工艺流程和工艺设备的选择和计算
化工设备选型及设计计算

化工设备选型及设计计算1. 简介化工设备的选型及设计计算在化工工程设计中起着至关重要的作用。
合理的设备选型和设计计算可以提高生产效率、降低生产成本,同时保证设备的安全运行。
本文将介绍化工设备的选型和设计计算的基本原理和方法。
2. 化工设备选型2.1 设备选型的原则在进行设备选型时,需要考虑以下几个原则:1.工艺要求:设备的选型必须满足工艺流程的要求,包括温度、压力、流量、反应时间等方面。
2.材料的适应性:设备的材料必须能适应工艺介质的性质,包括酸碱性、腐蚀性、温度和压力等。
3.经济性:设备的选型应综合考虑设备的投资和运行成本。
2.2 设备选型的步骤设备选型的步骤一般包括以下几个方面:1.确定工艺流程:首先需要确定工艺流程,包括反应过程、分离过程等。
根据工艺流程确定所需的设备种类。
2.评估设备性能:评估设备的性能指标,包括设备的传热效率、传质效率、搅拌效果等。
3.比较不同设备类型:根据设备的性能指标,比较不同种类的设备,选择经济合理且能满足工艺流程要求的设备。
4.考虑设备的维护和运行成本:除了设备的投资成本外,还需要考虑设备的维护和运行成本,包括能耗、人力和维护费用等。
3. 化工设备设计计算3.1 设计计算的目的化工设备的设计计算是为了确定设备的主要参数和尺寸,包括设备的体积、负荷、结构等。
3.2 设计计算的基本原理设备的设计计算是根据工艺流程和设备的选型结果进行的。
根据工艺流程,可以确定设备的工艺参数,如温度、压力、流量等。
根据设备的选型结果,可以确定设备的尺寸和结构。
3.3 设计计算的步骤设计计算的步骤一般包括以下几个方面:1.确定工艺参数:根据工艺流程确定设备的工艺参数,如温度、压力、流量等。
2.确定设备的尺寸:根据工艺参数和设备选型结果,确定设备的尺寸,如设备的直径、高度等。
3.计算设备的负荷:根据工艺参数和设备的尺寸,计算设备的负荷,包括传热负荷、传质负荷等。
4.设计设备的结构:根据设备的尺寸和负荷,设计设备的结构,包括设备的支撑、连接等。
车间工艺流程的选择和工艺设备的选型

车间工艺流程的选择和工艺设备的选型答案:(1)合理性。
即设备必须满足工艺一般要求,设备与工艺流程、生产规模、工艺操作条件、工艺控制水平相适应,又能充分发挥设备的能力。
(2)先进性。
要求设备的运转可靠性、自控水平、生产能力、转化率、收率、效率要尽可能达到先进水平。
(3)安全性。
要求安全可靠、操作稳定、弹性好、无事故隐患。
对工艺和建筑、地基、厂房等无苛刻要求;工人在操作时,劳动强度小,尽量避免高温高压高空作业,尽量不用有毒有害的设备附件附料。
(4)经济性。
设备投资省,易于加工、维修、更新,没有特殊的维护要求,运行费用减少。
引进先进设备,亦应反复对比报价,考察设备性能,考虑是否易于被国内消化吸收和改进利用,避免盲目性。
题目:工艺设备的选型与计算时工厂设计的重要组成部分,在设备选型时应考虑哪些因素?答案:满足生产工艺要求;机械化和自动化水平;设备性能良好;管理、维修方便、工艺布置合理;节约能源;使用场合及设备来源;技术经济比较。
扩展:工艺流程选择是指在可能采用的多种工艺流程中选择一种最佳工艺流程,以确定从原料投入到成品产出的整个生产过程。
工艺流程选择直接影响到设备选型、厂房布置、产品的产量和质量以及生产经营管理等。
不同的工艺流程对工艺设计方案的优劣起着关键性作用。
为了适应市场需求变化,工艺技术必须具有一定的灵活性,能根据产品多品种、多功能及其升级换代需要作相应的调整或改变。
在选择工艺流程时应注意以下要求:(1)根据产品的种类、特征和所用原料的特点来选择合适的工艺流程。
特别是主要原材料的选择对工艺流程的影响很大,甚至有决定性影响。
(2) 工艺流程选择应力求先进、可靠,能满足生产要求。
要根据科学技术发展的需要与各项生产建设条件的可能,积极采用成熟的新工艺和新技术,尽快提高生产过程的机械化和自动化水平。
(3) 工艺程序要尽可能紧凑集中,以减少加工件在制造过程中的运行距离,缩短生产周期,便于生产组织管理,降低劳动耗费和生产成本。
工艺流程设计与工艺流程的选择
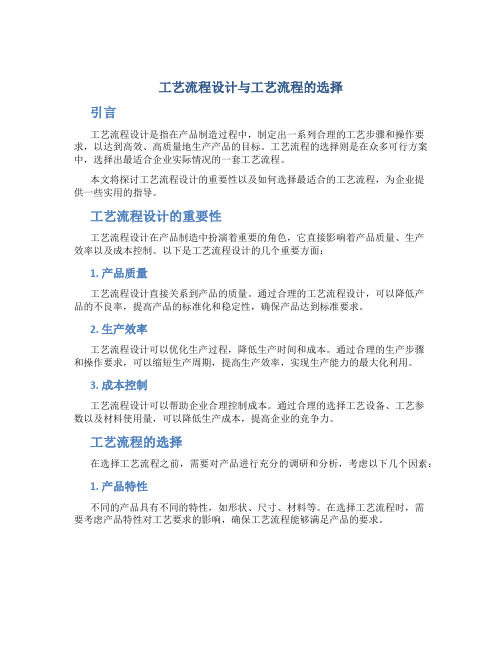
工艺流程设计与工艺流程的选择引言工艺流程设计是指在产品制造过程中,制定出一系列合理的工艺步骤和操作要求,以达到高效、高质量地生产产品的目标。
工艺流程的选择则是在众多可行方案中,选择出最适合企业实际情况的一套工艺流程。
本文将探讨工艺流程设计的重要性以及如何选择最适合的工艺流程,为企业提供一些实用的指导。
工艺流程设计的重要性工艺流程设计在产品制造中扮演着重要的角色,它直接影响着产品质量、生产效率以及成本控制。
以下是工艺流程设计的几个重要方面:1. 产品质量工艺流程设计直接关系到产品的质量。
通过合理的工艺流程设计,可以降低产品的不良率,提高产品的标准化和稳定性,确保产品达到标准要求。
2. 生产效率工艺流程设计可以优化生产过程,降低生产时间和成本。
通过合理的生产步骤和操作要求,可以缩短生产周期,提高生产效率,实现生产能力的最大化利用。
3. 成本控制工艺流程设计可以帮助企业合理控制成本。
通过合理的选择工艺设备、工艺参数以及材料使用量,可以降低生产成本,提高企业的竞争力。
工艺流程的选择在选择工艺流程之前,需要对产品进行充分的调研和分析,考虑以下几个因素:1. 产品特性不同的产品具有不同的特性,如形状、尺寸、材料等。
在选择工艺流程时,需要考虑产品特性对工艺要求的影响,确保工艺流程能够满足产品的要求。
2. 设备和工艺参数选择工艺流程时需要考虑具体的设备和工艺参数。
不同工艺设备有不同的性能和特点,工艺参数的不同也会对产品质量和生产效率产生影响。
因此,要选择适合的设备和调整合理的工艺参数。
3. 生产能力和规模不同企业的生产能力和规模各不相同,要根据企业实际情况选择合适的工艺流程。
对于小规模生产的企业来说,可以采用简单、成本低的工艺流程;而对于大规模生产的企业来说,可以选择自动化、高效率的工艺流程。
4. 成本和效益选择工艺流程时还需要考虑成本和效益的平衡。
工艺流程的选择应该在满足产品要求的基础上,尽可能降低生产成本,并确保能够带来良好的经济效益。
工艺计算及工艺设备选型

工艺计算及工艺设备选型工艺计算是指在工程设计过程中,为了确保所选用的工艺设备能够满足生产需求,对工艺参数进行计算的过程。
工艺设备选型则是指在工程设计过程中,根据工艺计算结果和生产需求,选取合适的工艺设备的过程。
本文将从计算和选型两个方面进行介绍。
一、工艺计算在进行工艺计算之前,需要明确以下几个方面的信息:生产需求、原料属性、产品要求、工艺流程。
1.生产需求:包括生产能力、生产周期等。
根据生产需求,确定最终的产品产量和生产周期。
2.原料属性:包括原料的物化性质、组成、含量等。
通过对原料的分析,确定所需的处理参数。
3.产品要求:包括产品的规格、质量要求等。
根据产品规格和质量要求,确定产品的工艺参数。
4.工艺流程:包括加工步骤、处理方式等。
根据工艺流程,确定所需的操作和工艺参数。
在明确了以上信息后,就可以进行具体的工艺计算。
主要包括以下几个方面:1.流量计算:根据生产需求和工艺流程中的液体或气体的流量要求,计算所需的流量。
2.传热计算:根据工艺流程中的传热要求,计算所需的传热面积、传热系数和热效率。
3.负荷计算:根据生产需求和工艺流程中的能量消耗,计算所需的功率、能耗和负荷。
4.设备尺寸计算:根据工艺流程中的物料流动、混合、分离等的要求,计算所需的设备尺寸。
5.设备强度计算:根据工艺流程中的物料流动、压力、温度等的要求,计算所需的设备强度。
在进行工艺设备选型之前,需要先进行工艺计算,确保所选设备能够满足生产需求。
同时,还需要考虑以下几个方面的因素:设备技术参数、设备品牌、设备成本、设备可维护性等。
1.设备技术参数:根据工艺计算结果,选取技术参数能够满足工艺要求的设备。
例如,选取适合的泵的扬程和流量,选取适合的换热器的传热面积和传热系数。
2.设备品牌:考虑设备的质量和可靠性,选择知名品牌的设备。
这样可以提高设备的可用性和维护性,降低设备故障率和维修成本。
3.设备成本:根据企业的实际情况和经济条件,选择合适的设备成本。
工艺流程中的工艺设备选型

工艺流程中的工艺设备选型工艺流程是指将原始物料通过一系列生产工艺的加工和转化,最终得到所需产品的过程。
而工艺设备则是为了完成这一流程而必要的设备和工具。
在工艺流程中,正确选择适合的工艺设备是确保生产效率和产品质量的关键。
一、工艺流程需求分析在进行工艺设备选型之前,首先需要进行工艺流程的需求分析。
这包括了对原料性质、工艺步骤和技术要求的全面了解。
只有明确了工艺流程的需求,才能更准确地选择适合的工艺设备。
二、工艺设备选型原则1. 与工艺流程需求相匹配:工艺设备的性能参数和技术指标要与工艺流程的需求相匹配,能够满足生产的要求。
2. 能耗合理:工艺设备在使用过程中应该具备较高的能效,能够尽量降低能耗。
3. 操作维护便捷:工艺设备应该操作简便,易于维护和清洁,以提高工作效率。
4. 质量可靠:工艺设备应该具备较高的质量可靠性,以确保生产的连续性和稳定性。
5. 经济可行:在选择工艺设备时,还需要考虑到其价格、性能和使用成本,以确保经济可行性。
三、工艺设备选型步骤1. 调研市场:通过调研市场,了解不同厂家和品牌的工艺设备,包括其性能、价格和售后服务等方面的信息。
2. 比较分析:根据工艺流程需求和选型原则,对不同的工艺设备进行比较分析,筛选出合适的候选设备。
3. 实地考察:对候选设备进行实地考察,了解其生产工艺、设备结构和操作方式等细节,评估其与需求的匹配度。
4. 技术交流:与工艺设备厂家进行技术交流,进一步了解设备的性能和适用范围,并获得厂家提供的技术支持和售后服务保障。
5. 综合评估:综合考虑市场调研、比较分析、实地考察和技术交流的结果,评估各工艺设备的优劣,最终确定最佳选型方案。
四、案例分析以某食品加工厂为例进行工艺设备选型。
该厂生产过程包括原料清洗、破碎、搅拌、杀菌、包装等工序。
根据工艺流程需求和选型原则,应选择能够满足高效清洗、碾磨破碎、均匀搅拌、高温杀菌和自动包装的工艺设备。
通过市场调研,比较分析不同厂家的产品,厂方决定选择一家具有多年行业经验、技术先进、售后服务完善的设备厂家。
选矿厂设计相关计算
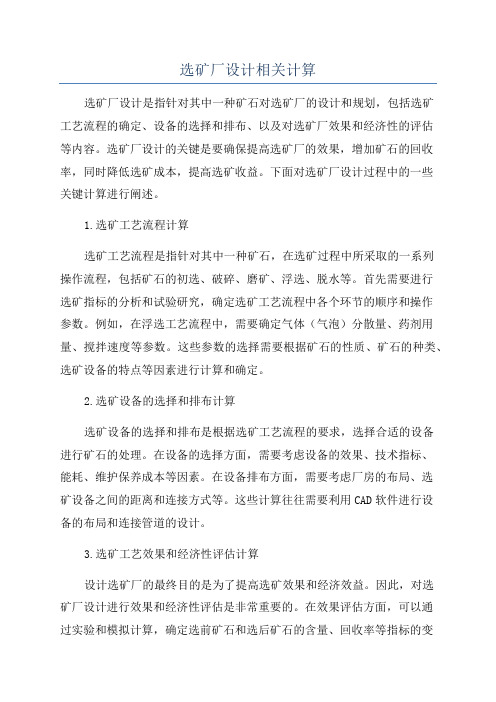
选矿厂设计相关计算选矿厂设计是指针对其中一种矿石对选矿厂的设计和规划,包括选矿工艺流程的确定、设备的选择和排布、以及对选矿厂效果和经济性的评估等内容。
选矿厂设计的关键是要确保提高选矿厂的效果,增加矿石的回收率,同时降低选矿成本,提高选矿收益。
下面对选矿厂设计过程中的一些关键计算进行阐述。
1.选矿工艺流程计算选矿工艺流程是指针对其中一种矿石,在选矿过程中所采取的一系列操作流程,包括矿石的初选、破碎、磨矿、浮选、脱水等。
首先需要进行选矿指标的分析和试验研究,确定选矿工艺流程中各个环节的顺序和操作参数。
例如,在浮选工艺流程中,需要确定气体(气泡)分散量、药剂用量、搅拌速度等参数。
这些参数的选择需要根据矿石的性质、矿石的种类、选矿设备的特点等因素进行计算和确定。
2.选矿设备的选择和排布计算选矿设备的选择和排布是根据选矿工艺流程的要求,选择合适的设备进行矿石的处理。
在设备的选择方面,需要考虑设备的效果、技术指标、能耗、维护保养成本等因素。
在设备排布方面,需要考虑厂房的布局、选矿设备之间的距离和连接方式等。
这些计算往往需要利用CAD软件进行设备的布局和连接管道的设计。
3.选矿工艺效果和经济性评估计算设计选矿厂的最终目的是为了提高选矿效果和经济效益。
因此,对选矿厂设计进行效果和经济性评估是非常重要的。
在效果评估方面,可以通过实验和模拟计算,确定选前矿石和选后矿石的含量、回收率等指标的变化。
在经济性评估方面,需要计算选矿厂的投资成本、运营成本、生产能力、矿石回收率和选矿收益等指标。
通过比较不同设计方案的经济性指标,选择最优的选矿工艺和设备配置方案。
4.选矿工艺参数的调整和优化计算选矿厂设计不是一个一次性的过程,而是一个持续改进和优化的过程。
通过实际运行情况的监测和数据分析,可以对选矿工艺流程中的参数进行调整和优化。
例如,根据浮选过程中的实时测量数据,可以调整气泡分散量和药剂用量,以提高浮选效果。
这些参数的调整和优化需要进行计算和模拟,以确定调整后的参数对选矿效果的影响。
选煤工艺流程及设备选型设计资料

第一章、选煤工艺流程一、选择选煤工艺流程的总要求选择选煤工艺流程应以原料煤性质、用户对产品的要求、最大产率和最高经济效益等因素为依据,正确确定一个比较简单、合理可行并且能满足技术经济要求的工艺流程。
选择选煤工艺流程应遵循以下基本原则:1)根据原料煤性质采用相适应的具有先进技术和生产可靠的加工方法。
2)根据用户的要求能分选去不同质量规格的产品。
3)在满足产品质量要求的前提下获得最大精煤产率,同时力求最高的经济效益和社会效益。
二、选择选煤工艺流程的一般原则选煤工艺流程由各个不同作业和生产环节组成。
选择各项作业和生产环节的一般原则分述如下:1、入选上、下限煤炭入选上、下限由三方面因素相互制约确定,即用户要求、入选原料煤的有关性质和分选设备的适宜处理粒级。
2、选煤方法现在选煤厂使用最多的选煤方法有重介分选和跳汰分选。
重介选较跳汰选分选效率高,但生产和维护成本高。
在洗难选煤时有优势,一般情况下易选或中等可选性煤,应优先考虑跳汰分选法。
3、再选作业和再选物料的破碎1)一般难选煤应考虑设置再选作业,易选煤可不设业。
2)对于炼焦煤或是稀缺煤种,要考虑设置再选作业。
若虽是炼焦煤,但较难选,就要综合考虑是否设置再选作业。
3)另外从经济效益方面考虑。
再选时精煤的回收量,以及产生的次煤泥量对后序作业的影响。
4、浮选作业入选炼焦煤的大中型选煤厂一般均应设置浮选作业处理煤泥,有些动力煤的可浮性较差,对灰分要求也不太严,可不设浮选作业。
5、产品脱水块煤一次脱水一般采用振动脱水筛,二次脱水则采用立式离心机或卧式振动离心机;煤泥或是浮选精煤则常用压滤机进行一次性脱水作业;浮选尾煤一般经过浓缩后,也用压滤机一次性脱水,尾煤数量很少时可考虑用沉淀池回收。
6、浓缩浮选尾矿的预脱水常采用浓缩作业,浓缩设备一般有耙式浓缩机和浓缩池,为了提高浓缩效果,可在浓缩机中安设斜管和在入料中添加絮凝剂。
7、干燥干燥作业一般仅在严寒地区为了防止精煤冻结,在运输距离较远时可设置干燥作业。
工艺流程的选择
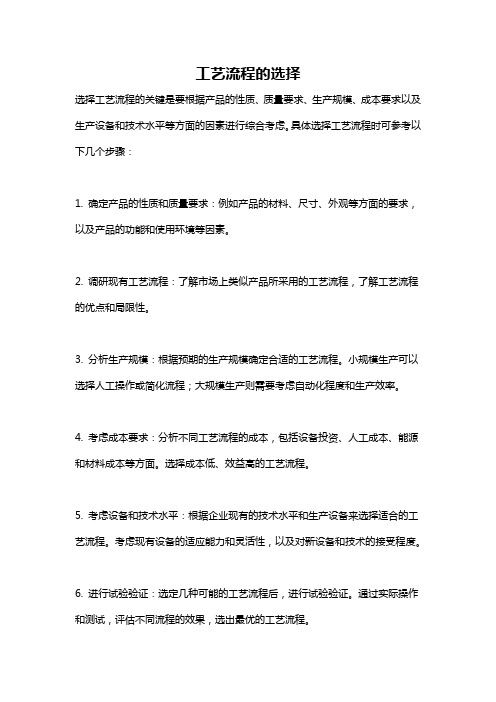
工艺流程的选择
选择工艺流程的关键是要根据产品的性质、质量要求、生产规模、成本要求以及生产设备和技术水平等方面的因素进行综合考虑。
具体选择工艺流程时可参考以下几个步骤:
1. 确定产品的性质和质量要求:例如产品的材料、尺寸、外观等方面的要求,以及产品的功能和使用环境等因素。
2. 调研现有工艺流程:了解市场上类似产品所采用的工艺流程,了解工艺流程的优点和局限性。
3. 分析生产规模:根据预期的生产规模确定合适的工艺流程。
小规模生产可以选择人工操作或简化流程;大规模生产则需要考虑自动化程度和生产效率。
4. 考虑成本要求:分析不同工艺流程的成本,包括设备投资、人工成本、能源和材料成本等方面。
选择成本低、效益高的工艺流程。
5. 考虑设备和技术水平:根据企业现有的技术水平和生产设备来选择适合的工艺流程。
考虑现有设备的适应能力和灵活性,以及对新设备和技术的接受程度。
6. 进行试验验证:选定几种可能的工艺流程后,进行试验验证。
通过实际操作和测试,评估不同流程的效果,选出最优的工艺流程。
7. 持续改进:工艺流程的选择不是一次性的决策,随着技术和市场的变化,还需要持续改进和优化工艺流程,提高产品质量和生产效率。
总之,选择工艺流程需要进行全面的分析和考虑,综合各种因素权衡取舍,以达到最佳的生产效果和经济效益。
- 1、下载文档前请自行甄别文档内容的完整性,平台不提供额外的编辑、内容补充、找答案等附加服务。
- 2、"仅部分预览"的文档,不可在线预览部分如存在完整性等问题,可反馈申请退款(可完整预览的文档不适用该条件!)。
- 3、如文档侵犯您的权益,请联系客服反馈,我们会尽快为您处理(人工客服工作时间:9:00-18:30)。
3.3.1.2 破碎工艺流程的选择
根据上述原矿最大粒度范围(即200~1400mm)和破碎 最终产物粒度范围(即球磨机为10~20mm),常用破 碎流程的总破碎比范围为:
3.3.1.2 破碎工艺流程的选择
破碎比的确定:破碎机的最大给矿粒度和其合适排矿 粒度之比。
3.3.1.2 破碎工艺流程的选择 给矿最大粒度: 破碎机的最大排矿粒度与其排矿口之比值Z的参数以及 排矿中大于排矿口尺寸的过大颗粒含有率S有关
车间名称
年作业率 (%)
年工作时间 (d)
日工作时间 (班)
班工作时间 (h)
破碎及洗矿 57~73.5
330
3
5~6.5
自磨及选别 80~85
290~320
3
8
球磨及选别 85~90.4
320~330
3
8
精矿脱水 68~90.4
250~330
3
8
3.2.2处理量的确定 选矿厂的处理量是指各车间年、日和小时处理量。 破碎车间和主厂房(指磨矿、选别车间)指年、日和小 时处理原矿量。 精矿脱水车间指年、日和小时处理精矿量。 主厂房年或日处理原矿量,称为选矿厂规模。 有色金属矿选矿厂。常用日处理原矿量表示选矿厂规模。 黑色金属矿选矿厂,常用年处理原矿量表示选矿厂规模。 重选厂的规模是指日处理合格原矿量(即选出部分废石后 的原矿)。
E、手选的必要性 但对某些矿石,仍然非常必要
3.3.2 破碎工艺流程的计算
3.3.2.1 计算的内容、目的及原理 计算的内容:
计算各破碎产物和筛分产物的重量Q(t/h)和产率 γ(%)。如果破碎流程中有手选、洗矿或重、磁选作 业时,则还应计算手选、洗矿或重、磁选作业等产 物的品位和回收率。
3 工艺流程的选择与计算
设计的目的 ⑴ 设计合理的工艺流程; ⑵ 选择合适的工艺设备,进行合理的设备配置; ⑶ 设计合适的厂房结构,确保生产的正常进行; ⑷ 配置必要的劳动定员,以满足正常生产的需要
3.1 工艺流程选择的原则 (1)根据试验研究部门提供或推荐的工艺流程 (2)根据建厂地区技术经济条件及建厂规模; (3)考虑建厂地区气候条件和水文地质条件; (4)考虑工艺技术水平及发展趋势; (5)进行多方案技术经济比较。
c.小时处理量 由于破碎车间和磨矿车间的日工作小时数不同,因此, 两者的小时处理量总是不同的
3.3 破碎工艺流程的选择和计算
3.3.1 破碎工艺流程的选择 3.3.1.1 破碎工艺流程类型和常用破碎工艺流程
破碎工艺流程类型
3.3.1.1 破碎工艺流程类型和常用破碎工艺流程 常用破碎工艺流程
3.3.1.2 破碎工艺流程的选择
所以,破碎前的预先筛分总是有利的。另外矿石的 含泥含水量高也应该加预先筛分。
设置预先筛分的缺点是:增加厂房高度,增加基建 投资和设备配置较复杂。
因此,在下列情况下,可以不设预先筛分: 难碎性矿石,细粒含量少; 破碎机有富余的生产能力; 受地形限制,难于设置预先筛分; 大型选矿厂的粗碎机给矿采用车厢直接倒入,即所 谓挤满给矿等。
3.2 选矿厂工作制度、设备作业率和处理量的确定
3.2.1选矿厂工作制度、设备作业率
选矿厂工作制度是指选矿厂各车间的工作制度,是根据各 车间设备年作业率确定的。 设备作业率是指各车间设备全年实际运转小时数与全年日 历小时数(即365d×24h=8760h)之比。
3.2.1选矿厂工作制度、设备作业率 主要设备作业率和作业时间
破碎工艺流程的选择,主要解决5个问题;即确定 破碎段数;洗矿必要性;手选必要性;预先筛分必 要性;检查筛分必要性等。
A、 确定破碎段数
(1)破碎段数的确定。破碎段数取决于选矿厂的原矿最大 粒度与破碎最终产物粒度,即取决总破碎比(S)。 总破碎比等于原矿最大粒度(D)除以破碎最终产物粒度(d)。 即S=D/d
根据破碎机样本,并通过上表推算,得到各种类型破 碎机的破碎比。
3.3.1.2 破碎工艺流程的选择
破碎段数的结论是: 常用破碎流程应是二段或三段。 特殊情况可考虑四段破碎流程。
3.3.1.2 破碎工艺流程的选择 B、预先筛分的必要性
3.3.1.2 破碎工艺流程的选择
3.3.1.2 破碎工艺流程的选择
3.2.2处理量的确定 a.年处理量 年处理量以选矿厂规模为计算依据: (1)无手选或洗矿等预选作业时,破碎车间年处理量与磨 矿车间年处理量相同。
(2)有手选或洗矿等作业时,破碎车间年处理量大于磨矿 车间年处理量。破碎车间年处理量为:
3.2.2处理量的确定 b.日处理量
破碎车间和磨矿车间的日处理虽可能相同,也可 能不同,取决于其车间的年处理量和年工作天数。
3.3.1.2 破碎工艺流程的选择
最终产物粒度 破碎最终产物粒度视选矿厂规模、磨矿细度和选别的 工艺要求而定。由于磨矿作业电耗占选矿厂总电耗的 50%~60%,而破碎作业仅占10%~15%。因此,设 计时要尽可能减小破碎最终产物粒度。
3.3.1.2 破碎工艺流程的选择
适宜的给矿粒度范围: 球磨机为10~20mm; 棒磨机开路时为15~20mm,含泥含水比较多时,可增 到20~25mm; 砾磨机需要部分破碎最终产物作磨矿介质时为 40~100mm; 自磨机为200~350mm。跳汰机给矿粒度小于20mm; 重介质选矿为25~3mm。
3.3.1.2 破碎工艺流程的选择
原矿最大粒度
选 (mm)
地下开采
采矿方法
原矿最大粒度 (mm)
大型
3~6 1200~1500 深孔采矿 500~600
中型
0.5~2 600~1000 深孔采矿 400~500
小型
0.4~1
450~800 浅孔采矿 200~350
3.3.1.2 破碎工艺流程的选择
C、检查筛分的必要性 过大颗粒,最大相对粒度,相对粒度
3.3.1.2 破碎工艺流程的选择
结论: 只在最后一段破碎设置检查筛分,以控制最终破 碎产物粒度,前面各段破碎不设置检查筛分。
3.3.1.2 破碎工艺流程的选择
D、洗矿的必要性 选矿厂处理含泥量较多的氧化矿,或含泥多、水分高的矿 石时,必须设置洗矿作业。一般认为原矿含水大于5%、 含泥(-0.074mm)超过5%~8%,就应考虑洗矿;有些需要 预选(如手选、光电选、重介质选等)的矿石,预选前需设 置洗矿。所以,洗矿要视具体情况而定。