浅析高硫原油对炼油设备的腐蚀与防护
加工含硫原油的设备腐蚀问题与对策

加工含硫原油的设备腐蚀问题与对策*摘要综述了加工含硫原油对设备的腐蚀问题和应采取的对策。
认为应提高原料油和产品的脱硫能力,和做好工艺防腐及设备的选材工作。
关键词含硫原油性质腐蚀与防护世界原油的硫含量在不断升高,目前硫含量在1%以上的原油占世界原油总产量的55%以上。
据预测原油平均相对密度将上升到 3 g/cm3,硫含量将上升到%。
2001年中国石油化工集团公司下发了《加工高含硫原油安全管理规定》,明确含硫量在1%以上的原油为高含硫原油。
随着我国沿海炼油厂加工含硫原油规模的不断扩大和我国环保要求的不断提高,加工含硫原油所面临的问题也越来越多。
含硫原油有两个比较突出的特点,一是硫含量高,如伊朗拉万原油的硫含量达%,其大于500℃的减压渣油硫含量高达%;二是轻馏分多,蜡油收率较高,如沙特拜里原油小于180℃轻馏分质量收率达%,而我国胜利原油小于180℃轻馏分质量收率只有%(几乎不含C3和C4)。
因此加工含硫原油带来了加工工艺的改动、设备的腐蚀与防护,以及环境保护等问题。
1 含硫原油的主要性质含硫原油主要来自中东,如沙特、伊朗、伊拉克、阿联酋、科威特、阿曼等国家,其主要性质见表1。
从中可见,含硫原油与中国胜利原油相比,轻馏分都较多,密度、粘度、酸值、胶质、凝点和闪点都较低,钒含量则普遍较高,各段馏分的硫含量都较高。
表1 含硫原油的主要性质原油种类伊朗拉万沙特轻质伊朗重质伊朗轻质沙特拜里加蓬曼吉美国北坡阿曼阿联酋穆尔班中国胜利评价日期1997-08-06 1995-03-061997-03-051995-08-271995-12-231997-06-231998-07-271997-07-171993-06-031998-05-20含量,% 0密度/()凝点/℃-22 <-30 <-30 -16 <-30 -15 <-30 <-30 -7 15 开口闪点<28 <21 <21 28 <18 <28 47 <25 <29 57●/℃50℃粘度/()酸值(KOH)/()残碳,%盐含量/()蜡含量,%硅胶胶4 质, %沥青质,%镍含量(×10-6)钒含量(×10-6)HK-180℃收率,%180~260℃收率,%260~360℃收率,%360~500℃收率,%>500℃收率,%汽油含硫,%煤油含硫,%柴油含硫,%蜡油含硫,%减渣含硫,%注:均油轮采样。
加工高硫原油的腐蚀机理及预防措施
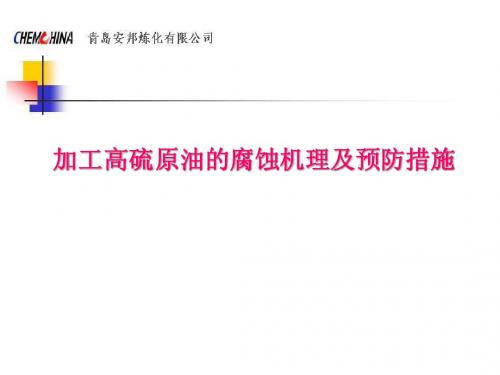
一、高硫原油的划分 根据硫含量分类: 根据硫含量分类: 1、硫含量低于0.5%称为低硫原油。 、硫含量低于 称为低硫原油。 称为低硫原油 2、硫含量0.5%-1.5%称为含硫原油。 、硫含量 称为含硫原油。 称为含硫原油 3、硫含量大于1.5%称为高硫原油。 、硫含量大于 称为高硫原油。 称为高硫原油 二、原油中含硫化合物的类型及重要的含硫化合物 原油中含硫化合物按性质划分时,可分为两大类: 原油中含硫化合物按性质划分时,可分为两大类:活性硫化物和 非活性硫化物 、活性硫化物 、 在活性硫化物中,主要包括元素硫、硫化氢、硫醇等, 在活性硫化物中,主要包括元素硫、硫化氢、硫醇等,它们共同 的特点是对炼油设备有较强的腐蚀作用。此外, 的特点是对炼油设备有较强的腐蚀作用。此外,硫醇还有令人厌恶的 臭味。 臭味。
原油 名称 硫含量% 胜利原油 伊朗轻质 1 1.35 硫含量% 0.008 0.06 硫分布% 0.02 0.6 硫含量% 0.343 1.18 硫分布% 6 15 硫含量% 0.68 1.62 硫分布% 17.9 16.9 硫含量% 1.54 3.0 硫分布% 76 65.4 汽油 柴油 减压馏分油 减压渣油
2、非活性硫化物 、 在非活性硫化物中,主要包括硫醚、噻吩、二硫化物等,它们的共 在非活性硫化物中,主要包括硫醚、噻吩、二硫化物等, 同特点是对炼油设备无明显腐蚀作用,因此称为非活性硫化物。 同特点是对炼油设备无明显腐蚀作用,因此称为非活性硫化物。值得注 意的是这些非活性硫化物热稳定性差, 意的是这些非活性硫化物热稳定性差,容易在热加工过程中受到不同程 度的破坏,并转化成其他类型的硫化物。 度的破坏,并转化成其他类型的硫化物。 三、原油及其馏分的硫含量和硫分布 原油中的硫含量变化范围为0.05%-14%,但大部分原油的硫含量都 , 原油中的硫含量变化范围为 低于4%,硫分布在原油所有馏分中。石脑油的硫含量最低, 低于 ,硫分布在原油所有馏分中。石脑油的硫含量最低,随着沸点的 增加,石油馏分的硫含量呈倍数递增的趋势,而随着相对分子量的增大, 增加,石油馏分的硫含量呈倍数递增的趋势,而随着相对分子量的增大, 石油馏分每个分子中硫原子的平均数随着沸点的升高而迅速增大。 石油馏分每个分子中硫原子的平均数随着沸点的升高而迅速增大。
加工高氯原油对炼油设备的腐蚀与防护

2 0 1 3年 5月下旬 以来 , 由于 胜利 管 输原 油有
原油 正 常 情 况 下 有 机 氯 质 量 浓 度 小 于 2 . 0
机氯含量大幅升高 , 造成炼油企业部分装置 降量
或 停工 , 加 大 了全 厂 油品加 工的调度 难度 , 影 响生
●
、 _ 一
^ 、
化铵) 堵塞 、 腐蚀 泄 漏 等 , 尤 其 是 氯 化 物对 不 锈 钢
材 质 的设备 易造 成应 力开 裂 。 目前 暂未 找到 更有 效 的脱 氯办 法 , 而 且 高含 有 机 氯 原 油加 工 对 生 产 和设备 的潜 在影 响仍 将延 续 。
琶
暑
=、
●
F i g . 2 Di s t r i b u t i o n f o r t h e d i s t i l l a t e s o f o r g a n o e h l o r i n e i n c r u d e o i l
总氯; —— 初馏~ 2 0 4  ̄ C ; 一
时间 月一 日)
图 2 原 油 有 机 氯 的 馏 分 分 布
1 高 含氯原 油特 点及 对生 产影 响 1 . 1 高 含氯 原油 分布 特点 2 0 1 3年 5月 下 旬 开 始 , 山东 、 华北、 沿江 l 0 家 炼油 企业 先后 发现 胜利 管输 原油 有机 氯含 量大 幅升高 , 质量 浓度 经 常大 于 1 0 mg / L ( 见图 1 ) 。
产任务的完成 , 而且高氯原油的加工对设备腐蚀
成 为影 响装 置长 周期 运行 潜在 安全 隐患 。受 加工 高氯原 油影 响 的主要 装置 为 常减压 、 催化 裂化 、 焦 化 装置 分馏 塔顶 以及 催 化 重 整 、 加 氢 装 置反 应 器 后 换热 器 和 空 冷 系 统 , 主要 问题 表 现 为 结 盐 ( 氯
高含硫原油储罐的腐蚀及防护
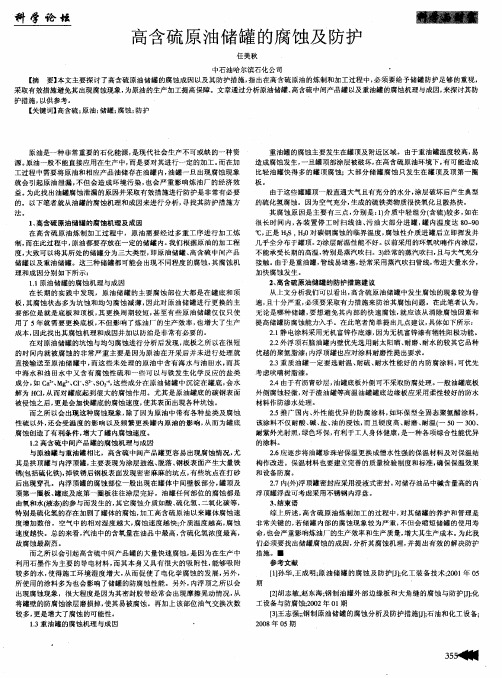
℃, 正是 H 2 s, H 对碳钢腐蚀 的临界温度 , 腐蚀性介质进罐后 立即挥发并 几乎全分布于罐顶。 2 ) 涂 层耐温性 能不好 。以前采用的环氧 吠喃作 内涂层,
不 能 承 受 长 期 的高 温 , 特 别 是 蒸 汽 吹 扫 。3 1 经常的蒸汽吹扫, 且与 大 气 充 分
接触 。由于是重油罐 , 管 线易堵塞 , 经常采用蒸汽吹扫管线, 带进大量水分, 加快 腐 蚀 发 生 。 2 、 高含硫原油储罐的防护措施建议 从上文分析我们可 以看 出, 高含硫原油储罐中发生腐蚀的现象较为普 遍, 且十分严重 , 必须要采取有力措施来防治其腐蚀 问题 。在此笔者认为 , 无论是哪种储罐 , 要想避 免其 内部 的快速 腐蚀, 就应该从 消除腐蚀因素和 提高储罐 防腐蚀能力入手 。在此笔者简单提出几 点建议 , 具体如下所示: 2 . 1 静 电涂料采用无机富锌作底 漆, 因为无机 富锌漆有牺牲阳极功能。 2 . 2外浮顶石脑油罐 内壁优先选用耐太阳晒、 耐磨、 耐水 的较其它品种 优越 的聚氨脂漆 ; 内浮项罐也应对涂料耐磨性提出要求 2 - 3重质油罐一定要选 耐温、 耐硫 、 耐水性能好 的内防腐涂 料, 可优先 考虑 吠喃树脂漆 。 2 . 4由于有沥青砂层 , 油罐底板外侧可不采取防腐处理 。 一般 油罐底板 外侧腐蚀轻微 , 对于渣油罐等高温油罐罐底边缘板应采用柔性较好 的防水 材料 作防渗水 处理 。
科 学 论 坛
高含硫 原油储 罐 的腐蚀及 防护
任美秋 中石油 哈尔滨石化公 司 【 摘 要】 本文主要探 讨了高含硫原油储罐 的腐蚀 成因以及其 防护措施 , 指出在高含硫原油 的炼制和加工过程 中, 必须要给予储罐 防护足够 的重视 , 采取有效措施避免其 出现腐蚀现象 , 为原油 的生产加 工提 高保障 。文章通过分析原油储罐、 高含硫中间产品罐以及 重油罐 的腐蚀机理与成因, 来探 讨其 防 护措施 , 以供参考 。 【 关键 词】 高含硫 ; 原油; 储罐 ; 腐蚀 ; 防护
浅析高硫原油加工过程的腐蚀与防腐技术
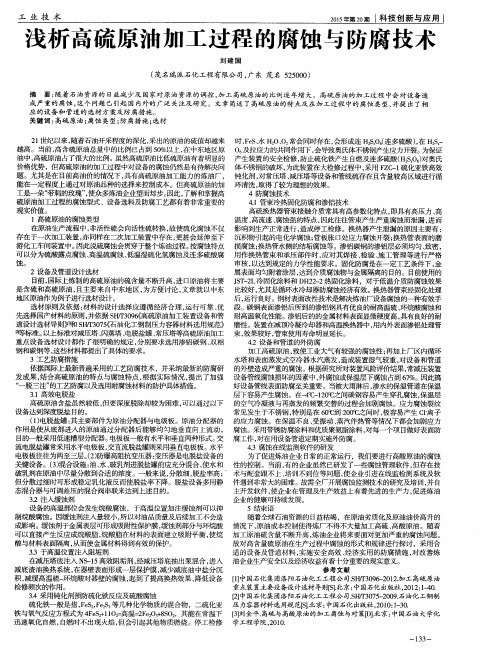
2 0 1 5 年 第2 0 期I 科技创 新 与应用
浅 析 高硫 原油 加工过 程 的腐蚀 与 防腐 技术
刘 广 东 茂名 5 2 5 0 0 0 )
摘 要: 随 着石 油资 源 的 日益减 少及 国 家对 原 油资 源 的调 控 , 加 工 高硫 原 油的 比例 逐 年 增 大 。高硫 原 油 的加 工过 程 中会 对设 备 造 成严 重 的 腐蚀 , 这 个 问题 已 引起 国 内外 的广 泛 关 注及研 究 。文章 简述 了高硫 原 油的 特 点及 在加 工过 程 中的 腐蚀 类 型 , 并提 出了相 应 的 设备 和 管 道 的 选材 方 案及 防 腐措 施 。 关键 词 : 高硫 原 油 ; 腐蚀类型; 防腐措 施 ; 选 材 时, F e S 、 水H : O 、 O 常会 同时存在 , 会形 成 连 H 2 s O ( 连多硫 酸 ) , 在H 2 s 一 O 及 拉应力 的共 同作用下 , 会 导致奥 氏体 不锈钢产生 应力开裂 。 为保 证 产生装置 的安全 检修 , 防止硫化 铁产生 自燃及 连多硫酸 ( H 2 s 0 ) 对奥 氏 体不锈钢 的破坏 , 为此 装置在大检 修过程 中 , 采用 F Z C 一 1 硫化 亚铁高效 钝化剂 , 对常压塔 、 减压塔等设备和管线硫存在且含量较高区域进行循 环清洗 , 取得 了较为理想 的效果 。 工是一朵“ 带刺的玫瑰” , 使众多炼油企业望而却步。 因此 , 了解和掌握高 4防腐蚀技术 硫原油加工过程的腐蚀型式、设备选料及防腐工艺都有着非常重要的 4 . 1管束冷热固化防腐和渗铝技术 现实价 值 。 高硫换热器管柬接触介质常具有高参数化特点 , 即具有高压力 、 高 1高硫原 油的腐 蚀类 型 温度 、 高流速 、 腐蚀强 的特点 , 因此往往 管束产 生严重 腐蚀 而泄漏 , 进而 在 原油生产 流程 中 , 非潘 l 生 硫 会 向活性硫转 换 , 故使 硫化腐 蚀不仅 影 响到生产 正常进 行 , 造成 停工检 修 。换热 器产生 泄漏 的原 因主要有 : 存 在 于一次 加工装 置 , 亦 同样 在二 次加工装 置 中存 在 , 更甚 会延伸 至下 沉 积物引起 的 电化 学腐蚀 ; 管板胀 口处应力 腐蚀开 裂 ; 换热 管表 面的磨 枋 争 化工车间装置 中 。 因此 说硫腐 蚀会贯穿 于整个 炼油过 程。 按腐 蚀特点 损腐 蚀 ; 换热管水侧 的结垢腐 蚀等 。渗铝碳钢 的渗铝层必须 均匀 、 致密 , 可以分为硫酸露点腐蚀、 高温硫腐蚀 、 低温湿硫化氢腐蚀及连多硫酸腐 用作换热管束和承压部件时 , 应对其焊接 、 检验 、 施工管理等进行严格 蚀。 审核 , 以达到规定的力学性能要求。固化防腐是在一定工艺条件下, 金 2设 备及管 道设计 选材 属表 面均匀 附着涂 层 , 达到介质腐 蚀物与 金属隔离 的 目的 。目 前 使用的 目前 , 国际上炼制 的高硫 原油 的硫含量 不断 升高 , 进 口原油将 主要 J S T - 2 L冷 固化涂料 和 D H 2 2 - 2 热 固化涂料 ,对于低 温介质 防腐蚀效 果 是 含硫 和高 硫原 油 , 且 主要来 自中东地 区 , 为方便 讨 论 , 文 章就 以中东 比较好 , 尤 其是循环水 冷却器 防腐 蚀经济有效 。换热器 管束 经 固化 处理 地 区原油作 为例子进 行选材设 计。 后, 运行 良好 。钢材表 面改 J 生 技术是 解决炼 油厂设备腐蚀 的一种有效 手 选 材 原则及 依据 : 材料 的设计 选择 应遵 循 经济合 理 , 运 行 可靠 、 优 段 。 碳钢表 面渗铝后 所到 的渗铝 钢具有优 良的耐高温硫 、 环 烷酸腐蚀 和 先选择国产材料的原则, 并依据 S I - I  ̄3 0 9 6 ( < 高硫原油加工装置设备和管 耐高温氧化 胜能。 渗铝后的的金属材料表面显微硬度高, 具有良好的耐 道设 计选材导 则 口 S I  ̄3 0 7 5 < < 石油 化工钢 制压力容 器材料 选用规 范》 磨 陛。 装置 在减顶冷 凝冷却器 和高温换热器 中 , 用 内外表 面渗铝处理 管 等标 准。 以上标 准对减压塔 、 闪蒸塔 、 电脱盐罐 、 常压塔等 高硫原油加 工 束 , 效 果较好 , 管束 使用寿命 明显延长 。 重点 设备选 材设 计都作 了很 明确 的规定 , 分别要 求选用 渗铝碳 钢 、 双相 4 . 2设备 和管道 的外 防腐 钢和碳 钢等 , 这些 材料都提 出了具体 的要求 。 加工高 疏原油 , 致 使工业 大气有较 强 的腐 蚀 陛 ; 再 加上厂 区内循 环 3工艺 防腐措施 水塔和表面蒸发式空冷器水汽蒸发, 造成装置湿气较重 , 对设备和管道 依据国际上最新普遍采用的工艺防腐技术 ,并采纳最新的防腐研 的外壁造成严重的腐蚀。根据研究所对装置风险评价结果, 常减压装置 发成果, 结合高硫原油的特点与腐蚀特点 , 根据实际情况, 提出了加强 设备管线腐蚀损坏的因素中, 外腐蚀或保温层下腐蚀 占到 6 7 %。因此搞 脱 三 注” 的工艺防腐 以及选用 耐腐蚀材料 的防护具体 措施 。 好设 备管线表 面防腐至 关重要 。当被 大雨淋后 , 渗水 的保温管道 在保温 3 _ 1高 效电脱盐 层下 容易产生腐 蚀 。在_ 1 4 ℃一 1 2 0  ̄ C 之 间碳钢容 易产生穿 孔腐蚀 , 保 温层 高硫 原油含 盐虽然 较低 , 但 要深度脱 除却较 为 困难 , 可 以通 过以下 的空 气冷凝 液与再 蒸发 的频繁交替 的过程 会加剧腐 蚀 。应力 腐蚀 裂纹 设 备达 到深度脱盐 目的 。 常见 发生 于不锈钢 , 特 别是在 6 0  ̄ C  ̄2 0 0  ̄ C 之间 时 , 极 容易产 生 c l _ 离子 ( 1 ) 电脱盐罐 : 其主 要部件 为原油分 配器与 电级板 。原 油分配 器 的 的应 力腐蚀 。在保温 不 良、 受 振动 、 蒸 汽伴 热管 等 隋况 下都会 加剧应 力 作 用是 使从 底部 进入 的原 油通过 分配 器后 能够 均匀 地垂 直 向上 流动 , 腐蚀 。采用带锈 防腐涂料 和优质聚氨脂 涂料 , 对每一个 项 目做 好表 面防 目的一般 采用低速槽 型分配 器。 电极 板一般有水平 和垂直 两种形式 。 交 腐工作 , 对 在用设备管 道定期实施 外防腐 。 流 电脱盐罐 常采用水 平 电极板 , 交 直流脱盐罐 则采用垂 直 电极板 。水平 4 _ 3腐蚀 在线监测 软件 的研发 电极板 往往 为两至三 层 。 ( 2 ) 防爆 高阻抗变 压器 : 变压器是 电脱盐设 备的 为了促进炼油企业 日常的正常运行,我们要进行高酸原油的腐蚀 关键设备。( 3 ) 混合设施: 油、 水、 破乳剂进脱盐罐前应充分混合, 使水和 性 的控 制 。当前 , 有 的企业 虽然 已研发 了一些腐 蚀管理 软件 , 但 存在 技 破 乳剂在原 油 中尽量 分散到合适 的浓度 。一般 来说 , 分散细 , 脱 盐率高 ; 术与配 套跟不 上 、 培训 不到位 等问题 , 使企 业 引进 在线监 检测 系统及 软 但分散过细时可形成稳定乳化液反而使脱盐率下降。脱盐设备多用静 件遇到非 常大 的困难 。故需全 厂开展腐蚀监 测技术 的研 究及培训 , 并自 态混合 器与 可调差压 的混合 阀串联 来达到上述 目的。 主开发 软件 , 使企 业在管 理及生产 效益上 有着先 进的生产 力 , 促 进炼 油 3 . 2注入缓蚀 剂 企业 的健康 可持续发 展。 设 备 的高 温部位会 发生烷 酸腐蚀 ,于高温 位置加 注缓蚀 剂可 以抑 5结束 语 制烷 酸腐蚀 。因缓蚀剂 注入量较小 , 所 以对油 品质量及后续 加工不会造 随着全球 石油资源 的 日 益 枯竭 ,在原油 劣质化及 原油油 价高升 的 成影 响。缓蚀剂 于金属表 层可形成 吸附性保 护膜 , 缓 蚀剂部 分与环烷 酸 情 况下 , 原 油成本 控制使得 炼厂不 得不大 量加工 高硫 、 高 酸原油 。随着 可 以直 接产 生反应 成烷 酸脂 , 烷酸脂 在材料 的表 面建立 吸附平衡 , 使烷 加 工原油硫 含量 不断升 高 , 炼油企 业将来 要面对更 加严重 的腐蚀 问题 。 酸与材料 表面 隔离 , 从 而使金属 材料得 到有效 的保 护 。 故 对高含 量硫原 油在生产 过程 中腐蚀 的形 式 和规 律进行 探讨 , 采 用合 3 . 3于 高温位置 注入阻垢剂 适 的设 备及管 道材 料 , 实施 安全 高 效 、 经 济实用 的防腐 措施 , 对改 善炼 在减压塔底注入 N S - - 1 5 高效阻垢剂, 经减压塔底抽出泵混合, 进入 油企 业生产安 全以及经济 收益有着 十分重要 的现实意义 。 参考文献 减底渣油换热系统 , 在器壁表面形成一层保护膜, 减少减底油中盐分沉 积, 减缓 高温硫 一 环烷 酸对器 壁的腐 蚀 , 起到 了提高换 热效 果 , 降低 设备 [ 1 ] 中国石化 集 团洛 阳石油化 工工程 公 司. S H f F 3 0 9 6 — 2 0 1 2 . 加 工 高硫 原 油 检修 频次 的作用 。 重 点装置主要 设备 设计 选材导则『 S 1 . 北京 : 中国石化 出版社 , 2 0 1 2 : 1 - 4 0 .
含硫原油对炼油设备的腐蚀与对策

含硫原油对炼油设备的腐蚀与对策摘要:在实际的炼油中,经常会有含硫原油和高含硫原油需要加工,这种原油对炼油设备的腐蚀是剧烈的,生产中需要提出有效可行的办法来减少腐蚀保证生产。
关键词:腐蚀硫化物对策目前含硫原油尤其是高含硫原油大大的超过了设备要求含硫量的设计值。
在加工这些原油的过程中就会产生大量的硫化氢,对炼油设备、管路等都带来了极大的腐蚀,严重的甚至会造成安全事故。
因此,如何做好含硫原油加工的防腐工作就成为了眼前必要的课题。
本文主要是从腐蚀的情况、腐蚀机理出发来讨论相关的应对策略。
一、腐蚀情况原油中的硫包括了多种形式:元素硫、硫化氢、硫醇、硫醚、二硫化物、咪吩类化合物,以及分子量大、结构复杂的含硫化合物。
根据原油中硫含量的不同可以分为超低硫原油(S2 ),一般将原油中存在的硫分为活性硫和非活性硫,,元素硫、硫化氢和低分子硫醇等能直接与金属作用而引起设备的腐蚀,统称为活性硫,其余不能直接与金属作用的硫化物统称为非活性硫。
在实际的加工过程中,非活性硫还有可能转变成为活性硫,,使得硫腐蚀会从一次加工装置转移到二次加工装置,甚至逐渐延伸到下游的化工装置。
加上硫腐蚀与氧化物、氯化物、氮化物、氰化物等腐蚀介质的共同作用,形成了错综复杂的腐蚀体系,炼厂装置设备管线因此而发生腐蚀,造成泄漏而停工检修,甚至导致发生安全事故,严重影响生产的稳定运行。
另外腐蚀也是造成企业运营成本的一个重要因素,出现的腐蚀导致了设备的使用寿命减少,维修次数和费用增加,从经济方面考虑也急需控制好设备的腐蚀情况。
二、腐蚀机理在炼油过程中,存在于原油中的各种硫化物会在加工过程分解成硫化氢,从而对设备进行腐蚀,腐蚀的形式也是具有多样性,包括全面腐蚀、坑蚀、氢鼓泡、氢诱发阶梯裂纹、氢脆及硫化物应力腐蚀破裂等。
1.HCI-H2S-H2OS腐蚀此类腐蚀主要是由于无机盐与原油中的硫反应而造成的。
无机盐包括NaCl、MgCI2、CaCI2等盐类,经加热水解后与硫生成氯化氢,而硫化物就会分解生成硫化氢。
浅谈含硫原油的腐蚀及保护措施
浅谈含硫原油的腐蚀及保护措施摘要:炼油设备的腐蚀不但给炼油厂造成经济损失,而且对环境也会产生污染。
设备腐蚀带来的资源消耗是一种巨大的浪费。
本文将就炼油厂设备腐蚀的原因以及解决方法展开讨论。
关键词:炼油厂;炼油设备;腐蚀原因;防护措施随着从中东、西北地区从中亚进口含硫原油数量的大幅度增加,以及国内含硫油田的开发,原油平均含硫量逐年增高。
原油硫含量的增加,使加工高硫原油的设备,包括进口的不锈钢设备和管道,发生严重的硫腐蚀。
正常生产中由于硫腐蚀时常引发破裂、燃烧、爆炸等恶性事故,同时还导致严重的环境污染。
原油中所含硫和硫化物的总量称之为原油的硫含量,其中的硫化物主要是有机硫化物,也有少量的单质硫和硫化氢,其主要类型有:单质硫S,硫化氢H2S,硫醇RSH,硫醚RSR,二硫化物RSSR。
可以和金属直接反应生成硫化物叫做活性硫,如单质硫、硫化氢和硫醇:S+Fe→FeS H2S+Fe→FeS+H2RCH2CH2SH+Fe →FeS+RCH=CH2+H2一.低温湿硫化氢腐蚀在低温下H2S只有溶解水中才具有腐蚀性。
通常低温下由于金属表面存在着水或水膜,而铁发生腐蚀反应: H2S+Fe→FeS+H2在搅动H2O中的悬浮S时可使pH值下降到1.8,认为这是S在H2O中的歧化反应引起的:4S+4H2O →3H2S+H2SO4硫与钢的直接接触,起到有效阴极的作用而加速腐蚀。
在水溶液中硫引起碳钢腐蚀的反应为:阳极过程: Fe→ Fe2++2e—Fe+H2O→ Fe(OH)++H++2e—阴极过程:Sn+2e →Sn2- Sn2-→S2-+S n-1二.高温硫化物腐蚀腹有诗书气自华高温下硫和硫化氢能直接与金属发生反应,生成金属的硫化物,其主要腐蚀反应过程为:S+Fe→FeS H2S+Fe→FeS+H2高温下H2S可发生分解,产生的元素硫具有很高的活性,与Fe发生反应极为强烈:H2S →H2+S S+Fe→ FeS原油中含的部分硫醇,在200℃以上也可以与铁直接发生反应产生硫化铁腐蚀产物:RCH2CH2SH+Fe→RCH2CH3+FeS+H2连多硫酸的形成及其腐蚀过程,如在催化裂化装置烟气管道中,高温部位(400~600℃)又有SO2和CO存在时:SO2+2CO →2CO2+S S+Fe→ FeS2SO2+O2→2SO3 SO3+H2O →H2SO4FeS+H2SO4→FeSO4+H2S H2S+H2SO4→4H2SxO6+S反应过程使在运行中形成的FeS膜破坏,腐蚀反应过程中形成的S和H2S又可参与金属的腐蚀过程,所以对材料的腐蚀具有自催化作用,过程中形成的亚硫酸,应力腐蚀开裂有诱发作用。
原油储罐底板腐蚀原因分析及防护对策
原油储罐底板腐蚀原因分析及防护对策摘要:针对中国石化塔河炼化有限责任公司原油储罐底板腐蚀严重的问题,分析了产生腐蚀的原因,提出了罐底板采用涂料与牺牲阳极联合保护,支柱对应处底板增焊不锈钢板等防护措施。
关键词:原油;储罐;腐蚀;防护;涂料;牺牲阳极1前言中国石化塔河炼化有限责任公司(以下简称“塔河炼化公司”)现具有500万吨/年原油综合加工能力,加工塔河原油,该原油密度高、盐含量高、粘度大、沥青质含量高。
近年来,其性质进一步劣质化,密度接近0.96g/cm3、盐含量400-600mg/l、硫含量〉2%,由于原油性质属于高硫原油,使原油储罐等设备的腐蚀日趋严重,2016年10月1#装置大检修时已发生原油储罐底板因腐蚀导致开裂。
因此,搞清原油储罐底板的腐蚀机理,制订合理的防护措施,对于确保原油储罐安全长周期运行具有十分重要的意义。
2原油储罐底板腐蚀状况塔河炼化公司现有原油储罐7台,总容量18万立方米。
单台原油储罐的最大容量为50000m3,最小为10000m3,平均容量为25000m3。
在装置建成投产第一个运行周期内,塔河炼化公司原油储罐底板的腐蚀问题并不是很突出,防腐措施基本上采用单独涂料防腐,选用的涂料既有导静电的(如H99-1环氧导静电涂料),也有绝缘性的(如氰凝PA106涂料)。
随着含硫原油加工数量的不断增加,原油储罐底板的腐蚀呈现加剧趋势。
2016年10月1#装置大检修时已发生T106原油储罐底板因腐蚀导致开裂。
对于其它原油储罐,虽然没有因腐蚀穿孔而导致漏油的情况,但罐底板都存在较严重的腐蚀现象。
原油储罐底板的腐蚀特征基本一致,腐蚀最严重的部位集中在底板最外圈等沉积水较多的浮盘支柱下面,底板腐蚀穿孔基本发生在该部位(见图1),罐底板其它部位主要表现为坑蚀,钢板表面存在大小、深浅不一的腐蚀坑(见图2)。
图1 原油储罐底板腐蚀开裂图图2T106原油储罐底板表面坑蚀3腐蚀原因分析3.1罐底板坑蚀原因分析3.1.1原油沉积水的腐蚀。
炼制高硫原油的腐蚀情况与防护措施
93பைடு நூலகம்4
95 3
1 6 30 . - 9 5
15 _ .一l8
26 2
13 O
07 .9
02 .
左 右腐 蚀 就 不 明显 了 。 非 活 性 硫 包 括 硫 醚 ( — — R )二 硫 醚 ( — — — )环 硫 醚 、 R S ,’ R S S R/’ 噻 吩 、 硫 化 物 等 , 特 点 不 能 与 铁 直 接 发 生 反 应 , 是 受 热 后 分解 , 多 其 而 生 成 活性 硫 , 金 属 产 生 强 烈 的 腐蚀 作 用 。 对 高温 下 活 性 硫 的 腐 蚀 规 律 基 本服 从 化 学 腐 蚀规 律 ,即 一 般 来 说 , 温 度 升 高 , 蚀 加 快 ; 化 物 浓 度 高 , 蚀 加 快 ; 度 高 , 分 解 快 而 腐 硫 腐 温 热
现分 几 种情 况 分 析 其 腐 蚀 过 程 : 含硫条 件下 , 如果有环 烷酸同时存在 , 可以将高温硫腐蚀 时生成 11 低 温 ( 10C) 油 部 位 的 腐 蚀 . ≤ 2 ̄ 轻 e 同 从 低温 腐 蚀 部 位 主要 是 常 压 塔 上 部 五 层 塔 盘 、 底 及 部 分 挥 发 线 及 的 F S保 护 膜 溶 解 , 时 又生 成 活 性 H , 而发 生 更为 强 烈 的腐 蚀 。 塔
多, 活性 硫 浓 度 增 加 , 蚀 加 快 。 腐 1 高 温 下 硫 化 物 与 环 烷 酸 共 存 的腐 蚀 . 3
辽 河 油
98 4
02 .4
3. 42
32 .8
海 洋 油
92 4
03 _
5 6
32 .
1 原 油 中 的 腐蚀 性 介 质 对 设 备 的 腐 蚀 机理
浅析高硫原油对炼油设备的腐蚀与防护
浅析高硫原油对炼油设备的腐蚀与防护Abstract This article describes the corrosion characteristics of Middle East crude oil,main types of sulphide cor rosion and relevant preventive measures as well as the way to strengthen the cor rosion preventing research and implement scientific management.1 概述广州石油化工总厂经过二期扩建和改造,原油处理能力已达770万t/a,原油来源多数为进口原油,1997年原油进口量达总处理量的97%,预测亚太地区石油产量日趋减少,中东地区,特别是沙特原油仍稳定供应,中东原油占世界贮量的65%。
由于中东原油普遍含硫高且价格相对较低,所以广石化总厂选择炼中东高硫原油的比例越来越多,从而造成炼油装置中硫的腐蚀将越加严重。
需要尽快对设备防腐蚀问题进行深入研究,正确选择有关装置的设备材料及防腐措施,确保加工含高硫原油装置的正常运转。
2 中东油的腐蚀特点2.1含硫原油的腐蚀源原油中的硫化物主要有硫醇(RSH)、硫醚(RSR')、硫化氢(H2S)、多硫化物(RMS N )等。
这些硫化物中参与腐蚀反应的主要是H2S、S、RSH和易分解成H2S的硫化物,一般称其为腐蚀源或活性硫。
不同的原油所含硫化物的组成不同,即使总含量接近,在加工过程中生成的活性硫化物量也可能出现较大的差别。
如图1所示。
以含硫相近的阿拉伯原油(含硫1.7%)与伊朗原油(含硫1.4%)相比,在250~330℃馏分中的H2S含量,阿拉伯原油高达180mg/L,而伊朗原油只有20mg /L,就是说该馏分所在常减压分馏塔部位前其腐蚀基本没有,而炼阿拉伯原油时要比炼伊朗原油时产生H2S含量严重得多.硫含量不同的原油,腐蚀部位也不一样。
- 1、下载文档前请自行甄别文档内容的完整性,平台不提供额外的编辑、内容补充、找答案等附加服务。
- 2、"仅部分预览"的文档,不可在线预览部分如存在完整性等问题,可反馈申请退款(可完整预览的文档不适用该条件!)。
- 3、如文档侵犯您的权益,请联系客服反馈,我们会尽快为您处理(人工客服工作时间:9:00-18:30)。
浅析高硫原油对炼油设备的腐蚀与防护----转载(2008-07-27 14:26:37)转载标签:跟着火炬看中国h2硫化物应力腐蚀高硫原油中东杂谈1 概述广州石油化工总厂经过二期扩建和改造,原油处理能力已达770万t/a,原油来源多数为进口原油,1997年原油进口量达总处理量的97%,预测亚太地区石油产量日趋减少,中东地区,特别是沙特原油仍稳定供应,中东原油占世界贮量的65%。
由于中东原油普遍含硫高且价格相对较低,所以广石化总厂选择炼中东高硫原油的比例越来越多,从而造成炼油装置中硫的腐蚀将越加严重。
需要尽快对设备防腐蚀问题进行深入研究,正确选择有关装置的设备材料及防腐措施,确保加工含高硫原油装置的正常运转。
2 中东油的腐蚀特点2.1含硫原油的腐蚀源原油中的硫化物主要有硫醇(RSH)、硫醚(RSR')、硫化氢(H2S)、多硫化物(RM SN)等。
这些硫化物中参与腐蚀反应的主要是H2S、S、RSH和易分解成H2S的硫化物,一般称其为腐蚀源或活性硫。
不同的原油所含硫化物的组成不同,即使总含量接近,在加工过程中生成的活性硫化物量也可能出现较大的差别。
如图1所示。
以含硫相近的阿拉伯原油(含硫1.7%)与伊朗原油(含硫1.4%)相比,在250~330℃馏分中的H2S含量,阿拉伯原油高达180mg/L,而伊朗原油只有20mg/L,就是说该馏分所在常减压分馏塔部位前其腐蚀基本没有,而炼阿拉伯原油时要比炼伊朗原油时产生H2S含量严重得多.硫含量不同的原油,腐蚀部位也不一样。
圣玛丽原油含硫量高达4.7%,但在300℃以下几乎全部分解成H2S。
也就是说,只有在常压塔腐蚀严重。
而苏门答腊原油的含硫量仅有 0.6%,但在300℃以上才分解出H2S。
所以,在减压塔系统腐蚀比较严重。
因此,应根据进口原油的种类,以及腐蚀源不易确定等情况,合理地选择设备的材质和防腐措施。
图1 不同原油硫含量分布1-含硫1.7%阿拉伯原油 2.含硫4.7%圣玛丽原油3-含硫3.0%卡胡吉原油4-含硫2.7%科威特原油5-含硫1.4%伊朗原油6-含硫1.0%凯伦原油7-含硫0.6%苏门答腊原油2.2硫化物的一般腐蚀规律原油中的硫醚(RSR')和二硫化物(RSSR)热稳定性较差,当温度达到130~160℃就可以分解出H2S,正戊硫醇在400℃才有10%被分解。
因此,硫化物的腐蚀与原油中的硫含量无直接关系,只与操作温度有关。
(1)当温度<120℃时,硫化物未分解,在无水情况下对设备无腐蚀,含水时则形成H2S -H2O型腐蚀。
(2)当温度在120~240℃时,硫化物的分解较少,对设备腐蚀较轻。
(3)当温度在240~340℃时,硫化物分解加快,对设备腐蚀加重。
(4)当温度在340~400℃时,H2S开始分解为H2和S,元素S与Fe反应生成Fe S,设备腐蚀会很快。
(5)当温度在426~430℃时,高温硫对设备腐蚀速度最快。
(6)当温度>480℃时,H2S几乎完全分解,设备腐蚀率下降。
(7)当温度>500℃时,进入高温氧化腐蚀区,不属硫化物的腐蚀范围。
总的来说,温度升高,腐蚀加快;硫化物浓度高,腐蚀加快;温度高,热分解快而多,活性硫浓度增加,腐蚀加快。
图2为各种钢在含硫原油中腐蚀率随温度的变化规律。
图3为设备温度,H2S量与腐蚀的关系。
图2 钢在含S 1.5%原油中的近似腐蚀率图3 温度、H2S量与腐蚀的关系3 硫化物的主要腐蚀类型及其防护3.1低温轻油部位的HCl-H2S-H2O腐蚀及防护原油开采出来时伴有水份,这些水份含有NaCl、CaCl2、MgCl2等盐类。
在炼制中,MgCl2和CaCl2很容易受热水解生成腐蚀性很强的HCl;原油中的硫化物则分解成H2S。
水解生成的HCl和H2S随着轻组分及水分从塔顶逸出,在塔顶部和冷凝冷却系统中形成pH值很低的冷凝液,即形成了HCl-H2S-H2 O型腐蚀介质,使设备受到严重腐蚀。
这种腐蚀常出现在常减压装置的初馏塔顶部和常压塔顶部的塔壁,塔盘以及相应的冷凝冷却系统。
例如广石化炼油(一)蒸馏常压塔塔顶部,工艺条件:t油气=110℃,P= 0.05MPa,材质:20R衬18-8钢板,1989~1993年大修均发现原衬里局部腐蚀开裂现象,经分析属应力腐蚀破裂。
1993年大修将衬里改成双相不锈钢后效果很好,在1994~ 1997年大修中检查,该双相不锈钢(00Cr18Ni5Mo3Si2)衬里均光洁,无裂纹,无鼓泡,焊缝完好。
实践证明:HCl-H2S-H2O型腐蚀,碳钢产生均匀腐蚀, Cr13型钢为点蚀,18-8钢为应力腐蚀破裂。
影响的主要因素是氯离子含量,而H2S 则是HCl电化学腐蚀的促进剂。
上述部位的防腐蚀措施,除了从选材方面控制减少腐蚀外,还应从工艺操作中加强“一脱三注” ,以保证氯离子含量不超标,开好电脱盐系统,使其出口含盐量控制在<3mg/L范围内。
另外冷凝、冷却器可采用CH784涂料、漆酚酞涂料作为防护层,效果也很好。
3.2高温硫化氢腐蚀与防护原油中的硫化物在高温下分解出以H2S为主的活性硫化物与钢反应生成FeS,当炼油设备壁温高于250℃时腐蚀开始加快,在340~400℃时,硫化氢分解成S+H2,产生元素硫比H2S有更强的活性,在此温度下低级醇也能与铁反应。
温度在430℃时腐蚀率最高,但当温度高于450℃时,腐蚀率将明显降低,如图4。
硫化氢浓度的大小与腐蚀率成正比例关系,腐蚀产物FeS膜具有阻碍H2S进一步接触钢的作用。
在开始时速度很快,以后逐渐降低,直至一个恒定的速度。
当采用含铬合金钢时,钢的表面形成双层垢层,外层为多孔的硫化亚铁,内层为致密的Cr2O3,当Cr含量大于5%时则可生成比较稳定的尖晶石型化合物,如FeCr2O4垢层。
因此,含Cr占5%以上的合金钢有良好的耐高温硫化氢腐蚀性能。
图4 加工含硫1.4%~1.5%的原油时温度对碳钢加热炉管腐蚀率的影响加氢装置属于H2~H2S腐蚀介质存在环境,它对碳钢和低铬钢的腐蚀速率将随着温度升高而增加,特别是硫化氢和氢共存时比H2S单独存在时产生的腐蚀还要激烈和严重。
氢起着催化剂的作用,加速腐蚀的进行。
广石化炼油厂炼中东油属高温硫化氢腐蚀的装置有常减压蒸馏、催化、加氢精制、减粘等,在腐蚀严重的环境可采用Cr9Mo和18-8钢。
例如加氢(二)反应器,规格Φ2600×2 060×(110+3+3);主体材质为2 1/4 Cr1Mo,内衬E309+E347;设计压力为8.63MPa,设计温度为425℃,介质为H2、H2S,硫化氢含量为2%。
该反应器自1991年9月投产运行至1994年10月停工进行全面检验,结果是:筒体、焊缝、衬里表面均无腐蚀裂纹,内堆焊层铁素体含量3%~5%属正常,渗透探伤抽查合格。
可见,该反应器在设计选材、制造等的防腐蚀措施是可行的。
又例如炼油(一)蒸馏常压塔转油线,介质为油汽,温度为360℃,压力为0.05MPa,该转油线原来材质为碳钢,最高腐蚀速率在20m m/a以上,平均7.3~13.4mm/a,1988年将碳钢改换成18-8钢后,腐蚀速率下降为0 .4mm/a以下,多次大修检查,均未发现点蚀,裂纹等现象。
3.3高温钒的腐蚀中东高硫原油中含钒量较高,如伊朗、阿拉伯重油等原油中含钒量均超过30mg /L,有必要重视钒腐蚀的问题。
在催化裂化再生器中,钒除了破坏分子筛结构而使催化剂失去活性和选择性外,还会在高温燃烧过程中生成V2O5。
钒的氧化物既能破坏金属保护膜,还能与Cr2O3(含铬钢表面的氧化层)形成复合氧化物,使铬镍耐热钢受到破坏。
例如加热炉的燃烧中钒含量过高也会造成严重腐蚀,因此防止钒腐蚀,也是加工含硫原油的重大课题。
3.4连多硫酸(H2S X O6)的腐蚀与防护连多硫酸很容易引起奥氏体不锈钢产生晶间型的应力腐蚀破裂。
H2S X O6是在装置停车时由硫化物膜,水和氧生成的。
其反应如下:3FeS+5O2=Fe2O3*FeO+3SO2SO2+H2O=H2SO3H2SO3+H2S=mH2S X O6+nS连多硫酸腐蚀是非常危险的。
当水含有微量的连多硫酸的钾盐,就可以使敏化的奥氏体不锈钢在室温下产生应力腐蚀破裂。
靠近焊缝的区域长期在高温(350~450℃)下工作后,在连多硫酸的作用下特别容易产生这种破坏。
例如某炼油厂烟机系统波纹管(材质为18-8进出口共6 个),从1990年10月安装开工到1991年3月停机,实际运行3个多月,其中因故障停机10余次,在最后一次停机期间全部发生了腐蚀开裂。
经中船总公司七院七二五所分析认为,波纹管的快速失效是由于波纹管在使用过程发生了敏化,停工期间产生的H2S X O6使得波纹管发生了晶间型腐蚀开裂。
又如日本昭和石油(株)川山奇炼油厂粗汽油脱硫装置和炼油脱硫装置的几台冷凝器的浮头盖连接螺栓多根发生折断(诊断为应力腐蚀开裂)。
国内也有加氢精制装置的不锈钢(18-8)换热器在停工检修时,靠近管板胀口处的管子发生断裂和管板出现裂纹(未经过消应处理)的实例。
防止此类应力腐蚀的措施:(1)尽量减少开停工的次数,避免设备在停工时产生H2S XO6的可能性。
(2)停工期间对设备进行充N2保护,防止H2S X O6的生成,或用碱液进行局部清洗,把设备表面生成的H2S X O6中和掉。
(3)在设备的制造和安装焊接时,尽可能采取措施减少热应力和焊接变形引起的残余应力。
(4)材料选用:应选用不易形成贫铬区的稳定型不锈钢(如SUS347、SUS321等),并控制好稳定化元素(如 Nb、Ti)的含量,也可选用奥氏体+铁素体双相不锈钢或铁素体不锈钢。
4 加强防腐蚀技术的研究和科学管理目前我厂大量加工中东高含硫原油,硫化物对炼油设备的腐蚀将更加严重,因此,必须加强防腐蚀技术的研究和科学管理,采用科学信息管理的手段,加强防腐监控工作。
(1)建立原油加工档案及其腐蚀数据库,包括不同油种的硫化物在不同馏分段的分布数据;不同活性硫化物在不同温度和浓度下的腐蚀数据。
(2)建立工艺防腐数据库:研究适合于各个油种的“一脱三注”的工艺条件及助剂,抗腐蚀破坏的催化剂等。
(3)建立缓蚀剂、中和剂、防腐涂料等使用的数据库。
(4)建立材料防腐的数据库,实行材质升级后的跟踪。
(5)建立重点装置腐蚀严重部位,关键设备的腐蚀跟踪档案。
(6)综合各种含硫原油的基础数据,优化工艺条件及设备选材,实现炼油装置长周期运转。