甲醇装置简介和重点部位及设备
甲醇装置工艺概述
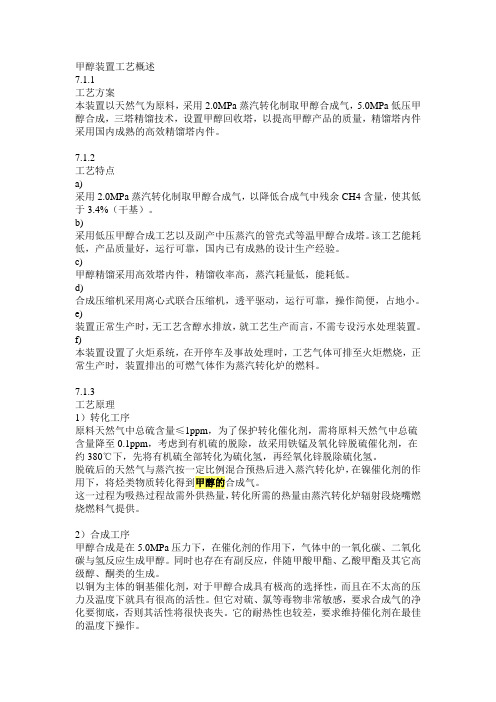
甲醇装置工艺概述7.1.1工艺方案本装置以天然气为原料,采用2.0MPa蒸汽转化制取甲醇合成气,5.0MPa低压甲醇合成,三塔精馏技术,设置甲醇回收塔,以提高甲醇产品的质量,精馏塔内件采用国内成熟的高效精馏塔内件。
7.1.2工艺特点a)采用2.0MPa蒸汽转化制取甲醇合成气,以降低合成气中残余CH4含量,使其低于3.4%(干基)。
b)采用低压甲醇合成工艺以及副产中压蒸汽的管壳式等温甲醇合成塔。
该工艺能耗低,产品质量好,运行可靠,国内已有成熟的设计生产经验。
c)甲醇精馏采用高效塔内件,精馏收率高,蒸汽耗量低,能耗低。
d)合成压缩机采用离心式联合压缩机,透平驱动,运行可靠,操作简便,占地小。
e)装置正常生产时,无工艺含醇水排放,就工艺生产而言,不需专设污水处理装置。
f)本装置设置了火炬系统,在开停车及事故处理时,工艺气体可排至火炬燃烧,正常生产时,装置排出的可燃气体作为蒸汽转化炉的燃料。
7.1.3工艺原理1)转化工序原料天然气中总硫含量≤1ppm,为了保护转化催化剂,需将原料天然气中总硫含量降至0.1ppm,考虑到有机硫的脱除,故采用铁锰及氧化锌脱硫催化剂,在约380℃下,先将有机硫全部转化为硫化氢,再经氧化锌脱除硫化氢。
脱硫后的天然气与蒸汽按一定比例混合预热后进入蒸汽转化炉,在镍催化剂的作用下,将烃类物质转化得到甲醇的合成气。
这一过程为吸热过程故需外供热量,转化所需的热量由蒸汽转化炉辐射段烧嘴燃烧燃料气提供。
2)合成工序甲醇合成是在5.0MPa压力下,在催化剂的作用下,气体中的一氧化碳、二氧化碳与氢反应生成甲醇。
同时也存在有副反应,伴随甲酸甲酯、乙酸甲酯及其它高级醇、酮类的生成。
以铜为主体的铜基催化剂,对于甲醇合成具有极高的选择性,而且在不太高的压力及温度下就具有很高的活性。
但它对硫、氯等毒物非常敏感,要求合成气的净化要彻底,否则其活性将很快丧失。
它的耐热性也较差,要求维持催化剂在最佳的温度下操作。
甲醇合成装置工艺流程及关键控制点分析简介
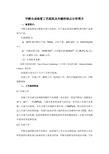
甲醇合成装置工艺流程及关键控制点分析简介一、装置简介:甲醇合成装置是以煤基合成气为原料,生产满足要求的MTO级甲醇产品和氢气产品。
(1)装置能力:a)MTO级甲醇日产量:5500t,小时产量:229.167t(以100%CH3OH 计)。
b)日输出氢气量:15456 Nm3,小时输出量644Nm3,(以99.5% H2计)。
(2)年操作小时:8000小时。
(3)专利技术来源:装置引进英国DPT(Davy Process Technology)公司的工艺包和JMC(Johnson Matthey Catalyst)催化剂。
(4)装置主要由以下几个工艺单元组成:压缩工序、合成工序、精馏工序、氢回收工序、蒸汽冷凝液回收工序、甲醇裂解制氢二、工艺流程简述2.1压缩工序压缩工序合成气压缩机和循环气压缩机。
来自界区(低温甲醇洗)的煤基合成气~30℃、~5.2MPaG,与膜分离来的富氢气混合后,依次进入合成气分离器、合成气压缩机,并在合成气压缩机中增压到~7.8MPaG。
增压后的合成气进入合成气净化预热器,用蒸汽加热并喷入锅炉给水以水解其中的COS,然后进入合成气净化槽,脱除残留的对合成催化剂有毒害的微量组份。
合成气净化槽中装填有净化催化剂。
2.2 合成工序甲醇合成回路由两个串联在一起的蒸汽上升式反应塔组成。
这种串联方式比传统流程在催化剂与设备投资上要更为经济。
甲醇合成塔为径向流反应器,气体通过装填在壳侧的催化剂,发生甲醇合成反应。
反应器内温度由管内上升的蒸汽控制。
副产蒸汽过热后送出界区。
来自合成气压缩机的净化后的合成气分为两股,其中大部分合成气和循环气混合,经过合成回路1号中间换热器加热后,进入1号甲醇合成塔进行甲醇合成反应。
甲醇合成反应在~280℃、~7.46MPaG下,在催化剂的作用下进行,该反应为放热反应。
主要的两个反应如下:CO + 2H2→ CH3OH + QCO2 + 3H2 → CH3OH + H2O + Q反应热副产~2.1MPaG的中压饱和蒸汽,经1号甲醇合成汽包分离后,进入装置内蒸汽总管。
20万吨甲醇装置工艺简介

5
改进与提高
2011年以来,由于天然气供应不足停车两个月(2010年12月3日-2011
年2月9日),利用此次机会更换了新的进口触媒,不断的对甲醇工艺进 行思考探索,装置整体消耗出现了大幅度的降低,尤其是2011年7月消耗
创历史最低:1022NM3/T(车间计量987NM3/T )。节能减排相当有效每
15
工艺流程图——说明
来自西部公司的天然气经过减压后压力1.4MP进入配
气站,流量为19122 Nm3/h的原料天然气进入天然气 压缩机K01101进行压缩,压缩后的天然气温度103℃
、压力2.85MPa送往天然气转化工序。
在天然气压缩前分离掉天然气中的轻质油等杂质(基
本没有液体)。
甲醇原料天然气压缩机K01101是由电机驱动的两级
压缩
天然气 转化 CO2 烟 道 气
K 01301
3.9MPa 工艺蒸汽
循环气 CO2 压缩
CO2
回收
19
19
工艺流程图——说明
合成气压缩机K01301的作用有两个,一是将来自转化工序的
转化气和氢回收工序的氢气加压后送到合成工序生产甲醇;二
是为合成塔气体循环提供动力。
经过合成气压缩机前5级压缩后,进入6级循环段压缩的气体
工艺上的转化工序采用一段炉蒸汽转化、压缩工序选用德国阿特拉
斯制造的多轴离心式压缩机、透平是德国西门子公司生产、CO2回 收是南化院的MEA溶液回收工艺包、精馏工序选取天津大学的三塔 工艺流程、氢回收采用普里森膜渗透技术、甲醇合成反应器选的是 具有自主知识产权的杭州林达公司制造的低压均温型合成塔。
4
4
合成反应过程中CO\CO2的单程转化率只有25~40%
甲醇的技术装备与设施
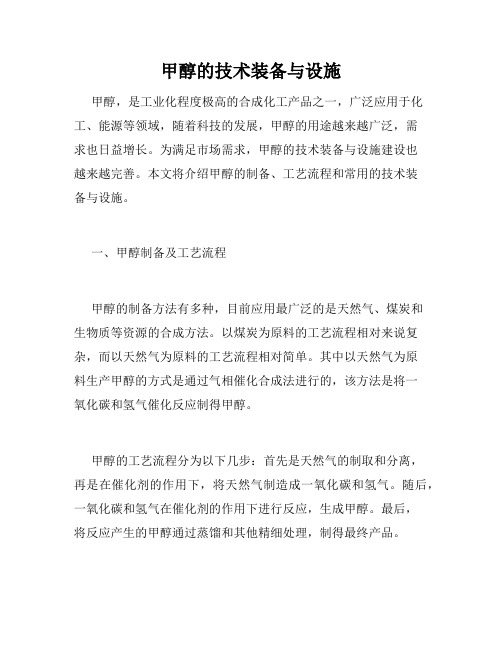
甲醇的技术装备与设施甲醇,是工业化程度极高的合成化工产品之一,广泛应用于化工、能源等领域,随着科技的发展,甲醇的用途越来越广泛,需求也日益增长。
为满足市场需求,甲醇的技术装备与设施建设也越来越完善。
本文将介绍甲醇的制备、工艺流程和常用的技术装备与设施。
一、甲醇制备及工艺流程甲醇的制备方法有多种,目前应用最广泛的是天然气、煤炭和生物质等资源的合成方法。
以煤炭为原料的工艺流程相对来说复杂,而以天然气为原料的工艺流程相对简单。
其中以天然气为原料生产甲醇的方式是通过气相催化合成法进行的,该方法是将一氧化碳和氢气催化反应制得甲醇。
甲醇的工艺流程分为以下几步:首先是天然气的制取和分离,再是在催化剂的作用下,将天然气制造成一氧化碳和氢气。
随后,一氧化碳和氢气在催化剂的作用下进行反应,生成甲醇。
最后,将反应产生的甲醇通过蒸馏和其他精细处理,制得最终产品。
二、甲醇的技术装备与设施1. 合成反应装置合成反应装置是甲醇制备工艺的核心设备之一,通常包括加气管、催化剂层和冷却水管等附件,它们的结构设计和装配工艺对甲醇合成反应的效果有重要影响。
目前从合成装置技术方面来看,常用的有固定床反应器、移动床反应器,流化床反应器等。
2. 精馏装置精馏装置是使甲醇精馏纯化、去除杂质的重要设备,包括粗精馏器、回流塔、精馏塔、加热系统、冷却系统等部分。
甲醇的精馏过程非常复杂,因此精馏塔的结构和操作控制至关重要。
通常采用的装置有常压塔、减压塔、等压塔和蒸汽回流塔等,其中蒸汽回流塔是目前甲醇精馏的主要方式。
3. 生产储罐生产储罐是指用于储存甲醇的设备,通常采用圆柱形或球形储罐,包括罐壁、罐盖、进气口、排出口、抽气口和检查孔等部分,有一定的环保和安全措施。
甲醇的储存需要安全性强且环保的设施,以免对人体和环境造成危害。
4. 废气回收设备甲醇合成过程会产生大量的废气,包括一氧化碳、二氧化碳、甲烷、氢气等物质。
因此,甲醇生产场地需要配置废气回收设备,用于收集和处理废气,减少对环境的污染和腐蚀。
甲醇装置大中型设备吊装方案
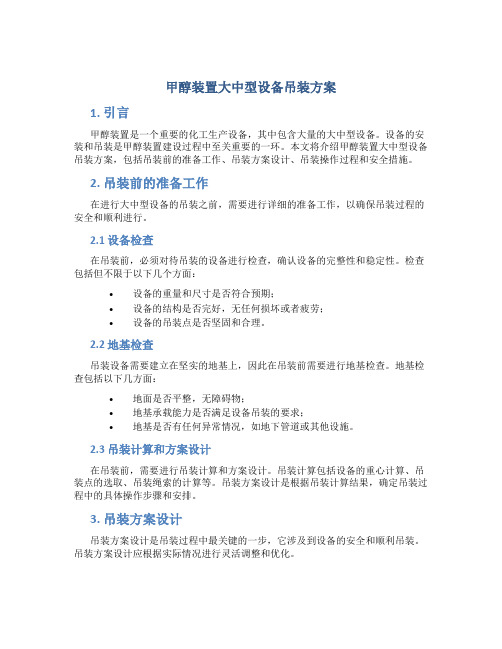
甲醇装置大中型设备吊装方案1. 引言甲醇装置是一个重要的化工生产设备,其中包含大量的大中型设备。
设备的安装和吊装是甲醇装置建设过程中至关重要的一环。
本文将介绍甲醇装置大中型设备吊装方案,包括吊装前的准备工作、吊装方案设计、吊装操作过程和安全措施。
2. 吊装前的准备工作在进行大中型设备的吊装之前,需要进行详细的准备工作,以确保吊装过程的安全和顺利进行。
2.1 设备检查在吊装前,必须对待吊装的设备进行检查,确认设备的完整性和稳定性。
检查包括但不限于以下几个方面:•设备的重量和尺寸是否符合预期;•设备的结构是否完好,无任何损坏或者疲劳;•设备的吊装点是否坚固和合理。
2.2 地基检查吊装设备需要建立在坚实的地基上,因此在吊装前需要进行地基检查。
地基检查包括以下几方面:•地面是否平整,无障碍物;•地基承载能力是否满足设备吊装的要求;•地基是否有任何异常情况,如地下管道或其他设施。
2.3 吊装计算和方案设计在吊装前,需要进行吊装计算和方案设计。
吊装计算包括设备的重心计算、吊装点的选取、吊装绳索的计算等。
吊装方案设计是根据吊装计算结果,确定吊装过程中的具体操作步骤和安排。
3. 吊装方案设计吊装方案设计是吊装过程中最关键的一步,它涉及到设备的安全和顺利吊装。
吊装方案设计应根据实际情况进行灵活调整和优化。
3.1 吊装点的选取吊装点是吊装过程中最重要的一个环节。
吊装点的选取应根据设备的重心和结构特点进行合理选择。
吊装点应尽可能靠近设备的重心,并保证设备在吊装过程中能够保持稳定。
3.2 吊装绳索的选择和布置吊装绳索的选择和布置也是吊装方案设计的重要内容。
吊装绳索的选择应根据设备的重量和结构特点进行合理选择。
吊装绳索的布置要保证吊装力的均衡分配,避免设备在吊装过程中产生不稳定或者倾斜。
3.3 吊装设备的安全措施在吊装过程中,必须采取一系列的安全措施,以保证设备和人员的安全。
这些安全措施包括但不限于以下几个方面:•制定详细的吊装操作流程和安全规范;•严格执行人员的吊装操作资质要求;•配备足够的安全保护装备,如安全帽、安全绳等;•定期进行设备和吊装绳索的检查和维护。
甲醇合成装置工艺说明

甲醇合成装置工艺说明目录1 概述2 技术概况3 工艺技术方案选择4 工艺流程简述5 物料平衡6 消耗7 主要操作条件8 主要设备选型9 技术和设备来源10 节能11 三废排放12 装置占地13 定员1 概述甲醇合成装置将来自低温甲醇洗的净化气转化为粗甲醇。
拟采用德国Lurgi低压甲醇合成技术。
粗甲醇送往甲醇精馏装置,弛放气去氢回收装置,闪蒸气去燃料气管网。
甲醇合成装置处理能力为507344Nm3/h净化气,甲醇产量为230吨/小时(以100%甲醇计)。
2技术概况甲醇工业化始于20世纪初,1923年德国BASF公司首先建立了一套采用Zn-Cr催化剂、合成压力为30.0MPa、规模为300吨/年的高压法甲醇生产装置。
20世纪60年代,甲醇工业随着选择性好、低温活性高的铜基催化剂开发成功而取得重大进展。
1966年英国ICI 公司研制成功Cu-Zn-Al催化剂后,推出ICI低压甲醇合成工艺,在所属Billingham工厂建立了工业化装置。
1971年德国Lurgi公司成功开发出采用活性更高的Cu-Zn-Al-V催化剂的另一著名低压法工艺-Lurgi工艺。
此后,世界各大公司竞相开发了各具特色的低压法工艺技术。
与高压法工艺相比,低压法工艺在投资和综合技术经济指标方面都具有显著优势。
以天然气为原料的甲醇厂,高压法能耗达64.8GJ/t甲醇,而大型低压法装置为29.5~31.5GJ/t 甲醇。
1970年代后国外新建的大中型甲醇装置全部采用低压法,高压法渐趋淘汰。
高、低压法甲醇生产主要操作条件如下:随着1997年德国Lurgi公司大甲醇(MegaMethanol)概念的提出,甲醇技术逐渐向大型化发展,Lurgi,Davy,Topsoe等公司相继提出大甲醇技术,各种甲醇合成技术,主要体现在甲醇合成反应器的设计上。
2.1 Lurgi甲醇反应器传统的Lurgi甲醇反应器为列管等温反应器,其结构形式与管壳式换热器非常类似,列管内装填催化剂,管间为沸腾水。
甲醇合成的主要设备
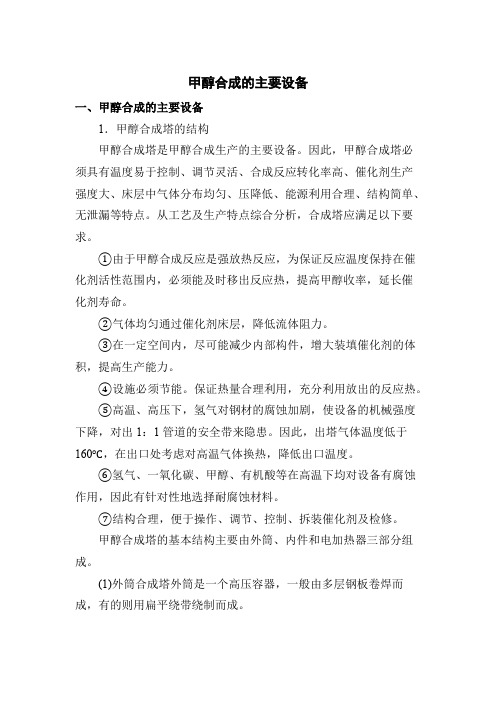
甲醇合成的主要设备一、甲醇合成的主要设备1.甲醇合成塔的结构甲醇合成塔是甲醇合成生产的主要设备。
因此,甲醇合成塔必须具有温度易于控制、调节灵活、合成反应转化率高、催化剂生产强度大、床层中气体分布均匀、压降低、能源利用合理、结构简单、无泄漏等特点。
从工艺及生产特点综合分析,合成塔应满足以下要求。
①由于甲醇合成反应是强放热反应,为保证反应温度保持在催化剂活性范围内,必须能及时移出反应热,提高甲醇收率,延长催化剂寿命。
②气体均匀通过催化剂床层,降低流体阻力。
③在一定空间内,尽可能减少内部构件,增大装填催化剂的体积,提高生产能力。
④设施必须节能。
保证热量合理利用,充分利用放出的反应热。
⑤高温、高压下,氢气对钢材的腐蚀加剧,使设备的机械强度下降,对出1:1管道的安全带来隐患。
因此,出塔气体温度低于160℃,在出口处考虑对高温气体换热,降低出口温度。
⑥氢气、一氧化碳、甲醇、有机酸等在高温下均对设备有腐蚀作用,因此有针对性地选择耐腐蚀材料。
⑦结构合理,便于操作、调节、控制、拆装催化剂及检修。
甲醇合成塔的基本结构主要由外筒、内件和电加热器三部分组成。
(1)外筒合成塔外筒是一个高压容器,一般由多层钢板卷焊而成,有的则用扁平绕带绕制而成。
(2)内件内件由催化剂筐和换热器两部分组成。
催化剂筐是填装催化剂进行合成反应的组合件。
换热器分两类,一是为满足开车时催化剂活性温度,对原料气进行加热的需要,可采用电加热器;二是对进出催化剂床层的反应气体进行热交换,以达到工艺生产要求。
①催化剂筐。
甲醇合成塔内件的设计主要是催化剂筐的设计,它的形式与结构需尽可能实现催化剂床层内最佳温度分布,一般连续冷管有自热式和外冷式两种结构。
自热式是利用反应热,用冷原料气为冷却剂,使催化剂床层降温,原料气体同时被加热。
自热式又分为单管逆流、双套管并流、三套管并流、单管并流以及U形管式。
外冷式是冷却剂采用其他介质进行冷却。
②换热器。
换热器的作用是回收合成气反应后的热量及提高冷原料气的温度。
煤制甲醇设备一览表

煤制甲醇设备一览表一、引言煤是我国主要的能源资源之一,而甲醇作为一种重要的化工原料和清洁燃料,对于能源结构调整和环境保护具有重要意义。
煤制甲醇是将煤转化为甲醇的工艺过程,其关键在于煤制甲醇设备的选用和优化。
二、煤制甲醇设备一览表以下是煤制甲醇常用的设备一览表:1. 煤气化设备煤气化是将煤转化为合成气的过程,合成气中主要成分为一氧化碳和氢气,是煤制甲醇的原料。
常用的煤气化设备有固定床煤气化炉、流化床煤气化炉和煤浆气化炉等。
2. 合成气净化设备合成气中含有一定的杂质,需要进行净化处理。
常用的合成气净化设备有除尘器、除硫器、除氮器等。
3. 合成气变换设备合成气变换是将一氧化碳和氢气转化为甲醇的过程。
常用的合成气变换设备有催化剂床、换热器、压力容器等。
4. 甲醇分离设备甲醇分离是将合成气中的甲醇从其他组分中分离出来的过程。
常用的甲醇分离设备有精馏塔、吸收塔、萃取塔等。
5. 废气处理设备煤制甲醇过程中会产生一些废气,包括煤气化废气、合成气净化废气和甲醇生产废气等。
这些废气中含有一些有害物质,需要进行处理和净化。
常用的废气处理设备有除尘器、脱硫装置、脱氮装置等。
6. 热力设备煤制甲醇过程中需要进行能量转化和供应,因此需要热力设备。
常用的热力设备有锅炉、热交换器、蒸汽发生器等。
7. 辅助设备除了上述主要设备外,煤制甲醇还需要一些辅助设备来保障生产运行的顺利进行,如压缩机、泵站、储存设备等。
三、煤制甲醇设备选型和优化在煤制甲醇项目中,设备的选型和优化是至关重要的一环。
选用合适的设备可以提高生产效率、降低能耗、增加产品质量和降低环境污染。
优化设备结构和工艺参数可以进一步提高设备的性能和经济效益。
1. 设备选型设备选型需要考虑煤的性质、产量要求、工艺流程以及经济效益等因素。
不同类型的煤制甲醇工艺可能需要不同的设备选型,如煤气化方式的选择会影响煤气化设备的选用,而甲醇生产工艺的选择会影响合成气变换和甲醇分离设备的选用。
- 1、下载文档前请自行甄别文档内容的完整性,平台不提供额外的编辑、内容补充、找答案等附加服务。
- 2、"仅部分预览"的文档,不可在线预览部分如存在完整性等问题,可反馈申请退款(可完整预览的文档不适用该条件!)。
- 3、如文档侵犯您的权益,请联系客服反馈,我们会尽快为您处理(人工客服工作时间:9:00-18:30)。
甲醇装置简介和重点部位及设备
一、装置简介
(一)装置发展及类型
以一氧化碳和氢为原料合成甲醇的生产技术始于20世纪20年代。
到50年代末,我国已掌握了甲醇和合成甲醇催化剂的制备技术。
60年代未,我国又实现了合成氨和合成甲醇的联合生产(简称联醇),联醇技术降低了合成氨和甲醇的生产成本。
20世纪60年代,世界上,低压法合成甲醇新工艺技术实现了工业化。
低压法由于其能耗低,逐步取代了原来的高压法合成甲醇工艺,并得到了快速发展。
80年代初,我国研制的低压合成甲醇催化剂已达到国际水平。
联醇工艺技术是合成氨生产过程中,利用合成氨原料气中一氧化碳、二氧化碳与氢气同时生产甲醇。
联醇工艺技术由于生产方式灵活、工艺简单、原料利用率高、成本低、效益好,在我国中型合成氨装置得到普遍的推广。
甲醇生产一般以天然气、轻油、重油、煤及某些加工过程中产生的尾气为原料。
制得的原料气通过净化,得到一氧化碳、二氧化碳与氢气,经合成生成甲醇。
典型的流程包括原料气制备、原料气净化、甲醇合成和粗甲醇精馏等工序。
甲醇装置生产工艺所采用的原料气制备与净化工艺,与合成氨装置相同或相类似。
原料气制备工艺类型一般有:煤(焦)固定床气化工艺;煤(焦)气流床气化工艺;渣油、水煤浆部分氧化制气工艺;烃类(轻
油、天然气)蒸汽转化制气工艺。
气体净化工艺类型也与合成氨原料气净化工艺类型相同,一般根据原料气的组成不同而采用不同的脱硫、变换、脱碳工艺技术。
甲醇的合成工艺类型主要有高压法和低压两种:前者操作温度300-400℃,操作压力30-50MPa(表);后者操作温度220-250℃,操作压力5.0—8.0MPa(表)。
甲醇合成塔类型:按气体流向分有轴向塔和径向塔;按床层换热方式分有内部换热式、中间换热式和中间冷凝式。
甲醇精馏有常压法和加压法,以及双塔精馏和三塔精馏两种流程。
低压法合成甲醇工艺技术目前发展的方向是:采用活性高、转化率高、选择性好的甲醇合成催化剂;采用温差小、阻力小、反应温度易控制、热能回收率高的均温型合成塔;并不断提高热量利用率和合成气利用率,向低能耗方向发展。
(二)单元组成与工艺流程
1.组成单元
甲醇生产装置采用的原料种类不同,工艺流程不同,其组成单元也不同。
现介绍以天然气为原料,采用低压合成工艺技术的甲醇生产装置。
装置由硫化物脱除(简称脱硫)、天然气蒸汽转化制气(简称转化)、合成气压缩(简称压缩)、甲醇合成(简称合成)、粗甲醇精馏(简称精馏)5个单元组成。
各单元介绍如下:
(1)脱硫
天然气与氢气混合进行加氢反应,将天然气中的不饱和烃、有机。