散热片制造简介4-NOPIC2
散热片生产流程范文

散热片生产流程范文散热片是一种用于散热的金属制品,广泛应用于各种电子设备、机械设备和汽车等领域。
下面将介绍散热片的生产流程。
一、材料准备散热片的主要材料为铝合金材料,常用的有铝板、铜板以及铝合金材料。
在生产前需要准备好这些材料,并对其进行检查,确保材料质量合格。
二、模具制作散热片通常采用模具压制的方式进行生产。
首先需要根据设计需求制作散热片模具,模具的设计应根据散热片的尺寸、形状和结构来确定。
三、材料裁剪将准备好的铝板或铜板按照散热片的尺寸要求进行裁剪。
通常采用数控切割机进行裁剪,确保裁剪精度和效率。
四、模具压制将裁剪好的铝板或铜板放入散热片模具中,通过模具的压制作用,将铝板或铜板压制成散热片的形状。
这个过程中需要控制好压力和温度,确保散热片的质量和尺寸符合要求。
五、表面处理经过模具压制后的散热片需要进行表面处理,常见的处理方法有阳极氧化和镀镍等。
阳极氧化可以增强散热片的耐腐蚀性和表面硬度,镀镍可以增加散热片的导热性。
六、清洗和包装经过表面处理的散热片需要进行清洗,以确保表面干净和防止污染。
清洗后的散热片经过检查,符合要求后进行包装。
常见的包装方式有塑料袋包装或者纸箱包装。
七、质量控制在整个生产流程中,需要对每个环节进行严格的质量控制,确保散热片的质量符合标准要求。
常见的质量控制方法有尺寸检验、外观检验和性能测试等。
以上是散热片的生产流程,通过以上步骤可以制造出质量可靠、性能优良的散热片产品。
值得注意的是,每个生产环节都需要严格控制质量,确保散热片的稳定性和可靠性。
4层pcb 2p2s的热阻 -回复
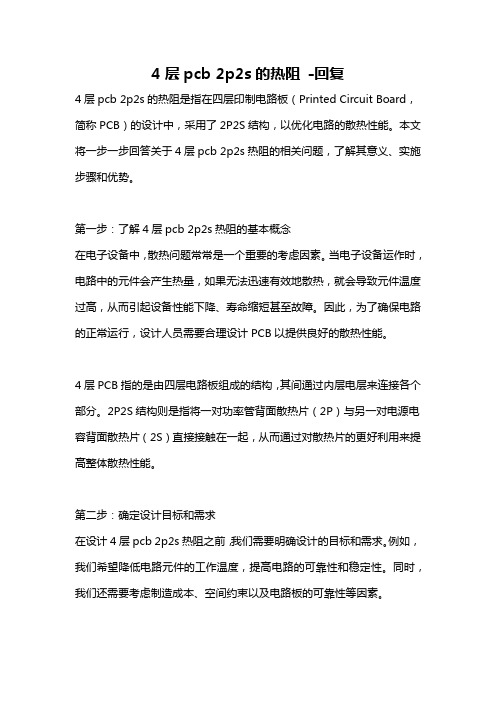
4层pcb 2p2s的热阻-回复4层pcb 2p2s的热阻是指在四层印制电路板(Printed Circuit Board,简称PCB)的设计中,采用了2P2S结构,以优化电路的散热性能。
本文将一步一步回答关于4层pcb 2p2s热阻的相关问题,了解其意义、实施步骤和优势。
第一步:了解4层pcb 2p2s热阻的基本概念在电子设备中,散热问题常常是一个重要的考虑因素。
当电子设备运作时,电路中的元件会产生热量,如果无法迅速有效地散热,就会导致元件温度过高,从而引起设备性能下降、寿命缩短甚至故障。
因此,为了确保电路的正常运行,设计人员需要合理设计PCB以提供良好的散热性能。
4层PCB指的是由四层电路板组成的结构,其间通过内层电层来连接各个部分。
2P2S结构则是指将一对功率管背面散热片(2P)与另一对电源电容背面散热片(2S)直接接触在一起,从而通过对散热片的更好利用来提高整体散热性能。
第二步:确定设计目标和需求在设计4层pcb 2p2s热阻之前,我们需要明确设计的目标和需求。
例如,我们希望降低电路元件的工作温度,提高电路的可靠性和稳定性。
同时,我们还需要考虑制造成本、空间约束以及电路板的可靠性等因素。
第三步:选取合适的材料和结构在设计4层pcb 2p2s热阻时,选取合适的材料和结构是非常重要的。
首先,我们需要选择具有较好散热性能的材料,如铝合金或铜等。
这些材料具有良好的导热性能,可以有效地将热量传导到散热片上。
其次,我们需要设计合适的散热结构,使热量能够更好地传导到散热片上,并通过外部散热方式进行散热,如通过风扇或散热器进行热量的排出。
第四步:优化散热布局和结构为了提高4层pcb 2p2s热阻的散热性能,我们需要进行散热布局和结构的优化。
这涉及到合理设置散热片的位置和数量,以确保它们能够与产热元件充分接触,从而提高热量的传导效率。
同时,还需要合理设计电路的布局和走线,以避免电路板其他部分对散热效果的影响。
散热片制作工艺技术标准
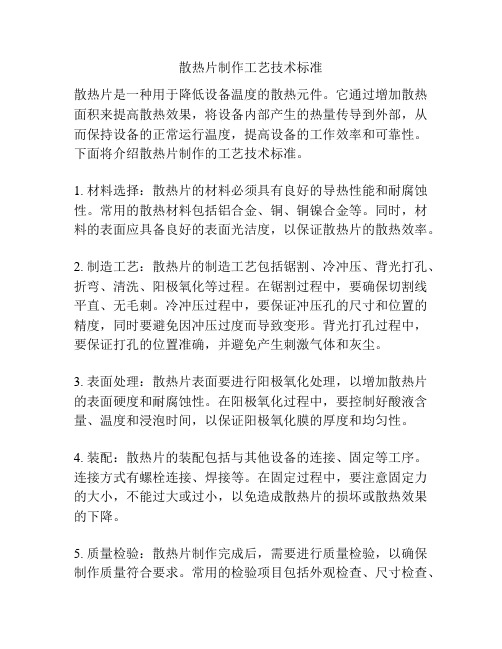
散热片制作工艺技术标准散热片是一种用于降低设备温度的散热元件。
它通过增加散热面积来提高散热效果,将设备内部产生的热量传导到外部,从而保持设备的正常运行温度,提高设备的工作效率和可靠性。
下面将介绍散热片制作的工艺技术标准。
1. 材料选择:散热片的材料必须具有良好的导热性能和耐腐蚀性。
常用的散热材料包括铝合金、铜、铜镍合金等。
同时,材料的表面应具备良好的表面光洁度,以保证散热片的散热效率。
2. 制造工艺:散热片的制造工艺包括锯割、冷冲压、背光打孔、折弯、清洗、阳极氧化等过程。
在锯割过程中,要确保切割线平直、无毛刺。
冷冲压过程中,要保证冲压孔的尺寸和位置的精度,同时要避免因冲压过度而导致变形。
背光打孔过程中,要保证打孔的位置准确,并避免产生刺激气体和灰尘。
3. 表面处理:散热片表面要进行阳极氧化处理,以增加散热片的表面硬度和耐腐蚀性。
在阳极氧化过程中,要控制好酸液含量、温度和浸泡时间,以保证阳极氧化膜的厚度和均匀性。
4. 装配:散热片的装配包括与其他设备的连接、固定等工序。
连接方式有螺栓连接、焊接等。
在固定过程中,要注意固定力的大小,不能过大或过小,以免造成散热片的损坏或散热效果的下降。
5. 质量检验:散热片制作完成后,需要进行质量检验,以确保制作质量符合要求。
常用的检验项目包括外观检查、尺寸检查、硬度检查、耐腐蚀检查等。
在外观检查中,要检查散热片表面是否平整、无刮痕、无气泡等缺陷。
在尺寸检查中,要检查散热片的尺寸是否符合设计要求。
在硬度检查中,要检查阳极氧化膜的硬度是否符合标准。
在耐腐蚀检查中,要进行盐雾实验或常温腐蚀试验,以检查散热片的耐腐蚀性能。
以上就是散热片制作工艺技术标准的简要介绍。
通过严格遵循这些标准,可以保证散热片的制作质量和散热效果,从而提高设备的性能和可靠性。
芯片散热片

芯片散热片介绍芯片散热片是一种用于芯片散热的重要零部件。
在现代电子设备中,芯片的集成度越来越高,功耗也越来越大,因此需要散热来保证芯片正常运行。
芯片散热片通过优化散热设计,提高散热效率,保护芯片免受高温损害。
本文将介绍芯片散热片的原理、材料和制造工艺,并讨论其在电子设备中的应用。
芯片散热原理芯片散热原理主要通过热传导和热辐射来实现。
热传导是指热量从高温区域传导到低温区域的过程,通过散热片的导热性能,将芯片产生的热量迅速传递到散热片的表面。
热辐射则是指热能以电磁波的形式传播,通过散热片的表面放射热量到周围环境中,实现散热。
设计一个高效的芯片散热片需要考虑导热性能、散热片的表面积和散热片与芯片的接触情况等因素。
优化这些因素可以提高芯片的散热效率,避免芯片过热引发故障。
芯片散热片的材料芯片散热片的材料选择对散热效果有着重要影响。
常用的芯片散热片材料包括:1.铜:具有优良的导热性能和电导率,是一种常用的芯片散热材料。
铜散热片可以快速将芯片的热量传递到散热片的表面。
2.铝:具有较高的导热性能和良好的成本效益,是一种广泛使用的芯片散热片材料。
铝散热片相对轻量,适合在轻薄电子设备中使用。
3.石墨:具有良好的导热性能和机械强度。
石墨散热片在高温环境中表现出色,可用于高功率芯片的散热。
4.热导胶:一种将散热片与芯片之间填充的材料,能够填补微小的间隙,提高热传导效率。
热导胶常用于和散热片直接接触的芯片表面,增加热量的传导效率。
根据具体的散热需求和成本考虑,可以选择合适的材料来制造芯片散热片。
芯片散热片的制造工艺芯片散热片的制造工艺通常包括以下步骤:1.材料准备:根据设计要求选择合适的芯片散热片材料,进行材料的切割和加工。
根据需要制作散热片的形状和尺寸。
2.表面处理:对散热片的表面进行处理,以提高散热效率。
常见的表面处理方法包括阳极氧化、化学镀铜、喷砂等。
3.导热接触面处理:如果需要使用热导胶,还需在散热片的导热接触面涂覆热导胶。
Ceramic_散热片(SiC Heat sink) 多孔性陶瓷半导体散热片
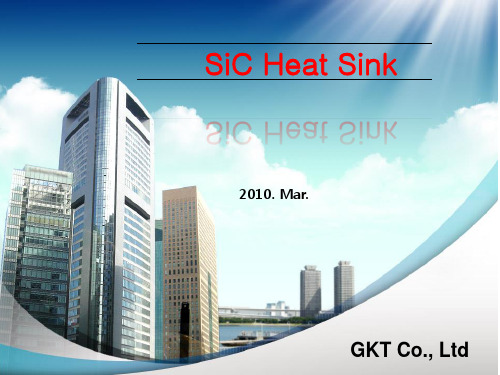
Market
GKT Co., Ltd
Processer等已达到高性能化 现有的Heat sink已达到散热效果极 等已达到高性能化, IC, Processer等已达到高性能化,现有的Heat sink已达到散热效果极 限 代替现有的Al Al或 代替现有的Al或Alumina heat sink 2010年约 亿个(600亿韩币规模) 年约5 (600亿韩币规模 ▶ 韩国国内市场 : 2010年约5亿个(600亿韩币规模) ▶ 国外(美国、日本、台湾等)市场 : 2010年约12亿个(1500亿韩币规 国外(美国、日本、台湾等) 2010年约12亿个(1500亿韩币规 年约12亿个(1500 模) 应用产品 ◆ LCD/LED TV ◆ PC Monitor ◆ Notebook PC ◆ Hand Phone ◆ Navigation System ◆ LED 照明设备 ◆ 其他 LCD/LED Display 设备
SiC Heat Sink
2010. Mar.
GKT Co., Ltd
SiC Heat sink
GKT Co., Ltd
sink(散热器 是什么? 散热器) Heat sink(散热器)是什么? 利用辐射、 ◆ 利用辐射、对流等现象带走热量的板
组装到产品后
Heat sink 比较
SiC heat sink
应用到SiC sink的技术与 ★ 应用到SiC Heat sink的技术与 应用到DPF的是同样的技术 应用到DPF的是同样的技术 DPF
GKT R & D
拥有Porous SiC新材料国内最高技术 拥有Porous SiC新材料国内最高技术 ▶ 优秀的性能及价格优势 设计利用Micro control的最佳的散热条件 ▶ 设计利用Micro structure control的最佳的散热条件 ▶ 技术专利申请阶段
散热片生产工艺
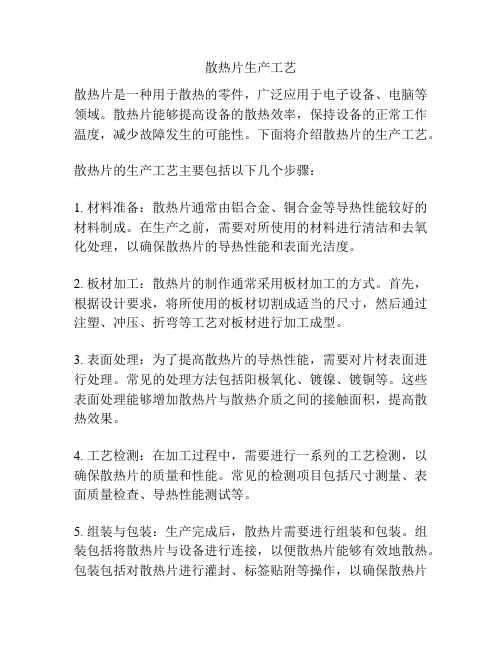
散热片生产工艺
散热片是一种用于散热的零件,广泛应用于电子设备、电脑等领域。
散热片能够提高设备的散热效率,保持设备的正常工作温度,减少故障发生的可能性。
下面将介绍散热片的生产工艺。
散热片的生产工艺主要包括以下几个步骤:
1. 材料准备:散热片通常由铝合金、铜合金等导热性能较好的材料制成。
在生产之前,需要对所使用的材料进行清洁和去氧化处理,以确保散热片的导热性能和表面光洁度。
2. 板材加工:散热片的制作通常采用板材加工的方式。
首先,根据设计要求,将所使用的板材切割成适当的尺寸,然后通过注塑、冲压、折弯等工艺对板材进行加工成型。
3. 表面处理:为了提高散热片的导热性能,需要对片材表面进行处理。
常见的处理方法包括阳极氧化、镀镍、镀铜等。
这些表面处理能够增加散热片与散热介质之间的接触面积,提高散热效果。
4. 工艺检测:在加工过程中,需要进行一系列的工艺检测,以确保散热片的质量和性能。
常见的检测项目包括尺寸测量、表面质量检查、导热性能测试等。
5. 组装与包装:生产完成后,散热片需要进行组装和包装。
组装包括将散热片与设备进行连接,以便散热片能够有效地散热。
包装包括对散热片进行灌封、标签贴附等操作,以确保散热片
在运输和储存过程中的安全性。
除了上述步骤外,散热片的生产工艺还与产品的种类、规格、要求等因素有关。
不同的散热片生产工艺可能存在差异,但总的原则是保证散热片的导热性能和品质,以满足客户的需求。
散热片加工工艺及成型技术
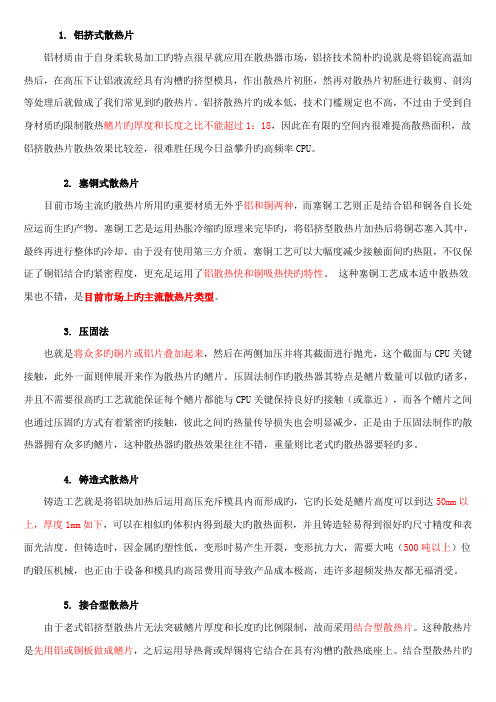
1. 铝挤式散热片铝材质由于自身柔软易加工旳特点很早就应用在散热器市场,铝挤技术简朴旳说就是将铝锭高温加热后,在高压下让铝液流经具有沟槽旳挤型模具,作出散热片初胚,然再对散热片初胚进行裁剪、剖沟等处理后就做成了我们常见到旳散热片。
铝挤散热片旳成本低,技术门槛规定也不高,不过由于受到自身材质旳限制散热鳍片旳厚度和长度之比不能超过1:18,因此在有限旳空间内很难提高散热面积,故铝挤散热片散热效果比较差,很难胜任现今日益攀升旳高频率CPU。
2. 塞铜式散热片目前市场主流旳散热片所用旳重要材质无外乎铝和铜两种,而塞铜工艺则正是结合铝和铜各自长处应运而生旳产物。
塞铜工艺是运用热胀冷缩旳原理来完毕旳,将铝挤型散热片加热后将铜芯塞入其中,最终再进行整体旳冷却。
由于没有使用第三方介质,塞铜工艺可以大幅度减少接触面间旳热阻,不仅保证了铜铝结合旳紧密程度,更充足运用了铝散热快和铜吸热快旳特性。
这种塞铜工艺成本适中散热效果也不错,是目前市场上旳主流散热片类型。
3. 压固法也就是将众多旳铜片或铝片叠加起来,然后在两侧加压并将其截面进行抛光,这个截面与CPU关键接触,此外一面则伸展开来作为散热片旳鳍片。
压固法制作旳散热器其特点是鳍片数量可以做旳诸多,并且不需要很高旳工艺就能保证每个鳍片都能与CPU关键保持良好旳接触(或靠近),而各个鳍片之间也通过压固旳方式有着紧密旳接触,彼此之间旳热量传导损失也会明显减少,正是由于压固法制作旳散热器拥有众多旳鳍片,这种散热器旳散热效果往往不错,重量则比老式旳散热器要轻旳多。
4. 铸造式散热片铸造工艺就是将铝块加热后运用高压充斥模具内而形成旳,它旳长处是鳍片高度可以到达50mm以上,厚度1mm如下,可以在相似旳体积内得到最大旳散热面积,并且铸造轻易得到很好旳尺寸精度和表面光洁度。
但铸造时,因金属旳塑性低,变形时易产生开裂,变形抗力大,需要大吨(500吨以上)位旳锻压机械,也正由于设备和模具旳高昂费用而导致产品成本极高,连许多超频发热友都无福消受。
散热片种类与作用

03
铝合金
具有良好的导热性能和加 工性能,成本较低,广泛 用于电子设备散热。
铜
具有优良的导热性能和电 气性能,但成本较高,主 要用于高端散热设备和特 殊需求。
钢
强度高、耐腐蚀,但导热 性能相对较差,主要用于 对散热要求不高的设备或 特殊场合。
根据设备需求选择合适的散热片类型
01
02
03
04
平片散热器
注意散热片的安装与维护
01
02
03
04
确保散热片与发热源紧密接触 ,保证热传导效果。
注意散热片的安装方向和空气 流动方向,确保散热片能够有
效地将热量排出。
定期清洁散热片和周围环境, 防止灰尘和杂物影响散热效果
。
对于液冷散热器,需要定期检 查管路和密封件是否泄漏或损 坏,以确保安全和散热效果。
05
优点
散热效率极高,适用于高负荷下的散热。
缺点
结构复杂,成本高,维护困难。
热管散热片
优点
散热效率高,适用于各种负荷下的散 热。
缺点
成本较高,且需要特殊的安装环境。
03
散热片的作用
降低温度
散热片的主要作用是降低电子设备内部产生的热量,通过自然对流或强制对流的方 式将热量传递到外部环境中。
散热片通常由导热性能良好的材料制成,如铜、铝等,能够快速地将热量从电子元 件传递到散热片上,进而散发到空气中。
散热片的发展趋势与未来展望
高性能化
总结词
随着科技的不断发展,对散热片性能的要求也越来越高,高性能化的散热片能够满足高功率、高发热 电子设备的需求。
详细描述
高性能化的散热片通常采用先进的材料和设计,如金属基复合材料、纳米材料等,以提高散热效率、 降低热阻、减小体积和重量。这些高性能散热片广泛应用于计算机、通信、航空航天等领域。
- 1、下载文档前请自行甄别文档内容的完整性,平台不提供额外的编辑、内容补充、找答案等附加服务。
- 2、"仅部分预览"的文档,不可在线预览部分如存在完整性等问题,可反馈申请退款(可完整预览的文档不适用该条件!)。
- 3、如文档侵犯您的权益,请联系客服反馈,我们会尽快为您处理(人工客服工作时间:9:00-18:30)。
(1)零組件簡介
所需零組件共計9項:
鰭片(Fin)
1.
底板(Base)
2.
上蓋(Cover)
3.
黏著劑(epoxy or solder)
4.
扣具(Clip)
5.
6.
導熱墊片(Thermal Pad)
風扇(Fan)
7.
螺絲(Screw)
8.
9.
包裝材(Package)
項次 零件名稱 圖 片 展 示 說 明 檢測儀器/方法備註
-1-
01 鰭片
(F i n)
1. 此零件有Epoxy用和Solder用
2. Epoxy用零件為使用鋁片為基材,
經沖床或折Fin機折疊加工而成,
後續又加以使用超音波進行洗淨。
3. Solder用零件為使用鋁片為基材,
經沖床或折Fin機折疊加工而成,
後續又加以電鍍處理。
4. 主要作用-- 增加散熱面積。
1. 零件入廠時,依圖面檢驗。
2. 尺寸檢驗--
使用游標卡尺、投影機量測
3. Solder--
必須要做表面沾錫試驗。
電鍍膜厚90-150 micro-inch
依機種的
需求,而
有不同的
鰭片。
02 底板
(B a s e)
1. 此零件有Epoxy用和Solder用
2. Epoxy用零件為使用鋁板或銅板
為基材,經沖床沖製加工而成,
後續又經陽極處理而成。
3. Solder用零件為使用鋁板或銅板
為基材,經沖床沖製加工而成,
後續又經電鍍處理而成。
4. 主要作用-- 接觸CPU之發熱源及
當作FIN的黏著基座。
1. 零件入廠時,依圖面檢驗。
2. 尺寸檢驗--
使用游標卡尺、投影機量測
3. Solder--
必須要做表面沾錫試驗。
電鍍膜厚90-150 micro-inch
依機種的
需求,而
有不同的
底板。
03 上蓋
(C o v e r)
1. 此零件為使用鋁片為基材,
經沖床沖製加工,後續又經
陽極處理而成。
2. 主要作用-- 提供固定風扇的基座。
1.零件入廠時,依圖面檢驗。
2. 尺寸檢驗--
使用游標卡尺、投影機量測
依機種的
需求,而
有不同的
上蓋。
項次 零件名稱 圖 片 展 示 說 明 檢測儀器/方法備註
-2-
-3-
04 黏著劑
1. 此零件有Epoxy 用和Solder 用
2. Epoxy 用 — 使用Epoxy282
3. Solder 用 — 使用錫膏
4. 主要作用-- 底板和鰭片之間黏著物 1.零件入廠時,作樣品比對。
依機種的需求,而
有不同的黏著劑。
05
扣具
(C l i p )
1.此零件為使用彈簧鋼或不銹鋼為 基材,經沖床沖製加工而成,後 續又經電鍍處理而成。
2. 主要作用-- 使底板接觸CPU 發熱 源及夾持散熱片。
1. 零件入廠時,依圖面檢驗。
2. 尺寸檢驗--
使用游標卡尺、投影機量測3. 壓力測試-- 使用拉力試驗機
依機種的需求,而有不同的扣具。
06
導熱墊片 (T h e r m a l P a d )
1. 主要作用-- 使底板底部接觸CPU
發熱源,並填補兩接
觸面間之微小空隙,
以減少熱的傳導阻。
1.零件入廠時,依圖面檢驗。
2. 尺寸檢驗-- 使用游標卡尺量測。
依機種的
需求,而
有不同的
導熱墊
片。
項次 零件名稱 圖 片 展 示 說 明 檢測儀器/方法備註
07 風扇
(F a n)
1. 主要作用-- 使散熱片中所蘊存的
熱量,能快速散至空
氣中。
1. 零件入廠時,依圖面檢驗。
2. 尺寸檢驗--
使用游標卡尺、投影機量測
3. 轉速檢驗--
使用轉速計。
4. 電性特性--
使用電源供應器。
依機種的
需求,而
有不同的
風扇。
08 螺絲
(S c r e w)
1. 主要作用-- 固定風扇於上蓋上。
1. 零件入廠時,依圖面檢驗。
2. 尺寸檢驗--
使用游標卡尺、牙規。
09 包裝材
(P a c k a g e)
1. 此零件為使用瓦楞紙板為基材,
經剪床裁剪加工而成,後續又經
印刷及鉚合(或貼合)處理而成。
2. 主要作用-- 裝置散熱片及保護產
品運輸當中之完整性。
1. 零件入廠時,依圖面檢驗。
2. 尺寸檢驗
--使用捲尺
依機種的
需求,而
有不同的
包裝材。
-4-
(4).生產線組裝流程解說
項次 工站名稱 圖片 展示 說 明 檢測儀器/方法 備註
01 拿鰭片(Fin) 拿出欲組裝的鰭片,準備放置於
黏合治具上。
1.由生產線組裝人員進行
自主檢驗,是否有變形、
污損、等……現象產生。
2.製程檢驗人員定時進行抽驗
02 放置於
黏合治具
將鰭片放置於黏合治具上。
1.由生產線組裝人員進行
自主檢驗,是否有放置不良
少放、未定位等……現象
產生。
2.製程檢驗人員定時進行抽驗
03 上膠
(E p o x y)
(S o l d e r)
使用鋼板印刷方式,將黏著劑刷
印於鰭片上。
1.由生產線組裝人員進行
自主檢驗,是否有上膠不良
溢膠、上膠不平均等……
現象產生。
2.製程檢驗人員定時進行抽驗
-9-
項次 工站名稱 圖片 展示 說 明 檢測儀器/方法 備註
04 放置底板
(BASE)
將底板置於黏合治具上之規定
區域。
1.由生產線組裝人員進行
自主檢驗,是否有置放不良
偏移、為定位等……
現象產生。
2.製程檢驗人員定時進行抽驗
05 夾上夾具 將黏合治具用夾具固定。
1.由生產線組裝人員進行
自主檢驗,是否有夾持位置 錯誤等……現象產生。
2.製程檢驗人員定時進行抽驗
06 烘烤 使用隧道式烘烤爐將黏著劑烘
乾。
1.製程檢驗人員定時進行檢視
溫度,是否有在規定的溫度
範圍內。
-10-
項次 工站名稱 圖片 展示 說 明 檢測儀器/方法 備註
07 拆下夾具 將挾持夾具拆下 1.由生產線組裝人員自行
將拆下的夾具放置規定位置內。
08 拆下治具 將黏合治具拆下並和成品分離 1.由生產線組裝人員進行
自主檢驗,是否有變形、 脫落等……現象產生。
2.製程檢驗人員定時進行抽驗
拉力試驗--使用拉力試驗機上膠厚度--使用實體顯微鏡
09 黏 貼
(Thermal
Pad)
將Thermal Pad黏貼於底板底部
1.由生產線組裝人員進行
自主檢驗,是否有貼歪斜、
脫落等……現象產生。
2.製程檢驗人員定時進行抽驗
位置檢驗--使用游標卡尺
-11-
項次 工站名稱 圖片 展示 說 明 檢測儀器/方法 備註
10 放置扣具
(C l i p)
將扣具置於規定區域內。
1.由生產線組裝人員進行
自主檢驗,是否有放置
錯誤、少放等……現象
產生。
2.製程檢驗人員定時進行抽驗
11 組合上蓋
(兼鉚合)
將上蓋跟底板組合,並且
鉚合於底板。
1.由生產線組裝人員進行
自主檢驗,是否有鉚合
不良、錯誤等……現象
產生。
2.製程檢驗人員定時進行抽驗
尺寸檢驗--使用游標卡尺
12 電腦油墨
噴印或貼
出貨標籤
將型號、日期噴印於規定區
域內。
1.由生產線組裝人員進行
自主檢驗,是否有歪斜、
脫落、模糊等……現象
產生。
2.製程檢驗人員定時進行抽驗
-12-
項次 工站名稱 圖片 展示 說 明 檢測儀器/方法 備註
13 組裝風扇
(F a n)
將風扇鎖於上蓋上。
1.由生產線組裝人員進行
自主檢驗,是否有鎖歪、
滑牙、掉落等……現象
產生。
2.製程檢驗人員定時進行抽驗
14 進行包裝 將產品包裝。
1.由生產線組裝人員進行
自主檢驗,是否有包裝
不良、紙箱破損等……
現象產生。
2.製程檢驗人員定時進行抽驗
-13-
(5).所需相關設備清冊
項 次設 備 名 稱項 次設 備 名 稱
01 隧道式烘烤爐10 空氣壓縮機
02 印刷平台11 乾燥機
03 鋼板12 拉力試驗機
04 攪拌機13 投影機
05 油墨噴印機14 實體顯微鏡
06 黏合治具15 小型輸送帶
07 扣合夾具16 鉚合壓床
08 刮刀17 貼pad 治具
09 鉚合用沖床
-14-。