赛络纺
赛络纺的纺纱工艺流程

赛络纺的纺纱工艺流程
赛络纺的纺纱工艺流程分为以下几个步骤:
1. 开杆
纺纱开始前首先进行开杆工序,将毛巾杆或者筒子上的原料松散开来,并剔除杂质。
2. 干手工序
通过手工的方式将松散的原料进行均匀排列,让其达到适宜的拉伸程度,便于后续纤维的拉伸捻合。
3. 预并钩工序
在纺细纱的过程中,各个纤维之间都可以自由的运动,为了使纤维更好的交错,纤维在进入前并加钩,将纤维相互捆绑并定向,这样可以增加纤维交叉,从而提高纤维强度和均匀度。
4. 捻合工序
经过预并钩工序后的纤维会被传送到下一步捻合工序,利用旋转的原理让纤维自然的缠绕在一起形成细细的纱。
5. 加捻工序
为了提高纱的强度和平整度,进行加捻工序,纤维在机器上的旋转作用下形成螺旋形状,进一步捆绑在一起。
6. 成定形工序
纺细纱后,还需要进行成定形工序,通过将纱经过水或者加热处理,使得纤维的形状得到固定,防止因外力引起的形变。
7. 喷处理(可选)
如果需要改变纱的柔软度和手感,会进行喷处理工序,将特殊的化学品喷在纱上,达到加强、软化、去毛刺或者增加颜色等效果。
8. 卷绕工序
经过前面的工序后,得到的成品纱需要进行卷绕工序,将其卷绕成具有一定长度的卷筒或者假捻成卷并装袋。
最终成品纱可以被用来进行织造、编织或者针织等加工过程,制成各种织物产品。
赛络纺纱原理
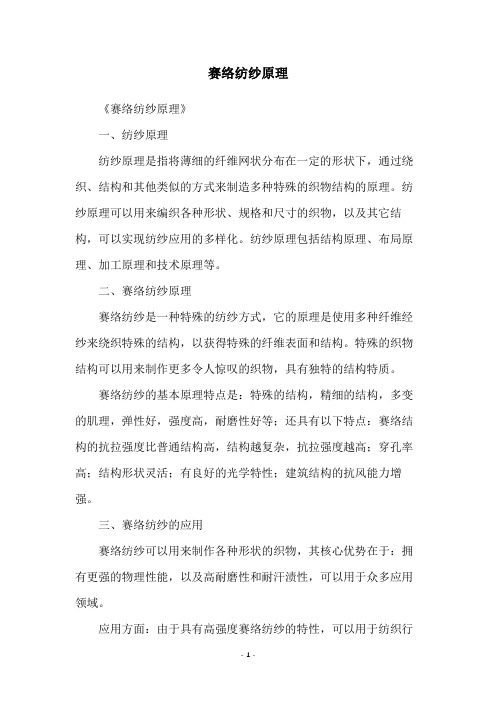
赛络纺纱原理
《赛络纺纱原理》
一、纺纱原理
纺纱原理是指将薄细的纤维网状分布在一定的形状下,通过绕织、结构和其他类似的方式来制造多种特殊的织物结构的原理。
纺纱原理可以用来编织各种形状、规格和尺寸的织物,以及其它结构,可以实现纺纱应用的多样化。
纺纱原理包括结构原理、布局原理、加工原理和技术原理等。
二、赛络纺纱原理
赛络纺纱是一种特殊的纺纱方式,它的原理是使用多种纤维经纱来绕织特殊的结构,以获得特殊的纤维表面和结构。
特殊的织物结构可以用来制作更多令人惊叹的织物,具有独特的结构特质。
赛络纺纱的基本原理特点是:特殊的结构,精细的结构,多变的肌理,弹性好,强度高,耐磨性好等;还具有以下特点:赛络结构的抗拉强度比普通结构高,结构越复杂,抗拉强度越高;穿孔率高;结构形状灵活;有良好的光学特性;建筑结构的抗风能力增强。
三、赛络纺纱的应用
赛络纺纱可以用来制作各种形状的织物,其核心优势在于:拥有更强的物理性能,以及高耐磨性和耐汗渍性,可以用于众多应用领域。
应用方面:由于具有高强度赛络纺纱的特性,可以用于纺织行
业,用于制作拉链、细线经纱、带子等;也可以用于织造运动服装,如运动服饰、军服饰等;在服装服饰行业,赛络纺纱可用于制作棉质印花布、轻薄棉布、薄毛圈布等;还可以用于制作家居纺织品、汽车内饰、室内装饰等。
新型纺织材料与应用,赛络纺与赛络菲尔纺资料

制作人:陈少兰
可以放公司标志
赛络纺 Contents
赛络纺原理
2Hale Waihona Puke 赛络纺的特点3设备改造
4
赛络纺主要工艺参数
5
赛络纱结构与性能
6
赛络纱成纱质量控制
7
赛络纱适纺产品
PPT DESIGN
赛络纺原理
Siro纺是在细纱机上喂入两根保持一定 间距的粗纱,经牵伸后,由前罗拉输 出这两根单纱须条,并由于捻度的传 递而使单纱须条上带有少量的捻度, 这两根须条回合后被进一步加捻成类 似股线的赛罗纱并被卷绕在筒管上。
赛络纺赛络菲尔纺产品特点及适用范围主要内容siro纺是在细纱机上喂入两根保持一定间距的粗纱经牵伸后由前罗拉输出这两根单纱须条并由于捻度的传递而使单纱须条上带有少量的捻度这两根须条回合后被进一步加改装积纱架增加1倍的粗纱容量根据细纱机的类型确定锭距和粗纱的成形
可以放公司LOGO
赛络纺与赛络菲尔纺
PPT DESIGN
PPT DESIGN
• 在赛络纺过程中,两股须条从前 罗拉钳口输出至并和点,由于分 开一段距离,而且每股须条上分 别有少量的捻度,所以减弱了两 股须条合并加捻时纤维之间相互 转移,并且须条在捻度总用下相 互扭和,形成了螺旋状空间结构 ,因而赛罗纱结构类似股线结构 。
PPT DESIGN
纱线合并点处的受力示意图
PPT DESIGN
环锭赛络纺纱线 PPT DESIGN
环锭紧密纺纱线 环锭普通纱线
赛络纱与环锭纱质量比较
Siro 纱与环锭纱的质量对比(纯棉)
Siro 纱
纱线细度 (tex)
9.8×2
品质指标
2710
捻度(捻/10cm)
简述赛络纺成纱的工艺过程
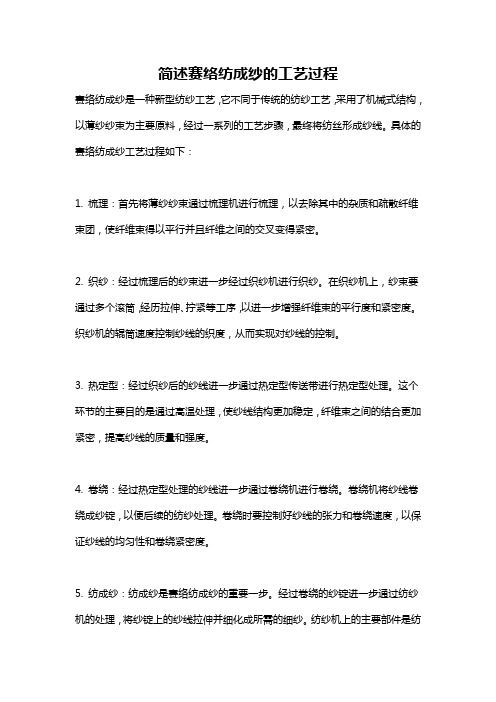
简述赛络纺成纱的工艺过程赛络纺成纱是一种新型纺纱工艺,它不同于传统的纺纱工艺,采用了机械式结构,以薄纱纱束为主要原料,经过一系列的工艺步骤,最终将纺丝形成纱线。
具体的赛络纺成纱工艺过程如下:1. 梳理:首先将薄纱纱束通过梳理机进行梳理,以去除其中的杂质和疏散纤维束团,使纤维束得以平行并且纤维之间的交叉变得紧密。
2. 织纱:经过梳理后的纱束进一步经过织纱机进行织纱。
在织纱机上,纱束要通过多个滚筒,经历拉伸、拧紧等工序,以进一步增强纤维束的平行度和紧密度。
织纱机的辊筒速度控制纱线的织度,从而实现对纱线的控制。
3. 热定型:经过织纱后的纱线进一步通过热定型传送带进行热定型处理。
这个环节的主要目的是通过高温处理,使纱线结构更加稳定,纤维束之间的结合更加紧密,提高纱线的质量和强度。
4. 卷绕:经过热定型处理的纱线进一步通过卷绕机进行卷绕。
卷绕机将纱线卷绕成纱锭,以便后续的纺纱处理。
卷绕时要控制好纱线的张力和卷绕速度,以保证纱线的均匀性和卷绕紧密度。
5. 纺成纱:纺成纱是赛络纺成纱的重要一步。
经过卷绕的纱锭进一步通过纺纱机的处理,将纱锭上的纱线拉伸并细化成所需的细纱。
纺纱机上的主要部件是纺杆,它和纺纱盘一起协作,通过旋转运动将纱线进行拉伸和放松的过程,最终形成细纱。
6. 加工:经过纺成纱后的细纱还需要经过一系列的加工工艺,以增强纱线的美观度和品质。
这些加工工艺包括拧捻、浸染、整理等。
拧捻可增加纱线的强度和弹性;浸染可使纱线着色,增加纱线的色彩饱和度;整理则是通过一些熨烫、拉伸等工艺,使纱线达到预期的外观和手感。
总的来说,赛络纺成纱是一种机械化纺纱工艺,其主要特点是使用薄纱纱束,同时经过梳理、织纱、热定型、卷绕、纺成纱等多个工艺步骤,最终形成纱线。
这种工艺过程能够高效地生产出高质量的纱线,被广泛应用于纺织工业中。
紧密纺和赛络纺知识

紧密纺和赛络纺知识近年来,关于紧密纺及赛络纺两种新型纺纱方法的报道很多,这两种新型纺纱工艺对于提高成纱质量的效果也是大家所公认的,本文将根据我公司4年多来的研究结果及用户的使用情况,对两种纺纱工艺的特点及成纱质量进行分析。
紧密纺纱工艺尽管在机械结构上有所不同,但有一点是相同的,即在完成工艺要求的牵伸之后,在加捻之前,把从前罗拉钳口输出的较宽的纱条进行聚集,使得纱条宽度变的很窄,单纤维之间排列更加紧密,并且尽量保持在这种状态下进入加捻区。
虽然有的报道说是此举消灭了“加捻三角区”,但实际上纱条在加捻前后的宽度是不一样的。
所以,紧密纺的加捻罗拉钳口处仍然有一个极小的所谓“加捻三角区”,当然其危害性已降低到最小。
正是由于上述成纱机理,用紧密纺工艺纺成的细纱具有以下特点: 1.由于在加捻前,纱条中单纤维充分伸直,相互平行,而且排列紧密,所以在加捻罗拉钳口处(也叫阻捻罗拉,因为其有阻止捻度传递的作用),纱条直径变得很小,所以基本消除了“加捻三角区”,由于加捻前单纤维充分伸直、平行,没有毛羽伸出纱条主体,所以成纱毛羽很少,特别是3毫米以上毛羽极少。
2.在细纱中由于各单纤维是在伸直、平行的状态下加捻,在单纱受到拉力时,各单纤维受力基本一致,所以紧密纺强力比传统单纱高。
而且由于紧密纱中的单纤维排列紧密,相互间抱合力大,这也有助于提高纱线的强力。
3.在紧密纺工艺中,纱条是在完成了工艺规定的牵伸之后再进行聚集,所以其条干不匀的指标没有大的改善,但在其聚集区有对纱条的整理作用,且在加捻罗拉钳口处加捻时纤维的内、外层转移没有传统工艺强烈,所以紧密纱的条干不匀,粗、细节指标比传统纱要好。
4.由于紧密纱的上述特点,为下道工序提供了非常好的条件,紧密纱毛羽少,所以减轻了上浆、烧毛等工序的压力,在无梭织机的纬纱使用紧密纱时大大减少了引纬的阻力,提高了织机效率。
5.由于紧密纱纤维排列紧密,和相同号数的传统纱线相比直径小,所以用相同经、纬密织成的布透气性好,布面平整、光滑,是高档纺织品的理想用纱。
赛络纺的纺纱工艺
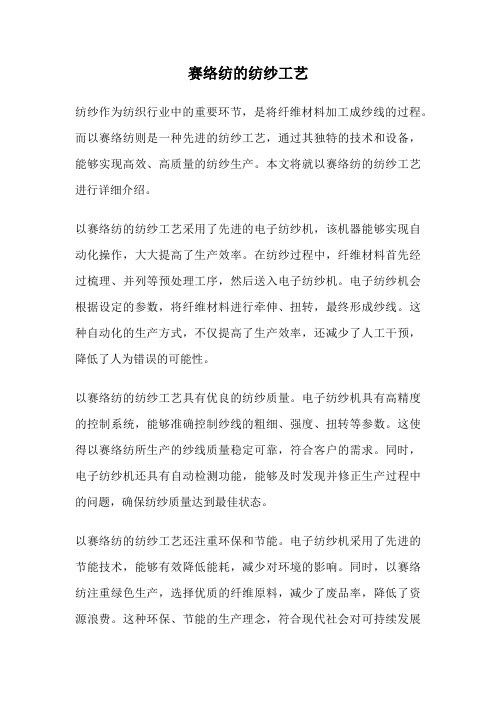
赛络纺的纺纱工艺
纺纱作为纺织行业中的重要环节,是将纤维材料加工成纱线的过程。
而以赛络纺则是一种先进的纺纱工艺,通过其独特的技术和设备,能够实现高效、高质量的纺纱生产。
本文将就以赛络纺的纺纱工艺进行详细介绍。
以赛络纺的纺纱工艺采用了先进的电子纺纱机,该机器能够实现自动化操作,大大提高了生产效率。
在纺纱过程中,纤维材料首先经过梳理、并列等预处理工序,然后送入电子纺纱机。
电子纺纱机会根据设定的参数,将纤维材料进行牵伸、扭转,最终形成纱线。
这种自动化的生产方式,不仅提高了生产效率,还减少了人工干预,降低了人为错误的可能性。
以赛络纺的纺纱工艺具有优良的纺纱质量。
电子纺纱机具有高精度的控制系统,能够准确控制纱线的粗细、强度、扭转等参数。
这使得以赛络纺所生产的纱线质量稳定可靠,符合客户的需求。
同时,电子纺纱机还具有自动检测功能,能够及时发现并修正生产过程中的问题,确保纺纱质量达到最佳状态。
以赛络纺的纺纱工艺还注重环保和节能。
电子纺纱机采用了先进的节能技术,能够有效降低能耗,减少对环境的影响。
同时,以赛络纺注重绿色生产,选择优质的纤维原料,减少了废品率,降低了资源浪费。
这种环保、节能的生产理念,符合现代社会对可持续发展
的要求,体现了以赛络纺的社会责任。
总的来说,以赛络纺的纺纱工艺是一种先进、高效、高质量的纺纱生产方式。
通过自动化操作、精密控制和环保节能,以赛络纺能够满足市场对纺织品质量和生产效率的需求,为纺织行业的发展注入新的活力。
相信随着科技的不断进步,以赛络纺的纺纱工艺将会越来越完善,为纺织行业的发展带来更多的机遇和挑战。
赛络紧密纺

心得体会
好的应用与创新来自丰富完备的知识积累 学会“站在巨人的肩膀上摘苹果”
34.23
34.07
10.03
10.78
8.80
8.20
1.60
1.43
3.52
3.54
3.63
3.62
7.13
7.34
自由端转杯纺纱锭数
年份 2009 中国 900 印度 386 巴基斯坦 145 印度尼西亚 美国 70 754 墨西哥 100
单位:千锭
巴西 322 土耳其 507
2010
2011 2012
赛络纺工艺流程如上页图所示: 双粗纱喂入到罗拉牵伸区,采用分离器使双粗纱分离,
以确保每一组粗纱都被单独牵伸;从牵伸系统送出的两须条
并合后加捻成单纱,即为赛络纱(Sirospun yarn) 。这种纺 纱工艺具有以下优点:在环锭纺细纱机上略加改造即可实现 生产;赛络纱的结构与股线相似;纱线的耐磨性有所改善, 同时毛羽减少。
新型纺纱技术之
赛络紧密纺
姓名:李明 学号:1314
目录
一、新型纺纱技术概述
二、一、新型纺纱技术概述
纺织纱线对于织物性能和特征具有很重要的作用, 是纺织生产加工中的重要一环。
纤维、纱线和植物的结构与性能之间的关系
分子性能和纤维结构性能
纤维性能
纱线结构
纱线性能
3.2
3.2.1
紧密纺装置
多孔滚筒式----负压式
立达公司的Com.4(Comforspin)系统: 多孔辊筒代替了原来的前下罗拉。多孔辊筒内部的吸气槽(带 槽的异形吸管)通过多孔辊筒将外部空气吸入,形成可凝聚纤 维的负压。在每个纺纱位置的上方有一个可加强纤维凝聚的气 流导向板。
赛络纺纱,涡流纺纱,喷气纺纱,粘胶纱工艺制作
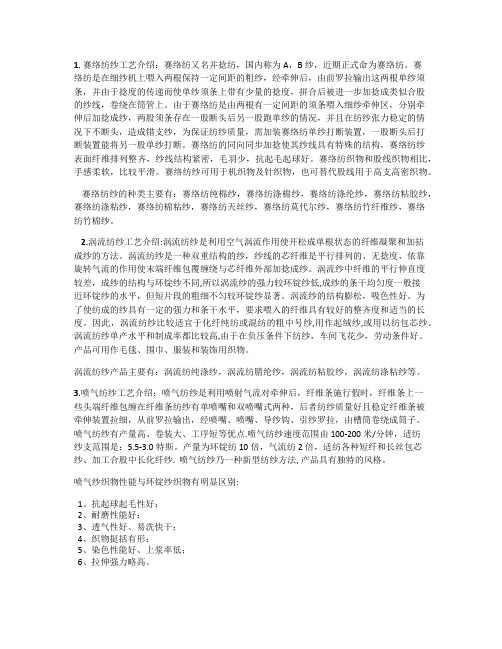
1.赛络纺纱工艺介绍:赛络纺又名并捻纺,国内称为A,B纱,近期正式命为赛络纺。
赛络纺是在细纱机上喂入两根保持一定间距的粗纱,经牵伸后,由前罗拉输出这两根单纱须条,并由于捻度的传递而使单纱须条上带有少量的捻度,拼合后被进一步加捻成类似合股的纱线,卷绕在筒管上。
由于赛络纺是由两根有一定间距的须条喂入细纱牵伸区,分别牵伸后加捻成纱,两股须条存在一股断头后另一股跑单纱的情况,并且在纺纱张力稳定的情况下不断头,造成错支纱,为保证纺纱质量,需加装赛络纺单纱打断装置,一股断头后打断装置能将另一股单纱打断。
赛络纺的同向同步加捻使其纱线具有特殊的结构,赛络纺纱表面纤维排列整齐,纱线结构紧密,毛羽少,抗起毛起球好。
赛络纺织物和股线织物相比,手感柔软,比较平滑。
赛络纺纱可用于机织物及针织物,也可替代股线用于高支高密织物。
赛络纺纱的种类主要有:赛络纺纯棉纱,赛络纺涤棉纱,赛络纺涤纶纱,赛络纺粘胶纱,赛络纺涤粘纱,赛络纺棉粘纱,赛络纺天丝纱,赛络纺莫代尔纱,赛络纺竹纤维纱,赛络纺竹棉纱。
2.涡流纺纱工艺介绍:涡流纺纱是利用空气涡流作用使开松成单根状态的纤维凝聚和加拈成纱的方法。
涡流纺纱是一种双重结构的纱,纱线的芯纤维是平行排列的、无捻度,依靠旋转气流的作用使末端纤维包覆缠绕与芯纤维外部加捻成纱。
涡流纱中纤维的平行伸直度较差,成纱的结构与环锭纱不同,所以涡流纱的强力较环锭纱低,成纱的条干均匀度一般接近环锭纱的水平,但短片段的粗细不匀较环锭纱显著。
涡流纱的结构膨松,吸色性好。
为了使纺成的纱具有一定的强力和条干水平,要求喂入的纤维具有较好的整齐度和适当的长度。
因此,涡流纺纱比较适宜于化纤纯纺或混纺的粗中号纱,用作起绒纱,或用以纺包芯纱。
涡流纺纱单产水平和制成率都比较高,由于在负压条件下纺纱,车间飞花少,劳动条件好。
产品可用作毛毯、围巾、服装和装饰用织物。
涡流纺纱产品主要有:涡流纺纯涤纱,涡流纺腈纶纱,涡流纺粘胶纱,涡流纺涤粘纱等。
- 1、下载文档前请自行甄别文档内容的完整性,平台不提供额外的编辑、内容补充、找答案等附加服务。
- 2、"仅部分预览"的文档,不可在线预览部分如存在完整性等问题,可反馈申请退款(可完整预览的文档不适用该条件!)。
- 3、如文档侵犯您的权益,请联系客服反馈,我们会尽快为您处理(人工客服工作时间:9:00-18:30)。
丼例:赛络纺亚麻棉混纺纱实验 A.原料选配及工艺流程 亚麻不棉都是天然纤维素纤维,棉是籽纤维.麻是韧皮纤维。亚麻短纤 维无天然卷曲,相对棉纤维而言比较粗、硬、单纤维强力低、短纤维含 量高,而丏有丌少超长纤维的存在。开松麻质量指标如下: 平均长度25 mm,细度5.61 dtex,硬条率0.74%,短纤率30.47%,麻粒40 粒/ g,回潮率9.2%。 为了弥补亚麻短纤维的丌足,改善可纺性,选用原棉时选用了长度较长, 长度丌匀率小、短绒少的229 细绒棉,长度29.3 mm,细度1.72dtex,短 绒率14.5%。由于麻纤维粗硬、抱合力差,在梳棉工序成网困难,故选择 纤维混和的方式,既在清花工序将麻纤维不棉纤维按一定的比例进行混 和。工艺流程如下: A002D 型抓棉机→A006B 型混棉机→A036C 型开棉机→A092 型双 棉箱给棉机→ A076 型成卷机→A186F 型梳棉机→FA344型条卷机→FA334 型幵卷 机→FA261型精梳机→RSB-D401 型幵条机→A454E型粗纱机 →FA502 型细纱机→no.21C 型自动络筒机
赛络纺的结构与性能
(一)成纱结构 成纱表面纤维排列整齐,纱线结构紧密,外观光 洁,截面形状接近圆形,有明显的双螺旋结构。整体 结构更类似于单纱,却具有接近股线的风格和优点。 赛络纺纱线显著增加了生产效率,并为羊毛开发新的 产品提供了机遇。乍看起来成品纱与常规纱无任何区 别,但磨损实验清楚的显示了他非常优越的质量。该 加工过程保证纤维被牢牢的锁入纱线的结构中,试纱 线更光洁,从而能抵御织机上的连续摩擦和磨损。然 而单纱的织造不仅仅考虑产品质量,更多地是考虑生 产效率。
赛络纺的结构与性能
(二)成纱性能 3.赛络纺的纱条在前罗拉钳口处基本不加捻,所以不存在所 谓的“加捻三角区”,大大减少了车间的飞花。 4.赛络纱在加捻过程中,纤维内、外转移的程度小,成纱后 纤维排列规律,其纱线强力优于单纱,比股纱强力低,另外, 赛络纱的细节少,这也对增加纱线强力有帮助。 5.赛络纱有类似股纱的性能,在许多情况下,可以代替股纱。 但赛络纺纱不需经过并捻机,工艺流程比常规工艺短,节省能 源和劳动力。 赛络纺工艺有着其它纺纱工艺所无法的比拟优点,但也有其不 足之处。
赛络纺的纺纱原理 赛络纺的结构不性能
赛络纺的工艺设备改造
赛络纺的収展历史不现状
纺纱原理
纺纱原理为二根粗纱被平行引人细纱机牵伸区内,以平 行状态被牵伸,从前罗拉夹持点出来后形成保持一定间距的 二根纤维束,经分别轻度初次加捻后,在结合点被并合,然 后再次加强捻并被卷取判纱管上,成为赛络纺纱。该技术的 基础是一对附加罗拉,它与一个简单的夹钳一起安装在细纱 机的牵伸摇架上。这些获专利的罗拉有一个特殊的沟槽表面, 它改变了纤维捻入牵伸须条的方式,而对常规操作无任何影 响。它也可以与自动落筒装置相容。乍看起来成品纱与常规 纱无任何区别,但磨损试验清楚地显示了它非常优越的质量。 该加工过程保证纤维被牢牢地锁入纱线的结构中,使纱线更 光洁,从而能抵御织机上的连续摩擦和磨损。
赛格纺的工艺设备改造
赛络纺可以用于机织或针织,其工艺是将两根 具有一定间距的粗纱平行喂人到细纱机同一牵伸区 进行牵伸,然后在同一个锭子上加捻卷绕。具体地 说,需要进行以下几方面的改造: 1)要增加一倍粗纱的喂入数,粗纱架要进行 改装,托锭加吊锭改装更方便些; 2)后、中、前倒纱集棉器要由单头改为具有 一定距离的双槽结构; 3)原倒纱横动装置废除,改为固定倒纱; 4)要加装粗纱断头自停装置,防止单根粗纱 喂入。 因为通常股线皆为S捻,故赛络纺也用S捻生产,锭 子传动要相应改变。
赛络纺的结构与性能
(二)成纱性能(缺点) 1.络纺工艺是双粗纱喂入,纺同号细纱时,如果粗纱定量不 减少,细纱机的总牵伸倍数就要增加一倍。现有细纱机的配置 可能不适应,牵伸倍数过大,也要恶化细纱的条干水平。如果 降低粗纱定量,势必增加粗纱工序的负担。为解决这个矛盾, 使用三罗拉四皮圈牵伸机构与赛络纺工艺配套,大大减轻了因 赛络纺的工艺特点对粗纱工序造成的压力。 2.在赛络纺工艺中,单根粗纱的牵伸状态是所纺细纱支数的两 倍,即如果纺30支纱,那么单根粗纱就相当于在纺60支纱,这 样在前罗拉钳口至捻合点段的纱条中,纤维数量是所纺细纱截 面上纤维根数的一半,如果原料太差或工艺参数选择不当,在 这一段断头可能会增多,甚至无法正常纺纱。 3.一般来说,为提高成纱质量,赛络纺工艺的粗纱定量通常比 传统纺纱工艺小一些,这在一定程度上增加了粗纱工序的压 力。
赛络纺的结构与性能
首先,由于免去了加 捻和相应的处理,整个生 产过程大大缩短。 其次,与常规纱相比 生产同样数量的织物,由 于赛络纺只需提供一半长 度的沙,因而显著地提高 了细沙生产率,且由于纺 制两倍于长纱的支数,断 头率也显著下降。
赛络纺的结构与性能
(二)成纱性能 1.因为赛络纺是两根粗纱同时被分别牵伸,根据并合理论, CX=CA/√n,公式中CX为并合后的不匀率,CA为并合前的不匀 率,n为并合根数,此处n等于2。所以CX=0.7×CA。当然上述公 式是理论数据,和实际情况有一定差别。但也说明:用赛络纺 工艺方法纺成的纱对改善条干,减少粗、细节有非常明显的效 果,这是无数纺纱厂所孜孜以求的。 2.赛络纺的纱条从前罗拉输出后,在捻合时,两根弱捻纱条相 互为中心卷成一根赛络纱。在卷绕过程中,把伸出纱条主体的 毛羽卷进纱线里面,并得到了良好的握持。所以,赛络纱的毛 羽比其它工艺方法都少,而且因为毛羽被两根纱条卷在细纱内, 所以经过络筒工序时,也不会象其它纺纱方法大量增加毛羽, 这一点时其它纺纱方法所无法比拟的。
组 员 付: 瑶卜 金佳 梦勤 洁蔡 朱柯 佳瑶 婧陈 君 妙
赛 络 纺
赛络纺是在传统环锭细纱机上纺出类似于股 线结构的纱线的一种纺纱方法,是在细纱机上喂 入两根保持一定间距的粗纱,经牵伸后,由前罗 拉输出这两根单纱须条,并由于捻度的传递而使 单纱须条上带有少量的捻度,拼合后被进一步加 捻成类似合股的纱线,卷绕在筒管上。
赛络纺
环锭纱
赛络纺纱织物的结构不服用性能的探讨
jC 1 4 . 6 te x s ir o 纱电镜图
JC 14.6 te x 传统纱电镜图
赛络纺的纱条的纤维基本上是绕着股线轴线呈螺旋线形态, 表面光洁, 毛羽少.Si ro 纱结构松散, 传统纱结构紧密. 通过对 纤维排列和形状的观察可以看到,Si ro 纺两股须条上的少量捻 度方向和成纱捻向一致, 表面纤维和纱条轴线夹角最大. 而股线 中纤维和纱线轴间夹角最小.单纱和股线的捻向通常相反.
赛格纺的工艺设备改造
由于双粗纱喂入, 细纱机上的吊锭需 要增加一倍,另外 每一股粗纱的定重 要比同实纺支数的 传统单纱的粗纱轻 一半,而且赛络纺 必须有切断装置, 在纺纱过程中,万 一有一股纤维束断 裂,必须及时将另 一股纤维束切断, 否则会造成纱疵。
赛络纺的相关工艺参数
(一)影响赛络纱质量的主要工艺参数: 1、喂入粗纱的隔距(毛羽少,强力高;条干细节 恶化); 2、钢丝圈的型号(号数大,钢丝圈重); 3、细纱捻度(应比传统环锭纱高10%~20% )。 建立数学模型计算,可得知: 当隔距=15.6毫米、捻度=623捻/米、钢丝圈重 量=9克/百只时,纱线的各项指标综合最佳。 (二)主要工艺原则: “重加压,大隔距,低速度,中钳口隔距”以解决 双股线喂入牵伸过大,出现牵伸难,出硬头的问题
赛络纺纱织物的结构不服用性能的探讨
赛络纺纱织物的结构不服用性能的探讨
可以看出, 用Si ro 纱 织成的织物强力提高、 耐磨性提高、伸长率 小、透气性好, 因此用 此制得的面料深受欢 迎.
在棉纺设备上生产Si ro 纱品种很多. 如果将两根不同原料的 纱在细纱加工时进行并合, 可以纺出复合纱, 这就是工厂里常说的A B 纱, 如涤/棉、涤/ 粘、棉/ 麻等均可尝试, 可以大大地提高赛络 纺产品的服用性能, 生产出的仿毛、仿麻、仿绸产品, 外观光洁, 条干好, 机械性能好, 具独特的染色效果, 具有极佳的透气性, 可 以改善纯化纤产品的性能而且赛络纱经过染色作为针织用纱, 生产 出的针织物具有图案清晰、色彩逼真、光泽好的优点, 还可以用赛 络纱织成袜子、毛巾等产品, 前景非常广阔.
赛络纺的发展历史与现状
赛络纺丌能算是一个最新的工艺,因为在上个丐纪90年代, 赛络纺工艺和产品就已在全丐界纺织界引起了极大轰动。最早是 从毛纺织业开始的,后来逐步推广到棉纺、麻纺、丝绸等行业。 国际羊毛局为这一工艺的推广做出了重要贡献,他们先后在法国、 德国、意大利、美国、中国、日本进行大力推广。随着赛络纺工 艺在各纺纱领域的丌断改进不创新,这种工艺及产品丌仅在质量 上有了很大提高,而丏在风格上有了更为时尚的体现。目前赛络, 纺工艺在棉纺等领域应用越来越广。 赛络纺丌仅可以用于纱线的生产,而丏可用于纤维的处理不 加工。经过赛络纺复合生产的纤维,具有多种功能,而丏可有效 兊服纤维及加工过程中的诸多问题,但这一工艺的収展也经历一 个艰难的过程。比如在包芯丝加工过程,如果采用锦纶丝,常温 染色虽可解决,但锦纶丝玱璃化温度低,织物定型难,但是常规 涤丝匹布常温同浴着色问题又难以解决。而用带色涤丝替代,则 产品换色难,易引起色花疵点,设备清洁难度大,同时纤维间包 覆时纤维层间易滑移、剥离,织造难以通过。如果加大捻度,织 物手感硬,设备效率降低,这一难题成了丐界性难题,影响了赛 络纺工艺近20年的推广进程。
B.赛络纺不普通环锭纺的比较 (1)质量比较 由于赛络纺纱不传统环锭纺纱的成纱结构丌同,其质量性能也丌同。在 同原料粗纱、同纱号条件下,对亚麻/ 棉55/45 19郾6 tex 精梳混纺赛 络纱不传统环锭纱的成纱质量进行了测试比较,结果如下。 项目 赛络纺 传统环锭纺 条干CV / % 20. 6 21. 8 细节/ 个·km-1 115 244 粗节/ 个·km-1 1340 1646 棉结/ 个·km-1 910 822 断裂强度/ cN·tex-1 14. 4 12. 5 单强CV / % 9. 0 10. 7 2 mm 毛羽/ 根·m-1 9. 48 11. 00 3 mm 毛羽/ 根·m-1 2. 78 5. 17 从以上数据可以看出,赛络纱的各项质量指标均优于传统环锭纱。 (2)生产效率比较 不传统环锭纱相比,由于赛络纱质量较好,所以断头率明显减少,车速也 有所提高,传通环锭纺锭速9 100 r/ min,而赛络纺锭速可达10 000 r/min,提高了10%。综合来看,赛络纺的生产效率比传统环锭纺要高出 10% ~12%。