自动车床凸轮设计
自动车床凸轮设计教程

1.自动车床主要靠凸轮来控制加工过程,能否设计出一套好的凸轮,是体现自动车床师傅的技术高低的一个标准。
凸轮设计计算的资料不多,在此,我将一些基本的凸轮计算方法送给大家。
凸轮是由一组或多组螺旋线组成的,这是一种端面螺旋线,又称阿基米德螺线。
其形成的主要原理是:由A点作等速旋转运动,同时又使A点沿半径作等速移动,形成了一条复合运动轨迹的端面螺线。
这就是等速凸轮的曲线。
凸轮的计算有几个专用名称:1、上升曲线——凸轮上升的起点到最高点的弧线称为上升曲线2、下降曲线——凸轮下降的最高点到最低点的弧线称为下降曲线3、升角——从凸轮的上升起点到最高点的角度,即上升曲线的角度。
我们定个代号为φ。
4、降角——从凸轮的最高点到最低点的角度,即下降曲线的角度。
代号为φ1。
5、升距——凸轮上升曲线的最大半径与最小半径之差。
我们给定代号为h,单位是毫米。
6、降距——凸轮下降曲线的最大半径与最小半径之差。
代号为h1。
7、导程——即凸轮的曲线导程,就是假定凸轮曲线的升角(或降角)为360°时凸轮的升距(或降距)。
代号为L,单位是毫米。
8、常数——是凸轮计算的一个常数,它是通过计算得来的。
代号为K。
凸轮的升角与降角是给定的数值,根据加工零件尺寸计算得来的。
凸轮的常数等于凸轮的升距除以凸轮的升角,即K=h/φ。
由此得h=Kφ。
凸轮的导程等于360°乘以常数,即L=360°K。
由此得L=360°h/φ。
举个例子:一个凸轮曲线的升距为10毫米,升角为180°,求凸轮的曲线导程。
(见下图) 解:L=360°h/φ=360°×10÷180°=20毫米升角(或降角)是360°的凸轮,其升距(或降距)即等于导程。
这只是一般的凸轮基本计算方法,比较简单,而自动车床上的凸轮,有些比较简单,有些则比较复杂。
在实际运用中,许多人只是靠经验来设计,用手工制作,不需要计算,而要用机床加工凸轮,特别是用数控机床加工凸轮,却是需要先计算出凸轮的导程,才能进行电脑程序设计。
产品机构-棘轮-槽轮-凸轮等机构工作原理汇总
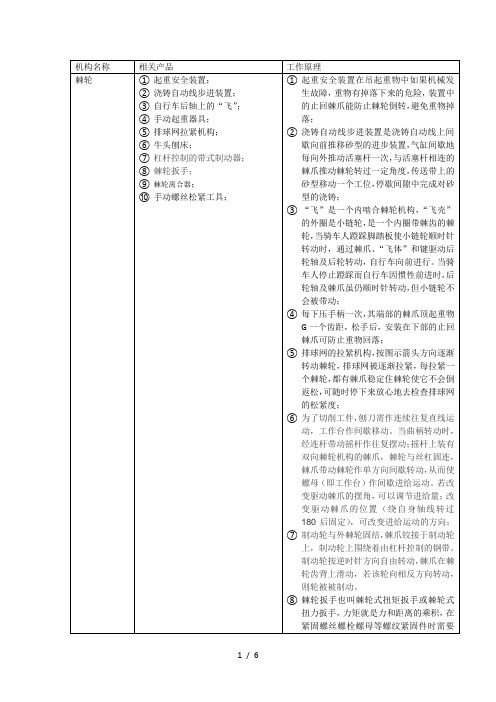
3“飞”是一个内啮合棘轮机构,“飞壳”的外圈是小链轮,是一个内圈带棘齿的棘轮,当骑车人蹬踩脚踏板使小链轮顺时针转动时,通过棘爪、“飞体”和键驱动后轮轴及后轮转动,自行车向前进行。当骑车人停止蹬踩而自行车因惯性前进时,后轮轴及棘爪虽仍顺时针转动,但小链轮不会被带动;
5蜂窝煤机冲压部分主要有四根滑杆、滑梁、冲杆、冲杆座、冲头、活动压盘、活动模底、弹簧构成。当蜂窝煤机动转由两齿轮转动通过拉杆带动滑梁,冲头下行时,迫使冲头下移,活动盘上移弹簧紧缩,把煤压成型并把煤冲成,成型煤的松实,由弹簧压紧活动压盘,把煤压紧所决定。
6启动电源,下料机电机得电驱动主动带轮1转动,通过V带传动使从动带轮2与同轴蜗杆3同步转动,由蜗杆3和蜗轮4组成的减速机构对输出轴O1―O1实现减速。接着工作机构分两路传动实现定长送料和剪切下料;
2气缸盖中有进气道和排气道,内装进、排气门。新鲜充量(即空气或空气与燃料的可燃混合气)经空气滤清器、进气管、进气道和进气门充入气缸。膨胀后的燃气经排气门、排气道和排气管,最后经排气消声器排入大气。进、排气门的开启和关闭是由凸轮轴上的进、排气凸轮,通过挺柱、推杆、摇臂和气门弹簧等传动件分别加以控制的,这一套机件称为内燃机配气机构。通常由空气滤清器、进气管、排气管和排气消声器组成进排气系统。为了向气缸内供入燃料,内燃机均设有供油系统。汽油机通过安装在进气管入口端的化油器将空气与汽油按一定比例(空燃比)混合,然后经进气管供入气缸,由汽油机点火系统控制的电火花定时点燃。柴油机的燃油则通过柴油机喷油系统喷入燃烧室,在高温高压下自行着火燃烧。
自动车床凸轮设计详解
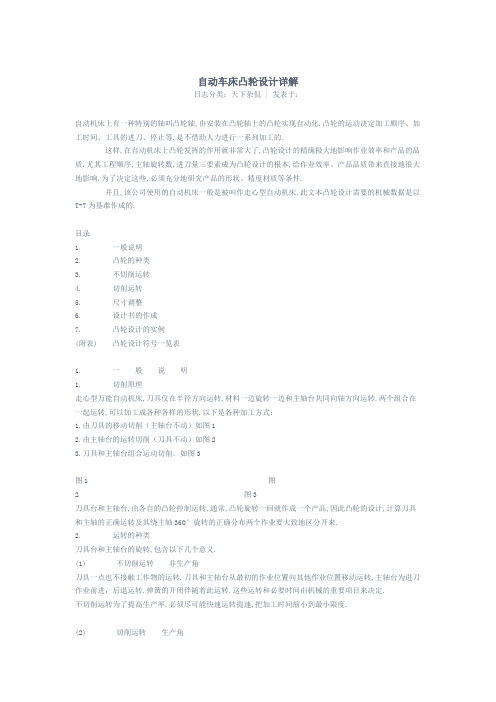
自动车床凸轮设计详解日志分类:天下杂侃 | 发表于:自动机床上有一种特别的轴叫凸轮轴,由安装在凸轮轴上的凸轮实现自动化.凸轮的运动决定加工顺序、加工时间、工具的进刀、停止等,是不借助人力进行一系列加工的.这样,在自动机床上凸轮发挥的作用就非常大了,凸轮设计的精确极大地影响作业效率和产品的品质.尤其工程顺序,主轴旋转数,进刀量三要素成为凸轮设计的根本,给作业效率、产品品质带来直接地很大地影响.为了决定这些,必须充分地研究产品的形状、精度材质等条件.并且,该公司使用的自动机床一般是被叫作走心型自动机床.此文本凸轮设计需要的机械数据是以T-7为基准作成的.目录1. 一般说明2. 凸轮的种类3. 不切削运转4. 切削运转5. 尺寸调整6. 设计书的作成7. 凸轮设计的实例(附表) 凸轮设计符号一览表1. 一般说明1. 切削原理走心型万能自动机床,刀具仅在半径方向运转,材料一边旋转一边和主轴台共同向轴方向运转.两个组合在一起运转,可以加工成各种各样的形状.以下是各种加工方式:1.由刀具的移动切削(主轴台不动)如图12.由主轴台的运转切削(刀具不动)如图23.刀具和主轴台组合运动切削。
如图3图1 图2 图3刀具台和主轴台,由各自的凸轮控制运转,通常,凸轮旋转一回就作成一个产品,因此凸轮的设计,计算刀具和主轴的正确运转及其绕主轴360°旋转的正确分布两个作业要大致地区分开来.2. 运转的种类刀具台和主轴台的旋转,包含以下几个意义.(1) 不切削运转非生产角刀具一点也不接触工作物的运转.刀具和主轴台从最初的作业位置向其他作业位置移动运转,主轴台为进刀作业前进,后退运转.弹簧的开闭伴随着此运转.这些运转和必要时间由机械的重要项目来决定.不切削运转为了提高生产率,必须尽可能快速运转提速,把加工时间缩小到最小限度.(2) 切削运转生产角是由一个或两个以上的刀具进行加工的运转.这跟工作物的材质,精加工精度,切削面粗糙度,使用刀具的材质等有直接联系.3. 主轴台的运转HS凸轮主轴台的前进是从板凸轮主轴推动进行,后退由一根弹簧进行.对于主轴台的运转,凸轮的设计可以从1∶1到1∶3的任意值来设定.为了减少不切削运转的时间,选择1∶1更好,但是短的产品和要求特别高精度的部品则选定1∶2或者1∶3.高级精密的设计根据产品选1∶2的多.该公司通常使用1∶2.4. 刀具台的运转(1) 刀番号标准刀具台有5个如图4称为1号刀具台,..5号刀具台.(2) 天平刀架1号刀具台和2号刀具台安装在摆动杆上.此刀具的运转是凸轮运转高度的1/3,构造方面也比其他刀具台好,所以主要用于精度较高的重要部分的精加工切削.并且凸轮的上升有使2号刀具台前进切入,同时使1号刀具台后退的作用.凸轮的下降有与其相反的效果.因此除了主轴台以及1号刀具台的其他所有的刀具台随凸轮上升而前进,(随凸轮)下降而后退.但是,只有1号刀具台与此相反,1号刀具台前进凸轮下降,1号刀具台后退凸轮上升.这是在凸轮设计中必须要注意的事项.(3) VT刀架刀具台3,4,5号刀具台能够由各自的凸轮单独前进、后退运转.这些VT刀架刀具台主要用于粗加工,倒角,突切等作业,必要的话也可以用于精加工切削.3号刀具台的杆比为1∶1(刀具和凸轮的运转相同),4,5号刀具台则变成1∶2(刀具的运转是凸轮运转的1/2),根据情况调整杆比稍微变更也是可以的.附件的杆比,除了特别的部品外一般为1∶1.主轴台HS 1:1~1:3天平刀架NO。
自动车床凸轮设计辅助工具
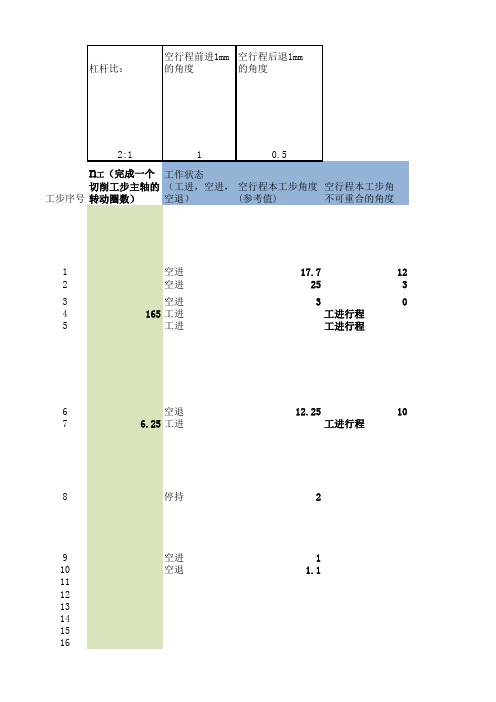
8
停持
9
空进
10
空退
11
12
13
14
15
16
12.25
10
工进行程
2
1 1.1
17 18 19 20 21 22 23 24 25 26 27 28 29 30 31 32 33 34 35 36 37
Σn工
空行程 本工位角 之和 重复的角
度
171.25 62.05
位移 角度 生成位移角度曲 线,带入UG或者 SW的表达式来驱 动曲线模型
凸轮内孔 为22mm公 差为 +0.05、 -0mm
切削速度
(m/min 材料直径 主轴转速
)
(mm) RPM
60
圈数 600
7
生产效率 (个/分
5
2730
工进
空进
每个切削
动作完成
后,停持
2°角
度,且视
为空行程
角度
空退
停持
实际待加 提前量 实际位移 工尺寸 (0.2~0.5) 切断刀
其他
被加工部位走刀量 间隙 (查表可得)
17.7 25
3 3.3
0
15.0 25.0
1.5 2.8
0.2
2.0
0.5
0.5
0.1000
0.0200
1.0
0.0400
0.5
杠杆比:
空行程前进1mm 空行程后退1mm
的角度
的角度
2:1
1
0.5
n工(完成一个 工作状态
切削工步主轴的 (工进,空进, 空行程本工步角度 空行程本工步角
工步序号 转动圈数) 空退)
凸轮机构
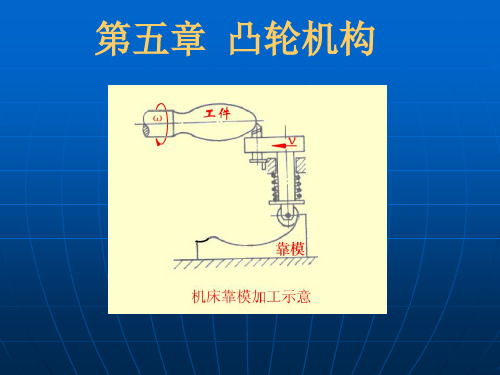
B6
4. 偏心尖顶直动从动件盘形凸轮轮廓曲线的设计
第四节凸轮机构基本尺寸的确定
凸轮工作轮廓必须满足以下要求: (1)保证从动件能实现预定的运动规律
(2)传力性能良好,不能自锁
(3)结构紧凑
(4)满足强度和安装等要求 为此,设计时应注意处理好
1.滚子半径的选择 2.凸轮机构的压力角 3.凸轮基圆半径的确定 4.凸轮机构的材料
(a)推程 (b)回程
2.等加速等减速运动规律
是指凸轮以等角速度转动时,从动件在一个行程中,前半行程作 等加速运动,后半行程作等减速运动的运动规律。 运动线图如图所示。其位移曲线为两段光滑相连开口相反的抛物 线,速度曲线为斜直线,加速度曲线为平直线。推程位移线图作图 方法演示。
由图可见,在推(回) 程的始末点和前、后半程 的交接处,加速度有限的 突变,因而惯性力也产生 有限的突变,由此将对机 构造成有限大小的冲击, 这种冲击称为“柔性冲击” 或“软冲”。因此这种运 动规律只适用于中速、中 载的场合。
3.按锁合方式分:力锁合、形锁合
锁合是指从动件与凸轮之间始终保持的高副接触的装置。
(1)力锁合凸轮机构
依靠重力、弹 力或其他外力 来锁合
(2)形锁合凸轮机构
依靠凸轮和从 动件几何形状 来保证锁合
4.按从动件运动方式分:
从动件导路是否通过凸轮回转中心
对心直动从动件凸轮机构 偏置移动从动件凸轮机构
直动从动件凸轮机构 摆动从动件凸轮机构
rT<0.8ρmin ρmin>1~5mm rT =(0.1~0.5)rb
二、凸轮机构的压力角
1.压力角:不计摩擦时,凸轮对从 动件的作用力(法向力)与从动件 上受力点速度方向所夹的锐角。 该力可分解为两个分力 :
第三章 凸轮机构介绍

凸轮传动是通过凸轮与从动件间的接触来传递运动和动力,是一种 常见的高副机构,结构简单,只要设计出适当的凸轮轮廓曲线,就 可以使从动件实现任何预定的复杂运动规律。 §3-1 凸轮机构应用和分类 一、凸轮机构的组成和应用
内燃机
配气机构
凸轮式内燃机配气机构
自动车床上的走刀机构 1、组成:凸轮,从动件,机架 2、作用:将凸轮的转动或移动转变为从动件的移动或摆动 3、特点:(1)只需设计适当的凸轮轮廓,便可使从动件得到所需的 运动规律 (1)结构简单、紧凑,工作可靠,容易设计; (2)高副接触,易磨损 4、应用:适用于传力不大的控制机构和调节机构
推杆运动规律选取应从便于加工和动力特性来考虑。
低速轻载凸轮机构:采用圆弧、直线等易于加工的曲线作为凸 轮轮廓曲线。
高速凸轮机构:首先考虑动力特性,以避免产生过大的冲击。
大质量从动件不宜选用νmax太大的运动规律 高速度从动件不宜选用amax太大的运动规律
(2)机器工作过程对从动件的的运动规律有特殊要求
4、偏臵直动尖顶从动件盘形凸轮机构 已知条件:已知凸轮的基圆半径为r0,凸轮沿逆时针方向等速回转。 从动画中看,从动件 而推杆的运动规律已知,已知偏距e。试设计。
在反转运动中依次占 据的位臵将不在是以 凸轮回转中心作出的 径向线,而是始终与O 保持一偏距e的直线, 因此若以凸轮回转中 心O为圆心,以偏距e 为半径作圆(称为偏 距圆),则从动件在 反转运动中依次占据 的位臵必然都是偏距 圆的切线,(图 中 …)从 动件的位移 ( …) 也应沿切线量取。然 后将 …等点 用光滑的曲线连接起 来,既得偏臵直动尖 顶从动件盘形凸轮轮
按从动件运动形式 可分为直动从动件(又分为对心直动从动件和偏臵直动从动件) 和摆动从动件两种。
自动车床凸轮设计教程

1.自动车床主要靠凸轮来控制加工过程,能否设计出一套好的凸轮,是体现自动车床师傅的技术高低的一个标准。
凸轮设计计算的资料不多,在此,我将一些基本的凸轮计算方法送给大家。
凸轮是由一组或多组螺旋线组成的,这是一种端面螺旋线,又称阿基米德螺线。
其形成的主要原理是:由A点作等速旋转运动,同时又使A点沿半径作等速移动,形成了一条复合运动轨迹的端面螺线。
这就是等速凸轮的曲线。
凸轮的计算有几个专用名称:1、上升曲线——凸轮上升的起点到最高点的弧线称为上升曲线2、下降曲线——凸轮下降的最高点到最低点的弧线称为下降曲线3、升角——从凸轮的上升起点到最高点的角度,即上升曲线的角度。
我们定个代号为φ。
4、降角——从凸轮的最高点到最低点的角度,即下降曲线的角度。
代号为φ1。
5、升距——凸轮上升曲线的最大半径与最小半径之差。
我们给定代号为h,单位是毫米。
6、降距——凸轮下降曲线的最大半径与最小半径之差。
代号为h1。
7、导程——即凸轮的曲线导程,就是假定凸轮曲线的升角(或降角)为360°时凸轮的升距(或降距)。
代号为L,单位是毫米。
8、常数——是凸轮计算的一个常数,它是通过计算得来的。
代号为K。
凸轮的升角与降角是给定的数值,根据加工零件尺寸计算得来的。
凸轮的常数等于凸轮的升距除以凸轮的升角,即K=h/φ。
由此得h=Kφ。
凸轮的导程等于360°乘以常数,即L=360°K。
由此得L=360°h/φ。
举个例子:一个凸轮曲线的升距为10毫米,升角为180°,求凸轮的曲线导程。
(见下图) -解:L=360°h/φ=360°×10÷180°=20毫米升角(或降角)是360°的凸轮,其升距(或降距)即等于导程。
这只是一般的凸轮基本计算方法,比较简单,而自动车床上的凸轮,有些比较简单,有些则比较复杂。
在实际运用中,许多人只是靠经验来设计,用手工制作,不需要计算,而要用机床加工凸轮,特别是用数控机床加工凸轮,却是需要先计算出凸轮的导程,才能进行电脑程序设计。
机械设计基础 第四章

(1) 盘形凸轮机构
盘形凸轮机构是最常见的凸轮机构, 其机构中的凸轮是绕固定轴线转动并具 有变化向径的盘形零件,如图4-2所示。
图4-2 内燃机配气机构
(2) 移动凸轮机构
当盘形凸轮的 回转中心趋于无穷 远时,凸轮不再转 动,而是相对于机 架作直线往复运动, 这种凸轮机构称为 移动凸轮机构(参见 图4-4)。
用光滑的曲线连接这些点便得到推程等加速段的位移线图,等
减速段的位移线图可用同样的方法求得。
等加速、等减速运动规律的位移、速度、加速度线图如图 4-10所示。由图4-10(c) 可知,等加速、等减速运动规律在运动 起点O、中点A 和终点B 的加速度突变为有限值,从动件会产生 柔性冲击,适用于中速场合。
4.3 盘形凸轮轮廓的绘制
凸轮轮廓的设计方法有作图法和解析法两种。其中,作图 法直观、方便,精确度较低,但一般能满足机械的要求;解析 法精确高,计算工作量大。本节主要介绍作图法。
4.3.1 凸轮轮廓曲线设计的基本原理
凸轮机构工作时,凸轮是运动的,而绘在图纸上的凸轮是静 止的。因此,绘制凸轮轮廓时可采用反转法。
s
2h
2 0
2
(4-2)
等加速、等减速运动规律的位移线图的画法为:
将推程角
0 两等分,每等分为
0 2
;
将行程两等分,每等分 h ,将 0 若干等分,
2
2
得点1、2、3、…,过这些点作横坐标的垂线。
将 h 分成相同的等分,得点1′、2′、3′、…,连01′、02′、
2
03′、…与相应的横坐标的垂线分别相交于点1″、2″、3″、…,
图4-5 平底从动件
3. 按从动件与凸轮保持接触的方式分
(1) 力锁合的凸轮机构
- 1、下载文档前请自行甄别文档内容的完整性,平台不提供额外的编辑、内容补充、找答案等附加服务。
- 2、"仅部分预览"的文档,不可在线预览部分如存在完整性等问题,可反馈申请退款(可完整预览的文档不适用该条件!)。
- 3、如文档侵犯您的权益,请联系客服反馈,我们会尽快为您处理(人工客服工作时间:9:00-18:30)。
自动车床主要靠凸轮来控制加工过程,能否设计出一套好的凸轮,是体现自动车床师傅的技术高低的一个标准。
凸轮设计计算的资料不多,在此,我将一些基本的凸轮计算方法送给大家。
凸轮是由一组或多组螺旋线组成的,这是一种端面螺旋线,又称阿基米德螺线。
其形成的主要原理是:由A点作等速旋转运动,同时又使A点沿半径作等速移动,形成了一条复合运动轨迹的端面螺线。
这就是等速凸轮的曲线。
凸轮的计算有几个专用名称:1、上升曲线——凸轮上升的起点到最高点的弧线称为上升曲线2、下降曲线——凸轮下降的最高点到最低点的弧线称为下降曲线3、升角——从凸轮的上升起点到最高点的角度,即上升曲线的角度。
我们定个代号为φ。
4、降角——从凸轮的最高点到最低点的角度,即下降曲线的角度。
代号为φ1。
5、升距——凸轮上升曲线的最大半径与最小半径之差。
我们给定代号为h,单位是毫米。
6、降距——凸轮下降曲线的最大半径与最小半径之差。
代号为h1。
7、导程——即凸轮的曲线导程,就是假定凸轮曲线的升角(或降角)为360°时凸轮的升距(或降距)。
代号为L,单位是毫米。
8、常数——是凸轮计算的一个常数,它是通过计算得来的。
代号为K。
凸轮的升角与降角是给定的数值,根据加工零件尺寸计算得来的。
凸轮的常数等于凸轮的升距除以凸轮的升角,即K=h/φ。
由此得h=Kφ。
凸轮的导程等于360°乘以常数,即L=360°K。
由此得L=360°h/φ。
举个例子:一个凸轮曲线的升距为10毫米,升角为180°,求凸轮的曲线导程。
(见下图) 解:L=360°h/φ=360°×10÷180°=20毫米升角(或降角)是360°的凸轮,其升距(或降距)即等于导程。
这只是一般的凸轮基本计算方法,比较简单,而自动车床上的凸轮,有些比较简单,有些则比较复杂。
在实际运用中,许多人只是靠经验来设计,用手工制作,不需要计算,而要用机床加工凸轮,特别是用数控机床加工凸轮,却是需要先计算出凸轮的导程,才能进行电脑程序设计。
要设计凸轮有几点在开始前就要了解的.在我们拿到产品图纸的时候,看好材料,根据材料大小和材质将这款产品的主轴转速先计算出来.计算主轴转速公式是[切削速度乘1000]除以材料直径.切削速度是根据材质得来的,在购买材料时供应商提供.单位是米/分钟.材料硬度越大,切削速度就越小,切的太快的话热量太大会导致材料变形, 所以切削速度已知的.切削速度乘1000就是把米/分钟换算成毫米/分钟,在除以材料直径就是主轴每分钟的转速了.材料直径是每转的长度,切削速度是刀尖每分钟可以移动的距离.主轴转速求出来了,就要将一个产品需要多少转可以做出来,这个转的圈数求出来.主轴转速除以每个产品需要的圈数就是生产效率.[单位.个/分钟]每款不同的产品,我们看到图纸的时候就先要将它的加工工艺给确定下来.加工工艺其实就是加工方法,走芯机5把刀具怎么安排,怎么加工,哪把刀具先做,按顺序将它安排,这样就是确定加工工艺.确定加工工艺的时候有几点应该注意的地方.一. 2把相邻的刀具最好不安排在一前一后顺序加工,应该错开刀具安排,这样就容易避免刀具相撞.二. 确定一条基准线,一般以切断刀的靠近中心架夹头的那个面为基准.其余的4把刀具在靠近基准面时留有一点距离.后面会有例子.三. 尽量不要安排2把刀同时加工,以免互相干扰,出现不稳定情况.当然也有些例外的,比如2把倒角一起加工有时候是可以的.四. 合理的安排刀具,在刀具够用的时候倒角可以用成型刀最好.区分好行程和空行程的步骤.行程就是刀具在加工的时候;空行程则是刀具在未加工的时候.我们在这开始讲空行程的角度计算方法:1. 凸轮开关夹,夹头弹开的时候的角度是10度,夹紧角度是15度.2. 根据算得的生产效率来确定凸轮上升下降的空行程所要乘的比例系数.当生产效率小于或者等于3的时候,凸轮上升角度比例系数是1比1,也就是凸轮每上升1毫米,角度为1度.凸轮下降角度比例系数是1比0.7,也就是凸轮每下降1毫米,角度为0.7度.当生产效率小于等于8大于3的时候,凸轮上升角度比例系数是1比1.5,也就是凸轮每上升1毫米,角度为1.5度.凸轮下降角度比例系数是1比1,也就是凸轮每下降1毫米,角度为1度.当生产效率小于等于14大于8的时候,凸轮上升角度比例系数是1比2,也就是凸轮每上升1毫米,角度为2度.凸轮下降角度比例系数是1比1.3,也就是凸轮每下降1毫米,角度为1.3度.当生产效率大于14的时候,凸轮上升角度比例系数是1比2.5,也就是凸轮每上升1毫米,角度为2.5度.凸轮下降角度比例系数是1比1.7,也就是凸轮每下降1毫米,角度为1.7度.生产效率实际指的就是凸轮轴每分钟转的圈数,而不是产品每分钟做的个数,因为产品简单的时候我们设计的时候甚至可以每圈做2,3个产品,可能更多.空行程说清楚了也就是这两个要点.凸轮空行程的凸轮上升下降角度可以根据第2点全计算出来.由于纵切自动车床一般都具有五个刀架和附件装置,因此它的加工工艺范围比较广,许多复杂的轴类零件也可以用这种机床一次加工完成。
在纵切单轴自动车床上可以进行下列一些工作:车圆柱面、车倒角、车锥面、沉割加工、切断、车圆弧、打中心孔、钻孔、绞孔、镗孔、功内外螺纹、冲方孔等等其他工作。
前面我们讲完了空行程的计算方法,这里讲行程的计算方法.凸轮设计里面除了行程剩下的全是空行程.在这也可以反过来用.行程里面刀具加工的方法很多:1. 左车外径2. 右车外径3. 成型刀倒角,圆弧,插槽等等4. 切断(1) 平面切断(2) 圆弧切断(3) 斜面切断(4) 切断面往里面凹进去,也可以是产品后面打中心孔5. 打中心孔(钩刀钩平底孔)6. 根据凸轮和刀具配合移动走倒角,或者走圆弧7. 沉割刀具清理外径根部圆角或者批锋8. 钻孔9. 功牙,套牙10 冲方孔(孔是正多边型的)自动车床,以其无可替代的加工手段的优势,正在为越来越多的厂家所青睐。
而自动车床使用的凸轮的设计,则成为使用此类机床的厂家所必须要掌握的一门技术。
自动车床凸轮的设计,即编写凸轮调整卡,对于不了解其本来面貌的人来讲,神秘、深奥;当对它有了稍微粗浅了解的人,又会觉得不过如此而已,稍学即会。
其实,此项技术和其他任何门类的技术一样,“会易精难”。
依据机床说明书的提示来编写完成的凸轮设计调整卡,不一定是好的设计作品。
一个优秀的设计作品,包括以下内容:一,合理的工步编排。
二,合理的设定走刀量。
三,能得出较高的生产率。
此外,还应在制造凸轮、调整机床时易于操作。
也可以这样说,要想作出一件比较优秀的设计作品,前提是能够深刻体味各个设计步骤的实质性的意义。
只有这样才能做到,你的设计作品与机床说明书中提示的方法相比较,不只是形似,而是神似,甚至比其更优秀。
考核一个设计作品的优劣,最重要的标准是其最后得出的生产率的高低;生产率的高低,取决于工作角度总和的大小;而工作角度总和的大小,则取决于工步编排得是否合理。
由此看来,合理的编排工步,在整个设计过程中,具有着相当重要的作用。
要想做好工步编排,一是要有相当时间的工作经验的积累;二是要有丰富的想象力,这一点尤其重要。
一、生产率的计算方法与作用作为投资人,都希望在尽可能短的时间内,得到尽可能高的效益;作为生产过程的组织者,都希望机床能生产数量和品种都尽可能多的产品,以缓解交货期代来的时间压力;作为操作工,都希望机床能够优质高产,以获得较高的收入。
所以说,希望优质高产是所有与机床有关联的人的共同愿望。
那麽,现在就分析一下下面的这个公式,就可以知道机床的生产率究竟是怎样形成的了。
N 不难看出,这是一个多元一次分式方程式。
在这一公式里,A=————————函括了整个设计过程的全部计算内容。
Σn工÷Σa工×360°式中:A=生产率单位=件/分N=主轴转数单位=转/分n工=某切削工步工作时的主轴转数α工=某切削工步工作时占用的角度∑:希腊字母。
表示在计算过程中某项数值的累计总和。
首先,介绍几个在设计中使用的专用名词:工步——生产过程中每一个动作称做一个工步。
切削时主轴转数——完成某一切削工步时主轴转过的圈数。
工作角度——完成某一切削工步时所占用的角度。
在“车”加工中,无论使用的是哪种类型车床,在切削前都要先确定:①主轴转数。
②每次进刀多少毫米(进刀深度)。
③走刀时的速度(走刀量)。
这就是平常所说的“切削三要素”。
自动车加工时的主轴转数,是由被加工材料的种类和直径决定的。
例:切削直径10毫米A3棒料时(此钢种属低碳钢),根据说明书中切削速度表给出的数值,是60m/分。
即:60×1000/(10×3.1416)≈1910(转)据此,就可确定机床最接近此数值的主轴转数。
准确的选择主轴转数,是保持零件加工时工艺尺寸稳定的关键,这一点往往容易被忽略。
如果主轴转数过快,直接影响刀具的使用寿命;而主轴转数过慢,又会因切削速度不够而造成加工的零件工艺尺寸不稳定、光洁度不高等等缺陷。
其他类型的车床,在加工零件时,一般是一次加工一个零件,每个部位可能会分若干次进刀,当尺寸发生变化时可随时采取措施。
自动车床就不同了,它一经启动,零件就会不断产出。
主轴转数设定的准确与否,直接影响的就是、生产效率。
也可以这样讲,当我们确定了所要生产的产品,也就同时确定了主轴转数。
综上所述,我们在进行凸轮设计时,可以把主轴转数N当作一个常量来设定;无疑,(Σn工/Σα工)×360°是一个变量。
N设:(Σn工/Σα工)×360°=W。
公式则可成为为: A= ——W根据数学的计算法则,A的值与W的值成反比。
只有W的值尽可能的小,A的值才能尽可能的大。
那么,怎样才能使W即(Σn工/Σα工)×360°的值尽可能的小呢?二、设计公式的分析与使用在一篇凸轮设计调整卡中,工步编排得是否完美,直接影响着(Σn工÷Σα工)×360°值的大小。
也就是说,(Σn工÷Σα工)×360°的值,是编排完工步后计算的结果。
前面提到,作好工步编排,既需要相应的工作经验,更需要丰富的想象力。
这一点,充分体显在凸轮设计开始前,对每把刀所要加工的部位的设定上。
合理的使用每一把刀,是使一件设计作品尽可能完美的前提。
本文后面有几篇范例,都是经工作实践检验证明是较为成功的作品,读者可作为设计时的参考。
下面只从计算的角度分析一下:怎样才能使(Σn工÷Σα工)×360°的值尽可能的小。
Σn工公式:Σn工÷Σα工×360° = W 即:—————×360° = WΣα工公式中①Σn工——累计切削工步主轴转数的总和。