注塑工艺对颜色的影响
注塑缺陷描述及解决方案

注塑缺陷描述及解决方案一、注塑缺陷描述注塑是一种常用的塑料加工方法,但在注塑过程中常会出现一些缺陷。
以下是常见的注塑缺陷描述:1. 气泡:注塑制品表面出现小气泡,影响外观质量。
2. 热缩:制品在注塑后出现尺寸变化,导致尺寸不准确。
3. 热分解:注塑过程中,塑料材料发生热分解,导致制品表面出现黑斑或发黄。
4. 热裂纹:注塑制品在冷却过程中出现裂纹。
5. 短射:注塑模具中未完全填充塑料材料,导致制品缺少部分或完全缺失。
6. 缩痕:注塑制品表面出现凹陷或凸起的痕迹。
7. 毛边:注塑制品边缘出现毛糙或不平整。
8. 色差:注塑制品颜色不均匀或与预期颜色不符。
二、解决方案针对以上注塑缺陷,可以采取以下解决方案:1. 气泡:增加注塑过程中的压力和温度,使用抗气泡添加剂,调整注塑工艺参数。
2. 热缩:优化注塑模具设计,增加冷却系统,控制注塑过程中的温度。
3. 热分解:选择合适的塑料材料,避免过高的注塑温度,加强模具通风。
4. 热裂纹:优化注塑模具设计,增加冷却时间,降低注塑温度。
5. 短射:调整注塑工艺参数,增加注塑压力和速度,优化模具结构。
6. 缩痕:增加注塑压力和温度,调整模具结构,增加冷却时间。
7. 毛边:优化模具设计,增加模具表面光洁度,调整注塑工艺参数。
8. 色差:选择合适的塑料材料,控制注塑温度和时间,使用色母粒。
除了以上解决方案,还可以通过对注塑设备进行维护保养,提高操作人员的技术水平,加强质量检验等措施来预防和解决注塑缺陷问题。
总结:注塑缺陷是在注塑加工过程中常见的问题,但通过合理的解决方案可以有效降低缺陷率,提高注塑制品的质量。
在实际生产中,需要根据具体情况选择合适的解决方案,并进行持续改进和优化,以确保注塑制品的质量和生产效率。
注塑产品的色差控制
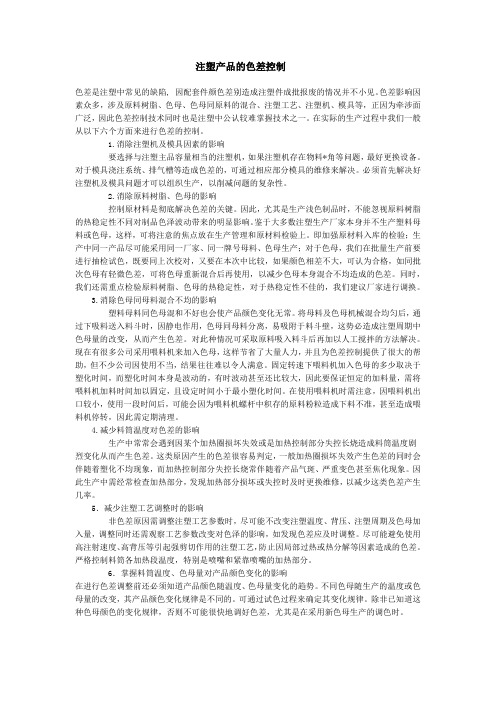
注塑产品的色差控制色差是注塑中常见的缺陷, 因配套件颜色差别造成注塑件成批报废的情况并不小见。
色差影响因素众多,涉及原料树脂、色母、色母同原料的混合、注塑工艺、注塑机、模具等,正因为牵涉面广泛,因此色差控制技术同时也是注塑中公认较难掌握技术之一。
在实际的生产过程中我们一般从以下六个方面来进行色差的控制。
1.消除注塑机及模具因素的影响要选择与注塑主品容量相当的注塑机,如果注塑机存在物料*角等问题,最好更换设备。
对于模具浇注系统、排气槽等造成色差的,可通过相应部分模具的维修来解决。
必须首先解决好注塑机及模具问题才可以组织生产,以削减问题的复杂性。
2.消除原料树脂、色母的影响控制原材料是彻底解决色差的关键。
因此,尤其是生产浅色制品时,不能忽视原料树脂的热稳定性不同对制品色泽波动带来的明显影响。
鉴于大多数注塑生产厂家本身并不生产塑料母料或色母,这样,可将注意的焦点放在生产管理和原材料检验上。
即加强原材料入库的检验;生产中同一产品尽可能采用同一厂家、同一牌号母料、色母生产;对于色母,我们在批量生产前要进行抽检试色,既要同上次校对,又要在本次中比较,如果颜色相差不大,可认为合格,如同批次色母有轻微色差,可将色母重新混合后再使用,以减少色母本身混合不均造成的色差。
同时,我们还需重点检验原料树脂、色母的热稳定性,对于热稳定性不佳的,我们建议厂家进行调换。
3.消除色母同母料混合不均的影响塑料母料同色母混和不好也会使产品颜色变化无常。
将母料及色母机械混合均匀后,通过下吸料送入料斗时,因静电作用,色母同母料分离,易吸附于料斗壁,这势必造成注塑周期中色母量的改变,从而产生色差。
对此种情况可采取原料吸入料斗后再加以人工搅拌的方法解决。
现在有很多公司采用喂料机来加入色母,这样节省了大量人力,并且为色差控制提供了很大的帮助,但不少公司因使用不当,结果往往难以令人满意。
固定转速下喂料机加入色母的多少取决于塑化时间,而塑化时间本身是波动的,有时波动甚至还比较大,因此要保证恒定的加料量,需将喂料机加料时间加以固定,且设定时间小于最小塑化时间。
注塑件和橡胶件外观检验标准

注塑件和橡胶件外观检验标准注塑件和橡胶件外观检验标准注塑件和橡胶件广泛应用于生活中的各种工业制品和消费品中,如手机、电脑、汽车、家具、玩具、家电等。
随着生产技术的不断提高和市场需求的增加,注塑件和橡胶件的外观质量要求也越来越高,需要严格的外观检验标准。
一、注塑件外观检验标准注塑件的外观检验主要包括以下方面:1. 产品尺寸:注塑件的尺寸精度对产品的装配、使用效果和外观质量都有着重要的影响。
在外观检验中应测量每个注塑件的长、宽、高、壁厚、平面度和直线度等尺寸参数,同时还要判断是否符合产品的设计要求和工艺要求。
2. 表面光泽:注塑件的表面光泽直接影响产品的美观度和质感。
在外观检验中应观察注塑件的表面光泽是否均匀、透明、光滑,是否有气泡、流痕、杂色和裂纹等缺陷。
3. 颜色:注塑件的颜色是产品的一个重要设计元素,同样也会直接影响产品的外观质量和市场竞争力。
在外观检验中应判断注塑件颜色是否与设计要求相符,是否有色差、条纹、斑点等缺陷。
4. 表面纹路:注塑件的表面纹路是由模具形状和表面涂料决定的,对产品的外观风格、品质印象和形象表现有着很大的影响。
在外观检验中应观察注塑件的表面纹路是否清晰、细致、对称,是否有错位、漏涂、脱落等缺陷。
5. 计量单位规定的其他要求:注塑件的外观检验还涵盖了其他一些计量单位规定的要求,如凹坑、异物、起泡、磨痕、翘曲等缺陷的判断和评定。
以上是注塑件外观检验的主要标准。
需要强调的是,在检验中应严格按照相应的标准操作,确保检验结果的准确性和公正性。
同时,产品质量问题应及时反馈到生产过程中,采取有效措施加以改进和完善。
二、橡胶件外观检验标准橡胶件的外观检验同样是非常重要的一环,因为橡胶件广泛应用于汽车零部件、机械设备、生活用品等领域,如果外观出现问题,就会直接影响产品的安全性和使用寿命。
橡胶件的外观检验主要包括以下五个方面:1. 外观:橡胶件的外观必须完美,无异物、磨损痕迹、表面气泡、开裂、拉伸变形等现象,同时也必须无橡胶污染等。
注塑品出现颜色问题的原因

注塑品出现颜色问题的原因来源:塑料论坛()一、设备方面(1)设备不干净。
灰尘或其它粉尘沉积在料斗上使物料受污染变色。
(2)热电偶、温控仪或加热系统失调造成温控失灵。
(3)机筒中有障碍物,易促进塑料降解;机筒或螺槽内卡有金属异物,不断磨削使塑料变色。
二、模具方面(1)模具排气不良,塑料被绝热压缩,在高温高压下与氧气剧烈反应,烧伤塑料。
(2)模具浇口太小。
(3)料中或模内润滑剂、脱模剂太多。
必要时应定期清洁料筒,清除比塑料耐热性还差的抗静电性等添加剂。
(4)喷嘴孔、主流道及分流道尺寸太小。
三、工艺方面(1)螺杆转速太高、预塑背压太大。
(2)机筒、喷嘴温度太高。
(3)注射压力太高、时间过长,注射速度太快使制品变色。
四、原料方面(1)物料被污染。
(2)水分及挥发物含量高。
(3)着色剂、添加剂分解。
黑斑或黑液造成这种缺陷的原因主要是在设备和原料方面:一、设备方面(1)机筒中有焦黑的材料。
(2)机筒有裂痕。
(3)螺杆或柱塞磨损。
(4)料斗附近不清洁。
二、模具方面(1)型腔内有油。
(2)从顶出装置中渗入油。
三、原料方面:(1)原料不清洁。
(2)润滑剂不足。
烧焦暗纹一、设备方面:注射热敏性塑料后,机筒未清洗干净或喷嘴处有料垫导致注射开始时排气不畅。
二、模具方面:(1)排气不良。
(2)浇口小或浇口位置不当。
(3)型腔局部阻力大,使料流汇合较慢造成排气困难。
三、工艺方面:(1)机筒、喷嘴温度太高。
(2)注射压力或预塑背压太高。
(3)注射速度太快或注射周期太长。
四、原料方面:(1)颗粒不均,且含有粉末。
(2)原料中挥发物含量高。
(3)润滑剂、脱模剂用量过多。
参考:/thread-45413-1-4.html 中国塑料网:/。
渐变色注塑原理

渐变色注塑原理渐变色注塑原理渐变色注塑技术是一种先进的注塑成型技术,其优点是可以制作出具有渐变颜色的注塑制品,使制品具有更加丰富的色彩层次感,从而在外观上更具吸引力。
渐变色注塑技术在汽车、电子、玩具等领域得到了广泛应用,如汽车仪表盘、手机、电器外壳等制品。
下面就让我们来了解一下渐变色注塑的原理。
1. 渐变色注塑原理渐变色注塑技术主要是在注塑成型过程中通过调控注塑机的色料供给量,使得塑料制品产生颜色逐渐变化的效果。
渐变色注塑制品的颜色转变是由两种或多种颜色的塑料物料注入同一成型模具中,通过控制色料供给的方式实现。
技术最为复杂的是颜料的量渐变和位置渐变两种方法。
2. 渐变色注塑的实现方法(1)颜料量渐变法颜料量渐变法是通过改变塑料颜料的供给量实现渐变色的注塑制品。
对于颜料的供给量,可以通过调节注射机的料量控制阀、调节螺杆的转速和混合块的位置等方式来实现。
需要掌握颜料的温度和颜色之间的关系。
温度高时所使用的颜料浓度不需要太高,否则会导致出现颜色不均。
在此基础上,通过改变颜料供给量使其逐渐变化,同时要确保塑料物料注入模具中的前后颜色能够有足够的平滑转变,从而实现连续和平缓的渐变色。
在实现颜色量渐变的同时还需要考虑颜色位置的转变,从而得到更加具有层次感的渐变色注塑制品。
(2)颜色位置渐变法颜色位置渐变法是一种通过调节模具或注塑机的方式实现渐变色的方法。
该方法需要在模具中设置不同的颜色分隔带,从而使制品颜色位置逐渐转变。
在注塑成型过程中,改变颜色分隔带的位置,以及颜料的供给量和顺序,从而实现颜色位置逐渐变化的效果。
这种方法需要在模具制作中充分考虑颜色位置分隔带的设置,以及注塑机的流量、口径等方面的参数调节,因此较为耗费时间和费用。
3. 渐变色注塑的优势(1)颜色多样通过渐变色注塑技术,制品可以呈现出具有丰富层次、多样的颜色,从而在外观上更具吸引力。
这种技术可以大大提高产品的美观度和装饰性,从而增加产品的市场竞争力。
铃木技术标准SESN3211b
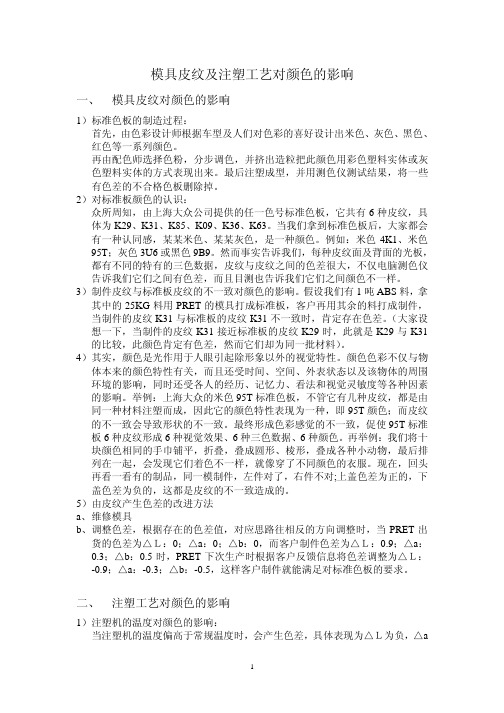
模具皮纹及注塑工艺对颜色的影响一、 模具皮纹对颜色的影响1)标准色板的制造过程:首先,由色彩设计师根据车型及人们对色彩的喜好设计出米色、灰色、黑色、红色等一系列颜色。
再由配色师选择色粉,分步调色,并挤出造粒把此颜色用彩色塑料实体或灰色塑料实体的方式表现出来。
最后注塑成型,并用测色仪测试结果,将一些有色差的不合格色板删除掉。
2)对标准板颜色的认识:众所周知,由上海大众公司提供的任一色号标准色板,它共有6种皮纹,具体为K29、K31、K85、K09、K36、K63。
当我们拿到标准色板后,大家都会有一种认同感,某某米色、某某灰色,是一种颜色。
例如:米色4K1、米色95T;灰色3U6或黑色9B9。
然而事实告诉我们,每种皮纹面及背面的光板,都有不同的特有的三色数据,皮纹与皮纹之间的色差很大,不仅电脑测色仪告诉我们它们之间有色差,而且目测也告诉我们它们之间颜色不一样。
3)制件皮纹与标准板皮纹的不一致对颜色的影响。
假设我们有1吨ABS料,拿其中的25KG料用PRET的模具打成标准板,客户再用其余的料打成制件,当制件的皮纹K31与标准板的皮纹K31不一致时,肯定存在色差。
(大家设想一下,当制件的皮纹K31接近标准板的皮纹K29时,此就是K29与K31的比较,此颜色肯定有色差,然而它们却为同一批材料)。
4)其实,颜色是光作用于人眼引起除形象以外的视觉特性。
颜色色彩不仅与物体本来的颜色特性有关,而且还受时间、空间、外表状态以及该物体的周围环境的影响,同时还受各人的经历、记忆力、看法和视觉灵敏度等各种因素的影响。
举例:上海大众的米色95T标准色板,不管它有几种皮纹,都是由同一种材料注塑而成,因此它的颜色特性表现为一种,即95T颜色;而皮纹的不一致会导致形状的不一致。
最终形成色彩感觉的不一致,促使95T标准板6种皮纹形成6种视觉效果、6种三色数据、6种颜色。
再举例:我们将十块颜色相同的手巾铺平,折叠,叠成圆形、棱形,叠成各种小动物,最后排列在一起,会发现它们着色不一样,就像穿了不同颜色的衣服。
注塑工艺对颜色的影响
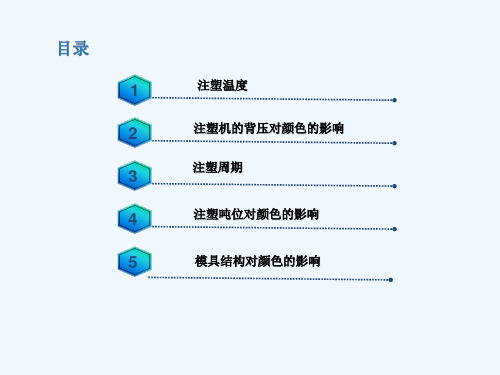
注塑温度
2
注塑机的背压对颜Βιβλιοθήκη 的影响注塑周期34
注塑吨位对颜色的影响
5
模具结构对颜色的影响
色差是注塑中常见的缺陷,色差影响因素众多,涉及 原料树脂、色粉色母、色母同原料的混合、注塑工艺参数 、注塑机型号等等,在实际的生产过程中我们一般从以下 五个方面来进行色差的控制。
2
影响色差的因素
压力
B
温度 A
8
四. 注塑机 因不同品牌的注塑机,其制造结构差别,如料
筒的紧贴程度以及螺杆结构的差别,引起塑料熔化状 态的不同造成着色树脂中颜料分散状态不一样,而形 成着色差异。
9
五 注塑吨位对颜色的影响 (即注塑制件的大小) 注塑机注塑制件越大,色差的偏差越大,因为在颜 色开发及QC检验时,用的都是小型注塑机,打的是小色 板,到了客户那里现场生产成品时,往往会放大,色差 表现为偏深,当有的材料是用原材料加色母生产时,颜 色的放大现象更明显。
10
六.模具结构对颜色的影响 * 模具结构越复杂,要求材料流动性越高。为提高材料流
动性,必须要求注塑机的温度、压力速度调高,备压及 保压周期作相应调整,最终影响颜色的色差。 * 模具结构越复杂,打成的制件饱和度越不一致即制件的 光泽度、皮纹面越不一致,严重影响色差。 如:有的制品同一模制件,左件对了,右件不对;上盖 色差为正的,下盖色差为负的,这都是以上原因造成的
色差
五大因素
C 注塑周期
模具的结构 E
D 注塑机吨位
3
一. 温度
* 不同树脂,不同颜料, 所承受温度也不同,当注塑 机的温度偏高于常规温度时,会产生色差,具体表现为 L* 为负, a*为正, b*为正,即向偏深偏红偏黄发展,如当时 配色造粒采用的色粉不耐温,达不到此温度,此时会出现颜 色偏差放大,甚到会发生变色,褪色
添加剂和注塑工艺对AES颜色稳定性的影响

苯乙烯 共聚物 ( AE S树脂 )的宏观颜色变化 与其橡胶 形态密切相关 ,而橡胶形态受
配方中添加剂组分的影响很大 。另外,注塑工艺也会影 响 A E S注塑样 品的宏观颜色 变化。通过在体系 中加入润滑剂硬脂 酸钙或芥酸酰胺 ,可 以有效地控制 A ES注塑样
品的颜色变化 。
关键 词:A E S ;颜色稳 定性 ;润滑剂 ;注塑工艺 中图分类号 :06 3 1 . 2 4 文献标识码 :A
系 的耐 候性 的作 用 。A E S树 脂 的制 备方 法和 微观 相 结构均 与 A BS相 似 ,基 本物理 性 能也与
AB S相 当【 6 引 。A E S较 A BS的 明显优 势 在于 ,AE S中的橡 胶 组分 几乎 不含 不饱 和双键 ,而 AB S的主 要 成分 是含 大 量不饱 和 双键 的 丁二烯 橡 胶 , 因而 A ES较 A BS有 更好 的光 稳 定性和
表 1 实验材料及 生产厂家
1 . 2 仪 器 C o l o r E y e 7 0 0 0 A色 差 测试 仪 ( 美国G r e t a g Ma c b e t h公 司 ) ;C E M1 0 0 一 C XI I 透 射 电子 显
收稿 日期 :2 0 1 2 . 1 0 . 3 0 作者简介 :聂德林 ( 1 9 7 3 ~ ) ,男,湖北孝感人 ,工程师 ,硕 士;从事改性塑料 的研 究 。 通 讯作者 d u r o n g h u a @k i n g f a . c o m. c n
2 8
广 卅 l化 学
第3 8卷 第 1期
2 0 1 3年 3月
广 州 化 学
Gua n g z h o u Che mi s t r y
- 1、下载文档前请自行甄别文档内容的完整性,平台不提供额外的编辑、内容补充、找答案等附加服务。
- 2、"仅部分预览"的文档,不可在线预览部分如存在完整性等问题,可反馈申请退款(可完整预览的文档不适用该条件!)。
- 3、如文档侵犯您的权益,请联系客服反馈,我们会尽快为您处理(人工客服工作时间:9:00-18:30)。
GWM-PPT V2010.1
6
注塑温度使用表
注塑参考温度
塑料名称 注塑温度/℃ 塑料名称
烘料温度
烘料温度/℃ 烘料时间/分钟
ABS GPPS
200~230 200~220
ABS PA6
80~90 90~100
30~90 60~90
HIPS
PP PC PA66 PA6 PMMA POM LDPE
200~220
GWM-PPT V2010.1
一. 温度
* 生产中常常会遇到因某个加热圈损坏失效,或是热 控 制部分失控长烧造成料筒温度剧烈变化从而产生色差。 这类原因产生的色差很容易判定,一般加热圈损坏失效产 生色差的同时会伴随着塑化不均现象,而加热控制部分失 控长烧常伴随着产品气斑、严重变色甚至焦化现象。因此 生产中需经常检查加热部分,发现加热部分损坏 或失控时 及时更换维修,以减少这类色差产生几率。
8
三.注塑周期
即保压、冷却时间、注塑压力、注塑速度等,都会 对颜色产生影响 (表现同1) 非色差原因需调整注塑工艺参数时,尽可能不改 变注塑温度、背压、注塑周期,调整同时还需观察工艺参 数改变对色泽的影响,如发现色差应及时调整。尽可能避 免使用高注射速度、高背压等引起强剪切作用的注塑工艺 ,防止因局部过热或热分解等因素造成的色差。严格控制 料筒各加热段温度,特别是喷嘴和紧靠喷嘴的加热部分。
讲师:刘建红 课时:45分钟 目的:了解影响色差的因素及解决方法 时间:2012年11月20日
GWM-PPT V2010.1
1
注塑温度 注塑机的背压对颜色的影响 注塑周期
2
3 4
注塑吨位对颜色的影响
5
模具结构对颜色的影响
GWM-PPT V2010.1
色差是注塑中常见的缺陷,色差影响因素众多,涉及 原料树脂、色粉色母、色母同原料的混合、注塑工艺参数
、注塑机型号等等,在实际的生产过程中我们一般从以下 五个方面来进行色差的控制。
GWM-PPT V2010.1
3
影响色差的因素
压力
B
温度
A
色差
C
注塑周期
五大因素
模具的结构
E
D
注塑机吨位
GWM-PPT V2010.1
4
一. 温度 * 不同树脂,不同颜料, 所承受温度也不同,当注塑 机的温度偏高于常规温度时,会产生色差,具体表现为 L* 为负, a*为正, b*为正,即向偏深偏红偏黄发展,如当时 配色造粒采用的色粉不耐温,达不到此温度,此时会出现颜 色偏差放大,甚到会发生变色,褪色 * 在进行色差调整前还必须知道产品颜色随温度、色粉 量变化的趋势。不同色粉随生产的温度或色粉量的改变,其 产品颜色变化规律是不同的。可通过试色打色板等过程来确 定其变化规律。
GWM-PPT V2010.1
12
* 要选择与注塑主品容量相当的注塑机,如果注塑机存
在物料死角等问题,最好更换设备。对于模具浇注系统、 排气槽等造成色差的,可通过相应部分模具的维修模来解
决。必须首先解决好注塑机及模具问题才可以组织生产, 以削减问题的复杂性。
GWM-PPT V2010.1
13
关于本节的思考
* *
*
影响色差的主要因素是什么? 产品出现色差的表现是什么? ABS原料的注塑温度是多少?
GWM-PPT V2010.1
14
GWM-PPT V2010.1
15
7
二 注塑机的压力对颜色的影响 压力可分为注塑压力,保压压力,背压压力,对 色差的影响主要是背压,增大背压会使塑化的料筒 内壁和螺杆表面摩擦剪切作用增强,螺杆摩擦的增 大,对于不耐温的有机颜料及染料会出现变色,具 体表现为 L*为负, a*为正, b*为正,即向偏深偏 红偏黄发展。
GWM-PPT V2010.1
180~210 280~300 250~260 240~250 230~250 190~200 180~190
PA66
PMMA PC POM
90~100
90~100 100~120 80~90
60~90
60~90 60~120 60~90
HPDE
180~190
GWM-PPT V2010.1
汇报人:×××
GWM-PPT V2010.1
9
四. 注塑机 因不同品牌的注塑机,其制造结构差别,如料 筒的紧贴程度以及螺杆结构的差别,引起塑料熔化状 态的不同造成着色树脂中颜料分散状态不一样,而形 成着色差异。
GWM-PPT V2010.1
10
五 注塑吨位对颜色的影响 (即注塑制件的大小)
注塑机注塑制件越大,色差的偏差越大,因为在颜 色开发及QC检验时,用的都是小型注塑机,打的是小色 板,到了客户那里现场生产成品时,往往会放大,色差
表现为偏深,当有的材料是用原材料加色母生产时,颜
色的放大现象更明显。
GWM六.模具结构对颜色的影响 * 模具结构越复杂,要求材料流动性越高。为提高材料流 动性,必须要求注塑机的温度、压力速度调高,备压及
保压周期作相应调整,最终影响颜色的色差。
* 模具结构越复杂,打成的制件饱和度越不一致即制件的 光泽度、皮纹面越不一致,严重影响色差。 如:有的制品同一模制件,左件对了,右件不对;上盖 色差为正的,下盖色差为负的,这都是以上原因造成的