注塑件常见品质问题及原因分析
注塑品质问题总结范文

一、前言注塑工艺在塑料制品的生产中占据着重要的地位,然而,在注塑生产过程中,品质问题时有发生,严重影响了产品的质量和企业的声誉。
为了提高注塑产品的品质,减少品质问题的发生,现将我司近期注塑品质问题进行总结分析,并提出改进措施。
二、品质问题总结1. 产品外观缺陷(1)表面有油污、划痕、气泡等。
(2)产品尺寸不稳定,存在较大公差。
2. 产品内部缺陷(1)产品内部有空洞、缩孔、熔接痕等。
(2)产品内部有冷料、飞边等杂质。
3. 材料问题(1)原材料质量不稳定,导致产品性能波动。
(2)材料配比不当,影响产品性能。
4. 设备问题(1)模具设计不合理,导致产品缺陷。
(2)设备磨损严重,影响产品质量。
5. 操作问题(1)操作人员技能水平不足,导致产品品质下降。
(2)生产过程不规范,存在安全隐患。
三、原因分析1. 原材料问题:原材料质量不稳定,供应商管理不到位。
2. 设备问题:设备维护保养不及时,模具设计不合理。
3. 操作问题:操作人员技能水平不足,生产过程不规范。
4. 管理问题:品质管理制度不完善,缺乏有效的监督机制。
四、改进措施1. 优化原材料采购流程,提高原材料质量。
2. 加强设备维护保养,确保设备正常运行。
3. 提高操作人员技能水平,规范生产过程。
4. 完善品质管理制度,加强监督机制。
5. 加强与供应商的沟通与合作,提高原材料质量。
五、总结通过本次注塑品质问题总结,我司将针对存在的问题,采取有效措施进行改进。
在今后的生产过程中,我们要高度重视注塑品质问题,不断提高产品质量,以满足客户需求,提升企业竞争力。
同时,要加强员工培训,提高整体素质,确保生产过程规范化、标准化。
相信在全体员工的共同努力下,我司的注塑品质一定会得到全面提升。
注塑件常见缺陷及原因分析【详解】
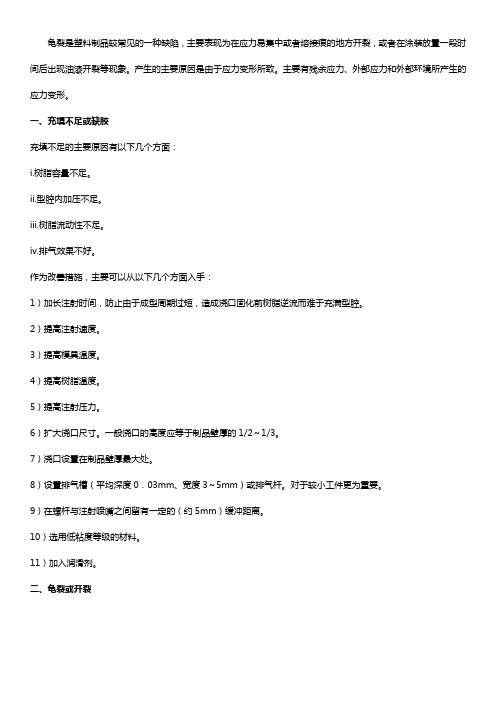
龟裂是塑料制品较常见的一种缺陷,主要表现为在应力易集中或者熔接痕的地方开裂,或者在涂装放置一段时间后出现油漆开裂等现象。
产生的主要原因是由于应力变形所致。
主要有残余应力、外部应力和外部环境所产生的应力变形。
一、充填不足或缺胶充填不足的主要原因有以下几个方面:i.树脂容量不足。
ii.型腔内加压不足。
iii.树脂流动性不足。
iv.排气效果不好。
作为改善措施,主要可以从以下几个方面入手:1)加长注射时间,防止由于成型周期过短,造成浇口固化前树脂逆流而难于充满型腔。
2)提高注射速度。
3)提高模具温度。
4)提高树脂温度。
5)提高注射压力。
6)扩大浇口尺寸。
一般浇口的高度应等于制品壁厚的1/2~1/3。
7)浇口设置在制品壁厚最大处。
8)设置排气槽(平均深度0.03mm、宽度3~5mm)或排气杆。
对于较小工件更为重要。
9)在螺杆与注射喷嘴之间留有一定的(约5mm)缓冲距离。
10)选用低粘度等级的材料。
11)加入润滑剂。
二、龟裂或开裂龟裂是塑料制品较常见的一种缺陷,主要表现为在应力易集中或者熔接痕的地方开裂,或者在涂装放置一段时间后出现油漆开裂等现象。
产生的主要原因是由于应力变形所致。
主要有残余应力、外部应力和外部环境所产生的应力变形。
(一)残余应力引起的龟裂残余应力主要由于以下三种情况,即充填过剩、脱模推出和金属镶嵌件造成的。
作为在充填过剩的情况下产生的龟裂,其解决方法主要可从以下几方面入手:1)由于直浇口压力损失最小,所以,如果龟裂最主要产生在直浇口附近,则可考虑改用多点分布点浇口、侧浇口及柄形浇口方式。
2)在保证树脂不分解、不劣化的前提下,适当提高树脂温度可以降低熔融粘度,提高流动性,同时也可以降低注射压力,以减小应力。
3)一般情况下,模温较低时容易产生应力,应适当提高温度。
但当注射速度较高时,即使模温低一些,也可减低应力的产生。
4)注射和保压时间过长也会产生应力,将其适当缩短或进行Th次保压切换效果较好。
注塑模具各类问题原因分析及解决办法
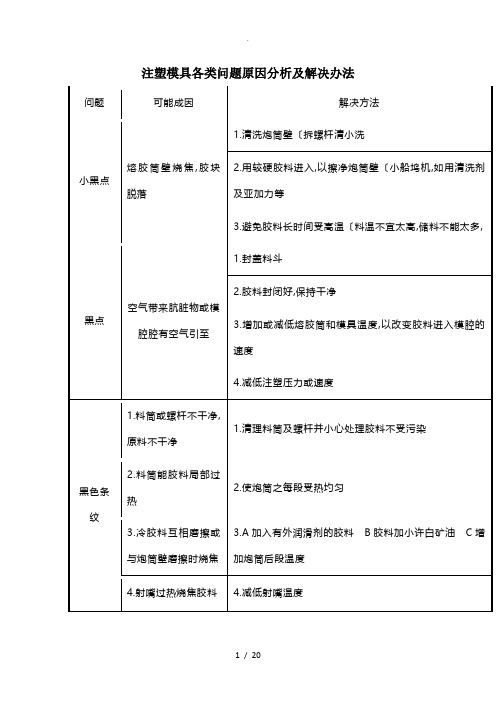
注塑模具各类问题原因分析及解决办法注塑成型过程中,制品收缩凹陷是比较常见的现象。
造成这种情况的主要原因有:机台方面<1>射嘴孔太大造成融料回流而出现收缩,太小时阻力大料量不足出现收缩。
<2>锁模力不足造成飞边也会出现收缩,应检查锁模系统是否有问题。
<3>塑化量不足应选用塑化量大的机台,检查螺杆与料筒是否磨损。
模具方面<1>制件设计要使壁厚均匀,保证收缩一致。
<2>模具的冷却、加温系统要保证各部份的温度一致。
<3>浇注系统要保证通畅,阻力不能过大,如主流道、分流道、浇口的尺寸要适当,光洁度要足够,过渡区要圆弧过渡。
<4>对薄件应提高温度,保证料流畅顺,对厚壁制件应降低模温。
<5>浇口要对称开设,尽量开设在制件厚壁部位,应增加冷料井容积。
塑料方面结晶性的塑料比非结晶性塑料收缩历害,加工时要适当增加料量,或在塑料中加成换剂,以加快结晶,减少收缩凹陷。
加工方面<1>料筒温度过高,容积变化大,特别是前炉温度,对流动性差的塑料应适当提高温度、保证畅顺。
<2>注射压力、速度、背压过低、注射时间过短,使料量或密度不足而收缩压力、速度、背压过大、时间过长造成飞边而出现收缩。
<3>加料量即缓冲垫过大时消耗注射压力,过小时,料量不足。
<4>对于不要求精度的制件,在注射保压完毕,外层基本冷凝硬化而夹心部份尚柔软又能顶出的制件,及早出模,让其在空气或热水中缓慢冷却,可以使收缩凹陷平缓而不那么显眼又不影响使用。
2注塑件震纹的原因分析PS等刚性塑料制件在其浇口附近的表面,以浇口为中心的形成密集的波纹,有时称为震纹。
产生原因是熔体粘度过大而以滞流形式充模时,前端的料一接触到型腔表面便很快冷凝收缩起来,而后来的熔料又胀开已收缩的冷料继续前进过程的不断交替使料流在前进中形成了表面震纹。
解决办法<1>提高料筒温度特别是射嘴温度,还应提高模具温度。
常见注塑缺陷及解决方案
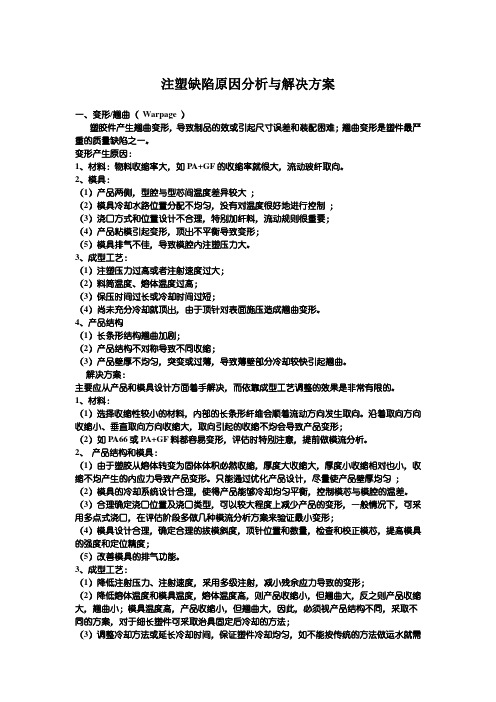
注塑缺陷原因分析与解决方案一、变形/翘曲(Warpage )塑胶件产生翘曲变形,导致制品的效或引起尺寸误差和装配困难;翘曲变形是塑件最严重的质量缺陷之一。
变形产生原因:1、材料:物料收缩率大,如PA+GF的收缩率就很大,流动玻纤取向。
2、模具:(1)产品两侧,型腔与型芯间温度差异较大;(2)模具冷却水路位置分配不均匀,没有对温度很好地进行控制;(3)浇口方式和位置设计不合理,特别加纤料,流动规则很重要;(4)产品粘模引起变形,顶出不平衡导致变形;(5)模具排气不佳,导致模腔内注塑压力大。
3、成型工艺:(1)注塑压力过高或者注射速度过大;(2)料筒温度、熔体温度过高;(3)保压时间过长或冷却时间过短;(4)尚未充分冷却就顶出,由于顶针对表面施压造成翘曲变形。
4、产品结构(1)长条形结构翘曲加剧;(2)产品结构不对称导致不同收缩;(3)产品壁厚不均匀,突变或过薄,导致薄壁部分冷却较快引起翘曲。
解决方案:主要应从产品和模具设计方面着手解决,而依靠成型工艺调整的效果是非常有限的。
1、材料:(1)选择收缩性较小的材料,内部的长条形纤维会顺着流动方向发生取向。
沿着取向方向收缩小、垂直取向方向收缩大,取向引起的收缩不均会导致产品变形;(2)如PA66或PA+GF料都容易变形,评估时特别注意,提前做模流分析。
2、产品结构和模具:(1)由于塑胶从熔体转变为固体体积必然收缩,厚度大收缩大,厚度小收缩相对也小,收缩不均产生的内应力导致产品变形。
只能通过优化产品设计,尽量使产品壁厚均匀;(2)模具的冷却系统设计合理,使得产品能够冷却均匀平衡,控制模芯与模腔的温差。
(3)合理确定浇口位置及浇口类型,可以较大程度上减少产品的变形,一般情况下,可采用多点式浇口,在评估阶段多做几种模流分析方案来验证最小变形;(4)模具设计合理,确定合理的拔模斜度,顶针位置和数量,检查和校正模芯,提高模具的强度和定位精度;(5)改善模具的排气功能。
注塑常见问题及分析

1.塑料缩水就是塑料收缩的问题,很少有资料谈过.塑料收缩有四种情况:热收缩、相变收缩、取向收缩、压缩收缩与弹性恢复。
收缩过程有三部分组成:浇口凝固前的收缩、冷却收缩和脱模后收缩。
2. 缩水的主要原因:1,注射量不够2,熔体温度过高3,注射压力和保压压力过小4,注射时间和保压时间过少5,注射速度过大6模具温度不当3. 缩孔的主要原因:1,注射量不够2,注射压力太低3,注射速度不当4,模具温度过低4.注塑件缺胶、不饱模---Short Shot原因分析☐塑胶熔体未完全充满型腔。
☐塑胶材料流动性不好。
❖对策☐制品与注塑机匹配不当,注塑机塑化能力或注射量不足。
☐料温、模温太低,塑胶在当前压力下流动困难,射胶速度太慢、保压或保压压力过低。
☐塑料熔化不充分,流动性不好,导致注射压力损失大。
☐增加浇口数,浇口位置布置要合理、多腔不平衡排布充填。
☐流道中冷料井预留不足或不当,冷料头进入型腔而阻碍塑胶之正常流动,增加冷料穴。
☐喷嘴、流道和浇口太小,流程太长,塑胶填充阻力过大。
☐模具排气不良时,空气无法排除。
5.披峰(毛边)---Burring & Flashing❖原因分析☐塑胶熔体流入分模面或镶件配合面将发生-Burring。
☐锁模力足够,但在主浇道与分流道会合处产生薄膜状多余胶料为Flash ❖对策☐锁模力不足,射入型腔的高压塑胶使分模面或镶件配合面产生间隙,塑胶熔体溢进此间隙。
☐模具(固定侧)未充分接触机台喷嘴,公母模产生间隙。
(没装紧)☐模温对曲轴式锁模系统的影响。
☐提高模板的强度和平行度。
☐模具导柱套摩损/模具安装板受损/拉杆(哥林柱)强度不足发生弯曲,导致分模面偏移。
☐异物附着分模面。
排气槽太深。
☐型腔投影面过大/塑胶温度太高/过保压。
6.❖表面缩水、缩孔(真空泡)--Sink Mark & Void & Bubble❖原因分析☐制品表面产生凹陷的现象。
☐由塑胶体积收缩产生,常见于局部肉厚区域,如加强筋或柱位与面交接区域。
注塑件常见品质问题及原因分析报告、解决方法

注塑件常见品质问题及原因分析、解决方法一、注塑件常见品质问题塑胶件成型后,与预定的质量标准(检验标准)有一定的差异,而不能满足下工序要求,这就是塑胶件缺陷,即常说的品质问题,要研究这些缺陷产生原因,并将其降至最低程度,总体来说,这些缺陷不外乎是由如下几方面造成:模具、原材料、工艺参数、设备、环境、人员。
现将缺陷问题总结如下:1、色差:注塑件颜色与该单标准色样用肉眼观看有差异,判为色差,在标准的光源下(D65)。
2、填充不足(缺胶):注塑件不饱满,出现气泡、空隙、缩孔等,与标准样板不符称为缺胶。
3、翘曲变形:塑胶件形状在塑件脱模后或稍后一段时间内产生旋转和扭曲现象,如有直边朝里,或朝外变曲或平坦部分有起伏,如产品脚不平等与原模具设计有差异称为变形,有局部和整体变形之分。
4、熔接痕(纹):在塑胶件表面的线状痕迹,由塑胶在模具内汇合在一起所形成,而熔体在其交汇处未完全熔合在一起,彼此不能熔为一体即产生熔接纹,多表现为一直线,由深向浅发展,此现象对外观和力学性能有一定影响。
5、波纹:注塑件表面有螺旋状或云雾状的波形凹凸不平的表征现象,或透明产品的里面有波状纹,称为波纹。
6、溢边(飞边、披锋):在注塑件四周沿分型线的地方或模具密封面出现薄薄的(飞边)胶料,称为溢边。
7、银丝纹:注塑件表面的很长的、针状银白色如霜一般的细纹,开口方向沿着料流方向,在塑件未完全充满的地方,流体前端较粗糙,称为银丝纹(银纹)。
8、色泽不均(混色):注塑件表面的色泽不是均一的,有深浅和不同色相,称为混色。
9、光泽不良(暗色):注塑件表面为灰暗无光或光泽不均匀称为暗色或光泽不良。
10、脱模不良(脱模变形):与翘曲变形相似,注塑件成型后不能顺利的从模具中脱出,有变形、拉裂、拉伤等、称为脱模不良。
11、裂纹及破裂:塑胶件表面出现空隙的裂纹和由此形成的破损现象。
12、糊斑(烧焦):在塑件的表面或内部出现许多暗黑色的条纹或黑点,称为糊斑或烧焦。
常见注塑件缺陷及解决的方法
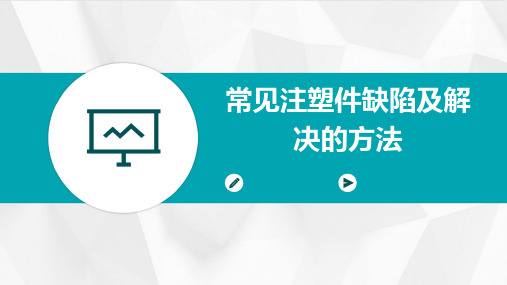
充填不足
01
总结词
充填不足是指注塑件在成型过程中未能完全填满 模具型腔,导致部分区域出现缺料或凹陷。
02
详细描述
充填不足通常是由于注射速度慢、注射压力不足、 模具温度过高或塑料流动性差等原因引起的。
缩痕
总结词
缩痕是指注塑件表面出现凹陷或收缩痕迹,影响 外观和尺寸精度。
详细描述
缩痕通常是由于塑料冷却过程中收缩率不均、模 具温度不均匀或注射压力不足等原因引起的。
常见注塑件缺陷及解 决的方法
目录
• 常见注塑件缺陷 • 注塑件缺陷原因分析 • 解决注塑件缺陷的方法 • 案例分析
01
常见注塑件缺陷
翘曲与扭曲
总结词
翘曲与扭曲是指注塑件形状发生扭曲或弯曲,不符合设 计要求。
详细描述
翘曲与扭曲通常是由于模具设计不合理、塑料收缩率差 异、注射温度和压力不适当等原因引起的。
环境条件的控制Байду номын сангаас
总结词
保持稳定的环境条件对注塑件的质量至关重 要,包括温度、湿度和清洁度等。
详细描述
确保注塑车间温度、湿度稳定,保持环境清 洁、无尘。定期对设备和环境进行清理和消 毒,防止污染和细菌滋生。同时,要关注天 气变化和季节性温差对注塑件质量的影响,
采取相应的措施进行调节。
04
案例分析
案例一:翘曲与扭曲缺陷的解决
材料选择与控制
总结词
选择合适的材料,控制材料质量是解决注塑件缺陷的重要步骤。
详细描述
根据产品使用要求和工艺特性,选择具有良好流动性和成型性的材料。同时, 要确保材料干燥、清洁,无杂质和污染。定期对材料进行质量检查,确保其性 能稳定。
模具优化与维护
常见注塑缺陷及解决方案
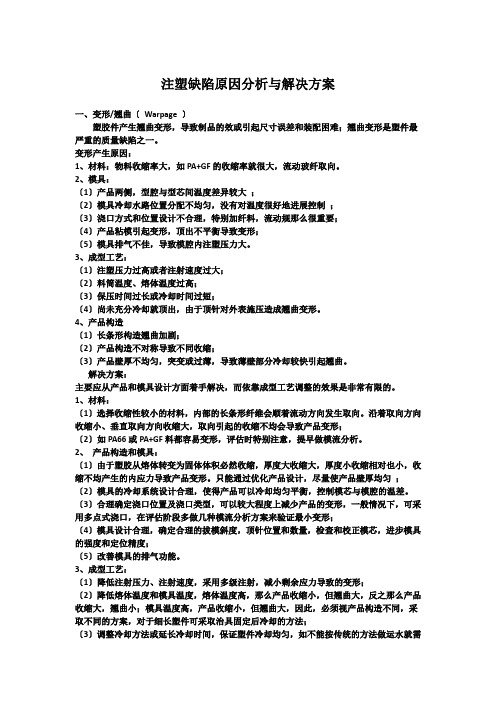
注塑缺陷原因分析与解决方案一、变形/翘曲〔Warpage 〕塑胶件产生翘曲变形,导致制品的效或引起尺寸误差和装配困难;翘曲变形是塑件最严重的质量缺陷之一。
变形产生原因:1、材料:物料收缩率大,如PA+GF的收缩率就很大,流动玻纤取向。
2、模具:〔1〕产品两侧,型腔与型芯间温度差异较大;〔2〕模具冷却水路位置分配不均匀,没有对温度很好地进展控制;〔3〕浇口方式和位置设计不合理,特别加纤料,流动规那么很重要;〔4〕产品粘模引起变形,顶出不平衡导致变形;〔5〕模具排气不佳,导致模腔内注塑压力大。
3、成型工艺:〔1〕注塑压力过高或者注射速度过大;〔2〕料筒温度、熔体温度过高;〔3〕保压时间过长或冷却时间过短;〔4〕尚未充分冷却就顶出,由于顶针对外表施压造成翘曲变形。
4、产品构造〔1〕长条形构造翘曲加剧;〔2〕产品构造不对称导致不同收缩;〔3〕产品壁厚不均匀,突变或过薄,导致薄壁部分冷却较快引起翘曲。
解决方案:主要应从产品和模具设计方面着手解决,而依靠成型工艺调整的效果是非常有限的。
1、材料:〔1〕选择收缩性较小的材料,内部的长条形纤维会顺着流动方向发生取向。
沿着取向方向收缩小、垂直取向方向收缩大,取向引起的收缩不均会导致产品变形;〔2〕如PA66或PA+GF料都容易变形,评估时特别注意,提早做模流分析。
2、产品构造和模具:〔1〕由于塑胶从熔体转变为固体体积必然收缩,厚度大收缩大,厚度小收缩相对也小,收缩不均产生的内应力导致产品变形。
只能通过优化产品设计,尽量使产品壁厚均匀;〔2〕模具的冷却系统设计合理,使得产品可以冷却均匀平衡,控制模芯与模腔的温差。
〔3〕合理确定浇口位置及浇口类型,可以较大程度上减少产品的变形,一般情况下,可采用多点式浇口,在评估阶段多做几种模流分析方案来验证最小变形;〔4〕模具设计合理,确定合理的拔模斜度,顶针位置和数量,检查和校正模芯,进步模具的强度和定位精度;〔5〕改善模具的排气功能。
- 1、下载文档前请自行甄别文档内容的完整性,平台不提供额外的编辑、内容补充、找答案等附加服务。
- 2、"仅部分预览"的文档,不可在线预览部分如存在完整性等问题,可反馈申请退款(可完整预览的文档不适用该条件!)。
- 3、如文档侵犯您的权益,请联系客服反馈,我们会尽快为您处理(人工客服工作时间:9:00-18:30)。
注塑件常见品质问题及原因分析、解决方法一、注塑件常见品质问题塑胶件成型后,与预定的质量标准(检验标准)有一定的差异,而不能满足下工序要求,这就是塑胶件缺陷,即常说的品质问题,要研究这些缺陷产生原因,并将其降至最低程度,总体来说,这些缺陷不外乎是由如下几方面造成:模具、原材料、工艺参数、设备、环境、人员。
现将缺陷问题总结如下:1、色差:注塑件颜色与该单标准色样用肉眼观看有差异,判为色差,在标准的光源下(D65)。
2、填充不足(缺胶):注塑件不饱满,出现气泡、空隙、缩孔等,与标准样板不符称为缺胶。
3、翘曲变形:塑胶件形状在塑件脱模后或稍后一段时间内产生旋转和扭曲现象,如有直边朝里,或朝外变曲或平坦部分有起伏,如产品脚不平等与原模具设计有差异称为变形,有局部和整体变形之分。
4、熔接痕(纹):在塑胶件表面的线状痕迹,由塑胶在模具内汇合在一起所形成,而熔体在其交汇处未完全熔合在一起,彼此不能熔为一体即产生熔接纹,多表现为一直线,由深向浅发展,此现象对外观和力学性能有一定影响。
5、波纹:注塑件表面有螺旋状或云雾状的波形凹凸不平的表征现象,或透明产品的里面有波状纹,称为波纹。
6、溢边(飞边、披锋):在注塑件四周沿分型线的地方或模具密封面出现薄薄的(飞边)胶料,称为溢边。
7、银丝纹:注塑件表面的很长的、针状银白色如霜一般的细纹,开口方向沿着料流方向,在塑件未完全充满的地方,流体前端较粗糙,称为银丝纹(银纹)。
8、色泽不均(混色):注塑件表面的色泽不是均一的,有深浅和不同色相,称为混色。
9、光泽不良(暗色):注塑件表面为灰暗无光或光泽不均匀称为暗色或光泽不良。
10、脱模不良(脱模变形):与翘曲变形相似,注塑件成型后不能顺利的从模具中脱出,有变形、拉裂、拉伤等、称为脱模不良。
11、裂纹及破裂:塑胶件表面出现空隙的裂纹和由此形成的破损现象。
12、糊斑(烧焦):在塑件的表面或内部出现许多暗黑色的条纹或黑点,称为糊斑或烧焦。
13、尺寸不符:注塑件在成型过程中,不能保持原来预定的尺寸精度称为尺寸不符。
14、气泡及暗泡:注塑件内部有孔隙,气泡是制品成型后内部形成体积较小或成串孔隙的缺陷,暗泡是塑胶内部产生的真空孔洞。
15、表面混蚀:注塑件表面呈现无光、泛白、浊雾状外观称为混蚀。
16、凹陷:注塑件表面不平整、光滑、向内产生浅坑或陷窝。
17、冷料(冷胶):注塑件表面由冷胶形成的色泽、性能与本体均不同的塑料。
18、顶白/顶高:注塑件表面有明显发白或高出原平面。
19、白点:注塑件内有白色的粒点,粒点又叫“鱼眼”,多反映在透明制品上。
20、强度不够(脆裂):注塑件的强度比预期强度低,使塑胶件不能承受预定的负裁二、常见品质(缺陷)问题产生原因1、色差:①原材料方面因素:包括色粉更换、塑胶材料牌号更改,定型剂更换。
②原材料品种不同:如PP料与ABS料或PC料要求同一种色,但因材料品种不同而有轻微色差,但允许有一限度范围。
③设备工艺原因:A、温度;B、压力;C熔胶时间等工艺因素影响。
④环境因素:料筒未清干净,烘料斗有灰尘,模具有油污等。
⑤色粉本身因素:有些色粉不受温,且制品很易受温度变化而改变。
如:9278烤箱提手(A2945兰)。
2、充填不足(缺胶):①模具方面:A、浇注系统设计不合理,浇注系统是熔体进入模腔的通道,对塑料件成型质量有很大关系,浇口不平行,浇口的位置不是在壁厚部位;B、模具排气结构不良;C、熔体中的杂质或冷料阻塞流道;D、模具温度未达要求。
②原料方面:A、原材料含水量过大;B、原料中易挥发物超标;C、原材料中杂质或再生料过多。
③注塑机方面:A、注射量不足:如用150T机生产180T产品。
B、喷嘴为异物堵塞,喷嘴孔太小;C、原料供应不足:如料筒堵塞,水口料影响下料;D、止逆阀故障;E、注射行程不够。
④成型操作方面:A、模具温度过低;B、注射压力太低;C、保压时间太短;D、注射速度太慢;E、熔体温度太低。
3、翘曲变形:①模具方面:主要是针对模具设计方面不合理原因造成,在此不作讲述。
②成型操作方面:A、注射压力过高,流体方向和垂直流向方向分子取向相差较大,塑胶力图恢复原有的卷曲状态,所以流体流动方向上的收缩大于垂直流动方向上的收缩;B、熔体温度过高;C、保压压力过高:保压压力高时,塑料中的内压力过高,在脱模后内应力的释放使塑胶件产生翘曲变形;D、熔体流速太慢;E、回火温度过高或时间太长。
③原材料方面:PP/PA料容易变形。
4、熔接痕(纹):①模具方面:A、浇口数量太多,即进胶点多,进胶口截面积过小;B、模具无冷料穴或冷料穴位置不正确;C、模具冷却系统设计不合理,熔体在模中冷却太快且不均匀。
②原料方面:A、脱模剂用量太多,或使用不符合的脱模剂;B、熔体的流动性差,在成型时易产生熔接痕;C、原料中含水份较多或挥发物含量过高。
③成型操作方面:A、熔体温度过低,低温熔体的分流汇合性能较差,容易形成熔接纹;B、熔体注射压力过低,使得注射速度过慢,熔体在型腔中的温度不相同,这时熔体在分流汇合时就易产生熔接纹。
④注塑机设计和塑胶件设计方面:在此不作讲述。
5、波纹:①模具方面:与熔接纹大同小异,但需特别强调的是冷料对波纹影响最大。
②原料方面:A、熔体流动性差是产生波纹的主要原因,如:PMMA、PC、AS等透明料制品;B、当ABS 材料是经改性为共聚型高分子材料时,如加工温度过高,树脂及润滑剂会产生挥发性气体,这些气体使塑胶件表面形成波纹。
③成型操作方面:A、注射速度过小;B、熔体流速过大;C、模具温度偏低;D、保压时间短;E、射嘴温度低。
6、溢边(飞边、披锋):①模具方面:产生飞边最大原因是由模具引起。
A、模具分型面加工粗糙;B、型腔及抽芯部分的滑动件磨损过多。
②原料方面:熔体流动性好材料,如:PP料、PA料、PS料。
③成型操作方面:A、注射压力过大;B、熔体温度高;C、注射压力;D、注射压力分布不均,充模速度不均;E、注射量过多,使模腔内压力过大。
7、银丝纹:①模具与注塑机方面:不作讲述。
②原料方面:A、原料水份是产生水气银丝纹的原因;B、原料受高温降解;C、脱模剂产生少量挥发性气体。
③成型操作方面:A、熔体温度过高;B、熔体在高温下停留的时间过长;C、熔体在模腔中保压时间过长;D、注射速度过快。
8、色泽不均(混色):①模具与注塑机方面不讲述;②原料方面:A、着色剂的热稳定性差;B、着色剂分散效果不理想;C、色粉份量太大,如1包25KG料用色粉300克以上;D、加波纤产品容易有浮纤,造成原料不均,产生混色;E、原料杂质多,使制品表面色泽不一。
③成型操作方面:A、料筒温度过高,使熔体在料筒内分解;B、塑化不良,即熔体不能完全均匀地相熔;C、熔体在料筒中停留时间过长;D、注射和保压时间太长,背压大。
9、光泽不良(暗色):①模具和注塑机方面不讲述。
②原料方面:A、熔体的流动性太差,使塑件表面不致密;B、原料再生料过多;C、原料中添加剂的分散性能太差;D、原料水分或易挥发物含量过高;E、原料本身问题:如PBT、PA+30%GF,PBT+10%GF、PPS。
③成型操作方面:A、冷却不够;B、注射速度偏小,压力较低;C、保压时间太短;D、熔体的流动性能差;E、填充波纤太多,如PA+30%GF。
10、脱模不良(脱模变形):①模具方面:主查的原因是由于模具设计不当造成,占90%以上。
在此不讲述。
②原料方面:A、原料中混入异物;B、脱模剂效果不良;C、软质塑件比硬塑件难脱模。
③成型操作方面:A、注射压力过大,熔体温度过高,流动性差;B、塑件产生飞边;C、喷嘴温度过低,冷却时间太短;D、注塑时间和保压时间过长。
11、裂纹和破裂:①模具及塑机方面在此不作讲述②原料方面:A、原料吸水性大,加热后易分解脆化,造成破裂;B、原料中加入再生料较多;C、两种不能相熔的组分混合在一起;D、材料本身轫度太低,或刚性太强和有内应力,如PBT、PBT+GF、PC、ABS、PMMA。
③成型操作方面:A、注射压力过大,使得残余应力增大;B、保压时间过长;C、内应力未消除,如PC和PMMA料为特出。
12、糊斑(烧焦):①模具及塑机方面在此不讲述。
②原料方面:A、原材料中水分和易挥发物含量过高;B、原料熔融指数太大,使用润滑剂过多;C、原料需高温才能塑化的,如PBT、PPS等。
③成型操作方面:A、注射速度过大;B、熔体的温度高;C、注射压力大。
13、尺寸不符:①模具及塑机方面在此不讲述。
②原料方面:A、不同塑料的收率不同,造成尺寸不稳定,所以模具设计分PP/ABS/PPS/PS料模;B、水口料添加量及定型剂的添加量。
③成型操作方面:A、注射压力过小或注射速度过低;B、充模时间和保压时间较短;C、模温过低。
14、气泡和暗泡:①模具及塑机方面在此不讲述。
②原料方面:A、原料水分含量过多,烘料时间短及烘料温度低;B、原材料收缩率过大,如PA66;C、再生料过多。
③成型操作方面:A、注射速度过快,时间过短,气体来不及排出;B、保压时间不足;C、冷却不均匀或冷却时间不够;D、熔体温度与模具温度过高,引起挥发分释出成形气泡。
15、表面混蚀:大体与光泽不良相似在此不讲述。
16、凹陷(缩水):①模具和塑机方面不讲述。
②原料方面:A、熔体(树脂)收缩率太大,没加定型剂;B、流动性差,润滑剂太少;C 填充剂少。
③成型操作方面:A、注射压力过低,速度太慢;B、注射时间和保压时间太短;C、熔体温度和模具温度太高;D、制件胶位较厚,特别是丝筒针位。
17、冷料(冷胶):①模具和塑机方面不讲述。
②原料方面:轫性大的材料易造成冷胶,由于产品脱模时,水口胶丝易拉长且断后粘附于模具上,造成第二PCS产品有冷胶。
③成型操作方面:A、熔体温度太低,塑化不良;B、模具温度过低和熔体的流动性太差;C、冷胶与混色往往会同时出现。
18、顶白/顶高:①模具与塑机方面在此不作讲述。
②原料方面:主要与原材料有关,如PP料不易顶白,易顶高;ABS料易顶白,易顶高。
③成型操作方面:A、注射压力太大;B、熔体温度过高,模具温度过低,两者温差大;C、冷却时间短;D、保压压力太高,保压时间太长。
19、白点:①模具方面及塑机方面一般没影响。
②原材料方面:A、原料颗粒大小相差较大,造成难塑化或塑化不均匀;B、原料中混有异料或不相熔的原料;C、原料本身特性造成,如,透明料较多。
③成型操作方面:A、料筒温度低;B、螺杆的转速太快,周期短;C、背压太低。
20、强度不够(脆裂):①模具与塑机方面一般不影响。
②原材料方面:A、原材料本身脆是最主要因素(即材料强度低);B、再生料过多;C、不同型号材料相混合;D、填充剂太多;E、加波纤材料比例大。
③成型操作方面:A、料筒温度过高,熔体降解或分解;B、模具温度太低,塑件成型性能受损,强度下降;C、注射压力太低和熔体的流动性太差;D、制件壁薄,受力不均匀。