常压塔温度控制系统讲解
仪表控制方案及主要仪表性能

8 仪表控制方案及主要仪表性能8.1 仪表控制方案8.1.1 原油流控(FRC101、FRC102、FRC103、FRC104、FRC105、FRC105A)控制原油进装置流量,同时将原油均匀地分为六路与各热源换热,保证原油量的平稳和各支路换后温度基本相等。
8.1.2 电脱盐混合阀压降控制(PdRC201、PdRc202、PdRC203、PdRC204)分别控制一级和二级电脱盐油水混合强度,保证各罐的脱盐效果。
8.1.3 电脱盐压力控制(PRC101)与脱后原油流量控制(FRC111、FRC112、FRC113、FRC114)实行压力——流量串级控制,以压力控制为主回路,流量控制为付回路,达到原油四路分支流量均匀、换热稳定和脱盐压力平稳的目的。
8.1.4 初馏塔顶温控(TRC302)根据产品质量的要求,通过与初馏塔顶回流量控制回路(FRC302)的串级来达到控制初顶温度的目的。
8.1.5 常压塔顶温控(TRC330)根据常顶和各侧线产品的质量要求,通过控制常顶回流量的大小来达到控制常压塔顶温度的目的。
8.1.6 闪蒸塔底液位控制(LRC304)与常压炉六路进料流控(FRC601-FRC606)实行液位——流量串级控制,以闪底液控为主回路,常压炉六路进料流控为付回路,达到闪蒸塔底液位平稳、常压炉各支路流量稳定、均匀的目的。
8.1.7 常压炉出口温度控制(TRC609A)通过与常压炉燃料气压力控制(PRC616)实行温度——压力串级控制,以常压炉出口温控为主回路,常压炉燃料气压控为付回路,使常压炉出口温度维持在指标范围以内。
8.1.8 常压塔底液位控制(LRC305)通过与减压炉八路进料流量控制(FRC651-FRC658)实行液位——流量串级控制,以常压塔底液控为主回路,减压炉八路进料流控为付回路,达到常压塔底液位平稳,减压炉进料各支路流量稳定、均匀的目的。
8.1.9 减压炉出口温度控制(TRC660)通过与减压炉燃料气压力控制(PRC667)实行温度——压力串级控制,以减压炉出口温控为主回路,减压炉燃料气压控为付回路,使减压炉出口温度稳定在指标范围以内。
常压塔温度控制系统

⑷ 注意工艺操作的合理性、经济性。
简单控制系统由四个基本环节做成,被控对象、测量变送装置、控制器、 执行器四个部分的传递函数分别为Go(S),Gm(S),Gc(S),Gv(S)。简单控制 系统是最基本的控制系统。约占工业控制系统的80%以上。只有在简单 控制系统不能满足生产更高要求的情况下,才用复杂控制系统。 单回路控制系统是最基本的控制系统,由于其结构简单,投资少,易于 调整,操作维护比较方便,又能满足此系统的控制要求。所以本套系统 可采用简单的单回路控制。系统的流程图如下:
在串级控制系统中,由于引入了一个副回路,不仅能及早克 服进入副回路的扰动,而且又能改善过程特性。副调节器具有 “粗调”的作用,主调节器具有“细调”的作用,从而使其控 制品质得到进一步提高。当以塔顶采出液为主要产品时,往往 以精馏段的温度为衡量质量的间接指标,这时可选精馏段某点 温度作为被控参数(间接反应塔顶采出液的纯度),以回流量 QL作为被控变量做成单回路控制系统,亦可以组成串级控制系 统。
(2)当干扰首先进入精馏段时,例如进料产生的干扰首先引起精 馏段和塔顶参数的变化,故用精馏段温度控制比较及时,动态响应 比较迅速。
(3)串级控制系统的流量回路岁回流罐液位与压力、精馏塔内压 力等于干扰对回流量的影响有较强的抑制,可实现被控参数的高精 度控制。
一线温度控制系统设计
对于炼油厂常压塔温度控制系统中一线温度的检测,可以用简单 控制系统实现,生产过程是按质量指标进行控制,按理应该以直接 反应产品质量的变量作为被控参数,但有时由于缺乏检测直接反应 产品质量参数的有效手段,无所岁产品质量作为直接检测;所以对 炼油厂精馏塔出口产品的检测就转化为对一线温度的检测,蒸馏塔 的一线出口温度是被控参数,从而间接检测产品质量。温度变送器 TT将采集到的出口温度的信号送入温度控制器TC,控制器通过控制调 节阀的开度,进而调节了进入精馏塔的冷凝水的量,从而控制了温 度,使之保持在被控参数上。
甲醇三塔精馏存在问题分析

煤化工与甲醇化 工 设 计 通 讯Coal Cemical MethanolChemical Engineering Design Communications·6·第46卷第12期2020年12月1 概况刘化集团公司年产甲醇100kt ,精馏采用三塔精馏、萃取、加压精馏,汽提塔环保塔。
预塔为全填料塔,在预精馏塔中除去甲醇溶解的气体及低沸点杂质,主要是二甲醚。
在常压塔中除去水及高沸点杂质,从加压塔、常压塔采出合格的精甲醇产品。
2 三塔流程的特点精甲醇的精馏过程是利用粗甲醇中各组分的挥发度不同,进行精馏操作,甲醇易溶于水,加入萃取水与甲醇相溶,根据水与甲醇密度、沸点不同,在精馏塔内实现分离,利用多次部分汽化和部分冷凝的方法,经填料、塔盘上传至换热,以达到完全分离各组分的目的。
节能型三塔流程与双塔流程相比具有如下特点。
2.1 节能甲醇精馏系统,预塔与加压塔底部虹吸式再沸器,利用0.6MPa 蒸汽提供热源,壳程甲醇混合液受热,甲醇沸点64.5℃,从甲醇混合液溢出,变成甲醇蒸汽。
一般流程都考虑废热的回收利用,蒸汽冷凝水用来加热进料的粗甲醇。
一般粗醇温度20℃左右。
加热后进入预塔可以达到70℃左右,利于精馏操作。
多效利用热源蒸汽的潜热,将原双塔流程的主精馏塔分为两个塔,第一塔加压操作塔(约0.6MPa ),第二塔为常压操作塔,由于增加加压操作顶部气相甲醇的液化温度约为124℃,远高于常压塔塔釜液体(主要为水)的沸点,气相出口可作为常压塔再沸器热源。
这一过程称为双效法,较双塔流程(单效法)可节约热能,一般在正常操作条件下,比较理想的能耗为每精制1t 精甲醇消耗 折蒸汽约1t 左右。
双效法三塔流程节能效果明显2.2 降低精甲醇中乙醇含量精馏塔底部靠蒸汽提供,蒸汽加入量大,塔温上升,重组分上移,水和乙醇共沸物上移,影响精甲醇的产品质量,蒸汽加入量过大,上升汽速度增快,有可能造成液泛。
因此精馏塔温升应小于1℃/h 。
常压塔控制设计

第1章常压塔工程实例1.1 工艺生产过程简介常减压装置是用来加工原油的第一个装置,是根据原油的沸点不同,用蒸馏的方法从原油中分离出各种石油组份,即汽油、煤油、柴油及各种组份的润滑油料和二次加工原料。
在石油炼制过程中,常、减压塔是具有多侧线产品的塔。
常减压装置一般包括三个部分,即初馏部分、常压部分和减压部分。
常压塔是一个复合塔,非标准精馏塔,只有精馏段,没有提馏段。
一般只能是塔顶出产品或塔底出产品,不能两者兼得。
而常压塔把原油切割成汽油、煤油、轻柴油、重柴油和重油,塔底没有再沸器,而通入水蒸汽,没有提馏段。
这样侧线产品中必然有相当数量的轻组分。
解决的办法是增加汽提塔。
过热水蒸汽420℃。
常压塔的负荷往往决定了炼油厂的生产能力,所以负荷是很大的。
另一方面,它是一个多馏份的切割塔,所以产品纯度没有一般精馏塔要求高,各侧线产品纯度允许在一定的馏份范围内变化,这是多馏份蒸馏塔的特点。
常减压工艺流程可以简化为:根据原油中各组份的沸点(挥发度)不同,将混合物切割成不同沸点的“馏份”。
即是利用加热炉将原油进行加热,生成汽、液两相,在常压塔中,使汽、液两相充分的热交换和质量交换,在提供塔顶回流的条件下对原油进行精馏,从塔顶分馏出沸点较低的产品,汽油。
从塔底分出沸点较高的产品,重油,塔中间抽出,得到侧线产品,即煤油、柴油、蜡油等。
常压蒸馏后剩下的重油组份分子量较大,在高温下易分解(500 ℃左右),为了将常压重油中的各种沸点的润滑油组份分离出来,采用在减压塔(真空蒸馏方法)塔顶使用蒸汽喷射泵、间冷器抽真空的方法,使加热后的常压重油在负压条件下进行分馏,从而使高沸点的组份在相应的温度下依次馏出做为润滑油料。
这是因为石油沸点与压力的关系是:压力低,油品的沸点就越低。
另外,还采用水蒸汽汽提法来提高拔出率和质量。
初馏塔塔顶可以出初馏点~130℃的馏份作为重整原料。
也可不作为产品,作为常压塔的侧线回流打入常压塔。
初馏塔底馏份用泵送入常压加热炉,被加热至规定温度,再进入塔内。
常压加热炉系统培训讲义课件.
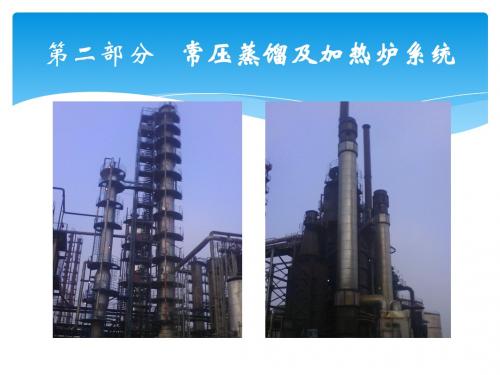
2、塔器日常维护
(1)加强塔顶塔壁和各短接的测厚监测,特别是不走介质的短接。 (2)柴油段的高温环烷酸腐蚀,这些部位主要是常二抽出到过汽化 油抽出,平时要加强测厚和巡检。 (3)进料段的气液两相冲刷腐蚀,检修时要加强这些部位的检查。 (4)塔底以及提馏段塔盘的环烷酸硫腐蚀,检修时要加强这些部位 的检查。 (5)平时要注意平台栏杆是否锈蚀开裂,保温是否有大面积脱落。
3、塔器安全附件
(1)安全阀: (2)压力表:
4、塔盘的作用、原理、分类
作用:塔盘的作用是提供传质传热场所,主要分离指标为分离效率。 原理:塔盘上有浮阀,阀片可以在导向内自由升降。
5、空气冷却器
A、空冷器投用操作 B、空冷器甩出操作
6、离心泵 (1)离心泵的原理
第二部分 常压蒸馏及加热炉系统
一、常压蒸馏工艺流程介绍
1、初馏系统工艺流程 原油经电脱盐系统脱水脱盐合格后,经过二级换热 系统升温至220-240℃,然后进入初馏塔进料段,气 液两相的进料进入初馏塔之后,气相上升液相下降。
2、常压系统工艺流程 升温到370℃左右的初底油又变为气液两相,经过常 压炉转油线,进入常压塔进料段,气相上升液相下 降。
二、 环 保 1、概述 环保即环境保护,是指减少和消除化工生产中的废水、废气和废渣(简称“三 废”)对周围环境的污染和对生态平衡及人体健康的影响,防治污染,改善环 境,化害为利等工作。 2、日常环保工作 通过工艺的合理改造,达到减少三废排放的目的。加强管理工作,使废水、废 渣排入指定区域进行处理。对装臵有可能产生废气、有毒有害气体的露天部位 进行遮盖。对容易产生有毒有害气体的部位加设有毒有害气体检测仪进行实时 监测。 3、雨季清污分流工作 雨季当装臵面临较大降水时,要立即启动清污分流应急处理预案。 4、检修环保工作 检修过程中产生的各种固体废弃物,要分类放臵;在征得运行部同意后放到指 定地点,严禁随意堆放污染环境。 5、事故环保工作 装臵内存储有大量有毒有害物质和各类油品,当发生事故时可能导致这些物质 外泄。需要做的是将油品管路泄漏处最近上下游阀门关闭,用细沙或者拦油索 等设臵隔离带,防止油污蔓延或进入明沟,将其引入下水井或者回收;对于有 毒有害物质,在保证人员安全的前提下及时堵漏,对外泄的部分进行喷水稀释 并通知下风向车间人员注意防范。
常减压蒸馏装置自动控制解决方案(精)
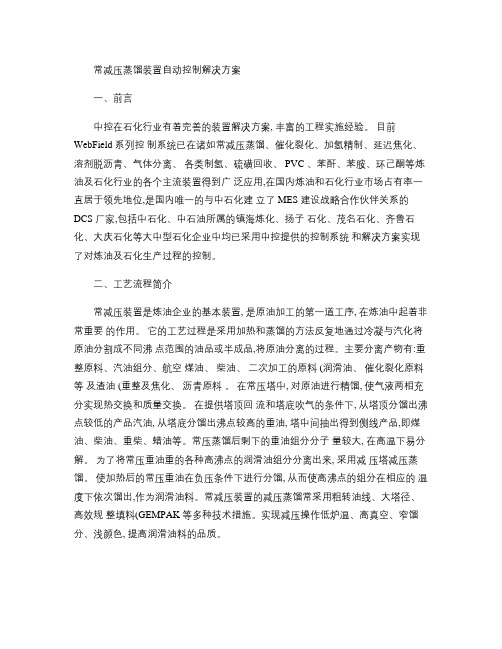
常减压蒸馏装置自动控制解决方案一、前言中控在石化行业有着完善的装置解决方案, 丰富的工程实施经验。
目前WebField 系列控制系统已在诸如常减压蒸馏、催化裂化、加氢精制、延迟焦化、溶剂脱沥青、气体分离、各类制氢、硫磺回收、 PVC 、苯酐、苯胺、环己酮等炼油及石化行业的各个主流装置得到广泛应用,在国内炼油和石化行业市场占有率一直居于领先地位,是国内唯一的与中石化建立了 MES 建设战略合作伙伴关系的DCS 厂家,包括中石化、中石油所属的镇海炼化、扬子石化、茂名石化、齐鲁石化、大庆石化等大中型石化企业中均已采用中控提供的控制系统和解决方案实现了对炼油及石化生产过程的控制。
二、工艺流程简介常减压装置是炼油企业的基本装置, 是原油加工的第一道工序, 在炼油中起着非常重要的作用。
它的工艺过程是采用加热和蒸馏的方法反复地通过冷凝与汽化将原油分割成不同沸点范围的油品或半成品,将原油分离的过程。
主要分离产物有:重整原料、汽油组分、航空煤油、柴油、二次加工的原料 (润滑油、催化裂化原料等及渣油 (重整及焦化、沥青原料。
在常压塔中, 对原油进行精馏, 使气液两相充分实现热交换和质量交换。
在提供塔顶回流和塔底吹气的条件下, 从塔顶分馏出沸点较低的产品汽油, 从塔底分馏出沸点较高的重油, 塔中间抽出得到侧线产品,即煤油、柴油、重柴、蜡油等。
常压蒸馏后剩下的重油组分分子量较大, 在高温下易分解。
为了将常压重油重的各种高沸点的润滑油组分分离出来, 采用减压塔减压蒸馏。
使加热后的常压重油在负压条件下进行分馏, 从而使高沸点的组分在相应的温度下依次馏出,作为润滑油料。
常减压装置的减压蒸馏常采用粗转油线、大塔径、高效规整填料(GEMPAK 等多种技术措施。
实现减压操作低炉温、高真空、窄馏分、浅颜色, 提高润滑油料的品质。
原油图 1 常减压装置工艺流程图三、控制方案3.1 装置关键控制常减压装置通常以常规单回路控制为主,辅以串级、均匀和切换等少量复杂控制。
常压塔工作温度
常压塔工作温度1. 常压塔的概述常压塔是一种常用的化工设备,用于分离和精馏液体混合物,常用于炼油、化工、石化等行业。
其工作原理是利用不同组分的沸点差异,通过加热和冷却,将液体混合物分解成不同纯度的组分。
2. 常压塔的工作温度及重要性常压塔的工作温度是其正常运行所必需的关键参数之一。
工作温度的设定对塔内物料的分离效果、能耗、设备寿命等方面产生重要影响。
正常工作温度的选择应综合考虑以下几个因素:2.1 物料性质常压塔处理的液体混合物通常由多种组分组成,不同组分的沸点不同。
选择适当的工作温度可以实现对目标组分的有效分离。
然而,如果温度过高,可能会引起组分之间的相互反应,影响分离效果。
2.2 泵功耗在常压塔中,需要通过加热、冷却等设备对液体混合物进行处理。
不同工作温度下,设备的能耗会有所不同。
一般来说,较高的工作温度会增加设备的能耗,增加运营成本。
2.3 设备寿命常压塔是一种长期稳定运行的设备,其内部受到不同温度下物料的冲击和腐蚀。
选择合适的工作温度可以降低对设备的腐蚀程度,延长设备的寿命。
3. 常压塔的工作温度控制常压塔的工作温度通常通过控制加热和冷却的方式进行调节。
常见的温度控制方法有以下几种:3.1 加热方式常压塔的加热方式包括直接加热和间接加热两种形式。
直接加热就是将燃烧产生的热能直接传递给塔体,通过燃烧炉、高温烟气等方式进行加热。
间接加热则通过热交换器将热能传递给塔体。
3.2 冷却方式常压塔的冷却方式一般采用水冷、空冷、冷凝等方式。
水冷是指通过循环水或直接注入水冷却塔体。
空冷则利用外界的自然空气实现冷却。
冷凝是将热蒸汽通过冷凝器冷却为液体。
3.3 温度控制系统常压塔通常配备温度控制系统,以实现对工作温度的精确控制。
控制系统通常包括温度传感器、控制器、执行机构等。
通过对温度传感器的监测,控制器可以调节加热或冷却设备的工作状态,以控制塔内的工作温度。
4. 常压塔工作温度的优化为了提高常压塔的效率和降低运营成本,需要对工作温度进行优化。
常压塔顶系统腐蚀与控制
2020年第20卷第11期腐蚀与防护技术常压塔顶系统腐蚀与控制李春树(中国石化天津分公司,天津300132)摘要:常压塔顶系统是炼油生产装置中腐蚀问题易发多发部位。
分析认为初凝区酸腐蚀、铵(胺)盐垢下腐蚀、多项流冲蚀、应力腐蚀开裂是塔顶系统腐蚀的主要腐蚀机理;设备或管线减薄、穿孔或焊缝开裂泄漏是塔顶系统腐蚀的主要表现形式。
提出从装置规划设计、设备制造安装、原料控制和工艺操作、腐蚀监检测和运行维护多个环节入手,采取综合措施,进行腐蚀控制。
关键词:常压塔;低温部位;初凝区;铵盐;腐蚀DOI:10.3969/j.issn.1672-7932.2020.11.0121常压塔顶系统腐蚀概述1.1常压塔顶系统简介蒸馏装置常顶系统常见的工艺流程为单回流罐流程,塔顶油气经油气线从常压塔顶出来,流经换热器、空气冷却器、水冷器,进塔顶回流罐,少部分液体产品回流,分液体产品、气体产品、污水从系统流出。
塔顶油气温度在130X左右,从换热器出来为80X左右,从空冷器出来在60X左右,经水冷器冷却后在40X至50X左右。
塔顶回流温度也在40X至50X左右。
不同的装置在规划上,对产品收率和能量回收要求不同,设备配置和工艺参数条件有所不同。
为控制塔顶系统腐蚀,在塔顶油气进常顶换热器之前的管道上,向塔顶油气注入中和剂、缓蚀剂、水。
也有的装置塔顶采用双回流罐流程,经换热器后进第一台回流罐,也叫热回流罐,部分回流,其余物料经空冷水冷后,进第二台回流罐,也叫冷回流罐,分馏出产品和污水,流出系统。
双回流罐流程的塔顶塔顶注水在第一台回流罐之后,希望回流温度在水露点之上,在105X左右。
塔顶循环系统一般在140X左右抽出,110X左右返回塔内。
1.2常压塔顶系统腐蚀机理常压塔顶系统设备管道选材以碳钢为主,管道选材通常为碳钢,设备选材较为复杂,但常压塔顶一般为碳钢复合铁素体不锈钢、双相不锈钢、超级奥氏体不锈钢、蒙乃尔合金。
换热器管束选用双相钢、钛材,空冷器选材一般为碳钢或双相钢。
原油蒸馏装置常压塔控制系统
原油蒸馏装置常压塔控制系统设计摘要DCS在我国炼油厂应用已有15年历史,有20多家炼油企业安装使用了不同型号的DCS,对常减压装置、催化裂化装置、催化重整装置、加氢精制、油品调合等实施过程控制和生产管理。
其中有十几套DCS用于原油蒸馏,多数是用于常减压装置的单回路控制和前馈、串级、选择、比值等复杂回路控制。
有几家炼油厂开发并实施了先进控制策略。
下面介绍DCS用原油蒸馏生产过程的主要控制回路和先进控制软件的开发和应用情况。
辽河原油属于低硫中间基原油,含环烷酸多根据原油的性质、特点和市场的需求主要生产重整汽油、航空煤油、轻柴油、重柴油、混合蜡油、渣油等。
装置由原油电脱盐、常减压蒸馏、渣油减粘裂化、航煤精制部分组成。
根据加工含环烷酸原油的特点,结合加工含环烷酸原油的经验,优化了设备选型及选材,采用了目前最先进技术既初馏塔、常压塔塔盘为ADV高效塔盘。
减压塔采用规整填料,处理物料能力大,汽、液接触均匀,传质效果较好。
以实现装置长周期运行。
高温部位设备和管线全部采用不锈钢材质,以达到防腐的目的。
初顶、常顶用空冷代替水冷,节约了用水量,也减少了三废处理量。
常压塔设顶循环回流和二个中段回流,以使塔内汽、液相负荷分布均匀,提高塔的处理能力,减小塔顶冷凝器的负荷。
为了降低减压塔内真空高度,提高沸点,减压塔采用二级抽真空器。
即蒸汽喷射泵和水环抽真空泵。
在采用新工艺新设备的同时优化了工艺流程,为了节能常压系统采用4台空冷器,为增加处理量常压炉四路进料四路出。
为使相当数量的中间馏分得到合理利用,因为它们是很多的二次加工原料,又能从中生产国民经济所需的各种润滑油、蜡、沥青的原料。
因此本设计采用三段汽化蒸馏,即预汽化—常压蒸馏—减压蒸馏。
关键词:原油;常减压蒸馏塔;控制系统。
Crude oil distillation unitatmospheric tower control system designAbstractDCS in our refinery application for 15 years history, has more than 20 refining enterprise installed the different types of DCS, often relief devices, catalytic cracking, catalytic reforming device, hydrotreating, oil products to attune, the implementation of process control and production management. There are more than ten sets of DCS for crude oil distillation, majority is used for often of pressure-relief device single loop control and feedforward, cascade, selection, such complex loop control. The ratio Several refineries in the development and implementation of the advanced control strategy. Here with crude oil distillation process of DCS the main control circuit and advanced control software development and application situation.Liaohe oil belong to low sulphur crude oil, including among the naphthenic acid more according to the nature of the crude oil, characteristics and the demand of the market main production reforming gasoline, kerosene, diesel oil, heavy diesel, light mixed wax, directness, etc. Device by oil electricity desalination, often vacuum distillation, reduce glue residue cracking, and HangMei refined parts. According to processing including the naphthenic acid crude oil, combined with the naphthenic acid crude oil processing experience, optimize the selection of equipment and material, and adopted the most advanced technology, atmospheric distillation tower early both tata dish for ADV efficient tray. The reduced pressure tower neat padding materials handled, ability, air, liquid contact even, mass transfer effect is good. In order to realize the long period operation device. High temperature parts equipment and piping all adopt the stainless steel material, in order to achieve anticorrosive purpose. First, often be of top air cooling water, saving water instead of, also reduced the capacity of "three wastes". Atmospheric tower set top cycle and two middle backflow backflow, in order to make the tower in steam, liquid loading distribution uniformity, improve the processing power, reduce the tower top condenser load. In order to reduce the reduced pressure the tower in height, improve the boiling point vacuum, vacuum pumping, the reduced pressure tower is secondary. Namely steam injection pump and water ring smoke vacuum pump.In the new process of new equipment and optimize the process, in order to energy savingatmospheric system USES four units of air tanks to increase capacity, atmospheric pressure furnace four ways of incoming four the road.To make a number of the middle of the fractions get reasonable use, because they are a lot of secondary processing raw material, and national economy from production all kinds of wax, lubricating oil, asphalt material. So this design USES the three sections of vaporization, namely the vaporization distillation-atmospheric distillation-vacuum distillation.Keywords: crude oil; often vacuum distillation tower; Control system.目录摘要 (Ⅰ)英文摘要 (Ⅲ)第一章绪论 (1)第二章工艺流程设计 (3)2.1原料油性质及产品性质 (3)2.1.1原料油性质、来源 (3)2.1.2产品性质 (3)2.2工艺流程 (3)2.2.1原油换热系统 (4)2.2.2常压系统 (4)2.2.3减压系统 (4)第三章常减压装置主要控制回路 (6)3.1加压炉 (6)3.2常压塔、减压塔中段回流热负荷控制 (7)3.3提交加热炉效率的控制 (7)3.3.1炉膛压力控制 (7)3.3.2烟道气氧含量控制 (7)3.4加热炉出口温度控制 (7)3.5常压塔解耦控制 (8)第四章原油蒸馏先进控制 (8)4.1 DCS的控制结构层 (8)4.2原油蒸馏的先进控制策略 (9)4.2.1常压塔多变量控制 (9)4.2.2 LQG自校正控制 (9)4.2.3中段回流计算 (10)4.2.4自动提降量模型 (11)第五章炼油厂常压塔温度控制系统设计的方案 (12)5.1过程控制系统方案设计的基本要求 (12)5.2常压塔温度控制系统的总体设计 (13)第六章炼油厂常压塔温度控制系统设计内容 (14)6.1精馏塔控制系统的组成与结构 (14)6.2主要内容与设计步骤 (15)6.2.1 被控参数的选择 (16)6.2.2温度变送器的选择 (17)6.2.3温度调节器的选择 (18)6.2.4执行器的选择 (19)6.3一线温度控制系统设计 (20)6.4一线温度控制的主要内容与仪器选择 (21)第七章 DCS编程 (22)第八章结论 (36)第九章参考文献 (37)第十章谢辞 (38)第一章绪论石油是一种主要由碳氢化合物组成的复杂混合物。
常压塔一线温度与塔顶温度串级自动控制系统小结
常压塔一线温度与塔顶温度串级自动控制系统小结下载提示:该文档是本店铺精心编制而成的,希望大家下载后,能够帮助大家解决实际问题。
文档下载后可定制修改,请根据实际需要进行调整和使用,谢谢!本店铺为大家提供各种类型的实用资料,如教育随笔、日记赏析、句子摘抄、古诗大全、经典美文、话题作文、工作总结、词语解析、文案摘录、其他资料等等,想了解不同资料格式和写法,敬请关注!Download tips: This document is carefully compiled by this editor. I hope that after you download it, it can help you solve practical problems. The document can be customized and modified after downloading, please adjust and use it according to actual needs, thank you! In addition, this shop provides you with various types of practical materials, such as educational essays, diary appreciation, sentence excerpts, ancient poems, classic articles, topic composition, work summary, word parsing, copy excerpts, other materials and so on, want to know different data formats and writing methods, please pay attention!常压塔一线温度与塔顶温度串级自动控制系统小结1. 引言在化工生产中,常压塔是至关重要的设备之一,其操作稳定性直接影响生产效率与产品质量。
- 1、下载文档前请自行甄别文档内容的完整性,平台不提供额外的编辑、内容补充、找答案等附加服务。
- 2、"仅部分预览"的文档,不可在线预览部分如存在完整性等问题,可反馈申请退款(可完整预览的文档不适用该条件!)。
- 3、如文档侵犯您的权益,请联系客服反馈,我们会尽快为您处理(人工客服工作时间:9:00-18:30)。
串级温度控制系统是常见的精馏段温度控制方案,如下图:
精馏段温度控制系统
整个系统包括两个控制回路,主回路和副回路。副回 路由副变量检测变送、副调节器、调节阀和副过程构成; 主回路由主变量检测变送、主调节器、副调节器、调节阀、 副过程和主过程构成。串级控制系统采用两套检测变送器 和两个调节器,前一个调节器的输出作为后一个调节器的 设定,后一个调节器的输出送往调节阀。前一个调节器称 为主调节器,它所检测和控制的变量称主变量(主被控参 数),即工艺控制指标;后一个调节器称为副调节器,它 所检测和控制的变量称副变量(副被控参数),是为了稳 定主变量而引入的辅助变量。
一线温度控制系统
一线温度控制系统框图
系统的框图如下:
精馏段控制的系统框 图
图中Gc1(S)为主控制器;Gc2(S)为副控制器;Gv(S)为控制器; Go2(S)为回流量QL;Go1(S)精馏塔的塔板温度。
精馏段温度控制系统有如下特点
(1)用精馏段的温度作为间接质量指标,能较迅速、直接的反映 提馏段产品质量。在以塔顶采出物为主要产品,对塔顶产品成分的 纯度要求高于对塔低产品成分的要求时,往往采用精馏段温度控制 系统方案。 (2)当干扰首先进入精馏段时,例如进料产生的干扰首先引起精 馏段和塔顶参数的变化,故用精馏段温度控制比较及时,动态响应 比较迅速。 (3)串级控制系统的流量回路岁回流罐液位与压力、精馏塔内压 力等于干扰对回流量的影响有较强的抑制,可实现被控参数的高精 度控制。
常压塔温度控制系统设计
• 被控参数的选择:塔顶馏出物(或塔底残液)的浓度应选作被控参数,
因为它最直接地反映了产品的质量。目前对成分的测量尚有一定困难, 于是一般采用塔顶(或塔底)温度代替浓度作为被控参数。
• 温度变送器和调节器的选择:目前在工业领域被广泛采用的是
DDZ-Ⅲ型仪表(采用了线性集成电路,长期运行中稳定可靠,扩大了调 节器的功能,易于组成各种变型调节器)。
• 执行器的选择:从生产工艺的安全考虑,一旦控制系统发生故障,
要保证人身的安全,炼油厂的精馏塔温度控制 • 系统,不可以让精馏塔处于太低的温度,所以 • 执行器应选择气关阀。
气关阀
精馏塔控制系统的组成与结构
炼油厂常压塔是一种精馏塔,进入常压塔的油品经过精馏被 分离成塔顶汽油,塔底重油,一线航空没有,二线轻柴油,三 线重柴油,等三个侧线产品。工艺要求塔顶出口温度应保持在 70±0.5℃,一线温度应保持在60±0.5℃。 在串级控制系统中,由于引入了一个副回路,不仅能及早克 服进入副回路的扰动,而且又能改善过程特性。副调节器具有 “粗调”的作用,主调节器具有“细调”的作用,从而使其控 制品质得到进一步提高。当以塔顶采出液为主要产品时,往往 以精馏段的温度为衡量质量的间接指标,这时可选精馏段某点 温度作为被控参数(间接反应塔顶采出液的纯度),以回流量 QL作为被控变量做成单回路控制系统,亦可以组成串级控制系 统。
一线温度控制系统设计
对于炼油厂常压塔温度控制系统中一线温度的检测,可以用简单 控制系统实现,生产过程是按质量指标进行控制,按理应该以直接 反应产品质量的变量作为被控参数,但有时由于缺乏检测直接反应 产品质量参数的有效手段,无所岁产品质量作为直接检测;所以对 炼油厂精馏塔出口产品的检测就转化为对一线温度的检测,蒸馏塔 的一线出口温度是被控参数,从而间接检测产品质量。温度变送器 TT将采集到的出口温度的信号送入温度控制器TC,控制器通过控制调 节阀的开度,进而调节了进入精馏塔的冷凝水的量,从而控制了温 度,使之保持在被控参数上。
常压塔温度控制系统
第五组成员:杨文元 贺俊杰 孙伟东 张 炼油厂的原油蒸馏装置多采用的典型三段汽化常减压蒸馏流程:
常压塔的工艺流程图
炼油厂常压塔总体流程图
常压蒸馏预处理后的原油经加热后送 入常压蒸馏装置的初馏塔,蒸馏出大部 分轻汽油。初馏塔底原油经加热至 360~370°C,进入常压蒸馏塔(塔 板数36~48),该塔的塔顶产物为汽 油馏分(又称石脑油),与初馏塔顶 的轻汽油一起可作为催化重整原料, 或作为石油化工原料,或作为汽油调 合组分。常压塔侧线出料进入汽提塔, 用水蒸气或再沸器加热,蒸发出轻组分, 以控制轻组分含量。一线为即航空煤 油,二线为轻柴油馏分,三线为重柴 油,塔底产物即常压渣油(即重油)。 在石化工业中,许多原料中间产品或 粗成品往往是右若干成分组成的混合 物,需要经过精馏过程进行分离。 精馏是利用混合液中不同组分挥发温 度的差异将各组分分离的过程。 精馏塔是精馏过程的关键设备,是过 程控制的重要控制对象。
⑷ 注意工艺操作的合理性、经济性。
简单控制系统由四个基本环节做成,被控对象、测量变送装置、控制器、 执行器四个部分的传递函数分别为Go(S),Gm(S),Gc(S),Gv(S)。简单控制 系统是最基本的控制系统。约占工业控制系统的80%以上。只有在简单 控制系统不能满足生产更高要求的情况下,才用复杂控制系统。 单回路控制系统是最基本的控制系统,由于其结构简单,投资少,易于 调整,操作维护比较方便,又能满足此系统的控制要求。所以本套系统 可采用简单的单回路控制。系统的流程图如下:
根据过程特性选择控制参数的一般原则 ⑴ 选择过程控制通道的放大系数要适当大一些;时间常数要适当 小一些;纯时延愈小愈好,在有纯时延的情况下,与之比应小一些 (小于1),若其比值过大,则不利于控制。
⑵ 选择过程扰动通道的放大系数应尽可能小;时间常数要大;扰 动引入系统的位置要远离控制过程(即靠近调节阀);容量时延愈大, 则有利于控制。 ⑶ 广义过程(包括调节阀和测量变送器)由几个一阶环节组成,在选 择控制参数时,应尽量设法把几个时间常数错开,使其中一个时问 常数比其他时间常数大得多,同时注意减小第二、第三个时间常数。