注塑常见问题及分析
注塑品质问题总结范文

一、前言注塑工艺在塑料制品的生产中占据着重要的地位,然而,在注塑生产过程中,品质问题时有发生,严重影响了产品的质量和企业的声誉。
为了提高注塑产品的品质,减少品质问题的发生,现将我司近期注塑品质问题进行总结分析,并提出改进措施。
二、品质问题总结1. 产品外观缺陷(1)表面有油污、划痕、气泡等。
(2)产品尺寸不稳定,存在较大公差。
2. 产品内部缺陷(1)产品内部有空洞、缩孔、熔接痕等。
(2)产品内部有冷料、飞边等杂质。
3. 材料问题(1)原材料质量不稳定,导致产品性能波动。
(2)材料配比不当,影响产品性能。
4. 设备问题(1)模具设计不合理,导致产品缺陷。
(2)设备磨损严重,影响产品质量。
5. 操作问题(1)操作人员技能水平不足,导致产品品质下降。
(2)生产过程不规范,存在安全隐患。
三、原因分析1. 原材料问题:原材料质量不稳定,供应商管理不到位。
2. 设备问题:设备维护保养不及时,模具设计不合理。
3. 操作问题:操作人员技能水平不足,生产过程不规范。
4. 管理问题:品质管理制度不完善,缺乏有效的监督机制。
四、改进措施1. 优化原材料采购流程,提高原材料质量。
2. 加强设备维护保养,确保设备正常运行。
3. 提高操作人员技能水平,规范生产过程。
4. 完善品质管理制度,加强监督机制。
5. 加强与供应商的沟通与合作,提高原材料质量。
五、总结通过本次注塑品质问题总结,我司将针对存在的问题,采取有效措施进行改进。
在今后的生产过程中,我们要高度重视注塑品质问题,不断提高产品质量,以满足客户需求,提升企业竞争力。
同时,要加强员工培训,提高整体素质,确保生产过程规范化、标准化。
相信在全体员工的共同努力下,我司的注塑品质一定会得到全面提升。
注塑车间问题点和改善对策

在注塑车间,可能会遇到各种问题,这些问题在生产过程中需要特别关注并寻求相应
的改善对策。
以下是常见的问题点以及相应的改善措施:
1. 产品质量问题:在注塑过程中,可能会出现短射、翘曲、裂纹、瑕疵等质量问题。
要改善这些问题,首先要进行原因分析,如模具设计、注塑工艺参数和原材料等。
针
对性地对问题进行调整(如调整注塑速度、压力、温度等),并进行严格的质量控制。
2. 设备故障:"机器、模具和辅助设备可能都会发生故障。
正确的维护和保养是防止故障的关键,例如定期检查润滑系统、更换磨损零件、定期清洁模具等。
3. 低生产效率:提高生产效率是提升注塑车间竞争力的关键。
改善方法包括:减少模
具更换和调试时间、采用自动化设备减少人工干预、优化生产排程和工艺参数等。
4. 浪费问题:在注塑过程中,可能会产生原材料、能源和人力等方面的浪费。
合理安
排生产计划、提高原材料利用率、节约能源(如优化加热和制冷系统)等措施,可以
降低浪费并提高整体效益。
5. 安全问题:注塑车间的生产安全非常重要,包括操作安全、消防安全、职业健康等
方面。
加强员工培训,提高安全意识和操作技能;确保车间内部的通风、照明和消防
等条件良好;合理布局生产线,以避免安全隐患。
6. 人员问题:员工流动性、技能短缺等问题可能影响注塑车间的生产效率和质量。
通
过制定合理的员工福利、培训和晋升政策,可以提高员工满意度和职业素养,从而提
高生产效果。
综上所述,在面对注塑车间的各种问题时,应想方设法地改进生产流程、提高效率和
质量、确保安全,并充分关注员工的发展及满意度。
注塑常见缺陷和原因分析
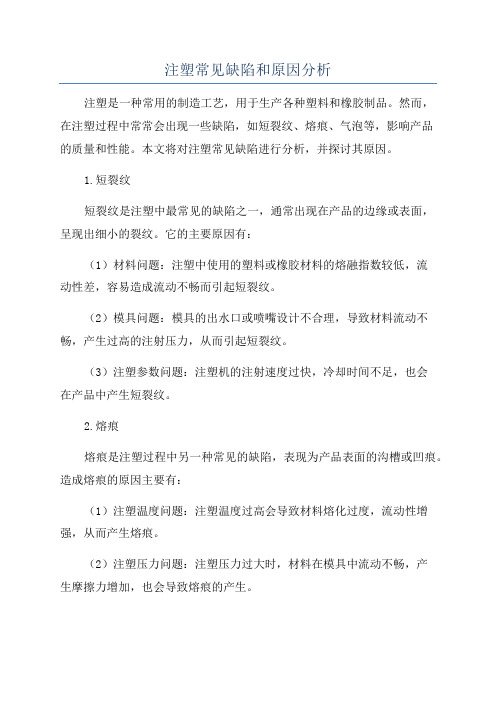
注塑常见缺陷和原因分析注塑是一种常用的制造工艺,用于生产各种塑料和橡胶制品。
然而,在注塑过程中常常会出现一些缺陷,如短裂纹、熔痕、气泡等,影响产品的质量和性能。
本文将对注塑常见缺陷进行分析,并探讨其原因。
1.短裂纹短裂纹是注塑中最常见的缺陷之一,通常出现在产品的边缘或表面,呈现出细小的裂纹。
它的主要原因有:(1)材料问题:注塑中使用的塑料或橡胶材料的熔融指数较低,流动性差,容易造成流动不畅而引起短裂纹。
(2)模具问题:模具的出水口或喷嘴设计不合理,导致材料流动不畅,产生过高的注射压力,从而引起短裂纹。
(3)注塑参数问题:注塑机的注射速度过快,冷却时间不足,也会在产品中产生短裂纹。
2.熔痕熔痕是注塑过程中另一种常见的缺陷,表现为产品表面的沟槽或凹痕。
造成熔痕的原因主要有:(1)注塑温度问题:注塑温度过高会导致材料熔化过度,流动性增强,从而产生熔痕。
(2)注塑压力问题:注塑压力过大时,材料在模具中流动不畅,产生摩擦力增加,也会导致熔痕的产生。
(3)模具设计问题:如果模具中的出水口或喷嘴设计不合理,也会在产品表面形成熔痕。
3.气泡气泡是注塑中常见的缺陷,表现为产品内部或表面的空腔。
气泡的形成原因有:(1)材料问题:注塑材料中含有过多的水分或挥发性物质,注塑过程中被加热蒸发,生成气泡。
(2)注塑温度过高:高温会导致材料熔化过度,容易产生气泡。
(3)注塑压力问题:过高的注塑压力会使材料在注塑过程中产生剧烈的振动,从而引起气泡。
(4)模具问题:模具中存在堵塞或不良的冷却系统,也会导致气泡的产生。
4.缩短问题缩短是指产品在冷却过程中出现尺寸缩小的现象。
产生缩短的主要原因有:(1)注塑温度过低:低温会使注塑材料的熔融程度不足,流动性降低,产生缩短。
(2)冷却时间不足:注塑材料冷却时间不足会导致产品未完全固化,容易产生缩短。
(3)注塑压力问题:过大的注塑压力会使产品产生内部的应力,引起尺寸缩小。
(4)模具问题:模具中存在过多的冷却系统,会导致材料过度冷却而使产品缩短。
注塑过程中常见的问题及解决方案

注塑过程中常见的问题及解决方案一、飞边(披锋)1. 问题描述- 这飞边就像塑料偷偷长出来的小翅膀,在注塑件的边缘或者分型面那里冒出来,看着可闹心了。
就像好好的一块蛋糕,边缘突然多出了一些不规则的奶油坨坨。
2. 解决方案- 首先得检查模具的合模力。
要是合模力不够,那塑料就会像调皮的小孩从门缝里挤出来。
适当增加合模力,把模具紧紧抱住,让塑料乖乖待在该待的地方。
- 模具的磨损也会导致飞边。
就像穿破了的鞋子会漏脚指头一样,磨损的模具缝隙变大了。
这时候就得修模啦,把那些磨损的地方补一补或者磨平。
- 注塑压力也不能太大。
如果压力太大,塑料就像被大力士猛推的水,到处乱流。
降低注塑压力,找到一个合适的值,既能把模具填满,又不会让塑料溢出来。
二、短射(缺料)1. 问题描述- 短射就像给一个杯子倒水,结果没倒满一样。
注塑件看着不完整,有些地方该有塑料的却空着,就像一个没发育好的小怪物。
2. 解决方案- 先看看注塑压力是不是太小。
压力小的话,塑料就像没力气的小蚂蚁,爬不到模具的每个角落。
增加注塑压力,让塑料充满整个模具型腔。
- 塑料的流动性也很关键。
如果塑料太黏,就像浓稠的糨糊,很难流到模具的远端。
这时候可以提高料筒温度,让塑料变得稀一点,流动性更好,就像把糨糊加热变成稀粥一样,能顺利流到各个地方。
- 浇口尺寸也可能有问题。
要是浇口太小,就像一个小得可怜的水龙头,水流不出来多少。
适当扩大浇口尺寸,让塑料能畅快地流进模具。
三、气泡(气穴)1. 问题描述2. 解决方案- 注塑速度可能太快了。
塑料像一阵风呼呼地冲进模具,把空气都裹在里面了。
降低注塑速度,让塑料慢慢流进去,就像散步一样,这样空气就有机会跑出来了。
- 模具的排气也很重要。
如果模具没有排气孔或者排气不良,空气就被困在里面出不来。
在模具上开排气槽或者使用透气钢材料,给空气一条逃跑的路。
- 塑料干燥不彻底也会产生气泡。
如果塑料里有水份,加热的时候就会变成水蒸气,形成气泡。
注塑缺陷原因分析与解决方案
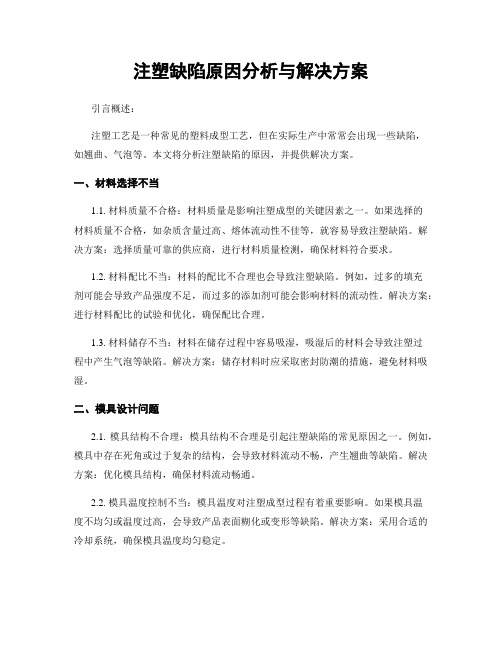
注塑缺陷原因分析与解决方案引言概述:注塑工艺是一种常见的塑料成型工艺,但在实际生产中常常会出现一些缺陷,如翘曲、气泡等。
本文将分析注塑缺陷的原因,并提供解决方案。
一、材料选择不当1.1. 材料质量不合格:材料质量是影响注塑成型的关键因素之一。
如果选择的材料质量不合格,如杂质含量过高、熔体流动性不佳等,就容易导致注塑缺陷。
解决方案:选择质量可靠的供应商,进行材料质量检测,确保材料符合要求。
1.2. 材料配比不当:材料的配比不合理也会导致注塑缺陷。
例如,过多的填充剂可能会导致产品强度不足,而过多的添加剂可能会影响材料的流动性。
解决方案:进行材料配比的试验和优化,确保配比合理。
1.3. 材料储存不当:材料在储存过程中容易吸湿,吸湿后的材料会导致注塑过程中产生气泡等缺陷。
解决方案:储存材料时应采取密封防潮的措施,避免材料吸湿。
二、模具设计问题2.1. 模具结构不合理:模具结构不合理是引起注塑缺陷的常见原因之一。
例如,模具中存在死角或过于复杂的结构,会导致材料流动不畅,产生翘曲等缺陷。
解决方案:优化模具结构,确保材料流动畅通。
2.2. 模具温度控制不当:模具温度对注塑成型过程有着重要影响。
如果模具温度不均匀或温度过高,会导致产品表面糊化或变形等缺陷。
解决方案:采用合适的冷却系统,确保模具温度均匀稳定。
2.3. 模具磨损严重:模具长时间使用后会出现磨损,磨损严重的模具会导致产品尺寸不准确或表面粗糙等缺陷。
解决方案:定期检查和维护模具,及时更换磨损严重的模具部件。
三、注塑工艺参数设置不当3.1. 注射压力过高或过低:注射压力是影响注塑成型的关键参数之一。
如果注射压力过高,会导致产品变形或开裂,而注射压力过低则会导致产品表面光洁度不高。
解决方案:根据产品要求和材料特性,合理设置注射压力。
3.2. 注射速度不合理:注射速度对产品的充填和冷却过程有着重要影响。
如果注射速度过快,会导致产品内部产生气泡或短射,而注射速度过慢则会导致产品表面瑕疵。
模具注塑常见问题及解决方法

模具注塑常见问题及解决方法模具注塑是一种常见的制造工艺,广泛应用于汽车、电子、家电等行业。
然而,在注塑过程中常会遇到一些问题,例如产品质量不合格、生产效率低下等。
本文将针对这些常见问题进行分析,并提出相应的解决方法。
1. 产品尺寸不准确产品尺寸不准确是模具注塑过程中常见的问题之一。
造成尺寸不准确的原因可能有很多,例如模具设计不合理、注塑机调试不当等。
解决这个问题的方法是对模具进行优化设计,确保模具的尺寸精度和稳定性;同时,对注塑机进行精确调试,保证注塑过程的准确性。
2. 产品表面缺陷产品表面缺陷是另一个常见的问题,例如气泡、痕迹、烧焦等。
这些表面缺陷会影响产品的外观和质量。
要解决这个问题,可以从以下几个方面入手:优化模具通气系统,确保注塑过程中的气体能够顺利排出;调整注塑参数,控制注塑温度和压力,避免过高或过低造成烧焦或气泡;定期清洁模具,防止灰尘和杂质对产品表面造成影响。
3. 模具磨损严重模具在长期使用过程中会出现磨损,导致产品尺寸不准确或者产生其他问题。
要解决这个问题,可以采取以下几种措施:定期对模具进行保养和维护,及时更换磨损严重的零部件;使用高质量的模具材料,提高模具的耐磨性;注塑过程中控制好注塑温度和压力,避免过高过低造成模具磨损。
4. 注塑机故障注塑机故障是导致生产效率低下的主要原因之一。
为了避免注塑机故障,可以采取以下几个措施:定期对注塑机进行维护和保养,清洁注塑机内部的杂质和积聚物;使用高质量的注塑机零部件,避免因零部件质量差导致故障;培训操作人员,提高其对注塑机的操作技能和维修能力。
5. 塑料材料选择不当塑料材料的选择对注塑产品的质量和性能有很大影响。
如果选择的塑料材料不合适,可能会导致产品强度不足、耐热性差等问题。
因此,在进行模具注塑之前,应仔细选择合适的塑料材料,根据产品的要求和使用环境来进行选择。
6. 生产成本过高生产成本过高是许多企业关注的问题。
要降低生产成本,可以从以下几个方面入手:优化模具设计,减少材料的浪费;提高注塑机的效率,减少能耗;采用高效的生产工艺,提高生产效率。
注塑工艺常见问题和解决
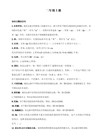
六、呈现问题:合模边挤出塑料。
原因:因料温及注压过高,或锁模力不足。
解决方法:1.降低注压及筒固化温度 2.缩短注时 3.减少注料速度 4.改用高锁模力机 5.改造合模表面紧配合及清理合模表面 6.转用低粘度料。
七、呈现问题:塑件表面呈凹痕。
原因:因塑件表面误时冷却,因其表面凹痕。
解决方法:1.增加注料速率 2.提高模槽内压(二次压力)3.降低筒料固化温度 4.提高注塑流量 5.增加注速 6.延长注时 7.使模具温度均匀 8.更改浇口位置 9.扩大浇口 10.缩短模具流道。
解决方法:1.提高料温 2.提高注温 3.增加注速 4.接缝线外设冷料池 5.设放气口 6.改变浇口位或浇口 7.不要用脱模剂 8.转用易流动的低粘度类原料。
四、呈现问题:塑件呈现空洞。
原因:因塑料在熔料固化期间表面接触低温模壁,收缩集中于厚壁段而造成空洞,或因夹气做成空洞。
解决方法:1.提高注压(及二次压力) 2.延长注时 3.降低料筒固化温度 4.消减模壁厚度至6mm以下,必要时设置等壁厚助线,及去除多余壁厚 5.扩大浇口 6.缩短流道 7.调匀模温 8.更改浇口位置,排除夹气。
二、呈现问题:塑件呈银纹形。
原因:因塑料含水份,混料不均匀,注塑时夹气,添加剂或脱模剂过多。
解决方法:1.加强回压 2.减慢注速 3.清理料筒 4.提高模温 5.改浇口位置 6.扩大流道及浇口 7.烘料 8.料门中安装红外线灯。
三、呈现问题:塑胶接口不良。
原因:因塑料温度太低,不能熔化,或因气体排泄不足导致两股以上分流混合而产生发状细线或气泡。
五、呈现问题:塑件欠注或缺料。
原因:因机械注塑及塑化性能不足,料流不良,浇口截面太细,模壁太薄或泄气不良。
注塑件常见品质问题及原因分析报告、解决方法

注塑件常见品质问题及原因分析、解决方法一、注塑件常见品质问题塑胶件成型后,与预定的质量标准(检验标准)有一定的差异,而不能满足下工序要求,这就是塑胶件缺陷,即常说的品质问题,要研究这些缺陷产生原因,并将其降至最低程度,总体来说,这些缺陷不外乎是由如下几方面造成:模具、原材料、工艺参数、设备、环境、人员。
现将缺陷问题总结如下:1、色差:注塑件颜色与该单标准色样用肉眼观看有差异,判为色差,在标准的光源下(D65)。
2、填充不足(缺胶):注塑件不饱满,出现气泡、空隙、缩孔等,与标准样板不符称为缺胶。
3、翘曲变形:塑胶件形状在塑件脱模后或稍后一段时间内产生旋转和扭曲现象,如有直边朝里,或朝外变曲或平坦部分有起伏,如产品脚不平等与原模具设计有差异称为变形,有局部和整体变形之分。
4、熔接痕(纹):在塑胶件表面的线状痕迹,由塑胶在模具内汇合在一起所形成,而熔体在其交汇处未完全熔合在一起,彼此不能熔为一体即产生熔接纹,多表现为一直线,由深向浅发展,此现象对外观和力学性能有一定影响。
5、波纹:注塑件表面有螺旋状或云雾状的波形凹凸不平的表征现象,或透明产品的里面有波状纹,称为波纹。
6、溢边(飞边、披锋):在注塑件四周沿分型线的地方或模具密封面出现薄薄的(飞边)胶料,称为溢边。
7、银丝纹:注塑件表面的很长的、针状银白色如霜一般的细纹,开口方向沿着料流方向,在塑件未完全充满的地方,流体前端较粗糙,称为银丝纹(银纹)。
8、色泽不均(混色):注塑件表面的色泽不是均一的,有深浅和不同色相,称为混色。
9、光泽不良(暗色):注塑件表面为灰暗无光或光泽不均匀称为暗色或光泽不良。
10、脱模不良(脱模变形):与翘曲变形相似,注塑件成型后不能顺利的从模具中脱出,有变形、拉裂、拉伤等、称为脱模不良。
11、裂纹及破裂:塑胶件表面出现空隙的裂纹和由此形成的破损现象。
12、糊斑(烧焦):在塑件的表面或内部出现许多暗黑色的条纹或黑点,称为糊斑或烧焦。
- 1、下载文档前请自行甄别文档内容的完整性,平台不提供额外的编辑、内容补充、找答案等附加服务。
- 2、"仅部分预览"的文档,不可在线预览部分如存在完整性等问题,可反馈申请退款(可完整预览的文档不适用该条件!)。
- 3、如文档侵犯您的权益,请联系客服反馈,我们会尽快为您处理(人工客服工作时间:9:00-18:30)。
1.塑料缩水就是塑料收缩的问题,很少有资料谈过.塑料收缩有四种情况:热收缩、相变收缩、取向收缩、压缩收缩与弹性恢复。
收缩过程有三部分组成:浇口凝固前的收缩、冷却收缩和脱模后收缩。
2. 缩水的主要原因:1,注射量不够2,熔体温度过高3,注射压力和保压压力过小4,注射时间和保压时间过少5,注射速度过大6模具温度不当3. 缩孔的主要原因:1,注射量不够2,注射压力太低3,注射速度不当4,模具温度过低4.注塑件缺胶、不饱模---Short Shot原因分析☐塑胶熔体未完全充满型腔。
☐塑胶材料流动性不好。
❖对策☐制品与注塑机匹配不当,注塑机塑化能力或注射量不足。
☐料温、模温太低,塑胶在当前压力下流动困难,射胶速度太慢、保压或保压压力过低。
☐塑料熔化不充分,流动性不好,导致注射压力损失大。
☐增加浇口数,浇口位置布置要合理、多腔不平衡排布充填。
☐流道中冷料井预留不足或不当,冷料头进入型腔而阻碍塑胶之正常流动,增加冷料穴。
☐喷嘴、流道和浇口太小,流程太长,塑胶填充阻力过大。
☐模具排气不良时,空气无法排除。
5.披峰(毛边)---Burring & Flashing❖原因分析☐塑胶熔体流入分模面或镶件配合面将发生-Burring。
☐锁模力足够,但在主浇道与分流道会合处产生薄膜状多余胶料为Flash ❖对策☐锁模力不足,射入型腔的高压塑胶使分模面或镶件配合面产生间隙,塑胶熔体溢进此间隙。
☐模具(固定侧)未充分接触机台喷嘴,公母模产生间隙。
(没装紧)☐模温对曲轴式锁模系统的影响。
☐提高模板的强度和平行度。
☐模具导柱套摩损/模具安装板受损/拉杆(哥林柱)强度不足发生弯曲,导致分模面偏移。
☐异物附着分模面。
排气槽太深。
☐型腔投影面过大/塑胶温度太高/过保压。
6.❖表面缩水、缩孔(真空泡)--Sink Mark & Void & Bubble❖原因分析☐制品表面产生凹陷的现象。
☐由塑胶体积收缩产生,常见于局部肉厚区域,如加强筋或柱位与面交接区域。
☐制品局部肉厚处在冷却过程中由于体积收缩所产生的真空泡,叫缩孔(Void)。
☐塑胶熔体含有空气、水分及挥发性气体时,在注塑成型过程空气、水分及挥发性气体进入制品内部而残留的空洞叫气泡(Bubble)。
❖对策☐增加浇口及流道尺寸,使压力有效作用于成型品的肉厚部。
必要时也可调整胶口位置。
☐提高保压压力、延长保压时间。
☐提高填充速度,在塑胶冷却固化前可以达到充分压缩。
☐射胶转保压太快。
☐使肉厚变化圆滑些,并提高此部分的冷却效率。
☐胶粒预先充分干燥除去水份。
☐料筒温度设定不宜偏高,可有效防止塑料分解气体之产生。
☐换用小螺杆或机台,防止螺杆产生过剪切。
☐升高背压,使气体能由料筒排出。
☐适当降低填充速度,气体有充足时间排出。
7.❖银纹(料花、水花)---Sliver Streak❖原因分析☐制品表面或表面附近,沿塑料流动方向呈现的银白色条纹。
☐银丝的产生一般是塑胶中的水分或挥发物或附着模具表面的水分等气化所致,注塑机螺杆卷入空气有时也会产生银条。
☐材料有杂质。
❖对策☐塑胶含水分、挥发物、干燥不足。
☐塑料熔体过热或滞留料筒太久而分解,产生大量气体,排出不完全,在固化时便产生银丝。
☐模具温度过低,塑料熔体迅速固化导致排气不完全。
☐模具表面附有油或水分或脱模剂,蒸发而成气体状,随着塑料熔体的冷却固化而液化。
☐螺杆卷入空气,料斗下部的冷却充分,则料斗侧的温度低,与料筒有温度差,胶粒常擦伤螺杆,易带入空气。
☐注射初期排气不良。
初期射出的的塑料熔体迅速固化,因而气体排出不完全,发生银线。
☐注射压力过高、注射速度过快。
当肉厚变化剧烈时,流动中的压缩塑料熔体急速地减压而膨胀,挥发分解气体与模穴接触后液化。
8.❖烧焦、气纹—Burn Mark❖原因分析☐一般所谓的烧焦(Burn Mark)包括制品表面因塑胶降解导致的变色及制品的填充末端焦黑的现象。
☐烧焦是滞留型腔内的空气在塑料熔体填充时未能迅速排出(困气),被压缩而显著升温,将材料烧焦。
☐排气不良。
❖对策☐困气区域加强排气,使空气及时排出。
☐降低注射压力,但应注意压力下降后注射速度随之减慢,容易造成流痕及熔接痕及熔接痕恶化。
☐采用多段控制填充,在成型过程末端采用多段减速方式以利气体排出。
☐采用真空泵抽取型腔内的空气,使型腔在真空状态下填充。
☐清理排气槽,防止堵塞。
☐浇口太细或太长,导致塑胶降解。
☐排气槽、排气镶件等。
9.❖表面流纹(流痕)、水波纹---Flow Mark or Halo & Ripples❖原因分析☐塑胶熔体流动的痕迹,以浇口为中心而呈现的条纹波浪模样。
☐表面发生垂直流向的无数细纹,导致制品表面产生类似指纹的波纹。
❖对策☐流痕是最初流入型腔内的塑胶熔体冷却过快,与其后流入的塑胶熔体间形成界限所致。
☐残留于注塑机喷嘴前端的冷材料,若直接进入型腔内,造成流痕。
☐塑胶熔体温度低则粘度增大而发生流痕。
☐模温低则夺走大量的塑胶熔体热量,使塑胶熔体温度下降,粘度增大而发生流痕。
☐射出速度过慢,填充过程塑胶熔体温度降低增多,粘度增大而发生流痕。
☐在模具填充过程中,型腔内的塑胶熔体温度下降,以高粘度状态充填,接触模面的塑胶熔体以半固化状压入,表面发生垂直流向的无数细纹,导致制品表面产生类似指纹的波纹。
☐塑胶熔体温度再下降时,填充不完全就固化,造成充填不足。
☐波纹常发生于产品边缘附近和填充末端。
10.❖夹水纹(熔接痕)、喷射纹(蛇纹)---Weld & Meld & Line & Jetting❖原因分析☐模具采用多浇口进浇方案时,胶料流动前锋相互汇合;孔位和障碍物区域,胶料流动前锋也会被一分为二;壁厚不均匀的情况也会导致熔接痕。
☐高速通过浇口的塑胶熔体直接进入型腔,然后接触型腔表面而固化,接着被随后的塑胶熔体推挤,从而残留蛇行痕迹。
☐侧浇口,塑胶经过浇口后无滞料区域或滞料区域不充足时,容易产生喷痕。
❖对策☐减少浇口数量。
☐在熔合部附近增设材料溢料井,将熔合线移至溢料井,然后再将其切除。
☐调整浇口位置。
☐改变浇口位置、数目,将发生熔合线的位置移往他处。
☐在熔合线区域加强排气,速疏散此部分的空气及挥发物。
升高料温与模温,增强塑胶的流动性,提高融合时的料温。
☐提高注射压力,适当增加浇注系统尺寸。
☐增大射出速度。
☐缩短浇口与熔接区域的距离。
☐缩短浇口与熔接区域的距离。
☐减少脱模剂的使用。
☐调整浇口位置,使塑胶熔体通过浇口后碰撞销类或壁面。
☐改变浇口形式,采用重叠浇口或凸耳浇口,在浇口区域设置足够的滞料区域。
☐可减慢塑胶熔体的初段注射速度。
☐增大浇口厚度/横截面积,使流动前锋立即形成。
☐升高模具温度,防止材料快速固化。
11.❖表面裂纹(龟裂)、内应力开裂、顶白(顶爆) ---Cracking & Crazing❖原因分析☐制品表面裂痕严重而明显者为破裂(Cracking)。
☐制品表面呈毛发状裂纹,制品尖锐角处常呈现此现象谓之龟裂(Crazing),也常称为应力龟裂。
❖对策☐脱模不良;内应力过大;熔接线位置;浇口龟裂。
☐收缩差异导致内应力太大。
☐过度充填。
过大的射出压力导致过度充填,制品内部应力过大,脱模时造成裂纹。
同时,模具配件的变形也增大,更难脱模,肋常破裂。
☐ Insert – molding中界面龟裂。
塑料的膨胀系数为金属的数倍,成型后收缩产生应力造成该部位之龟裂(crazing),严重者破裂(cracking).☐模具表面温度太低时,纤维在拉伸状态下固化,配向引起的应力常造成龟裂。
☐化学物质和紫外线。
☐退火处理——制品成型后收缩较多,龟裂常常不立刻发生,而在若干时间后才发生。
应力龟裂的潜伏期为21天左右。
12.❖表面色差、混色、光泽不良、透明度不足---Discoloration❖原因分析☐制品表面失去材料本来的光泽,形成乳白色层膜、模糊状态等皆可称为表面光泽不良❖对策☐部分降解;塑化不均匀;回收料混合不均匀。
☐冷却不均;塑料降解。
☐模具表面的抛光不良。
☐模温太低。
☐使用过多的脱模剂或油脂性脱模剂亦是表面光泽不良的原因。
☐材料吸湿或含有挥发物及异质物混入污染亦是造成表面光泽不良的原因之一。
润滑剂过多或挥发物含量多时,塑胶经过浇口后,其压力下降而气化,凝结于模穴表面,发生乳白色模糊状,润滑剂粒子过大时发生浓白条纹。
☐原料含杂物;材料降解;温度低,塑化不良。
☐高温模有助改善透明度;干燥不充分;抛光不良。
保压力:即保持模腔内胶料不发生逆流,能保持尺寸精度,但重量不稳定。
对调较成品缩水问题起重要作用。
背压压力:镙杆后退时施于镙杆端部胶料的压力。
可减少料花、气泡的现象。
A:背压调节适当时,能增加熔胶密度,将料筒内空气所分解的气体排出,把胶料压实,使啤塑周期稳定,提高生产效率。
B:背压高时,镙杆转速即慢,阻力较大,料筒镙杆容易受损,由于镙杆磨擦热作用,内热增加,在外加热不变的情况下,会使料温上升,粘度下降,产生逆流和漏流,在喷嘴也容易产生流涎现象。
C:背压低时,镙杆转速即快,但难以把料筒内的胶料压实,胶粒不均匀,从而产生料花的现象,如加色粉的料即会出现深浅不同的色带。
注意:回料时镙杆应成旋转形,射胶时应成直线形。