用原料
1.4常用气体 1.4.1惰性气体 氮气、氩气等为冶金用惰性气体。主要用于二次钢水的保
护与隔离,以及对钢水精炼时的搅拌、吸气、去杂质等。 对人体的危害表现为窒息性伤害,浓度达到25g/m3时有危 险。 要求:干燥、干净、无杂质、水分<1%、纯度≥99.9%、 氧气<6PPm、氮气<20PPm、氧气+氮气≯20PPm 1.5钢包炉用材料 1.5.1冶金石灰: 采用转炉炼钢用活性石灰,保存期不得大于10天。
Si
74.0~80.0 72.0~80.0
化学成份,%
Mn
Cr
P
不大于
0.4
0.3
0.035
0.5
0.5
0.04
Si-Ca-Ba包芯线:
Si%
Ca% Ba% P%
≥50
≥14
≥14
≤0.02
Si-Ca包芯线:
Si%
Ca%
≥50
≥28
Al线:
P% ≤0.02
S% ≤0.03
S% ≤0.03
1、精炼过程用原料
二级 一级 特级
CaO% ≥85.0 ≥90.0 ≥92.0
SiO2% ≤3.5 ≤2.5 ≤1.5
炼钢厂RH精炼炉项目第二部分在线工艺设备

炼钢厂RH精炼炉项目技术规格书附件二设备技术规格书1.工艺设备技术规格书1.1钢包运输车(顶升钢包托盘)钢包运输车将钢包从钢水接收跨的承接位置输送到真空槽下脱气工位进行真空处理,然后送往保温剂添加工位。
本钢包运输台车最大承受输送钢包钢水的设计能力为320吨,钢包与钢水总重450吨。
该车采用电机驱动,可由机旁操作箱或主控室控制。
该车车体由框梁配高强度螺栓连成一体。
钢包放置在托盘上。
真空处理时,钢包与托盘一起被顶升。
该车两端装有紧急用拖钩,并设有车端缓冲器。
紧急情况下,可用一钢丝绳系在该车上,借助跨间的桥式起重机进行移动。
为此在该跨间需配有一钢绳滑轮。
车体内砌有耐火衬砖,万一发生跑钢可避免毁坏台车、轨道及液压升降设备。
在真空槽去渣壳时,可采用一专用支承构件,把渣罐放置钢包车上。
钢包运输台车有八个轮子,其中4个驱动轮,4个从动轮。
所用轨道型号为QU120起重机轨道。
这些轮子由锻钢制成。
该车轴承的润滑采用手动集中润滑系统。
该系统通过一手动给脂机把润滑脂由车上的分配器(它通过硬管和软管同每一轴承相连)注入到润滑点。
车子的两端各装有一闪光警灯并配备一个电子报警器。
每当车子运行时,这些报警装置进行报警。
钢包运输台车由两台鼠笼式电机驱动,电机连接联轴器、减速器和驱动轴。
速度通过变频控制。
刹车器设置位置安装在易于操作和维护之处,该刹车器的线圈与电机的控制要联锁。
钢包运输台车的电源由电缆卷筒(自动卷绕系统)来提供。
技术参数:* 车身总长约 10000mm总宽约 4800mm* 轨距 4200mm* 轮距 6700mm轮子直径约1000mm* 钢轨型号 QU120* 承载能力约255 t(包括钢水、钢包、接渣盘及冷钢) * 走行速度最大约 30m/min* 定位精度±15mm* 速度控制由变频器(VVVF)* 电源供给型式电缆卷筒、滑环转矩电动机减速机生产厂家SEW/FULANDE轴承生产厂家NSK/SKF设备估重170吨(含接渣盘)1.2钢包液压升降系统1.2.1 概述钢包升降系统用于在真空处理位,顶升钢包台车及盛有钢水的钢包,使RH真空浸渍管浸入钢水一定深度,待钢水处理结束后,再将钢包车及钢包降落在轨道上。
炼钢车间生产工艺简介

一 级 真 空 泵
二 级 真 空 泵
钢包
炼钢车间生产工艺简介
(2)主要功能:脱碳、脱气、调整钢水成份和温度、 去除夹杂等,尤其是脱[H]效果显著;
(3)冶炼钢种:重轨钢系列、弹簧钢系列、工业纯 铁等。
精诚合作
携手共赢
条材总厂一炼钢分厂炼钢车间
(3)[Mn]的氧化反应 [Mn]的氧化反应
炼钢生铁中含有一定量的[Mn],在炼钢熔池中,有一部分[Mn]会被氧化 炼钢生铁中含有一定量的[Mn],在炼钢熔池中,有一部分[Mn]会被氧化 [Mn] [Mn] 掉。
(4) 脱磷反应
造成钢材冷脆 有利于脱磷的条件—— 三高一低” ——“ 有利于脱磷的条件——“三高一低”: 高碱度、大渣量、 FeO)、 )、低温 高碱度、大渣量、高(FeO)、低温
炼钢车间生产工艺简介
3、炼钢用原材料
炼钢用原材料一般分为主原料、辅原料和各种气体介质。 一、主原料:铁水、废钢 二、辅原料:铁合金、造渣剂 1)铁合金: 吹炼终点脱除钢中多余的氧,并调整成 分达到 钢种规格,需加入铁合金以脱氧合金化 2)造渣剂:石灰、轻烧白云石、萤石等 三、气体介质:氧气、氩气、氮气等
2.2 VD炉简介
炼钢车间VD炉原计划于今年7月份拆除,在其基 础上建设2#RH炉,但在综合权衡其利弊后,拆 除计划暂时取消。 (1)主要设备:真空泵系统、炉盖、双工位地坑、 计测仪表及控制系统; (2)主要功能:真空脱气、去夹杂、均匀成份和 温度等,尤其是脱氮效果较好; (3)冶炼钢种:82B系列、帘线82A等对[N]要 求高的钢种。
炼钢车间生产工艺简介
一、炼钢基本原理与工艺
1、炼钢的基本任务
1).脱碳、脱磷、脱硫、脱氧; 2).去除有害气体和夹杂; 3).调整成分和温度;
- 1、下载文档前请自行甄别文档内容的完整性,平台不提供额外的编辑、内容补充、找答案等附加服务。
- 2、"仅部分预览"的文档,不可在线预览部分如存在完整性等问题,可反馈申请退款(可完整预览的文档不适用该条件!)。
- 3、如文档侵犯您的权益,请联系客服反馈,我们会尽快为您处理(人工客服工作时间:9:00-18:30)。
可编辑ppt
13
LF处理
钢水首次加温是为了使温度和化学成分均匀以 及熔渣。如果必须的话,进一步添加合成渣。 渣料熔化后,测温取样,接着继续升温。根据 试样分析的结果和钢种目标值,LF计算机算出 需要加入的LF的物料种类和物料量,并将指令 发送至上料系统PLC,该系统可根据LF计算机 指令在规定时间向LF加入规定牌号的剂量的造 渣料或铁合金并加入到钢包中。对有特殊要求 的钢种,可进行额外的加合金步骤,喂丝,软 搅拌纯净处理,或者液态钢水仅仅放在LF直到 下道工序准备接收("缓冲功能")。
LF为钢水提供了合金微调的条件,钢水在LF工 位进行合金微调处理可精确控制钢水成份,同 时LF的加热功能可以保证钢水的温度。
可编辑ppt
10
转炉出钢
为了消除炉渣(FeO,MnO)对后工艺处理 和连铸过程中的负面影响,在转炉中必 须少渣出钢。所要求的脱氧材料和合金 元素(大约占所要求量的90%)在出钢时加 入。出钢时和出钢后的惰性气体搅拌必 须良好,以提高均匀度。
可编辑ppt
7
设备组成:电气设备
高压设备 变压器 基础自动化及控制画面系统 仪表设备
可编辑ppt
8
设备组成:辅助设备
钢包台车 喂丝系统 测温取样装置 钢包底吹氩系统 电极接长和储放站 事故吹氩枪 加料溜槽系统 保温剂投入装置
可编辑ppt
9
LF钢包精炼炉精炼工艺
LF作为转炉的炉外精炼设备,对转炉的初炼钢 水进行温度控制、合金微调、脱氧、脱硫以及 对钢水成份和温度均匀化等精炼处理。与连铸 机配合时,LF在转炉与连铸机之间起到缓冲作 用,向连铸机及时提供合格钢水。
可编辑ppt
11
钢包运输
行车将钢包吊至LF钢包台车上,此时, 钢包底部吹氩管路自动接通,并开始吹 氩搅拌。在此工位,LF处理前的各项准 备就绪,如:电极准备、设备确认、通 电准备、冷却水准备、合金及辅材准备、 液压准备。完成之后,钢包台车开到LF 处理工位。
可编辑ppt
12
钢包处理
钢包被运到LF处理工位后,进行钢包处 理: 人工手动或自动测定渣厚、炉盖下 降、吹氩操作,吹氩搅拌的强度根据模 型调整,通过人工确认,并且全程吹氩。
可编辑ppt
14
LF处理
在达到目标温度和化学成分后精炼完成。 然后电极提升,炉盖提升,钢包台车从 精炼工位开到保温剂投入工位,投入保 温剂后台车开至钢包起吊工位,由行车 运到连铸机。开至钢包起吊工位,由行 车吊运到连铸机浇铸。
可编辑ppt
15
精炼工艺和设备
可编辑ppt
1
精炼设备
一台150吨LF钢包精炼炉 一台150吨RH真空脱气装置
可编辑ppt
2
生产工艺
BOF
LF RH
CCM
可编辑ppt
3
150吨LF钢包精炼炉介绍
可编辑ppt
4
LF钢包精炼炉具备功能
升温和精确调整液态钢水温度 深脱硫功能 深脱氧功能 减少钢中夹杂物和控制夹杂物形态 提高钢水的均匀度(温度和化学成分) 确保CC连浇、调节炼钢生产节奏 低的LF处理精炼成标
平均处理量150吨液态钢水,最大180吨
年处理能力 120万吨
平均处理周期 35分钟
升温速度 ≥ 4 °C/min
脱硫率
≥ 55%
电能消耗 ≤0.48~0.50 Kwh/t oC
电极消耗 ≤10~12 g/ Kwh
可编辑ppt
6
设备组成:主体设备
炉盖及其提升装置 电极调节机构 电极横臂(覆铜) 系统 变压器二次侧系统 水和其他介质系统 液压系统