注塑成型常见问题及对策37649
注塑过程中常见的问题及解决方案

注塑过程中常见的问题及解决方案一、飞边(披锋)1. 问题描述- 这飞边就像塑料偷偷长出来的小翅膀,在注塑件的边缘或者分型面那里冒出来,看着可闹心了。
就像好好的一块蛋糕,边缘突然多出了一些不规则的奶油坨坨。
2. 解决方案- 首先得检查模具的合模力。
要是合模力不够,那塑料就会像调皮的小孩从门缝里挤出来。
适当增加合模力,把模具紧紧抱住,让塑料乖乖待在该待的地方。
- 模具的磨损也会导致飞边。
就像穿破了的鞋子会漏脚指头一样,磨损的模具缝隙变大了。
这时候就得修模啦,把那些磨损的地方补一补或者磨平。
- 注塑压力也不能太大。
如果压力太大,塑料就像被大力士猛推的水,到处乱流。
降低注塑压力,找到一个合适的值,既能把模具填满,又不会让塑料溢出来。
二、短射(缺料)1. 问题描述- 短射就像给一个杯子倒水,结果没倒满一样。
注塑件看着不完整,有些地方该有塑料的却空着,就像一个没发育好的小怪物。
2. 解决方案- 先看看注塑压力是不是太小。
压力小的话,塑料就像没力气的小蚂蚁,爬不到模具的每个角落。
增加注塑压力,让塑料充满整个模具型腔。
- 塑料的流动性也很关键。
如果塑料太黏,就像浓稠的糨糊,很难流到模具的远端。
这时候可以提高料筒温度,让塑料变得稀一点,流动性更好,就像把糨糊加热变成稀粥一样,能顺利流到各个地方。
- 浇口尺寸也可能有问题。
要是浇口太小,就像一个小得可怜的水龙头,水流不出来多少。
适当扩大浇口尺寸,让塑料能畅快地流进模具。
三、气泡(气穴)1. 问题描述2. 解决方案- 注塑速度可能太快了。
塑料像一阵风呼呼地冲进模具,把空气都裹在里面了。
降低注塑速度,让塑料慢慢流进去,就像散步一样,这样空气就有机会跑出来了。
- 模具的排气也很重要。
如果模具没有排气孔或者排气不良,空气就被困在里面出不来。
在模具上开排气槽或者使用透气钢材料,给空气一条逃跑的路。
- 塑料干燥不彻底也会产生气泡。
如果塑料里有水份,加热的时候就会变成水蒸气,形成气泡。
注塑成型制品不良现象及解决办法

注塑成型制品不良现象及解决办法一、塑料制品充填不满1、成因:主要是缺料和注射压力与速度不妥(包括阻力造成压力过于耗损)。
2、解决措施:(1)机台方面:机台的塑化量或加热功率不定,应选用塑化量与加热功率大的机台;螺杆与料筒或过胶头等的磨损造成回料而出现实际充模量不中;热电偶或发热圈等加热系统故障造成料筒的实际温度过低;注射油缸的密封元件磨损造成漏油或回流,而不能达到所需的注射压力;射嘴内孔过小或射嘴中心度调节不当造成阻力过大而使压力消耗。
(2)模具方面:①模具局部或整体的温度过低造成入料困难,应适当提高模温;②模具的型腔的分布不平衡。
制件壁厚过薄造成压力消耗过磊而且充模不力。
应增加整个制件或局部的壁厚或可在填充不足处的附近,设置辅助流或浇口解决。
③模具的流道过小造成压力损耗;过大时会出现射胶无力;过于粗糙都会造成制件不满。
应适当设置流道的大小,主流道与分流道,浇口之间的过渡或本身的转弯处应用适当的圆弧过渡。
④模具的排气不良。
进入型腔的料受到来不及排走的气体压力的阻挡而造成充填不满。
可以充分利用螺杆的缝隙排气或降低锁模力利用分型面排气,必要时要开设排气沟道或气孔。
(3)制件不满反复出现的原因:①塑料原料粒度大小悬殊不均时会使加料份量不定。
②螺杆的过胶头、过胶圈及过胶垫圈的磨损过大,使熔料可能在螺杆处经与料筒内之间滑行及回流造成不满。
③入流口的冷却系统失效,使下料量不稳定。
④料筒调定的注料量不足,即缓冲垫过小会使射料时多时少而出现制件不满。
二、飞边1、成因:又称溢边、披锋、毛刺等,大多发生在模具的分合位置上,如动模和静模的分型面,滑块的滑配部位、镶件的绝隙、顶杆孔隙等处,飞边在很大程度上是由于模具或机台锁模力失效造成。
2、解决措施:(1)机台的最高锁模力不够应选用锁模力够的机台。
锁模机铰磨损或锁模油缸密封元件磨损出现滴油或回流而造成锁模力下降。
加温系统失控造成实际温度过高应检查热电偶、加热圈等是否有问题。
注塑成型常见不良及对策
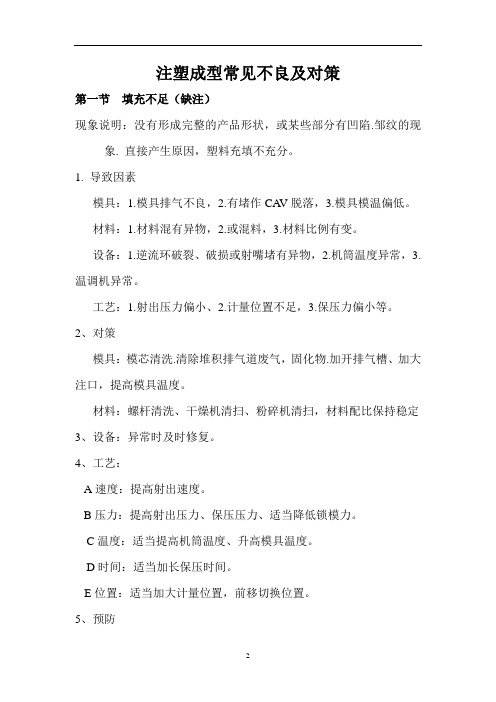
注塑成型常见不良及对策第一节填充不足(缺注)现象说明:没有形成完整的产品形状,或某些部分有凹陷.邹纹的现象. 直接产生原因,塑料充填不充分。
1. 导致因素模具:1.模具排气不良,2.有堵作CA V脱落,3.模具模温偏低。
材料:1.材料混有异物,2.或混料,3.材料比例有变。
设备:1.逆流环破裂、破损或射嘴堵有异物,2.机筒温度异常,3.温调机异常。
工艺:1.射出压力偏小、2.计量位置不足,3.保压力偏小等。
2、对策模具:模芯清洗.清除堆积排气道废气,固化物.加开排气槽、加大注口,提高模具温度。
材料:螺杆清洗、干燥机清扫、粉碎机清扫,材料配比保持稳定3、设备:异常时及时修复。
4、工艺:A速度:提高射出速度。
B压力:提高射出压力、保压压力、适当降低锁模力。
C温度:适当提高机筒温度、升高模具温度。
D时间:适当加长保压时间。
E位置:适当加大计量位置,前移切换位置。
5、预防A、产前模具分解清洗,产后及时防锈保养,生产过程中定时清洗。
B、现场异常处理必须防止金属物掉入螺杆。
C、材料管理操作,不可混料。
D、模具温度、成形条件定时点检。
第二章飞边现象说明:产品外围或内围形成薄膜状、超出完整产品形状。
产生原因:塑料充填过多或模芯缺损、配合间隙大、模芯腐蚀而造成。
1、飞边形成:A、模具本身(设计)缺陷产生飞边。
如:本司“408”B、型修后,配合间隙大,导致飞边。
2、正常量产出现飞边,主要有以下几点:A、材料干燥不充分,导致飞边。
B、产品压模,二次成形造成飞边。
如:本司PDIC BASE,产品压模,合模面受损,导致飞边。
C、模芯腐蚀,清洗后导致飞边。
如:82机种890产品。
D、模芯进胶:如本司“389”柱子合模线飞边(进胶造成)E、粉末、拉丝二次成形导致飞边,主要表现在二分模。
如:818F、混料:因材料流动指数变异导致飞边。
如90混有900P等G、材料比例(原:再):变更导致飞边。
H、设备异常:如计量不稳定,机筒温度异升高,模温升高。
注塑成型各种缺陷的现象及解决方法
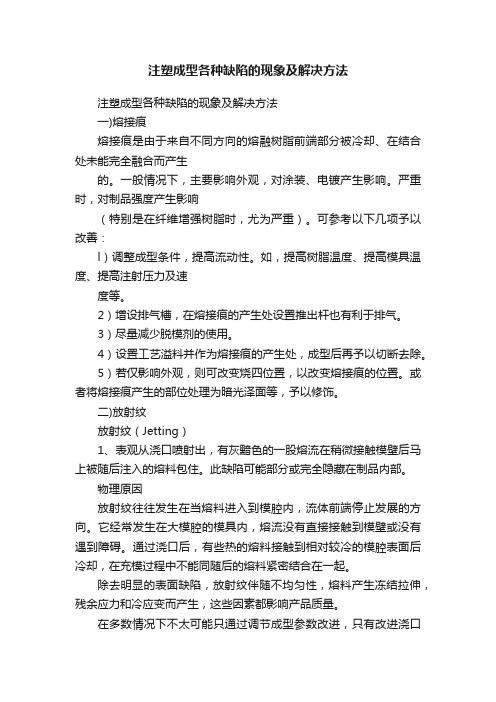
注塑成型各种缺陷的现象及解决方法注塑成型各种缺陷的现象及解决方法一)熔接痕熔接痕是由于来自不同方向的熔融树脂前端部分被冷却、在结合处未能完全融合而产生的。
一般情况下,主要影响外观,对涂装、电镀产生影响。
严重时,对制品强度产生影响(特别是在纤维增强树脂时,尤为严重)。
可参考以下几项予以改善:l)调整成型条件,提高流动性。
如,提高树脂温度、提高模具温度、提高注射压力及速度等。
2)增设排气槽,在熔接痕的产生处设置推出杆也有利于排气。
3)尽量减少脱模剂的使用。
4)设置工艺溢料并作为熔接痕的产生处,成型后再予以切断去除。
5)若仅影响外观,则可改变烧四位置,以改变熔接痕的位置。
或者将熔接痕产生的部位处理为暗光泽面等,予以修饰。
二)放射纹放射纹(Jetting)1、表观从浇口喷射出,有灰黯色的一股熔流在稍微接触模壁后马上被随后注入的熔料包住。
此缺陷可能部分或完全隐藏在制品内部。
物理原因放射纹往往发生在当熔料进入到模腔内,流体前端停止发展的方向。
它经常发生在大模腔的模具内,熔流没有直接接触到模壁或没有遇到障碍。
通过浇口后,有些热的熔料接触到相对较冷的模腔表面后冷却,在充模过程中不能同随后的熔料紧密结合在一起。
除去明显的表面缺陷,放射纹伴随不均匀性,熔料产生冻结拉伸,残余应力和冷应变而产生,这些因素都影响产品质量。
在多数情况下不太可能只通过调节成型参数改进,只有改进浇口位置和几何形状尺寸才可以避免。
与加工参数有关的原因与改良措施见下表:1、注射速度太快降低注射速度2、注射速度单级采用多级注射速度:慢-快3、熔料温度太低提高料筒温度(对热敏性材料只在计量区)。
增加低螺杆背压与设计有关的原因与改良措施见下表:1、浇口和模壁之间过渡不好提供圆弧过渡2、浇口太小增加浇口3、浇口位于截面厚度的中心浇口重定位,采用障碍注射、工艺溢料是指用手工在模具上開一條深一些的排气槽,在生產時此槽產生出來的(批峰),又叫工藝批峰,主要是用來改善燒膠或熔接痕,可將燒膠或熔接痕調整到此批峰上,生產后將其切除。
注塑成型常见不良现象及处理措施

注塑成型常见不良现象及处理措施注塑成型常见的不良现象有以下几种:
1. 短射:指注塑料进模型中未充满模腔,导致产品缺陷。
处理措施:增加注射
压力、延长注射时间、增加料缸温度、增加模具温度、增加模具出料口直径等。
2. 气泡:指产品表面或者内部浮现气泡,影响产品质量。
处理措施:增加注射
压力、延长注射时间、增加模具温度、增加料缸温度、增加模具出料口直径、增加模具排气孔等。
3. 热熔线:指产品表面浮现细小的线状缺陷,通常是由于注射速度过快导致的。
处理措施:减小注射速度、增加模具温度、增加模具出料口直径等。
4. 毛刺:指产品表面浮现细小的凸起,通常是由于模具设计不合理或者模具磨
损导致的。
处理措施:修复模具、修改模具设计、增加模具温度、增加模具出料口直径等。
5. 缩水:指产品尺寸缩小,通常是由于注射压力不足或者冷却时间不足导致的。
处理措施:增加注射压力、延长冷却时间、增加模具温度等。
6. 毛洞:指产品表面或者内部浮现凹陷,通常是由于注射速度过快或者模具设
计不合理导致的。
处理措施:减小注射速度、修改模具设计、增加模具温度等。
处理不良现象的关键是找到问题的根源,然后针对性地采取相应的处理措施。
同时,注塑成型过程中的参数控制和模具维护也是关键的因素,需要进行定期检查和调整。
注射成型塑件常见缺陷问题及改善措施
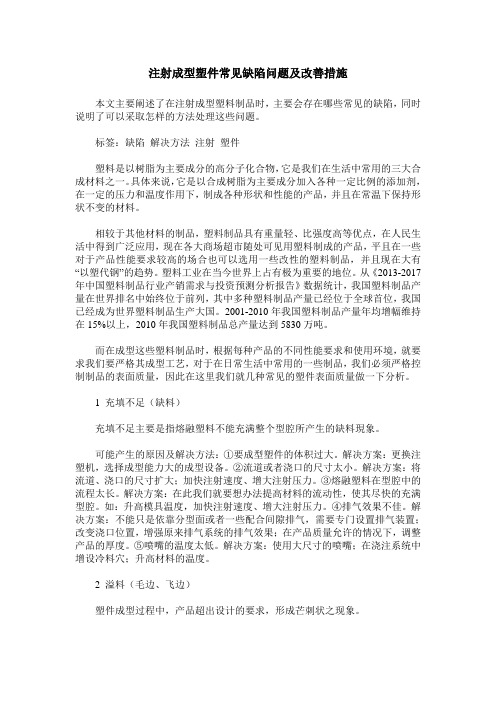
注射成型塑件常见缺陷问题及改善措施本文主要阐述了在注射成型塑料制品时,主要会存在哪些常见的缺陷,同时说明了可以采取怎样的方法处理这些问题。
标签:缺陷解决方法注射塑件塑料是以树脂为主要成分的高分子化合物,它是我们在生活中常用的三大合成材料之一。
具体来说,它是以合成树脂为主要成分加入各种一定比例的添加剂,在一定的压力和温度作用下,制成各种形状和性能的产品,并且在常温下保持形状不变的材料。
相较于其他材料的制品,塑料制品具有重量轻、比强度高等优点,在人民生活中得到广泛应用,现在各大商场超市随处可见用塑料制成的产品,平且在一些对于产品性能要求较高的场合也可以选用一些改性的塑料制品,并且现在大有“以塑代钢”的趋势。
塑料工业在当今世界上占有极为重要的地位。
从《2013-2017年中国塑料制品行业产销需求与投资预测分析报告》数据统计,我国塑料制品产量在世界排名中始终位于前列,其中多种塑料制品产量已经位于全球首位,我国已经成为世界塑料制品生产大国。
2001-2010年我国塑料制品产量年均增幅维持在15%以上,2010年我国塑料制品总产量达到5830万吨。
而在成型这些塑料制品时,根据每种产品的不同性能要求和使用环境,就要求我们要严格其成型工艺,对于在日常生活中常用的一些制品,我们必须严格控制制品的表面质量,因此在这里我们就几种常见的塑件表面质量做一下分析。
1 充填不足(缺料)充填不足主要是指熔融塑料不能充满整个型腔所产生的缺料現象。
可能产生的原因及解决方法:①要成型塑件的体积过大。
解决方案:更换注塑机,选择成型能力大的成型设备。
②流道或者浇口的尺寸太小。
解决方案:将流道、浇口的尺寸扩大;加快注射速度、增大注射压力。
③熔融塑料在型腔中的流程太长。
解决方案:在此我们就要想办法提高材料的流动性,使其尽快的充满型腔。
如:升高模具温度,加快注射速度、增大注射压力。
④排气效果不佳。
解决方案:不能只是依靠分型面或者一些配合间隙排气,需要专门设置排气装置;改变浇口位置,增强原来排气系统的排气效果;在产品质量允许的情况下,调整产品的厚度。
注射成型中常见缺陷及解决方法

注射成型中常见缺陷及解决方法注塑成型过程中,很容易发生一些异常现象,比如说:裂纹、制品表面有波纹、制品脆性强度下降、脱模难、制品尺寸不稳定、制品尺寸不稳定、制件脱皮分层、熔接痕、注射不满等,这些现象都会影响到成型模具的具体使用效果,因此我们需要找出相关因素以及解决方法。
裂纹1.模具太冷,调整模具温度。
2.冷却时间太长,降低冷却时间。
3.塑料和金属嵌件收缩不一样,对金属嵌件预热。
4.顶出装置倾斜不平衡,顶出截面积小或分布不当,调整顶出装置或合理安排顶杆数量及其位置。
5.制作斜度不够,脱模难,正确设计脱模斜度。
制品表面有波纹1.物料温度低,拈度大提高料温。
2.注射压力,料温高,可减少注射压力,反之则加大注射压力。
3.模具温度低,提高模具温度或增大注射压力。
4.注射速度太慢提高注射速度。
5.浇口太小,适当扩展浇口。
制品脆性强度下降1.料温太高,塑料分解,降低料温,控制物料在料筒内滞留时间。
2.塑料和嵌件处内应力过大,对嵌件预热,保证嵌件周围有一定厚度的塑料。
3.塑料回用次数多控制回料配比。
4.塑料含水,原料预热干燥。
脱模难1.模具顶出装置结构不良,改进顶出设计。
2.模腔脱模斜度不够,正确设计模具。
3.模腔温度不合适,适当控制模温。
4.模腔有接缝或存料,清理模具。
5.成型周期太短或太长,适当控制注塑周期6.模芯无进气孔,修改模具。
制品尺寸不稳定1.机器电路或油路系统不稳,修正电器或油压系统。
2.成型周期不一样,控制成型周期,使一致。
3.温度。
时间。
压力变化,调节,控制基本一致。
4.塑料颗粒大小不一,使用均一塑料。
5.回收下脚料与新料混合比例不均,控制混合比例,使均匀。
6.加料不均控制或调节加料均匀。
制件脱皮分层1.不同塑料混杂,采用单一品种的塑料。
2.同一塑料不同牌号混杂,采用同牌号的塑料。
3.塑化不良,提高成型温度。
4.混入异物,清理原材料,出去杂质。
熔接痕1.塑料温度太低提高机筒。
喷嘴及模具温度。
2.浇口太多减少浇口或改变浇口位置。
注塑成型常见问题和解决方案综合

射出保持壓不足
原料溫度低,流動性不足
料管溫度太低
射出速度太快
流痕
模具溫度太低
冷卻井太小
模具冷卻不適當
射嘴孔太小
Flow mark
模具設計
射出機
塑膠原料
更換材料
調整冷卻井
升高模具溫度
增加水路
成型不良對策
成型條件
增加墊料量
增加射出保持壓
延長保壓時間
增加料管溫度
升高原料溫度
減慢射出速度
流痕
加大射嘴孔
Flow mark
成型不良分析
塑膠原料
成型條件
原料中有揮發性成分
潤滑劑太多
用回收次料比例太多
用熱安定不好材料
料管內原料摩擦生熱或空氣 料管溫度太高 之絕熱壓縮引起之燃燒
冷卻環冷卻不良
原料在料管停留太久
射出速度太快
射出壓力太高
燒焦
模具內有油附著
排氣不良
澆口太小摩擦過熱分解
射嘴設計不良 (油壓封嘴)
料管太小
Burn Mark
(Torsion)。
塑膠原料
退火不適當
使用流動性 不好塑料
用流動方向成型縮收率差距大的塑料源自成型不良分析成型條件
射出速度太慢
保壓壓力未逐漸降低
射膠太飽(保壓時間太久)
料管溫度太低 模具溫度不適宜(太高; 保壓壓力太大
太低或未採用溫差)
冷卻時間不足
翹曲變形
模具冷卻不均 一或不充分
澆口位置不當
脫模方式不良
增加射嘴溫度
減少離型劑
增加料管溫度
加快射膠速度
熔接痕
增大澆口,橫澆口
更換料管
升高模具溫度
- 1、下载文档前请自行甄别文档内容的完整性,平台不提供额外的编辑、内容补充、找答案等附加服务。
- 2、"仅部分预览"的文档,不可在线预览部分如存在完整性等问题,可反馈申请退款(可完整预览的文档不适用该条件!)。
- 3、如文档侵犯您的权益,请联系客服反馈,我们会尽快为您处理(人工客服工作时间:9:00-18:30)。
1
注塑过程中的常见问题
? 气眼 ? 黑点或黑纹 ? 发脆 ? 烧焦 /焦痕 ? 飞边 /毛边 ? 分层起皮
2
注塑过程中的常见问题
? 流痕 ? 欠注 ? 银纹 /水花 ? 缩痕 ? 熔接痕
3
成型问题 -气眼
? 气眼是指空气被困在型腔内而使制件产生气泡的现象 . ? 它是由于两股熔体前锋交汇时气体无法从分型面、顶杆或排气孔中排出造成的。 ? 气眼通常位于熔体最后填充的地方。 ? 缺少排气口或排气口尺寸不足将导致在最后填充部位产生气眼或其他表面缺陷 . ? 如果制件设计薄厚不均,也非常容易造成气眼现象。
14
成型问题- 烧焦/焦痕
焦痕是指由于型腔内气体不能及时排走,导致在流动最末断产生烧黑现象。
焦痕形成原因 ? 型腔空气不能及时排走 ? 材料降解
过高熔体温度 过快螺杆转速 流道系统设计不当
15
案例(焦痕)
16
改进方法
模具设计 工艺条件
?在容易产生排气不良的地方增设排气系统 . ?加大主流道、分流道和浇口的尺寸
?增加注塑时间,降低注塑速度 ?降低料筒温度和喷嘴温度 ?降低注塑压力和保压压力 ?减少缓冲长度,使熔体不要在料筒中过填充。
20
成型问题 -分层起皮
分层起皮是指制件表面能被一层一层的剥离。
分层起皮原因分析 ? 混入不相容的其他高分子聚合物 ? 成型时使用过多的脱模剂 ? 型腔内熔体温度过低 ? 水分过多 ? 浇口和流道存在尖锐的角 ? 树脂温度不一致
?降低注塑压力 . ?降低注塑速度 . ?降低螺杆转速 . ?降低料筒温度 ?检查加热器、热电偶是否处于正常状态
17
成型问题 -飞边/毛边
飞边/毛边是指在模具分型面或顶杆等部位出现多余的塑料,使制件在上述地方 出现不规则的边角。
Flash
飞边产生原因
合模力不足
注塑过程中如果合模力过小,不足以抵消注塑压力,就极 易在分型面上产生飞边/毛边现象。
模具存在缺陷
如果模具发生变形,或者有异物存在分型面上,或者模具 设计上存在缺陷,都可能导致产生飞边/毛边现象
。
成型条件不合理
诸如熔体温度过高,注塑压力过大等工艺上的不合理均可 能导致产生飞边/毛边现象。
排气系统设计不当
如果排气系统设置不当,或排气槽太深,均会导致产生飞 边/毛边现象。
18
案例 (飞边)
6
成型问题 -黑点/黑纹
黑点/黑纹是指在制件表面存在黑色斑点或条纹,或是棕色条纹。
黑点/黑纹的起因 材料降解 : 塑胶过热分解将导致黑点或条纹。塑胶如果在封闭的料筒内、螺杆表面 停留时间过长, 将导致炭化降解,故而在注塑过程中产生黑点或条纹。 材料污染 : 塑胶中存在脏的回收料、异物、其他颜色的材料或易于降解的低分子材料,都可能引起 上述现象。空气中的粉尘也容易引起制件表面的黑点。
10
成型问题 -发脆
制件发脆是指制件在某些部位出现容易开裂或折断。发脆主要是由于材料降解导致 大分子断链,降低了大分子的分子量,从而使聚合物的整体物理性能下降。
发脆原因分析 ? 干燥条件不适合 ? 注塑温度设置不对 ? 浇口和流道系统设置不恰当 ? 螺杆设计不恰当 ? 熔接痕强度不高 ? 使用过多的回收料
21
案例 (分层起皮)
22
材料
模具设计 工艺条件
改进方法
?避免不相容的杂质或受污染的回收料混入原料中
?对所有存在尖锐角度的流道或浇口进行倒角处理,实现平滑过度 . ?增加料筒和模具温度 ?成型前对材料进行恰当的干燥处理 . ?避免使用过多的脱模剂
23
成型问题 -流痕
流痕是指在浇口附近呈波浪状的表面缺陷
流痕的原因分析 ? 熔体温度过低 ? 模温过低 ? 注塑速度过低 ? 注塑压力过低流痕)
25
改进方法
模具设计 工艺条件
?增大流道中冷料井的尺寸,以吸那更多的前锋冷料 . ?增大流道和浇口的尺寸 ?缩短主流道尺寸或改用热流道系统
7
案例 (黑纹)
8
改进方法 (1)
材料 模具设计
?采用无污染的原材料 ?将材料置于相对封闭的储料仓中 ?增加材料的热稳定性
?清洁顶杆和滑块 . ?改进排气系统 . ?清洁和抛光流道内的任何死角,保证不产生积料 ?注塑前清洁模具表面 .
9
改进方法 (2)
注塑机 工艺条件
?选择合适的注塑机吨位 ?检查料筒内表面、螺杆表面是否刮伤积料. ?降低料筒和喷嘴的温度. ?清洁注塑过程的各个环节. ?避免已经产生黑点/黑纹的料被重新回收利用.
13
改进方法 (2)
注塑机 工艺条件
?选择设计良好的螺杆,使塑化时温度分配更加均匀。如果材料温度不均, 在局部容易积聚过多热量,导致材料的降解
?降低料筒和喷嘴的温度 ? 降低背压、螺杆转速和注塑速度,减少过多剪切热的产生,避免聚合物分 解. ? 如果是熔解痕强度不足导致的发脆,则可以通过增加熔体温度,加大注塑 压力的方法,提高熔解痕强度
19
改进方法
模具设计
注塑机 成型工艺
?合理设计模具,保证模具合模时能够紧闭,不产生缝隙。 ?保障模具能够紧固在模板上,确保成型时不损伤模具 ?检查排气口的尺寸 ?清洁模具表面 ?打磨使模具产生合模不严的表面,使模具在锁模力能封闭得较好。
?设置适当大小的锁模力,保证注塑机的两块安装模板相互平行。 . ?增大注塑机型号,飞边可能是由于小注塑机的锁模力不足所至。
气眼可能引起的问题: 困在型腔内气体不能被及时排出,易导致出现表面 起泡,制件内部夹气,注塑不满等现象。
4
案例 (表面起泡)
Air bubble cut open
5
结构设计 模具设计 工艺条件
改进方法
?减少厚度的不一致,尽量保证壁厚均匀 . ?在最后填充的地方增设排气口 ?重新设计浇口和流道系统 . ?保证排气口足够大,使气体有足够的时间和空间排走 . ?降低最后一级注塑速度 . ?增加模温 ?优化注塑压力和保压压力
11
案例 (发脆)
12
改进方法 (1)
材料 模具设计
?注塑前设置适当的干燥条件 塑胶如果连续干燥几天或干燥温度过高,尽管可以除去挥发分等物 质,但同时也易导致材料降解,特别是热敏性塑料。 ?减少使用回收料,增加原生料的比例 . ?选用高强度的塑胶 .
?增大主流道、分流道和浇口尺寸 过小的主流道、分流道或浇口尺寸容易导致过多的剪切热从而导致 聚合物的分解。