设计作业 300t顶底复吹转炉炉型计算
转炉炉型设计计算
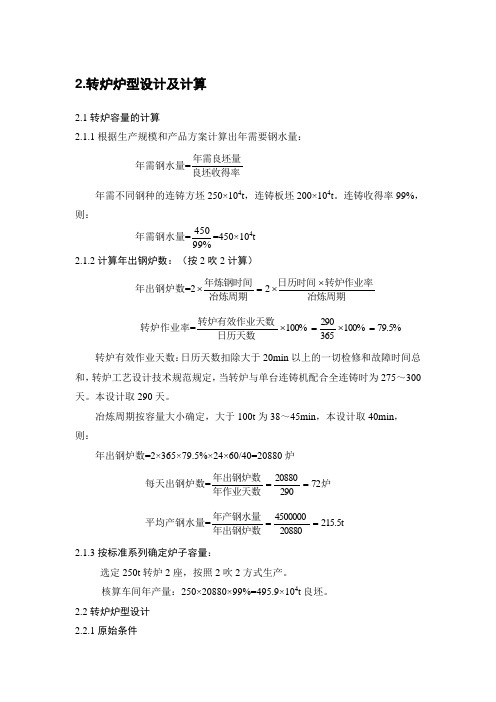
2.转炉炉型设计及计算2.1转炉容量的计算2.1.1根据生产规模和产品方案计算出年需要钢水量:年需钢水量=良坯收得率年需良坯量年需不同钢种的连铸方坯250×104t ,连铸板坯200×104t 。
连铸收得率99%,则:年需钢水量=99%450=450×104t 2.1.2计算年出钢炉数:(按2吹2计算) 年出钢炉数=2冶炼周期转炉作业率日历时间冶炼周期年炼钢时间⨯⨯=⨯2转炉作业率=79.5%100%365290100%=⨯=⨯日历天数转炉有效作业天数转炉有效作业天数:日历天数扣除大于20min 以上的一切检修和故障时间总和,转炉工艺设计技术规范规定,当转炉与单台连铸机配合全连铸时为275~300天。
本设计取290天。
冶炼周期按容量大小确定,大于100t 为38~45min ,本设计取40min , 则:年出钢炉数=2×365×79.5%×24×60/40=20880炉每天出钢炉数=炉年作业天数年出钢炉数7229020880==平均产钢水量=215.5t 208804500000==年出钢炉数年产钢水量2.1.3按标准系列确定炉子容量:选定250t 转炉2座,按照2吹2方式生产。
核算车间年产量:250×20880×99%=495.9×104t 良坯。
2.2转炉炉型设计 2.2.1原始条件炉子平均出钢量为250t ,铁水密度6.8g/cm 3,铁水收得率为92%。
2.2.2炉型选择顶底复吹转炉的炉型基本上与顶吹和底吹转炉相似;它介于顶吹转炉和底吹转炉之间。
为了满足顶底复吹的要求炉型趋于矮胖型,由于在炉底上设置底吹喷嘴,炉底为平底,所以根据原始数据,为了便于设置底部供气构件,选择截锥形炉型。
2.2.3炉容比炉容比指转炉有效容积V t 与公称容量T 之比值V t /T(m 3/t)。
V t 系炉帽、炉身和熔池三个内腔容积之和。
设计作业 300t顶底复吹转炉炉型计算

转炉炉型设计计算1.1原始数据(1)、转炉的公称容量为300t 。
(2)、采用顶底复吹冶炼工艺1.2 转炉的炉型选择图为常见转炉炉型(a)筒球型; (b)锥球型; (c)截锥型根据原始条件及采用顶底复吹工艺的要求,为便于安装底部供气元件,要求转炉底部为平的,所以本设计将采用截锥型炉型作为设计炉型。
1.3炉容比炉容比系指转炉有效容积与公称容量之比值。
转炉炉容比主要与供氧强度有关,与炉容量关系不大。
从目前实际情况来看,顶底复吹转炉炉容比一般取0.85~0.95m 3/t 。
本设计为300t ,取V/T=0.92 1.4熔池尺寸的计算 熔池直径的计算公式tGkD 式中 D ——熔池直径,m ;G ——新炉金属装入量,t ,可取公称容量; K ——系数,参见表1-1;t ——平均每炉钢纯吹氧时间,min表1-1 系数K 的推荐值b.确定吹氧时间表1.2 推荐的转炉纯吹氧时间本设计的转炉公称容量为300t ,又根据国家关于新建转炉的要求,吹氧时间在16min , 所以选择的吹氧时间为16min 。
取K=1.50 则)(495.61630050.1m t G K D =⋅=⋅= ② 截锥型熔池深度的计算公式为:)(822.1495.6574.0119.44574.0574.0222m D V D V h =⨯=⨯==)(金池 V 池=G/Y=44.119m 3 其中Y=6.8t/ m 3 ③熔池其他尺寸确定.)(546.4495.67.07.01m D D =⨯== 1.5炉帽尺寸的确定 ①炉口直径d 0.取)(2475.3495.65.00m d =⨯= ②炉帽倾角: 取︒60 ③炉帽高度H 帽: 取H 口=400mm ,)(76.260tan )2475.3495.6(21tan )(2100m d D H =⨯-=⋅-=θ锥 则整个炉帽高度为:)(06.33.076.2m H H H =+=+=锥口帽 在炉口处设置水箱试水冷炉口。
宝钢300t转炉复吹现状与发展

关 键 词 : 炉 ; 吹 ; 金 效 果 转 复 冶
中图分 类号 :F 2 文 献标 识码 : 文 章编 号 :0 8 7 6 20 )3 0 1 4 T79 B 10 —0 1 (0 2 0 —00 —0
Pr s ntS t a i n a d De eo m e to 0 m b n d Bl wi g Co e tr a o te e e i to n v l p n f3 0 tCo i e o n nv re tBa se l u
宝钢 转炉 实施 复 吹工 艺 以来 , 由于 复 吹本 身
所具有 的 良好 冶 金 效 果 , 宝 钢创 造 了较 大 的经 为
同, 可分 为 2 0余 种 模 式 的 复 吹方 式 ; 果 按 照 使 如
用 目的大致 可分 为 三种类 型 : 1弱搅 拌 型 复合 吹 ()
JA G Xa - n IN i f g oa ( a s e Sel kn l tS a g a C ia 20 4 ) B ot l t ma igPa 。h n h i hn 。0 9 e e n 1
Absr c : e tc n lg c lp rmees a d c aa trsis o o ie l w n o he 3 0 tc n t a t T e h oo ia aa tr n h rc e tc fc mb n d bo i g f rt 0 o — h i
Ke o d : o vr rC m ie lw n ; t lr c f c y W r s C n e e ; o nd Bo g Mea ug a ef t t b i l il e
1 前 言
种钢 种 。 ( ) 2 强搅拌 型 复合 吹炼 : 这种 类 型是 以提 高产 量为 主 , 适 合 冶 炼 低 碳 钢 。 ( ) 化 冶 炼 、 较 3强 提高废 钢 比的复 合 吹 炼 : 种 类 型适 合 于 高废 钢 这
300t转炉课程设计说明书

1 转炉物料平衡与热平衡计算炼钢过程的物料平衡与热平衡计算是建立在物质与能量守恒的基础上的。
其主要目的是比较整个冶炼过程中物料、能量的收入项和支出项,为改进操作工艺制度,确定合理的设计参数和提高炼钢技术经济指标提供定量依据。
物料平衡是计算转炉炼钢过程中加入炉内与参与炼钢的全部物料(如铁水、废钢、氧气、冷却剂、渣料、合金添加剂、被侵蚀的炉衬等)和炼钢过程的产物(如钢水、炉渣、炉气、烟尘等)之间的平衡关系。
热平衡是计算转炉炼钢过程的热量收入(如铁水物理热、化学热)和热量支出(如钢水、炉渣、炉气的物理热、冷却剂溶化和分解热)之间的平衡关系。
1.1 原始数据的选取1.1.1 原材料成分(表1-1~表1-5)表1-1 铁水、废钢成分(%)表1-3 各材料的热容(kJ/kg.K)表1-4 反应热效应(25℃)表1-5 铁合金成分(分子)及其回收率(分母)1.1.2假设条件根据各类转炉生产实际过程假设:(1)渣中铁珠量为渣量的8%;(2)喷溅损失为铁水量的1%;CO(3)熔池中碳的氧化生成90%CO,10%2Fe O (4)烟尘量为铁水量的1.6%,其中FeO为77%,23(5)炉衬侵蚀量为铁水量的0.5%;(6)炉气温度取1450℃,炉气中自由氧含量为总炉气量的0.5%;(7)氧气成分:98.5%氧气,1.5%氮气。
1.1.3冶炼钢种及规格成分要求冶炼低碳钢,以Q235钢为例,其规格成分为(%):C 0.14~0.22,Si 0.12~0.30,Mn 0.40~0.65,P≤0.045,S≤0.0501.2物料平衡计算物料平衡基本项目:(1)收入项:铁水、废钢、溶剂(石灰、萤石、白云石)、氧气、炉衬蚀损、铁合金。
(2)支出项:钢水、炉渣、烟尘、渣中铁珠、炉气、喷溅。
根据铁水、渣料质量及其冶炼钢种的要求,采用单渣法操作。
为了简化运算,以100 kg铁水为计算基础。
1.2.1渣量及其成分计算(1)铁水中元素氧化量(表1-6)氧化量=元素在铁水中的含量–元素在钢水中的含量表1-6 铁水中的元素氧化量由表1-6知:脱磷率= 0.135 / 0.15×100% =90%;脱硫率 =0.009 /0.025 ×100% =36%;钢中残锰量 =0.17 /0.5 ×100% =34%.(2)各元素耗氧量及氧化产物量(表1-7)表1-7 铁水中元素氧化量、氧化产物量*:假定炉内气化脱硫1/3;铁的氧化由表1-13得出。
300吨转炉炼钢车间设计
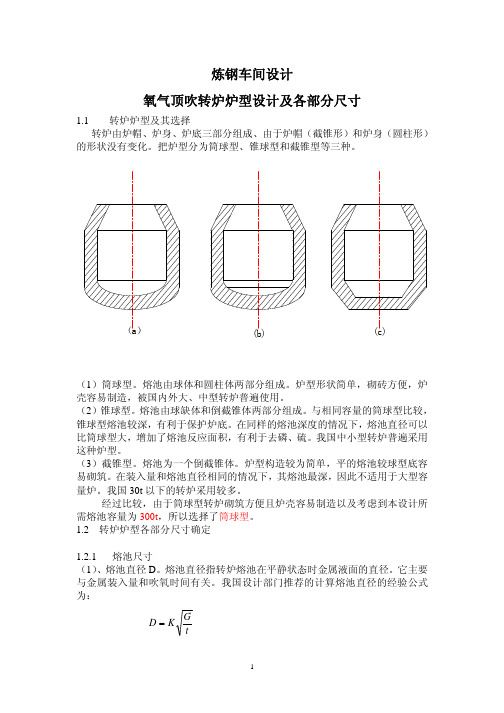
=8523-0.8358×(1600+273) =8523-1565 =6959 ㎏/m3 V 池=3×105÷6959=43.11 m3 因此 h
V池 0.046 D 3 0.79 D 2 43.11 0.046 6.213 0.79 6.212
表 3-1 氧气转炉平均冶炼时间 30 50 100-120 150 14~15 15~16 16~18 18~19 28~30 30~33 33~36 36~38
4
间夹有一层石棉板绝热层。 永久层贴紧炉壳(无绝热层时) ,维修时一般不予拆除。其主要作用是保护 炉壳。该层常用镁砖砌筑。 填充层介于永久层与工作层之间, 一般用焦油镁砂捣打而成, 厚度 80~100 ㎜。 其主要功能是减轻炉衬受热膨胀时对炉壳产生挤压和便于拆除工作层。 也有 的转炉不设填充层。本设计取用 100 ㎜。 工作层系指与金属、熔渣和炉气接触的内层炉衬,工作条件极其苛刻。目 前该层多用镁炭砖和焦油白云石砖综合砌筑。 炉帽可用二部煅烧镁砖,也可根据具体条件选用其他材质。 转炉各部位的炉衬厚度设计参考值如下表。 表 2-1 转炉炉衬厚度设计参考值 转炉容量 炉衬各部位名称 <100 100~200 >200 本设计选用 永久层厚度/㎜ 60~115 115~150 115~150 120 炉帽 工作层厚度/㎜ 400~600 500~600 550~650 500 永久层厚度/㎜ 115~150 115~200 115~200 120 炉身(加料侧) 工作层厚度/㎜ 550~700 700~800 750~850 700 永久层厚度/㎜ 115~150 115~200 115~200 120 炉身(出钢侧) 工作层厚度/㎜ 500~650 600~700 650~750 700 永久层厚度/㎜ 300~450 350~450 350~450 400 炉底 工作层厚度/㎜ 550~600 600~650 600~750 600
转炉技术参数
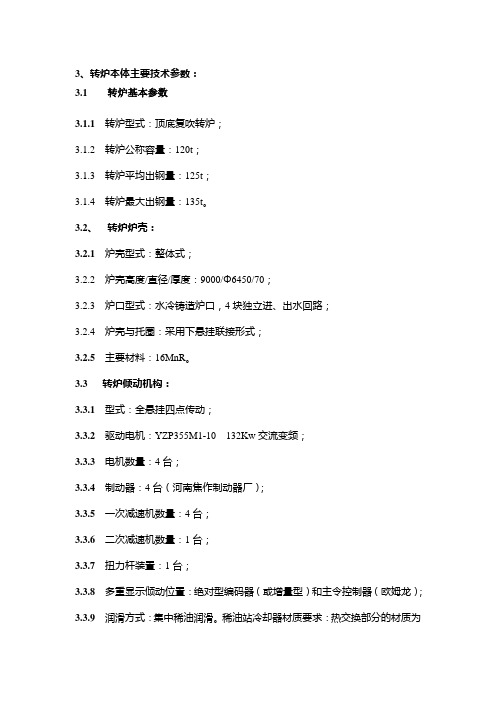
3、转炉本体主要技术参数:3.1 转炉基本参数3.1.1 转炉型式:顶底复吹转炉;3.1.2 转炉公称容量:120t;3.1.3 转炉平均出钢量:125t;3.1.4 转炉最大出钢量:135t。
3.2、转炉炉壳:3.2.1 炉壳型式:整体式;3.2.2 炉壳高度/直径/厚度:9000/Φ6450/70;3.2.3 炉口型式:水冷铸造炉口,4块独立进、出水回路;3.2.4 炉壳与托圈:采用下悬挂联接形式;3.2.5 主要材料:16MnR。
3.3 转炉倾动机构:3.3.1 型式:全悬挂四点传动;3.3.2驱动电机:YZP355M1-10 132Kw交流变频;3.3.3 电机数量:4台;3.3.4制动器:4台(河南焦作制动器厂);3.3.5一次减速机数量:4台;3.3.6二次减速机数量:1台;3.3.7扭力杆装置:1台;3.3.8多重显示倾动位置:绝对型编码器(或增量型)和主令控制器(欧姆龙);3.3.9 润滑方式:集中稀油润滑。
稀油站冷却器材质要求:热交换部分的材质为不锈钢316L,板式换热形式;管式冷却器材质为B10镍铜合金管。
集中稀油润滑站必须要有加热器、冷却器、液位计(流量超过250L用)、空气滤清器、回油过滤器等附件。
必须具备完整性。
选用螺杆泵(黄山、天津厂)。
3.4 一次减速机:3.4.1 精度:6级;3.4.2 齿面硬度:硬齿面;3.4.3齿轮主材料:20CrNi2MoA;3.4.4箱体:焊接式;3.4.5轴承:双列圆锥滚子轴承(瓦轴);单列深沟球轴承(瓦轴)。
3.5 二次减速机:3.5.1 精度:7级;3.5.2齿面硬度:中硬齿面;3.5.3齿轮:焊接式;3.5.4 齿圈材料:35CrMo;3.5.5箱体:焊接式;3.5.6轴承:单列圆柱滚子轴承()NU18/1250CC540(φ1500/φ1250/112);X圆柱滚子轴承(瓦轴)1250 DXRO--CA(φ1480/φ1250/70)。
300T转炉安装技术总结
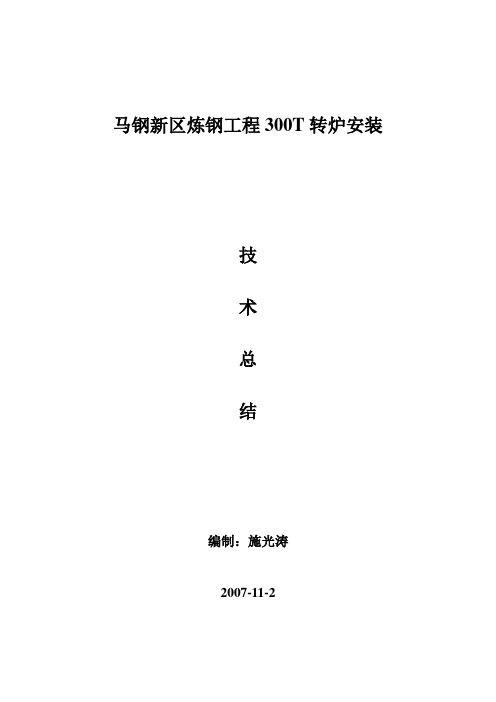
马钢新区炼钢工程300T转炉安装技术总结编制:施光涛2007-11-21.概述马钢新区“十一五”技术改造与结构调整项目:新建转炉与钢水精炼设施工程,在主厂房JK跨12-14线,一期工程安装2台全国最大,具有世界先进水平的300t转炉,采用顶底复合吹冶炼工艺,计算机动态控制,最大出钢量:320t/炉。
炉壳与托圈之间采用“奥钢联”ConLink连接技术:对称三点悬挂装置固定,每个固定点设上、下关节轴承,连接座分别焊接在下部炉体和托圈下方,在两耳轴的托圈下方设两组水平制动装置,主要承受转炉冶炼过程中水平方向的载荷。
倾动机构采用4点啮合全悬挂柔性传动装置,用扭力杆来平衡传动机构的扭矩。
每台300t转炉托圈总重:262t,炉壳重:238t,倾动装置重:170.663t,悬挂、制动装置重约:78t。
由于每台转炉具有体积大,组装后重达700t,安装位置无法用行车直接吊装到位,炉前12.2m操作平台,钢柱和基础、钢梁设计未考虑“滑移法”所承受的荷载。
宝钢、武钢、鞍钢的大型转炉都采用钢包“台车法”进行安装,但移动时易产生晃动、稳定性差,还不能将转炉及倾动装置整体移动到位。
经过多次商讨和研究,最终确定采用“组合法”进行安装。
“组合法”:将两台钢包台车连接在一起,在台车上设置支撑架撑住托圈,再将炉体吊至托圈上,同时在耳轴轴承座下方的平台梁上设置圆棒辊杠,通过台车移动和辊杠滚动一次性将转炉炉体、托圈、倾动装置安装到位。
这种方法确保了移动过程中的平衡和稳定,既安全又节省了安装时间。
2.安装工艺流程:3.施工准备3.1炉前▽12.2m操作平台,除留出托圈、炉壳和传动机构安装所需的位置外,按附图一所示编号的钢柱、钢梁必须安装到位.,炉下钢包车轨道施工结束;但28#钢柱待转炉安装到位以后才能安装。
3.2基础验收:接受、检查、复测转炉基础的中间交接资料;3.3基准点和埋设中心标板的埋设(附图二):以厂房柱基础中心为基准测量转炉安装中心并埋设中心标板,以测量控制网的基准标高为基准点埋设基准点;定期对基础进行沉降观测。
5 氧气转炉设计与车间设计-顶底复吹转炉设计

2.5.1 炉型主要参数及尺寸的确定
D (3)炉子尺寸的计算 D底 1)熔池直径的计算 根据我国设计部门推荐熔池直径,通常取熔池液面线 与截锥部分平齐,则 D底 (0.65 0.85) D
Vc= K1h D2, Vc= T/ρ,故T/ρ = K1h D2,则
D底-熔池底直径;T-转炉公称容量; K1、 K2-系数 见P30表2-9;h-熔池深度
对弱搅拌型,底吹气体采用氮气,会使钢中氮的含量 增加,这对要求含氮量低的钢水是不适宜的; 措施:吹炼前期(2/3时间段)吹氮,后期(1/3时间段)吹 氩,这样既可节省氩气又不致使钢中含氮量有明显增 加。 对于强搅拌型,采用顶底复合吹氧时,关键在于调节 顶吹与底吹氧气的流量比,以控制渣中氧化铁的含量; 顶底复合吹氧转炉炉内产生两个火点区,即下部火点 区和上部火点区: 下部火点区 可使由炉底吹入的氧气在氧气喷嘴周围 形成高温反应区,而进入高温反应区的氧气会剧烈膨 胀引起该区的过热金属对流,从而加剧熔池搅拌,进 而促进熔池脱碳。 上部点火区 主要促进熔渣的形成和脱碳反应。
类型
低压复吹 中压复吹 底部供气总管压力 MPa ≤2.5 2.5-3.0
代表性技术
容易堵塞,已经被淘汰 新日铁LD-CB法、日本钢管NK-CB法 日本川崎的LD-KGC法,底部供气强度可 以达到3.0 Nm3/t.min,吹炼效果好,设备 费用及运转费用比LD-CB法高;
高压复吹
6
3.0-5.0
2.5 顶底复吹转炉炉型及其主要参数
顶底复吹转炉吹炼工艺特点
反应速度快,热效率高,可实现炉内二次燃烧; 吹炼后期强化熔池搅拌,使钢—渣反应接近平衡; 保持顶吹转炉成渣速度快和底吹转炉吹炼平稳的双重优点; 由于搅拌力增强,进一步提高了钢水中的残锰量,提高了熔 池脱磷脱硫的冶金效果; 为了解顶底复吹炼转炉熔池的搅拌效果,同时使用两支副枪 在两个顶吹和顶底复吹熔池的不同点进行测温取样实验的结果 表明:顶吹转炉吹炼熔池中,含碳量为0.2%以下的低碳区内, 偏差值最大可为±0.07%;而在顶底复合吹炼中,即使在高碳 区内偏差值仅处于± 0.02%范围内,足见碳含量的分布均匀程 度在顶底复合吹炼法中大有改善,复合吹炼法的熔池温度均匀 化也有同样的良好效果。 改善了渣-钢的平衡条件,避免冶炼低碳钢(C=0.01~0.02%) 钢渣的过氧化;
- 1、下载文档前请自行甄别文档内容的完整性,平台不提供额外的编辑、内容补充、找答案等附加服务。
- 2、"仅部分预览"的文档,不可在线预览部分如存在完整性等问题,可反馈申请退款(可完整预览的文档不适用该条件!)。
- 3、如文档侵犯您的权益,请联系客服反馈,我们会尽快为您处理(人工客服工作时间:9:00-18:30)。
转炉炉型设计计算
1.1原始数据
(1)、转炉的公称容量为300t 。
(2)、采用顶底复吹冶炼工艺
1.2 转炉的炉型选择
图为常见转炉炉型
(a)筒球型; (b)锥球型; (c)截锥型
根据原始条件及采用顶底复吹工艺的要求,为便于安装底部供气元件,要求转炉底部为平的,所以本设计将采用截锥型炉型作为设计炉型。
1.3炉容比
炉容比系指转炉有效容积与公称容量之比值。
转炉炉容比主要与供氧强度有关,与炉容量关系不大。
从目前实际情况来看,顶底复吹转炉炉容比一般取0.85~0.95m 3/t 。
本设计为300t ,取V/T=0.92 1.4熔池尺寸的计算 熔池直径的计算公式
t
G
k
D 式中 D ——熔池直径,m ;
G ——新炉金属装入量,t ,可取公称容量; K ——系数,参见表1-1;
t ——平均每炉钢纯吹氧时间,min
表1-1 系数K 的推荐值
b.确定吹氧时间
表1.2 推荐的转炉纯吹氧时间
本设计的转炉公称容量为300t ,
又根据国家关于新建转炉的要求,吹氧时间在16min , 所以选择的吹氧时间为16min 。
取K=1.50 则)(495.616
30050.1m t G K D =⋅=⋅
= ② 截锥型熔池深度的计算公式为:
)(822.1495.6574.0119
.44574.0574.02
22m D V D V h =⨯=⨯==
)
(金池 V 池=G/Y=44.119m 3 其中Y=6.8t/ m 3 ③熔池其他尺寸确定.
)(546.4495.67.07.01m D D =⨯== 1.5炉帽尺寸的确定 ①炉口直径d 0.取
)(2475.3495.65.00m d =⨯= ②炉帽倾角: 取︒60 ③炉帽高度H 帽: 取H 口=400mm ,
)(76.260tan )2475.3495.6(2
1
tan )(2100m d D H =⨯-=⋅-=
θ锥 则整个炉帽高度为:
)(06.33.076.2m H H H =+=+=锥口帽 在炉口处设置水箱试水冷炉口。
炉帽体积:
3
20022022.6174.5848.2)
(12
4
m d Dd D H H d V V V =+=++⋅+
⋅⋅=+=锥口锥口帽π
π
1.6炉身尺寸确定
①炉膛直径D 膛=D(无加厚型)=6.495 m
②根据炉熔比为0.92,可求出炉子总容积为
)(27630092.03m V =⨯=总
)(66.17012.4422.612763m V V V V =--=--=帽池总身
③炉身高度
)(15.5)495.6(4
66
.1704
2
2
m D V H =⋅=
⋅=
π
π
身
身
则炉型内高
)(21.815.506.3m H H H =+=+=身帽内 1.7出钢口尺寸的确定 ①出钢口直径
)(24.030075.16375.163m T d T =⨯+=+= ②出钢口衬砖外径:
)(44.124.066m d d T ST =⨯== ③出钢口长度:
)(68.124.077m d L T T =⨯==
① 出钢口倾角β:︒=0β 1.8炉衬厚度确定
根据设计任务书:要求炉龄>2000,每冶炼一炉钢炉衬侵蚀厚度为
0.30~1.20mm/炉,拆炉是要求工作层应有80~100mm的残留层,
0.3×2000+100=700<850
所以炉身工作层选850mm,永久层选150mm.填充层100mm,
总厚度为:850+150+100=11000mm
炉壳内径为:
⨯
D=
D
=
=
2m
+
⨯
+
.8
695
(
1.1
1.1
.6
)
495
2
壳内
炉帽工作层600mm,永久层150mm.
炉底工作层800mm,
炉底永久层用标准镁砖砌一层455mm,
则炉底砖衬总厚度为800+455=1255mm
故炉壳内型高度为
06
.3
.5m
15
+
=
+
+
H=
.1
287
(
)
.1
.
11
822
255
壳
工作层材质全部采用镁碳砖。
1.9炉壳厚度确定
炉身部分选85mm厚的钢板,炉帽和炉底部分选用70mm厚的钢板.则
H
07
H=
.0m
11
=
+
=
+
.
357
(
)
.
11
07
287
.0
总
内
1.10验算高径比
30.1695
.8357
.11==壳总D H 符合高宽比推荐值1.25~1.45之间,因此认为所设计的炉子尺寸基本上是合适的,能够保证转炉的正常冶炼进行。
根据上述计算的炉型尺寸绘制出炉型如图所示。