钢包耐火材料的改善
墨钢玉在钢包耐火材料中的应用
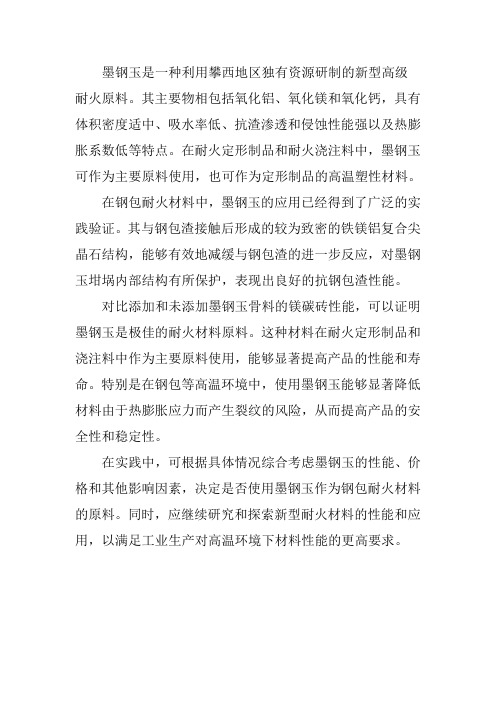
墨钢玉是一种利用攀西地区独有资源研制的新型高级耐火原料。
其主要物相包括氧化铝、氧化镁和氧化钙,具有体积密度适中、吸水率低、抗渣渗透和侵蚀性能强以及热膨胀系数低等特点。
在耐火定形制品和耐火浇注料中,墨钢玉可作为主要原料使用,也可作为定形制品的高温塑性材料。
在钢包耐火材料中,墨钢玉的应用已经得到了广泛的实践验证。
其与钢包渣接触后形成的较为致密的铁镁铝复合尖晶石结构,能够有效地减缓与钢包渣的进一步反应,对墨钢玉坩埚内部结构有所保护,表现出良好的抗钢包渣性能。
对比添加和未添加墨钢玉骨料的镁碳砖性能,可以证明墨钢玉是极佳的耐火材料原料。
这种材料在耐火定形制品和浇注料中作为主要原料使用,能够显著提高产品的性能和寿命。
特别是在钢包等高温环境中,使用墨钢玉能够显著降低材料由于热膨胀应力而产生裂纹的风险,从而提高产品的安全性和稳定性。
在实践中,可根据具体情况综合考虑墨钢玉的性能、价格和其他影响因素,决定是否使用墨钢玉作为钢包耐火材料的原料。
同时,应继续研究和探索新型耐火材料的性能和应用,以满足工业生产对高温环境下材料性能的更高要求。
提高精炼钢包使用寿命与降低钢包耐材成本的策略探讨
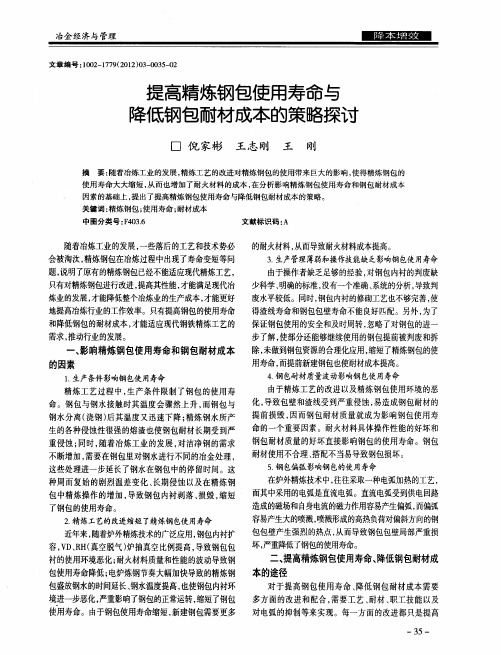
命。钢包与钢水接触时其温度会骤然上升, 而钢包与
钢水分离( 浇钢) 后其温度又迅速下降 ; 精炼钢水所产 生的各种侵蚀性很强的熔渣也使钢包耐材长期受到严 重侵蚀 ; 同时 , 冶炼工业的发展 , 随着 对洁净钢 的需求 不断增加 , 需要在钢包里对钢水进行不同的冶金处理 , 这些处理进一步延长 了钢水在钢包中的停留时间。这 种周 而复始的剧烈温差变化 、 长期侵蚀以及在精炼钢
命的一个重要因素。耐火材料具体操作性能的好坏和
钢包耐材质量的好坏直接影响钢包的使用寿命。钢包
耐材使用不合理、 搭配不当易导致钢包损坏。 5钢 包偏弧影响钢 包的使用寿命 .
在炉外精炼技术中, 往往采取一种电弧加热的工艺 ,
包中精炼操作的增加, 导致钢包内衬剥落、 损毁, 缩短 了钢包的使用寿命。 2精炼工艺的改进缩短了精炼钢 包 . 使用寿命
一
包使用寿命降低; 炉炼钢节奏大幅加快导致的精炼钢 电 包盛放钢水的时间延长、 钢水温 度提高, 也使钢包内衬环 境进一步恶化, 严重影响了钢包的正常运转 , 缩短了钢包 使用寿命。由 于钢包使用寿命缩短, 新建钢包需要更多
3 5—
21年第3 02 期
使用寿命 、 降低耐材成本的一个要素。科学合理的整 体改进 , 有利于精炼行业的发展。 1改进钢包 . 修砌工艺, 选择成本合理、 质量过关的耐材
钢包的结构主要分为钢包工作层 、 钢包永久层 、 钢 包隔热层和钢包 的钢质包 壁。在 包壁永 久层浇筑方 面 , 以用浇筑高铝尖晶石质 自流浇注料来代替砌筑 可 高铝砖 , 去除砖缝 , 提高永久层的整体强度 , 也有利于 对其局部修补。对于包壁的隔热层 , 要使用新型钢包
钢包耐火材料损坏原因及提高使用寿命的措施
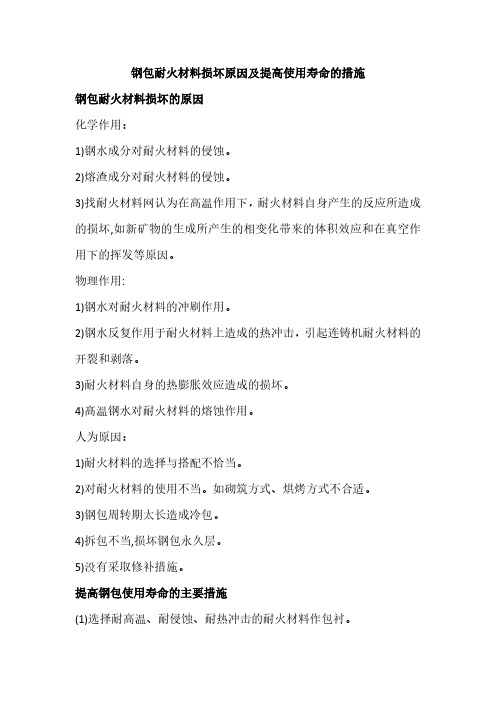
钢包耐火材料损坏原因及提高使用寿命的措施钢包耐火材料损坏的原因化学作用:1)钢水成分对耐火材料的侵蚀。
2)熔渣成分对耐火材料的侵蚀。
3)找耐火材料网认为在高温作用下,耐火材料自身产生的反应所造成的损坏,如新矿物的生成所产生的相变化带来的体积效应和在真空作用下的挥发等原因。
物理作用:1)钢水对耐火材料的冲刷作用。
2)钢水反复作用于耐火材料上造成的热冲击,引起连铸机耐火材料的开裂和剥落。
3)耐火材料自身的热膨胀效应造成的损坏。
4)髙温钢水对耐火材料的熔蚀作用。
人为原因:1)耐火材料的选择与搭配不恰当。
2)对耐火材料的使用不当。
如砌筑方式、烘烤方式不合适。
3)钢包周转期太长造成冷包。
4)拆包不当,损坏钢包永久层。
5)没有采取修补措施。
提高钢包使用寿命的主要措施(1)选择耐高温、耐侵蚀、耐热冲击的耐火材料作包衬。
(2)正确选择和搭配耐火材料,做到均衡砌包。
(3)了解所选用的耐火材料的性能,合理制订钢包的使用条件,如烘烤制度的制订等。
(4)尽可能加快钢包的使用周期,做到“红包”工作。
’(5)对包衬耐火材料损坏部分,及时进行喷补处理。
清理钢包维护包衬操作步骤(1)上一炉浇注完毕,尽快将钢包内余钢残渣倒尽。
(2)及时清理包口冷钢残渣。
(3)若包底有冷钢则必须将钢包横卧,用氧气将冷钢进行熔化清除。
(4)检查钢包渣线、包底、包壁、座砖损坏情况,及时进行修补及维护:a.由于砌筑或衬砖质量上的原因,钢包在使用过程中会造成局部的破损。
因此在淸除残钢残淹后,应修补侵蚀严重的部位。
b.为了提高钢包的使用寿命及防止漏钢,应该及时进行热修。
如热灌砖缝:热灌砖缝法是用调的较稀的火砖粉-水玻璃浆(或其他耐火粉料加粘结剂调和后),灌人砖缝内,由于水玻璃遇热起泡,故而往往要连续补几次。
热补孔洞:热补孔洞法是用较稠的火砖粉-水玻璃膏(或其他耐火粉料加粘结剂调和后)投补,并适当拍打。
热补座砖:热补座砖法同热补孔洞法。
修补应在安装水口以后进行,并用相当于水口砖外径的铁盖将水口挡住,防止泥料掉在水口上。
钢包用含碳耐火材料的开发

混合 3 mi n , 加 水后 在 混 合 机 内再 混 合 3 m i n , 然后 开
始 成 型试样 ; 将 成型 的试 样 在 室温 下 的模 具 中硬化 2 4 h , 随后 脱模 , 并在 1 1 0 c c下 干燥 2 4 h 。 利用 所 制 成 的尺 寸 为 4 0 m m ×4 0 a r m ×1 6 0 am r 和2 5 a r m X 2 5 a r m ×2 5 0 a r m 柱 状 试 样 测 定 了 开 口气
验
低水 泥触 变性 耐火 浇注 料 。
2 . 4 石 墨 的 加 入 掺入 到 A I , O 一 Mg O耐 火材 料 中 。在 使用 鳞 片 状 石 墨 时会 产 生 以下 f h J 题: ① 鳞 片状石 墨颗 粒料 的聚集 会 降低 单 位 比表 面 积 ; ② 能使 氧 化铝 一 石 墨 压球 混合 料 的 密度 最 小 ; ③ 采
式 加入 到 A 1 , O 一 Mg O耐 火材料 中。
2 . 3 配 料 组 成
2 2 0  ̄ C下 进行 加 热处 理 。制 成 的样块 的体 积 密 度 介
于2 . 5 5 ~ 2 . 6 0 g ・ c n l 之 间。将加 热处 理后 的样 块破 碎 成大 颗粒 和 中颗粒形 式 。
添加氧 化铝 一 石 墨压 球 颗 粒料 的 A 1 , O 一 Mg O— C浇注 料 的配料组 成 列于表 1 。 2 . 8 试样 的制 备 利用振 动 台 ( 振幅 0 . 4 a r m, 频率 6 0 H z ) 以振 动 成 型 的方法 制 备 了试 样 。在 制 备 试 样 时 , 先 将 干料
膨 胀增 大 、 高温压 缩性 提 高以及 高温抗 折强 度 降低 ,
钢包操作条件对耐火材料使用寿命的影响_田守信

式中: X、 r、 σ、 θ、 η 和 t 分别为渣渗透深度、 耐火材料 气孔半径、 表面张力、 润湿角、 渣黏度和渗透时间。 由 (4) 式可知, 渣向耐火材料渗透深度与渣黏 度的平方根成反比。因此渣黏度降低, 导致扩散深 度增加, 即渣黏度降低, 会使耐火材料反应变质层 加厚, 导致了侵蚀增加。渣渗入的耐火材料层的耐 火度降低, 烧结致密度增加, 与耐火材料原始层的 热膨胀等性能差异增加, 在钢包间歇使用过程中, 导致渣渗透层裂纹和剥落, 从而造成了耐火材料包 衬损耗。因此, 提高渣的黏度能降低耐火材料包衬 的侵蚀, 提高钢包的使用寿命。可以通过添加适量 的白云石和选用合理的造渣剂而控制渣黏度, 达到 减少耐火材料侵蚀和提高钢包使用寿命的目的。 2.4 真空处理的影响 很多精炼设备具有真空处理功能, 如 LF-VD、 VOD、 RH 和 DH 等。真空条件对耐火材料的损耗特 别是含碳耐火材料具有很大影响。根据化学平衡 原理, 在真空条件下, 将促进下列反应向右进行, 造 成耐火材料内部气化: MgO+C=Mg↑+CO↑, 4MgO+ 2Al=3Mg↑+MgAl2O4, MgO+Si=Mg↑+SiO↑, 5MgO+ B4C=5Mg↑+CO↑+2B2O2↑。 上述反应导致了含碳耐火材料内部松散, 强度 下降, 甚至粉化, 使包衬的使用寿命随 VD 比例和处 理时间的延长而线性下降[8]。因此, 在高温真空条 件下, 不宜选择铝粉、 硅粉和碳化硼这些易与氧化 镁发生氧化还原反应的添加物。它们不但不能提 高钢包的使用寿命, 反而降低使用寿命。而 CaO 不 易与碳发生氧化还原反应, 所以在一定条件下, MgO-CaO-C 比镁碳更适合这些特殊条件。 2.5 超高温的影响 在冶炼不锈钢过程中需要超高温, 即在 AOD 和 VOD 精炼炉内往往出现 1 700 ℃以上高温。温度增 加, 显著提高了耐火材料的侵蚀速度, 因此超高温 会导致耐火材料的严重侵蚀。超高温不但使渣黏 度降低和溶解度增加而导致熔蚀速度加快, 而且对 于含碳耐火材料严重影响了下列氧化还原反应: MgO+C=Mg↑+CO↑-热量, MgO+2Al=Mg↑+Al2O ↑-热量, MgO+Si=Mg↑+SiO↑-热量, 5MgO+B4C=
中间包用耐火材料的常见问题及解决措施

科技视界Science &Technology VisionScience &Technology Vision 科技视界中间包是炼钢连铸过程中承接高温钢水的一个重要容器,钢水从钢包中注入中间包然后进入结晶器形成钢坯,对保证洁净炼钢和多炉连浇至关重要。
中间包的生产和使用过程中需要用到多种耐火材料,包括干式料、水口、挡渣墙系列、连铸三大件等。
中间包耐火材料在使用过程中容易出现工作衬无强度、水口开裂渗钢、湍流器上浮等问题,严重影响了连铸的稳定生产,所以很好地解决中间包耐火材料的问题显得非常重要。
1中间包耐火材料的配置中间包耐火材料包括永久层浇注料、工作层干式料、水口及座砖、挡渣墙系列和连铸三大件。
1.1永久层永久层介于工作层与中包壳之间,不与钢液和钢渣直接接触,主要起隔热和保护包壳的作用。
一般用铝镁浇注料浇注。
1.2工作层工作层与钢液、钢渣直接接触,需要承受钢液的冲刷、钢渣的侵蚀和渗透。
工作层大多采用镁质干式料,镁质干式料抗渣性好、施工方便、易于解体,还能起到净化钢液的作用。
1.3水口及座砖中包水口是钢液从中间包进入结晶器的通道,需要承受钢液的冲刷和温度的急剧变化;座砖则是起到保护和固定水口的作用,不与钢液直接接触。
中包水口多是锆芯和高铝坯体复合而成,座砖一般是高铝材质。
1.4挡渣墙系列挡渣墙系列耐火材料主要包括挡渣墙、侧板、背板和湍流器,需承受钢液的冲刷、钢渣的侵蚀和渗透。
一般采用镁质材料制成。
1.5连铸三大件连铸三大件包括大包套管、塞棒和浸入式水口,需要承受钢液的冲刷、钢渣的侵蚀和渗透。
塞棒用于浇注时控制钢液流量,大包套管和浸入式水口用于保护浇注,隔绝空气,防止钢液二次氧化。
连铸三大件多是铝碳材质,有时也加入部分氧化锆。
2中间包耐材常见的问题及解决措施2.1干式料无强度中间包投入使用前,工作层干式料需要具备一定的低温强度,低温强度主要靠振动和烘烤获得。
干式料经过振动和烘烤脱模后,经常会出现局部无强度或强度低的情况,极易造成塌包,影响连铸的安全生产。
伯利恒钢铁公司雀点厂钢包耐火材料寿命的提高

19 9 8年 开 始 , 引 进 了 高 温 烧 成 铝 尖 品 石 低 水 泥 浇 注 料 生 产 的 座 砖 。 首 次 试 验 , 这 种 预 烧 砖 使 用了 8 9次 , 预 示 了 这 种 座 砖 具 有 更 高 寿 命 的 前 这 景 。 在 此 期 间 ,座 砖 高 度 增 加 了 6 .rm, 同 时 . 25 a
20 0 2年 第 2期 51
寿命 提 高 了 。 雀 点 厂 没 有 使 用 的 是 没 有 多 孑 底 吹 透 气 L
维普资讯
《f 恒 钢 铁 公 司 雀点 厂 钢 包 耐火 材 料 寿 命 的提 高 》 自利
CS T C IC E HN0 0G L Y
维普资讯
重 钢技术
《 侑利恒钢铁公 司雀点厂 钢包耐火制 寿命 的提 高 》 料
伯 利 恒 钢 铁 公 司 雀 点 厂 钢 包 耐 火 材 料 寿 命 的 提 高
J me Bar n R ih r ah a sO re t c ad F s
过 去 常 用 较 低 质 量 的 第 二 套 座 砖 以 配 包 壁 砖 的
寿命 。
钢 包 耐 火 材 料 实 践
钢 包 耐 火 材 料 总 体 寿命 取 决 于钢 包 中各 种耐 火 材 料 成 分 的性 能 。要 使 钢 包 获 得 更 高 的寿命 ,
耐 火材 料 必 须 按 这 样 一 种 ‘ 来 选 择 一 一 即 各 种 式 耐 火 材 料 的 性 能 要 相 互 配 并 能 为 按 需 要 进 行 操 作 提 供 多 种 选 择 。 为 配 高 性 能 的 座 砖 ,钢 包 其 余 部 分 使 用 改 进 后 的 耐 火 制‘ 后 , 钢 包 耐 火 材 料 料
高性能钢包耐火材料用镁铝尖晶石

高性能钢包耐火材料用镁铝尖晶石Raymond P.RacherAlmatis Inc.501West Park RoadLeetsdale,PA15056,USARobert W.McConnellAlmatis Inc4701Alcoa RoadBauxite,AR72011USAAndreas BuhrAlmatis GmbH,Olof-Palme-Str.37,D-60439Frankfurt/MainGermany摘要优质钢的生产要求钢在钢包中进行更多的处理。
这对钢包用耐火材料有显著的影响,例如需要透气砖等高性能功能耐火材料。
增加出钢温度,较长的停留时间,侵蚀性更强的二次冶炼等操作的改变要求耐火材料衬更薄,寿命更长。
这些综合因素重新唤起了对镁铝尖晶石研究的兴趣。
镁铝尖晶石已经作为各种类型用于炼钢用耐火材料很多年了。
本文阐述了尖晶石的生产、理化性能和使用性能,也讨论了尖晶石应用的进展情况。
1 引言本文讨论了镁铝尖晶石的结构、性能和应用,尤其描述了镁铝尖晶石在生产洁净钢用耐火材料上的优点。
镁铝尖晶石由于强的抗渣侵蚀性、优良的抗热震性和高温强度高等特点,越来越多的被应用于炼钢用耐火材料。
20世纪60年代中期最初生产的尖晶石耐火材料是通过氧化铝和镁砖中的方镁石的原位反应制备的,用于水泥窑的内衬。
高质量的预合成尖晶石使得发展优质不定形耐火材料和耐火砖成为可能。
2 性能2.1 结构镁铝尖晶石是具有相同晶体结构的氧化物中的一种,这种晶体结构称为尖晶石结构。
尖晶石组有二十多种氧化物,但只有很少数是常见的。
尖晶石组的结构式是AB2O4,这里A代表二价金属离子,例如镁、铁、镍、锰和/或锌,B代表三价金属离子,例如铝、铁、铬或锰。
除非特别指明,本文的尖晶石表示MgAl2O4,矿物尖晶石是二元系统MgO–Al2O3的唯一化合物。
尖晶石族矿物的明显特征是,它是一种组分可被替代的固溶体,尖晶石组分中一种或两种都可以被这组矿物中的其他组分大量的代替,而且是在晶体结构不改变或晶格没有任何变形的情况下。
- 1、下载文档前请自行甄别文档内容的完整性,平台不提供额外的编辑、内容补充、找答案等附加服务。
- 2、"仅部分预览"的文档,不可在线预览部分如存在完整性等问题,可反馈申请退款(可完整预览的文档不适用该条件!)。
- 3、如文档侵犯您的权益,请联系客服反馈,我们会尽快为您处理(人工客服工作时间:9:00-18:30)。
钢包耐火材料的改善
2008.10.20
前言
原来,日新制钢公司吴制铁所一炼钢车间所用钢包,在承受钢流冲击部位一直使用预制砌块(p reastblock)。
使用钢包时,钢流冲击砌块的剥离成了限制钢包寿命提高的主要障碍,从而使得钢包寿命近几年来一直踏步不前。
因此,对此砌块耐材质量进行了以下改善:首先是为了提高砌块的耐蚀性、耐热冲击性而使之在浇注施工时进行低水分化;进而为了抑制低水含量引发的内应力,在耐材内加入0.4wt%的木片,缓和了内应力而抑制了龟裂。
从而将钢包寿命提高了5%。
2 一炼钢车间钢包使用状况
如表1所示,钢包的使用条件苛刻:出钢温度偏高(>1700℃),每日的受钢次数低(仅5ch),从而使砌块既要承受高温钢流的冲刷,还要承受急冷急热可能造成的裂纹和剥离。
表1 钢包使用条件
3 钢包内衬纵剖面图
图1为所用钢包内衬耐材的纵剖面图:净空、渣线、水口部位采用MgO—C质耐材,在钢液熔池部位的侧壁、包底、钢流冲击砌块则采用了A12O3一MgO质耐材;另外,抗钢流冲击砌块设置在包底的中央部位。
图1 钢包内衬断面
4 钢包维修图表及维修部位
表2为钢包维修图表:钢包每使用50~55ch即进行一次中修,经三次中修后,在寿命为210 ch左右时再进行周期性整体维修(即大修)。
对钢流冲击砌块和水口砖,每次中修都要更换;而对于包底、侧壁、渣线部位耐材,则在第二次中修时进行增厚或更换。
表2 钢包修理图表
图2表示钢包开始维修时需要维修的部位。
由图2中数据可知:在需要维修的各个部位中,次数最多的是钢流冲击砌块、46次、占了64.8%;其次分别是渣线(占20%)、侧壁和包底(占1 0%)、水口(占5.2%)。
因此,为了延长钢包寿命,首先就需要改善该砌块的材质。
图2 钢包开始维修时的凹槽部位
5 砌块寿命的提高
5.1 砌块的损坏形态
其损坏形态如图3所示:钢包在实际使用了15ch后,由于出钢时砌块承受钢流的冲击大,故使用之初就在其中央部产生了裂纹,龟裂的扩展就造成了材料的剥落,从而缩短了使用寿命。
因此,提高耐材的耐剥离性十分重要。
图3 钢流冲刷砌块的损坏形态
5.2 砌块用浇注块的低水分化
5.2.1 低水分施工浇注块的开发
承受钢流冲击后,砌块上产生龟裂,主要是冲击造成的机械剥离和熔渣引起的结构性剥离。
为了抑制这种破坏,是实现浇注块的低水分化、提高其强度,并将之致密化以抑制渣的浸润。
在减少浇注块的水分时,为了提高材料的流动性,将用作填充料的氧化铝(Al23O3)从电熔Al203改为烧结A1203;而且,还将加入的有机纤维量减少了25%。
表3为低水分材料与原来材料的质量特性对比。
由于改善了材料本身的流动性,可将施工时的加水量从原来的4.2%减至3.8%,从而降低了表观气孔率,提高了抗压强度;另外,为了缓和致密化造成材料膨胀量的增大,将氧化镁(Mg0)加入量从原来的8.1%减至6.2%。
表3 低水分材料的质量特性
★未加粗粒、SUS纤维时
5.2.2 低水分施工浇注块的使用效果
图4为低水分材料实际使用时的外观照片:在使用12ch的初期,砌块中央部产生了龟裂;在使用的中~末期的43ch时,初期发生的中央部龟裂扩展了,表面的凹凸也变大了;在其后的51c h时,部分材料完全剥离,露出了永久(Permanent)层砖,故停用维修。
图4 实际使用时的低水分材的外观图片
从使用时的状态观察而判断低水分材的损坏不是熔损而是碎裂造成的,即因材料致密化而使膨胀增大,所产生的内应力未被吸收,从而造成了龟裂,当裂纹扩展至工作面时,材料就会产生大的剥落。
5.3 加入木片的砌块用浇注块的开发
5.3.1 木片加入量的研究
因材料的低水分化而导致其致密化时,弊端是因材料膨胀量和强度的增大而使其内应力增大,从而引发了龟裂。
因此,其对策是在材料的内部加入木片,以吸收膨胀量和内应力,从而抑制龟裂的发生。
在添加了木片的研究中,进行了材料的残余膨胀的对比试验。
图5为其试验条件;图6为其试验结果。
试验是在进行了1500℃×3h的3个周期反复加热后,测定了材料的残余膨胀。
结果查明:材料的残余膨胀量,有随木片加入量的增加而下降的倾向;然而,当木片加入量>0.4wt%时,此倾向就变小了。
故将木片的实际加入量选定为0.4wt%。
图5 残余膨胀比较试验条件
图6 残余膨胀比较试验结果
在添加木片时,为了使材料更低水分化、提高耐蚀性,并抑制过烧结,决定将A1203超微粉更换为强酸洗的低氧化钠铝钒土(1ow soda),就可以在加水量3.6%的条件下施工。
另外,为了实现材料的低膨胀化,决定将材料中的MgO含量从低水分材的6.2%减至5.3%。
表4为木片添加材料的质量特性:材料进一步低水分化的结果,是可以提高其抗压强度而降低其表观气孔率。
表4 木片添加材料的质量特性
★未加粗粒、SUS纤维、木片时
图7为添加木片的抗钢流冲击砌块干燥后的施工体外周部与中央部断面照片;表5为该砌块上、中、下部的物性值。
表5 钢流冲击砌块不同部位物性值
图7中的黑色部分为木片所在位置,干燥时烧损而成了孔隙,木片按纵、横、斜方向不均匀地分散,即使外周和中央部也无明显偏聚。
然而,在距底面30㎜处没有木片,如表6所示的表观气孔率也低,这是施工振动使木片上浮所致,但木片在整体结构中还是分散的。
图7 加入了木片的钢流冲击砌块的断面照片
5.3.2 加入木片的浇注块的实用结果
图8表示实际使用木片添加材时的外观照片:在使用中期(经27ch后)砌块发生的龟裂也小,工作面上未见剥离而是保持了平滑状态,充分说明添加的木片确实具有抑制材料表面产生龟裂的效果。
图8 实际使用加入木片材时的外观照片
即使是在使用末期(使用54ch后),砌块中央部的龟裂也较细。
未发现会导致材料大剥离的龟裂产生,且其表面也很平滑。
图9表示原来材料与木片添加材料使用后的外观照片对比:前者使用48ch后,最薄的残余厚度仅30mm,表面凹凸也大,且产生了很多与工作面不平行的龟裂,从而造成砌块的剥离损坏;
而后者就是在使用了59ch之后,最薄处仍厚达60mm,无大的龟裂,且可以确认是木片所在位置阻止了龟裂扩展。
图9 材料用后的外观照片
图10表示砌块分别使用原来材、低水分材和木片添加材时的使用寿命对比:前者寿命的波动大(范围33~62ch),平均值低到46.1ch;低水分材因致密化造成的膨胀大并引发了内应力,从而出现了明显剥离,寿命较原来材也没提高,试验2次就中止了;后者的寿命高(平均53.5ch),且波动小(47~60ch)。
图10 不同材料钢流冲击砌块的使用寿命比较
图11表示一炼钢车间钢包寿命和成本的变化:因添加木片砌块的开发和钢包其它耐材的改善,使钢包寿命从210ch提高至铲了220ch,即提高了大约5%,而且,还有进一步提高的潜力;钢包成本至2004年下半年也比原来大约下降了8%左右。
图11 一炼钢车间钢包寿命和成本的变化
6 结语
日新制钢公司·吴制铁所一炼钢车间在提高本来就已经处于200ch较先进水平的钢包寿命时,针对性地对抗钢流冲击砌块的质量进行了改善,结果如下:
(1)为了抑制砌块的龟裂剥离,首先是降低浇注块施工水分以使之致密化并提高抗压强度,还相应调整了MgO、Al203用料及有机纤维加入量。
结果,因膨胀和内应力增大,改善效果不理想。
(2)在试验研究基础上,决定向材料中加入了0.4wt%的木片,同时调整A1203用料和MgO含量,结果改善了砌块用材料的一系列物性值,从而使已处于高水平的钢包寿命提高了5%,成本下降了8%。