紧密赛络纺成纱机理及.
赛络纺纱原理
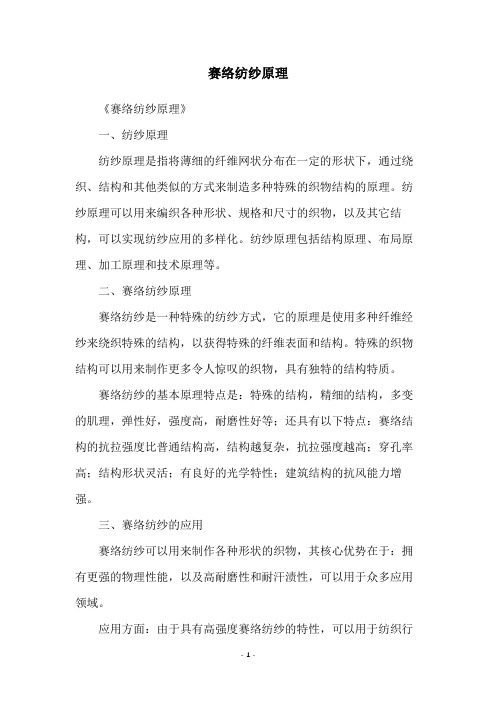
赛络纺纱原理
《赛络纺纱原理》
一、纺纱原理
纺纱原理是指将薄细的纤维网状分布在一定的形状下,通过绕织、结构和其他类似的方式来制造多种特殊的织物结构的原理。
纺纱原理可以用来编织各种形状、规格和尺寸的织物,以及其它结构,可以实现纺纱应用的多样化。
纺纱原理包括结构原理、布局原理、加工原理和技术原理等。
二、赛络纺纱原理
赛络纺纱是一种特殊的纺纱方式,它的原理是使用多种纤维经纱来绕织特殊的结构,以获得特殊的纤维表面和结构。
特殊的织物结构可以用来制作更多令人惊叹的织物,具有独特的结构特质。
赛络纺纱的基本原理特点是:特殊的结构,精细的结构,多变的肌理,弹性好,强度高,耐磨性好等;还具有以下特点:赛络结构的抗拉强度比普通结构高,结构越复杂,抗拉强度越高;穿孔率高;结构形状灵活;有良好的光学特性;建筑结构的抗风能力增强。
三、赛络纺纱的应用
赛络纺纱可以用来制作各种形状的织物,其核心优势在于:拥有更强的物理性能,以及高耐磨性和耐汗渍性,可以用于众多应用领域。
应用方面:由于具有高强度赛络纺纱的特性,可以用于纺织行
业,用于制作拉链、细线经纱、带子等;也可以用于织造运动服装,如运动服饰、军服饰等;在服装服饰行业,赛络纺纱可用于制作棉质印花布、轻薄棉布、薄毛圈布等;还可以用于制作家居纺织品、汽车内饰、室内装饰等。
紧密纺纱的原理性能特点及产品开发
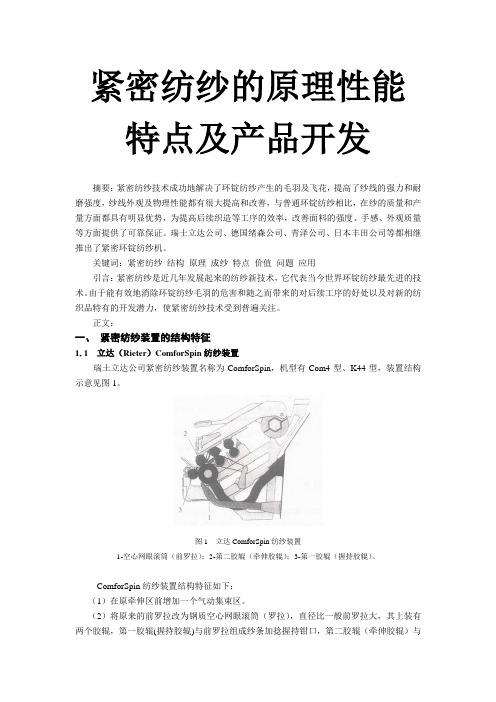
紧密纺纱的原理性能特点及产品开发摘要:紧密纺纱技术成功地解决了环锭纺纱产生的毛羽及飞花,提高了纱线的强力和耐磨强度,纱线外观及物理性能都有很大提高和改善,与普通环锭纺纱相比,在纱的质量和产量方面都具有明显优势,为提高后续织造等工序的效率,改善面料的强度、手感、外观质量等方面提供了可靠保证。
瑞士立达公司、德国绪森公司、青泽公司、日本丰田公司等都相继推出了紧密环锭纺纱机。
关键词:紧密纺纱结构原理成纱特点价值问题应用引言:紧密纺纱是近几年发展起来的纺纱新技术,它代表当今世界环锭纺纱最先进的技术。
由于能有效地消除环锭纺纱毛羽的危害和随之而带来的对后续工序的好处以及对新的纺织品特有的开发潜力,使紧密纺纱技术受到普遍关注。
正文:一、紧密纺纱装置的结构特征1.1 立达(Rieter)ComforSpin纺纱装置瑞土立达公司紧密纺纱装置名称为ComforSpin,机型有Com4型、K44型,装置结构示意见图1。
图1 立达ComforSpin纺纱装置1-空心网眼滚筒(前罗拉);2-第二胶辊(牵伸胶辊);3-第一胶辊(握持胶辊)。
ComforSpin纺纱装置结构特征如下:(1)在原牵伸区前增加一个气动集束区。
(2)将原来的前罗拉改为钢质空心网眼滚筒(罗拉),直径比一般前罗拉大,其上装有两个胶辊,第一胶辊(握持胶辊)与前罗拉组成纱条加捻握持钳口,第二胶辊(牵伸胶辊)与前罗拉组成牵伸区的前牵伸钳口。
第一胶辊与第二胶辊间为须条的集聚区。
(3)前罗拉为钢质网眼滚筒,形似一个小尘笼,内有圆形截面吸聚管(负压)与吸风风机等组成吸聚罗拉,即有负压的前罗拉。
圆形截面吸聚管上装有一块开了一个由后向前逐渐变窄的V形狭槽的工程塑料部件组成的吸气槽,V形槽长度跟须条与前罗拉接触长度相适应,并与输出方向有一定偏斜度,当在主牵伸区须条离开牵伸钳口时,因负压的吸附作用,须条由V形槽控制在网眼前罗拉上,并向前输送到第一胶辊处,即握持钳口处。
1.2 绪森(Suessen)Elite纺纱装置德国绪森公司紧密纺纱装置名称为Elite,机型有Fiomax E1型、Fiomax E2型,装置结构示意见图2。
紧密纺和赛络纺知识

紧密纺和赛络纺知识近年来,关于紧密纺及赛络纺两种新型纺纱方法的报道很多,这两种新型纺纱工艺对于提高成纱质量的效果也是大家所公认的,本文将根据我公司4年多来的研究结果及用户的使用情况,对两种纺纱工艺的特点及成纱质量进行分析。
紧密纺纱工艺尽管在机械结构上有所不同,但有一点是相同的,即在完成工艺要求的牵伸之后,在加捻之前,把从前罗拉钳口输出的较宽的纱条进行聚集,使得纱条宽度变的很窄,单纤维之间排列更加紧密,并且尽量保持在这种状态下进入加捻区。
虽然有的报道说是此举消灭了“加捻三角区”,但实际上纱条在加捻前后的宽度是不一样的。
所以,紧密纺的加捻罗拉钳口处仍然有一个极小的所谓“加捻三角区”,当然其危害性已降低到最小。
正是由于上述成纱机理,用紧密纺工艺纺成的细纱具有以下特点: 1.由于在加捻前,纱条中单纤维充分伸直,相互平行,而且排列紧密,所以在加捻罗拉钳口处(也叫阻捻罗拉,因为其有阻止捻度传递的作用),纱条直径变得很小,所以基本消除了“加捻三角区”,由于加捻前单纤维充分伸直、平行,没有毛羽伸出纱条主体,所以成纱毛羽很少,特别是3毫米以上毛羽极少。
2.在细纱中由于各单纤维是在伸直、平行的状态下加捻,在单纱受到拉力时,各单纤维受力基本一致,所以紧密纺强力比传统单纱高。
而且由于紧密纱中的单纤维排列紧密,相互间抱合力大,这也有助于提高纱线的强力。
3.在紧密纺工艺中,纱条是在完成了工艺规定的牵伸之后再进行聚集,所以其条干不匀的指标没有大的改善,但在其聚集区有对纱条的整理作用,且在加捻罗拉钳口处加捻时纤维的内、外层转移没有传统工艺强烈,所以紧密纱的条干不匀,粗、细节指标比传统纱要好。
4.由于紧密纱的上述特点,为下道工序提供了非常好的条件,紧密纱毛羽少,所以减轻了上浆、烧毛等工序的压力,在无梭织机的纬纱使用紧密纱时大大减少了引纬的阻力,提高了织机效率。
5.由于紧密纱纤维排列紧密,和相同号数的传统纱线相比直径小,所以用相同经、纬密织成的布透气性好,布面平整、光滑,是高档纺织品的理想用纱。
紧密赛络纺成纱机理及.

(二)纱线对比研究
加捻纱线的纵向结构分析(350倍)
紧密塞络纺棉纱
紧密纺棉纱
赛络纺棉纱
普通环锭纺棉纱
退捻后纱线的纵向结构(100倍)
紧密赛 络纱 赛络纱 紧密纱 传统环 锭纱
紧密赛 络纱 赛络纱 紧密纱 传统环 锭纱
小结
自制紧密赛络纺纱装置结合了集聚与合股的 双重作用,可有效减小加捻三角区,成纱毛 羽明显减少,尤其是长毛羽可基本消除;纱 线的同向同步加捻,使其结构更加清晰紧密, 表面纤维排列整齐顺直,截面形状也更圆, 退捻后有明显的双股结构;成纱强伸性能和 条干得到了较好的改进。与普通环锭纺单纱、 赛络纱、紧密纱相比,紧密赛络纱突显其优 越性。
10 310 335 360 385 410 捻系数
粗细节和棉结/个
30 25 20 15 10
5 0
310 335 360 385 410 捻系数
断裂强力/cN
吸风负压对纱线性能的影
440 430 420 410 400 390 380
1500
2100 2700 吸风负压/Pa
断裂伸长率/%
5.4 5.2
14.5×2/29
80 70 60 50 40 30 20 10 0
14.5×2/29
9.7×2/19.4 纱线细度/tex
9.7×2/19.4 纱线细度/tex
7.3×2/14.6 7.3×2/14.6
紧密赛 络纱 赛络纱
紧密纱
传统环 锭纱
9.7×2/19.4 纱线细度/tex
紧密纺_赛络纺纺纱经验及其探讨_王方水

紧密纺、赛络纺纺纱经验及其探讨王方水,郭 恒,贾云辉(鲁泰纺织股份有限公司,山东淄博 255100)摘要:介绍了紧密纺、赛络纺等新型纺纱技术原理及紧密纺纱线在色织面料方面的应用;分析紧密纺、赛络纺技术的优点及不足,并将其与普通纺进行对比,指出紧密纺、赛络纺技术生产的纱线质量好、强力高、毛羽少、条干均匀以及下游工序产品质量可进一步提高;加强对设备的日常维护、保养、保持器材部件清洁、运转正常,对充分发挥新型纺纱技术的优势至关重要,但企业要充分考虑其成本因素,应加速研发具有自己特色和自主知识产权,纺织企业能够接受的整机型和改造型的紧密纺细纱机及装置,以提高企业的竞争力。
关键词:紧密纺;塞络纺;优势;不足;器材配置;日常维护;竞争力中图分类号:TS104.7 文献标识码:A 文章编号:1001-9634(2009)03-0057-04收稿日期:2008-10-28作者简介:王方水(1961 ),男,山东淄博人,工程师,主要从事纺纱色织布的研究。
1 紧密纺等新型纺纱自1999年巴黎国际纺织机械展览会,立达(R-ieter )、青泽(Zinser )、绪森(Suessen)等国外纺机公司推出生产紧密纱的环锭细纱机以来,紧密纺纱技术迅速风靡整个纺织界。
紧密纺纱技术对改善纱线品质、提高成纱强力、减少毛羽等方面已经由实践证实,得到了快速发展。
欧洲计划用5a~10a 以紧密纺纱机全部替代普通环锭纺纱机,更有专家预言,未来属于紧密纺。
1.1 紧密纺纱原理紧密纺纱系统多数采用空气动力学原理,在纺纱三角区位置,通过一组集聚元件,使牵伸后的松散纤维须条经过负压吸聚管表面时,利用空气导向作用使纤维紧密地抱合在一起,经导向胶辊输出加捻成纱,纺纱过程中加捻三角区变得很小,基本消失,大大减少浮游外露纤维(即毛羽)的数量。
还有一种紧密纺纱系统不采用吸风而采用机械-磁铁原理工作,如瑞士罗托卡夫特公司生产的罗卡斯(Ro Co S)紧密纺系统装置,其前胶辊和引纱胶辊置于前下罗拉之上,磁性紧密器置于两个胶辊之间,共同形成紧密区。
紧密赛络纺纱技术在细纱工艺中的应用探讨_王晓丽
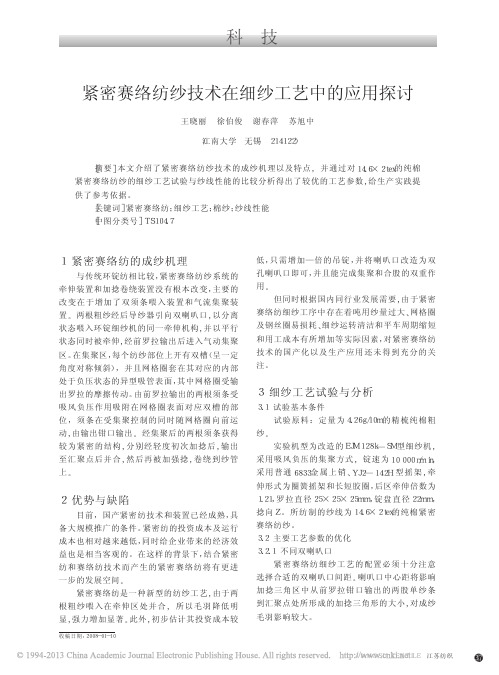
科技紧密赛络纺纱技术在细纱工艺中的应用探讨王晓丽徐伯俊谢春萍苏旭中(江南大学无锡214122)[摘要]本文介绍了紧密赛络纺纱技术的成纱机理以及特点,并通过对14.6×2tex的纯棉紧密赛络纺纱的细纱工艺试验与纱线性能的比较分析得出了较优的工艺参数,给生产实践提供了参考依据。
[关键词]紧密赛络纺;细纱工艺;棉纱;纱线性能[中图分类号]TS104.71紧密赛络纺的成纱机理与传统环锭纺相比较,紧密赛络纺纱系统的牵伸装置和加捻卷绕装置没有根本改变,主要的改变在于增加了双须条喂入装置和气流集聚装置。
两根粗纱经后导纱器引向双喇叭口,以分离状态喂入环锭细纱机的同一牵伸机构,并以平行状态同时被牵伸,经前罗拉输出后进入气动集聚区。
在集聚区,每个纺纱部位上开有双槽(呈一定角度对称倾斜),并且网格圈套在其对应的内部处于负压状态的异型吸管表面,其中网格圈受输出罗拉的摩擦传动。
由前罗拉输出的两根须条受吸风负压作用吸附在网格圈表面对应双槽的部位,须条在受集聚控制的同时随网格圈向前运动,由输出钳口输出。
经集聚后的两根须条获得较为紧密的结构,分别经轻度初次加捻后,输出至汇聚点后并合,然后再被加强捻,卷绕到纱管上。
2优势与缺陷目前,国产紧密纺技术和装置已经成熟,具备大规模推广的条件。
紧密纺的投资成本及运行成本也相对越来越低,同时给企业带来的经济效益也是相当客观的。
在这样的背景下,结合紧密纺和赛络纺技术而产生的紧密赛络纺将有更进一步的发展空间。
紧密赛络纺是一种新型的纺纱工艺,由于两根粗纱喂入在牵伸区处并合,所以毛羽降低明显,强力增加显著。
此外,初步估计其投资成本较低,只需增加—倍的吊锭,并将喇叭口改造为双孔喇叭口即可,并且能完成集聚和合股的双重作用。
但同时根据国内同行业发展需要,由于紧密赛络纺细纱工序中存在着吨用纱量过大、网格圈及钢丝圈易损耗、细纱运转清洁和平车周期缩短和用工成本有所增加等实际因素,对紧密赛络纺技术的国产化以及生产应用还未得到充分的关注。
赛络紧密纺资料

3.1 紧密纺纱的原理
为在环锭纺纱机上达到上述要求,需要在牵伸系统 后面加一个凝聚区,它通常由带狭槽的异形截面吸管 和多孔网格皮圈组成或者由多孔辊筒和辊筒内带长糟 的异形截面吸管组成,以及其他的凝聚装置。
异形截面吸管内呈负压状态, 异形截面吸管的每 个纺纱位置如图有一个长槽。当纤维须条离开钳口时, 它们就被长槽头端的负压气流控制,并被压向带皮圈 多孔辊简的表面;在负压的吸引下,纤维须条沿着长 槽运行至长糟的尾端。纤维须条在整个长槽上都受到 负压控制,使各根纤维紧密排列。
的抖动,加捻平衡受到干扰,因此须条也具有一定捻度。 须条上的平衡捻度大小取决于汇聚点以上须条上的扭矩与 并台加捻时成纱中的扭矩之间的平衡。因而,在平衡状态 下,须条中的捻度,仅仅取决于加捻时的成纱捻度和成纱 须条中的螺旋线半径。
2.1.2 汇聚点位置
双须条纺纱时,只要汇聚点处的加捻平衡受到干扰,在 纱线形成时,须条捻 度被捕获。即使在普通的双须条成纱 过程中(即加捻平衡无抖动),由于须条中的粗、细节和纺 纱张力存在连续随机变化:这导致加捻平衡有细微抖动, 因此,须条捻度也会发生相对较少的随机变异。研究表明, 加捻平衡的周期性抖动,能导致须条位置相当大的变化。
2.3 新发展---赛络菲尔纺
三、紧密纺纱(集聚纺纱)
3.1 紧密纺纱的原理 3.2 紧密纺装置 3.3 紧密纺纱线结构及性能
三、紧密纺纱(集聚纺纱)
毛羽是预测纱线性能的主要指标之一,它是影响纱线后加 工及其产品档次的主要因素。然所有长度超过3mm的毛羽都会 给后续加工和织物质量带来很大危害。
0.1
0
粗节(+50%)/km 10.0
8.0
2.0
棉结(+200%)/km 17
紧密纺纱的原理
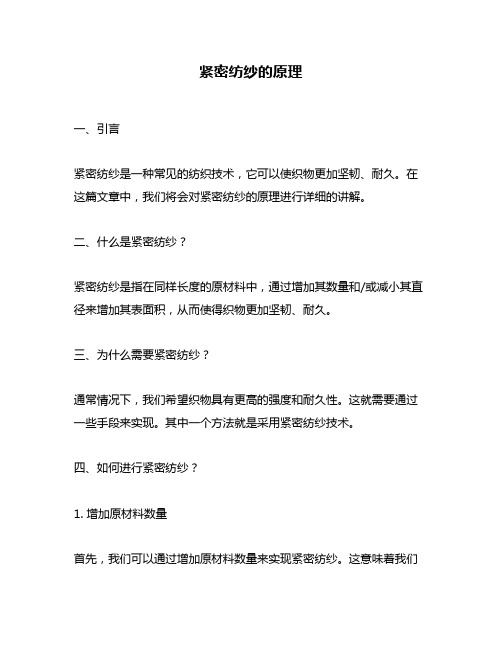
紧密纺纱的原理一、引言紧密纺纱是一种常见的纺织技术,它可以使织物更加坚韧、耐久。
在这篇文章中,我们将会对紧密纺纱的原理进行详细的讲解。
二、什么是紧密纺纱?紧密纺纱是指在同样长度的原材料中,通过增加其数量和/或减小其直径来增加其表面积,从而使得织物更加坚韧、耐久。
三、为什么需要紧密纺纱?通常情况下,我们希望织物具有更高的强度和耐久性。
这就需要通过一些手段来实现。
其中一个方法就是采用紧密纺纱技术。
四、如何进行紧密纺纱?1. 增加原材料数量首先,我们可以通过增加原材料数量来实现紧密纺纱。
这意味着我们需要使用更多的原材料来制造同样长度的线。
这样做会导致线变得更加厚实,表面积也会相应地增大。
2. 减小原材料直径另外一个方法是减小原材料直径。
这意味着我们需要使用更细的线来制造同样长度的织物。
这样做会导致线变得更加细长,表面积也会相应地增大。
3. 组合方法最后,我们可以结合上述两种方法来实现紧密纺纱。
这意味着我们需要同时增加原材料数量和减小原材料直径。
这样做会使得线变得更加厚实和细长,表面积也会相应地增大。
五、如何选择紧密纺纱的方法?通常情况下,我们需要根据具体的需求来选择不同的紧密纺纱方法。
如果需要制造更坚韧、耐久的织物,那么可以选择组合方法;如果只是需要提高织物的强度或耐久性,那么可以选择其中一种方法即可。
六、结论通过本文的讲解,我们了解了紧密纺纱的原理以及如何进行紧密纺纱。
在实际生产中,我们可以根据具体需求来选择不同的紧密纺纱方法,以达到最佳效果。
- 1、下载文档前请自行甄别文档内容的完整性,平台不提供额外的编辑、内容补充、找答案等附加服务。
- 2、"仅部分预览"的文档,不可在线预览部分如存在完整性等问题,可反馈申请退款(可完整预览的文档不适用该条件!)。
- 3、如文档侵犯您的权益,请联系客服反馈,我们会尽快为您处理(人工客服工作时间:9:00-18:30)。
断裂强力/cN
捻系数对纱线性能的影响
420 400 380 360 340 320 300
310 335 360 385 410
捻系数
断裂伸长率/%
5.1 5
4.9 4.8 4.7 4.6 4.5 4.4 4.3 4.2
310 335 360 382 410
捻系数
1-2mm毛羽数/根· (10m)-1
申请发明专利: [1]谢春萍,杨丽丽,徐伯俊等.一种用于自清洁网格圈的紧密纺
撑杆.
谢 谢!!!
2.3、成纱机理:
b1 〉 b2 , h1 〉 h2
赛络纺
紧密赛络
2.4、纱线捻度的形成与分布
捻回可用下式表达 :
T1 T2 LSTZ /(1 4 2 R2TZ 2 )
试中:LS——汇聚点上方的纱条长度;
TZ——股纱的单位长度捻度;
R——螺旋状纱线半径。
一般:
T1=T2=0.8T Z或 a1=a2=0.55aZ
本课题通过对紧密赛络纺的成纱机理和集聚区流场 分析,进行集聚区集聚效果的研究,设计开发合理 的集聚元件,以此对该技术进行了详细的研究,旨 在通过设备改造达到集聚纺与赛络纺的良好结合。 具有深远的理论和现实意义。
主要研究内容
成纱机理研究
纺纱原理 集聚区须条集聚过程
成纱机理 纱线捻度的形
成与分布
集聚区流场研究 流场理论研究
紧密赛络纺纱装 置关键部件研究
须条喂入装置
汇流理论 流场试验研究
集聚区流场的分布规律 轴向风压分布规律
异形管内部深度方向流场分布规律
粗纱筒子架 导纱杆 双喇叭口
气流集聚装置
异形吸风管
双槽设计与优化 网格套圈
传动组件(罗拉盒) 吸风设备
国产细纱机上纺 纱实验
工艺研究
捻系数 吸风负压 集聚牵伸 纺纱效果研究
紧密塞络纺棉纱
紧密纺棉纱
赛络纺棉纱
普通环锭纺棉纱
1-2mm毛羽/根·(10m)-1
断裂强力/cN
对比试验纱线性能的测试
700 600 500 400 300 200 100
0 14.5×2/29
1200 1000 800 600 400 200
0 14.5×2/29
9.7×2/19.4 纱线细度/tex
粗细节和棉结/个
1-2mm毛羽数/根·(10m)-1
320 315 310 305 300 295 290 285 280 275
1500
2100 2700 吸风负压/Pa
50 45 40 35 30 25
20 15 10 5 0
1500
2100 2700 吸风负压/Pa
3-9mm毛羽数/根· (10m)-1
结构
纱线外观结构 纱线解捻后结构
性能
强伸性能 毛羽 条干
二、紧密赛络纺成纱机理研究
紧密塞络纺纺纱原理图 1-双喇叭嘴;2-粗纱;3-后罗拉;4-中罗拉;5-前罗拉;6-异 型吸聚管;7-网格圈;8-控制钳口;9-汇聚点;10-钢丝圈;
11-锭子
2.2、紧密赛络纺中纤维束的运动情况:
vq :前罗拉运动速度; vo :网格套圈的运动速度
0 I II III IV V VI 变频器调节的六档风机频率
3800
3600
3400
Po 3200 3000
Ⅰ Ⅱ
2800
Ⅲ
P
2600 2400
Ⅳ Ⅴ
2200
Ⅵ
2000 1800
1600 1400
1200 1000
1 2 3 4 5 6 7 8 9 10 11 12
异型管上的不同槽口
四、自制紧 密赛络纺纱 装置
集聚牵伸
70
60
50
40
30
20
10
0 1.03
1.05
1.08
集聚牵伸
(1) 紧密赛络纱特殊的成纱机理使其捻系数的取值不 同于普通纱的规定,纺制9.72×2tex的紧密赛络棉纱, 捻系数为360左右时,纱线基本性能指标最好。
(2)负压大小影响气流对纤维的集聚作用,吸风负压 太小,气流横向集聚力不能有效集聚纤维,负压一 般范围为1800Pa—2500Pa。
7.3×2/14.6
9.7×2/19.4 7.3×2/14.6
纱线细度/tex 80
70 60 50 40 30 20 10
0
条干不匀率CV/%
14.5×2/29
紧密赛 络纱 赛络纱 紧密纱 传统环 锭纱
紧密赛 络纱 赛络纱 紧密纱 传统环 锭纱
断裂伸长率/%
3-9mm毛羽/根·(10m)-1
7 6 5 4 3 2 1 0
式中: a1, a2, aZ为相对应的捻系数。
紧密赛络纱汇聚点示意图:
三、集聚区流场的研究
3.1、集聚区流场的理论研究
紧密塞络纺所研究的流体对象是较高压力下的气体, 所以必须按照空气动力学的原理来进行分析讨论。
异型管槽口附近形成负压,周围空气不断地被吸入, 该异型管槽口就是吸风口,当吸风口面积较小时, 可以认为是一个“点汇” , 即根据汇流理论 ,吸风 口内任意一点的空气流速和吸风口流速的比值与该 点离开吸风口的距离平方成反比。
(3)紧密塞络纺纱中设置附加张力牵伸既可以使纤维 进一步伸直,促进纤维有效集聚,减少纱线毛羽, 另外附加牵伸可以纺制高支纱。附加张力牵伸倍数 范围一般控制在1.050~1.065较好。
(二)纱线对比研究
加捻纱线的纵向结构分析(350倍)
紧密塞络纺棉纱
紧密纺棉纱
赛络纺棉纱
普通环锭纺棉纱
退捻后纱线的纵向结构(100倍)
5 4.8 4.6 4.4 4.2
1500
2100 2700
吸风负压/Pa
3-9mm毛羽数/根· (10m)-1
4.5 4
3.5 3
2.5 2
1.5 1
0.5 0 1500 2100 2700
吸风负压/Pa
条干CV值/%
12 11.8 11.6 11.4 11.2
11 10.8 1500
2100 2700 吸风负压/Pa
发表论文清单 :
1、杨丽丽,谢春萍等.紧密赛络纺纱技术在棉纺中的应用探讨. 《国际纺织导报》,2006,10
2、杨丽丽,谢春萍等.紧密塞络纺棉纱的结构及性能研究. 《纺织导报》,2006,12
3、杨丽丽,谢春萍等.捻系数对紧密赛络纺纱线性能的影响. 《上海纺织科技》,已录用
4、谢春萍,杨丽丽等.紧密赛络纺集聚效果及纱线结构分析. 《纺织学报》,已录用
470 460 450 440 430 420 410 400 390 380 370 360
310 335 360 385 410
捻系数
3-9mm毛羽数/根· (10m)-1
10 9 8 7 6 5 4 3 2 1 0 310 335 360 385 410
捻系数
条干CV值/%
10.8 10.7 10.6 10.5 10.4 10.3 10.2 10.1
3.2、集聚区流场的试验研究
本测试实验根据流体力学的基本原理,使 用美国TSI公司生产的8702型DP-CALC®风 压风速计,加装软管及探针,测量流场及 异型管内部风压及风速。集聚区风压由风 机提供,风压大小由变频器调解。
轴向风压分布规律
风压/Pa
风压/Pa
5000 4000 3000 2000 1000
紧密赛络纺成纱机理及 关键部件的研究
Research for the mechanism and key set of compact-siro spinning system
谢春萍 教授 学 院 : 纺织服装学院 日 期 : 二○○六年十二月
一、课题目的及意义
紧密赛络纺纱技术的优点引起了国内外生产厂家的 极大兴趣,但作为一种探索性的实验技术,国内外 的应用实例很少,目前还没有与此相关的技术方面 的详细报道,且国内尚未有成熟的具有我国知识产 权的紧密赛络纺技术出现。
集聚牵伸
6 5 4 3 2 1 0 1.03 1.04 1.05 1.065 1.08
集聚牵伸
条干CV值/%
11.6
11.5
11.4
11.3
11.2
11.1
11
10.9 1.03
1.05
1.08
集聚牵伸
1-2mm毛羽数/根·(10m)1
粗细节和棉结/个
400
350
300
250
200
150
100 1.03 1.04 1.05 1.065 1.08
五、国产细纱机上紧密赛络纺纺 纱实验
实验条件及工艺参数
纺纱条件:定量:4.25 g/10m精梳纯棉粗纱、EJM128K 细纱机 、捻向:Z 、锭盘直径:22mm、锭速: 12500(r/min)。
紧密塞络纺纱工艺参数:捻系数、吸风负压、集聚牵 伸
测试仪器:长岭纺电YG172A纱线毛羽测试仪、YG063全 自动单纱强力仪、YG135G条干仪,Union公司生产的 DZ3视频变焦显微镜。
紧密赛 络纱 赛络纱 紧密纱 传统环 锭纱
紧密赛 络纱 赛络纱 紧密纱 传环 锭纱
小结
自制紧密赛络纺纱装置结合了集聚与合股的 双重作用,可有效减小加捻三角区,成纱毛 羽明显减少,尤其是长毛羽可基本消除;纱 线的同向同步加捻,使其结构更加清晰紧密, 表面纤维排列整齐顺直,截面形状也更圆, 退捻后有明显的双股结构;成纱强伸性能和 条干得到了较好的改进。与普通环锭纺单纱、 赛络纱、紧密纱相比,紧密赛络纱突显其优 越性。
断裂强力/cN
集聚牵伸对纱线性能的影响