挤出成型工艺参数包括温度
peek挤出造粒参数

peek挤出造粒参数
PEEK的挤出造粒参数主要包括以下几点:
1. 温度控制:根据原料和产品的不同,温度设置在230°C\~370°C之间。
2. 螺杆转速:螺杆转速通常在100\~150rpm之间,但具体转速应视产品
要求和设备性能而定。
3. 模头温度:模头温度对产品的成型质量和外观影响较大,一般设置在270°C\~300°C之间。
4. 牵引速度:牵引速度决定了产品的厚度和生产效率,通常在
20\~50m/min之间。
5. 收卷张力:收卷张力决定了产品的致密度和平整度,通常在2\~8kg之间。
6. 添加剂使用:根据需要,可以添加一定比例的增强剂、阻燃剂、抗菌剂等添加剂。
7. 冷却时间:冷却时间对产品的性能和生产效率有影响,一般冷却时间在
10\~30秒之间。
8. 切割长度:根据需要,可以设定不同的切割长度,切割长度一般在
10\~30mm之间。
9. 供料速度:供料速度决定了挤出机的生产效率,供料速度在
30\~120r/min之间。
10. 设备配置:根据生产需要,可以选择不同配置的挤出机、切粒机、干燥机等设备。
请注意,这些参数不是固定的,具体需要根据设备性能、产品要求以及生产环境等因素进行调整。
同时,还需要注意安全操作规程,确保生产过程中的安全。
EVA加工成型工艺条件

EVA加工成型工艺条件
(1)注射成型工艺
机器活塞或螺杆式均可
机筒温度120度~180度
模具温度20度~40度
注射压力60MPa (随不一样型号EVA而变)
成型周期40~70S
树脂温度185度~195度
(2)挤出成型工艺(片材)
机器通用∲65μm挤出机
机筒温度110度~145度
机头温度130度~145度
牵引辊温度30度~60度
冷却辊温度30度~40度
(3)中空成型工艺(以∲40μm螺杆挤出机中空成型条件)机筒温度分三段为 100度 130度 140度
机头温度140度
模具温度20度~25度
树脂温度150度
压缩空气力400~500kPa
闭模压力2.5~3MPa
冷却加热吹塑时间25S(25r/min转速时挤出量80-90g/min)
EVA|V6110M
生产企业:扬子巴斯夫规格用途
技术参数。
塑料异型材挤出工艺参数设定、控制依据与标准

塑料异型材挤出工艺参数设定、控制依据与标准绪言塑料异型材是在挤出机一定温度和螺杆摩擦、压延、剪切作用下均衡塑化加工成型的。
挤出机各项工艺参数,即挤出温度,螺杆温度,给料速度,挤出速度,牵引速度,熔体压力,扭矩,口模熔压,型材密实度,口模与定型模真空度,定型冷却温度,牵引压力等项参数技术指标的设定和控制对挤出型材塑化的外观和内在质量十分重要。
正确设定和控制以上工艺参数是每一个型材生产操作者应具备的技术技能。
现根据笔者十几年工作经验,将以什么为基准,正确设定和控制各项工艺参数以及出现一些非常情况的应对措施,谈一点自已的看法和意见,与行业各位行家交流,共勉,以共同促进塑料异型材质量水平提高。
不当之处请批评、指正。
塑料异型材工艺参数设定和控制依据与标准1、挤出温度的设定和控制由于PVC-U物料对温度比较敏感,塑料异型材挤出成型是在塑化温度和降解温度之间相对狭窄的温度区域进行的。
因锥形双螺杆机挤出型材供物料塑化,并抑制物料降解,分别对应有两个热源与冷源:一个热源是电加热圈提供给机筒的外热。
外热温控系统大致由10个温控点组成。
依据物料在挤出过程各个阶段的形态,承担热量供应工作。
因此可归纳为加温、恒温、保温三个区域。
其中加温与恒温区主要在挤出机内进行,以排气孔为界划分为两个相对独立又互为关联的部分。
所供热量由仪表电器进行控制。
依据挤出型材工艺要求,设定温度值,启动机筒各段电加热圈工作,当机筒加热达到设定温度值时,则通过温度传感器给模块数据,自动切断加热电源,加热停止,此时螺筒处于保温状态;当显示温度达不到设定温度指标参数时,加热圈就一直不间断工作。
另一个热源是由螺筒和螺杆产生的摩擦、压延、剪切热(简称剪切热),是不能自控的,主要由给料速度和螺杆结构形式所决定;一个冷源是安装在螺筒熔融段与计量段位置上的风机实施的。
当螺筒加热时,风机不工作,当显示温度达到或超过设定温度指标参数,螺筒加热圈加热停止的同时,温控系统自动启动冷却风机,进行强制冷却;另一个冷源是螺杆内部调温装置,通过预先设定一个温度指标,启动螺杆芯温电机、调温装置的加热器对油箱导热介质(硅油)加热,当螺杆物料温度高于设定温度时,通过温度控制元件控制水冷却装置对油箱内导热介质(硅油)进行冷却。
挤出成型工艺参数包括温度

挤出成型工艺参数包括温度、压力、挤出速率和牵引速度等。
1. 温度温度是挤出成型得以顺利进行的重要条件之一。
从粉状或粒状的固态物料开始,高温制品从机头中挤出,经历了一个复杂的温度变化过程。
严格来讲,挤出成型温度应指塑料熔体的温度,但该温度却在很大程度上取决于料筒和螺杆的温度,一小部分来自在料筒中混合时产生的摩擦热,所以经常用料筒温度近似表示成型温度。
由于料筒和塑料温度在螺杆各段是有差异的,为了使塑料在料筒中输送、熔融、均化和挤出的过程顺利进行,以便高效率地生产高质量制件,关键问题是控制好料筒各段温度,料筒温度的调节是靠挤出机的加热冷却系统和温度控制系统来实现的。
机头温度必须控制在塑料热分解温度以下,而口模处的温度可比机头温度稍低一些,但应保证塑料熔体具有良好的流动性。
此外,成型过程中温度的波动和温差,将使塑件产生残余应力、各点强度不均匀和表面灰暗无光泽等缺陷。
产生这种波动和温差的因素很多,如加热、冷却系统不稳定,螺杆转速变化等,但以螺杆设计和选用的好坏影响最大。
表9-1是几种塑料挤出成型管材、片材和板材及薄膜等的温度参数。
2. 压力在挤出过程中,由于料流的阻力,螺杆槽深度的变化,以及过滤网、过滤板和口模等产生阻碍,因而沿料筒轴线方向,在塑料内部产生一定的压力。
这种压力是塑料变为均匀熔体并得到致密塑件的重要条件之一。
增加机头压力可以提高挤出熔体的混合均匀性和稳定性,提高产品致密度,但机头压力过大将影响产量。
和温度一样,压力随时间的变化也会产生周期性波动,这种波动对塑件质量同样有不利影响,螺杆转速的变化,加热、冷却系统的不稳定都是产生压力波动的原因。
为了减少压力波动,应合理控制螺杆转速,保证加热和冷却装置的温度控制精度。
3. 挤出速率挤出速率(亦称挤出速度)是单位时间内挤出机口模挤出的塑料质量(单位为kg/h)或长度(单位为m/min)。
挤出速度的大小表征着挤出生产能力的高低。
影响挤出速度的因素很多,如机头、螺杆和料筒的结构、螺杆转速、加热冷却系统结构和塑料的特性等。
挤出成型工艺参数包括
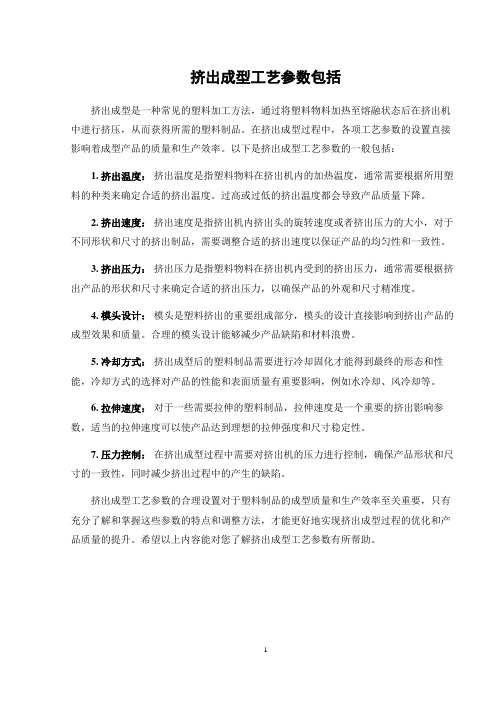
挤出成型工艺参数包括挤出成型是一种常见的塑料加工方法,通过将塑料物料加热至熔融状态后在挤出机中进行挤压,从而获得所需的塑料制品。
在挤出成型过程中,各项工艺参数的设置直接影响着成型产品的质量和生产效率。
以下是挤出成型工艺参数的一般包括:1. 挤出温度:挤出温度是指塑料物料在挤出机内的加热温度,通常需要根据所用塑料的种类来确定合适的挤出温度。
过高或过低的挤出温度都会导致产品质量下降。
2. 挤出速度:挤出速度是指挤出机内挤出头的旋转速度或者挤出压力的大小,对于不同形状和尺寸的挤出制品,需要调整合适的挤出速度以保证产品的均匀性和一致性。
3. 挤出压力:挤出压力是指塑料物料在挤出机内受到的挤出压力,通常需要根据挤出产品的形状和尺寸来确定合适的挤出压力,以确保产品的外观和尺寸精准度。
4. 模头设计:模头是塑料挤出的重要组成部分,模头的设计直接影响到挤出产品的成型效果和质量。
合理的模头设计能够减少产品缺陷和材料浪费。
5. 冷却方式:挤出成型后的塑料制品需要进行冷却固化才能得到最终的形态和性能,冷却方式的选择对产品的性能和表面质量有重要影响,例如水冷却、风冷却等。
6. 拉伸速度:对于一些需要拉伸的塑料制品,拉伸速度是一个重要的挤出影响参数,适当的拉伸速度可以使产品达到理想的拉伸强度和尺寸稳定性。
7. 压力控制:在挤出成型过程中需要对挤出机的压力进行控制,确保产品形状和尺寸的一致性,同时减少挤出过程中的产生的缺陷。
挤出成型工艺参数的合理设置对于塑料制品的成型质量和生产效率至关重要,只有充分了解和掌握这些参数的特点和调整方法,才能更好地实现挤出成型过程的优化和产品质量的提升。
希望以上内容能对您了解挤出成型工艺参数有所帮助。
1。
塑料成型工艺与模具设计考试复习题4

试卷二答案一、填空题1.在注射成型中应控制合理的温度,即控制料筒、喷嘴和模具温度。
2.根据塑料的特性和使用要求,塑件需进行塑后处理,常进行退火和调质处理。
3.塑料模具的组成零件按其用途可以分为成型零件与结构零件两大类。
4.在注射成型时为了便于塑件的脱模,在一般情况下,使塑件在开模时留在动模上。
5.塑料一般是由树脂和添加剂组成。
6.塑料注射模主要用来成型热塑性塑料件。
压缩成型主要用来成型热固性塑料件。
7.排气是塑件成型的需要,引气是塑件脱模的需要。
8.注射模的浇注系统有主流道、分流道、浇口、冷料穴等组成。
9.凹模其形式有整体式和组合式两种类型。
10.导向机构的形式主要有导柱导向和锥面定位两种。
11.树脂分为天然树脂和合成树脂。
12.注射模塑最主要的工艺条件,即“三要素”是压力、时间和温度。
一、填空题1.从尽量减少散热面积考虑,热塑性塑料注射模分流道宜采用的断面形状是圆形。
2. 塑料的主要成份有树脂、填充剂、增塑剂、着色剂、润滑剂、稳定剂。
3.热固性塑料压缩模用来成型压缩率高的塑料,而用纤维填料的塑料宜用不溢式压缩模具。
4.塑料按性能及用途可分为通用塑料、工程塑料、增强塑料。
5.热固性塑料的工艺性能有:收缩性、流动性、压缩率、水分与挥化物含量、固化特性。
6.塑料的加工温度区间应该为粘流态温度与分解温度之间。
热固性塑料的工艺性能有:收缩性、流动性、压缩率、水分与挥化物含量、固化特性。
7.对大型塑件尺寸精度影响最大的因素是成型收缩率误差。
8. 塑料在变化的过程中出现三种但却不同的物理状态:玻璃态、高弹态、粘流态。
9. 牛顿型流体包括粘性流体、粘弹性流体和时间依赖性流体。
10. 从成型工艺出发,欲获得理想的粘度,主要取决于对温度、剪切速率和压力这三个条件的合理选择和控制。
11. 料流方向取决于料流进入型腔的位置,故在型腔一定时影响分子定向方向的因素是浇口位置。
.8. 注射模塑工艺包括成型前的准备、注射、后处理等工作。
挤出成型工艺参数有哪些

挤出成型工艺参数有哪些
挤出成型是一种常见的塑料加工工艺,通过加热和压力使塑料颗粒在挤出机中经过螺杆挤出,最终成型为所需的产品。
在挤出成型过程中,需要根据不同的塑料材料和成型要求来调整一系列工艺参数,以确保最终产品的质量和性能。
首先,挤出成型工艺参数中最重要的是挤出温度。
挤出温度是指挤出机不同部位的温度设置,通常包括料筒温度、模头温度和模具温度。
不同类型的塑料材料需要在不同的温度下进行挤出,过高或过低的温度都会影响挤出成型的效果,甚至导致产品质量问题。
其次,挤出速度也是一个至关重要的参数。
挤出速度取决于螺杆的旋转速度以及料筒的进料速度,控制好挤出速度可以有效地控制产品的尺寸和表面光洁度。
过快的挤出速度可能导致产生内部应力过大,从而影响产品的外观和力学性能。
除了温度和速度外,压力也是挤出成型中不可忽视的参数之一。
合理的挤出压力可以保证塑料材料充分填充模腔,避免产生气泡和瑕疵,并且有利于产品的密实性和强度。
同时,压力的大小也要根据产品形状和尺寸的不同做出相应的调整,以求达到最佳的成型效果。
此外,挤出成型还需考虑挤出机的螺杆转速、冷却方式、模具结构等参数。
螺杆转速的选择直接影响塑料材料的挤出速度和均匀性,冷却方式则关系到产品的收缩率和外观质量,模具结构的设计要符合产品的形状和尺寸需求,以确保最终产品达到设计要求。
综上所述,挤出成型工艺参数多种多样,需要综合考虑材料特性、产品要求和设备性能等因素,通过合理的调整和控制来实现挤出成型过程中的稳定性和高效性,从而生产出优质的塑料制品。
1。
挤出成型的工艺参数有哪些
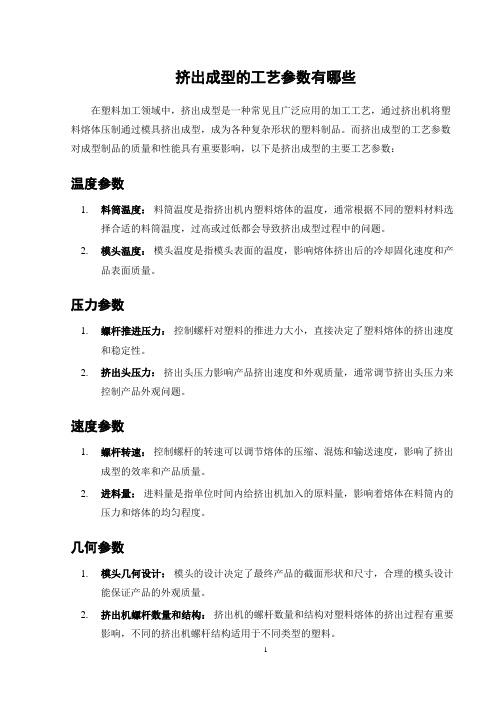
挤出成型的工艺参数有哪些在塑料加工领域中,挤出成型是一种常见且广泛应用的加工工艺,通过挤出机将塑料熔体压制通过模具挤出成型,成为各种复杂形状的塑料制品。
而挤出成型的工艺参数对成型制品的质量和性能具有重要影响,以下是挤出成型的主要工艺参数:温度参数1.料筒温度:料筒温度是指挤出机内塑料熔体的温度,通常根据不同的塑料材料选择合适的料筒温度,过高或过低都会导致挤出成型过程中的问题。
2.模头温度:模头温度是指模头表面的温度,影响熔体挤出后的冷却固化速度和产品表面质量。
压力参数1.螺杆推进压力:控制螺杆对塑料的推进力大小,直接决定了塑料熔体的挤出速度和稳定性。
2.挤出头压力:挤出头压力影响产品挤出速度和外观质量,通常调节挤出头压力来控制产品外观问题。
速度参数1.螺杆转速:控制螺杆的转速可以调节熔体的压缩、混炼和输送速度,影响了挤出成型的效率和产品质量。
2.进料量:进料量是指单位时间内给挤出机加入的原料量,影响着熔体在料筒内的压力和熔体的均匀程度。
几何参数1.模头几何设计:模头的设计决定了最终产品的截面形状和尺寸,合理的模头设计能保证产品的外观质量。
2.挤出机螺杆数量和结构:挤出机的螺杆数量和结构对塑料熔体的挤出过程有重要影响,不同的挤出机螺杆结构适用于不同类型的塑料。
其他参数1.冷却参数:产品挤出后需要经过冷却固化阶段,控制冷却方式和速度对产品的成型完整性和尺寸稳定性具有重要作用。
2.模具温度:模具温度对产品的收缩率和表面质量有直接影响,适当调节模具温度能够改善产品的表面光滑度和尺寸精度。
以上便是挤出成型的主要工艺参数,通过对这些参数的合理控制和调节,可以提高挤出成型制品的质量稳定性和生产效率,从而满足不同行业对塑料制品的需求。
- 1、下载文档前请自行甄别文档内容的完整性,平台不提供额外的编辑、内容补充、找答案等附加服务。
- 2、"仅部分预览"的文档,不可在线预览部分如存在完整性等问题,可反馈申请退款(可完整预览的文档不适用该条件!)。
- 3、如文档侵犯您的权益,请联系客服反馈,我们会尽快为您处理(人工客服工作时间:9:00-18:30)。
挤出成型工艺参数包括温度、压力、挤出速率和牵引速度等。
1. 温度
温度是挤出成型得以顺利进行的重要条件之一。
从粉状或粒状的固态物料开始,高温制品从机头中挤出,经历了一个复杂的温度变化过程。
严格来讲,挤出成型温度应指塑料熔体的温度,但该温度却在很大程度上取决于料筒和螺杆的温度,一小部分来自在料筒中混合时产生的摩擦热,所以经常用料筒温度近似表示成型温度。
由于料筒和塑料温度在螺杆各段是有差异的,为了使塑料在料筒中输送、熔融、均化和挤出的过程顺利进行,以便高效率地生产高质量制件,关键问题是控制好料筒各段温度,料筒温度的调节是靠挤出机的加热冷却系统和温度控制系统来实现的。
机头温度必须控制在塑料热分解温度以下,而口模处的温度可比机头温度稍低一些,但应保证塑料熔体具有良好的流动性。
此外,成型过程中温度的波动和温差,将使塑件产生残余应力、各点强度不均匀和表面灰暗无光泽等缺陷。
产生这种波动和温差的因素很多,如加热、冷却系统不稳定,螺杆转速变化等,但以螺杆设计和选用的好坏影响最大。
表9-1是几种塑料挤出成型管材、片材和板材及薄膜等的温度参数。
2. 压力
在挤出过程中,由于料流的阻力,螺杆槽深度的变化,以及过滤网、过滤板和口模等产生阻碍,因而沿料筒轴线方向,在塑料内部产生一定的压力。
这种压力是塑料变为均匀熔体并得到致密塑件的重要条件之一。
增加机头压力可以提高挤出熔体的混合均匀性和稳定性,提高产品致密度,但机头压力过大将影响产量。
和温度一样,压力随时间的变化也会产生周期性波动,这种波动对塑件质量同样有不利影响,螺杆转速的变化,加热、冷却系统的不稳定都是产生压力波动的原因。
为了减少压力波动,应合理控制螺杆转速,保证加热和冷却装置的温度控制精度。
3. 挤出速率
挤出速率(亦称挤出速度)是单位时间内挤出机口模挤出的塑料质量(单位为kg/h)或长度(单位为m/min)。
挤出速度的大小表征着挤出生产能力的高低。
影响挤出速度的因素很多,如机头、螺杆和料筒的结构、螺杆转速、加热冷却系统结构和塑料的特性等。
理论和实践都证明,挤出速率随螺杆直径、螺旋槽深度、均化段长度和螺杆转速的增大而增大,随螺杆末端熔体压力和螺杆与料筒间隙增大而增大。
在挤出机的结构和塑料品种及塑件类型已确定的情况下,挤出速率仅与螺杆转速有关,因此,调整螺杆转速是控制挤出速率的主要措施。
挤出速率在生产过程中也存在波动现象,这将影响塑件的几何形状和尺寸精度。
因此,除了正确确定螺杆结构和尺寸参数之外,还应严格控制螺杆转速,严格控制挤出温度,防止因温度改变而引起挤出压力和熔体粘度变化,从而导致挤出速度的波动。
Welcome To Download
欢迎您的下载,资料仅供参考!。