能量系统优化典型技术—界面技术
综合能源系统效能优化技术
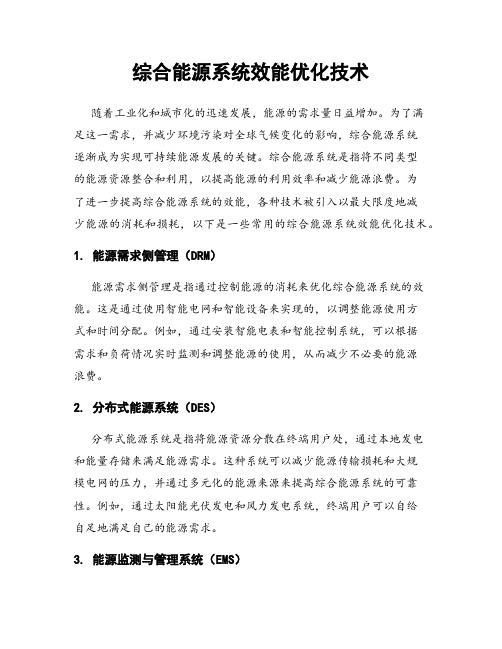
综合能源系统效能优化技术随着工业化和城市化的迅速发展,能源的需求量日益增加。
为了满足这一需求,并减少环境污染对全球气候变化的影响,综合能源系统逐渐成为实现可持续能源发展的关键。
综合能源系统是指将不同类型的能源资源整合和利用,以提高能源的利用效率和减少能源浪费。
为了进一步提高综合能源系统的效能,各种技术被引入以最大限度地减少能源的消耗和损耗,以下是一些常用的综合能源系统效能优化技术。
1. 能源需求侧管理(DRM)能源需求侧管理是指通过控制能源的消耗来优化综合能源系统的效能。
这是通过使用智能电网和智能设备来实现的,以调整能源使用方式和时间分配。
例如,通过安装智能电表和智能控制系统,可以根据需求和负荷情况实时监测和调整能源的使用,从而减少不必要的能源浪费。
2. 分布式能源系统(DES)分布式能源系统是指将能源资源分散在终端用户处,通过本地发电和能量存储来满足能源需求。
这种系统可以减少能源传输损耗和大规模电网的压力,并通过多元化的能源来源来提高综合能源系统的可靠性。
例如,通过太阳能光伏发电和风力发电系统,终端用户可以自给自足地满足自己的能源需求。
3. 能源监测与管理系统(EMS)能源监测与管理系统是一种集成的软硬件系统,用于实时监测和管理综合能源系统的性能和效能。
通过使用传感器、数据采集设备和分析软件,EMS可以提供准确的能源使用数据和综合分析,帮助运营者实时调整能源供应和需求,以优化综合能源系统的效能。
此外,EMS还可以提供预测和智能控制功能,以便根据未来的需求和条件进行能源管理决策。
4. 能量回收与利用技术能量回收和利用技术是指将综合能源系统中产生的废热、废气和废水等能量资源进行回收和再利用。
例如,在工业生产过程中,可以使用热交换器将废热转化为其他形式的能量,用于供暖、供电或供水等用途。
这样一来,不仅减少了能源的浪费,还提高了综合能源系统的整体效能。
5. 智能优化算法智能优化算法是一种基于人工智能的技术,用于优化综合能源系统的运行和管理。
高能量密度电池材料的研究与应用

高能量密度电池材料的研究与应用电池的发明和应用已经有上百年的历史了。
电池的作用是将化学能转化为电能,但传统的电池在储能密度和电容上受到严重的限制。
随着科学技术的不断发展,高能量密度电池的研究逐渐成为新的热点,为未来的能源储存和利用发挥出重要的作用。
一、理论基础电池的储电方式是通过电特性进行储存的。
由于电荷的特性,在两端之间建立的电荷的差异能够作为电能存储。
同时,制造电池时要选择适当的电解液和电极材料,为电池储能的性能和效率提供保障。
高能量密度电池的研究主要是从材料的角度来考虑,如何材料的结构、成分、状态等影响了电池的性能,如何优化电池材料,以提高电池的储能密度和电容值。
二、新型高能量密度电池材料1.锂离子电池材料锂离子电池已经成为目前最广泛应用的新能源电池,锂离子电池材料的研究是高能量密度电池材料下一个重要方面。
在锂离子电池的正极材料中,常用的有钴酸锂、镍酸锂、三元材料、钛酸锂等材料。
其中,钴酸锂具有较高的容量,但是价格昂贵,资源稀缺;镍酸锂容量较大,但是容易氧化,容易损坏;三元材料相较于前两者具有更高的安全性和稳定性,但是容量较小;钛酸锂具有较高的安全性,但是其容量还不足以满足现代电动汽车的应用。
因此,研究者需要对这些材料进行深入分析,优化材料的结构和性能,提高材料的储能容量和安全性能。
2.锂硫电池材料锂硫电池具有较高的理论储能密度,未来广泛应用的领域之一。
但是,在其实际应用过程中,出现了电解液易揮发、充电轻松损耗、硫化物渗透加重循环寿命缺陷等问题。
目前的研究主要是尝试寻找新型电解液,增强电解液的化学稳定性,同时优化锂硫电池的电极材料,为锂硫电池的生产和应用提供支撑和保障。
3.其他电池材料除了锂离子电池和锂硫电池,锂空气电池、钠离子电池、铁离子电池等也是研究的热门。
各类电池材料的研究都是为了寻找更高储能量和电容量的新型电池。
铁离子电池具有良好的安全性和环保性,现已被广泛应用于新能源领域。
钠离子电池则是因为钠货源丰富而备受瞩目。
新能源汽车动力系统的优化与节能技术
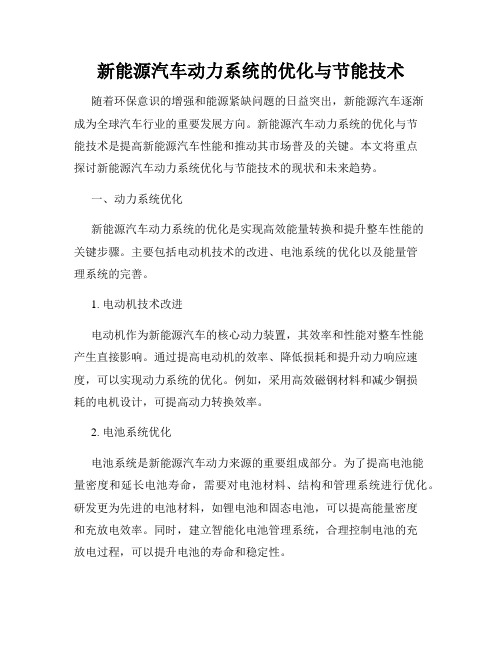
新能源汽车动力系统的优化与节能技术随着环保意识的增强和能源紧缺问题的日益突出,新能源汽车逐渐成为全球汽车行业的重要发展方向。
新能源汽车动力系统的优化与节能技术是提高新能源汽车性能和推动其市场普及的关键。
本文将重点探讨新能源汽车动力系统优化与节能技术的现状和未来趋势。
一、动力系统优化新能源汽车动力系统的优化是实现高效能量转换和提升整车性能的关键步骤。
主要包括电动机技术的改进、电池系统的优化以及能量管理系统的完善。
1. 电动机技术改进电动机作为新能源汽车的核心动力装置,其效率和性能对整车性能产生直接影响。
通过提高电动机的效率、降低损耗和提升动力响应速度,可以实现动力系统的优化。
例如,采用高效磁钢材料和减少铜损耗的电机设计,可提高动力转换效率。
2. 电池系统优化电池系统是新能源汽车动力来源的重要组成部分。
为了提高电池能量密度和延长电池寿命,需要对电池材料、结构和管理系统进行优化。
研发更为先进的电池材料,如锂电池和固态电池,可以提高能量密度和充放电效率。
同时,建立智能化电池管理系统,合理控制电池的充放电过程,可以提升电池的寿命和稳定性。
3. 能量管理系统完善新能源汽车的能量管理系统是整个动力系统的大脑,通过智能化控制和协调各个子系统的运行,实现能量的高效利用。
通过优化能量管理算法和控制策略,可以最大程度地提高能量转化效率和减少能量损耗。
例如,采用智能预测控制策略,根据驾驶条件和路线规划,合理分配动力输出和能量回收,进一步提高新能源汽车的续航里程。
二、节能技术应用除了动力系统的优化,新能源汽车的节能技术应用也是提高能源利用效率和降低污染排放的关键。
主要包括车身轻量化技术、动力总成能量回收利用以及智能能源管理系统的应用等。
1. 车身轻量化技术采用轻量化材料和优化设计,降低车身重量是提高新能源汽车能效的重要手段。
例如,使用高强度钢材、铝合金和碳纤维等轻量化材料,可以减轻车身质量,并优化车身结构,提高整车刚度和安全性。
利用热力学技术实现碳减排目标
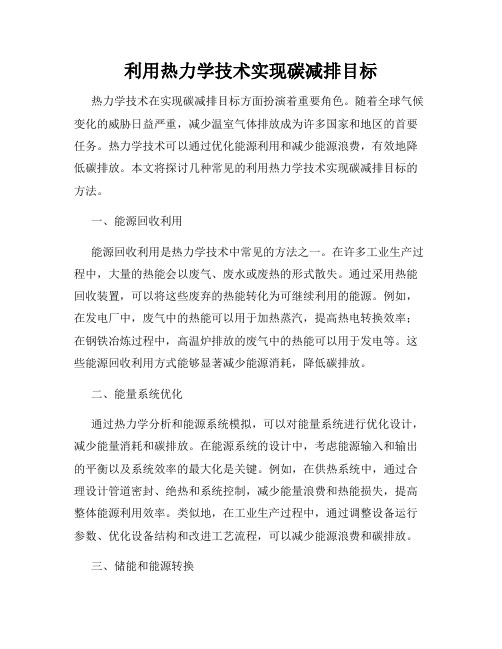
利用热力学技术实现碳减排目标热力学技术在实现碳减排目标方面扮演着重要角色。
随着全球气候变化的威胁日益严重,减少温室气体排放成为许多国家和地区的首要任务。
热力学技术可以通过优化能源利用和减少能源浪费,有效地降低碳排放。
本文将探讨几种常见的利用热力学技术实现碳减排目标的方法。
一、能源回收利用能源回收利用是热力学技术中常见的方法之一。
在许多工业生产过程中,大量的热能会以废气、废水或废热的形式散失。
通过采用热能回收装置,可以将这些废弃的热能转化为可继续利用的能源。
例如,在发电厂中,废气中的热能可以用于加热蒸汽,提高热电转换效率;在钢铁冶炼过程中,高温炉排放的废气中的热能可以用于发电等。
这些能源回收利用方式能够显著减少能源消耗,降低碳排放。
二、能量系统优化通过热力学分析和能源系统模拟,可以对能量系统进行优化设计,减少能量消耗和碳排放。
在能源系统的设计中,考虑能源输入和输出的平衡以及系统效率的最大化是关键。
例如,在供热系统中,通过合理设计管道密封、绝热和系统控制,减少能量浪费和热能损失,提高整体能源利用效率。
类似地,在工业生产过程中,通过调整设备运行参数、优化设备结构和改进工艺流程,可以减少能源浪费和碳排放。
三、储能和能源转换热力学技术还可以用于能源储存和转换,进一步实现碳减排目标。
在可再生能源领域,储能是一个重要的挑战。
通过热能储存技术,可以将可再生能源转化为可供随时使用的能源。
例如,热储能技术中的相变材料可以在过剩能量时储存热能,在需求高峰时释放热能,以平衡供需之间的差异。
这种储能技术能够提高可再生能源的利用率,减少碳排放。
四、碳捕获和碳利用碳捕获和碳利用是实施碳减排目标的关键措施之一。
热力学技术可以用于碳捕获过程中的能量优化和效率提升。
例如,利用吸收剂捕获工业废气中的二氧化碳,通过控制吸收剂的温度和压力,可以提高碳捕获过程的能效。
此外,热力学技术还可以在碳利用过程中发挥重要作用。
通过高温反应和催化剂,将碳从废气中分离出来,并转化为烃类化合物或有机物,可以实现碳资源的再利用。
新能源汽车动力系统的能量管理与优化

新能源汽车动力系统的能量管理与优化随着汽车产业的发展,新能源汽车逐渐成为了人们关注的热点。
新能源汽车动力系统是其核心技术,而能量管理与优化是保证动力系统高效运行的关键。
本文将探讨新能源汽车动力系统的能量管理与优化方法。
一、能量管理的重要性能量管理是指对动力系统中各种能源的分配与调控,以达到最佳的能源利用效率。
新能源汽车使用的能源主要包括电能、化学能等,而能量管理的优化可以提高动力系统的续航里程、减少能源的浪费等。
因此,能量管理的重要性不言而喻。
二、能量管理策略1. 车辆动力需求预测在能量管理过程中,车辆动力需求预测是关键的一步。
通过对路况、驾驶行为等进行分析,可以准确预测车辆未来的动力需求,从而合理分配能源,提高能源利用效率。
2. 能量分配与调控基于车辆动力需求的预测,可以对动力系统中的能源进行合理的分配与调控。
例如,可以根据路况的不同,调整电动机的输出功率,并合理利用动力系统中的能量储存装置,如电池、超级电容器等,实现能量的高效利用。
3. 能量回收与再利用在新能源汽车中,能量回收与再利用是一种重要的节能策略。
通过对制动过程中释放的能量进行回收,再利用于电池充电等方面,可以有效提高能源的利用效率,延长续航里程。
三、能量优化技术1. 充电策略优化充电是新能源汽车中重要的能量补充方式。
通过优化充电策略,可以提高充电效率,减少充电时间,进而提高整个动力系统的能量利用率。
2. 能量损耗降低动力系统中存在一定的能量损耗,如电池、电驱动器等的能量转换效率不是很高。
因此,通过优化设备的设计和使用,减少能量损耗,可以提高整个系统的能量利用效率。
3. 车辆重量控制车辆重量对能源消耗有着直接的影响。
通过采用轻量化材料、优化车辆结构等手段,可以减轻车辆重量,降低能源的消耗,提高能源的利用效率。
四、新能源汽车动力系统的挑战与未来发展虽然新能源汽车动力系统在能量管理和优化方面取得了很大的进步,但仍面临一些挑战。
例如,充电基础设施不完善、电池技术有待改进等。
热力学系统与界面

热力学系统与界面热力学系统与界面是研究能量传递和物质交换的重要领域。
热力学系统是由一定物质组成的物理系统,它可以通过与外界发生能量交换和物质交换来实现动态平衡。
界面是系统内部不同物质或相的分界面,它具有特殊的物理和化学性质。
本文将重点探讨热力学系统与界面之间的相互作用以及相关的研究进展。
一、热力学系统与界面的相互作用热力学系统与界面之间存在着相互作用,界面会对系统的热力学性质产生影响,同时系统的物理性质也会影响界面的行为。
在这个相互作用过程中,热力学的基本规律得到了广泛应用。
1. 界面的表面能和曲率效应界面的表面能是指单位面积上界面所含的自由能。
表面能的大小与界面的物理性质及其周围物质的性质有关。
例如,液体表面存在着相对较高的表面能,这使得液体呈现出比较封闭的形状和特性。
曲率效应是指当界面发生弯曲时,由于曲率不同导致的表面能变化。
这种变化会对界面的稳定性和相平衡产生重要影响。
2. 界面的表面张力表面张力是指液体表面处的分子间相互作用力导致的张力。
表面张力使得液体表面具有一定的弹性和压力差,从而影响界面物质交换和能量传递的速率。
例如,液滴在空气中的形状可以通过表面张力来解释。
表面张力也是液体能够在毛细管中上升或下降的基础。
3. 系统与界面的传质行为热力学系统与界面之间的物质传输是界面科学的重要研究内容之一。
界面的渗透性决定了物质能否通过界面进入或离开系统。
界面上存在着传质的速率,这与物质的浓度梯度、界面本身的特性以及传质物质的性质有关。
传质行为不仅仅发生在液体-气体界面,还发生在液体-液体、固体-气体和固体-液体等多种界面上。
二、研究热力学系统与界面的方法与技术为了深入研究热力学系统与界面之间的相互作用,科学家们开发出了许多方法和技术。
这些方法和技术能够帮助我们揭示热力学系统在界面上的行为和变化。
1. 表面张力测量方法目前,测量表面张力的常用方法有静力法、动态法和悬滴法等。
这些方法通过测量液滴形状的变化来计算表面张力。
新能源发电系统中的能效优化技术教程
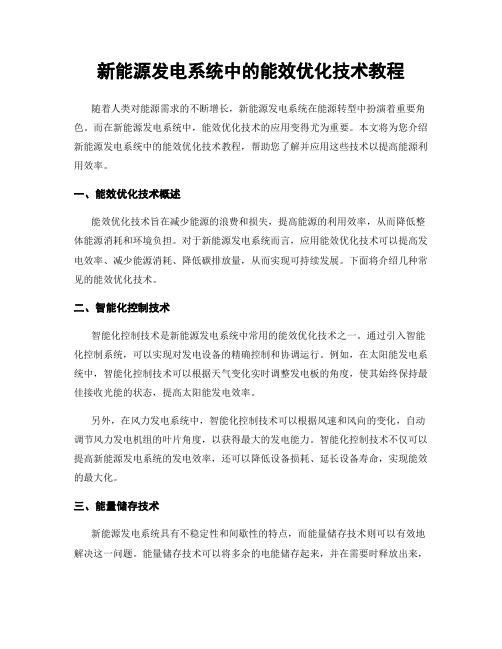
新能源发电系统中的能效优化技术教程随着人类对能源需求的不断增长,新能源发电系统在能源转型中扮演着重要角色。
而在新能源发电系统中,能效优化技术的应用变得尤为重要。
本文将为您介绍新能源发电系统中的能效优化技术教程,帮助您了解并应用这些技术以提高能源利用效率。
一、能效优化技术概述能效优化技术旨在减少能源的浪费和损失,提高能源的利用效率,从而降低整体能源消耗和环境负担。
对于新能源发电系统而言,应用能效优化技术可以提高发电效率、减少能源消耗、降低碳排放量,从而实现可持续发展。
下面将介绍几种常见的能效优化技术。
二、智能化控制技术智能化控制技术是新能源发电系统中常用的能效优化技术之一。
通过引入智能化控制系统,可以实现对发电设备的精确控制和协调运行。
例如,在太阳能发电系统中,智能化控制技术可以根据天气变化实时调整发电板的角度,使其始终保持最佳接收光能的状态,提高太阳能发电效率。
另外,在风力发电系统中,智能化控制技术可以根据风速和风向的变化,自动调节风力发电机组的叶片角度,以获得最大的发电能力。
智能化控制技术不仅可以提高新能源发电系统的发电效率,还可以降低设备损耗、延长设备寿命,实现能效的最大化。
三、能量储存技术新能源发电系统具有不稳定性和间歇性的特点,而能量储存技术则可以有效地解决这一问题。
能量储存技术可以将多余的电能储存起来,并在需要时释放出来,以保证供电的连续性和稳定性。
目前,常见的能量储存技术包括电池储能技术、超级电容器储能技术和储热技术等。
电池储能技术广泛应用于新能源发电系统中,例如太阳能电池板产生的多余电能可以被储存在电池中,并在夜间或云天气时使用。
超级电容器储能技术具有高功率密度、长寿命和快速充放电等特点,被广泛应用于风力发电系统和电动汽车等领域。
储热技术则可以利用低谷电价时将电能转化为热能储存起来,后续再利用。
四、智能能源管理系统智能能源管理系统是在新能源发电系统中实现能效优化的重要手段之一。
该系统通过对电力需求和发电能力进行实时监测和调节,使得供需双方能够实现最佳匹配。
能量管理系统

谢谢观看 DOCS
• 核心功能包括: • 数据采集:通过各种传感器和仪表收集能源使用数据 • 数据处理:对采集到的数据进行清洗、整理和分析 • 数据分析:利用统计和预测技术,挖掘能源使用中的潜在问题和优化空间 • 能源优化:根据分析结果,提供节能措施和管理策略,指导企业合理使用和分配能源
能量管理系统在工业领域的应用背景
• 统计分析:利用统计方法分析能源数据,发现数据中的规律和趋势 • 预测分析:利用预测技术预测未来能源消耗,为能源优化提供依据 • 数据挖掘:利用数据挖掘技术发现数据中的潜在问题和优化空间
能量管理系统的性能评估与优化方法
性能评估方法:
• 定量评估:通过数据指标评估系统性能,如响应时间、准确率等 • 定性评估:通过用户体验和专家意见评估系统性能,如易用性、实用性等
02
能量管理系统的组成与结构
能量管理系统的硬件组成及其作用
硬件组成主要包括:
• 传感器:用于测量各种能源参数,如温度、压力、流量等 • 仪表:用于显示和记录能源数据,如电能表、燃气表等 • 通信设备:用于实现数据传输和通信,如以太网交换机、无线通信模块等 • 服务器:用于存储和管理能源数据,如工业控制计算机、数据库服务器等
04
能量管理系统的分析与评估
能量管理系统的数据分析与挖掘技术
数据分析与挖掘的应用:
• 设备性能分析:分析设备运行数据,发现设备性能的优劣和改进空间 • 生产过程优化:分析生产过程数据,发现生产过程中的瓶颈和优化方向 • 能源消耗预测:预测未来能源消耗,为能源管理和优化提供决策支持
数据分析与挖掘技术:
对能量管理系统未来研究的建议与展望
研究建议:
• 加强理论研究:深入研究能量管理系统的原理和方法,提高系统的科学性和实用性 • 注重技术创新:关注新技术的发展,将新技术应用于能量管理系统,提高系统技术水平 • 深化应用研究:针对不同行业和企业特点,开展能量管理系统的应用研究,提高系统的适 用性和效果
- 1、下载文档前请自行甄别文档内容的完整性,平台不提供额外的编辑、内容补充、找答案等附加服务。
- 2、"仅部分预览"的文档,不可在线预览部分如存在完整性等问题,可反馈申请退款(可完整预览的文档不适用该条件!)。
- 3、如文档侵犯您的权益,请联系客服反馈,我们会尽快为您处理(人工客服工作时间:9:00-18:30)。
入炉铸坯温度 加热至出坯温度所需要的能量, MJ/t
1000℃ 131.06
800℃ 305.81
600℃ 480.56
400℃ 655.31
25℃ 982.97
节约温度即是节能!
连铸-热区段界面技术应用案例—热送热装 唐山钢铁公司第二炼钢 - 轧钢厂在 1996 年、 2003 年分别建立了 第1棒材轧钢车间和第2棒材轧钢车间。第1轧钢车间全部采用切分 轧制技术生产 ∅ 12mm~∅18mm 螺纹钢(一座加热炉 +18 架棒材轧 机机组);第二棒材轧钢车间全部生产∅20mm以上的螺纹钢。 在技术改造过程中,高度重视炼钢车间与第 1 、第 2 轧钢厂之 间的平面布置关系(流程网络),特别是 6# 连铸机和第 1 棒材车 间之间紧凑-顺畅的铸坯输送路线,走行距离为241.1m;5#连铸机 和第2棒材车间之间的更为紧凑-顺畅的铸坯输送路线,铸坯的走 行距离为 81.5m 。现在两个棒材车间分别与 5# 、 6# 连铸机固定供 坯生产,实际钢材产量已达220万吨/年。其中铸机-加热炉之间铸 坯的高温直接入炉技术、铸机定重供坯技术以及与此相关的切分 轧制等生产工艺改进,有着重要的作用。
20.79% 11639 31.00% 18.42% 8.16% 0.00% 0.00% 2433 1509 0 0 6.48% 4.02% 0.00% 0.00%
33.87% 21283 52.63% 21963 58.50%
5. 总结
界面技术优化可以加速物质流运转速度和过程运输时间 节奏,因此可以减少物质流运输过程的能量损失,如铁水 温度损失和铸坯温度损失。 面这些技术仅需要少量的硬件 投资,而且仅是操作过程的优化即可取显著的节能效果、 经济效益和社会效益。
年节约生产成本总额50375万元,吨钢共节约成本77.5元 ①减少铁水温降损失节能约 18.6kgce/t-钢, 节约生产成本20304 万元; ②降低电耗:年节约用电约1770万度。按0.56元/度计算,每年 可节省电费 991.2万元; ③铁钢界面流程紧凑,铁水运输距离短,生产组织有序、高效 ,平均每年增加产量约27万吨,增加产量而增加的效益按吨钢385 元计算,年增加效益10395万元; ④年降低耐火材料、氧气、脱硫剂消耗,降低铁路维护费用、减 少人力成本、节约土地使用费、折旧成本等约18684.8万元。
5
钢铁工业节能途径:
通过节能技术应用节能, 如CDQ, TRT , 煤气回收利用技术 (OG, LT, CCPP …) 优化流程操作的“界面技术”节能: 减少热铁水、液态钢水 和钢坯的温度损失…
煤气回收利用网络 CDQ 余热回收 TRT
钢水 显热 钢坯 显热
铁水 显热
节能技术
“界面技术”,优化界面操作与运行 6
界面技术值得关注!
Thank you for your attentions! 谢谢!
26
高炉-转炉流程
(铁矿石为基础)
粗钢产量 中近90% 以上是转 炉钢.
电炉流程
(以废钢为基础)
从20世纪80年代起的单体节能、工序节能到90年代的流程优 化带来的系统节能,自1990年以来,中国钢铁工业节能与环 保都取得了巨大的成就。从1990年到1999年的十年间,我国 钢产量增长了将近一倍,而能源消耗总量仅增加了约31%。
钢铁工业节能多关注节能技术节能, 因此节能技术普及率显著 提高. 但流程操作优化, 尤其是界面运行与优化通常被忽视。
普及率
年份
1990~2010年中国钢铁工业CDQ 、 TRT 技术普及率
7
钢铁生产过程中有多次的升温和降温过程 维持高温过程消耗很多能量 加快高温过程的运转速度,减少温度损失即是节能– 界面技术 节能
(2)社会效益
通 过 加 速铁 水 包运转过程 ,减少铁水温 降, 可以节约 3985753GJ/a , 可以减少废气4896tonne/a,可以减少 CO2 排放3.36Mt/a,减少SO2排放2312t/a 减少铁水倒罐过程粉尘产生 5560t/a,而且粉尘排放可以 减少 33.6t/a. “ 一包到底 ” 模式已被中国钢铁企业所接受,并在一 些重大工程建设中得以应用,重钢新区建设项目,首钢京 唐钢厂……
10
钢铁生产流程界面技术发展和动态运行优化
DL “紊流”
s.b s.s
DL
工序、装置静态能力估算
s.b s.s
单元工序、装置内部半动态
DL
“层流”
DL
单元工序、装置内部半动态和部分工序间动态-有序运行
全流程动态-有序-协调-连续运行 11
3.炼铁-炼钢区段(BF-BOF)界面技术
模式Ⅰ:高炉-铁水包倒包-转炉
能量系统优化典型技术—“界面技术” 应用案例
钢铁研究总院(CSIRI) 2013年7月,江苏
1
内容提纲
1. 中国钢铁工业节能技术的发展 2. 钢铁生产流程动态运行与界面技术 3. 炼铁-炼钢区段(BF-BOF)界面技术与应用案例 4. 连铸-热轧区段(CC-HR)界面技术与应用案例 5. 总结
2
1. 中国钢铁工业节能技术的发展
模式Ⅱ:高炉-鱼雷罐脱硫-铁水包-转炉
模式Ⅲ:高炉—铁水包脱硫-转炉(”一包到底” )
炼铁-炼钢区段不同界面模式间的比较
界面模式类型 模式Ⅰ:高炉-铁水包倒包-转炉 模式Ⅱ:高炉-鱼雷罐脱硫 -铁 水包-转炉 模式Ⅲ:高炉-铁水包脱硫-转炉 ( “一包到底”) 铁水转换容 铁水输送周期, 铁水温降, 入炉铁水温 器次数 min ℃ 度,℃ 2 1 0 157.2 180.7 127.5 142.4 174.1 100.5 1307.6 1285.9 1349.5
“一包到底”模式取消了铁水倒包环节,因此减少了铁水倒换容 器过程中空气冷却及新容器包壁吸热产生的铁水温降, 同时铁水 输送时间缩短。而且, 避免了倒包过程中的炉尘排放。 与其它两 种模式相比: “ 一包到底”模式下,铁水温降分别减少了42℃ 和 74℃, 相当 于节约能源损失49.2MJ/t-铁 和86.7MJ/t-铁 铁水输送周期缩短了约 30min 和 53min
与传统的鱼雷罐(模式Ⅱ)模式相比,沙钢炼铁-炼钢区段“一包到 底”技术应用取得如下效果(以 650万吨生产流程产量规模计): (1)经济效益 减少占地面积527000m2, 相当于0.081m2/t-钢; ① 取消鱼雷罐车的编组站及铁路等,节约用地约500000m2; ②取消了炼铁区域的铁水包修理设施,取消了倒包坑、过跨车、 倒渣、除尘等设施,节约用地约27000m2; 节约投资费用约46094万元,吨钢节约投资70.91元; ①节约占地面积527000m2、节约征地费31404万元; ②节约建筑面积10200m2,厂房建筑费用2040万元; ③节约铁路轨道投资约3000万元; ④节约铁水罐车(含耐火材料)投资约 9650万元。
4. 连铸-热轧区段(CC-HR)界面技术
加热炉燃料消耗与铸坯入炉温度和目标出坯温度密切相关,尤 其是铸坯入炉温度。铸坯入炉温度越低,加热炉燃耗越高。而连铸 -热区段界面技术的优劣决定了铸坯入炉温度。
Heat needed by reheating
入炉铸坯温度与加热能耗的关系
目前主要模式有四种: 模式一:连铸-板坯库-加热炉-轧制(CCR)。 连铸坯浇铸出来后先送到板坯库存放,根据轧制计划的需要, 在一定的时间之后装炉轧制。 模式二:连铸-保温坑-加热炉-轧制(HCR)。 连铸坯浇铸出来后先送到保温坑存放,根据轧制计划的需要, 在一定的时间之后装炉轧制,板坯装炉温度一般为400~700℃,也称 为温装。 模式三:连铸-辊道-加热炉-轧制(DHCR)。 连铸坯浇铸出来后直接通过输送辊道装入加热炉进行短时间加 热然后轧制,装炉温度都在700--1000℃。 模式四:连铸-辊道-边角补热-轧制(HDR)。 连铸坯浇铸出来后直接运输至热轧机轧制,途中针对板坯采用 边角加热措施,一般轧制温度在1100℃以上。
1990~1999年中国钢铁工业节能手段节能量及其构成比例
序号 1 2 3 4 合计
类别 ①优化钢铁生产流程 ②采用节能技术和装备 ③钢铁生产辅料等改善 ④能源管理
*1 tce = 29.26 GJ
节能量 (万tce*) 1870 870 710 1150 4600
构成比例, (%) 40.7% 18.9% 15. 4% 25.0% 100%
图1唐钢第二炼钢-轧钢厂的平面布置图
温装炉有关技术参数的逐项对比
5#铸机-第2 棒材车间之 间铸坯直接 装炉温度提 高对加热炉 煤气消耗的 影响实绩
表 5#铸机-第2棒材车间之间铸坯直接装炉温度的进步
月份 月铸坯表面温度 (℃) ~810 810~830 830~850 850~870 870~890 890以上 2012年1月 根数 0 20652 18843 3467 0 0 百分比 0.00% 48.07% 43.86% 8.07% 0.00% 0.00% 2012年2月 根数 2628 8453 6431 1475 0 0 百分比 13.84% 44.52% 7.77% 0.00% 0 2012年3月 根数 8407 7449 3300 0 0 百分比 2012年4月 根数 百分比
4
从2000年到2005年,粗钢产量增加了175%, 但钢铁工 业能源消耗仅增加了120%. “十一五”期间(2006年到2010年),重点大中型钢 铁企业吨钢综合能耗由 2006 年的18.9GJ/t 降至2010年 的17.7GJ/t, 降幅约6.3%, 尤其关键节能技术普及率, 如TRT、CDQ、干法除尘技术及副产煤气综合利用技 术等,显著提高.
炼铁-炼钢界面“一包到底”技术应用案例
沙钢是较早采用“一包到底”技术的钢厂之一,并在“一包到 底”技术应用方面主要实现了几个方面的创新: 实施了“四个一致”的设计,保证了超高超宽铁水包平稳、 安全运行 建立了炼铁厂负责制的铁水称量管理体制,集成开发了无基 坑称重轨、在线连续称重系统、空包重量循环跟踪等10项技术, 保证了铁水精确计量和装入量目标命中率。 首创炼钢厂管控铁水包运行的管理制度,促进了铁水包快速 周转,实现了铁水包在线快速编组、快速维护、快速上线,为 稳定高效低成本脱硫提供了保障。 开发了铁水信息和铁水包运行时间在线跟踪系统。 因此,炼铁-炼钢区段界面总体布局简洁,物流顺畅,区域布置 紧凑,输送线路短、物流顺畅,铁水温降少,节能减排效果显著。