激光焊接原理与主要工艺参数
激光焊接技术原理及工艺分析

激光焊接技术原理及工艺分析
激光焊接技术是一种高精密性焊接技术,其原理是利用高能量激光束对焊接材料进行
熔化并加热,使其达到熔化状态,然后使母材和焊材熔合,形成焊缝。
激光焊接技术具有
焊缝小、熔化深度浅、热影响区小、熔池凝固速度快、焊接速度快、成形美观等优点。
激光焊接工艺主要包括焊缝设计、焊接参数选择、设备调试、工艺控制等几个方面。
焊缝设计需要根据焊接材料的性质和焊接要求来确定焊缝的形状和尺寸。
焊接参数的选择
包括激光功率、焊缝速度、焊接气体种类和流量等,需要根据材料特性和焊接要求进行选择。
设备调试主要包括激光器的调试和光束传输系统的调试等。
工艺控制主要包括工件定位、焊接过程中的温度控制和焊接质量的检测等。
激光焊接工艺有很多种,其中比较常用的是峰值功率调制焊接、脉冲时间调制焊接和
连续波焊接等。
峰值功率调制焊接是在一定时间内增加激光功率,使焊接材料快速熔化和
凝固,从而实现焊接。
脉冲时间调制焊接是通过调节激光脉冲时间和脉冲频率,实现焊接
材料的熔化和凝固。
连续波焊接则是将激光束连续发射,通过控制焊接速度和功率,实现
材料融化和凝固。
激光焊接技术在飞机、船舶、汽车、机器人以及电子设备等领域的应用越来越广泛。
它不仅可以替代传统的焊接工艺,在提高焊接质量的同时,也能够提高生产效率和生产率。
未来,激光焊接技术有望进一步发展,成为高精度微观加工和大型结构焊接等领域的重要
工艺。
激光焊接技术原理及工艺分析
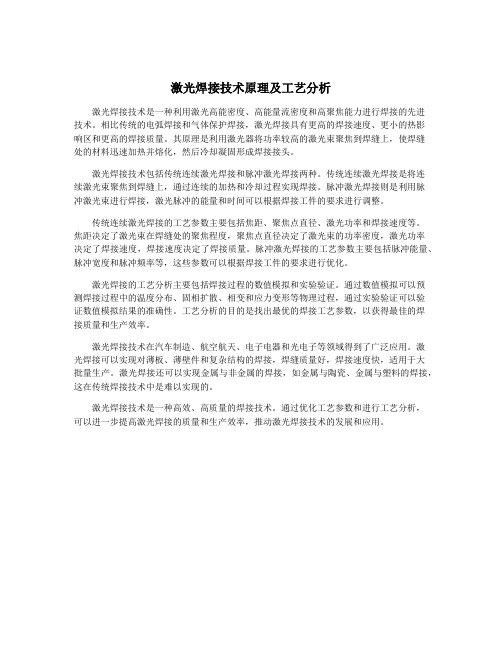
激光焊接技术原理及工艺分析激光焊接技术是一种利用激光高能密度、高能量流密度和高聚焦能力进行焊接的先进技术。
相比传统的电弧焊接和气体保护焊接,激光焊接具有更高的焊接速度、更小的热影响区和更高的焊接质量。
其原理是利用激光器将功率较高的激光束聚焦到焊缝上,使焊缝处的材料迅速加热并熔化,然后冷却凝固形成焊接接头。
激光焊接技术包括传统连续激光焊接和脉冲激光焊接两种。
传统连续激光焊接是将连续激光束聚焦到焊缝上,通过连续的加热和冷却过程实现焊接。
脉冲激光焊接则是利用脉冲激光束进行焊接,激光脉冲的能量和时间可以根据焊接工件的要求进行调整。
传统连续激光焊接的工艺参数主要包括焦距、聚焦点直径、激光功率和焊接速度等。
焦距决定了激光束在焊缝处的聚焦程度,聚焦点直径决定了激光束的功率密度,激光功率决定了焊接速度,焊接速度决定了焊接质量。
脉冲激光焊接的工艺参数主要包括脉冲能量、脉冲宽度和脉冲频率等,这些参数可以根据焊接工件的要求进行优化。
激光焊接的工艺分析主要包括焊接过程的数值模拟和实验验证。
通过数值模拟可以预测焊接过程中的温度分布、固相扩散、相变和应力变形等物理过程,通过实验验证可以验证数值模拟结果的准确性。
工艺分析的目的是找出最优的焊接工艺参数,以获得最佳的焊接质量和生产效率。
激光焊接技术在汽车制造、航空航天、电子电器和光电子等领域得到了广泛应用。
激光焊接可以实现对薄板、薄壁件和复杂结构的焊接,焊缝质量好,焊接速度快,适用于大批量生产。
激光焊接还可以实现金属与非金属的焊接,如金属与陶瓷、金属与塑料的焊接,这在传统焊接技术中是难以实现的。
激光焊接技术是一种高效、高质量的焊接技术。
通过优化工艺参数和进行工艺分析,可以进一步提高激光焊接的质量和生产效率,推动激光焊接技术的发展和应用。
(整理)laser-beam welding Microsoft Word 文档

激光焊接的原理、优缺点及工艺参数激光焊接的原理激光焊接是利用高能量的激光脉冲对材料进行微小区域内的局部加热,激光辐射的能量通过热传导向材料的内部扩散,将材料熔化后形成特定熔池。
它是一种新型的焊接方式,激光焊接主要针对薄壁材料、精密零件的焊接,可实现点焊、对接焊、叠焊、密封焊等,深宽比高,焊缝宽度小,热影响区小、变形小,焊接速度快,焊缝平整、美观,焊后无需处理或只需简单处理,焊缝质量高,无气孔,可精确控制,聚焦光点小,定位精度高,易实现自动化。
焊接特性属于熔融焊接,以激光束为能源,冲击在焊件接头上。
激光束可由平面光学元件(如镜子)导引,随后再以反射聚焦元件或镜片将光束投射在焊缝上。
激光焊接属非接触式焊接,作业过程不需加压,但需使用惰性气体以防熔池氧化,填料金属偶有使用。
激光焊可以与MIG焊组成激光MIG复合焊,实现大熔深焊接,同时热输入量比MIG焊大为减小。
激光焊接的主要优点(1)可将入热量降到最低的需要量,热影响区金相变化范围小,且因热传导所导致的变形亦最低。
(2)32mm板厚单道焊接的焊接工艺参数业经检定合格,可降低厚板焊接所需的时间甚至可省掉填料金属的使用。
(3)不需使用电极,没有电极污染或受损的顾虑。
且因不属于接触式焊接制程,机具的耗损及变形接可降至最低。
(4)激光束易于聚焦、对准及受光学仪器所导引,可放置在离工件适当之距离,且可在工件周围的机具或障碍间再导引,其他焊接法则因受到上述的空间限制而无法发挥。
(5)工件可放置在封闭的空间(经抽真空或内部气体环境在控制下)。
(6)激光束可聚焦在很小的区域,可焊接小型且间隔相近的部件。
(7)可焊材质种类范围大,亦可相互接合各种异质材料。
(8)易于以自动化进行高速焊接,亦可以数位或电脑控制。
(9)焊接薄材或细径线材时,不会像电弧焊接般易有回熔的困扰。
(10)不受磁场所影响(电弧焊接及电子束焊接则容易),能精确的对准焊件。
(11)可焊接不同物性(如不同电阻)的两种金属。
光纤激光焊接工艺原理

光纤激光焊接工艺原理光纤激光焊接是一种高精度、高效率的焊接方法,广泛应用于汽车制造、航空航天、电子设备等行业。
它利用激光束的高能量密度和光纤的柔性传导特性,将工件表面局部加热,使其熔化并形成焊缝。
本文将从光纤激光焊接的原理、工艺参数、优势和应用领域等方面进行介绍。
一、光纤激光焊接的原理光纤激光焊接的原理是利用激光束的高能量密度将焊接区域加热至熔点以上,使金属材料熔化并形成焊缝。
在光纤激光焊接中,激光器将激光束传输到焊接头部,然后通过光纤将激光束传导到焊接点。
在焊接点,激光束与工件表面交互作用,产生局部加热。
随着工件加热,金属材料熔化并形成焊缝,然后冷却固化,实现焊接。
光纤激光焊接的原理主要包括两个方面:激光束与工件相互作用和激光能量的转化。
激光束与工件表面相互作用时,激光能量被吸收,使工件表面温度升高。
当温度达到熔点以上时,金属材料开始熔化。
激光能量的转化涉及激光束的吸收、传导和辐射。
激光束通过吸收介质的能量转化为热能,然后通过传导和辐射传输到焊接点。
二、光纤激光焊接的工艺参数光纤激光焊接的工艺参数对焊接质量和效率起着重要作用。
其中,激光功率、激光脉冲频率、焦距和光斑直径是影响焊接效果的关键参数。
1. 激光功率:激光功率决定了焊接过程中的能量输入量。
适当的激光功率可以保证焊缝的充分熔化和深度穿透,提高焊接质量。
2. 激光脉冲频率:激光脉冲频率决定了激光束的作用时间。
适当的脉冲频率可以控制焊接过程中的热输入量,实现焊接参数的精确控制。
3. 焦距:焦距是指激光束从激光头到焊接点的距离。
适当的焦距可以控制激光束的聚焦深度和焦斑直径,影响焊接深度和焊缝质量。
4. 光斑直径:光斑直径决定了激光束的能量密度分布。
适当的光斑直径可以实现焊接过程中的热输入均匀分布,提高焊接质量。
三、光纤激光焊接的优势光纤激光焊接相比传统焊接方法具有许多优势。
1. 高能量密度:光纤激光焊接利用激光束的高能量密度,可以在较小的热影响区域内实现高温熔化,减少热影响和变形。
激光焊接工艺参数讲解

激光焊接原理与主要工艺参数作者:opticsky 日期:2006-12-01字体大小: 小中大1.激光焊接原理激光焊接可以采用连续或脉冲激光束加以实现,激光焊接的原理可分为热传导型焊接和激光深熔焊接。
功率密度小于104~105 W/cm2为热传导焊,此时熔深浅、焊接速度慢;功率密度大于105~107 W/cm2时,金属表面受热作用下凹成“孔穴”,形成深熔焊,具有焊接速度快、深宽比大的特点。
其中热传导型激光焊接原理为:激光辐射加热待加工表面,表面热量通过热传导向内部扩散,通过控制激光脉冲的宽度、能量、峰功率和重复频率等激光参数,使工件熔化,形成特定的熔池。
用于齿轮焊接和冶金薄板焊接用的激光焊接机主要涉及激光深熔焊接。
下面重点介绍激光深熔焊接的原理。
激光深熔焊接一般采用连续激光光束完成材料的连接,其冶金物理过程与电子束焊接极为相似,即能量转换机制是通过“小孔”(Key-hole)结构来完成的。
在足够高的功率密度激光照射下,材料产生蒸发并形成小孔。
这个充满蒸气的小孔犹如一个黑体,几乎吸收全部的入射光束能量,孔腔内平衡温度达2500 0C左右,热量从这个高温孔腔外壁传递出来,使包围着这个孔腔四周的金属熔化。
小孔内充满在光束照射下壁体材料连续蒸发产生的高温蒸汽,小孔四壁包围着熔融金属,液态金属四周包围着固体材料(而在大多数常规焊接过程和激光传导焊接中,能量首先沉积于工件表面,然后靠传递输送到内部)。
孔壁外液体流动和壁层表面张力与孔腔内连续产生的蒸汽压力相持并保持着动态平衡。
光束不断进入小孔,小孔外的材料在连续流动,随着光束移动,小孔始终处于流动的稳定状态。
就是说,小孔和围着孔壁的熔融金属随着前导光束前进速度向前移动,熔融金属充填着小孔移开后留下的空隙并随之冷凝,焊缝于是形成。
上述过程的所有这一切发生得如此快,使焊接速度很容易达到每分钟数米。
2. 激光深熔焊接的主要工艺参数1激光功率。
激光焊接中存在一个激光能量密度阈值,低于此值,熔深很浅,一旦达到或超过此值,熔深会大幅度提高。
激光焊接工艺方法和技术

激光焊接工艺方法和技术激光焊接是激光加工材料加工技术应用的重要方面之一。
70年代主要用于焊接薄壁材料和低速焊接,焊接过程属于热传导型,即激光辐射加热工件表面,表面热量通过热传导向内部扩散,通过控制激光脉冲的宽度、能量、峰值功率和重复频率等参数,使工件熔化,形成特定的熔池。
由于激光焊接作为一种高质量、高精度、低变形、高效率和高速度的焊接方法,随着高功率CO2和高功率的YAG 激光器以及光纤传输技术的完善、金属钼焊接聚束物镜等的研制成功,使其在机械制造、航空航天、汽车工业、粉末冶金、生物医学微电子行业等领域的应用越来越广。
一、激光焊接的工艺参数。
1、功率密度。
功率密度是激光加工中最关键的参数之一。
采用较高的功率密度,在微秒时间范围内,表层即可加热至沸点,产生大量汽化。
因此,高功率密度对于材料去除加工,如打孔、切割、雕刻有利。
对于较低功率密度,表层温度达到沸点需要经历数毫秒,在表层汽化前,底层达到熔点,易形成良好的熔融焊接。
因此,在传导型激光焊接中,功率密度在范围在104~106W/cm2。
2、激光脉冲波形。
激光脉冲波形在激光焊接中是一个重要问题,尤其对于薄片焊接更为重要。
当高强度激光束射至材料表面,金属表面将会有60~98%的激光能量反射而损失掉,且反射率随表面温度变化。
在一个激光脉冲作用期间内,金属反射率的变化很大。
3、激光脉冲宽度。
脉宽是脉冲激光焊接的重要参数之一,它既是区别于材料去除和材料熔化的重要参数,也是决定加工设备造价及体积的关键参数。
4、离焦量对焊接质量的影响。
激光焊接通常需要一定的离做文章一,因为激光焦点处光斑中心的功率密度过高,容易蒸发成孔。
离开激光焦点的各平面上,功率密度分布相对均匀。
离焦方式有两种:正离焦与负离焦。
焦平面位于工件上方为正离焦,反之为负离焦。
按几何光学理论,当正负离做文章一相等时,所对应平面上功率密度近似相同,但实际上所获得的熔池形状不同。
负离焦时,可获得更大的熔深,这与熔池的形成过程有关。
手持激光焊工艺焊接参数
手持激光焊工艺焊接参数手持激光焊工艺是一种高效快捷的焊接工艺,其主要应用于微细零件或未联接组件的精确加工。
这种工艺不仅具有无接触、高频率和低损耗等优点,而且特别适用于薄板和复杂构形的结构件。
而对于手持激光焊接工艺的焊接参数调节是影响焊接质量的重要因素。
一、手持激光焊接工艺1. 工艺原理手持激光焊接传统的钳工焊接方式存在无法到达的区域,操作过程繁琐且需要一定的技术要求。
手持激光焊是一种便携式的激光加工方式,通过将激光光束聚焦到较小的点上,从而产生高能量密度的热源,达到局部熔化的目的,完成部件的焊接。
2. 工艺优势与传统的焊接方式相比,手持激光焊可以大大缩短生产周期和减少物料的浪费,同时保持高精度和准确性。
此外,手持激光焊工艺还有如下优势:(1)材料使用效率高手持激光焊接过程中,激光光束能够被集成到经典焊接过程中所不可达到的难以处理的区域。
激光焊接利用高能量密度光束准确地融化焊点,从而可以在节省较大发生缺陷的部位时,使得材料使用效率更高。
(2)焊缝质量高手持激光焊接工艺焊接接头的质量比较高,其气氛是最容易控制的。
因为焊接时产生的热输入较低,从而可以减少焊接区域较大的应力问题,并保证零件焊接质量。
(3)适应性强手持激光焊接对各种材料都有很好的适应性,而且在焊接时不会改变材料的化学性质和物理特性。
二、手持激光焊接参数1. 激光功率激光功率是手持激光焊接工艺的一个重要参数。
当激光功率增加时,焊接速度会更快,但是焊缝的深度和宽度也会更大。
因此,需要根据实际的焊接要求选择适当的激光功率。
2. 焊接速度焊接速度也是手持激光焊接的重要参数之一。
当焊接速度较快时,焊缝是窄而深的。
反之,当焊接速度较慢时,焊缝会更宽而浅。
因此,在选择焊接速度时应根据实际要求进行选择。
3. 焦距焊缝的最终质量和形状与焦距有极大的关系。
当将焦距增加时,焊缝的深度会增加,而焊缝的宽度会减小,相反,当缩短焦距时,焊缝会变得更宽而更浅。
因此,需要根据实际情况进行选择。
激光焊接技术原理及工艺分析
激光焊接技术原理及工艺分析激光焊接技术是一种高效、精密的焊接方法,广泛应用于汽车制造、航天航空、电子电气、金属加工等领域。
它具有焊缝窄、热影响区小、焊接速度快、焊接变形小等优点,因此备受行业的青睐。
本文将对激光焊接技术的原理及工艺进行深入分析,以便更好地应用于实际生产中。
一、激光焊接技术原理激光焊接技术是利用高能密度激光束对工件进行局部加热,使其熔化并与填充材料熔合,从而实现焊接的一种焊接方法。
激光焊接技术的焊接原理主要包括热传导和熔化两个过程。
1. 热传导过程激光束照射到被焊接工件表面时,会迅速将能量转移到工件内部,并在其表面形成一个“热源区”。
在热源区内,温度迅速升高,使金属材料发生相变,从而产生熔化现象。
热传导过程是激光焊接的关键步骤,决定了焊接质量和效率。
2. 熔化过程一旦工件表面温度达到熔点,金属材料便开始熔化,并与填充材料一起形成一层融合的熔池。
激光束的高能密度可以使金属材料迅速熔化,从而实现高速、高效的焊接过程。
二、激光焊接工艺分析激光焊接工艺主要包括焊接设备、工艺参数、焊接过程控制等方面。
下面将分别对这些方面进行分析。
1. 焊接设备激光焊接的设备主要由激光器、光纤传输系统、焊接头及其控制系统等组成。
激光器是激光焊接的核心部件,它产生高能密度的激光束,然后通过光纤传输系统输送到焊接头。
焊接头通过镜片对激光束进行聚焦和调节,然后照射到工件表面进行焊接。
2. 工艺参数激光焊接的工艺参数包括激光功率、焦距、焊接速度、频率等多个方面。
这些参数的选择直接影响到焊接效果和质量。
一般来说,激光功率越大,焊接速度越快,焊接效果越好。
而焦距、频率等参数则需要根据具体的焊接材料和厚度进行调节。
3. 焊接过程控制激光焊接的过程控制是确保焊接质量的关键。
焊接过程需要对激光功率、焊接速度、焦距等参数进行精确控制,同时还需要考虑到工件的热变形、填充材料的均匀性等因素。
现代化的焊接设备通常配备了先进的焊接控制系统,能够通过实时监控和反馈机制来实现焊接过程的精确控制。
激光焊接技术原理及工艺分析
激光焊接技术原理及工艺分析激光焊接是一种利用高能量激光束进行材料焊接的技术。
它将激光光束聚焦到焊接点上,通过高能量密度的激光束短时间内加热材料,使其熔化并形成焊缝。
激光焊接的原理是利用激光的高强度和高能量密度。
激光是由激光器产生的一种狭窄、一致、相干的光束,具有较高的单色性和方向性。
激光束经过透镜聚焦后,能够将光束的能量集中到一个非常小的点上,从而形成高能量密度的光斑。
在这个高能量密度的光斑中,材料会迅速升温,达到熔化温度并形成焊缝。
激光焊接的工艺分析主要包括以下几个方面:1. 激光参数选择:激光焊接中,激光的功率、波长、脉冲频率等参数都会对焊接效果产生影响,需要根据具体材料和焊接要求选择合适的参数。
功率过大会产生焊缝熔穿,功率过小则焊缝质量不达标。
2. 材料选择:不同材料对激光焊接的适应性不同。
一些金属材料如铝合金、不锈钢等较容易进行激光焊接,而一些非金属材料如聚合物、陶瓷等则较难焊接。
3. 聚焦方式选择:激光焊接中,激光束的聚焦方式可以采用透镜、镜面反射等方法。
选择适当的聚焦方式可以提高焊接效果和效率。
4. 热影响区分析:激光焊接产生的高能量热源会对周围材料产生热影响,造成热变形、应力集中等问题。
需要通过优化焊接参数和调整焊接工艺,减小热影响区,降低热变形和应力。
5. 焊接质量控制:激光焊接中,焊缝形状、焊缝宽度、焊接深度等焊接质量指标直接影响焊接的可靠性。
需要通过严格控制焊接工艺参数和焊接设备的运行状态,保证焊接质量。
激光焊接技术具有焊接速度快、热影响区小、焊缝质量高等优势,已广泛应用于汽车制造、航空航天、电子电器等行业。
随着激光技术的不断发展,激光焊接技术将会在更多领域得到应用。
激光焊接技术的工艺与方法
激光焊接技术的工艺与方法激光焊接技术是一种非常重要且广泛应用于工业生产领域的焊接方法。
它利用高能量密度的激光束来加热工件表面,使其达到熔化点,然后通过材料的自身熔化来进行焊接。
激光焊接技术具有高精度、高效率和不受材料性质限制等优点,因此在汽车制造、电子设备、航空航天等领域得到广泛应用。
本文将重点探讨激光焊接技术的一些常见工艺与方法,以及其在实际应用中的一些注意事项。
一、工艺常见方法1.传统激光焊接传统激光焊接是指使用高功率连续波激光进行焊接的方法。
其工作原理是将激光束聚焦到非常小的焦点上,通过光能的聚焦来使工件表面局部熔化,形成焊缝。
该方法适用于焊接厚度较大的工件,具有焊缝宽度窄、焊缝深度大的优点。
然而,由于激光能量密度较高,容易引起工件变形和热裂纹等问题,需要进行严格的控制和预热处理。
2.脉冲激光焊接脉冲激光焊接是指使用高能量脉冲激光进行焊接的方法。
相比传统激光焊接,脉冲激光焊接的能量密度更高,激光束作用时间更短,因此在焊接过程中对工件的热影响较小。
这种方法适用于对焊接过程热输入要求较低的材料,如薄板、精密仪器等。
脉冲激光焊接还可以实现连续拼接焊接和高速激光焊接等特殊要求。
3.深熔激光焊接深熔激光焊接是一种通过在焊接过程中使工件局部熔化并加热至汽化温度,利用金属蒸汽对激光束进行抑制,从而实现深熔焊接的方法。
该方法适用于要求焊缝深度较大的工件,如不锈钢、铝合金等。
在深熔激光焊接过程中,需要控制好激光束的功率和速度,以确保焊缝的质量和形状。
二、实际应用注意事项1.材料选择在激光焊接过程中,不同材料对激光的吸收率和热传导率不同,因此在选择焊接材料时需要考虑其适应激光焊接的特性。
同时还需要考虑材料的熔点、热膨胀系数等参数,以确保焊接质量。
2.焊接参数控制激光焊接的参数包括激光功率、激光束直径、焦距、焊接速度等多个方面。
这些参数的选择和控制直接影响焊缝的质量和性能。
因此,在实际应用中需要通过试验和实践确定最佳的焊接参数。
- 1、下载文档前请自行甄别文档内容的完整性,平台不提供额外的编辑、内容补充、找答案等附加服务。
- 2、"仅部分预览"的文档,不可在线预览部分如存在完整性等问题,可反馈申请退款(可完整预览的文档不适用该条件!)。
- 3、如文档侵犯您的权益,请联系客服反馈,我们会尽快为您处理(人工客服工作时间:9:00-18:30)。
1.激光焊接原理激光焊接可以采用连续或脉冲激光束加以实现,激光焊接的原理可分为热传导型焊接和激光深熔焊接。
功率密度小于104~105 W/cm2为热传导焊,此时熔深浅、焊接速度慢;功率密度大于105~107 W/cm2时,金属表面受热作用下凹成“孔穴”,形成深熔焊,具有焊接速度快、深宽比大的特点。
其中热传导型激光焊接原理为:激光辐射加热待加工表面,表面热量通过热传导向内部扩散,通过控制激光脉冲的宽度、能量、峰功率和重复频率等激光参数,使工件熔化,形成特定的熔池。
用于齿轮焊接和冶金薄板焊接用的激光焊接机主要涉及激光深熔焊接。
下面重点介绍激光深熔焊接的原理。
激光深熔焊接一般采用连续激光光束完成材料的连接,其冶金物理过程与电子束焊接极为相似,即能量转换机制是通过“小孔”(Key-hole)结构来完成的。
在足够高的功率密度激光照射下,材料产生蒸发并形成小孔。
这个充满蒸气的小孔犹如一个黑体,几乎吸收全部的入射光束能量,孔腔内平衡温度达2500 0C左右,热量从这个高温孔腔外壁传递出来,使包围着这个孔腔四周的金属熔化。
小孔内充满在光束照射下壁体材料连续蒸发产生的高温蒸汽,小孔四壁包围着熔融金属,液态金属四周包围着固体材料(而在大多数常规焊接过程和激光传导焊接中,能量首先沉积于工件表面,然后靠传递输送到内部)。
孔壁外液体流动和壁层表面张力与孔腔内连续产生的蒸汽压力相持并保持着动态平衡。
光束不断进入小孔,小孔外的材料在连续流动,随着光束移动,小孔始终处于流动的稳定状态。
就是说,小孔和围着孔壁的熔融金属随着前导光束前进速度向前移动,熔融金属充填着小孔移开后留下的空隙并随之冷凝,焊缝于是形成。
上述过程的所有这一切发生得如此快,使焊接速度很容易达到每分钟数米。
2. 激光深熔焊接的主要工艺参数1)激光功率。
激光焊接中存在一个激光能量密度阈值,低于此值,熔深很浅,一旦达到或超过此值,熔深会大幅度提高。
只有当工件上的激光功率密度超过阈值(与材料有关),等离子体才会产生,这标志着稳定深熔焊的进行。
如果激光功率低于此阈值,工件仅发生表面熔化,也即焊接以稳定热传导型进行。
而当激光功率密度处于小孔形成的临界条件附近时,深熔焊和传导焊交替进行,成为不稳定焊接过程,导致熔深波动很大。
激光深熔焊时,激光功率同时控制熔透深度和焊接速度。
焊接的熔深直接与光束功率密度有关,且是入射光束功率和光束焦斑的函数。
一般来说,对一定直径的激光束,熔深随着光束功率提高而增加。
2)光束焦斑。
光束斑点大小是激光焊接的最重要变量之一,因为它决定功率密度。
但对高功率激光来说,对它的测量是一个难题,尽管已经有很多间接测量技术。
光束焦点衍射极限光斑尺寸可以根据光衍射理论计算,但由于聚焦透镜像差的存在,实际光斑要比计算值偏大。
最简单的实测方法是等温度轮廓法,即用厚纸烧焦和穿透聚丙烯板后测量焦斑和穿孔直径。
这种方法要通过测量实践,掌握好激光功率大小和光束作用的时间。
3)材料吸收值。
材料对激光的吸收取决于材料的一些重要性能,如吸收率、反射率、热导率、熔化温度、蒸发温度等,其中最重要的是吸收率。
影响材料对激光光束的吸收率的因素包括两个方面:首先是材料的电阻系数,经过对材料抛光表面的吸收率测量发现,材料吸收率与电阻系数的平方根成正比,而电阻系数又随温度而变化;其次,材料的表面状态(或者光洁度)对光束吸收率有较重要影响,从而对焊接效果产生明显作用。
CO2激光器的输出波长通常为10.6μm,陶瓷、玻璃、橡胶、塑料等非金属对它的吸收率在室温就很高,而金属材料在室温时对它的吸收很差,直到材料一旦熔化乃至气化,它的吸收才急剧增加。
采用表面涂层或表面生成氧化膜的方法,提高材料对光束的吸收很有效。
4)焊接速度。
焊接速度对熔深影响较大,提高速度会使熔深变浅,但速度过低又会导致材料过度熔化、工件焊穿。
所以,对一定激光功率和一定厚度的某特定材料有一个合适的焊接速度范围,并在其中相应速度值时可获得最大熔深。
图10-2给出了1018钢焊接速度与熔深的关系。
5)保护气体。
激光焊接过程常使用惰性气体来保护熔池,当某些材料焊接可不计较表面氧化时则也可不考虑保护,但对大多数应用场合则常使用氦、氩、氮等气体作保护,使工件在焊接过程中免受氧化。
氦气不易电离(电离能量较高),可让激光顺利通过,光束能量不受阻碍地直达工件表面。
这是激光焊接时使用最有效的保护气体,但价格比较贵。
氩气比较便宜,密度较大,所以保护效果较好。
但它易受高温金属等离子体电离,结果屏蔽了部分光束射向工件,减少了焊接的有效激光功率,也损害焊接速度与熔深。
使用氩气保护的焊件表面要比使用氦气保护时来得光滑。
氮气作为保护气体最便宜,但对某些类型不锈钢焊接时并不适用,主要是由于冶金学方面问题,如吸收,有时会在搭接区产生气孔。
使用保护气体的第二个作用是保护聚焦透镜免受金属蒸气污染和液体熔滴的溅射。
特别在高功率激光焊接时,由于其喷出物变得非常有力,此时保护透镜则更为必要。
保护气体的第三个作用是对驱散高功率激光焊接产生的等离子屏蔽很有效。
金属蒸气吸收激光束电离成等离子云,金属蒸气周围的保护气体也会因受热而电离。
如果等离子体存在过多,激光束在某种程度上被等离子体消耗。
等离子体作为第二种能量存在于工作表面,使得熔深变浅、焊接熔池表面变宽。
通过增加电子与离子和中性原子三体碰撞来增加电子的复合速率,以降低等离子体中的电子密度。
中性原子越轻,碰撞频率越高,复合速率越高;另一方面,只有电离能高的保护气体,才不致因气体本身的电离而增加电子密度。
表常用气体和金属的原子(分子)量和电离能=============================================================材料氦氩氮铝镁铁------------------------------------------------------------原子(分子)量 4 40 28 27 24 56电离能(eV) 24.46 15.68 14.5 5.96 7.61 7.83=============================================================从表可知,等离子体云尺寸与采用的保护气体不同而变化,氦气最小,氮气次之,使用氩气时最大。
等离子体尺寸越大,熔深则越浅。
造成这种差别的原因首先由于气体分子的电离程度不同,另外也由于保护气体不同密度引起金属蒸气扩散差别。
氦气电离最小,密度最小,它能很快地驱除从金属熔池产生的上升的金属蒸气。
所以用氦作保护气体,可最大程度地抑制等离子体,从而增加熔深,提高焊接速度;由于质轻而能逸出,不易造成气孔。
当然,从我们实际焊接的效果看,用氩气保护的效果还不错。
等离子云对熔深的影响在低焊接速度区最为明显。
当焊接速度提高时,它的影响就会减弱。
保护气体是通过喷嘴口以一定的压力射出到达工件表面的,喷嘴的流体力学形状和出口的直径大小十分重要。
它必须以足够大以驱使喷出的保护气体覆盖焊接表面,但为了有效保护透镜,阻止金属蒸气污染或金属飞溅损伤透镜,喷口大小也要加以限制。
流量也要加以控制,否则保护气的层流变成紊流,大气卷入熔池,最终形成气孔。
为了提高保护效果,还可用附加的侧向吹气的方式,即通过一较小直径的喷管将保护气体以一定的角度直接射入深熔焊接的小孔。
保护气体不仅抑制了工件表面的等离子体云,而且对孔内的等离子体及小孔的形成施加影响,熔深进一步增大,获得深宽比较为理想的焊缝。
但是,此种方法要求精确控制气流量大小、方向,否则容易产生紊流而破坏熔池,导致焊接过程难以稳定。
6)透镜焦距。
焊接时通常采用聚焦方式会聚激光,一般选用63~254mm(2.5”~10”)焦距的透镜。
聚焦光斑大小与焦距成正比,焦距越短,光斑越小。
但焦距长短也影响焦深,即焦深随着焦距同步增加,所以短焦距可提高功率密度,但因焦深小,必须精确保持透镜与工件的间距,且熔深也不大。
由于受焊接过程中产生的飞溅物和激光模式的影响,实际焊接使用的最短焦深多为焦距126mm(5”)。
当接缝较大或需要通过加大光斑尺寸来增加焊缝时,可选择254mm(10”)焦距的透镜,在此情况下,为了达到深熔小孔效应,需要更高的激光输出功率(功率密度)。
当激光功率超过2kW时,特别是对于10.6μm的CO2激光束,由于采用特殊光学材料构成光学系统,为了避免聚焦透镜遭光学破坏的危险,经常选用反射聚焦方法,一般采用抛光铜镜作反射镜。
由于能有效冷却,它常被推荐用于高功率激光束聚焦。
7)焦点位置。
焊接时,为了保持足够功率密度,焦点位置至关重要。
焦点与工件表面相对位置的变化直接影响焊缝宽度与深度。
图2-6表示焦点位置对1018钢熔深及缝宽的影响。
在大多数激光焊接应用场合,通常将焦点的位置设置在工件表面之下大约所需熔深的1/4处。
8)激光束位置。
对不同的材料进行激光焊接时,激光束位置控制着焊缝的最终质量,特别是对接接头的情况比搭接结头的情况对此更为敏感。
例如,当淬火钢齿轮焊接到低碳钢鼓轮,正确控制激光束位置将有利于产生主要有低碳组分组成的焊缝,这种焊缝具有较好的抗裂性。
有些应用场合,被焊接工件的几何形状需要激光束偏转一个角度,当光束轴线与接头平面间偏转角度在100度以内时,工件对激光能量的吸收不会受到影响。
9)焊接起始、终止点的激光功率渐升、渐降控制。
激光深熔焊接时,不管焊缝深浅,小孔现象始终存在。
当焊接过程终止、关闭功率开关时,焊缝尾端将出现凹坑。
另外,当激光焊层覆盖原先焊缝时,会出现对激光束过度吸收,导致焊件过热或产生气孔。
为了防止上述现象发生,可对功率起止点编制程序,使功率起始和终止时间变成可调,即起始功率用电子学方法在一个短时间内从零升至设置功率值,并调节焊接时间,最后在焊接终止时使功率由设置功率逐渐降至零值。
1. 激光深熔焊特征及优、缺点(-)激光深熔焊的特征1) 高的深宽比。
因为熔融金属围着圆柱形高温蒸气腔体形成并延伸向工件,焊缝就变成深而窄。
2) 最小热输入。
因为小孔内的温度非常高,熔化过程发生得极快,输入工件热量很低,热变形和热影响区很小。
3) 高致密性。
因为充满高温蒸气的小孔有利于焊接熔池搅拌和气体逸出,导致生成无气孔的熔透焊缝。
焊后高的冷却速度又易使焊缝组织细微化。
4) 强固焊缝。
因为炽热热源和对非金属组分的充分吸收,降低杂质含量、改变夹杂尺寸和其在熔池中的分布。
焊接过程无需电极或填充焊丝,熔化区受污染少,使得焊缝强度、韧性至少相当于甚至超过母体金属。
5) 精确控制。
因为聚焦光点很小,焊缝可以高精确定位。
激光输出无“惯性”,可在高速下急停和重新起始,用数控光束移动技术则可焊接复杂工件。
6) 非接触大气焊接过程。
因为能量来自光子束,与工件无物理接触,所以没有外力施加工件。