第三章--硫化物的脱除
硫化物脱除工艺

硫化物脱除工艺
工艺概述
硫化物脱除工艺的主要步骤包括:预处理、吸附和再生。
1. 预处理
在吸附之前,首先需要对含有硫化物的物质进行预处理。
这可
以包括去除杂质、调整pH值等操作,以提高后续吸附过程的效果。
2. 吸附
吸附是硫化物脱除工艺的核心步骤。
一种常用的吸附剂是活性炭,它能有效吸附硫化物。
将活性炭投加到含有硫化物的物质中,
经过一定时间的接触,硫化物将被吸附在活性炭上。
3. 再生
吸附剂饱和后,需要进行再生。
再生的过程可以通过多种方法进行,如热解、酸碱洗等。
再生后的吸附剂可以继续用于下一轮吸附,降低成本和资源消耗。
工艺优势
该硫化物脱除工艺具有以下优势:
1. 简单:工艺步骤简单明了,易于操作和控制。
2. 高效:吸附剂能够有效地吸附硫化物,提高去除效率。
3. 可再生:吸附剂可以通过再生过程得到回收和再利用,提高资源利用率。
4. 无法确认的引用:我们不引用未经证实的内容,确保文档的准确性和可信度。
结论
硫化物脱除工艺是一项重要的环保工艺,该工艺通过预处理、吸附和再生步骤,能有效去除硫化物污染物。
该工艺具有简单、高效和可再生的优势,可在实际应用中发挥重要作用。
请注意:以上所述内容仅为概述,具体实施时需根据不同情况进行调整和优化。
_无机化工单元工艺3
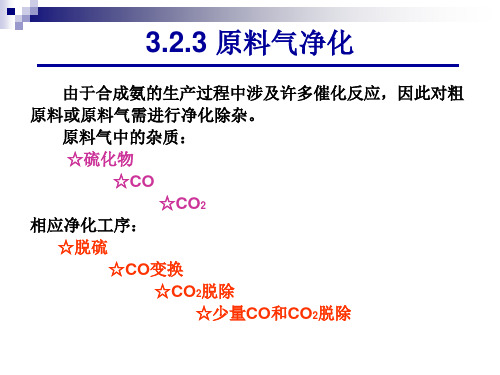
可使S含量 降到0.1ppm 以下,可单 独使用,也 可与加氢转 化催化剂串 联使用
氧化锌脱硫的工业条件: ★脱无机硫200℃,脱有机硫350-450 ℃。 ★硫容量0.15-0.30kg/kg 氧化锌脱硫特点: ★反应不可逆,脱硫剂无法再生; ★脱硫较完全,适合脱微量硫; ★硫含量较高时,需与其他方法配合使用。 ★脱硫反应瞬间完成。 脱硫反应特征: 是一种气固相反应,反应在氧化锌的微孔内表面上进行 ,反应速度属于内扩散控制。 因此,氧化锌脱硫剂均制成高空隙率的球形小颗粒,反 应几乎是瞬时的,反应区域较窄。
增加水蒸气用量,既有利于提高一氧化碳的变 换率,又有利于提高变换反应速度,同时抑制 副反应。但能耗增加。
1、山东兖州鲁南化肥厂原始开车的摸索过程中,曾经出
现过一次由于将人变换炉汽气 比控制太低 ,造成发 生急剧的甲烷化反应,床层超温至802℃。 2、蒸汽用量大,导致炉温垮温事故。
注:实际生产中,可测定原料气和变换气中的CO,且视为干基, 一氧化碳的转化率:
应的发生。
e 电耗降低
a 腐蚀加剧(点蚀 ),设备使用寿命缩短。 (尤其是采用耐硫变换催化剂流程) b 有机硫转化↓
缺点
B、温度
(1)热力学角度
logKp=2183/T-0.09361logT+0.632×10-3T-1.08×10-7T2-2.298
温度/℃ Kp
200 227.9
250 86.51
吸收反应 NH4OH+H2S=NH4HS+H2O O
OH
氧化反应
NH4HS+
+H2O =
NH4OH+
+S
O
OH
OH
O
化学工艺学 合成气中硫化物和二氧化碳的脱除

合成气中硫化物和二氧化碳的脱除1.1合成气中硫化物的脱除在制气时,所用的气、液、固三类原料均含硫化物。
在制气时转化成硫化氢和有机硫气体,它们会使催化剂中毒,腐蚀金属管道和设备,危害很大,必须脱除,并回收利用这些硫资源。
1.1.1硫化物的危害硫化物是制气过程中最常见、最重要的催化剂毒物,极少量硫化物就会使催化剂中毒,使催化剂活性降低直至完全失活。
硫化物主要有硫化氢和有机硫化物,后者在高温和水蒸气、氢气作用下也转变成硫化氢。
用天然气或轻油制气时,为避免蒸汽转化催化剂中毒,已预选将原料彻底脱硫,转化生成的气体中无硫化物。
煤或重质油制气时,氧化过程不用催化剂,不用对原料预脱硫,因此产生的气体中有硫,在下一步加工前必须进行脱脱硫。
1.1.2硫化物脱除的方法分类脱硫方法要根据硫化物的含量、种类和要求的净化度来选定,还要考虑技术条件和经济性,有时可用多种脱硫方法组合来达到对脱硫净化度的要求。
按脱硫剂状态来分,有干法、湿法两大类。
干法脱硫可分为吸附法和催化转化法,湿法脱硫可分为化学吸收法、物理吸收法、物理-化学吸收法和湿式氧化法。
下面主要介绍湿法脱硫中的物理吸收法(NHD)。
1.1.3 NHD脱硫方法湿法脱硫剂为液体,一般用于含硫量高、处理量大的气体的脱硫。
其中物理吸收法是利用有机溶剂在一定压力下进行物理吸收脱硫,然后减压而释放出硫化物气体,溶剂得以再生。
主要有冷甲醇法、此外还有碳酸丙烯酯法、N-甲基吡啶烷酮法、NHD法等,主要介绍NHD法。
1.1.3.1原理及工艺流程NHD溶剂是一种有机溶剂(聚乙二醇二甲醚),它对气体中硫化物和二氧化碳具有较大的溶解能力,尤其是对硫化氢有良好的选择吸收性,NHD溶剂物化性能稳定,蒸气压低,挥发损失小,无气味、无毒、不腐蚀、不分解。
该工艺能耗低、消耗低、成本低,运转时溶剂耗损少,是一种较理想的物理吸收剂,适合于以煤(油)为原料,酸气分压较高的合成气等的气体净化,脱硫时需消耗少量热量,脱碳时需消耗少量冷量,属低能耗的净化方法。
焦炉气制甲醇工艺中硫化物的脱除研究
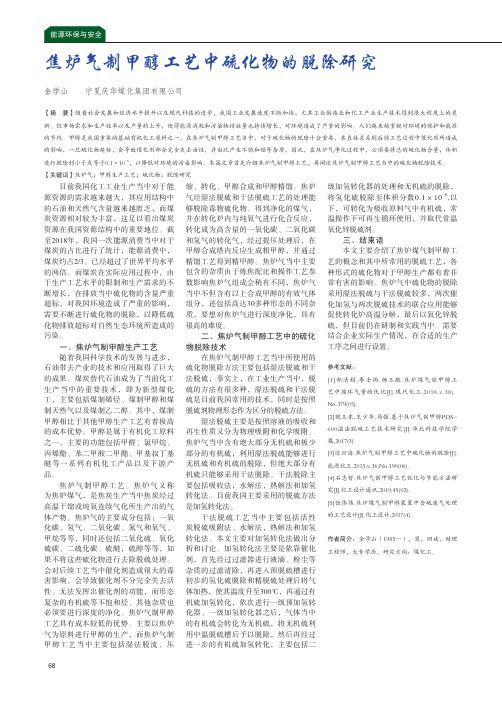
68目前我国化工工业生产当中对于能源资源的需求越来越大,其应用结构中的石油和天然气含量越来越匮乏,而煤炭资源相对较为丰富,这足以看出煤炭资源在我国资源结构中的重要地位。
截至2018年,我国一次能源消费当中对于煤炭的占比进行了统计,能源消费中,煤炭约占2/3。
已经超过了世界平均水平的两倍。
而煤炭在实际应用过程中,由于生产工艺水平的限制和生产需求的不断增长,在排放当中硫化物的含量严重超标,对我国环境造成了严重的影响,需要不断进行硫化物的脱除,以降低硫化物排放超标对自然生态环境所造成的污染。
一、焦炉气制甲醇生产工艺随着我国科学技术的发展与进步,石油带去产业的技术和应用取得了巨大的成果。
煤炭替代石油成为了当前化工生产当中的重要技术,即为新型煤化工,主要包括煤制烯烃、煤制甲醇和煤制天然气以及煤制乙二醇。
其中,煤制甲醇相比于其他甲醇生产工艺有着极高的成本优势。
甲醇是属于有机化工原料之一,主要的功能包括甲醛、氯甲烷、丙烯酯、苯二甲酸二甲酯、甲基叔丁基醚等一系列有机化工产品以及下游产品。
焦炉气制甲醇工艺。
焦炉气又称为焦炉煤气,是焦炭生产当中焦炭经过高温干馏或纯氧连续气化所生产出的气体产物。
焦炉气的主要成分包括:一氧化碳、氢气、二氧化碳、氮气和氧气、甲烷等等,同时还包括二氧化硫、氧化硫碳、二硫化碳、硫醚,硫醇等等,如果不将这些硫化物进行去除脱硫处理。
会对后续工艺当中催化剂造成很大的毒害影响,会导致催化剂不分完全失去活性。
无法发挥出催化剂的功能,而形态复杂的有机硫等不饱和烃、其他杂质也必须要进行深度的净化。
焦炉气制甲醇工艺具有成本较低的优势。
主要以焦炉气为原料进行甲醇的生产,而焦炉气制甲醇工艺当中主要包括湿法脱流、压缩、转化、甲醇合成和甲醇精馏。
焦炉气经湿法脱硫和干法脱硫工艺的处理能够脱除毒物硫化物。
得到净化的煤气,并在转化炉内与纯氧气进行化合反应,转化成为高含量的一氧化碳、二氧化碳和氢气的转化气,经过提压处理后,在甲醇合成塔内反应生成粗甲醇,并通过精馏工艺得到精甲醇。
石油化工脱硫方法

石油化工脱硫方法随着环保和市场对石化产品中硫含量要求越来越苛刻,石油化工中硫化物脱除,尤其是较难脱除的有机硫化物脱除方法已成为各石化企业和研究者关注的热点。
本文就近年来有机硫化物脱除方法的研究进展进行综述,介绍了加氢转化、生物脱除技术、超生婆脱硫、沸石脱硫、液相吸附脱硫、离子液脱硫等,展望了有机硫脱除技术发展远景。
关键词:有机硫;脱除;石油化工随着世界范围环保要求日益严格,人们对石油产品质量要求也越来越苛刻,尤其是对燃烧后形成SO2、SO3继而与大气中水结合形成酸雾、酸雨严重影响生态环境和人们日常生活的硫化物含量限制。
世界各国对燃油中的硫提出了越来越严格的限制,以汽油为例,2005年欧美要求含硫质量分数降低到30×10-6~50×10-6,至2006年,欧洲、德国、日本、美国等国家和地区要求汽油中硫含量低于10~50µg/g,甚至提出生产含硫质量分数为5×10-6~10×10-6的“无硫汽油;”自2005年起,我国供应北京、上海的汽油招待相当于欧洲Ⅲ排放标准的汽油规格,即含硫质量分数低于150×10-6。
为了满足人们对石油产品高质量的要求和维护生产安全稳定进行,石油化工各生产企业不断改进生产过程中的脱硫工气。
石油化工生产过程中涉及到的硫化物可分为无机硫化物和有机硫化物,无机硫化物较容易脱除,本文就比较难脱除的有机硫脱除技术新进展进行综述。
1 加氢转化脱硫天然气、液化气、炼厂气、石脑油及重油中常含有二硫化碳、硫醇、硫醚、羰基硫和噻吩等有机硫化物,热分解温度较高,且不易脱除。
加氢转化脱硫技术是最有效的脱除手段之一。
有机硫在加氢转化催化剂作用下加氢分解生成硫化氢(H2S)和相应的烷烃或芳烃,生成的H2S可由氧化锌等脱硫剂脱除达到很好的脱除效果。
近年来,国外开发出几种典型的催化裂化(FCC)汽油脱硫新工艺,如ExxonMobil公司的SCANFining工艺和OCTGAIN工艺、LFP公司的Prime-G+工艺和UOP公司的ISAL工艺;在中内,中国石化抚顺石油化工研究院(FRIPP)针对我国FCC汽油的不同特点,开发出了OCT-M、FRS和催化裂化(FCC)汽油加氢脱硫/降烯烃技术并在国内石化企业得到成功应用;还开发了FH-DS柴油深度加氢脱硫催化剂,成功应用于福建炼油化工有限公司柴油加氢装置[1,2],此外洛阳石油化工工程公司工程研究院开发出催化裂化汽油加氢脱硫及芳构化工气技术Hydro-GAP[3]。
粗原料气的净化—硫化物的脱除(合成氨生产)

由脱随塔流出的富液,送至脱硫闪蒸槽而后进人H2S提浓塔,塔顶进液 为脱硫贫液,中部进液为脱硫富液。在H2S提浓塔后还有一个闪蒸槽。 闪 蒸气压缩后作为H2S提浓塔的气提气。由H2S提浓塔出来的气体含H2S25% 左右,可直接送至克劳斯法制硫装置。由脱碳闪蒸槽出来的闪蒸气含CO2 99%左右,可作尿素生产原料之用。
本书仅对近年来备受人们关注的Slexol怯(中国称为NHD法)脱硫作简介。此法 1965 年首先由美国Alied Chenical公司采用,至今已有 40多套装置在各国运 行。脱硫剂的主体成分为聚乙二醇二甲醒,商品名为Selexol。它是一种聚乙 二醇二甲醚同系物混合体。分子式为CH3O CH-O- CH2 nCH。 式中n为3-9。 平均相对分子质量为22-242。各种同系物的质量分数,%大致如下。
3、脱硫剂活性好,容易再生,定额消耗低
脱硫剂活性好,容易再生,可以降低生产的费用,符合工业生 产的经济性。
4、不易发生硫堵
硫堵:进脱硫塔气体的成分不好,杂志耗量较高;反应时析出的 硫不能及时排出;脱硫塔淋喷密度不够;再生空气量不足,吹风强度 低等原因造成硫堵。
5、脱硫剂价廉易得
采用最多的是廉价的石灰、石灰石和用石灰质药剂配制的碱性溶 液。以提高生产的经济性。
酞菁钴价格昂贵,但用量很少,脱硫液中PDS含量仅在数十个cm3/ m3左右。PDS的吨氨耗量一般在1.3-2.5g左右,因而运行的经济效益也较 显著。
此法也可脱除部分有机硫。若脱硫液中存在大量的氰化物,仍能导致 PDS中毒,但约经60h靠其自身的排毒作用,其脱硫活性可以逐渐恢复。 PDS对人体无毒,不会发生设备硫堵,无腐蚀性。
再
较高的温度有利于硫磺的分离,使析出的硫易于凝聚,
生
化工工艺学__复习

化⼯⼯艺学__复习第⼆章制⽓# 热量的供给⽅式不同有两种制备粗原料⽓的⽅法:1外部供热的蒸汽转化法; 2内部蓄热的间歇操作法# ⽓态烃蒸汽转化反应在⾼温有催化剂存在的条件下可实现下述反应:CH4(g) + H2O(g) = CO(g) + 3H2(g) CO(g) + H2O(g) = CO2(g) + H2(g)但要完成这⼀⼯业过程,必须对可能发⽣的主要反应及副反应进⾏详细研究。
主要的副反应有CH4(g) = C (s) + 2H2(g) ;2CO(g) = CO2(g) + C(s) ; CO(g) + H2(g) = C(s) + H2O(g)# CH4转化反应热⼒学:甲烷蒸汽转化在⾼温、⾼⽔碳⽐和低压下进⾏为好# CH4转化反应的动⼒学分析:反应主要取决于在催化剂内表⾯的反应,所以该反应控制步骤为内表⾯控制。
因此减⼩粒度增加内表⾯积有利于扩散过程和提⾼反应速率。
#防⽌析炭的措施:A 配料时增⼤S/C,从热⼒学上去消除B选⽤适宜的催化剂C选择适宜的操作条件。
#析碳的处理析炭不严重,可减压、减原料⽓,提⾼S/C,甚⾄可停进天然⽓,利⽤析炭逆反应除碳析炭严重,可通⼊蒸汽为载体,加⼊少量空⽓燃烧碳,但空⽓量⼀定要严格控制,结束后对催化剂进⾏还原。
#转化过程描述;⼀段转化完成转化⼤部分任务;⼆段炉转化剩余甲烷和加⼊原料氮⽓空⽓加⼊量对⼆段炉出⼝⽓组成和温度有⽆影响,如何影响?P97#对转化催化剂的要求⾼活性、强度好、耐热性好、抗析炭能⼒强.(转化催化剂所处⼯况转化温度⾼、⽔蒸⽓和氢⽓分压⾼、流速⼤、可能析炭)#转化催化剂的基本组成NiO为最主要活性成份。
实际加速反应的活性成份是Ni,所以使⽤前必须进⾏还原反应,使氧化态变成还原态Ni NiO(s) +H2(g) = Ni(s) + H2O(g)#催化剂制备制备⽅法有三种:沉淀法、浸渍法、混合法,这三种⽅法最后都需要进⾏⾼温焙烧,从⽽使催化剂有⾜够的机械强度#转化分为⼆段的原因:A转化条件不允许;B补充合成所需要的氮⽓#为什么⽤⼆段转化⽅式?转化率⾼必须转化温度⾼,全部⽤很⾼温度,设备和过程控制都不利,设备费⽤和操作费⽤都⾼。
脱硫方法
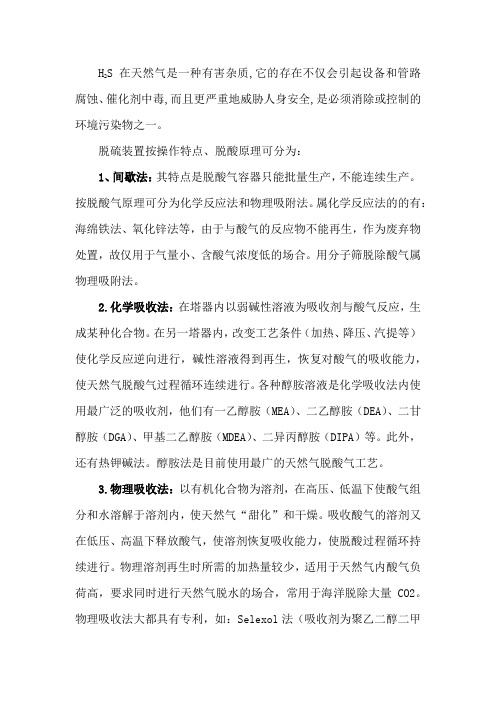
H2S在天然气是一种有害杂质,它的存在不仅会引起设备和管路腐蚀、催化剂中毒,而且更严重地威胁人身安全,是必须消除或控制的环境污染物之一。
脱硫装置按操作特点、脱酸原理可分为:1、间歇法:其特点是脱酸气容器只能批量生产,不能连续生产。
按脱酸气原理可分为化学反应法和物理吸附法。
属化学反应法的的有:海绵铁法、氧化锌法等,由于与酸气的反应物不能再生,作为废弃物处置,故仅用于气量小、含酸气浓度低的场合。
用分子筛脱除酸气属物理吸附法。
2.化学吸收法:在塔器内以弱碱性溶液为吸收剂与酸气反应,生成某种化合物。
在另一塔器内,改变工艺条件(加热、降压、汽提等)使化学反应逆向进行,碱性溶液得到再生,恢复对酸气的吸收能力,使天然气脱酸气过程循环连续进行。
各种醇胺溶液是化学吸收法内使用最广泛的吸收剂,他们有一乙醇胺(MEA)、二乙醇胺(DEA)、二甘醇胺(DGA)、甲基二乙醇胺(MDEA)、二异丙醇胺(DIPA)等。
此外,还有热钾碱法。
醇胺法是目前使用最广的天然气脱酸气工艺。
3.物理吸收法:以有机化合物为溶剂,在高压、低温下使酸气组分和水溶解于溶剂内,使天然气“甜化”和干燥。
吸收酸气的溶剂又在低压、高温下释放酸气,使溶剂恢复吸收能力,使脱酸过程循环持续进行。
物理溶剂再生时所需的加热量较少,适用于天然气内酸气负荷高,要求同时进行天然气脱水的场合,常用于海洋脱除大量CO2。
物理吸收法大都具有专利,如:Selexol法(吸收剂为聚乙二醇二甲醚)、Rectisol法(吸收剂为甲醇)、Fluor法(吸收剂为碳酸丙烯)等。
4.混合溶剂吸收法:由物理溶剂和化学溶剂配制的混合溶剂,兼有物理吸收和化学吸收剂性质。
如:Sulfinol法(吸收剂为属物理溶剂的环丁砜和属化学溶剂的DIPA或MDEA的混合溶剂,称砜胺法)。
5.直接氧化法:对H2S直接氧化使其转换成元素硫,如:Claus (克劳斯)法、LOCAT法、Stretford(蒽醌)法,Sulfa-check等。
- 1、下载文档前请自行甄别文档内容的完整性,平台不提供额外的编辑、内容补充、找答案等附加服务。
- 2、"仅部分预览"的文档,不可在线预览部分如存在完整性等问题,可反馈申请退款(可完整预览的文档不适用该条件!)。
- 3、如文档侵犯您的权益,请联系客服反馈,我们会尽快为您处理(人工客服工作时间:9:00-18:30)。
第三章硫化物的脱除半水煤气中,因煤的种类不同而含有数量不等的硫化物。
这些硫化物对含合成氨生产有着严重危害,必须首先予以除去,以保证后工段工作顺利进行。
在合成氨生产中,要求经过脱硫后的半水煤气中H2S含量在0.07g.m3(标)以下,碳化气中H2S含量在0.01g/m3(标)以下。
对于联醇生产厂则在求碳化气硫化物含量在0.1mg/m3(标)以下。
脱硫方法很多,可分为干法和湿法两大类,其中湿式氧化法脱硫多用于半水煤气和变换气的一次脱硫,而干法脱硫多用于变换气脱硫和碳化气的精脱硫。
一、湿式氧化法脱硫1、半水煤气中的硫化物主要有哪几种?它们的主要性质是什么?半水煤气中的硫化物的种类因煤的种类不同而含有数量不等的硫化物。
这些硫化物主要是硫化氢,约占硫化物总量的90%。
另外还含有少量的有机硫化物,主要是二硫化碳、羰基硫、硫醇等。
硫化物的主要性质分述如下。
(1)硫化氢,分子式H2S,是无色气体,有类似腐烂鸡蛋的恶臭味。
性剧毒。
易溶于水,其水溶液呈酸性,能与碱生成盐。
可用碱溶液来吸收它以除去气体中的硫化氢。
硫化氢有很强的还原能力,易被氧化成硫磺和水,这一性质被广泛地用于脱除硫化氢并副产硫磺的工艺上。
硫化氢还容易与金属、金属氧化物或金属的盐类生成金属硫化物。
(2)二硫化碳,分子式CS2,无色液体,难溶于中,与碱的水溶液发生反应:3CS2+6KOH K2CO3+3K2CS3+3H2O二硫化碳还可被氢还原,视反应条件可生成硫化氢、硫醇或其他有机硫化物,在高温下与水蒸汽作用几乎可完全转化为硫化氢。
(3)羰基硫,分子式COS,是无色无嗅的气体,微溶于水。
干燥的COS较稳定,在高温下有可能分解为二硫化碳和二氧化碳,9000C可分解出硫。
在高温下可与水蒸汽作用转化成硫化氢。
与碱的水溶液一起能缓缓地进行下面的反应:COS+2NaOH Na2CSO2+H2O生成的硫化碳酸盐不稳定,可分解成碳酸钠和硫化钠Na2CSO2+2NaOH Na2S+H2O+Na2CO3(4)硫醇,分子式RSH(R为烷基),低分子硫醇具有令人厌恶的气味,浓度仅为1×10-3g/L,就可被人感觉出来。
有毒。
不溶于水。
呈酸性,其酸性比相应的醉类强,能与金属盐类或碱作用。
硫醇在加热条件下可分解成烯烃与硫化氢,分解温度150~2500C。
2、硫化物对合成氨生产工艺过程有何危害?(1)对催化剂的危害硫是甲烷化催化剂、高(中)温变换催化剂、甲醇合成催化剂和氨合成催化剂的主要毒物之一,能使它们的活性和寿命显著降低。
(2)对产品质量的危害碳铵生产过程中,当变换气中H2S含量高时,在碳化母液中积累增高。
使母液粘度增大,碳铵结晶变细,不仅造成分离困难,同时,由于生成FeS沉淀致使碳铵颜色变黑。
H2S带入制碱过程,在碳化时生成难溶的铁硫化合物致使重碱变黑。
在尿素生产过程中,H2S进入尿素合成塔时会生成硫脲——[CS(NH2)2]污染尿素产品,降低产品质量。
(3)对碳酸丙烯酯脱碳操作的危害H2S进入碳酸丙烯酯脱碳系统,于空气汽提过程中生成硫磺,特别是系统中有铁时,能加速H2S氧化成硫的反应。
硫磺附着在液面计上影响液面观察,硫磺、油污和机械杂质结成厚厚的垢层附着在贫液水冷器管子内壁上影响传热,甚至堵塞换热器管。
硫磺沉积在填料表面上还会造成填料堵塞。
(4)对铜洗操作的危害铜氨液吸收H2S生成CuS沉淀,这种沉淀物颗粒很细,悬浮在溶液中导致中导致溶液粘度增大,发泡性增强,铜耗上升,破坏铜洗系统的正常运行。
(5)对金属腐蚀H2S能使碳钢设备及管线发生失重腐蚀,应力腐蚀、氢脆和氢鼓泡,使设备及管线寿命减短。
(6)对人体的毒害H2S是强烈的神经毒,接触人的呼吸道粘膜后,即分解成Na2S,加之本身的酸性对人的呼吸道粘膜有明显的刺激作用。
H2S经呼吸系统进入血液中来不及氧化时就会引起全身中毒反应,随H2S浓度的增加会造成呼吸麻痹、窒息以致停止呼吸而死亡。
3、何谓湿式氧化法脱硫?主要有哪几种?以碱性溶液吸收酸性气体硫化氢,同时选择适当的氧化催化剂,将溶液中被吸收的硫化氢氧化成单体硫,因而使脱硫溶液得到再生,并获得副产品硫磺。
此后,还原态的氧化催化剂可由空气氧化成氧化态再循环使用。
此法采用溶液吸收,且氧化再生是其特点,故将此脱硫方法称为湿式氧化法脱硫。
该法脱硫主要用于半水煤气和变换气脱硫。
目前小合成氨厂常用的湿式氧化法脱硫有:氨水催化法、改良ADA法、栲胶法、PDS法、KCK法、MSQ 法和络合铁法等。
4、氨水催化法脱硫及其主要控制指标是怎样的?氨水催化法采用8~25滴度的氨水,其中加0.2~0.3g/L对苯二酚作催化剂,使溶解于液相的硫化氢氧化为元素硫,其吸收和再生的反应分别为:吸收反应NH3+H2S ==== NH4HS再生反应NH4HS+1/2O2NH3+S+H2O对苯二酚为还原态,其氧化态为对苯二醌。
由于对苯二醌的氧化电位较高(0.699V),因此对苯二酚浓度不能过高,否则容易发生如下副反应,从而影响硫的得率,即2NH4HS+2O2(NH4)2S2O3+H2O本法有氨损失较大的缺点,此外,溶液的硫容量较低,仅为0.1~0.15g/L。
当煤气中硫化氢含量高时,所需的溶液循环量较大,电耗也随之增高。
本法的气体净化度可小于50mg/m3(标)。
主要控制指标:NH3含量度8~25tt对苯二酚含量0.2~0.3g/L悬浮硫含量<0.5g/LH2S含量<0.015g/L(NH4)2S2O3含量<50g/L5、改良ADA法脱硫及其主要控制指标是怎样的?ADA法发展初期,由于析硫过程缓慢,生成硫代硫酸盐较多。
后来发现溶液中添加偏钒酸钠后,使硫氧化速度大为提高,从而形成了现今的改良ADA法。
改良ADA脱硫的主要反应如下。
(1)脱硫塔中的反应以PH8.5~9.2的稀碱液吸收硫化氢生成硫氢化物。
Na2CO3+H2S NaH+NaHCO3硫氢化物与偏钒酸钠反应转化成元素硫:2NaHS+4NaVO3+H2O Na2V4O9+4NaOH+2S氧化态ADA氧化焦性偏钒酸钠生成偏钒酸钠:Na2V4O9+2adA(氧化态)+2NaOH+H2O 4NaVO3+2ADA(还原态)(2)再生过程中的反应还原态ADA被空气中的氧氧化成氧化态,然后溶液用泵送入吸收塔循环使用。
2ADA(还原态)+O22ADA(氧化态)+2H2O改良ADA溶液组分中,碳酸钠(Na2CO3)作吸收介质,ADA为析硫的载气体,偏钒酸盐为ADA析硫过程的催化剂,溶液中加入酒石酸钾钠的目的在于稳定溶液中的钒,防止生成“钒-氧-硫”复合物沉淀。
改良ADA法是技术成熟、过程规范程度高、溶液性能稳定、技术经济指标较好的脱硫方法。
该方法还具有硫磺回收率高,回收的硫磺纯度高,溶液对人和生物无毒害作用,对碳钢无腐蚀作用等优点。
国内改良ADA法脱硫遇到的最大问题是易发生硫磺堵塞脱硫塔内的填料。
主要控制指标:总碱度0.4NPH值8.5~9.2ADA 3~5g/LNaVO3 1~2g/LKnaC4H4O6 1g/L吸收温度15~400C6、栲胶法脱硫及其主要控制指标是怎样的?栲胶是聚酚类(丹宁)物质,可代替ADA作载氧体,价格低廉,且栲胶本身还是良好的钒铬合剂,不需添置加酒石酸钾钠等络合剂。
此法的吸收效果与ADA相近,且具有不容易堵塞脱硫塔填料、栲胶资源丰富、价格便宜等优点。
但配制脱硫液和往系统中补加栲胶时都要经过加热溶化制备过程。
主要控制指标:总碱度0.4NPH值8.5~9.0栲胶含量1~2g/LNaVO3含量1~1.5g/L吸收温度30~400C再生温度35~450C喷射器脱硫液压力0.2~0.3MPa7、PDS法脱硫及其主要控制指标是怎样的?PDS是肽莆钴酸盐系化合物的混合物,它具有较高的催化活性。
PDS脱硫与其他各种湿式氧化法脱硫具有相同的生产工艺,因此由ADA法或栲胶法改为PDS脱硫不需要更改原有工艺,只是以PDS代替脱硫液中ADA或栲胶即可。
PDS的催化活性好,用量少,消耗低。
溶液再生时生成硫泡沫的硫晶体粒子大,易于分离,故脱硫液中的悬浮硫含量较低。
该方法不仅脱除无机硫,对有机硫也有很好的脱除效果。
PDS对人体无毒害作用,脱硫液对设备基本无腐蚀。
PDS的加入方式是一个很重要、关系成败的问题。
由于脱硫液中PDS含量特低,且容易被硫泡沫带走损失掉,若集中加入,将导致PDS未参加反应就被泡沫带出系统且损失多,所以须采用24小时连续滴加方式加入。
主要控制指标:总碱度0.4NPH值8~8.5PDS含量约~3mg/kg脱硫温度20~400C再生温度25~450C吸收液气比8~11L/m38、湿式氧化法脱硫的工艺流程一般是怎样的?湿式氧化法脱硫的工艺流程如图3-1所示。
来自造气工段的半水煤气,经焦炭过滤器除去所含的部分粉尘、煤焦油杂质后,由罗茨风机增压送入气体冷却塔冷却,然后进入脱硫塔与贫液接触吸收,半水煤气中的硫化氢被贫液吸收。
脱硫后的半水煤气从脱硫塔出来,经清洗塔洗去所带杂质后,再经静电除焦油塔进一步除去焦油等杂质后,去压缩工段一段进口总水分离器。
吸收了硫化氢的富液流入富液槽,由富液泵打入喷射再生槽的喷射器,与喷射吸入的空气进行氧化反应。
氧化反应后的溶液再进入再生硫泡沫浮选槽继续氧化再生,并浮选出硫泡沫。
再生后的贫液经液位调节器流入贫液槽,再由贫液泵打入脱硫塔循环使用。
富液在再生槽中氧化再生所析出的硫泡沫,由槽顶溢流入硫泡沫槽,再经离心机分离得硫膏,硫膏放入熔硫釜用蒸汽间接加热,经熔融精制,制成硫锭。
分离得到的母液可直接放入贫液槽,循环使用。
连续熔硫釜工艺流程为硫泡沫从浮选再生槽上部溢流回收至硫泡沫槽,再用泵将硫泡沫打至连续熔硫釜。
在熔硫釜内,硫泡沫经夹套蒸汽加热后温度由上而下逐渐升高至1400C左右,熔融态硫膏由底部放硫阀排出至硫磺回收盆,冷却后即成硫锭产品。
硫泡沫夹带的脱硫液由上部溢流至回收槽,再回流至贫液槽,继续作脱硫循环作用。
9、湿式氧化法脱硫的正常操作要点有哪些?湿式氧化法脱硫操作中应掌握以下要点:(1)保证脱硫液质量。
①根据脱硫液成分,及时补加氨(或碳酸钠)及其他催化剂,保证脱硫液成分符合工艺指标。
②保证喷射再生器进口的富液压力,稳定自吸空气量,控制好再生温度,使富液氧化再生完全。
并保持再生槽液面上的硫泡沫溢流正常,降低脱硫液中的悬浮硫含量。
保证脱硫液质量。
(2)保证半水煤气脱硫效果。
根据半水煤气的气量及硫化氢含量的变化,及时调节液气比。
当半水煤气硫化氢含量增高时,如增大液气比仍不能保证脱硫效率,可适当提高脱硫液中氨(或碳酸钠)和其他脱硫剂的含量,或通知造气改烧低硫煤。
(3)严防气柜抽瘪以及机、泵抽负压、抽空。
①经常注意气柜高度变化,当高率降至低限位置时,应立即与压缩工段联系减量生产,防止气柜抽瘪。