AGV自动导引小车结构系统全设计
AGV自动导引小车的设计
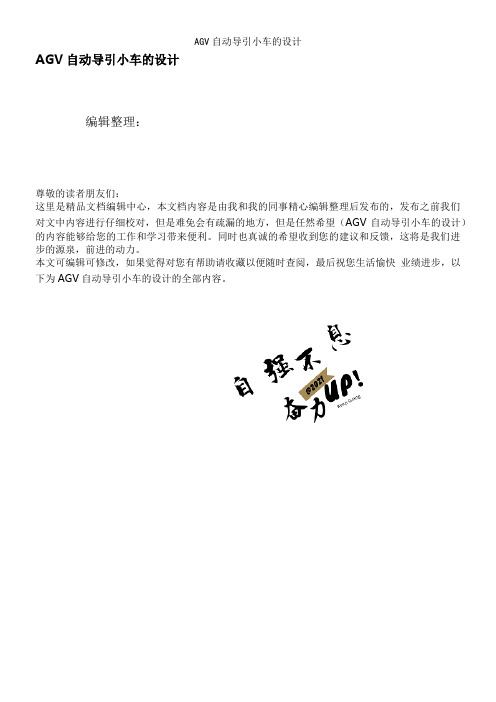
AGV自动导引小车的设计编辑整理:尊敬的读者朋友们:这里是精品文档编辑中心,本文档内容是由我和我的同事精心编辑整理后发布的,发布之前我们对文中内容进行仔细校对,但是难免会有疏漏的地方,但是任然希望(AGV自动导引小车的设计)的内容能够给您的工作和学习带来便利。
同时也真诚的希望收到您的建议和反馈,这将是我们进步的源泉,前进的动力。
本文可编辑可修改,如果觉得对您有帮助请收藏以便随时查阅,最后祝您生活愉快业绩进步,以下为AGV自动导引小车的设计的全部内容。
XXXXXXX毕业设计题目 AGV自动导引小车的设计英文题目the Design of AGV AutomaticGuided Vehicles院系专业姓名年级指导教师二零一五年六月本科生毕业论文(设计)独创性声明本人声明所呈交的毕业论文(设计)是本人在导师指导下进行的研究工作及取得的研究成果,除了文中特别加以标注和致谢的地方外,本论文中没有抄袭他人研究成果和伪造数据等行为。
本科毕业设计答辩稿与学校提交的相似度检测文本完全一致。
论文(设计)作者签名:日期:指导教师签名:日期:本科生毕业论文(设计)使用授权声明九江学院有权保留并向国家有关部门或机构送交毕业论文(设计)的复印件和磁盘,允许毕业论文(设计)被查阅和借阅。
本人授权九江学院可以将本科毕业论文(设计)的全部或部分内容编入有关数据库进行检索,可以采用影印、缩印或其他复印手段保存、汇编毕业论文(设计)。
论文(设计)作者签名:日期:指导教师签名:日期:摘要AGV是自动导引小车(Automated Guided Vehicle)的英文缩写。
它是指电磁或光学自动导引装置的设备,能按照规定的行驶路径,并具有安全保护功能的作用。
本次设计主要对自动导引小车的发展历史、种类以及小车结构设计和小车的技术参数进行说明,提出AGV导引小车设计的研究内容;然后说明自动导引小车总体设计,对于传感器的选用及规格参数也进行详细的论述及说明;在自动导引小车的机械设计部分中对车轮轴和轴承的选取和校核进行了比较全面的分析,这也是本次设计的主要部分,然后再从小车的结构出发,用Pro/E对小车进行三维建模,详细伺服驱动电动机的选取,齿轮的设计与选取,还有驱动方式和车轮的选择,最后说明传感器的布置;接着对自动导引小车的驱动系统和行驶过程也进行了比较全面的分析论述,分析小车在行驶过程中的驱动力、行驶阻力、行驶的附着条件与附着率,以及主减速比的选择和电源部分选择,这些都用来提高小车的性能;最后说明本次设计的结论和展望。
自动导引小车AGV的结构设计及自主移动规划
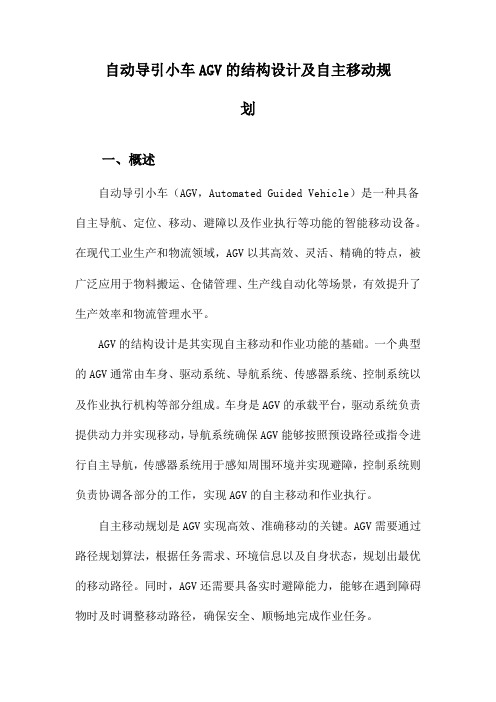
自动导引小车AGV的结构设计及自主移动规划一、概述自动导引小车(AGV,Automated Guided Vehicle)是一种具备自主导航、定位、移动、避障以及作业执行等功能的智能移动设备。
在现代工业生产和物流领域,AGV以其高效、灵活、精确的特点,被广泛应用于物料搬运、仓储管理、生产线自动化等场景,有效提升了生产效率和物流管理水平。
AGV的结构设计是其实现自主移动和作业功能的基础。
一个典型的AGV通常由车身、驱动系统、导航系统、传感器系统、控制系统以及作业执行机构等部分组成。
车身是AGV的承载平台,驱动系统负责提供动力并实现移动,导航系统确保AGV能够按照预设路径或指令进行自主导航,传感器系统用于感知周围环境并实现避障,控制系统则负责协调各部分的工作,实现AGV的自主移动和作业执行。
自主移动规划是AGV实现高效、准确移动的关键。
AGV需要通过路径规划算法,根据任务需求、环境信息以及自身状态,规划出最优的移动路径。
同时,AGV还需要具备实时避障能力,能够在遇到障碍物时及时调整移动路径,确保安全、顺畅地完成作业任务。
对AGV的结构设计及自主移动规划进行研究,不仅有助于提升AGV的性能和稳定性,还有助于推动工业生产和物流领域的自动化、智能化发展。
本文将从AGV的结构设计和自主移动规划两个方面进行深入探讨,为AGV的研发和应用提供有益的参考和借鉴。
1. AGV的定义与功能自动导引小车(Automated Guided Vehicle,简称AGV)是一种装备有电磁或光学等自动导引装置,能够沿规定的路径自动行驶,具有安全保护以及各种移载功能的运输车。
AGV是现代物流系统中的一种高效、灵活、智能的运输设备,广泛应用于制造业、仓储业、港口、机场等领域。
运输功能:AGV能够根据系统指令,自动将物料或产品从起点运输到终点,完成物料的搬运工作。
AGV的载重能力可以根据实际需求进行选择,从几百公斤到几吨不等。
导航功能:AGV通过内置的导航系统,如激光导航、电磁导航、视觉导航等,实现精确的路径规划和跟踪。
AGV整体集成系统结构设计
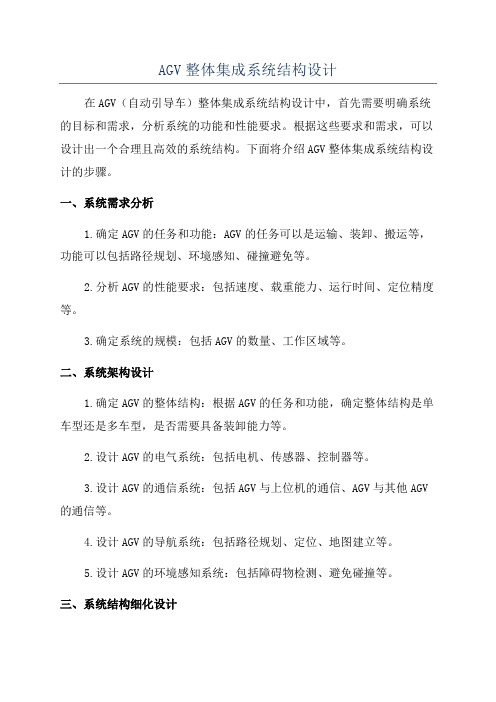
AGV整体集成系统结构设计在AGV(自动引导车)整体集成系统结构设计中,首先需要明确系统的目标和需求,分析系统的功能和性能要求。
根据这些要求和需求,可以设计出一个合理且高效的系统结构。
下面将介绍AGV整体集成系统结构设计的步骤。
一、系统需求分析1.确定AGV的任务和功能:AGV的任务可以是运输、装卸、搬运等,功能可以包括路径规划、环境感知、碰撞避免等。
2.分析AGV的性能要求:包括速度、载重能力、运行时间、定位精度等。
3.确定系统的规模:包括AGV的数量、工作区域等。
二、系统架构设计1.确定AGV的整体结构:根据AGV的任务和功能,确定整体结构是单车型还是多车型,是否需要具备装卸能力等。
2.设计AGV的电气系统:包括电机、传感器、控制器等。
3.设计AGV的通信系统:包括AGV与上位机的通信、AGV与其他AGV 的通信等。
4.设计AGV的导航系统:包括路径规划、定位、地图建立等。
5.设计AGV的环境感知系统:包括障碍物检测、避免碰撞等。
三、系统结构细化设计1.根据AGV的整体结构,确定每个子系统的具体组成和功能。
2.设计AGV的控制系统:包括运动控制、任务调度等。
3.设计AGV的传感器系统:包括位置传感器、距离传感器等。
4.设计AGV的通信系统:包括通信协议、通信接口等。
5.设计AGV的软件系统:包括路径规划算法、碰撞避免算法等。
四、系统实现和测试1.按照设计完成AGV的硬件和软件开发。
2.进行系统集成测试,验证各子系统的功能和性能。
3.进行实际环境下的系统测试,调整系统参数和算法,提高系统的稳定性和可靠性。
五、系统优化和改进1.根据实际运行情况和用户的反馈,对系统进行优化和改进。
2.优化系统性能,提高AGV的行驶速度和定位精度。
3.发现和修复系统中的故障和缺陷,提高系统的稳定性和可靠性。
以上是AGV整体集成系统结构设计的主要步骤,每个步骤中都需要进行详细的设计,并根据实际情况进行调整和改进。
通过合理的系统结构设计,可以最大程度地满足AGV的需求和性能要求,提高AGV的效率和工作质量。
固定路径自动引导车(AGV)的控制系统设计

固定路径自动引导车(AGV)的控制系统设计摘要随着工厂自动化、计算机集成制造系统技术的逐步发展以及柔性制造系统、自动化立体仓库的广泛应用,AGVA(utomatieGuidedVehiele)即自动导引车作为联系和调节离散型物流系统以使其作业连续化的必要的自动化搬运装卸手段,其应用范围和技术水平得到了迅猛的发展。
AGV是以微控制器为控制核心、蓄电池为动力、装有非接触导引装置的无人驾驶自动导引运载车,其自动作业的基本功能是导向行驶、认址停准和移交载荷。
作为当代物流处理自动化的有效手段和柔性制造系统的关键设备,AGV已经得到了越来越广泛的应用,对AGV的研究也具有十分重要的理论意义和现实意义。
发展现状作出综述,系统地分析了自动导引车的特点、类型和技术组成,并对关键技术加以进一步的说明.本课题设计了一辆自动导引车,进行了系统总体设计,利用反射式光电红外收发管作为AGV(Automated Guided Vehicle)寻航检测装置,蓄电池和直流马达作为驱动装置,舵机作为方向控制装置,用单片机作为控制器来控制各个模块协同工作,以实现自动导引车自动导航。
关键词:单片机,AGV,红外传感器,PIDA fixed path Automatic Guided Vehicle (AGV) control systemdesignAbstractAs the factory automation, computer integrated manufacturing systems technology, as well as the progressive development of flexible manufacturing systems, automated warehouse extensive use, AGVA (utomatieGuidedVehiele) is automatically guided vehicle as an associate and regulation of discrete logistics system to make it necessary for continuous operation automated transport loading and unloading means, its scope of application and level of technology has seen rapid development.AGV is a micro-controller to control the core, battery-powered, equipped with a non-contact guiding devices, unmanned automatic guided transport vehicles, its automatic operation’s basic function is to guide traffic and identifying potential sites and the transfer of load to stop。
AGV自动导引小车结构系统全设计
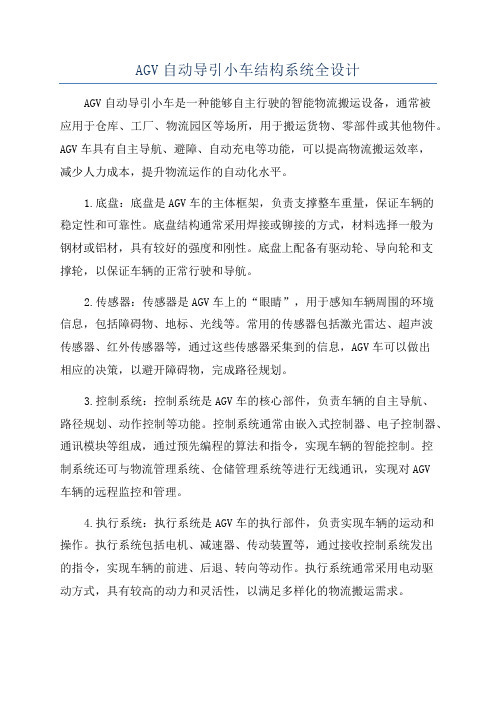
AGV自动导引小车结构系统全设计AGV自动导引小车是一种能够自主行驶的智能物流搬运设备,通常被应用于仓库、工厂、物流园区等场所,用于搬运货物、零部件或其他物件。
AGV车具有自主导航、避障、自动充电等功能,可以提高物流搬运效率,减少人力成本,提升物流运作的自动化水平。
1.底盘:底盘是AGV车的主体框架,负责支撑整车重量,保证车辆的稳定性和可靠性。
底盘结构通常采用焊接或铆接的方式,材料选择一般为钢材或铝材,具有较好的强度和刚性。
底盘上配备有驱动轮、导向轮和支撑轮,以保证车辆的正常行驶和导航。
2.传感器:传感器是AGV车上的“眼睛”,用于感知车辆周围的环境信息,包括障碍物、地标、光线等。
常用的传感器包括激光雷达、超声波传感器、红外传感器等,通过这些传感器采集到的信息,AGV车可以做出相应的决策,以避开障碍物,完成路径规划。
3.控制系统:控制系统是AGV车的核心部件,负责车辆的自主导航、路径规划、动作控制等功能。
控制系统通常由嵌入式控制器、电子控制器、通讯模块等组成,通过预先编程的算法和指令,实现车辆的智能控制。
控制系统还可与物流管理系统、仓储管理系统等进行无线通讯,实现对AGV车辆的远程监控和管理。
4.执行系统:执行系统是AGV车的执行部件,负责实现车辆的运动和操作。
执行系统包括电机、减速器、传动装置等,通过接收控制系统发出的指令,实现车辆的前进、后退、转向等动作。
执行系统通常采用电动驱动方式,具有较高的动力和灵活性,以满足多样化的物流搬运需求。
综上所述,AGV自动导引小车的结构系统设计是一个复杂而精密的工程,需要整合底盘、传感器、控制系统、执行系统等多个部件,确保车辆具有良好的稳定性、可靠性和智能性。
未来随着智能物流技术的不断发展和应用,AGV车将会越来越普及,成为物流搬运领域的重要工具。
AGV自动导引小车结构系统全设计

AGV自动导引小车结构系统全设计引言AGV(Automated Guided Vehicle,即自动导引车)是指通过感应、识别或该车上安装的导航装置自动行驶的无人搬运车辆。
因其可靠、效率高等优点,被广泛应用于物流、制造、医药等领域。
本文旨在介绍AGV自动导引小车的结构设计方案。
AGV结构设计底盘AGV底盘是AGV的核心部位,主要包括车轮、电机、减速机、底盘板等组成。
底盘板是AGV底盘的承载物,一般使用铝合金材料制作,极为坚固。
车轮和电机组成了小车的驱动系统,根据小车的载重量和行驶路面情况来选型。
感应装置AGV的感应装置包括激光导航、地磁导航、视觉导航等系统。
比较常用的是激光导航。
AGV底盘上安装了激光传感器,利用激光雷达扫描环境,并通过预设的地图实现路径规划。
控制器AGV的控制器主要由单片机和驱动电路组成。
单片机采用高性能控制器,可对底盘、感应装置、电机等进行控制,实现车辆的自动化控制。
驱动电路负责将单片机的指令转换为电机控制信号,驱动车轮和减速机的正常运转。
能源装置AGV的能源装置包括电池、供电系统等组成。
电池可选择干电池或锂电池,也可以根据具体使用环境选择太阳能电池、燃料电池等其他新型电池。
附件装置附件装置包括保护装置、报警装置、码表、标志等。
保护装置主要是为了保护AGV在行驶过程中不受到损伤,报警装置主要是为了保证人员和设备的安全。
码表和标志用于标识AGV通过的位置和行驶方向。
,AGV自动导引小车的结构设计是非常重要的,它关乎到自动导引小车的运动性能、控制性能、载重能力等多个方面。
通过合理的层次结构,可以使AGV铰接点处变得更加稳定、方便,整机的使用寿命更加延长。
因此,在设计过程中,需要根据具体使用环境和需求,选用合适的材料和设备,以达到最优的效果。
机电一体化课程设计 自动导引小车(AGV)设计方案
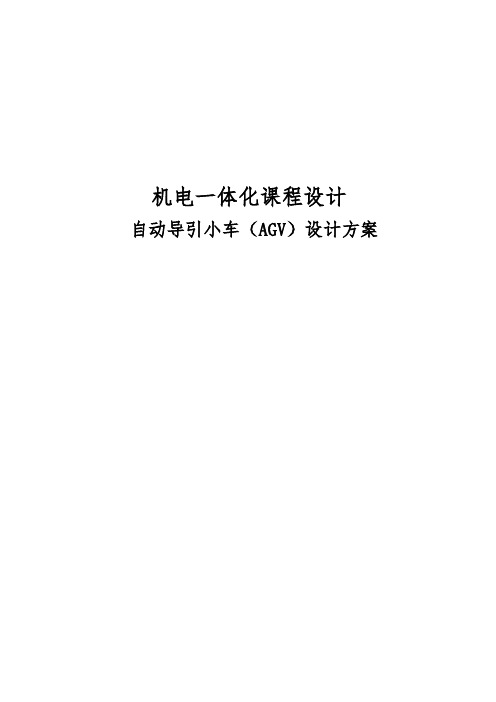
机电一体化课程设计自动导引小车(AGV)设计方案目录一、绪论............................................. - 4 -1.1 AGV概述....................................... - 4 -1.2 AGV国内外研究现状............................. - 6 -1.3 AGV的应用范围:............................... - 9 -1.4 AGV的发展趋势分析:.......................... - 11 -1.5 AGV的市场前景分析:.......................... - 12 -二、总体方案设计.................................... - 14 -2.1 设计方案概述: ................................ - 14 -2.2 传感器部分初步设计:........................... - 14 -2.3 机械结构及驱动部分初步设计:................... - 14 -2.4 控制部分初步设计: ............................ - 15 -三、传感器部分设计.................................. - 18 -四、机械结构及驱动部分设计.......................... - 20 -4.1车体的设计:................................... - 20 -4.2车轮及转向装置选择:........................... - 20 -4.3电机的选择:................................... - 21 -4.4驱动部分校核计算:............................. - 24 -4.5蓄电池的选择:................................. - 25 -4.6总体机械结构设计及建模: ........................ - 27 -五、控制部分设计.................................... - 30 -5.1电源模块:..................................... - 30 -5.2驱动模块....................................... - 30 -5.3循迹模块....................................... - 32 -5.4避障模块....................................... - 33 -5.5主控制模块..................................... - 34 -六、项目总结与感悟.................................. - 37 -七、参考文献........................................ - 39 -八、附录............................................ - 40 -8.1 车体结构ANSYS仿真报告: ........................ - 40 -Project ............................................. - 40 -Contents .......................................... - 41 -Units ............................................. - 41 -Model (C4) ........................................ - 41 -Geometry ......................................... - 41 -Coordinate Systems ............................... - 53 -Connections ...................................... - 54 -Mesh ............................................. - 68 -Static Structural (C5) ............................ - 70 -Solution (C6) .................................... - 73 -Material Data ..................................... - 74 -Structural Steel ................................. - 75 -8.2 单片机控制程序: ............................... - 76 -一、绪论1.1 AGV概述(1)AGV的简介:根据美国物流协会定义,AGV(Automated Guided Vehicle)是指装备有电磁或光学导引装置,能够按照规定的导引路线行驶,具有小车运行和停车装置、安全保护装置以及具有各种移载功能的运输小车。
AGV自动导引小车结构系统全设计-图文

AGV自动导引小车结构系统全设计-图文自动导引小车(Automated Guided Vehicle,AGV)是一种能自主导航、运送物品并完成特定任务的智能机器人。
它可以在仓储物流、制造业、医疗设备、机场等领域广泛应用,提高工作效率和生产效益。
下面将详细介绍AGV自动导引小车的结构系统设计。
车体部分:AGV的车体设计通常采用框架结构,以提供支撑和保护内部组件。
车体采用轻量化材料制造,如铝合金或碳纤维复合材料,以提高车体的强度和刚性,同时保持车体的轻便性。
车体上还设有各种接口和支架,以便安装和固定其他组件和设备。
导航系统部分:AGV的导航系统是控制AGV自主导航的重要组成部分。
常见的导航系统包括激光导航、视觉导航和磁导航等。
激光导航是利用安装在AGV上的激光传感器扫描周围环境,结合预先建立的地图进行定位和导航。
视觉导航是通过安装摄像头和图像处理算法,实时识别环境中的标记物或参考物进行导航。
磁导航是在地面上铺设磁性条纹或导线,AGV感应到这些条纹或导线并进行导航。
控制系统部分:AGV的控制系统负责指导和控制AGV完成特定任务。
控制系统包括主控制器、编码器、驱动器和电机等。
主控制器是AGV的大脑,接收导航系统和传感器系统的信息,并进行路径规划和任务分配。
编码器用于测量车轮转速和转向角度等数据,从而精确控制车辆的运动。
驱动器和电机负责提供动力和驱动车轮转动。
能源系统部分:AGV的能源系统主要是供电系统。
通常采用电池作为能源,其容量根据车辆的负载和工作时间进行选择。
电池需要能够长时间供电,同时体积小、重量轻,以确保AGV的灵活性和运行时间。
传感器系统部分:AGV的传感器系统用于感知周围环境和识别物体等。
常见的传感器包括激光传感器、摄像头、超声波传感器和接近传感器等。
这些传感器可以提供准确的环境信息,帮助AGV进行导航、避障和物品识别等。
以上就是AGV自动导引小车结构系统的设计。
通过合理的设计和配置,AGV可以实现自主导航、物品运输和完成特定任务。
- 1、下载文档前请自行甄别文档内容的完整性,平台不提供额外的编辑、内容补充、找答案等附加服务。
- 2、"仅部分预览"的文档,不可在线预览部分如存在完整性等问题,可反馈申请退款(可完整预览的文档不适用该条件!)。
- 3、如文档侵犯您的权益,请联系客服反馈,我们会尽快为您处理(人工客服工作时间:9:00-18:30)。
第二章 机械部分设计2.1设计任务设计一台自动导引小车AGV ,可以在水平面上按照预先设定的轨迹行驶。
本设计采用AT89C51单片机作为控制系统来控制小车的行驶,从而实现小车的左、右转弯,直走,倒退,停止功能。
其设计参数如下:自动导引小车的长度:500mm 自动导引小车的宽度:300mm 自动导引小车的行驶速度:100mm/s2.2确定机械传动方案 2.3直流伺服电动机的选择伺服电动机的主要参数是功率(KW)。
但是,选择伺服电动机并不按功率,而是更根据下列三个指标选择。
运动参数:AGV 行走的速度为100mm/s ,则车轮的转速为πd 10001000622.75min 3.14140v n r ⨯==≈⨯ (2-1) 电机的转速选择蜗轮-蜗杆的减速比 i=626222.751410.5min n in r ==⨯=电 (2-2)自动导引小车的受力分析:图2-3 车轮受力简图小车车架自重为P 3ρ 2.85100.50.30.0329.8134P abhg N ==⨯⨯⨯⨯⨯≈ (2-3)小车的载荷为G 359.8343G m g N ==⨯=(2-4) 取坐标系OXYZ 如图2-3所示,列出平衡方程由于两前轮及两后轮关于Y 轴对称,则 A B F F =,C D F F =0zF=∑, 220A C F F P G +--= (2-5)0xM=∑, 0.0750.1720.30C G P F --+⨯⨯= (2-6)解得 157.66A B F F N == 80.84C D F F N == 两驱动后轮的受力情况如图2-4所示:滚动摩阻力偶矩f M 的大小介于零与最大值之间,即m a x 0f M M ≤≤ (2-7)max δ0.006157.660.946==⨯=⋅N M F N m (2-8)其中δ滚动摩阻系数,查表5-2[2],δ=2~10,取δ=6mm 牵引力F 为 max 0.94613.50.072M F N d === (2-9)图2-4 后轮受力 图2-5摩擦系数 µ 牵引力 F N 重物的重力 W N 滚子直径 D mm 传递效率 ŋ 传动装置减速比 1/G1) 求换算到电机轴上的负荷力矩(L T )()19.8••21000L F W D T G μη+=⨯(2-10)13.50.15157.6614019.80.726210000.587N m+⨯=⨯⨯⨯=⋅取η=0.7, W =157.66N , μ=0.152) 求换算到电机轴上的负荷惯性(L J )()2121342L Z J J J J J Z ⎛⎫=+++ ⎪⎝⎭(2-11)()2210.00003490.0047660.0001310.0000604620.000036189⎛⎫=+++ ⎪⎝⎭=⋅kg m 其中 1J 为车轮的转动惯量;2J 为蜗杆的转动惯量;3J 为蜗轮的转动惯量;4J 为蜗轮轴的转动惯量。
3) 电机的选定根据额定转矩和惯量匹配条件,选择直流伺服电动机。
电机型号及参数:MAXON F2260 Ø60mm 石墨电刷 80W21290M J gcm =匹配条件为[3] 2max 361.89L L J J gcm ==max0.251L MJ J << (2-12) 即 361.890.251<<1290⇒0.250.28051<<惯量J 21290361.891651.89M L J J J gcm =+=+= (2-13) 其中M J 为伺服电动机转子惯量故电机满足要求。
4) 快移时的加速性能最大空载加速转矩发生在自动导引小车携带工件,从静止以阶跃指令加速到伺服电机最高转速max n 时。
这个最大空载加速转矩就是伺服电动机的最大输出转矩max T 。
max max 22 3.1440001651.890.9160600.076a n T J J N m t πθ⨯⨯===⨯=⋅⨯ (2-14) 加速时间 440.0190.07a M T T s ==⨯= (2-15) 其中 机械时间常数19M T ms =2.4联轴器的设计由于电动机轴直径为Φ8mm ,并且输出轴削平了一部分与蜗杆轴联接部分轴径为Ф12mm ,故其结构设计如图2-6所示。
图2-6联轴器机构图联轴器采用安全联轴器,销钉直径d 可按剪切强度计算,即[4]d =(2-16)销钉材料选用45钢。
查表5-2[5] 优质碳素结构钢(GB 699-88)45 调质 ≤200mm b σ=637MPa s σ=353MPa s δ=17%Ψ=35% 20.39k MJ m α= 硬度217~255HBS销钉的许用切应力为[]()0.7~0.80.75637477.75B MPa τσ==⨯= (2-17)过载限制系数k 值 查表14-4[4]取k=1.6T=0.321N•m0.646d mm =≈选用d=5mm 满足剪切强度要求。
2.5蜗杆传动设计1.选择蜗杆的传动类型根据GB/T 10085-1988的推荐,采用渐开线蜗杆(ZI)。
2.选择材料蜗杆要求表面硬度和耐磨性较高,故材料选用40Cr 。
蜗轮用灰铸铁HT200制造,采用金属模铸造。
3.蜗杆传动的受力分析 确定作用在蜗轮上的转矩T2按Z=1,估取效率[4]η=0.7,则6662221120.080.79.55109.55109.55102350822.75P P T N mm n n i η⨯=⨯=⨯⨯=⨯⨯=⋅ (2-18)图2-7 蜗轮-蜗杆受力分析各力的大小计算为11212258765.2218t a T F F N d ⨯===≈ (2-19) 21222223508606.6677.5a t T F F N d ⨯===≈ (2-20) 00122tan 20606.66tan 20220.8r r t F F F N ===⨯≈ (2-21) 4.按齿根弯曲疲劳强度进行设计根据开式蜗杆传动的设计准则,按齿根弯曲疲劳强度进行设计。
蜗轮轮齿因弯曲强度不足而失效的情况,多数发生在蜗轮齿数较多或开式传动中。
弯曲疲劳强度条件设计的公式为[4][]221221.53Fa F KT m d Y Y z βσ≥∙ (2-22)确定载荷系数K [4]由于工作载荷较稳定,故取载荷分布不均系数K β=1,由表11-15[4]选取使用系数KA =1.15。
由于转速不高,冲击不大,可取动载系数KV =1.1,则1.151 1.1 1.265A V K K K K β=⋅⋅=⨯⨯= (2-23)由表11-8[4]得,蜗轮的基本许用弯曲应力[]34F MPa σ= 假设 262z = γ=3°10'48",蜗轮的当量齿数22336262.29cos cos 310γ==≈V z z °´48˝(2-24)根据20x =,262.29V z =,从图11-19[4]中可查得齿形系数2 2.3Fa Y =螺旋角系数 310110.9773140βγ=-=-=Y °´48˝°140?(2-25) 231 1.53 1.26523508 2.30.977334.376248m d mm ⨯⨯≥⨯⨯=⨯ 由表11-2[4]得中心距a=50mm 模数m=1.25mm 分度圆直径122.4d mm =23135m d mm =蜗杆头数11z = 直径系数17.92 分度圆导程角γ=3°11′38″ 蜗轮齿数262z = 变位系数20.04x =+5.蜗杆与蜗轮的主要参数与几何尺寸1)蜗杆轴向齿距 3.14 1.253.925a p m m m π==⨯= (2-26) 齿顶圆直径 *11222.4211.2524.9a d d ha m mm =+=+⨯⨯= (2-27) 齿根圆直径()()*11222.421 1.250.25 1.2519.275f d d ha m c mm =-+=-⨯⨯+⨯= (2-28)蜗杆轴向齿厚 113.14 1.25 1.962522a s m mm π==⨯⨯= (2-29)2)蜗轮传动比 2162621z i z === (2-30) 蜗轮分度圆直径 22 1.256277.5d mz mm ==⨯= (2-31) 蜗轮喉圆直径 ()()*222277.521.2510.0480.1a d d m h a x m m=++=+⨯⨯+= (2-32)蜗轮齿根圆直径()()**222277.52 1.2510.040.2574.475f d d m ha x c mm =--+=-⨯⨯-+=(2-33)蜗轮咽喉母圆半径22115080.19.9522g a r a d mm =-=-⨯=(2-34)6.精度等级公差和表面粗糙度的确定考虑到所设计的自动导引小车属于精密传动,从GB/T 10089-1988圆柱蜗杆、蜗轮精度中选择6级精度,侧隙种类为7.热平衡核算由于该蜗轮-蜗杆传动是开式传动,蜗轮-蜗杆产生的热传递到空气中,故无须热平衡计算。
2.6轴的设计 2.6.1前轮轴的设计前轮轴只承受弯矩而不承受扭矩,故属于心轴。
图2-8 前轮轴结构1.求作用在轴上的力自动导引小车的前轮受力,受力如图2-9a)所示。
C F F =180.8440.422C F F F N ==⨯=1´˝=22.轴的结构设计1)拟定轴上零件的装配方案装配方案是:左轮辐板、右轮辐板、螺母、套筒、滚动轴承、轴用弹性挡圈依次从轴的右端向左安装,左端只安装滚动轴承和轴用弹性挡圈。
这样就对各轴段的粗细顺序作了初步安排。
2)根据轴向定位的要求确定轴的各段直径和长度(1)初步选择滚动轴承。
自动导引小车前轮轴只受弯矩的作用,主要承受径向力而轴向力较小,故选用单列深沟球轴承。
由轴承产品目录中初步选取单列深沟球轴承6004,其尺寸为d×D×T=20mm×42mm×12mm ,故20d d d mm ===ⅠⅢⅨ。
右端滚动轴承采用轴肩进行轴向定位。
由手册上查得6004型轴承的定位轴肩高度h=2.5mm ,因此取25d mm =Ⅳ。
(2)取安装左、右轮辐处的轴段Ⅵ的直径30d mm =Ⅵ;轮辐的左端采用轴肩定位,右端用螺母夹紧轮辐。
已知轮辐的宽度为34mm ,为了使螺母端面可靠地压紧左右轮辐,此轴段应略短于轮辐的宽度,故取32l mm =Ⅵ。
左右轮辐的左段采用轴肩定位,轴肩高度0.07h d >,取h=3mm ,则轴环处的直径36V d mm =。
轴环宽度b≥1.4h ,取5V l mm =。