纺织专业知识-紧密纺与环锭纺的比较
纺织专业知识-紧密纺与环锭纺的比较

<1>紧密纺是在改进的新型环锭细纱机上进行纺纱的一种新型纺纱技术。
其纺纱机理主要是:在环锭细纱机牵引装置前增加了一个纤维凝聚区,基本消除了前罗拉至加捻点之间的纺纱加捻三角区。
纤维须条从前罗拉前口输出后,先经过异形吸风管外套网眼皮圈,须条在网眼皮圈上运动,由于气流的收缩和聚合作用,通过异形管的吸风槽使须条集聚、转动,逐步从扁平带状转为圆柱体,纤维的端头均捻入纱线内,因此成纱非常紧密,纱线外观光洁、毛羽少。
紧密纺纱线强力较高,毛羽较少。
<2>赛络纺是由两根有一定间距的须条喂入细纱牵伸区,分别牵伸后加捻成纱,两股须条存在一股断头后另一股跑单纱的情况,并且在纺纱张力稳定的情况下不断头,造成错支纱,为保证纺纱质量,需加装赛络纺单纱打断装置,一股断头后打断装置能将另一股单纱打断。
新西兰羊毛研究机构的子公司发展公司是首批授权的赛络纺技术传授者之一,该技术能生产单股精梳毛纱,这种纱可以不经上浆或任何后整理而直接作为经纱进行织造。
无须双股并纱或应用保护涂层面而直接织造单股纱的能力,长期来一直是精梳毛纺业追寻的目标。
赛络纺纱线显着增加了生产效率,并为羊毛开发新的产品提供了机遇。
该技术的基础是一对附加罗拉,它与一个简单的夹钳一起安装在细纱机的牵伸摇架上。
这些获专利的罗拉有一个特殊的沟槽表面,它改变了纤维捻入牵伸须条的方式,而对常规操作无任何影响。
它也可以与自动落筒装置相容。
乍看起来成品纱与常规纱无任何区别,但磨损试验清楚地显示了它非常优越的质量。
该加工过程保证纤维被牢牢地锁入纱线的结构中,使纱线更光洁,从而能抵御织机上的连续摩擦和磨损。
然而,单纱的织造不仅仅考虑产品质量,更多的是考虑生产效率。
首先,由于免去了加捻和相应的处理,整个生产过程大大缩短。
其次,与常规纱相比生产同样数量的织物,由于赛络纺只需提供一半长度的纱,因而显着地提高了细纱生产率,且由于纺制两倍于常规纱的支数,断头率也显着下降。
在可织单纱计划的中试阶段,意大利、澳大利亚和新西兰的工厂将该罗拉各安装了一台细纱机,生产出商业批量的纱,接着将这些纱织入一系列的织物中。
紧密纺纱技术特点及与普通环锭纺纱性质的比较
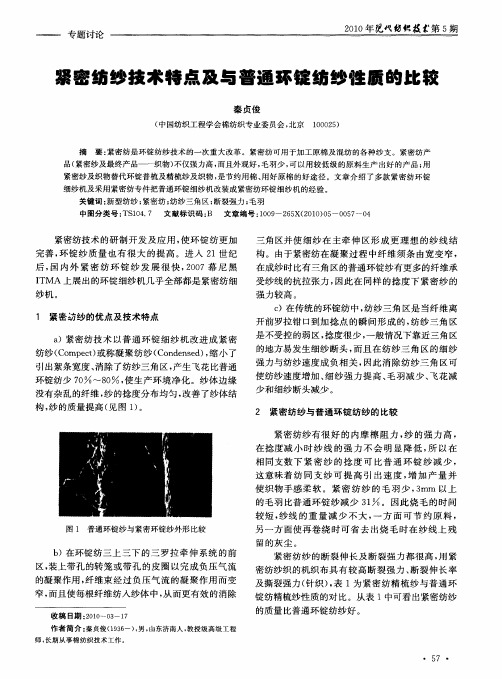
引 出絮条宽 度 、 消除 了纺纱 三 角 区 , 产生 飞花 比普 通 环锭纺 少 7 ~8 , 0 O 使生 产 环 境净 化 。纱 体 边 缘
没有杂 乱 的纤维 , 的捻度 分 布均匀 , 善 了纱体 结 纱 改 构 , 的质量 提高 ( 图 1 。 纱 见 )
中 图分 类 号 : S 0 . 文 献 标 识 码 : 文 章 编 号 :0 9 2 5 2 1 )5 0 5 ~ O T 14 7 B 10 - 6 X(0 O O — 0 7 4
紧密 纺技 术 的研 制 开 发 及 应 用 , 环 锭 纺更 加 使
三角 区并 使 细 纱 在 主牵 伸 区形 成 更 理 想 的 纱 线 结
较短 , 线 的重量减 少不 大 , 方 面可节 约原料 , 纱 一
图 1 普通环锭纱与 紧密环锭纱外形 比较
另 一方 面 使 再 卷绕 时 可 省 去 出烧 毛 时 在 纱 线 上 残
留的灰 尘 。
b )在 环锭 纺 三上 三下 的 三 罗拉 牵 伸 系统 的前
紧 密纺 纱 的 断 裂伸 长 及 断 裂强 力 都很 高 , 紧 用 密纺 纱织 的机 织 布具 有 较 高 断 裂 强 力 、 裂 伸 长率 断
紧 密 纺纱 有 很 好 的 内摩 檫 阻力 , 的 强 力 高 , 纱
在 捻 度减 小 时 纱 线 的 强 力 不 会 明 显 降 低 , 以在 所 相 同支数 下 紧 密 纱 的 捻 度 可 比普 通 环 锭 纱 减 少 , 这 意 味着 纺 同 支 纱 可 提 高 引 出 速 度 , 加 产 量 并 增 使 织 物手 感 柔 软 。紧 密 纺 纱 的 毛 羽 少 , mm 以上 3 的毛羽 比普 通环 锭 纱 减 少 3 。 因此 烧 毛 的时 间 1
环锭纺、气流纺、喷气纺、涡流纺、赛络纺、紧密纺简介

环锭纺、气流纺、喷气纺、涡流纺、赛络纺、紧密纺简介环锭纺、气流纺、喷气纺、涡流纺、赛络纺、紧密纺简介环锭纺环锭纺纱是现时市场上用量最多,最通用之纺纱方法,条子或粗纱经牵伸后的纤维条通过环锭钢丝圈旋转引入,筒管卷绕速度比钢丝圈快,棉纱被加捻制成细纱.广泛应用于各种短纤维的纺纱工程.如普梳,精梳及混纺,钢丝圈由筒管通过纱条带动绕钢领回转.进行加捻,同时,钢领的摩擦使其转速略小于筒管而得到卷绕.纺纱速度高,环锭纱的形态,为纤维大多呈内外转移的圆锥形螺旋线,使纤维在纱中内外缠绕联结,纱的结构紧密,强力高,适用于制线以及机织和针织等各种产品。
环锭纺(精梳)流程:清花间--梳棉--预并条--条并卷--精梳--头道并条--二道并条--粗纱--细纱--络筒环锭纺(普梳)流程:清花间--梳棉--头道并条--二道并条--粗纱--细纱--络筒气流纺气流纺不用锭子,主要靠分梳辊、纺杯、假捻装置等多个部件。
分梳辊用来抓取和分梳喂入的棉条纤维,同过他的高速回转所产生的离心力可把抓取的纤维甩出。
纺杯是个小小的金属杯子,他的旋转速度比分梳辊高出10倍以上,由此产生的离心作用,把杯子里的空气向外排;根据流体压强的原理,使棉纤维进入气流杯,并形成纤维流,沿着杯的内壁不断运动。
这时,杯子外有一根纱头,把杯子内壁的纤维引出来,并连接起来,再加上杯子带着纱尾高速旋转所产生的钻作用,就好像一边“喂”棉纤维,一边加纱线搓捏,使纱线与杯子内壁的纤维连接,在纱筒的旋绕拉力下进行牵伸,连续不断的输出纱线,完成气流纺纱的过程。
气流纺的特征气流纺纱有速度大、纱卷大、适应性广、机构简单和不用锭子、钢领、钢丝圈的优点,可成倍的提高细纱的产量。
气流纺与环锭纺的区别气流纺与环锭纺一个是新型纺织技术,一个是老式纺纱技术。
气流纺是气流纺纱,而环锭纺则是机械纺,就是由锭子和钢铃、钢丝圈进行加捻,由罗拉进行牵伸。
而气流纺则是由气流方式输送纤维,由一端握持加捻。
一般来说,环锭纱毛羽较少,强度较高,品质较好。
紧密纺与环锭纺毛纱性能分析

纺织科 技 避展
・4 ・ 9
紧 密 纺 与 环 锭 纺 毛 纱 性 能 分 析
郭方霞 , 贾丽 霞 , 陶亚 琼
( 新疆大学 , 新疆 乌鲁木 齐 80 4 ) 3 0 6 摘 要: 通过实验 , 测试 同规格 的紧密纺精梳毛 纱与传 统环锭 纺精梳毛 纱的强力、 毛羽 、 条干等各种性 能, 并进行分析
线 在 加捻过 程 中可 以把 几 乎全 部纤 维 捻 入 纱 线 中 , 纤
原 料 : 毛 / VA(7 1) 环 锭 纺 管 纱 、 密纺 管 澳 P 8/ 3 、 紧
纱、 紧密纺筒纱 均为河南华成 毛纺有 限公 司提供。紧 密 纺精 梳毛 纱是 在 B 8 53型细 纱机 上安装 Ei le紧密 纺 t
注 : 中数据为 3 纱文统计结果的平均但。 表 批
文 章 编 号 :6 3 0 5 (0 0 0 -0 4 -0 17 - 3 6 2 1 )5 0 9 3
羊毛是纺织工业的重要原料之一 , 它吸湿性强 , 保
暖性 好 , 随着 人 们 消 费 观 念 的 改 变 和生 活水 平 的进 但
一
表 1 1. e 5 4tx传统纺和 紧密纺强力与伸长率 比较
比较 , 结果 表 明 , 数 相 同 , 号 紧密 纺 毛 纱 的 断 裂 强 力 、 断裂 伸 长 率 、 羽 、 干 等 性 能都 优 于传 统 环锭 纺 毛 纱 。 毛 条
关 键 词 : 密 纺 ; 锭 纺 ; 纱 ; 能 测 试 紧 环 毛 性
中图分类号 : 142 TS 0 .
文献 标 识 码 : B
・5 ・ 0
纺织科 技 避展
21 年第 5 00 期
紧密竹节纱与环锭竹节纱的性能比较
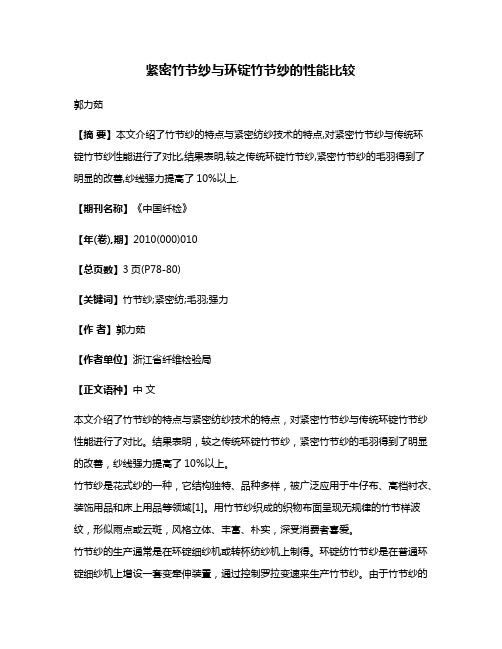
紧密竹节纱与环锭竹节纱的性能比较郭力茹【摘要】本文介绍了竹节纱的特点与紧密纺纱技术的特点,对紧密竹节纱与传统环锭竹节纱性能进行了对比,结果表明,较之传统环锭竹节纱,紧密竹节纱的毛羽得到了明显的改善,纱线强力提高了10%以上.【期刊名称】《中国纤检》【年(卷),期】2010(000)010【总页数】3页(P78-80)【关键词】竹节纱;紧密纺;毛羽;强力【作者】郭力茹【作者单位】浙江省纤维检验局【正文语种】中文本文介绍了竹节纱的特点与紧密纺纱技术的特点,对紧密竹节纱与传统环锭竹节纱性能进行了对比。
结果表明,较之传统环锭竹节纱,紧密竹节纱的毛羽得到了明显的改善,纱线强力提高了10%以上。
竹节纱是花式纱的一种,它结构独特、品种多样,被广泛应用于牛仔布、高档衬衣、装饰用品和床上用品等领域[1]。
用竹节纱织成的织物布面呈现无规律的竹节样波纹,形似雨点或云斑,风格立体、丰富、朴实,深受消费者喜爱。
竹节纱的生产通常是在环锭细纱机或转杯纺纱机上制得。
环锭纺竹节纱是在普通环锭细纱机上增设一套变牵伸装置,通过控制罗拉变速来生产竹节纱。
由于竹节纱的强力低,而紧密纺技术能明显提高单纱强力,故本文尝试采用紧密纺环锭细纱机纺制竹节纱,并与传统环锭纺竹节纱性能进行了对比分析。
1.1 竹节纱的结构特点竹节纱的外观特征是在长度方向上忽粗忽细,它的几何结构如图1所示。
竹节纱体由基纱部分(AB段)、竹节部分(CD段)和过渡部分组成。
其中过渡部分包括基纱转为竹节的渐变部分Δ1和由竹节转为基纱的渐变部分Δ2。
竹节纱的特征参数有基纱号数、竹节粗度D(倍率)、各段间距l1(节距)和各段竹节长度l2(节长)。
竹节纱按竹节的分布情况可分为无规律竹节纱和有规律竹节纱。
无规律竹节纱竹节呈零乱分布,竹节间没有固定的节距;有规律竹节纱又可分为等间距竹节纱和有规律不等间距竹节纱。
前者所有相邻竹节间间距相等,后者由数个不等节距分布的竹节形成一个循环周期。
1.2 竹节纱捻度分布特点竹节纱的捻度分布同一般纱线不同,不能达到均匀分布。
环锭纺、气流纺、喷气纺、涡流纺、赛络纺、紧密纺简介

环锭纺、气流纺、喷气纺、涡流纺、赛络纺、紧密纺简介环锭纺环锭纺纱是现时市场上用量最多,最通用之纺纱方法,条子或粗纱经牵伸后的纤维条通过环锭钢丝圈旋转引入,筒管卷绕速度比钢丝圈快,棉纱被加捻制成细纱.广泛应用于各种短纤维的纺纱工程.如普梳,精梳及混纺,钢丝圈由筒管通过纱条带动绕钢领回转.进行加捻,同时,钢领的摩擦使其转速略小于筒管而得到卷绕.纺纱速度高,环锭纱的形态,为纤维大多呈内外转移的圆锥形螺旋线,使纤维在纱中内外缠绕联结,纱的结构紧密,强力高,适用于制线以及机织和针织等各种产品。
环锭纺(精梳)流程:清花间--梳棉--预并条--条并卷--精梳--头道并条--二道并条--粗纱--细纱--络筒环锭纺(普梳)流程:清花间--梳棉--头道并条--二道并条--粗纱--细纱--络筒气流纺气流纺不用锭子,主要靠分梳辊、纺杯、假捻装置等多个部件。
分梳辊用来抓取和分梳喂入的棉条纤维,同过他的高速回转所产生的离心力可把抓取的纤维甩出。
纺杯是个小小的金属杯子,他的旋转速度比分梳辊高出10倍以上,由此产生的离心作用,把杯子里的空气向外排;根据流体压强的原理,使棉纤维进入气流杯,并形成纤维流,沿着杯的内壁不断运动。
这时,杯子外有一根纱头,把杯子内壁的纤维引出来,并连接起来,再加上杯子带着纱尾高速旋转所产生的钻作用,就好像一边“喂”棉纤维,一边加纱线搓捏,使纱线与杯子内壁的纤维连接,在纱筒的旋绕拉力下进行牵伸,连续不断的输出纱线,完成气流纺纱的过程。
气流纺的特征气流纺纱有速度大、纱卷大、适应性广、机构简单和不用锭子、钢领、钢丝圈的优点,可成倍的提高细纱的产量。
气流纺与环锭纺的区别气流纺与环锭纺一个是新型纺织技术,一个是老式纺纱技术。
气流纺是气流纺纱,而环锭纺则是机械纺,就是由锭子和钢铃、钢丝圈进行加捻,由罗拉进行牵伸。
而气流纺则是由气流方式输送纤维,由一端握持加捻。
一般来说,环锭纱毛羽较少,强度较高,品质较好。
气流纺工序短,原料短绒较多,纱线毛,支数和拈度不能很高,价格也较低。
正确看待紧密纺

一16第25届金国毛纺年会论文统环锭纺与紧密纺加捻区的比较见图1,左为传统环锭纺,右为紧密纺。
不管是什么形式的紧密纺,其基本原理都可以用图2表示。
从A-A、经C~C、到B—B为纤维收缩控制区。
目前,根据控制纤维的形式,可将紧密纺分为气动负压集聚式和机械集聚式两大类。
1.1气动负压集聚式利用负压气流使纤维须条收缩宽度。
根据吸附、凝聚纤维须条的位置,又可分为下凝聚和上凝聚。
几种典型的气动负压集聚式如表l。
.a矗A二灿之》们U墓.i“I『图1传统环锭纺与紧密纺加捻区的比较图2传统环锭纺与紧密纺成纱原理比较表l紧密纺纱设备的主要形式凝聚位置主要凝聚部件丰要开发厂商品名I:凝聚带孔胶髑套加罗拉德国青泽下凝聚抽吸辊瑞十赢达卡摩下凝聚嘲格嘲套或织物嘲加吸管德国绪森倚丽下凝聚嘲格嘲套或织物嘲加吸管意人利马佐卫下凝聚嘲格嘲或织物嘲加吸管、罗拉U本十Lu新锐下凝聚叫格嘲或织物嘲加吸管、罗挣浙江U发1.2机械集聚式不增加气动负压,只用固态机械使纤维须条收缩宽度。
其代表是瑞士罗托卡夫特(Rotorcrafl)公司的RoCoS型磁力紧密纺纱系统。
2几种典型的紧密纺系统2.1瑞士立达(Rieter)公司卡摩纺(Com4和ComforSpin)系统用带有密集小孔的金属导气辊代替了细纱机的前下罗拉,负压气流透过导气辊的凝聚小孔将纤维束向凝聚小孔中心线集聚。
随着导气辊的转动,集聚效应一赢延伸到导气辊与输出胶辊组成的输出钳口之下。
导气辊结构见图3,该紧密纺系统结构及原理如图4。
主要特点:无易损件,运行平稳可靠,结构简单精致;造价高,改装成本高,不能在传统细、{麦桃:E加装;前罗拉被直径较大的导气辊筒代替,影响了摩擦力界的理想分布,对提高条干均匀度不利,这一特点同时使可纺纤维的最短长度受到限制。
图3导气辊结构l~时皮鞭2一一气慑肆向鞭簟3一撇嘲皮瓤4一-t风糖惮5.-蒲筲獭袖孓一囊一梦摭7一炉髓嘲4corn4结构艨穰黼2.2德国青泽(Zinser)公司AirComTex系统采用四罗拉牵伸,前三根罗拉同传统设备一第25届全国毛纺年会论文17样为牢伸区,第四上输出胶棍连接吸风系统,异型截面的吸风管上外套打孔皮圈,用以集聚纤维。
环锭纺、气流纺、喷气纺、涡流纺、赛络纺、紧密纺简介
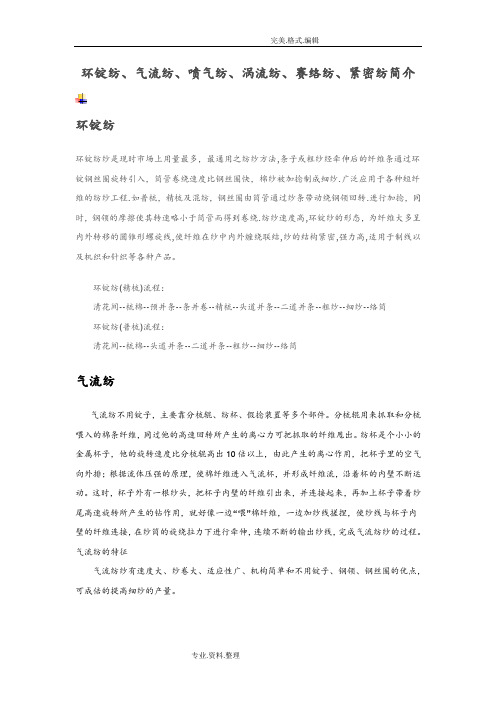
环锭纺、气流纺、喷气纺、涡流纺、赛络纺、紧密纺简介环锭纺环锭纺纱是现时市场上用量最多,最通用之纺纱方法,条子或粗纱经牵伸后的纤维条通过环锭钢丝圈旋转引入,筒管卷绕速度比钢丝圈快,棉纱被加捻制成细纱.广泛应用于各种短纤维的纺纱工程.如普梳,精梳及混纺,钢丝圈由筒管通过纱条带动绕钢领回转.进行加捻,同时,钢领的摩擦使其转速略小于筒管而得到卷绕.纺纱速度高,环锭纱的形态,为纤维大多呈内外转移的圆锥形螺旋线,使纤维在纱中内外缠绕联结,纱的结构紧密,强力高,适用于制线以及机织和针织等各种产品。
环锭纺(精梳)流程:清花间--梳棉--预并条--条并卷--精梳--头道并条--二道并条--粗纱--细纱--络筒环锭纺(普梳)流程:清花间--梳棉--头道并条--二道并条--粗纱--细纱--络筒气流纺气流纺不用锭子,主要靠分梳辊、纺杯、假捻装置等多个部件。
分梳辊用来抓取和分梳喂入的棉条纤维,同过他的高速回转所产生的离心力可把抓取的纤维甩出。
纺杯是个小小的金属杯子,他的旋转速度比分梳辊高出10倍以上,由此产生的离心作用,把杯子里的空气向外排;根据流体压强的原理,使棉纤维进入气流杯,并形成纤维流,沿着杯的内壁不断运动。
这时,杯子外有一根纱头,把杯子内壁的纤维引出来,并连接起来,再加上杯子带着纱尾高速旋转所产生的钻作用,就好像一边“喂”棉纤维,一边加纱线搓捏,使纱线与杯子内壁的纤维连接,在纱筒的旋绕拉力下进行牵伸,连续不断的输出纱线,完成气流纺纱的过程。
气流纺的特征气流纺纱有速度大、纱卷大、适应性广、机构简单和不用锭子、钢领、钢丝圈的优点,可成倍的提高细纱的产量。
气流纺与环锭纺的区别气流纺与环锭纺一个是新型纺织技术,一个是老式纺纱技术。
气流纺是气流纺纱,而环锭纺则是机械纺,就是由锭子和钢铃、钢丝圈进行加捻,由罗拉进行牵伸。
而气流纺则是由气流方式输送纤维,由一端握持加捻。
一般来说,环锭纱毛羽较少,强度较高,品质较好。
气流纺工序短,原料短绒较多,纱线毛,支数和拈度不能很高,价格也较低。
- 1、下载文档前请自行甄别文档内容的完整性,平台不提供额外的编辑、内容补充、找答案等附加服务。
- 2、"仅部分预览"的文档,不可在线预览部分如存在完整性等问题,可反馈申请退款(可完整预览的文档不适用该条件!)。
- 3、如文档侵犯您的权益,请联系客服反馈,我们会尽快为您处理(人工客服工作时间:9:00-18:30)。
<1>紧密纺是在改进的新型环锭细纱机上进行纺纱的一种新型纺纱技术。
其纺纱机理主要是:在环锭细纱机牵引装置前增加了一个纤维凝聚区,基本消除了前罗拉至加捻点之间的纺纱加捻三角区。
纤维须条从前罗拉前口输出后,先经过异形吸风管外套网眼皮圈,须条在网眼皮圈上运动,由于气流的收缩和聚合作用,通过异形管的吸风槽使须条集聚、转动,逐步从扁平带状转为圆柱体,纤维的端头均捻入纱线内,因此成纱非常紧密,纱线外观光洁、毛羽少。
紧密纺纱线强力较高,毛羽较少。
<2>赛络纺是由两根有一定间距的须条喂入细纱牵伸区,分别牵伸后加捻成纱,两股须条存在一股断头后另一股跑单纱的情况,并且在纺纱张力稳定的情况下不断头,造成错支纱,为保证纺纱质量,需加装赛络纺单纱打断装置,一股断头后打断装置能将另一股单纱打断。
新西兰羊毛研究机构的子公司发展公司是首批授权的赛络纺技术传授者之一,该技术能生产单股精梳毛纱,这种纱可以不经上浆或任何后整理而直接作为经纱进行织造。
无须双股并纱或应用保护涂层面而直接织造单股纱的能力,长期来一直是精梳毛纺业追寻的目标。
赛络纺纱线显着增加了生产效率,并为羊毛开发新的产品提供了机遇。
该技术的基础是一对附加罗拉,它与一个简单的夹钳一起安装在细纱机的牵伸摇架上。
这些获专利的罗拉有一个特殊的沟槽表面,它改变了纤维捻入牵伸须条的方式,而对常规操作无任何影响。
它也可以与自动落筒装置相容。
乍看起来成品纱与常规纱无任何区别,但磨损试验清楚地显示了它非常优越的质量。
该加工过程保证纤维被牢牢地锁入纱线的结构中,使纱线更光洁,从而能抵御织机上的连续摩擦和磨损。
然而,单纱的织造不仅仅考虑产品质量,更多的是考虑生产效率。
首先,由于免去了加捻和相应的处理,整个生产过程大大缩短。
其次,与常规纱相比生产同样数量的织物,由于赛络纺只需提供一半长度的纱,因而显着地提高了细纱生产率,且由于纺制两倍于常规纱的支数,断头率也显着下降。
在可织单纱计划的中试阶段,意大利、澳大利亚和新西兰的工厂将该罗拉各安装了一台细纱机,生产出商业批量的纱,接着将这些纱织入一系列的织物中。
所有的报告都反映出纺纱和织造的效率都是令人满意的。
在强力、伸长和均匀度方面,赛罗纺纱与传统的双股纱没有明显的差别。
纺纱后赛络纺纱将以普通的单股纱同样的方式进行自动蒸压定形、络筒、清纱和捻接。
采用赛罗纺纱技术纺股线可以省却两股并合和加捻的工序而降低生产成本。
它在环锭精纺机上平行喂入两根粗纱,经牵伸后在前罗拉输出再将两股须条加捻成纱。
印度纺织科学技术研究院对涤毛混纺比为55/45的赛罗纺纱工艺参数作了研究,并且与同等纱支的单纱和双纱作了对比。
在梳毛纺纱工艺系统中,采用3d涤纶和22.5μm羊毛以55/45混纺比纺Nm20赛络纱,用2.2d涤纶和20μm羊毛以55/45混纺比纺Nm35赛络纱,采用6、8、10、12、14mm五种不同的须条间距和75、85、95三种不同的捻系数分别进行试验。
成纱进行CV、纱疵、毛羽、单纱强力和断裂伸长以及耐磨性和压缩系数的对比。
同时与同等纱支的单纱和双纱进行对比。
试验结果表明,涤毛混纺的赛络纱的特性可以通过工艺参变数的选择而优化。
须条间距为10mm时成纱CV和耐磨性较好,然而间距增大会使细节增多。
当须条间距为12mm 时强力和断裂伸长最大。
须条间距不同对成纱毛羽因纱支而异,间距增加到10mm,则长短毛羽趋向减少。
须条间距对成纱压缩系数没有影响。
一般捻系数较大则成纱不匀,毛羽和压缩系数较低,强力和耐磨性较好。
除CV、纱疵和断裂伸长外,赛络纱的其他性能比同等纱支的单纱或双纱更好。
在赛络纺纱线结构中成纱与单股均有一定的捻度,其成纱过程中实际进行了二次加捻,其单股与成纱具有同向加捻的效果,从而纱线外表光洁、平滑、毛羽少、耐磨性能好,虽然是单纱但有股线的效果,可部分取代股线,因而减少了工序,降低了成本,增加了企业经济效益。
赛络纺与普通环锭纱相比,毛羽大大减少,为后道工序的织造提供了良好的条件。
由于双粗纱喂入,细纱机上的吊锭需要增加一倍,另外每一股粗纱的定重要比同实纺支数的传统单纱的粗纱轻一半,而且赛络纺必须有切断装置,在纺纱过程中,万一有一股纤维束断裂,必须及时将另一股纤维束切断,否则会造成纱疵。
有不少文章讨论赛络纺粗纱间距大小问题,笔者认为粗纱间距确实对纺纱质量有很大的<BR>关系,但却不能有一个定值。
为什么?因为这粗纱间距的确定还受原料情况的制约。
假设粗纱间距定14毫米,如果你的原料强力较差,或者段毛较多,设备状态较差那就很容易产生条干不匀以及断头增加,相反地你适当将开档缩小一点,那纱线条干质量断头数量就会有所改善。
反过来说,你定了粗纱间距以后,你必须控制你的原料物理指标使其符合纺纱要求。
赛络纺一般都配置打断器,打断器都依据粗纱间距来设计的,当须条间距变小后,纱线断头时打断器可能检测不出(无断头信号)从而不能打搅断另一股纤维束以致产生跑单纱的纱疵。
介绍了赛络纺纱技术的原理,在棉纺细纱机上的实现方法,赛络纺纯棉精梳纱、混纺纱和涤粘复合纱的纺纱工艺,对比分析了赛络纺成纱质量与环锭纺成纱质量。
认为赛络纱的成纱毛羽、条干、强力优于环锭纱,但细节差于环锭纱。
传统环锭纺纱成纱毛羽多,毛羽不仅影响纱线本身的表面光洁度和纤维强力利用系数,而且影响后工序加工的顺利进行。
另一方面随着织造技术进步,无梭织机对成纱质量的要求越来越高,毛羽问题更为突出。
为了减少成纱毛羽,可以在原料选配、工艺优化、器材选择和操作管理等方面采取措施。
同时,也可以应用纺纱新技术,如紧密纺纱技术、络筒机吹捻装置。
此外,赛络纺纱技术也可以减少成纱毛羽。
该纺纱原理是1975年~1976年由澳大利亚联邦科学与工业研究机构(CSIRO)发明,最初的目的是要减少毛纱毛羽。
1978年国际羊毛局将这项科研成果推向实用化,1980年正式向世界各国推荐。
赛络纺纱主要用于羊毛、毛型涤纶、腈纶的纯纺或混纺,在棉纺细纱机上也可以应用。
赛络纺纱技术在实际生产中实施起来非常简便,对环锭细纱机稍作改动即可,改造后的纺纱机既可纺制赛络纱线,也可以根据需要随时方便地恢复成原来的普通环锭细纱机。
1 赛络纺纱方法:赛络纱可以用于机织或针织,其工艺是将两根具有一定间距的粗纱平行喂人到细纱机同一牵伸区进行牵伸,然后在同一个锭子上加捻卷绕。
具体地说,需要进行以下几方面的改造:(1)改装粗纱架,增加一倍的粗纱吊锭,托锭加吊锭改装更方便些;(2)将原来牵伸机构中的横动喇叭口调换为双眼形式;(3)导纱横动装置固定在中央位置或作小动程横动;(4)增加断头自停装置,其作用是防止纺单纱现象,即当一根粗纱条断头时,为避免产生长片段细节纱疵,必须将另一根纱条也及时打断。
近年来,棉纺行业也开始引用这种纺纱方法。
一般棉纺所纺纱线多为本色纱,只要减少挡车工的看台数,可以不采用价格昂贵的断头自停装置。
2 赛络纺纱实践2.1纯棉精梳产品在改造过的细纱机上纺CJ 14.5 tex赛络纱,采用两种不同的纺纱工艺流程。
赛络纺CJ 14.5 tex与环锭纺CJ 14.5 tex成纱质鼍对比见表1。
从表1可以看出,赛络纱的条干CV值、单纱断裂强力、断裂伸长率等指标优于环锭纱,但细节偏多。
方案一所纺赛络纱的条干、细节、粗节、单强、伸长率等指标优于方案二,综合性能最佳。
参照2001年乌斯特公报,方案一的成纱条干、粗节、棉结都相当于5%~25%的水平,细节相当于25%~50%的水平。
2.2混纺产品在相同条件下纺制T/CJ 65/35 13.1 tex赛络纱和普通环锭纱,赛络纺纱工艺为:粗纱号数330tex,牵伸倍数(前×后)39.6倍×1.25倍,捻度34.5捻/m;细纱机前罗拉速度229 r/min,锭速17278 r/min。
成纱质量对比见表2。
同细度的赛络纱与环锭纱相比,赛络纱单强高,百米重量CV小,毛羽减少,条干质量基本相当,细节多,粗节、棉结数量相当。
2.3 复合纱当喂入两根粗纱为不同原料时,纺出纱为复合纱,又称AB纱。
利用赛络纺纱技术纺制T/R55/45 18.5 tex复合纱,细纱工艺为:涤纶粗纱定量3.9g/10 m,粘胶粗纱定量3.2g/10 m,细纱捻系数314,罗拉隔距19 mm×33 mm,后区牵伸倍数1.25倍,钳口隔距3.0 mm,钢丝圈型号FU5/0,前罗拉速度230 r/min,锭速14 400 r/min。
成纱质量为:条干CV 13.46%,细节5个/km,粗节46个/km,棉结59个/km,单强23.3 cN/tex,单强CV值5.72%,断裂伸长率10.86%,断裂伸长CV5.09%。
由此可以看出,赛络纺复合纱的质量指标比较理想。
3 结束语赛络纱质量较好,尤其是成纱毛羽、条干、强力指标优于环锭纱,可以满足机织和针织用纱要求。
赛络纱的缺点是细节偏多,主要是由于从前钳口输出两根纱条的汇聚点在纺纱过程中上下不断波动,引起汇聚点至前钳口一段纱条上的捻度大小发生变化,捻度小、意外牵伸大造成细节偏多。
同时赛络纺加工时要求细纱大牵伸、粗纱小定量,又影响到了经济效益,这方面需要进一步改进提高。
介绍了赛络纺纱技术的原理,在棉纺细纱机上的实现方法,赛络纺纯棉精梳纱、混纺纱和涤粘复合纱的纺纱工艺,对比分析了赛络纺成纱质量与环锭纺成纱质量。
认为赛络纱的成纱毛羽、条干、强力优于环锭纱,但细节差于环锭纱。
传统环锭纺纱成纱毛羽多,毛羽不仅影响纱线本身的表面光洁度和纤维强力利用系数,而且影响后工序加工的顺利进行。
另一方面随着织造技术进步,无梭织机对成纱质量的要求越来越高,毛羽问题更为突出。
为了减少成纱毛羽,可以在原料选配、工艺优化、器材选择和操作管理等方面采取措施。
同时,也可以应用纺纱新技术,如紧密纺纱技术、络筒机吹捻装置。
此外,赛络纺纱技术也可以减少成纱毛羽。
该纺纱原理是1975年~1976年由澳大利亚联邦科学与工业研究机构(CSIRO)发明,最初的目的是要减少毛纱毛羽。
1978年国际羊毛局将这项科研成果推向实用化,1980年正式向世界各国推荐。
赛络纺纱主要用于羊毛、毛型涤纶、腈纶的纯纺或混纺,在棉纺细纱机上也可以应用。
赛络纺纱技术在实际生产中实施起来非常简便,对环锭细纱机稍作改动即可,改造后的纺纱机既可纺制赛络纱线,也可以根据需要随时方便地恢复成原来的普通环锭细纱机。
1 赛络纺纱方法赛络纱可以用于机织或针织,其工艺是将两根具有一定间距的粗纱平行喂人到细纱机同一牵伸区进行牵伸,然后在同一个锭子上加捻卷绕。
具体地说,需要进行以下几方面的改造:(1)改装粗纱架,增加一倍的粗纱吊锭,托锭加吊锭改装更方便些;(2)将原来牵伸机构中的横动喇叭口调换为双眼形式;(3)导纱横动装置固定在中央位置或作小动程横动;(4)增加断头自停装置,其作用是防止纺单纱现象,即当一根粗纱条断头时,为避免产生长片段细节纱疵,必须将另一根纱条也及时打断。