基于ANSYS的O形密封圈磨损仿真方法研究
基于ANSYS的聚四氟乙烯密封圈仿真研究

基于ANSYS的聚四氟乙烯密封圈仿真研究作者:芦付臣张春堂于洋来源:《中国科技博览》2014年第34期[摘要]本文通过ANSYS软件对聚四氟乙烯密封圈进行有限元分析,研究了其密封性能,得到了安装状态和加载状态下聚四氟乙烯密封圈的等效应力分布和接触压力分布云图,发现聚四氟乙烯密封圈在正常情况下均能较好的密封能力,并可以密封较高压力的介质。
[关键词]聚四氟乙烯;密封圈;仿真研究;ANSYS中图分类号:TH137 文献标识码:A 文章编号:1009-914X(2014)34-0317-01引言聚四氟乙烯密封圈是由一个相对较薄的聚四氟乙烯环包覆一个橡胶O形圈组成,属于挤压式滑动密封。
它是靠聚四氟乙烯包覆环与轴和沟槽的表面相接触,在预压缩力和介质压力的共同作用下使聚四氟乙烯包覆环变形堵住轴与孔的间隙,橡胶O形圈被压缩也产生弹性力作用于包覆环,增加接触面的接触压力,阻抑油液流向低压区发生泄漏,从而实现密封。
目前,密封件的设计大多依靠实验进行,实验的诸多因素都会造成密封误差,导致密封实际应用时失效。
随着有限元技术的迅速发展和日趋成熟,设计人员越来越多的将各种实验通过相关的有限元软件来进行模拟分析,这不仅降低了实验成本,还缩短了产品的设计周期。
将有限元法引入到了密封件的设计上,对所设计的密封结构进行仿真分析,可以得到密封件的应力分布云图以及接触压力曲线等与密封能力直接相关的参数,对密封的寿命进行预测。
本文通过ANSYS 软件对聚四氟乙烯密封圈进行有限元分析,对其综合等效应力及接触应力的分布进行研究。
1 建立聚四氟乙烯密封圈有限元模型聚四氟乙烯密封圈模型包括旋转轴、O型圈、密封导套等组成。
在安装挤压的过程中,旋转轴与密封导套相对于密封件的弹性变形量极小,可以将旋转轴与密封导套近似看作刚体,以简化模型。
旋转轴与密封导套的材料均为不锈钢1Cr18Ni9Ti,弹性模量为210GPa,泊松比为0.3。
有限元分析过程中,鉴于其边界条件的复杂性,故将密封结构的旋转轴和密封导套作为整体进行分析。
ANSYS磨损分析报告

用有限元的方法模拟滑动摩擦磨损摘要磨损往往是影响产品寿命的一个主要因素。
因此磨损预测就成为工程的一个重要部分。
这篇论文介绍了用有限元软件ANSYS来模拟磨损的方法。
用线性磨损定律和欧拉解析积分提出了一个模型化的模拟程序。
然而,还要考虑保证模型的正确性和数学方法的收敛性。
分别用实验和有限元的方法分析了球形pin-on –disk系统在没有润滑条件下的接触问题,使用了Lim 和Ashby磨损图来区分磨损机理。
在给定几何尺寸和载荷的条件下,可以用有限元的方法模拟磨损,得到磨损率对滑动距离的对应关系。
有限元软件ANSYS非常适合解决接触问题和磨损模拟。
实际磨损率的分布X围在±40-60%的界限内会导致磨损模拟结果相当大的偏离。
因此这些结果必须在一个相对的值上进行估测,从而比较不同的设计。
关键词:磨损模拟;FEA;磨损试验;接触温度1.绪论摩擦副之间最可靠的摩擦学行为的知识可以通过做磨损实验来获得。
然而,当特别是设计改变时需要在日常的内部程序基础上进行迅速的估测。
已经进行了大量的研究工作来帮助设计者实现这一步。
已经证实一个给定系统滑动磨损的主要参数是接触载荷和相对滑动速度。
速度由机构运动来决定。
系统载荷怎么影响接触应力是很复杂的一个问题。
第一个分析两个弹性实体接触应力的人是赫兹。
他认为接触体是弹性的,接触部分为椭圆形,而且没有摩擦的。
这些假设被用在接触应力的计算中。
磨损发生在机械构件相互接触时。
一个重要的实际问题是在给定的时间里有多少的材料损失。
由于功能和加工误差等表面的形状是不同的。
而且会因为磨损和弹性变形而改变。
因此压力的分配就依赖于这些条件。
有限元的方法是一个通用的工具来解决应力应变的问题。
这篇论文使用有限元软件ANSYS5.0A分析了接触压力和磨损模拟。
2. 磨损模型磨损过程可以认为是动态的,由许多参数决定,这个过程的预测可以看作是一个初始值的问题。
从而磨损率就可以由一个总的方程来描述。
基于ANSYS的橡胶O型密封圈仿真分析

图1 二维计算模型网格图
1.2 数值模型
从物理意义上讲,两接触体之间不会相互渗
稳态力加载后,可得到刚度变形情况,并进而得出密封圈刚度—变形量关系曲线,如图3所示。
2.2 动力加载结果
对模型进行瞬态分析,并考虑材料的阻尼特性。
在ANSYS中,大部分动态阻尼分析被处理为粘滞阻尼[4],
F=[C]x (2)其中,[C]为阻尼常数,根据Reyleigh阻尼定义,[C]= [M]+ β[K]。
O型密封圈的橡胶阻尼属于β型阻尼,根据表1计算出阻尼率为0.07,刚度阻尼常数为0.008 9。
对模型输入压缩量为0.266 5 mm,交变位移函数为0.025sin(0.25×2π×t)的激励后,位移响应和载荷响应如图4和5所示。
可以看出,在0.180 82 s 前系统处于瞬态响应,之后趋于为稳态。
稳态部分的滞回曲线如图6所示。
(a)总变形量
(b)等效应力图2 静力仿真结果图3 刚度—变形量曲线
·
图4 位移响应
图5 载荷响应
图6 滞回曲线。
防止O形密封圈出现安装损伤的措施与方法

防止0形密封圈出现安装损伤的措施与方法王会,王迪,张红(西安航空制动科技有限公司,陕西兴平713106)摘 要:0形密封圈的安装质量影响液压、气动产品的密封性,通过分析0形密封圈的损伤机理,从密封结构设计和装配细节两个方面,对避免0形密封圈出现安装损伤的措施与方法进行了归纳说明。
关键词:0形密封圈;损伤机理;结构设计;装配方法中图分类号:TB42 文献标志码:A文章编号:1002-2333( 2021)05-0157-03Measures and Methods to Prevent Installation Damage of O-type Sealing RingWANG Hui, WANG Di, ZHANG Hong(Xi'an Aviation Brake Technology Co., Ltd., Xingping 713106, China)Abstract : The installation quality of O-type sealing ring affects the sealing property of hydraulic and pneumatic products.This paper analyzes the damage mechanism of O-type sealing ring, the measures and methods are summarized to avoid installation damage of O-type sealing ring from two spects of sealing structure design and assembly details.Keywords : O-type sealing ring; damage mechanism; structure design; assembly methods0引言O 形密封圈因为结构简单,目前仍是液压、气动产品 使用最为广泛的密封零件,它的安装质量直接关系到产 品的密封性。
##关于橡胶O形密封圈的Ansys分析

第28卷第4期 辽宁石油化工大学学报 Vo l.28 No.4 2008年12月 JOU R N AL OF L IA ON IN G U N IV ERSIT Y O F PET R OL EU M&CH EM ICA L T ECHN O LO GY Dec.2008文章编号:1672-6952(2008)04-0048-03关于橡胶O形密封圈的Ansys分析王 杰,谢禹钧*(辽宁石油化工大学机械学院,辽宁抚顺113001)摘 要: 利用有限元分析软件AN SY S,建立了橡胶O形圈及其边界的有限元模型,分析了不同油压和初始压缩率下形状的变化和应力的分布,以及最大接触压力和油压、初始压缩率的关系,描述了O形圈可能出现裂纹的位置,为合理地安装和使用提供了理论依据。
关键词: O形密封圈; Ansys; 接触压力; 有限元中图分类号:T Q336.42 文献标识码:AA nsys A nalysis of Rubber O-Sealing RingWAN G Jie,XIE Yu-jun*(Schoo l of M echanical Engineer ing,L iaoning Univer sity of P etr oleum&Chemical T echnolo gy,Fushun L iaoning113001,P.R.China)Received19M ay2008;r evised12Sep tember2008;accep ted8October2008Abstract: By utilizing f inite element analysis softw are A N SY S,a finite element model fo r r ubber O-sealing r ing and its bo undry w as set up.T he chang e o f shape and stress distr ibut ion under different oil pressur e and initial compressibility w as analyzed,and the relatio ns betw een max imum contact str ess,o il pressure and initial co mpr essibility was deduced.T hen the po sitio n o f po ssible cr ack w as described,w hich is a t heo retical basis fo r r easo nable installation and use.Key words: O-sealing ring;A nsys;Contact pressur e;F inite element*Co rr esponding author.T el.:+86-413-6865160;fax:+86-413-6865160;e-mail:y jx ie@O形橡胶密封圈具有结构紧凑、制造简单、拆装方便、成本低廉等特点,因此被广泛应用于汽车、动力、机械及石油化工等领域。
航天器中一种典型o形密封圈的有限元分析

航天器中一种典型o形密封圈的有限元分析中国近年来发展的航天技术已取得了巨大的进步,无论是在航天器的设计过程中,还是在航天器制造过程中,技术的发展取得了巨大的成就。
航天器的设计是一个复杂的过程,其中关键的部件之一就是密封圈,它是航天器制造的重要组成部分,起着重要的作用。
因此,密封圈如何设计和分析成为了航天器设计过程中至关重要的问题。
在航天器设计过程中,有一种典型的O形密封圈受到了广泛的关注,这种密封圈是由一条O形型的弹性环和一排放射形钉所构成,它们能够形成一个重要的密封和连接机构。
密封圈的设计必须确保其具有良好的性能,因此,密封圈的分析成为航天器设计过程中的一个重要方面。
有限元分析是用来计算复杂结构力学特性的一种算法。
它是以网格模型为基础,以节点为元素,通过网格划分复杂结构,定位节点所代表的结构元素,并对节点处的力学场进行分析和数字模拟,来预测结构的力学性能。
有限元分析在航天器设计中得到了广泛的应用,能够有效地预测结构的力学行为,节省大量的计算时间和资源。
本文的目的是使用有限元分析技术对航天器中的一种典型O形密封圈进行分析。
首先,将O形密封圈的几何特征详细地建模出来,用Abaqus有限元分析软件来建立有限元模型,并确定有限元模型的各个参数。
其次,有限元分析中的网格划分也是很重要的,因此,我们需要使用网格分析软件对O形密封圈的特征进行精细网格划分,以便对密封圈的数值模拟进行分析。
最后,利用网格划分并建立的有限元模型,在Abaqus软件中进行有限元分析,得到计算结果,也就是O形密封圈的受力分析结果,然后根据计算结果对密封圈的设计进行修改,以改善密封性能和使用寿命。
以上就是本文对航天器中一种典型O形密封圈的有限元分析的简要介绍。
有限元分析对于航天器设计有着至关重要的作用,它能够有效地预测结构的力学性能,提高设计质量,降低设计成本。
基于Ansys的橡胶O形密封圈的密封性能有限元分析
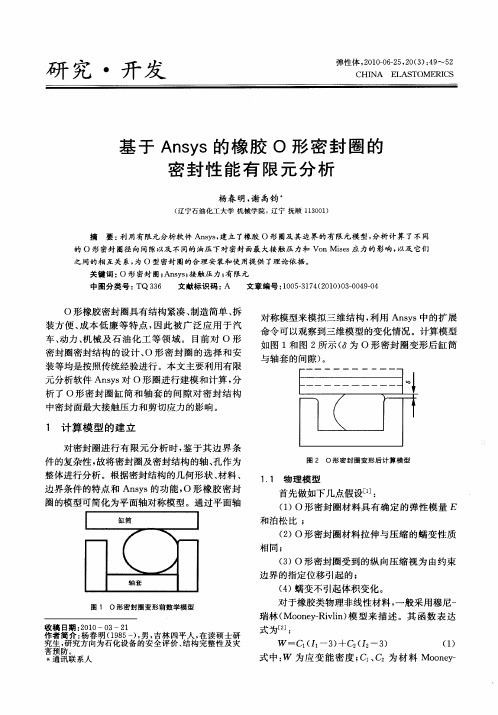
(3)
式中 :△u_A为橡胶密封圈上的一点 A 的增量位移
表 1 不 同油 压 、不 同径 向间 隙 条 件 下 最 大 Yon Mises应 力 的 数 值 N N /MPa
向量 ;,z为密封刚体的单位法 向向量 ;H 为接触距
离 容 限 。
若 满足 式 (3),则认 为 A点 与 刚体 接 触 上 了 。
接 触 问题属 于带 约 束 条 件 的 泛 函极 值 问题 ,最 常 用 的方 法有 Lagrange乘 子法 、罚 函数 法 以及 基 于 求 解器 的直 接 约 束 法 。本 文 采用 罚 单 元 法 ,在 对 模 型进行 完 网格 划 分 后 ,在 2个 可 能接 触 的界 面 上 的节 点之 间建 立接 触单 元 ,来 求解 O 形密 封 圈 与 刚体 间 的接触 问题 ]。
弹 性 体
第 2O卷
Rivlin系数 ; z为 第一 、第二 应变 张量 不变 量 。 裂纹 。而接触压力 的大 小反 应 了 O形 圈 的密封 能
应 力应 变关 系 即为 : a=OW /Oe
力 ,o形 圈保证 密封 的必要 条件是最 大接触 压力 大 (2) 于或 等于油 压 。所 以这 里 主要 利用 Ansys软 件分
摘 要 :利 用有 限元分析软件 Ansys,建 立 了橡胶 0形 圈及其 边界 的有 限元模 型,分析 计算 了不 同 的 0 形 密封 圈径 向 间 隙 以及 不 同 的 油压 下 对 密 封 面 最 大接 触 压 力 和 Von M ises应 力 的 影 响 ,以及 它 们 之 间 的相 互 关 系 ,为 0 型 密封 圈 的合 理 安 装 和 使 用提 供 了理 论依 据 。
(2)不 同油 压 、不 同径 向间 隙条 件 下 ,最 大接 触压 力 的数值 如 表 2所 示 。
磨损问题的仿真求解研究
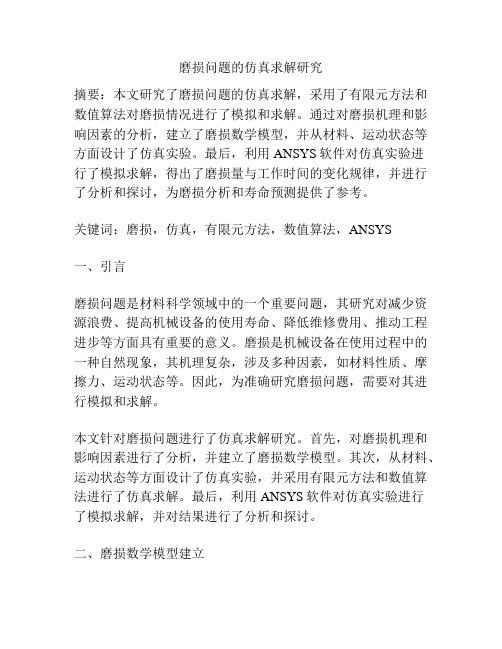
磨损问题的仿真求解研究摘要:本文研究了磨损问题的仿真求解,采用了有限元方法和数值算法对磨损情况进行了模拟和求解。
通过对磨损机理和影响因素的分析,建立了磨损数学模型,并从材料、运动状态等方面设计了仿真实验。
最后,利用ANSYS软件对仿真实验进行了模拟求解,得出了磨损量与工作时间的变化规律,并进行了分析和探讨,为磨损分析和寿命预测提供了参考。
关键词:磨损,仿真,有限元方法,数值算法,ANSYS一、引言磨损问题是材料科学领域中的一个重要问题,其研究对减少资源浪费、提高机械设备的使用寿命、降低维修费用、推动工程进步等方面具有重要的意义。
磨损是机械设备在使用过程中的一种自然现象,其机理复杂,涉及多种因素,如材料性质、摩擦力、运动状态等。
因此,为准确研究磨损问题,需要对其进行模拟和求解。
本文针对磨损问题进行了仿真求解研究。
首先,对磨损机理和影响因素进行了分析,并建立了磨损数学模型。
其次,从材料、运动状态等方面设计了仿真实验,并采用有限元方法和数值算法进行了仿真求解。
最后,利用ANSYS软件对仿真实验进行了模拟求解,并对结果进行了分析和探讨。
二、磨损数学模型建立磨损数学模型是研究磨损问题的重要基础。
在建立磨损数学模型时,需要考虑材料性质、运动状态、受力情况等多种因素。
本文基于磨损机理和影响因素的分析,建立了如下的磨损数学模型:$$W = kHd$$其中,$W$表示磨损量,$H$表示受力情况,$d$表示工作时间,$k$为比例系数。
该数学模型考虑了磨损与受力情况、工作时间、材料性质等因素的关系。
其中,受力情况是决定磨损量的重要因素,其受力情况的大小和方向都会对磨损量产生影响。
三、仿真实验设计为了验证磨损数学模型的有效性,本文利用有限元方法和数值算法对磨损情况进行了模拟和求解。
具体的仿真实验设计如下:1. 材料选择:本文选择了工程塑料作为材料,其具有良好的韧性和抗磨损性能。
2. 运动状态:本文采用了滑动摩擦运动状态,其运动状态为水平滑动,速度恒定,摩擦力为定值。
- 1、下载文档前请自行甄别文档内容的完整性,平台不提供额外的编辑、内容补充、找答案等附加服务。
- 2、"仅部分预览"的文档,不可在线预览部分如存在完整性等问题,可反馈申请退款(可完整预览的文档不适用该条件!)。
- 3、如文档侵犯您的权益,请联系客服反馈,我们会尽快为您处理(人工客服工作时间:9:00-18:30)。
基于ANSYS的O形密封圈磨损仿真方法研究常凯【摘要】Many products with wear-failure of O-ring appear in production.However,there is no related method of seal wear simulation to analyze these product issues.For solving this problem,firstly a method used for wear simulation of O-ring is proposed.The method is based on Archard friction and wear model and is implemented by structural analysis and thermal analysis of ANSYS software.The influence of contact pressure and frictional heat on the friction and wear are considered in themethod.Meanwhile,the grid reconstruction is used to solve the problem that is difficult to simulate the material wear in the simulation.The whole simulation process is realized by programming.Then according to engineering practice,a basis for judging the wear failure of O-ring is proposed.At last a concrete example of applying this method is given.%针对多型采用O形密封圈的产品磨损失效且无相关磨损仿真手段的现状,基于ARCHARD的摩擦磨损模型,利用ANSYS软件结构分析与热分析功能,提出了一种用于进行O形密封圈磨损仿真计算的方法.仿真过程中综合考虑了接触压力和摩擦热对摩擦磨损的影响,采用网格重构的方法解决了仿真过程中难于对材料磨损进行模拟的问题,并将仿真过程以编程的方式实现.结合工程实际,提出了判断O形密封圈磨损失效的依据.给出了应用此方法进行计算的具体算例.【期刊名称】《液压与气动》【年(卷),期】2018(000)002【总页数】6页(P98-103)【关键词】O形圈磨损;接触压力;摩擦热;网格重构技术;失效判据【作者】常凯【作者单位】航空工业庆安集团有限公司航空设备研究所,陕西西安710077【正文语种】中文【中图分类】TH137引言在液压系统中,由于密封介质被挤压的缘故,密封装置可能会直接与运动的零件接触,这使得由于接触产生的磨损成为影响密封寿命的一个重要因素。
在工作过程中,由于磨损引起的密封零件材料的损失会使密封压力降低从而引起泄漏。
严重的泄漏会导致整个液压系统的失效甚至造成严重的安全事故。
因此,对密封磨损过程以及磨损对密封压力的影响进行研究是十分必要的。
目前对于材料磨损的研究大都采用实验的方法来进行[1],其中销盘实验是研究材料磨损的一种常用方法。
一个设计合理的实验可以较好地模拟实际的工况从而预测密封材料的磨损。
然而这种实验需要耗费大量的物力和财力,即使针对同一种材料,初始条件的不同,实验结果也会有很大不同,使得实验的通用性很差,因此实验的方法不太适合应用于密封的设计阶段。
基于这些原因,许多学者开始利用数值仿真的方法来进行磨损方面的研究,其中有限单元法应用最为广泛。
Podra[2]利用有限元仿真的方法研究了金属和陶瓷之间的磨损现象。
Goda[3]通过有限元模型研究了高分子聚合材料的摩擦和磨损行为。
但这些研究的对象大都集中在硬材料上,对于磨损量更大的软材料,比如橡胶等材料,大都是通过实验的方法来研究其磨损现象和机理[4-5],对其仿真方法研究较少。
然而这些材料广泛应用于各类工程实际中,其磨损也是引起失效的重要因素,采用合理的仿真方法对其摩擦磨损行为进行预测,对于完善产品设计,提升产品性能具有重要意义。
本研究就是针对采用橡胶材料的O形密封圈进行磨损仿真研究的方法进行探索。
1 研究对象与磨损模型1.1 研究对象O形密封圈广泛应用于液压产品中需要密封的场合,防止泄漏,保证产品的正常工作。
O形密封圈常用在轴向静密封和轴向往复密封场合,此类密封结构中O形密封圈安装于轴或轴套上的沟槽中,由轴和轴套的配合对密封圈施加一定的压缩量,进而产生压力,实现对介质的密封(如图1、图2所示)。
图1 O形密封圈图2 O形密封圈安装示意1.2 磨损模型的选用对于磨损的研究,主要有IBM计算法、两个配合“联接”体的磨损计算法、简单粘着磨损计算法等,通过了解各种计算方法的适用范围,选择简单粘着磨损计算法[6],即Archard模型,进行橡胶材料的磨损分析。
根据Archard模型描述:一对运动副在运动过程中材料在一段时间内的磨损体积:(1)式中, dV为指定时间段内磨损体积; K为无量纲的磨损率; H为运动副中较软材料的硬度; F为运动副间的法向力; dL为此段时间内运动副两表面之间的相对运动距离。
定义Kh=K/H为材料的磨损率,则式(1)可写为:dV=Kh×F×dL(2)将上式两端同除以磨损面积S可得:dh=Kh×p×dL(3)式中, p为运动副间正压力; dh为磨损高度。
一般情况下,压力p是一个随时间变化的量。
则在运动副匀速运动的情况下,式(3)可写为:dh=Kh×p(t)×v×dt(4)式中, p(t)为随时间变化的压力; v为运动副间相对运动速度; dt为运动时间。
式(4)即作为后续仿真分析的数学模型。
1.3 材料磨损率的实验获取[7]上节模型中Kh被称为材料磨损率,可以表述为材料在单位时间内单位载荷下材料的磨损量,在仿真分析过程中,材料磨损率是一个重要参数,为使磨损仿真具有较高的准确性和实用性,须得到较准确的材料磨损率。
通常这一参数由实验来获取。
实验设备原理简图如图3所示。
图3 橡胶磨损实验装置原理简图如图3所示,液压缸提供压力F,曲柄滑块机构提供下试件的往复运动v,再辅之以润滑装置,试件夹持装置等,共同构成磨损实验的实验装置,通过电子天平测量试件实验前后质量的变化,计算得到磨损质量dm,从而得到材料的磨损率。
磨损率:(5)式中,ρ为指橡胶材料的密度。
2 磨损仿真的有限元实现2.1 摩擦热的考虑在产品运动过程中,特别是在高速运动场合下,密封区域必然由于摩擦磨损产生热量[8],会引起密封圈的变形。
因此在仿真过程中,需将这部分热量的影响考虑进去。
流体在节点处产生的切应力可表示为:ιi=fpi(6)式中, f为摩擦系数; pi为节点i的法向压力。
则密封区域节点i处的热流密度可表示为:qi=ψιiv=ψfpiv(7)式中,ψ为机械功转换为摩擦热的比率,参考相关文献[8],可认为完全转化,即取值为1。
如下图所示,在非密封区域,认为其温度保持恒定,温度为T=Tfluid;在密封区域,热载荷为热流密度,其值为qseal(p),具体区域位置如图4所示。
图4 热载荷添加示意图虽然橡胶的热传导系数与钢材料相比很小,但由于其热膨胀系数大,所以其热变形不能忽略。
其热流密度按下面公式计算:(8)式中, qseal(p)为指密封圈的热流密度; q(p)为指密封副处总热流密度;krubber、ksteel分别为密封圈和轴的刚度。
温度的变化会引起密封圈的线性膨胀,产生变形。
对于热变形引起的应变可当作初始应变施加在有限元模型上。
对于二维模型,初始应变可按下式计算:ε0=α(T-T0)(9)式中,ε0为应变;α为材料线膨胀系数;T、T0分别为变化后温度和初始温度。
2.2 接触压力p的求解基于1.3中模型可以看出,求解随时间变化的接触压力p是进行磨损仿真的难点。
接触压力的不断变化是由于磨损过程中密封材料的不断损失而引起的,现有的分析软件均不能自动模拟材料损失,所以如何模拟材料在仿真过程中不断损失的现象是进行磨损仿真的关键。
Nandor Bekesi[9]提出了全局网格重构的方法,但这种方法对磨损过程中密封件出现尖角时的网格重划分存在困难。
有学者提出了“杀死单元法”,指出当单元的接触压力超过预设的压力极限时,这个单元就被“杀掉”。
这种方法的局限在于材料损失的模拟是以单元为最小单位的,所以材料的磨损深度同受限于单元的尺寸,对于很微小的磨损量无法仿真,而且在“杀死”单元的过程中极易造成密封件仿真模型出现尖边、尖角的情况,影响计算结果。
LI Xin[8]提出了一种新的网格重构方法,不改变单元的个数,通过调整参与磨损单元以及附近单元的尺寸来模拟材料的磨损,但是这种方法中单元尺寸调整方法的选择十分关键,否则极易造成网格的畸形,使得仿真计算无法继续。
本研究利用有限元软件ANSYS的建模及网格划分功能,磨损后通过模型重构再划分网格的方法解决了网格重构中的一系列问题。
具体网格重构方法可分为以下几个步骤:(1) 建立初始模型(O形密封圈完好无损),完成初次有限元分析[10-13],其中包含热分析,得到运动副之间的接触压力p,根据式(4)得到各节点的磨损量dh;(2) 由磨损量dh得到新的磨损节点坐标: xnew=x-dh,ynew=y;(3) 提取新的密封圈外圈节点坐标,其中参与磨损的节点坐标由(x,y)变为(xnew,ynew),其余坐标保持不变;(4) 基于ANSYS平台,以新的节点坐标作为关键点重新建立密封圈的实体模型;(5) 以自由网格的形式重新划分网格,形成密封圈有限元模型,再进行有限元分析,得到接触压力。
对式(1)~式(5)循环进行,完成整个磨损过程的仿真。
上述过程主要通过O形密封圈在磨损过程中形状的变化来模拟密封圈材料的损失,O形密封圈形状的变化可以通过图5所示。
图5 网格重构过程2.3 仿真终止条件对于仿真计算终止条件,可以通过给定计算总时间或者磨损总量来设置。
但给定的时间或磨损量是否已使密封失效则很难界定。
基于此,计算的终止选择通过判定O形圈的压缩率是否满足最小压缩率的要求来实现,这是由于相关国家标准和行业标准中给定的最小压缩率均是大量实践经验的总结,是密封圈能可靠密封的最低要求。
对于O形密封圈,其压缩量可按图6所示,如下方式计算。
图6 O形密封圈安装时轴孔配合尺寸拉伸量:(10)与α有关的系数:(11)压缩量:(12)查找相关标准,得到动密封时所要求的密封圈最小压缩量w名义,在计算过程中,每一次循环中,比较磨损后密封圈压缩率w名义与w名义的大小,当w≤w名义时,则认为密封圈已失效,计算终止。