焊接技术标准规范汇总
焊接质量技术要求与规范
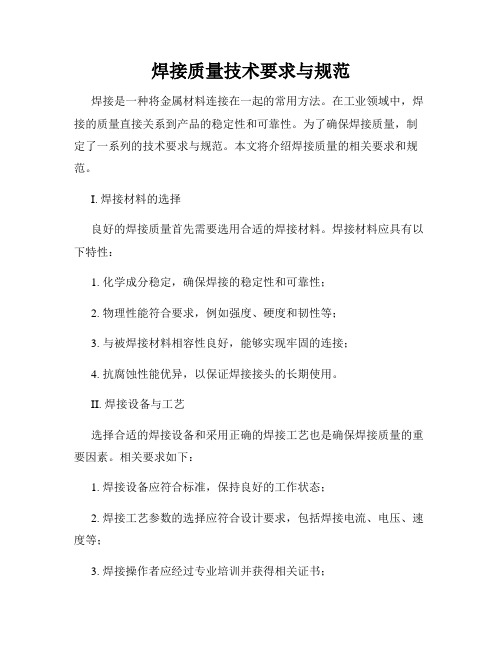
焊接质量技术要求与规范焊接是一种将金属材料连接在一起的常用方法。
在工业领域中,焊接的质量直接关系到产品的稳定性和可靠性。
为了确保焊接质量,制定了一系列的技术要求与规范。
本文将介绍焊接质量的相关要求和规范。
I. 焊接材料的选择良好的焊接质量首先需要选用合适的焊接材料。
焊接材料应具有以下特性:1. 化学成分稳定,确保焊接的稳定性和可靠性;2. 物理性能符合要求,例如强度、硬度和韧性等;3. 与被焊接材料相容性良好,能够实现牢固的连接;4. 抗腐蚀性能优异,以保证焊接接头的长期使用。
II. 焊接设备与工艺选择合适的焊接设备和采用正确的焊接工艺也是确保焊接质量的重要因素。
相关要求如下:1. 焊接设备应符合标准,保持良好的工作状态;2. 焊接工艺参数的选择应符合设计要求,包括焊接电流、电压、速度等;3. 焊接操作者应经过专业培训并获得相关证书;4. 焊接前的准备工作应仔细进行,确保焊接接头的质量。
III. 焊接表面处理焊接前的表面处理对焊接质量有重要影响。
必要的表面处理可以包括:1. 清洁焊接表面,去除杂质和氧化物等污染物;2. 使用适当的防焊剂,以防止氧化、腐蚀等问题;3. 对需要焊接的材料进行打磨或去毛刺处理,以保证焊接的平整度和连接质量。
IV. 焊接参数控制焊接参数的控制对焊接质量至关重要。
在焊接过程中,应做到以下几点:1. 准确控制焊接电流、电压和时间等参数;2. 确保焊接过程中的稳定性和均匀性;3. 防止过热和过深焊接等问题;4. 采用合适的焊接顺序,以保证整体焊接质量的一致性。
V. 检测与评估为了评估焊接质量,常常需要进行检测和评估。
以下是常用的焊接质量检测方法:1. 目测检查:通过肉眼观察焊接接头的外观,检查是否存在明显的焊接问题;2. 放射性检测:使用X射线或γ射线对焊缝进行检测,以发现内部缺陷;3. 超声波检测:利用超声波技术对焊缝进行检测,以发现焊接缺陷;4. 磁粉检测:利用磁粉或颗粒检测焊接接头的裂纹和缺陷。
手工焊接技术要求标准规范

手工焊接技术要求规范1、目的规范在制品加工中手工焊接操作,保证产品质量。
2、适用范围生产车间需进行手工焊接的工序及补焊等操作。
3、手工焊接使用的工具及要求3.1 焊锡丝的选择:直径为0.8mm或1.0mm的焊锡丝,用于电子或电类焊接;直径为0.6mm或0.7mm的焊锡丝,用于超小型电子元件焊接。
3.2烙铁的选用及要求:3.2.1 电烙铁的功率选用原则:1) 焊接集成电路、晶体管及其它受热易损件的元器件时,考虑选用20W内热式电烙铁。
2) 焊接较粗导线及同轴电缆时,考虑选用50W内热式电烙铁。
3) 焊接较大元器件时,如金属底盘接地焊片,应选100W以上的电烙铁。
3.2.2 电烙铁铁温度及焊接时间控制要求:1) 有铅恒温烙铁温度一般控制在280~360C之间,缺省设置为330± 10C, 焊接时间需小于3秒。
焊接时烙铁头同时接触在焊盘和元件引脚上,加热后送锡丝焊接。
部分元件的特殊焊接要求:SMD器件:焊接时烙铁头温度为:320± 10C ;焊接时间:每个焊点1~3 秒。
拆除元件时烙铁头温度:310~350C (注:根据CHIP件尺寸不同请使用不同的烙铁嘴。
)DIP器件:焊接时烙铁头温度为:330± 5C;焊接时间:2~3秒注:当焊接大功率(TO-220、TO-247、TO-264等封装)或焊点与大铜箔相连,上述温度无法焊接时,烙铁温度可升高至360C,当焊接敏感怕热零件(LED CCD传感器等)温度控制在260~300C。
2) 无铅制程无铅恒温烙铁温度一般控制在340~380C之间,缺省设置为360± 10 C,焊接时间小于3秒,要求烙铁的回温每秒钟就可将所失的温度拉回至设定温度。
3.2.3电烙铁使用注意事项:1) 电烙铁不宜长时间通电而不使用,这样容易使烙铁芯加速氧化而烧断,缩短其寿命,同时也会使烙铁头因长时间加热而氧化,甚至被严重氧化后很难再上锡。
2) 手工焊接使用的电烙铁需带防静电接地线,焊接时接地线必须可靠接地,防静电恒温电烙铁插头的接地端必须可靠接交流电源保护地。
焊接标准大全-焊接国家标准汇总
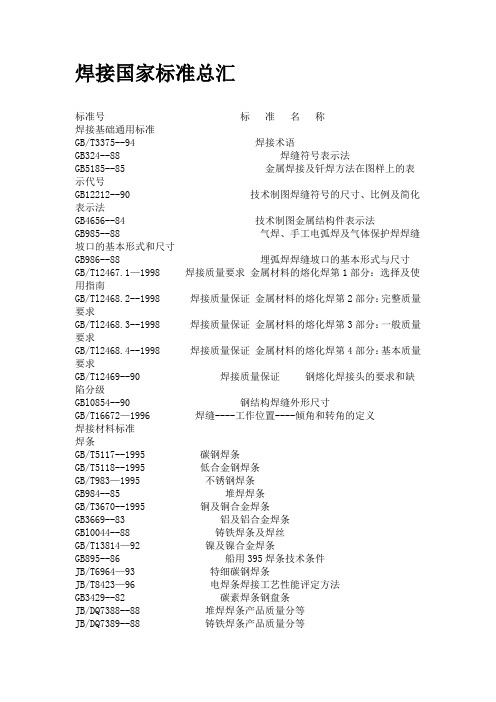
焊接国家标准总汇标准号标准名称焊接基础通用标准GB/T3375--94 焊接术语GB324--88 焊缝符号表示法GB5185--85 金属焊接及钎焊方法在图样上的表示代号GB12212--90 技术制图焊缝符号的尺寸、比例及简化表示法GB4656--84 技术制图金属结构件表示法GB985--88 气焊、手工电弧焊及气体保护焊焊缝坡口的基本形式和尺寸GB986--88 埋弧焊焊缝坡口的基本形式与尺寸GB/T12467.1—1998 焊接质量要求金属材料的熔化焊第1部分:选择及使用指南GB/Tl2468.2--1998 焊接质量保证金属材料的熔化焊第2部分:完整质量要求GB/Tl2468.3--1998 焊接质量保证金属材料的熔化焊第3部分:一般质量要求GB/Tl2468.4--1998 焊接质量保证金属材料的熔化焊第4部分:基本质量要求GB/T12469--90 焊接质量保证钢熔化焊接头的要求和缺陷分级GBl0854--90 钢结构焊缝外形尺寸GB/T16672—1996 焊缝----工作位置----倾角和转角的定义焊接材料标准焊条GB/T5117--1995 碳钢焊条GB/T5118--1995 低合金钢焊条GB/T983—1995 不锈钢焊条GB984--85 堆焊焊条GB/T3670--1995 铜及铜合金焊条GB3669--83 铝及铝合金焊条GBl0044--88 铸铁焊条及焊丝GB/T13814—92 镍及镍合金焊条GB895--86 船用395焊条技术条件JB/T6964—93 特细碳钢焊条JB/T8423—96 电焊条焊接工艺性能评定方法GB3429--82 碳素焊条钢盘条JB/DQ7388--88 堆焊焊条产品质量分等JB/DQ7389--88 铸铁焊条产品质量分等JB/DQ7390--88 碳钢、低合金钢、不锈钢焊条产品质量分等JB/T3223--96 焊接材料质量管理规程焊丝GB/T14957—94 熔化焊用钢丝GB/T14958--94 气体保护焊用钢丝GB/T8110--95 气体保护电弧焊用碳钢、低合金钢焊丝GBl0045--88 碳钢药芯焊丝GB9460--83 铜及铜合金焊丝GBl0858--89 铝及铝合金焊丝GB4242--84 焊接用不锈钢丝GB/T15620--1995 镍及镍合金焊丝JB/DQ7387--88 铜及铜合金焊丝产品质量分等焊剂GB5293--85 碳素钢埋弧焊用焊剂GBl2470--90 低合金钢埋弧焊焊剂钎料、钎剂GB/T6208--1995 钎料型号表示方法GBl0859---89 镍基钎料GBl0046--88 银基钎料GB/T6418--93 铜基钎料GB/T13815--92 铝基钎料GB/T13679--92 锰基钎料JB/T6045--92 硬钎焊用钎剂GB4906--85 电子器件用金、银及其合金钎焊料GB3131--88 锡铅焊料GB8012--87 铸造锡铅焊料焊接用气体GB6052--85 工业液体二氧化碳GB4842--84 氩气GB4844--84 氮气GB7445--87 氢气GB3863--83 工业用气态氧GB3864--83 工业用气态氮GB6819--86 溶解乙炔GBlll74--89 液化石油气GBl0624--89 高纯氩GBl0665--89 电石其它GB12174--90 碳弧气刨用碳棒焊接质量试验及检验标准钢材试验GBl954--80 镍铬奥氏体不锈钢铁素体含量测定方法GB6803--86 铁素体钢的无塑性转变温度落锤试验方法G132971--82 碳素钢和低合金钢断口试验方法焊接性试验GB4675.1--84 焊接性试验斜Y型坡口焊接裂纹试验方法GB4675.2—84 焊接性试验搭接接头(CTS)焊接裂纹试验方法GB4675.3--84 焊接性试验T型接头焊接裂纹试验方法GB4675.4--84 焊接性试验压板对接(FISCO)焊接裂纹试验方法GB4675.5—84 焊接热影响区最高硬度试验方法GB9447--88 焊接接头疲劳裂纹扩展速率试验方法GB/T13817--92 对接接头刚性拘束焊接裂纹试验方法GB2358--80 裂纹张开位移(COD)试验方法GB7032--86 T型角焊接头弯曲试验方法GB9446--88 焊接用插销冷裂纹试验方法GB4909.12—85 裸电线试验方法镀层可焊性试验焊球法GB2424.17--82 电工电子产品基本环境试验规程锡焊导则GB4074.26—83 漆包线试验方法焊锡试验JB/ZQ3690 钢板可焊性试验方法SJl798--81 印制板可焊性测试方法力学性能试验GB2649--89 焊接接头机械性能试验取样方法GB2650--89 焊接接头冲击试验方法GB2651—89 焊接接头拉伸试验方法GB2652—89 焊缝及熔敷金属拉伸试验方法GB2653--89 焊接接头弯曲及压扁试验方法GB2654--89 焊接接头及堆焊金属硬度试验方法GB2655--89 焊接接头应变时敏感性试验方法GB2656--81 焊接接头和焊缝金属的疲劳试验方法焊接材料试验GB3731--83 涂料焊条效率、金属回收率和熔敷系数的测定GB/T3965--1995 熔敷金属中扩散氢测定方法焊接检验GB/T12604.1--90 无损检测术语超声检测GB/T12604.2--90 无损检测术语射线检测GB/T12604.3--90 无损检测术语渗透检测GB/T12604.4--90 无损检测术语声发射检测GB/T12604.5--90 无损检测术语磁粉检测GB/T12604.6--90 无损检测术语涡流检测GB5618--85 线型象质计GB3323--87 钢熔化焊对接接头射线照相和质量分级GB/T12605--90 钢管环缝熔化焊对接接头射线透照工艺和质量分级GB/T14693--93 焊缝无损检测符号GBll343--89 接触式超声斜射探伤方法GBll345--89 钢焊缝手工超声波探伤方法和探伤结果的分级GBll344--89 接触式超声波脉冲回波法测厚GB2970--82 中厚钢板超声波探伤方法JBll52--81 锅炉和钢制压力容器对接焊缝超声波探伤GB/T15830—1995 钢制管道对接环缝超声波探伤方法和检验结果的分级GB827--80 船体焊缝超声波探伤GBl0866--89 锅炉受压元件焊接接头金相和断口检验方法GBll809---89 核燃料棒焊缝金相检验JB/T9215--1999 控制射线照相图像质量的方法JB/T9216--1999 控制渗透探伤材料质量的方法JB/T9217--1999 射线照相探伤方法JB/T9218--1999 渗透探伤方法JB3965--85 钢制压力容器磁粉探伤EJ187--80 磁粉探伤标准JB/T6061--92 焊缝磁粉检验方法和缺陷磁痕的分级JB/T6062--92 焊缝渗透检验方法和缺陷迹痕的分缀EJl86---80 着色探伤标准JB/ZQ3692 焊接熔透量的钻孔检验方法JB/ZQ3693 钢焊缝内部缺陷的破断试验方法GBll373--89 热喷涂涂层厚度的无损检测方法EJ188--80 焊缝真空盒检漏操作规程JBl612--82 锅炉水压试验技术条件GB9251--88 气瓶水压试验方法GB9252--88 气瓶疲劳试验方法GBl2135---89 气瓶定期检查站技术条件GBl2137--89 气瓶密封性试验方法GBll639--89 溶解乙炔气瓶多孔填料技术指标测定方法GB7446--87 氢气检验方法GB4843--84 氩气检验方法GB4845--84 氮气检验方法JB4730—94 压力容器无损检测DL/T820-2002 管道焊接接头超声波检验技术规程DL/T821-2002 钢制承压管道对接焊接接头射线检验技术规程DL/T541-94 钢熔化焊角焊缝射线照相方法和质量分级JB4744—2000 钢制压力容器产品焊接试板的力学性能检验焊接质量GB6416--86 影响钢熔化焊接头质量的技术因素GB6417--86 金属熔化焊焊缝缺陷分类及说明TJl2.1--81 建筑机械焊接质量规定JB/T6043--92 金属电阻焊接接头缺陷分类JB/ZQ3679 焊接部位的质量JB/ZQ3680 焊缝外观质量JB/TQ330--83 通风机焊接质量检验GB999--82 船体焊缝表面质量检验方法A-4 焊接方法及工艺标准GBl2219--90 钢筋气压焊GBll373--89 热喷涂金属件表面预处理通则JB/Z261--86 钨极惰性气体保护焊工艺方法JB/Z286--87 二氧化碳气体保护焊工艺规程JB/ZQ3687 手工电弧焊的焊接规范SDZ019--85 焊接通用技术条件J134251—86 摩擦焊通用技术条件ZBJ59002.1--88 热切割方法和分类ZBJ59002.2--88 热切割术语和定义ZBJ59002.3--88 热切割气割质量和尺寸偏差ZBJ59002.4—88 热切割等离子弧切割质量和尺寸偏差ZBJ59002.5--88 热切割气割表面质量样板JB/ZQ3688 钢板的自动切割ZBK540339--90 汽轮机铸钢件补焊技术条件NJ431—86 灰铸铁件缺陷焊补技术条件GBll630--89 三级铸钢锚链补焊技术条件GB/Z66--87 铜极金属极电弧焊JB/TQ368—84 泵用铸钢件焊补JB/TQ369---84 泵用铸铁件焊补HB/Z5l34--79 结构钢和不锈钢熔焊工艺JB/T6963—93 钢制件熔化焊工艺评定JB4708--2000 钢制压力容器焊接工艺评定JB4709—2000 钢制压力容器焊接规程DL/T752-2001 火力发电厂异种钢焊接技术规程DL/T819-2002 火力发电厂焊接热处理技术规程DL/T868-2004 焊接工艺评定规程DL/T869—2004 火力发电厂焊接技术规程焊接设备标准GB2900-22--85 电工名词术语电焊机GB8118--87 电弧焊机通用技术条件GB8366--87 电阻焊机通用技术条件GBl0249--88 电焊机型号编制方法GBl0977--89 摩擦焊机GB/T13164--91 埋弧焊机ZBJ64001--87 TIG焊焊炬技术条件ZBJ64003--87 弧焊整流器ZBJ64004188 MIG/MAG弧焊机ZBJ64005--88 电阻焊机控制器通用技术条件ZBJ64006--88 弧焊变压器ZBJ64008--88 电阻焊机变压器通用技术条件ZBJ64009--88 钨极惰性气体保护弧焊机(TIG焊机)技术条件ZBJ64016--89 MIG/MAG焊枪技术条件ZBJ64021—89 送丝装置技术条件ZBJ64022--89 引弧装置技术条件ZBJ64023--89 固定式点凸焊机JB5249--91 移动式点焊机JB5250--91 缝焊机ZBJ33002--90 焊接变位机ZBJ33003--90 焊接滚轮架JB5251--91 固定式对焊机JB685--92 直流弧焊发电机JB/DQ5593.1—90 电焊机产品质量分等总则JB/DQ5593.2--90 电焊机产品质量分等弧焊变压器.JB/DQ5593.3--90 电焊机产品质量分等便携式弧焊变压器JB/DQ5593.4--90 电焊机产品质量分等弧焊整流器JB/DQ5593.5--90 电焊机产品质量分等MIG/MAG弧焊机JB/DQ5593.6--90 电焊机产品质量分等TIG焊机JB/DQ5593.7--90 电焊机产品质量分等原动机弧焊发电机组JB/DQ5593.8--90 电焊机产品质量分等TIG焊焊炬JB/DQ5593.9--90 电焊机产品质量分等电焊机冷却用风机JB/DQ5593.10-90 电焊机产品质量分等MIG/MAG焊焊枪JB/DQ5593.11-90 电焊机产品质量分等电阻焊机控制器JB/DQ5593.12-90 电焊机产品质量分等摩擦焊机JB/Z152--81 电焊机系列型谱JB2751--80 等离子弧切割机JBJ33001—87 小车式火焰切割机JBl0860--89 快速割嘴GB5110--85 射吸式割炬JB/T5102--91 坐标式气割机JB5101--91 气割机用割炬JB6104--92 摇臂仿形气割机GB5107--85 焊接和气割用软管接头焊接安全与卫生标准GB9448—88 焊接与切割安全GBl0235--88 弧焊变压器防触电装置GB8197--87 防护屏安全要求GBl2011--89 绝缘皮鞋焊工培训与考试标准GB6419--86 潜水焊工考试规则JJl2.2--87 焊工技术考试规程EJ/Z3--78 焊工培训及考试规程DL/T679--1999 焊工技术考核规程JB/TQ338--84 通风机电焊工考核标准GB/T15169--94 钢熔化焊手焊工资格考试方法SDZ009--84 手工电弧焊及埋弧焊焊工考试规则JBll52--88 机械部焊工技术等级标准国家质量监督检验检疫总局锅炉压力容器压力管道焊工考试与管理规则(船舶)焊工考试规则冶金建设工程焊工考试规则。
焊接技术规范
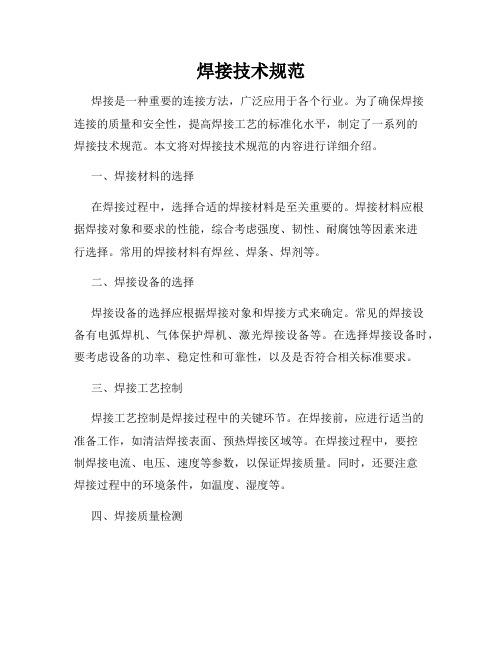
焊接技术规范焊接是一种重要的连接方法,广泛应用于各个行业。
为了确保焊接连接的质量和安全性,提高焊接工艺的标准化水平,制定了一系列的焊接技术规范。
本文将对焊接技术规范的内容进行详细介绍。
一、焊接材料的选择在焊接过程中,选择合适的焊接材料是至关重要的。
焊接材料应根据焊接对象和要求的性能,综合考虑强度、韧性、耐腐蚀等因素来进行选择。
常用的焊接材料有焊丝、焊条、焊剂等。
二、焊接设备的选择焊接设备的选择应根据焊接对象和焊接方式来确定。
常见的焊接设备有电弧焊机、气体保护焊机、激光焊接设备等。
在选择焊接设备时,要考虑设备的功率、稳定性和可靠性,以及是否符合相关标准要求。
三、焊接工艺控制焊接工艺控制是焊接过程中的关键环节。
在焊接前,应进行适当的准备工作,如清洁焊接表面、预热焊接区域等。
在焊接过程中,要控制焊接电流、电压、速度等参数,以保证焊接质量。
同时,还要注意焊接过程中的环境条件,如温度、湿度等。
四、焊接质量检测焊接完成后,需要进行焊接质量检测,以确保焊缝的质量和连接的可靠性。
常用的焊缝检测方法有目测检测、无损检测、金相检测等。
根据焊接对象和要求,选择合适的检测方法进行焊缝的评估和检验。
五、焊接安全注意事项焊接过程中存在一定的危险性,所以需要注意焊接安全。
首先要穿戴合适的防护用品,如焊接面罩、焊接手套、防火衣等。
其次要确保焊接环境通风良好,避免产生有害气体的聚集。
同时,还要注意焊接区域的火灾风险和电击风险,确保焊接操作的安全。
六、焊接技术标准为了规范焊接操作,提高焊接质量,制定了一系列的焊接技术标准。
焊接技术标准包括焊接工艺规程、焊接质量评定标准、焊接材料标准等。
在实际焊接操作中,要遵守相应的焊接技术标准,以确保焊接质量和工艺的合理性。
总结:焊接技术规范在焊接工艺中起着至关重要的作用。
通过选择合适的焊接材料和设备,控制焊接工艺,进行质量检测,注意焊接安全,并遵守焊接技术标准,可以保证焊接连接的质量和安全性。
不断提高焊接技术规范的水平,有助于推动焊接行业的发展,提高焊接工艺的标准化程度。
焊接技术规范
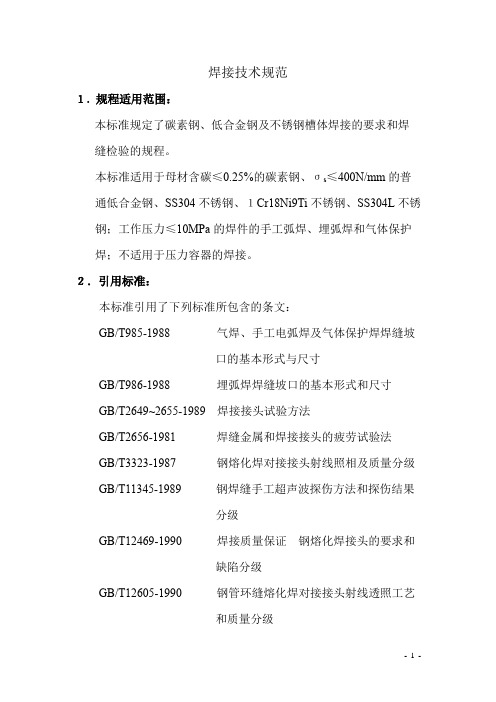
焊接技术规范1.规程适用范围:本标准规定了碳素钢、低合金钢及不锈钢槽体焊接的要求和焊缝检验的规程。
本标准适用于母材含碳≤0.25%的碳素钢、σs≤400N/mm的普通低合金钢、SS304不锈钢、1Cr18Ni9Ti不锈钢、SS304L不锈钢;工作压力≤10MPa的焊件的手工弧焊、埋弧焊和气体保护焊;不适用于压力容器的焊接。
2.引用标准:本标准引用了下列标准所包含的条文:GB/T985-1988 气焊、手工电弧焊及气体保护焊焊缝坡口的基本形式与尺寸GB/T986-1988 埋弧焊焊缝坡口的基本形式和尺寸GB/T2649~2655-1989 焊接接头试验方法GB/T2656-1981 焊缝金属和焊接接头的疲劳试验法GB/T3323-1987 钢熔化焊对接接头射线照相及质量分级GB/T11345-1989 钢焊缝手工超声波探伤方法和探伤结果分级GB/T12469-1990焊接质量保证钢熔化焊接头的要求和缺陷分级GB/T12605-1990 钢管环缝熔化焊对接接头射线透照工艺和质量分级GB/T15830-1995 钢制管道对接环焊缝超声波探伤方法和检验结果的分级JB/T5943-1991 工程机械焊接件通用技术条件JB/T6963-1993 钢制件焊熔化焊工艺评定JB/T7949-1995 钢结构焊缝外形尺寸3.焊接要求:3.1一般要求:3.1.1 焊接件的制造应符合经规定程序批准的产品、技术文件和本标准的规定;3.1.2 焊工和焊接检验、试验人员应经专门培训并考核合格后承担相应的工作;3.2焊接母材和焊接材料的要求:3.2.1用于焊接的母材(钢板、型钢、钢管等)和焊接材料(焊条、焊丝、焊剂)应有生产厂家质量保准书。
其材质、规格、尺寸应符合图样和技术文件的规定并经质检部门验收合格。
材料代用,应办理代用手续。
焊接母材和焊接材料的化学成分如下:表1Q235A碳素结构钢的化学成分表2不锈钢的化学成分表3 不锈钢焊接材料焊缝金属的主要成分3.2.2焊接材料的选用:依据材料类型和机械性能,对于碳素结构钢Q235A焊接材料选用焊条牌号为J422;对于SS304、1Cr18Ni9Ti不锈钢焊接材料选用焊条牌号为A132;对于SS304L不锈钢焊接材料选用焊条牌号为A002;3.2.3CO2的纯度应≥99.5%(体积法),含水量≤0.005%(重量法),当气体压力低于1MPa时,不能继续使用;3.2.4焊接材料应存放在干燥通风处,防止污染锈蚀。
焊接国家标准总汇资料
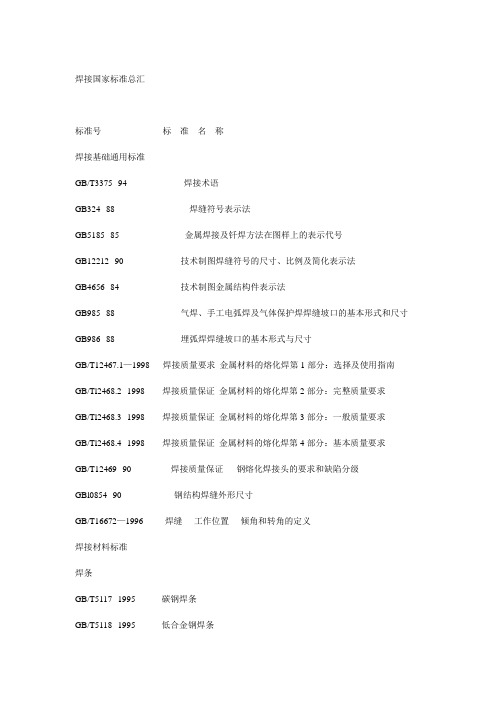
焊接国家标准总汇标准号标准名称焊接基础通用标准GB/T3375--94 焊接术语GB324--88 焊缝符号表示法GB5185--85 金属焊接及钎焊方法在图样上的表示代号GB12212--90 技术制图焊缝符号的尺寸、比例及简化表示法GB4656--84 技术制图金属结构件表示法GB985--88 气焊、手工电弧焊及气体保护焊焊缝坡口的基本形式和尺寸GB986--88 埋弧焊焊缝坡口的基本形式与尺寸GB/T12467.1—1998 焊接质量要求金属材料的熔化焊第1部分:选择及使用指南GB/Tl2468.2--1998 焊接质量保证金属材料的熔化焊第2部分:完整质量要求GB/Tl2468.3--1998 焊接质量保证金属材料的熔化焊第3部分:一般质量要求GB/Tl2468.4--1998 焊接质量保证金属材料的熔化焊第4部分:基本质量要求GB/T12469--90 焊接质量保证钢熔化焊接头的要求和缺陷分级GBl0854--90 钢结构焊缝外形尺寸GB/T16672—1996 焊缝----工作位置----倾角和转角的定义焊接材料标准焊条GB/T5117--1995 碳钢焊条GB/T5118--1995 低合金钢焊条GB/T983—1995 不锈钢焊条GB984--85 堆焊焊条GB/T3670--1995 铜及铜合金焊条GB3669--83 铝及铝合金焊条GBl0044--88 铸铁焊条及焊丝GB/T13814—92 镍及镍合金焊条GB895--86 船用395焊条技术条件JB/T6964—93 特细碳钢焊条JB/T8423—96 电焊条焊接工艺性能评定方法GB3429--82 碳素焊条钢盘条JB/DQ7388--88 堆焊焊条产品质量分等JB/DQ7389--88 铸铁焊条产品质量分等JB/DQ7390--88 碳钢、低合金钢、不锈钢焊条产品质量分等JB/T3223--96 焊接材料质量管理规程焊丝GB/T14957—94 熔化焊用钢丝GB/T14958--94 气体保护焊用钢丝GB/T8110--95 气体保护电弧焊用碳钢、低合金钢焊丝GBl0045--88 碳钢药芯焊丝GB9460--83 铜及铜合金焊丝GBl0858--89 铝及铝合金焊丝GB4242--84 焊接用不锈钢丝GB/T15620--1995 镍及镍合金焊丝JB/DQ7387--88 铜及铜合金焊丝产品质量分等焊剂GB5293--85 碳素钢埋弧焊用焊剂GBl2470--90 低合金钢埋弧焊焊剂钎料、钎剂GB/T6208--1995 钎料型号表示方法GBl0859---89 镍基钎料GBl0046--88 银基钎料GB/T6418--93 铜基钎料GB/T13815--92 铝基钎料GB/T13679--92 锰基钎料JB/T6045--92 硬钎焊用钎剂GB4906--85 电子器件用金、银及其合金钎焊料GB3131--88 锡铅焊料GB8012--87 铸造锡铅焊料焊接用气体GB6052--85 工业液体二氧化碳GB4842--84 氩气GB4844--84 氮气GB7445--87 氢气GB3863--83 工业用气态氧GB3864--83 工业用气态氮GB6819--86 溶解乙炔GBlll74--89 液化石油气GBl0624--89 高纯氩GBl0665--89 电石其它GB12174--90 碳弧气刨用碳棒焊接质量试验及检验标准钢材试验GBl954--80 镍铬奥氏体不锈钢铁素体含量测定方法GB6803--86 铁素体钢的无塑性转变温度落锤试验方法G132971--82 碳素钢和低合金钢断口试验方法焊接性试验GB4675.1--84 焊接性试验斜Y型坡口焊接裂纹试验方法GB4675.2—84 焊接性试验搭接接头(CTS)焊接裂纹试验方法GB4675.3--84 焊接性试验T型接头焊接裂纹试验方法GB4675.4--84 焊接性试验压板对接(FISCO)焊接裂纹试验方法GB4675.5—84 焊接热影响区最高硬度试验方法GB9447--88 焊接接头疲劳裂纹扩展速率试验方法GB/T13817--92 对接接头刚性拘束焊接裂纹试验方法GB2358--80 裂纹张开位移(COD)试验方法GB7032--86 T型角焊接头弯曲试验方法GB9446--88 焊接用插销冷裂纹试验方法GB4909.12—85 裸电线试验方法镀层可焊性试验焊球法GB2424.17--82 电工电子产品基本环境试验规程锡焊导则GB4074.26—83 漆包线试验方法焊锡试验JB/ZQ3690 钢板可焊性试验方法SJl798--81 印制板可焊性测试方法力学性能试验GB2649--89 焊接接头机械性能试验取样方法GB2650--89 焊接接头冲击试验方法GB2651—89 焊接接头拉伸试验方法GB2652—89 焊缝及熔敷金属拉伸试验方法GB2653--89 焊接接头弯曲及压扁试验方法GB2654--89 焊接接头及堆焊金属硬度试验方法GB2655--89 焊接接头应变时敏感性试验方法GB2656--81 焊接接头和焊缝金属的疲劳试验方法焊接材料试验GB3731--83 涂料焊条效率、金属回收率和熔敷系数的测定GB/T3965--1995 熔敷金属中扩散氢测定方法焊接检验GB/T12604.1--90 无损检测术语超声检测GB/T12604.2--90 无损检测术语射线检测GB/T12604.3--90 无损检测术语渗透检测GB/T12604.4--90 无损检测术语声发射检测GB/T12604.5--90 无损检测术语磁粉检测GB/T12604.6--90 无损检测术语涡流检测GB5618--85 线型象质计GB3323--87 钢熔化焊对接接头射线照相和质量分级GB/T12605--90 钢管环缝熔化焊对接接头射线透照工艺和质量分级GB/T14693--93 焊缝无损检测符号GBll343--89 接触式超声斜射探伤方法GBll345--89 钢焊缝手工超声波探伤方法和探伤结果的分级GBll344--89 接触式超声波脉冲回波法测厚GB2970--82 中厚钢板超声波探伤方法JBll52--81 锅炉和钢制压力容器对接焊缝超声波探伤GB/T15830—1995 钢制管道对接环缝超声波探伤方法和检验结果的分级GB827--80 船体焊缝超声波探伤GBl0866--89 锅炉受压元件焊接接头金相和断口检验方法GBll809---89 核燃料棒焊缝金相检验JB/T9215--1999 控制射线照相图像质量的方法JB/T9216--1999 控制渗透探伤材料质量的方法JB/T9217--1999 射线照相探伤方法JB/T9218--1999 渗透探伤方法JB3965--85 钢制压力容器磁粉探伤EJ187--80 磁粉探伤标准JB/T6061--92 焊缝磁粉检验方法和缺陷磁痕的分级JB/T6062--92 焊缝渗透检验方法和缺陷迹痕的分缀EJl86---80 着色探伤标准JB/ZQ3692 焊接熔透量的钻孔检验方法JB/ZQ3693 钢焊缝内部缺陷的破断试验方法GBll373--89 热喷涂涂层厚度的无损检测方法EJ188--80 焊缝真空盒检漏操作规程JBl612--82 锅炉水压试验技术条件GB9251--88 气瓶水压试验方法GB9252--88 气瓶疲劳试验方法GBl2135---89 气瓶定期检查站技术条件GBl2137--89 气瓶密封性试验方法GBll639--89 溶解乙炔气瓶多孔填料技术指标测定方法GB7446--87 氢气检验方法GB4843--84 氩气检验方法GB4845--84 氮气检验方法JB4730—94 压力容器无损检测DL/T820-2002 管道焊接接头超声波检验技术规程DL/T821-2002 钢制承压管道对接焊接接头射线检验技术规程DL/T541-94 钢熔化焊角焊缝射线照相方法和质量分级JB4744—2000 钢制压力容器产品焊接试板的力学性能检验焊接质量GB6416--86 影响钢熔化焊接头质量的技术因素GB6417--86 金属熔化焊焊缝缺陷分类及说明TJl2.1--81 建筑机械焊接质量规定JB/T6043--92 金属电阻焊接接头缺陷分类JB/ZQ3679 焊接部位的质量JB/ZQ3680 焊缝外观质量JB/TQ330--83 通风机焊接质量检验GB999--82 船体焊缝表面质量检验方法A-4 焊接方法及工艺标准GBl2219--90 钢筋气压焊GBll373--89 热喷涂金属件表面预处理通则JB/Z261--86 钨极惰性气体保护焊工艺方法JB/Z286--87 二氧化碳气体保护焊工艺规程JB/ZQ3687 手工电弧焊的焊接规范SDZ019--85 焊接通用技术条件J134251—86 摩擦焊通用技术条件ZBJ59002.1--88 热切割方法和分类ZBJ59002.2--88 热切割术语和定义ZBJ59002.3--88 热切割气割质量和尺寸偏差ZBJ59002.4—88 热切割等离子弧切割质量和尺寸偏差ZBJ59002.5--88 热切割气割表面质量样板JB/ZQ3688 钢板的自动切割ZBK540339--90 汽轮机铸钢件补焊技术条件NJ431—86 灰铸铁件缺陷焊补技术条件GBll630--89 三级铸钢锚链补焊技术条件GB/Z66--87 铜极金属极电弧焊JB/TQ368—84 泵用铸钢件焊补JB/TQ369---84 泵用铸铁件焊补HB/Z5l34--79 结构钢和不锈钢熔焊工艺JB/T6963—93 钢制件熔化焊工艺评定JB4708--2000 钢制压力容器焊接工艺评定JB4709—2000 钢制压力容器焊接规程DL/T752-2001 火力发电厂异种钢焊接技术规程DL/T819-2002 火力发电厂焊接热处理技术规程DL/T868-2004 焊接工艺评定规程DL/T869—2004 火力发电厂焊接技术规程焊接设备标准GB2900-22--85 电工名词术语电焊机GB8118--87 电弧焊机通用技术条件GB8366--87 电阻焊机通用技术条件GBl0249--88 电焊机型号编制方法GBl0977--89 摩擦焊机GB/T13164--91 埋弧焊机ZBJ64001--87 TIG焊焊炬技术条件ZBJ64003--87 弧焊整流器ZBJ64004188 MIG/MAG弧焊机ZBJ64005--88 电阻焊机控制器通用技术条件ZBJ64006--88 弧焊变压器ZBJ64008--88 电阻焊机变压器通用技术条件ZBJ64009--88 钨极惰性气体保护弧焊机(TIG焊机)技术条件ZBJ64016--89 MIG/MAG焊枪技术条件ZBJ64021—89 送丝装置技术条件ZBJ64022--89 引弧装置技术条件ZBJ64023--89 固定式点凸焊机JB5249--91 移动式点焊机JB5250--91 缝焊机ZBJ33002--90 焊接变位机ZBJ33003--90 焊接滚轮架JB5251--91 固定式对焊机JB685--92 直流弧焊发电机JB/DQ5593.1—90 电焊机产品质量分等总则JB/DQ5593.2--90 电焊机产品质量分等弧焊变压器.JB/DQ5593.3--90 电焊机产品质量分等便携式弧焊变压器JB/DQ5593.4--90 电焊机产品质量分等弧焊整流器JB/DQ5593.5--90 电焊机产品质量分等MIG/MAG弧焊机JB/DQ5593.6--90 电焊机产品质量分等TIG焊机JB/DQ5593.7--90 电焊机产品质量分等原动机弧焊发电机组JB/DQ5593.8--90 电焊机产品质量分等TIG焊焊炬JB/DQ5593.9--90 电焊机产品质量分等电焊机冷却用风机JB/DQ5593.10-90 电焊机产品质量分等MIG/MAG焊焊枪JB/DQ5593.11-90 电焊机产品质量分等电阻焊机控制器JB/DQ5593.12-90 电焊机产品质量分等摩擦焊机JB/Z152--81 电焊机系列型谱JB2751--80 等离子弧切割机JBJ33001—87 小车式火焰切割机JBl0860--89 快速割嘴GB5110--85 射吸式割炬JB/T5102--91 坐标式气割机JB5101--91 气割机用割炬JB6104--92 摇臂仿形气割机GB5107--85 焊接和气割用软管接头焊接安全与卫生标准GB9448—88 焊接与切割安全GBl0235--88 弧焊变压器防触电装置GB8197--87 防护屏安全要求GBl2011--89 绝缘皮鞋焊工培训与考试标准GB6419--86 潜水焊工考试规则JJl2.2--87 焊工技术考试规程EJ/Z3--78 焊工培训及考试规程DL/T679--1999 焊工技术考核规程JB/TQ338--84 通风机电焊工考核标准GB/T15169--94 钢熔化焊手焊工资格考试方法SDZ009--84 手工电弧焊及埋弧焊焊工考试规则JBll52--88 机械部焊工技术等级标准国家质量监督检验检疫总局锅炉压力容器压力管道焊工考试与管理规则(船舶)焊工考试规则冶金建设工程焊工考试规则。
焊接技术标准规范标准
1围1.1主题容本标准规定了电子电气产品焊接用材料和导线与接线端子、印制电路板组装件等的焊接要求以及质量保证措施。
1. 2适用围本标准适用于电子电气产品的焊接和检验。
2引用文件GB 3131-88锡铅焊料GB 9491-88锡焊用液态焊剂(松香基)QJ 3012-98电子电气产品元器件通孔安装技术要求QJ 165A-95电子电气产品安装通用技术要求QJ 2711-95静电放电敏感器件安装工艺技术要求3定义3. 1 MELF metal electrode leadless faceMELF是指焊有金属电极端面,作端面焊接的元器件。
4 一般要求4. 1环境要求4.1.1环境条件按QJ 165A中3. 1. 4条要求执行。
4.1.2焊接场所所需工具及设备应保持清洁整齐。
在焊接工位上应及时清除多余物(导线断头、焊料球、残留焊料等)。
禁止在焊接工位上饮食;禁止在工位上有化妆品以及与生产操作无关的东西。
4. 2工具、设备及人员要求4. 2. 1工具电烙铁应为温控型的,烙铁头空焊温度应保持在预选温度的士5. 5℃之,烙铁头的形状应符合焊接空间要求,并保证良好的接地。
4. 2. 2设备4. 2. 2. 1波峰焊设备波峰焊设备(包括焊剂装置、预热装置、焊槽)焊接前应能将印制板组装件预热到120℃以,在整个焊接过程中,焊料槽焊接温度的控制精度应维持在士5.5℃,并具有排气系统。
4.2.2.2再流焊设备再流焊设备应可将焊接表面迅速加热,并能在连续焊接操作时,迅速加热到预定温度的士6℃围。
加热源不应引起印制电路板或元器件的损坏,也不应在加热源与被焊金属直接接触时污染焊料。
再流焊设备包括采用平行等距电阻加热、短路棒电阻加热、热风加热、红外线加热、激光加热装置或非电烙铁热传导焊接的设备。
4. 2. 3人员操作人员应经过专业技术培训,熟悉本标准及相关工艺的规定,具有判别焊点合格或不合格的能力,并经考核合格上岗。
4. 3焊点4. 3. 1外观4.3.1.1 焊点表面应无气孔、非晶态,以及有连续良好的润湿。
各种焊接技术的规范
各种焊接技术的规范篇一:焊接技术标准附件3 上海同济同捷科技股份企业标准TJI/DG—2002汽车焊接技术标准(点焊)2002-04-28发布2002-05-01实施上海同济同捷科技股份发布TJI/DG-2002前言目的:本标准吸收了国外及国内汽车行业的技术标准而制订,为规范本公司在汽车产品设计、试制中焊接(点焊)的技术要求和质量。
非汽车产品的焊接(点焊)等效执行。
内容:1. 本标准的适用范围; 2. 点焊接头设计原则; 3. 焊点质量标准;4. 焊点质量的检验方法;5. 焊点接头的质量等级;本标准于2002年5月1日起实施。
本标准自生效之日起,本公司的点焊技术按本标准执行,原“试行”版本TJI/DG-2002作废,本版本为正式版本,电子版本由本版本覆盖。
本标准由上海同济同捷科技股份总师办提出。
本标准由上海同济同捷科技股份标准情报室归口管理。
本标准由上海同济同捷科技股份专家部起草。
本标准主要起草人:邬美华、薛永纯、江巧英。
上海同济同捷科技股份企业标准汽车焊接技术标准(点焊)TJI/DG—20021.适用范围1.1本标准是同捷公司负责确立或认可的汽车产品设计提供电阻点焊的焊接技术标准。
除非在焊接图纸上有特定的注释,确立不同的焊接要求,任何与本标准以外的特例,必须征得工艺人员同意。
1.2本标准适用于厚度6mm以下的低碳钢板(08、08AL、10、20、A2、A3等)、低合金高强度钢板(16Mn、09S iV)、含磷钢板(镀锌板、镀铝板、镀铅板等)的点焊。
1.3本标准未包括的材料厚度的点焊技术条件由现场工艺人员参照本标准自行在工艺技术文件中规定。
1.4本标准颁布前已有的产品图,如有不符合本标准之处可不作修改,新图纸设计或旧图纸换版时均符合本标准。
1.5 点焊种类:基本两种类型,结构点焊和工艺点焊。
1.5.1 结构点焊结构点焊是为了达到产品性能而设计的,所有点焊均为结构点焊,除非焊接图纸上特别注明工艺焊缝(点)。
焊接技术规范
※※目錄※※1.目的:规范焊接结构件的设计、制造及检验。
2.适用范围:本规范适用于本公司焊接结构件的设计、制造及检验。
3.引用标准:GB12212-90 《技术制图焊缝符号的尺寸、比例及简化表示法》GB324-88 《焊缝符号表示法》GB985-88 《气焊、手工电弧焊及气体保护焊焊缝坡口的基本形式与尺寸》GB6417-86 《金属熔化焊焊缝缺陷分类及说明》GB10854-89 《钢结构焊缝外形尺寸》4.参考标准:JB/T6753.4-93 《电工设备的设备购体公差焊接结构的一般公差》5.基本功能描述:金属焊接是用适当的手段,使两个分离的金属的物体产生原子或分子间结合而连接成一体的连接方式。
金属焊接是一种广泛采用的工艺手段。
6.技术要求:6.1焊接结构设计一般原则:电子设备结构设计中经常彩焊接结构形式。
在设计时应遵循一定的原则:6.1.1电子设备的结构件采用薄板类材料居多,如冷轧钢板,不锈钢板等,这类薄板件焊接变形较大,外协厂加工多彩二氧化碳保护焊和氩弧焊,生产效率较低,焊接后焊缝的打磨,消除应力集中和消除变形等增加了工艺步骤与成本。
建议结构设计中尽可能避免焊接结构。
6.1.2焊接结构设计中应尽可能减少焊接量。
对角焊缝而言,在保证强度的基础上,尽可能采用最小的焊脚尺寸。
6.1.3为控制焊接变形,应合理布置焊缝。
如有对称轴的焊接结构,焊缝应对称和分布等。
6.1.4必须在结构上保证每条焊缝能够方便地施焊和进行质量检查,焊缝周围要有足够的焊接和质量检查操作空间。
6.1.5电子设备结构往往从防锈的角度考虑对结构件进行电镀等电化学处理,如果焊接件整体电镀,需避免有截留电镀液的焊接结构,这种截留在焊接结构缝隙中的化学溶液会加速结构件的锈蚀。
6.2焊接结构一般公关如无特殊标注,要求焊接结构的一般公差达到以下A级要求:如有更高的要求,请在尺寸标注时直接标注公差。
6.2.1尺寸一般公差:表1 一般尺寸公差一般垂直度公差(若L∠W,则以长边L为基准)表26.3.1总则严格按照国标GB324-88《焊缝符号表示法》执行;可以按照国标GB12212-90《技术制图焊缝符号的尺寸、比例及简化表示法》对焊拉进行简化表示;可以依本规范对焊缝进行标注。
焊接技术标准规范汇总
焊接技术标准规范汇总1范围1.1主题内容本标准规定了电⼦电⽓产品焊接⽤材料和导线与接线端⼦、印制电路板组装件等的焊接要求以及质量保证措施。
1. 2适⽤范围本标准适⽤于电⼦电⽓产品的焊接和检验。
2引⽤⽂件GB 3131-88锡铅焊料GB 9491-88锡焊⽤液态焊剂(松⾹基)QJ 3012-98电⼦电⽓产品元器件通孔安装技术要求QJ 165A-95电⼦电⽓产品安装通⽤技术要求QJ 2711-95静电放电敏感器件安装⼯艺技术要求3定义3. 1 MELF metal electrode leadless faceMELF是指焊有⾦属电极端⾯,作端⾯焊接的元器件。
4 ⼀般要求4. 1环境要求4.1.1环境条件按QJ 165A中3. 1. 4条要求执⾏。
4.1.2焊接场所所需⼯具及设备应保持清洁整齐。
在焊接⼯位上应及时清除多余物(导线断头、焊料球、残留焊料等)。
禁⽌在焊接⼯位上饮⾷;禁⽌在⼯位上有化妆品以及与⽣产操作⽆关的东西。
4. 2⼯具、设备及⼈员要求4. 2. 1⼯具电烙铁应为温控型的,烙铁头空焊温度应保持在预选温度的⼠5. 5℃之内,烙铁头的形状应符合焊接空间要求,并保证良好的接地。
4. 2. 2设备4. 2. 2. 1波峰焊设备波峰焊设备(包括焊剂装置、预热装置、焊槽)焊接前应能将印制板组装件预热到120℃以内,在整个焊接过程中,焊料槽焊接温度的控制精度应维持在⼠5.5℃,并具有排⽓系统。
4.2.2.2再流焊设备再流焊设备应可将焊接表⾯迅速加热,并能在连续焊接操作时,迅速加热到预定温度的⼠6℃范围内。
加热源不应引起印制电路板或元器件的损坏,也不应在加热源与被焊⾦属直接接触时污染焊料。
再流焊设备包括采⽤平⾏等距电阻加热、短路棒电阻加热、热风加热、红外线加热、激光加热装置或⾮电烙铁热传导焊接的设备。
4. 2. 3⼈员操作⼈员应经过专业技术培训,熟悉本标准及相关⼯艺的规定,具有判别焊点合格或不合格的能⼒,并经考核合格上岗。
- 1、下载文档前请自行甄别文档内容的完整性,平台不提供额外的编辑、内容补充、找答案等附加服务。
- 2、"仅部分预览"的文档,不可在线预览部分如存在完整性等问题,可反馈申请退款(可完整预览的文档不适用该条件!)。
- 3、如文档侵犯您的权益,请联系客服反馈,我们会尽快为您处理(人工客服工作时间:9:00-18:30)。
1范围1.1主题内容本标准规定了电子电气产品焊接用材料和导线与接线端子、印制电路板组装件等的焊接要求以及质量保证措施。
1. 2适用范围本标准适用于电子电气产品的焊接和检验。
2引用文件GB 3131-88锡铅焊料GB 9491-88锡焊用液态焊剂(松香基)QJ 3012-98电子电气产品元器件通孔安装技术要求QJ 165A-95电子电气产品安装通用技术要求QJ 2711-95静电放电敏感器件安装工艺技术要求3定义3. 1 MELF metal electrode leadless faceMELF是指焊有金属电极端面,作端面焊接的元器件。
4 一般要求4. 1环境要求4.1.1环境条件按QJ 165A中3. 1. 4条要求执行。
4.1.2焊接场所所需工具及设备应保持清洁整齐。
在焊接工位上应及时清除多余物(导线断头、焊料球、残留焊料等)。
禁止在焊接工位上饮食;禁止在工位上有化妆品以及与生产操作无关的东西。
4. 2工具、设备及人员要求4. 2. 1工具电烙铁应为温控型的,烙铁头空焊温度应保持在预选温度的士5. 5℃之内,烙铁头的形状应符合焊接空间要求,并保证良好的接地。
4. 2. 2设备4. 2. 2. 1波峰焊设备波峰焊设备(包括焊剂装置、预热装置、焊槽)焊接前应能将印制板组装件预热到120℃以内,在整个焊接过程中,焊料槽焊接温度的控制精度应维持在士5.5℃,并具有排气系统。
4.2.2.2再流焊设备再流焊设备应可将焊接表面迅速加热,并能在连续焊接操作时,迅速加热到预定温度的士6℃范围内。
加热源不应引起印制电路板或元器件的损坏,也不应在加热源与被焊金属直接接触时污染焊料。
再流焊设备包括采用平行等距电阻加热、短路棒电阻加热、热风加热、红外线加热、激光加热装置或非电烙铁热传导焊接的设备。
4. 2. 3人员操作人员应经过专业技术培训,熟悉本标准及相关工艺的规定,具有判别焊点合格或不合格的能力,并经考核合格上岗。
4. 3焊点4. 3. 1外观4.3.1.1 焊点表面应无气孔、非晶态,以及有连续良好的润湿。
焊点不应露出基底金属、不应有锐边、拉尖、焊剂残渣以及夹杂。
与邻近导电通路之间焊料不应出现拉丝、桥接等现象。
4. 3. 1. 2当存在下列情况时焊点外表呈暗灰色是允许的。
a. 焊点焊接采用的不是HLSn60Pb焊料;b. 焊接部件为镀金或镀银;c. 焊点冷却速度缓慢(例如:热容量大的组装件经波峰焊或汽相焊之后),但不应有过热、过冷或受扰动的焊点。
4. 3. 2裂纹和气泡焊点的焊料与焊接部位间不应有裂纹、裂缝、裂口或隙缝。
气泡或气孔若与最小允许焊料量同时发生,则为不合格。
4. 3. 3润湿及焊缝焊料应润湿全部焊接部位的表面,并围绕焊点四周形成焊缝。
焊料润湿不良或润湿不完全,不应超出焊点四周10%焊料不应收缩成融滴或融球。
4. 3. 4焊料覆盖面焊料量应覆盖全部焊接部位,但焊料中导线的轮廓应可辨认。
4. 3. 5热缩焊焊点热缩焊装置形成的焊点其焊缝及焊接部件应清晰可见,焊料环应熔融,焊料沿引线流动,外部套管可以变色,但应可见焊区套管外的导线绝缘层,除轻微变色外,不应受损。
4. 4印制电路板组装件4. 4. 1导电体脱离基板焊接后,从印制电路板面至焊盘外侧下部边缘最大允许上翘距离,应为焊区或焊盘的厚度(高度)。
4.4.2组装件的清洁组装件焊接后应清除杂质(焊剂残渣、绝缘层残渣等)。
4. 5 热膨胀系数失配补偿元器件安装工艺或印制电路板设计,应能补偿元器件与印制电路板之间的热膨胀系数失配,安装工艺的补偿应限于元器件引线、元器件的特殊安装以及常规焊点。
禁止设计特殊的焊点外形作部分热膨胀系数失配补偿之用。
无引线元器件不应在槽形而和焊盘之间使用多余的内连线连接,无引线芯片载体仅底部端接时最小焊点高度一般为0. 2mm 。
4. 6 互连线的焊接点组装件间的互连线,应焊接在金属化孔或接线端上。
不应采用另加绝缘套管的镀锡裸线。
4. 7 表面安装的焊接手工焊接表面贴装多引线元器件时,应使用对角线方法依次焊接引线,最小焊接长度为1 ~ 2mm 。
4. 8 焊接温度、时间4. 8. 1 手工焊接温度一般应设定在260~300℃范围之内,焊接时间一般不大于水,对热敏元器件、片状元器件不超过2s,若在规定时间未完成焊接,应待焊点冷却后再复焊,非修复性复焊不得超过2次。
4. 8. 2 波峰焊机焊槽内温度应控制在250士5℃范围,焊接时间为3 ~3. 5s 。
4. 8. 3 再流焊焊接温度、时间按有关文件规定。
4. 9通孔充填焊料的要求对有引线或导线擂入的金属化孔充填焊料时,焊料只能从焊接面一侧流入小孔内的另一侧。
5详细要求5. 1焊接准备5. 1. 1 被焊导电体表面在焊接操作前应进行清洁处理。
5. 1. 2 导线、引线与接线端子在焊接前,应使用机械方法将其固定,防止导线、引线在端子上移动。
5. 1. 3 对镀金的元器件应经搪锡处理(高频器件、微电路除外)。
5. 1. 4 元器件安装应按QJ 3012要求执行。
5. 2 焊接材料5. 2. 1焊料应采用符合GB 3131的焊料制品HLSn60Pb或HLSn63Pb ,焊料外形任选,带芯焊料的焊剂应为R型或RM A型。
5. 2. 2 膏状焊料选用时应考虑焊料粉的颗粒形状、粘性、印刷性能、分解温度等技术指标,对焊料粉的氧化物应有控制。
5. 2. 3 焊剂应采用符合GB 9491的R型或RMA型松脂剂液体焊剂。
导线电缆焊接不应使用RA 型焊剂,其它场合使用RA型焊剂时应得到有关部门批准。
5. 3 焊接5. 3. 1导线、引线与接线端子的焊接5.3.1. 1 导线、引线与接线端的缠绕导线、引线在接线端子上缠绕最少为3/4圈,但不得超过一圈。
如图1所示。
对于直径小于0. 3mm的导线,最多可缠绕3圈。
5. 3. 1. 2 导线、引线最大截面积导线、引线与接线端连接部位的截面积,不应超过接线端子接线孔的截面积。
5. 3. 1. 3 接线端最多焊点数每个接线端子一般不应有三个以上的焊点。
5. 3. 1. 4 绝缘层间隙焊点焊料与导线的绝缘层间隙:a.最小间隙:绝缘层可紧靠焊料,但不能嵌入焊料,绝缘层不能熔融,烧焦或缩直径;b. 最大间隙:为两倍导线直径或1. 6mm。
5.3.1.5 导线、引线与接线端子的焊接焊料应在导线与接线端接触部分形成焊缝,焊料不应掩盖导线的轮廓,对槽形接线端,焊料可以充满焊槽。
如图2所示。
5.3.1.6 导线、引线与焊杯的焊接不应有超过=根的导线插人焊杯,多股芯线保持整齐,不应折断,并全部插入焊杯的底部,焊缝沿接触表面形成,焊料应润湿焊杯整个内侧,并至少充满杯口的75%,如图3、4所示。
5. 3. 2 印制电路板组装件的焊接5. 3. 2. 1 通孔焊接5. 3. 2. 1. 1引线或导线插装用孔对有引线或导线插入的金属化孔,通孔应充填焊料.焊料应从印制电路板一侧连续流到另一侧的元器件面,并覆盖焊盘面积的90%以上,焊料允许凹缩进孔内,凹缩量如图5所示。
5. 3. 2. 1. 2 引线弯曲半径部位的焊料正常的润湿,焊料应在元器件引线弯曲成形部位,但弯曲半径应暴露,焊料沿引线润湿如图6所示。
5.3.2.1.3 导线界面连接作为界面连接的单股镀锡铜线穿过通孔弯钩,弯钩要求应符合元器件引线弯钩要求,并与印制电路板两面的焊盘焊接。
如图7所示。
5. 3. 2. 1. 4 非支承孔合格焊点焊料与被焊表面应有小于90°的接触角。
5. 3. 2. 1. 5 无引线或导线插装的金属化孔这种通孔可不填充焊料。
当需填充焊料时焊料塞应满足图5所示的要求。
5. 3. 2. 2 表面安装焊接5. 3. 2. 2. 1 片状元器件的焊缝芯片在焊盘上面应75%以上的金属端帽覆盖,并有一条焊缝,焊缝向元器件端面上方延伸,高度为25%或1.0mm。
侧面不需要焊缝,焊料对元器件和焊料对焊盘的润湿角都应小于90°焊料不能把元器件本体上的非金属化部位包住。
如图8、9、10、11所示。
5. 3. 2. 2. 2 MELF的焊点外形MELF在焊盘上面应有75%以上的金属端帽的宽度和长度覆盖,如图12所示。
焊点应形成一条焊缝,焊缝向MELF侧面上方延伸高度为0. 1mm或25%D(金属端帽直径),如图13所示。
5. 3. 2. 2. 3 无引线槽形元器件上的焊缝无引线芯片载体在焊盘上面应有75%以上的金属化槽面宽度覆盖,并有一条焊缝,焊料垂直上升到外侧槽面的下部边缘,焊料对元器件和焊盘的润湿角都应小于90°,当无引线芯片载体仅有底部端接时,最小的焊点高度一般为0. 2mm,如图14所示。
5. 3. 2. 2. 4 无引线元器件平行度元器件每个端部下面的焊料厚度差异不大于0. 4mm,如图15所示。
5. 3.2.2.5 引线弯曲部位的外形引线的弯曲不应向元器件本体引线封口处延伸,弯曲引线到焊盘的角度大于45°,小于9 0°。
;如图16所示。
5. 3. 2. 2. 6 引线和焊盘的接触最小的接触长度,扁平引线为引线宽度,圆形引线为两倍直径,如图17所示。
侧向外伸趾端外伸应如图17、18所示范围内。
总的外伸量要保持在最小的接触长度,根部不应伸出焊盘,如图19所示。
5. 3. 2. 2.7引线离开焊盘的高度引线最小安装面翘离焊盘表面的最大值,圆形引线为引线直径(D)的一半,扁平或带状引线为引线厚度( T ) 两倍或0. 5mm,最小安装面内各点均应在直径一半或两倍引线高度这个最大间隙内,如图20所示。
最小安装面范围取决于引线接触长度以及引线直径或厚度。
5. 3. 2. 2. 8 最小焊料覆盖面圆形或扁圆形引线上的最小焊缝高度应为引线直径的25%,扁平引线上的最小焊缝高度处应有一条清晰可见的焊缝,该焊缝至少要从焊盘上升到引线侧面50%高处,焊料与引线焊盘等长,引线轮廓在焊料中应可见,如图21所示。
5.3.2.2.9 引线根部焊缝焊料应向引线上弯部延伸,但不能与元器件本体或引线封口接触,根部焊缝在引线根部和焊盘之间应连续不断,并延伸超出弯曲半径,根部不能伸出焊盘。
5. 3. 2. 2. 10 J形和V形引线的焊缝焊盘上应有75%以上的引线宽度覆盖并有一条焊缝,焊缝应向引线侧面上方延伸到引线内表面的高度,焊料不能与元器件封装的底部接触。
焊料沿“J”或“V”的圆弧处形成的焊缝应有一个引线宽度,如图22所示。
5. 3. 2. 2. 11 J形和V形元器件安装的平行度焊接后,元器件与印制电路板之间的间隙不应超过2. 5mm,如图23所示。
5. 4 质量保证措施5. 4. 1 潜在失效的预防5. 4. 1. 1 静电放电焊接时为防止元器件及电子部件的静电损伤,应按QJ 2711规定执行。