数控机床加工实例
数控车床零件的工艺分析及编程典型实例

数控车床零件的工艺分析及编程典型实例更新日期:来源:数控工作室根据下图所示的待车削零件,材料为45号钢,其中Ф85圆柱面不加工。
在数控车床上需要进行的工序为:切削Ф80mm 和Ф62mm 外圆;R70mm 弧面、锥面、退刀槽、螺纹及倒角。
要求分析工艺过程与工艺路线,编写加工程序。
图1 车削零件图1.零件加工工艺分析(1)设定工件坐标系按基准重合原则,将工件坐标系的原点设定在零件右端面与回转轴线的交点上,如图中Op点,并通过G50指令设定换刀点相对工件坐标系原点Op的坐标位置(200,100)(2)选择刀具根据零件图的加工要求,需要加工零件的端面、圆柱面、圆锥面、圆弧面、倒角以及切割螺纹退刀槽和螺纹,共需用三把刀具。
1号刀,外圆左偏刀,刀具型号为:CL-MTGNR-2020/R/1608 ISO30。
安装在1号刀位上。
3号刀,螺纹车刀,刀具型号为:TL-LHTR-2020/R/60/1.5 ISO30。
安装在3号刀位上。
5号刀,割槽刀,刀具型号为:ER-SGTFR-2012/R/3.0-0 IS030。
安装在5号刀位上。
(3)加工方案使用1号外圆左偏刀,先粗加工后精加工零件的端面和零件各段的外表面,粗加工时留0.5mm的精车余量;使用5号割槽刀切割螺纹退刀槽;然后使用3号螺纹车刀加工螺纹。
(4)确定切削用量切削深度:粗加工设定切削深度为3mm,精加工为0.5mm。
主轴转速:根据45号钢的切削性能,加工端面和各段外表面时设定切削速度为90m/min;车螺纹时设定主轴转速为250r/min。
进给速度:粗加工时设定进给速度为200mm/min,精加工时设定进给速度为50mm/min。
车削螺纹时设定进给速度为1.5mm/r。
2.编程与操作(1)编制程序(2)程序输入数控系统将程序在数控车床MDI方式下直接输入数控系统,或通过计算机通信接口将程序输入数控机床的数控系统。
然后在CRT 屏幕上模拟切削加工,检验程序的正确性。
数控铣床编程30例带图

实例一毛坯为70㎜×70㎜×18㎜板材,六面已粗加工过,要求数控铣出如图3-23所示的槽,工件材料为45钢。
1.根据图样要求、毛坯及前道工序加工情况,确定工艺方案及加工路线1)以已加工过的底面为定位基准,用通用台虎钳夹紧工件前后两侧面,台虎钳固定于铣床工作台上。
2)工步顺序①铣刀先走两个圆轨迹,再用左刀具半径补偿加工50㎜×50㎜四角倒圆的正方形。
②每次切深为2㎜,分二次加工完。
2.选择机床设备根据零件图样要求,选用经济型数控铣床即可达到要求。
故选用XKN7125型数控立式铣床。
3.选择刀具现采用φ10㎜的平底立铣刀,定义为T01,并把该刀具的直径输入刀具参数表中。
4.确定切削用量切削用量的具体数值应根据该机床性能、相关的手册并结合实际经验确定,详见加工程序。
5.确定工件坐标系和对刀点在XOY平面内确定以工件中心为工件原点,Z方向以工件表面为工件原点,建立工件坐标系,如图2-23所示。
采用手动对刀方法(操作与前面介绍的数控铣床对刀方法相同)把点O 作为对刀点。
6.编写程序按该机床规定的指令代码和程序段格式,把加工零件的全部工艺过程编写成程序清单。
考虑到加工图示的槽,深为4㎜,每次切深为2㎜,分二次加工完,则为编程方便,同时减少指令条数,可采用子程序。
该工件的加工程序如下(该程序用于XKN7125铣床):N0010 G00 Z2 S800 T1 M03N0020 X15 Y0 M08N0030 G20 N01 P1.-2 ;调一次子程序,槽深为2㎜N0040 G20 N01 P1.-4 ;再调一次子程序,槽深为4㎜N0050 G01 Z2 M09N0060 G00 X0 Y0 Z150N0070 M02 ;主程序结束N0010 G22 N01 ;子程序开始N0020 G01 ZP1 F80N0030 G03 X15 Y0 I-15 J0N0040 G01 X20N0050 G03 X20 YO I-20 J0N0060 G41 G01 X25 Y15 ;左刀补铣四角倒圆的正方形N0070 G03 X15 Y25 I-10 J0N0080 G01 X-15N0090 G03 X-25 Y15 I0 J-10N0100 G01 Y-15N0110 G03 X-15 Y-25 I10 J0N0120 G01 X15N0130 G03 X25 Y-15 I0 J10N0140 G01 Y0N0150 G40 G01 X15 Y0 ;左刀补取消N0160 G24 ;主程序结束实例二毛坯为120㎜×60㎜×10㎜板材,5㎜深的外轮廓已粗加工过,周边留2㎜余量,要求加工出如图2-24所示的外轮廓及φ20㎜的孔。
数控车床编程实例

如图2-16所示工件,毛坯为φ45㎜×120㎜棒材,材料为45钢,数控车削端面、外圆。
1.根据零件图样要求、毛坯情况,确定工艺方案及加工路线1)对短轴类零件,轴心线为工艺基准,用三爪自定心卡盘夹持φ45外圆,使工件伸出卡盘80㎜,一次装夹完成粗精加工。
2)工步顺序①粗车端面及φ40㎜外圆,留1㎜精车余量。
②精车φ40㎜外圆到尺寸。
2.选择机床设备根据零件图样要求,选用经济型数控车床即可达到要求。
故选用CK0630型数控卧式车床。
3.选择刀具根据加工要求,选用两把刀具,T01为90°粗车刀,T03为90°精车刀。
同时把两把刀在自动换刀刀架上安装好,且都对好刀,把它们的刀偏值输入相应的刀具参数中。
4.确定切削用量切削用量的具体数值应根据该机床性能、相关的手册并结合实际经验确定,详见加工程序。
5.确定工件坐标系、对刀点和换刀点确定以工件右端面与轴心线的交点O为工件原点,建立XOZ工件坐标系,如前页图2-16所示。
采用手动试切对刀方法(操作与前面介绍的数控车床对刀方法基本相同)把点O作为对刀点。
换刀点设置在工件坐标系下X55、Z20处。
6.编写程序(以CK0630车床为例)按该机床规定的指令代码和程序段格式,把加工零件的全部工艺过程编写成程序清单。
该工件的加工程序如下:N0010 G59 X0 Z100 ;设置工件原点N0020 G90N0030 G92 X55 Z20 ;设置换刀点N0040 M03 S600N0050 M06 T01 ;取1号90°偏刀,粗车N0060 G00 X46 Z0N0070 G01 X0 Z0N0080 G00 X0 Z1N0090 G00 X41 Z1N0100 G01 X41 Z-64 F80 ;粗车φ40㎜外圆,留1㎜精车余量N0110 G28N0120 G29 ;回换刀点N0130 M06 T03 ;取3号90°偏刀,精车N0140 G00 X40 Z1N0150 M03 S1000N0160 G01 X40 Z-64 F40 ;精车φ40㎜外圆到尺寸N0170 G00 X55 Z20N0180 M05N0190 M02实例二如图2-17所示变速手柄轴,毛坯为φ25㎜×100㎜棒材,材料为45钢,完成数控车削。
《数控机床操作与编程》实例

《数控机床操作与编程》实例数控机床是一种具有高精度、高效率和高稳定性的机床,广泛应用于各种机械加工行业。
通过编程控制机床的运动轨迹和速度,可以实现复杂的零件加工。
下面将介绍几个数控机床操作与编程的实例。
实例一:二维轮廓加工在数控机床上进行二维轮廓加工时,通常需要先进行编程,然后再将程序加载到机床上进行加工。
1.编程以绘制一个圆形的实例来进行说明,假设需要加工直径为100mm的圆形。
首先需要确定圆心坐标和半径。
假设圆心坐标为(X0,Y0),半径为R。
编程过程如下:N10G90G54G0X0Y0;G90表示绝对编程方式,G54指定工件坐标系,G0快速定位N20 G01 Z0.5 F100 ;G01线性插补指令,Z0.5表示下刀深度为0.5mm,F100表示给进速度N30G02X0Y0R;G02圆弧插补指令,X0Y0表示结束点的坐标,R表示半径,顺时针方向N40G00Z10;G00快速提刀N50M30;程序结束2.机床操作将编写好的程序保存到U盘或者其它存储设备上,插入到数控机床的USB接口或者其它相关接口上。
然后按照机床操作手册的要求,加载程序到机床上。
实例二:三维曲面加工在数控机床上进行三维曲面加工时,通常需要先进行编程,然后再将程序加载到机床上进行加工。
1.编程假设需要加工一个球形零件,球心坐标为(X0,Y0,Z0),半径为R。
编程过程如下:N10G90G54G0X0Y0Z0;G90表示绝对编程方式,G54指定工件坐标系,G0快速定位N20 G01 Z0.5 F100 ;G01线性插补指令,Z0.5表示下刀深度为0.5mm,F100表示给进速度N30G03X0Y0Z0R;G03圆弧插补指令,X0Y0Z0表示终点坐标,R表示半径,顺时针方向N40G00Z10;G00快速提刀N50M30;程序结束2.机床操作将编写好的程序保存到U盘或者其它存储设备上,插入到数控机床的USB接口或者其它相关接口上。
然后按照机床操作手册的要求,加载程序到机床上。
数控车床的孔加工编程方法举例
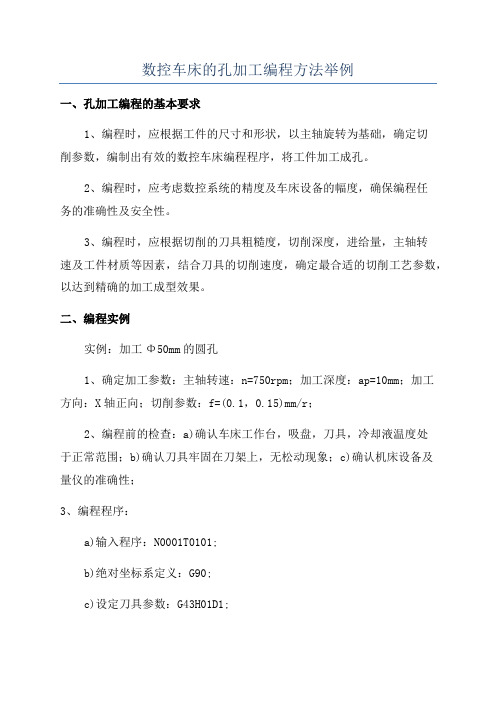
数控车床的孔加工编程方法举例
一、孔加工编程的基本要求
1、编程时,应根据工件的尺寸和形状,以主轴旋转为基础,确定切
削参数,编制出有效的数控车床编程程序,将工件加工成孔。
2、编程时,应考虑数控系统的精度及车床设备的幅度,确保编程任
务的准确性及安全性。
3、编程时,应根据切削的刀具粗糙度,切削深度,进给量,主轴转
速及工件材质等因素,结合刀具的切削速度,确定最合适的切削工艺参数,以达到精确的加工成型效果。
二、编程实例
实例:加工Φ50mm的圆孔
1、确定加工参数:主轴转速:n=750rpm;加工深度:ap=10mm;加工
方向:X轴正向;切削参数:f=(0.1,0.15)mm/r;
2、编程前的检查:a)确认车床工作台,吸盘,刀具,冷却液温度处
于正常范围;b)确认刀具牢固在刀架上,无松动现象;c)确认机床设备及
量仪的准确性;
3、编程程序:
a)输入程序:N0001T0101;
b)绝对坐标系定义:G90;
c)设定刀具参数:G43H01D1;
d)设定切削参数:G94S800;
e)设定绝对编码:G90;
f)设定主轴转速:S7500M03;
g)设定初始坐标:G0X50Z10;
h)开始加工:G02X50Z0R50F0.15;
i)停止主轴:M05;
j)空转:G04P2.0;
k)结束程序:M30;。
数控机床技术在汽车零部件加工中的应用实例
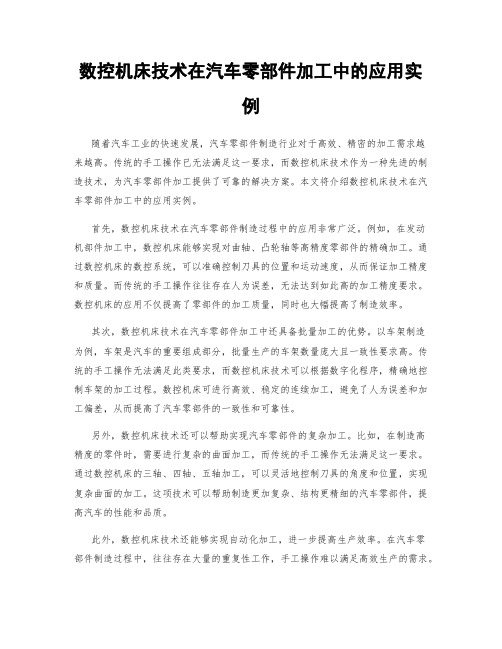
数控机床技术在汽车零部件加工中的应用实例随着汽车工业的快速发展,汽车零部件制造行业对于高效、精密的加工需求越来越高。
传统的手工操作已无法满足这一要求,而数控机床技术作为一种先进的制造技术,为汽车零部件加工提供了可靠的解决方案。
本文将介绍数控机床技术在汽车零部件加工中的应用实例。
首先,数控机床技术在汽车零部件制造过程中的应用非常广泛。
例如,在发动机部件加工中,数控机床能够实现对曲轴、凸轮轴等高精度零部件的精确加工。
通过数控机床的数控系统,可以准确控制刀具的位置和运动速度,从而保证加工精度和质量。
而传统的手工操作往往存在人为误差,无法达到如此高的加工精度要求。
数控机床的应用不仅提高了零部件的加工质量,同时也大幅提高了制造效率。
其次,数控机床技术在汽车零部件加工中还具备批量加工的优势。
以车架制造为例,车架是汽车的重要组成部分,批量生产的车架数量庞大且一致性要求高。
传统的手工操作无法满足此类要求,而数控机床技术可以根据数字化程序,精确地控制车架的加工过程。
数控机床可进行高效、稳定的连续加工,避免了人为误差和加工偏差,从而提高了汽车零部件的一致性和可靠性。
另外,数控机床技术还可以帮助实现汽车零部件的复杂加工。
比如,在制造高精度的零件时,需要进行复杂的曲面加工,而传统的手工操作无法满足这一要求。
通过数控机床的三轴、四轴、五轴加工,可以灵活地控制刀具的角度和位置,实现复杂曲面的加工。
这项技术可以帮助制造更加复杂、结构更精细的汽车零部件,提高汽车的性能和品质。
此外,数控机床技术还能够实现自动化加工,进一步提高生产效率。
在汽车零部件制造过程中,往往存在大量的重复性工作,手工操作难以满足高效生产的需求。
而数控机床通过数字化程序,实现了自动化加工过程,能够高效地完成重复性工作,提高生产效率,同时减少人力成本。
总体而言,数控机床技术在汽车零部件加工中的应用实例广泛且多样。
它不仅能够提高加工精度和质量,同时也能够批量生产零部件,并实现复杂和精细的加工。
机械工程中的数控加工技术应用实例
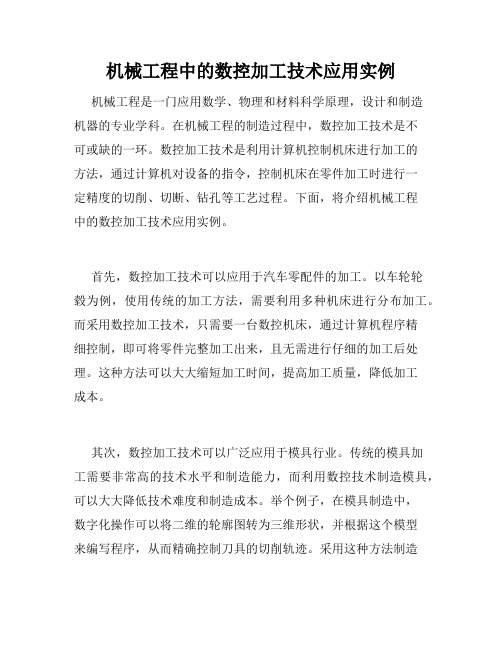
机械工程中的数控加工技术应用实例机械工程是一门应用数学、物理和材料科学原理,设计和制造机器的专业学科。
在机械工程的制造过程中,数控加工技术是不可或缺的一环。
数控加工技术是利用计算机控制机床进行加工的方法,通过计算机对设备的指令,控制机床在零件加工时进行一定精度的切削、切断、钻孔等工艺过程。
下面,将介绍机械工程中的数控加工技术应用实例。
首先,数控加工技术可以应用于汽车零配件的加工。
以车轮轮毂为例,使用传统的加工方法,需要利用多种机床进行分布加工。
而采用数控加工技术,只需要一台数控机床,通过计算机程序精细控制,即可将零件完整加工出来,且无需进行仔细的加工后处理。
这种方法可以大大缩短加工时间,提高加工质量,降低加工成本。
其次,数控加工技术可以广泛应用于模具行业。
传统的模具加工需要非常高的技术水平和制造能力,而利用数控技术制造模具,可以大大降低技术难度和制造成本。
举个例子,在模具制造中,数字化操作可以将二维的轮廓图转为三维形状,并根据这个模型来编写程序,从而精确控制刀具的切削轨迹。
采用这种方法制造的模具精度更加准确,且制造周期更短,满足高效、精密、短周期的要求。
再次,数控机床的应用使得加工精度大大提高。
在传统的车加工过程中,由于操作人员的操作差异以及切削刃具的特性,制造出的零件精度十分难以控制。
而在数控加工技术中,计算机通过精确的数学公式控制机床移动,可以对精度要求较高的零部件进行加工,制造性、可靠性、精度等方面都得到极高的保证。
最后,数控加工技术还能够利用智能化的技术为制造提供更多可能。
如工件控制系统可以自动进行质量检测和纠偏,进一步提高了制造精度和效率。
同时,这种智能化技术可以提供工件切割路径根据材料和刀具的特性的优化,减少加工时间并同时大幅度减少浪费。
因此,这种技术将在未来继续影响着机械制造行业。
综上所述,数控加工技术的应用是机械工程中必不可少的一部分,已经在生产制造中广泛应用。
相信随着科技的不断发展,数字化技术将在未来机械制造过程中发挥出更加巨大的作用。
数控机床车削加工例

数控机床车削加工例数控机床在现代制造业中扮演着重要的角色,具有高效、精度高、自动化程度高等优点。
数控机床具有多种功能,车削加工是其常见的一种加工方式。
本文将介绍数控机床车削加工的例子。
一、数控车床车削加工例在数控车床车削加工中,常用的零件有轴承、法兰、轮毂、齿轮、活塞等。
下面以轴承零件为例,介绍数控车床车削加工的步骤。
1、加工轴承外圆首先需要将工件夹在三爪卡盘上,然后将加工刀具放置于车床主轴上,将工件对准刀具,并确定加工中心。
接下来,根据加工轴承外圆的要求,设置车床的加工参数,包括进给速度、回程速度、切削深度、切削速度等。
最后启动数控机床,进行加工。
2、加工轴承内孔加工轴承内孔时,需要将工件夹在弹性夹头上,并将夹头插入主轴孔中,确定夹紧力度。
然后,在车床主轴上放置加工刀具,对准工件,并设置加工参数。
最后启动数控机床进行加工。
二、数控铣床加工例数控铣床也是常见的加工设备之一,常用于加工平面、倒角、凸轮等零件。
下面以平面零件为例,介绍数控铣床加工的步骤。
1、夹紧工件首先需要将工件夹在工件台上,并固定好位置。
确保工件夹紧力度适中,不会出现松动的情况。
2、设置刀具并定位根据加工要求,选择合适的刀具进行加工。
在铣床主轴上安装刀具后,需要对准工件进行定位,确定加工位置和加工范围。
3、设置加工参数根据加工要求,设置加工参数。
包括进给速度、回程速度、切削深度、切削速度等。
加工参数设置的好坏将会影响加工效果和精度。
4、启动铣床进行加工最后,启动数控铣床进行加工。
操作过程中需要注意观察机床运行状态和工件加工情况,及时调整参数,确保加工精度和效率。
总之,数控机床车削加工是现代制造业的基础,具有广泛的应用前景和市场需求。
同时,随着科技的发展和加工技术的提高,数控机床也在不断地升级和完善,让加工更加高效、精度更高、自动化程度更高,为人类创造更多的价值。
- 1、下载文档前请自行甄别文档内容的完整性,平台不提供额外的编辑、内容补充、找答案等附加服务。
- 2、"仅部分预览"的文档,不可在线预览部分如存在完整性等问题,可反馈申请退款(可完整预览的文档不适用该条件!)。
- 3、如文档侵犯您的权益,请联系客服反馈,我们会尽快为您处理(人工客服工作时间:9:00-18:30)。
配合件的数控加工摘要:随着数控加工技术的发展, 大量高精度多坐标数控机床的出现,机械加工已越来越倾向使用数控加工。
数控加工主要有以下两个优点:精度高,可以加工任何复杂的自由曲面且精度很高,可以满足结构复杂、高精度的需要。
操作简单,传统加工方法对工艺及操作人员的技术要求很高,稍有不慎就有可能导致零件报废。
现代数控加工技术只需机床操作人员在加工前输入相应的数控程序,机床就会严格按照数控程序进行加工。
可以预测,在未来几年内机械加工部分将继续以数控加工为主。
本文以配合件加工为例,从数控加工工艺分析,设备的选择,配合精度,刀具、夹具的选择,切削用量的选择,都经过了慎重考虑。
配合件种类繁多,范围太广,所以以车削,铣削为主,以轴承套、箱体为例,分析零件气概经过数控加工,确定合理工艺方案,保证工件的精度和工艺设计要求,以达到配合要求,最终完成的零件的加工。
关键词:工艺分析;加工方法;数控加工零件是机械中的最小单位,零件的配合组成了机构,机构之间的配合组成了机械,一部机器要能正常工作,发挥应有的作用,那么零件与零件之间的配合是保证的关键。
如今,随着机电一体化技术的迅速发展,数控机床已经日走趋普及。
加之对配合的零件之间的要求,零件表面的粗糙度,位置度等要求不断提高,普通机床很难达到,那么就需要在数控机床完成。
下面以数控车削加工的典型零件-盘套类零件,铣削为主的箱体类零件为例讨论配合件的加工。
(一)数控车削的典型零件-盘套类配合件的加工盘套类零件在机器设备中用得非常普遍,多与同属回转体零件的轴类零件配合,由于其功能不同,盘套类零件结构和尺寸有着很大的差别,但其结构仍有共同点,零件的主要表面为同轴度要求较高的内外圆表面,零件壁的厚度较薄且易变形,盘套类零件的结构一般由孔,外圆,端面,沟槽及内螺纹和外螺纹,内锥面和内型面组成。
常见的有轴承套,衬套,齿轮,带轮,轴承端盖等。
盘套类零件表面精度要求除尺寸外、形状精度外,内孔一般要作为配合和装配的基准,孔的直径尺寸等级一般为IT7,精密轴套可以取IT6,孔的形状精度应控制在孔径公差内,,一些精密套筒控制在孔径的公差的二分之一到三分之一,对于长度较长的轴套零件,除了圆度要求以外,还应注内孔面的圆柱度,端面对内孔轴线的圆跳动度和垂直度,以及两端面的的平行度等要求,为了保证零件的功用和提高其耐磨性,孔的表面粗糙度值Ra1.6-0.16um,甚至更高。
以数控车加工的典型零件盘套类零件,轴承套为例,讨论配合件的数控加工。
轴承套数控车削加工工艺(单件小批量生产),所用机床为CJK6240一、零件图工艺分析1)编程时取基本尺寸。
但由于要求配合,则有的配合尺寸需取中间值。
2)先确定基准,先加工左、右端面。
保证零件的长度尺寸。
3)内孔尺寸较小,镗1﹕20锥孔、φ32孔及15°斜面时需掉头装夹。
4)右端有螺纹,所以放在最后加工,由于高速车削挤压引起螺纹牙尖膨胀变形,因此外螺纹的外圆应车到最小极限尺寸,螺纹加工前,先将加工表面加工到实际直径尺寸,M45×1.5的螺纹,加工前的外圆直径为:D外≈D-(0.1~0.2165)P =45-0.2*1.5=44.7一般数控车床推荐车螺纹时的最高转速为:n≤1200P-k (k是保险系数,一般为80)加工螺纹时,长度应包括切入切出的空行程量,切入量一般取2-5mm,切出量一般取0.5-1mm。
也可无退刀曹轴承套的零件图二、确定装夹方案1)内孔加工时以外圆定位,用三爪自动定心卡盘夹紧。
2)加工外轮廓时,需要设一圆锥心轴装置,用三爪卡盘夹持心轴左端,心轴右端留有中心孔并用尾座顶尖顶紧。
外轮廓车削装夹方案三、加工顺序走刀路线依照基孔先行的原则,先加工内孔各表面,需要调头加工,由于右边有螺纹,所以放在最后加工。
再加工外轮廓表面。
由于该零件为单件小批量生产,外轮廓表面车削走刀路线可沿零件轮廓顺序进行。
加工前,先手动加工通孔。
四、走刀路线由于该零件为单件小批量生产,外轮廓表面车削走刀路线可沿零件轮廓顺序进行。
采用装夹,刀具集中原则,划分工序。
五.刀具选择序号刀具号刀具规格名称数量加工表面刀尖半径1 TO1 45°硬质合金端面车刀 1 车端面0.42 TO2 镗刀 1 镗内孔表面0.43 T03 93°外圆车刀 1 车各外圆0.44 T04 60°外螺纹车刀 1 车M45螺纹5 尾座¢28mm钻头 1 钻底孔六. 切削用量的选择七.加工程序O0001;G99 T0101; 选 45°硬质合金端面车刀M03S600; 主轴正转G00X85 Z2;GO1ZO F0.1; 先加工左面,车端面X-1;GOOX100 Z150;T0101; 换镗刀G00X82 Z2;G71U2R0.5; 利用复合指令车外圆各面G71P1Q2U0.5W0.2F0.3 S800;N1 GOO G42X46;GO1 Z2 F0.1;X49.97 Z-2;Z-30;X58;G02 X68Z-35 R5;GO1X74X78Z-37;N2 G40 Z-60;G70P1Q2S1000;GOOX100Z100;T0202; 换内孔镗刀车内孔GOOX25Z2;G71U2R0.5;G71P1Q2U-1W0.5F0.2 S600;N1GOOG41X35.1;GO1Z0 F0.05;X32Z-10;Z-29;G02X30Z-30 R1;N2G40X28;G70P1Q2;MO5; 主轴停M30 程序停止准备掉头加工右面(方法同左边加工相同,程序略)(二) 铣削为主的箱体类配合件的加工。
箱体类零件一般指是具有一个以上的孔系,内部有一定型腔或空腔,在长宽高方向有一定比例的零件,这类零件在机械,汽车,飞机制造业用得多,如汽车的发动机缸体,变速箱体,机床主轴箱,齿轮泵壳体等。
一.数控机床的选用方面。
箱体类零件一般是其它零件配合的载体。
都需要进行多工位孔系、轮廓及平面加工,公差要求较高,特别是形位公差要求较为严格,通常要经过铣、钻、扩、镗、铰、锪、攻丝等工序。
需要刀具多,在普通机床上加工难度大,工装套数多,费用高,加工周期长,需要多次装夹,找正,手工测量次数多,加工时还要频繁的换刀,工艺难制定,更重要的是精度难以保证。
这类零件在加工中心上加工,一次装夹可完成普通机床的60%--95%工序内容,零件各项精度一致性好,质量稳定,同时节约费用,缩短加工周期。
加工中心与数控铣床铣削加工是型腔模具加工的重要手段。
数控铣床是一种加工功能很强的数控机床,数控铣床是一种加工功能很强的数控机床,在数控加工中占据了重要地位。
现在数控铣床已全面向多轴化发展。
目前迅速发展的加工中已全面向多轴化发展。
目前在数控铣床和数控镗床的基础上产生了加工中心和柔性制造单元也是在数控铣床和数控镗床心和柔性制造单元。
铣削加工是型腔模具加工的重要手段。
并且现今产生了高速铣削,而高速铣削具有工件温升低、切削力小、加工平稳、加工质量好、加工效率高及可加工硬材料等,且高速铣削加工不仅可提高效率,而且也可提高表面质量,从而减轻了精加工负担,缩短了工期。
诸多优点。
因而在模具加工中日益受到重视。
加工箱体类零件的加工中心,当加工工位较多是时,需要工件台多次旋转角度才能完成的零件,一般选用卧式加工中心,当工位较少,且跨度不大时,可选用立式加工中心。
二.箱体零件加工方法。
(一)当既有孔,又有面时,应先铣面,后加工孔。
(二)所有孔系都应先完成所有孔的粗加工,再精加工。
(三)一般情况下,直径大于30的孔都应先铸出毛坯孔,在普通机床上完成毛坯孔的粗加工,给加工中心留4-6mm的加工余量,再上加工中心进行孔和面的加工,通常分为“粗镗—半精镗—孔端倒角—精镗”四个工步完成。
(四)直径小于30的孔,可以不铸出毛坯孔,但孔和孔的端面全部都得在加工中心上完成,可分为“锪平端面—打中心孔—钻—扩—孔端倒角—精镗”工步完成。
有同轴度要求的小孔,须采用“多锪平端面—(打中心孔)—钻—半精镗—孔端倒角—精镗”工步完成。
(五)在孔系加工中,先加工大孔,再加工小孔,特别是在大小孔相距很近的时候,更要采用这种方法。
(六)对于跨度较大的箱体的同轴孔加工,尽量采用调头加工的方法,以缩短刀辅具的径比,增加刀具刚性,提高加工质量。
(七)螺纹的加工方法,一般情况下,M6—M20的螺纹也可以在加工中心上完成攻螺纹。
M6以下和M20以上的螺纹可在加工中心上完成底孔,攻螺纹通过其它手段加工,因为加工中心的自动加工方式在攻小螺纹时,不能随机的控制加工状态,小丝锥容易折断,从面产生废品,由于刀具,辅具等因素的影响,在加工中心上攻M20以上的螺纹有一定的难度。
但可以通过特定程序,用镗刀片完成螺纹的切削。
(八)分析零件的形状及原材料的热处理状态,是否会在加工过程中变形,哪些部位最容易变形。
因为数控铣削最忌讳工件加工时变形,这这种变形不但无法保证加工质量,而且经常造成加工不能正常进行,这时应该考虑一些必要的工艺措施预防。
如对钢件进行调质处理,对铸件进行退火处理,对不能用热处理方法解决的问题,也可考虑粗加工,精加工及对称去余量的方法,此外,还要分析加工后的变形问题,采取工艺措施解决。
三.加工工序的划分在数控机床上加工箱体等配合件,工序比较集中,一般只需要一次装夹即可完成所有加工,通常可按照从简单到复杂的原则,先加工平面、沟槽,再加工内腔、外形,最后加工曲面,先加工精度要求低的,再加工精度要求较高的。
为了提高机床的使用寿命,保证数控机床的精度,降低零件的加工成本,通常把零件的粗加工,特别是零件的定位面在普通机床上加工。
四.铣削中刀具夹具的选择选择刀具的重要依据是被加工零件的几何形状和材料。
加工曲面类零件时,一般用球头刀,粗加工用两刀刃铣,半精加工和精加工用四刃铣刀。
刀刃娄还与刀具直径有关,铣较大平面时,一般采用刀片镶嵌式租车形面铣刀。
铣小平面或台阶时,一般采用通用铣刀,铣键槽时,一般用两刃键槽铣刀。
孔加工时,可采用钻头、镗刀、铰刀等孔加工刀具。
箱体的装夹和夹具的选择,在数控机床上加工中,既要保证加工质量,又要减少辅助时间,提高加工效率。
因此要选用能准确和迅速定位并夹紧的工件的装夹方法和夹具。
零件的定位基准应尽量与设计基准及测量重合,以减少定位误差为了不影响进给和切削加工在装夹工件时一定要将加工部位敞开,选择夹具时应尽量做到在一次装夹中将要求加工的面都加工出来。
五. 箱体零件的加工编程一般情况下,零件如尺寸少,相对确定,可以人工编程,如几何形状复杂的零件。
或有复杂曲面的零件,或几何形状并不复杂,但程序量很大的零件,这种加工编程计算相当复杂,应采用自动编程。
所谓自动编程,是指编程过程用计算机辅助的方法来自动完成。
这类自动编程系统数控编程的一般过程包括:零件几何造型CAD ,刀具定义,刀具相对于零件表面运动方式定义,切削加工参数确定,走刀轨迹、刀位文件的生成,加工过程的动态图形仿真,后置处理产生G代码程。