不同连铸工艺及品种的保护渣技术特征2
薄板坯高速连铸用结晶器保护渣

只有考虑了钢液、保护渣和结晶器本身这一 套完整的系统构成之后, 才能了解保护渣的特性 和效率。Hylsa 薄板坯连铸机使用球形粒状保护 渣的系统示于图 2。
考虑到熔渣边缘组成和结晶器镀层, 当液态 熔渣凝固时, 确定其结晶范围是有用的。研究发
# 34 #
1998 年 第 10 期( 第 36 卷# 总第 216 期)
渣膜。 在拉速为 5. 0m/ min 时保护渣 B 传递的总热
2. 92 MW/ m2, 而 保 护 渣 A 传 递 的 总 热 2. 80 MW/ m2, 克 分子比关系计 算结果表明, 保护渣 B 的导热率较高, 而结晶温度较低。
态保护渣还可提供瞬时润滑, 阻止富碳的不反应 的保护渣与钢接触, 这样可以减少增碳。 2. 2 球形粒状保护渣
在已有的高速传统板坯连铸结晶器保护渣技 术的基础上, 为满足拉速达 6. 0m/ min 的薄板坯的 特殊要求而开发了一种球形粒状保护渣。这种保 护渣具有极好的化学一致性、良好的流动性和环 境清洁度。
0. 64
0. 026
24. 62
0. 38~ 0. 07 0. 49~ 0. 15
130 @ 130( E) 128
0. 52
0. 017
30. 59
0. 49~ 0. 12
拉速 m/ min
1. 4 1. 6 4. 0 5. 0 4. 0 5. 0 5. 0 1. 2~ 1. 6 1. 6~ 2. 0
10. 42
连铸保护渣技术

连铸保护渣技术,作为连铸生产的关键技术之一,对连铸生产的顺行和铸坯质量有着至关重要的影响,尤其是铸坯表面缺陷,基本上都是在结晶器内形成的,与保护渣有直接关系。
近几年来,该技术在实践中,如空心颗粒渣等的开发和广泛使用,对铸坯质量的改善、连铸生产工艺的稳定起了很大促进作用。
同时渣的基础性能如润滑和传热特性的研究也一直受到人们的重视。
一、不同钢种对保护渣性能设计要求不同成分的钢种.其钢水特性及其凝固特点有别,从而决定了对保护渣性能方面的要求。
1、低碳钢首先钢中w(C)<0.08%或0.06%。
这类钢高温机械性能好,凝固过程中不存在严重的相变体积变化,内应力及裂纹敏感性小,故通常以较高拉坯速度进行生产,以提高生产率。
基于低碳钢本身的凝固特点和质量要求,设计时主要考虑渣的润滑及消耗。
较高拉速要求尽量增大结晶器热流,加速钢水凝固,防止粘结漏钢,这要求保护渣结晶温度低、凝固温度适中,以确保低碳钢结晶器保护渣在950℃以上处于非晶体状态,使发生粘结漏钢的可能性最小。
在高速浇注时,为使足够的液态保护渣能流入铸流和结晶器内表面之间的区域,确保良好的润滑和足够的消耗,通常保护渣粘度选择较低的范围。
另外,此类钢种初生铁素体坯壳中[P]、[S]偏析小,初生坯壳强度高,铸坯振痕较深,故应使用保温性能较好的保护渣,提高弯月面初生坯壳温度,有利于减轻振痕过深带来的危去。
因此,连铸低碳钢满足以上各要求,就要通过设计具有一定的传热性能、良好的保温性能、良好的非金属吸收、良好的润滑和性能稳定的保护渣来获得。
2、中碳钢中碳钢钢水凝固过程中发生己δ→γ相变,体积强烈收缩,此钢种裂纹敏感性大,容易产生表面裂纹,特别是高拉速时。
避免纵横向裂纹是首要考虑的问题,为此,中碳钢用保护渣设计的重点应放在控制从铸坯传往结晶器的热流上,限制结晶器热通量,希望保护渣具有较大热阻。
因此,应选用凝固温度高、结晶温度也高的保护渣,利用结晶质膜中的“气隙”,使保护渣传热速度减缓,有助于减小铸坯在冷却过程中产生的热应力。
品种钢优特钢连铸工艺技术

品种钢优特钢连铸工艺技术l 特殊钢连铸有什么特点?与普通钢连铸相比,特殊钢连铸具有以下特点:(1)特殊钢的合金元素较多,含量较高,碳含量范围大(0.02%~2.3%C),受合金元素影响,其凝固特性与普通碳素钢差异大。
(2)特殊钢的纯洁度、均匀性、气体含量、低倍组织、夹杂物形态等要求比普通碳素钢高。
(3)有些特殊钢含Cr、V、Ti、Nb、Al等活泼元素,极易与氧、氮反应生成高熔点化合物,给铸坯质量带来一定危害;还有些合金元素则与钢中碳生成碳化物或碳氮化物,容易产生高温固相析出,对钢的热塑性有重要影响。
(4)由于连铸过程的特殊冷却凝固条件,成分偏析和组织不均匀性更为突出。
2 针对特殊钢凝固的特点,特殊钢连铸需解决的关键技术问题有哪些?(1)提高钢液洁净度提高钢液洁净度的主要措施有:1)低铝洁净钢技术,通过采用非铝脱氧剂,在降低钢中残铝和氧化物夹杂中A1203比例的前提下,使钢中氧含量比传统铝脱氧显著降低;2)钢包软吹氩技术;3)钢包下渣自动检测及控制技术;4)中间包冶金技术;5)中间包和结晶器保护渣的优化;6)结晶器冶金技术。
(2)提高铸坯质量铸坯质量的提高主要依赖于连铸装备和工艺的优化,就我国目前现有装备而言,提高特殊钢铸坯质量的主要措施是采取低过热度浇铸与电磁搅拌相结合的办法来扩大等轴晶区,减轻偏析和疏松的集中度。
同时根据不同钢种的特点选择合适的保护渣、结晶器设计与冷却、二冷和拉坯制度,以防止裂纹等缺陷的产生。
为进一步提高铸坯质量,近年出现了一些新的技术:1)浇铸过程液面自动控制;2)结晶器和凝固末段电磁搅拌工艺优化;3)大方坯轻压下技术;4)利用外场或形核剂细化铸态组织技术;5)复式结晶器控制凝固组织技术;6)结晶器钢液流动控制技术等。
3 目前我国使用的中间包,尤其是方坯连铸机使用的中间包存在的突出问题表现在哪些方面?目前我国使用的中间包存在较多的问题,尤其是方坯连铸机用的中间包存在的问题更为突出。
连铸结晶器保护渣
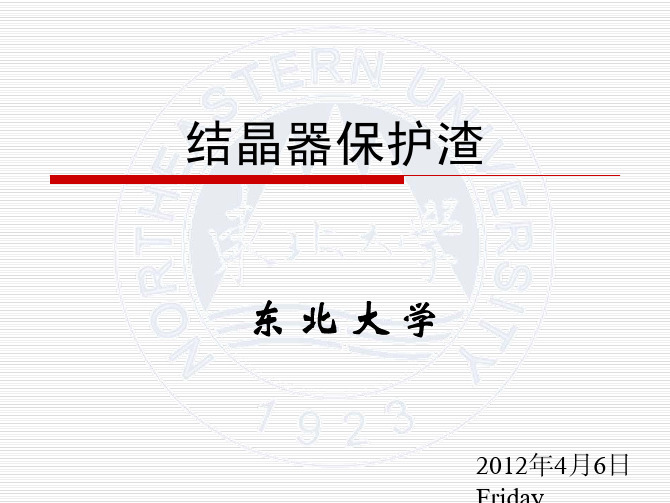
连铸技术
炭质材料对熔化速度的影响规律是:炭量越多, 炭的粒度越小和比表面积越大,则降低熔化速 度的作用越强烈。常用的炭质材料降低熔化速 度的顺序是:碳黑>高炭石墨> 土状石墨。。
27
3.3 保护渣粘性特征
连铸技术
保护渣粘度是控制结晶器与铸坯之传热和润滑的 重要参数。粘度过大,熔化的保护渣不易渗入 结晶器和铸坯之间的缝隙内,铸坯的润滑条件 恶化,导致坯壳不易从结晶器内拉出,甚至造 成粘性漏钢事故。粘度过低,熔化的保护渣大 量流入结晶器和铸坯之间,铸坯润滑和传热不 均,导致表面裂纹产生,产生废品。
19
连铸技术
20
硅氧离子团结构图
连铸技术
21
氧化物对保护渣熔体网络的作用
连铸技术
22
3 连铸保护渣的物理和化学性质
连铸技术
连铸过程对保护渣的物理及化学性质有一定的要 求。保护渣的熔化温度、粘度及表面张力的大 小取决于渣的化学成分。保护渣的研制和使用 过程要对其密度、熔化温度、粘度、表面张力 和溶解吸收非金属夹杂物能力等基本性质进行 测定。除了上述几个基本性质之外,保护渣的 熔融速度、熔融模型以及导热性也是衡量保护 渣性能的主要指标。
用于连铸保护渣的原材料种类繁多,分为天然矿 物(如石灰石、萤石、硅灰石、石英砂等)和 人造矿物(工业废渣、水泥熟料、玻璃粉、人 造硅灰石等)。
6Leabharlann 连铸技术保护渣组成、性能与原料选择之间的关系
7
连铸技术
保护渣的物性指标主要包括成分、熔点、熔速、 粘度等,这些指标主要取决于 CaO、SiO2、 Al2O3的百分含量、组成助熔剂和熔速调节剂 的成分及加入量。不同的钢种、断面或拉速对 保护渣的特性要求差别比较大,相应地,保护 渣的化学成分变化也很大。
连铸保护渣的生产工艺
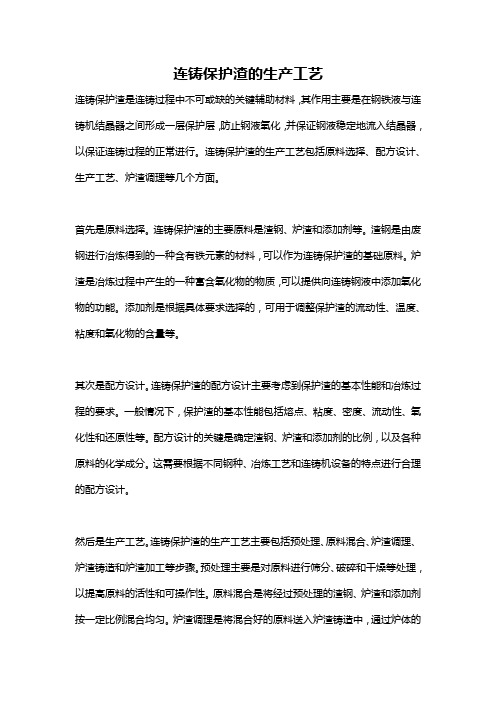
连铸保护渣的生产工艺连铸保护渣是连铸过程中不可或缺的关键辅助材料,其作用主要是在钢铁液与连铸机结晶器之间形成一层保护层,防止钢液氧化,并保证钢液稳定地流入结晶器,以保证连铸过程的正常进行。
连铸保护渣的生产工艺包括原料选择、配方设计、生产工艺、炉渣调理等几个方面。
首先是原料选择。
连铸保护渣的主要原料是渣钢、炉渣和添加剂等。
渣钢是由废钢进行冶炼得到的一种含有铁元素的材料,可以作为连铸保护渣的基础原料。
炉渣是冶炼过程中产生的一种富含氧化物的物质,可以提供向连铸钢液中添加氧化物的功能。
添加剂是根据具体要求选择的,可用于调整保护渣的流动性、温度、粘度和氧化物的含量等。
其次是配方设计。
连铸保护渣的配方设计主要考虑到保护渣的基本性能和冶炼过程的要求。
一般情况下,保护渣的基本性能包括熔点、粘度、密度、流动性、氧化性和还原性等。
配方设计的关键是确定渣钢、炉渣和添加剂的比例,以及各种原料的化学成分。
这需要根据不同钢种、冶炼工艺和连铸机设备的特点进行合理的配方设计。
然后是生产工艺。
连铸保护渣的生产工艺主要包括预处理、原料混合、炉渣调理、炉渣铸造和炉渣加工等步骤。
预处理主要是对原料进行筛分、破碎和干燥等处理,以提高原料的活性和可操作性。
原料混合是将经过预处理的渣钢、炉渣和添加剂按一定比例混合均匀。
炉渣调理是将混合好的原料送入炉渣铸造中,通过炉体的高温熔融和冷却过程,形成连铸保护渣。
最后是炉渣加工。
连铸保护渣在生产过程中需要经过一系列加工步骤,以获得符合要求的颗粒度和流动性。
加工步骤主要包括炉渣破碎、筛分、磁选和加热等。
炉渣破碎是将铸造好的保护渣进行碾压和破碎,得到符合要求的颗粒度。
筛分是将破碎后的保护渣按不同颗粒大小进行分级,以获得合适的颗粒粒径。
磁选是对炉渣中的磁性物质进行去除,以保证保护渣的纯净度。
加热是对筛分好的保护渣进行烘干,以提高保护渣的流动性和反应活性。
总的来说,连铸保护渣的生产工艺主要包括原料选择、配方设计、生产工艺和炉渣加工等几个方面。
不锈钢连铸保护渣概述

王雨 谢兵 王谦
刁江
(重庆大学材料科学与工程学院,400044)
摘要:概要介绍了不锈钢的性铯特点、主要生产工艺,保护渣的设计原则,围绕提高铸坯表面质量的表面质量,论 述了连铸保护渣的优化技术路线,对几个典型生产实例做了介绍。 关键词:不锈钢,连铸坯,表面质量,保护渣
1刚舌 不锈钢是最重要而又普及的金属材料之一,由于其具有许多优良的性能.如耐腐蚀、耐磨损、耐热、耐低温、 强度高、易加工等,因此广泛用于工业及民用领域的各个方面。自1954年加拿大阿特拉斯公司建造了第一台不锈钢 板坯连铸机以来,不锈钢连铸技术蓬勃发展,目前不锈钢连铸比已超过95%。高质量连铸坯生产已成为不锈钢降低 成本,提高成材率的关键…。 不锈钢中含有大量的cr、Ni、Ti等合金元素,不同品种具有不同的凝固特性;易氧化元素多,夹杂含量高,在 连铸过程中铸坯表面多出现凹陷、裂纹、深振痕及夹渣等缺陷。这些缺陷增加了铸坯修磨量,严重降低了不锈钢的 成材率。为满足性能要求,不锈钢表面质量要求比普碳钢严格,但其本身却极易产生表面缺陷,因此不锈钢连铸必 须选择合适的连铸保护渣并严格控制其理化性能。
物。这些夹杂物成群分布在铸坯表面下,恶化铸坯质量,并易于在水口内壁聚集,造成水口堵塞,给浇注操作带来
危害。这就要求不锈钢连铸保护渣具有较强的吸收和同化夹杂物的能力,而且在保护渣吸收夹杂物后,其性能仍然 能够满足连铸工艺的要求,即保证保护渣物化性能的稳定性。
150
4不锈钢表面缺陷及其对保护渣的要求
41口坑和裂纹 不锈钢铸坯表面易产生…坑.返与钢的化学成分打咒一如幽5所示,304舆氏体十锈制NilCr当量&为0 55, 铁索体凝固牢约为1.口坑敏感性母为强烈.430铁索体币锈钢则列19坑不敏感。通常下锈钢板坯口坑№方坯严重。 H坑处不仅结品组织粗化,而R常常伴础纵裂纹产生.见罔6,易导致溶钢或漏铜事触。同时使铸坯表面平整度差. 增加铸坯袁自修噼量或剥皮々。
连铸保护渣2
连铸保护渣2连铸保护渣是直接影响连铸稳定生产和改善铸坯质量的一种功能性消耗材料,它具有绝热保温,防止再氧化,吸收夹杂物,均匀传热,润滑坯壳等功能,在连铸工艺中起着至关重要的作用,由于保护渣的显著作用,各国连铸工作者对保护渣都非常重视.1保护渣的基本特性1.1保护渣的熔融特性保护渣在结晶器内的熔融过程示意图(略).保护渣在熔融状态时自上而下可形成粉渣层,烧结层及熔渣层3层结构,起绝热保温,防止再氧化,吸收夹杂物的作用;在结晶器与坯壳之间形成固态渣膜(玻璃质层,结晶质层)和液态渣膜两层结构,起到"润滑"和"控制传热"作用,靠结晶器一侧是固态层,造坯壳一侧是液态层;固态层中进一步分为玻璃质层和结晶质层,且有结晶粒度的差异.渣膜在厚度方向上的不同结构层,有着不同的"润滑"和"传热效应".日本NKK公司的一项研究证实[21,通过提高结晶温度可加快渣的结晶速度(实质上是增加渣膜中的结晶质层厚度),由此开发出一种可减少中碳钢表面纵裂的新型保护渣.然而,由于玻璃质层的组分质点是无序排列的,振动范围较大,体系内能也较大,因而热阻较小,对控制传热的影响较小;相反,结晶质层的热阻较大,对控制传热的影响较大.根据不同浇铸条件(钢种,断面,拉速等)对结晶器传热的不同要求,调整渣膜中玻璃质层和结晶质层的比例,可以达到改善坯壳向结晶器的传热,从而达到控制铸坯表面缺陷的目的.LZ保护渣的冶金特性1.2.1粘度粘度是保护渣的一个重要参数,粘度太大或太小,都会使渣膜厚薄不均,润滑传热不良,甚至引起收稿日期2003折-21作者简介:饶添荣(1974)男,福建龙岩人,工程师,从事炼钢连铸工艺工作.万方数据106江西冶金2003年12月坯壳悬挂撕裂.粘度与温度的关系式为[[3171二A" T"exp(B/T)式中,7为粘度〔泊);T为绝对温度;A,B为常数.对于一定成分的渣,随温度降低粘度呈突然性增大趋势,所以一般希望从弯月面到出结晶器的坯壳表面温度应大于1 150℃,且要求渣粘度不会发生突变,这对保持均匀渣膜厚度,确保良好润滑极其重要.1.2.2表面张力熔渣的表面张力和金一渣的界面张力决定了熔渣润湿钢的能力,它影响夹杂物分离,夹杂物吸收, 渣膜的润滑和铸坯的表面质量,是一项重要的冶金特性.结晶器液面有保护渣层覆盖时结晶器中钢液弯月面半径与表面张力和界面张力的关系为[[31y, = 5.43 x 10-2.二一./P,一P.) la口._.=a二一少二coso式中,Y.为弯月面半径;'_,为金一渣界面张力; ..,,.为钢,渣表面张力;9为润湿角;P. "o.为钢, 渣密度.若Y.大,弯月面凝固壳受钢水静压力作用贴向结晶器壁就越容易,润滑良好,坯壳裂纹也就难于发生.若Y.小,就会破坏弯月面的薄膜弹性性能,铸坯易于发生裂纹,夹渣等表面缺陷.1.2.3熔点与熔化速度保护渣的熔点的基本原则是必须低于结晶器内的钢水温度,只有这样保护渣才能熔化,一般为950 ℃一1200℃,主要取决于保护渣的的原料组成及其化学成分.熔化速度决定钢液面上形成熔渣层厚度和渣的消耗量.熔化速度过慢,形成熔渣层过薄,渣膜不均匀,润滑传热就不好;熔化速度过快,粉渣层很快消失,熔渣层易结壳,渣膜厚度增加,使传热减慢,坯壳减薄而易产生裂纹.因此,必须合理控制保护渣的熔化速度.保护渣熔化速度一般是由其成分中的炭粒子来控制完成的,控制能力的强弱决定于炭粒子的种类和数量[41.表现在它对造渣材料的分融能力和对造渣材料生成的熔体的流动阻滞能力.炭粒子的原材料常见的有炭黑和石墨.炭黑在温度较低区域里有很强的分融能力和控制效率,在高温区其作用却大为降低;石墨开始氧化的温度高且慢,控制高温能力强,故有延缓保护渣的烧结和熔化功能.1.2.4吸收溶解夹杂物的能力保护渣碱度提高,可改善保护渣吸收和溶解钢中夹杂物的动力学条件而有利于吸收夹杂物,但碱度过高,熔渣中易析出钙铝黄长石(2CaO从qSi02),枪晶石((3CaO.2Si02 - CaF2 )等高熔点物质,使熔渣的析晶温度和析晶能力增高,恶化保护渣的玻璃化特性,破坏了熔渣的均匀润滑和传热,引起铸坯缺陷甚至拉漏,故碱度控制应合理.2保护渣的选择与应用2.1保护渣原料的选择保护渣的主要成分为.O, SiO2, A1203, 990,Fe2O3, N% 0, K2 0, Li20, CaF2以及炭粒,Ca()和Si02 约占60%一70% , CaO/Si马(即碱度)之比通常在0.8一1.2.加人Na20, Cal,是为了降低熔化速度和粘度,炭粒起隔离熔滴,调节熔化速度的作用.保护渣原料的选择要做到组成合理,成分稳定;既要满足连铸质量的需要,又要经济节约,尽可能就地取材,充分利用当地的废弃资源.例如国内某些保护渣厂常用的保护渣原料有玻璃粉(SiO2大于70% , Na20大于13%),水泥,高炉渣,烟道灰,固态水玻璃,苏打,萤石等[31,由这些原料按照不同比例配制成需要的渣料.表1,表2分别示出了保护渣常用的基料及助熔剂的化学成分.表1保护渡常用基料的化学成分化学成分,%基料—si场Cs0鸽乌.鲍pMn0 Na,O残伪高炉渣25一3933一45 s一15 2一8 0.1一1.0 < 1电厂灰45一60 2一5 10一20 1一4 2一6 3一8'钾土60-65 1一2 1〕一IS 5一7 <13" 1一2水泥熟料19一2260一65 5-7 1一4 <6白渣45一5518一22 <9 0.25%的硬钢)一1.0,C为13%一14%,q1,为..3 Pa-s(用于软钢)一0.45(用于硬钢),熔渣层厚度3一5.5 mmo颗粒渣不适用于小方坯,因其熔化均匀,宜用于MCAK钢板坯和大方坯.德国Sulukl. k等人认为[91,保护渣中MnO为3 . 5 % , CaO/SiO2为0.9,11.为..25 Pa "s, Ta为900 ℃,T.为1 025℃,能满足c大于等于0.35%,Mn大于等于0.65%的大断面圆坯的表面质量要求.马钢连铸圆坯主要用于生产车轮轮箍用钢,此类钢由于含碳量,含锰量均较高,因此要求钢水纯净度很高,尤其是钢中气体([01, [H]-, [N])的含量,要求控制在很低的水平,以至冶炼时加Al量较高,在保护浇铸效果不佳的情况下,A1203和AIN夹杂将进一步增加,使圆坯表面易形成线状缺陷.浇铸这类钢,保护渣既要有好的润滑特性,又要有低的传热强度;因此,保护渣粘度要适当高些(,,为0.30-0.50 Pa- s);为了防范点状凹陷和确保有良好的吸收夹杂物的能力,碱度要适中(R为0. 90) [301渣中A12 Os含量要低些;另一方面要确保有一定渣耗量(0.45一0.70甲t) a2.2.3异型坯用保护渣马钢引进的3机3流异型坯/矩型坯连铸机,铸坯尺寸为异型坯:750 mm x 450 mm x 120 mm, 50 rim x 300 mm x 120 mm;矩型坯:;250 mm x 380 mm.因砂打石硼苏萤万方数据108江西冶金2003年12月其独特的截面形状和复杂的连铸工艺决定了对保护渣要求更为严格,马钢根据异型坯生产特点,选择了3类保护渣进行了生产试验研究:(1)低碱度(0.8),较高熔点(1 171℃)和粘度(1.39 Pa-s);(2)中碱度(1.02),较高熔点(1 188℃)和粘度(1.10 Pa-s);(3)中高碱度(1.12),较低熔点(1 145 9C)(0.84Pa- s);把这3类保护渣的理化性能与从韩国进口的相比较,第三类保护渣的效果与其一致,有利于改善异型坯表面质量.韩国异型坯保护渣成分如表3所示.根据马钢的生产实践,在设备条件和操作因素不变的情况下,异型坯表面裂纹与保护渣粘度和拉速有关,对于小断面异型坯控制,I .叽在0.5一0.6Pa " s " m/min;大断面控制在0.5 Pa "s"m/min时,能够防止异型坯腹板纵裂.表3韩国异型坯保护渣成分化学成分,%企业'ISQi0.50073Px01:::竺喻011光阳Indl印】s;oi Al,场31.36 12.2624.69 13.181._843491Fei 011.533.137.8024.2035.8219.56M酥】2.472.291._000.79Na}00.254.531._120.792.2.4溥板坯连铸用保护值墨西哥Hylsa公司的CSP连铸机,铸坯厚50mm,低碳钢拉速3.0一5.5 m/xnin.其所用保护渣, 开浇时用发热型渣,连浇时用球形空心颗粒渣(R为0.86, A1203为8.0% , Na2O+K20+Lie.为12%,F为6.5%,1},为0.18 Pa "s, Ta为1 300℃,T,为1 070℃,渣耗.095 kg) [u],这种开浇时和A铸时分别用不同类保护渣的作法,在实际使用中的效果很好,在薄板坯连铸中具有推广价值.马钢CSP薄板坯连铸机预计于2003年10月份建成投产,规格0.8一12.7二x 900一1 600 mm.由于CSP工艺具有拉速快,凝固快,易产生粘结漏钢以及铸坯表面质量差等特点,借鉴前人的经验,对保护渣的选用将综合考虑下列因素.(1)为了防止钢液二次氧化和确保具有良好的绝热保温性能,选择有良好铺展性,熔化均匀性和抗波动性的保护渣;(2)生产超低碳钢时,为了防止钢液增C,应采用低C或无C且熔化性能好的保护渣;(3)应有良好的吸收溶解A12 03夹杂的性能;(4)成渣快,玻璃化率高,润滑性能好,传热性能要均匀稳定;(5)环保和高性价比.3结语(I)保护渣具有绝热,保温,防止氧化,均匀传热,润滑和吸收夹杂物功能;(2)保护渣原料的选择应组成合理,成份稳定,既要满足连铸质量的需要,又要经济节约,尽可能就地取材,充分利用当地的废弃资源;(3)保护渣的选用应根据钢种,断面,拉速和振动参数等因素而定,在生产实践中应区别对待; (4)高拉速下,可选择低熔点,高熔速,低粘度,低析晶率和低析晶温度保护渣;(5)异型坯连铸保护渣,控制v K小断面在0.5一0. 67 Pa " s " m/min,大断面在0.5 Pa "s"m/min, 能够防止异型坯腹板纵裂;(6) CSP连铸用保护渣可采用低熔点,低粘度,低结晶温度,熔速快和玻璃性好的多组元保护渣。
连铸保护渣使用及几种漏钢形式介绍
连铸保护渣使用及几种漏钢形式介绍保护渣在连铸生产中是十分重要的。
然而保护渣性能的发挥与保护渣的正确使用方法是分不开的。
以下就保护渣的使用方法,及一些常见的铸坯缺陷讲述保护渣的正确使用方法。
一、表面纵横裂纹1、表面纵裂纹板坯表面发生纵裂纹,尤以碳含量在0.08—0.17%这个范围内的碳素结构钢和相应低合金钢为主。
主要原因是该类钢种的碳含量处于铁碳相图上的亚包晶范围或边缘,凝固时线收缩比较大,极易造成应力过于集中而致初生坯壳发生撕裂,从而产生纵裂纹。
1)钢水因素:A、钢水中的有害元素S、P、As等有害元素含量偏高,造成钢的热脆性和冷脆性增加,引发裂纹,根据经验:钢水中的S≥0.02%,P≥0.017%,发生纵裂纹的几率增加。
B、Mn/S比过小,一般Mn/S小于25,纵裂纹几率大大增加。
C、钢水的纯净度差,易引发纵裂纹等。
一、表面纵横裂纹2)设备因素A、结晶器锥度不合理,影响传热效果,易诱发纵裂纹。
B、结晶器铜板内部结构不密实,基体有气孔或杂质或镀层不均匀,易造成纵裂纹。
C、结晶器小槽局部有杂质堵塞或结垢,造成冷却不均易形成纵裂纹。
3)工艺因素A、结晶器水冷强度过大,易造成纵裂纹,主要体现在进出口水温差过大或热流密度过大上。
B、二冷水配水制度不合理,易造成纵裂纹扩张变大。
C、下水口不对中或倾斜,偏流或钢水出口处侵蚀严重,造成流场紊乱,易造成初生坯壳生长厚薄不均而致纵裂纹。
D、高过热度钢水浇铸易产生纵裂纹等等。
一、表面纵横裂纹4)操作因素A、加渣和挑渣造作不规则,易造成保护渣消耗流入不均匀,致使结晶器传热不均匀,影响坯壳的均匀成长而致应力过于集中而产生纵裂纹。
B、结晶器钢液面波动大或拉速单位时间内调整偏快,易产生纵裂纹。
C、拉速与浇钢温度不匹配易造成等。
一、表面纵横裂纹5)保护渣因素A、保护渣熔速、粘度、熔点不合理,易造成消耗过低和液渣层偏薄,容易产生纵裂纹。
B、保护渣的洗净率和析晶温度过低,造成传热过快,易产生纵裂纹。
最新连铸保护渣基础知识
最新连铸保护渣基础知识连铸保护渣在连铸过程中起着非常重要的作用,它可以保护钢水不受外界氧化,减少钢水中的杂质和气泡,并调整钢水的温度和流动性,确保最终铸造出高质量的产品。
本文将介绍最新连铸保护渣的基础知识,包括其主要成分、性能和应用。
一、连铸保护渣的主要成分连铸保护渣的主要成分通常包括氧化物、碳化物和氟化物等。
其中,氧化物是最常见的成分,包括SiO2、Al2O3、CaO、MgO等。
这些氧化物能够与钢水中的杂质和氧发生反应,形成不溶于钢水的氧化物渣和气泡,达到保护钢水的目的。
二、连铸保护渣的性能1. 抗渗透性:连铸保护渣应具有较好的抗渗透性,能形成一层致密的保护层,阻止钢水渗漏。
2. 熔化性:连铸保护渣应具有适当的熔化性,能够在高温下迅速熔化,并形成均匀的保护层。
3. 抗氧化性:连铸保护渣应具有较好的抗氧化性能,能够抵御高温氧化环境的侵蚀,保护钢水不受氧化。
4. 温度控制性:连铸保护渣应具有一定的温度控制性,能够吸收钢水的过剩热量,调整钢水的温度。
5. 流动性:连铸保护渣应具有一定的流动性,能够在结晶器内形成均匀的保护层,并顺利排出。
三、连铸保护渣的应用连铸保护渣广泛应用于钢铁冶炼和连铸过程中。
它可在连铸过程中形成一层保护层,保护钢水不受外界氧化,并减少钢水中的气泡和杂质。
此外,连铸保护渣还有以下应用:1. 调温:连铸保护渣可通过吸收钢水的过剩热量,调整钢水的温度,确保连铸过程中的温度控制。
2. 减少结晶器磨损:连铸保护渣可在结晶器内形成一层均匀的保护层,减少结晶器的磨损。
3. 改善钢水流动性:连铸保护渣具有一定的流动性,可改善钢水的流动性,使其在连铸过程中顺利流动。
4. 减少内包体生成:连铸保护渣中的氧化物和其他化合物能够与钢水中的氧和杂质发生反应,减少内包体的生成。
5. 提高产品质量:连铸保护渣能够保护钢水不受外界氧化,减少钢水中的杂质和气泡,从而提高最终产品的质量。
6. 减少能源消耗:连铸保护渣的应用可以减少能源消耗,提高冶炼效率。
钢种与保护渣的关系
钢种与保护渣的关系钢种与连铸保护渣的关系钢种与连铸保护渣的关系26 连铸保护渣技术,作为连铸生产的关键技术之一,对连铸生产的顺行和铸坯质量有着至关重要的影响,尤其是铸坯表面缺陷,基本上都是在结晶器内形成的,与保护渣有直接关系。
近几年来,该技术在实践中,如空心颗粒渣等的开发和广泛使用,对铸坯质量的改善、连铸生产工艺的稳定起了很大促进作用。
同时渣的基础性能如润滑和传热特性的研究也一直受到人们的重视。
一、不同钢种对保护渣性能设计要求不同成分的钢种.其钢水特性及其凝固特点有别,从而决定了对保护渣性能方面的要求。
1、低碳钢首先钢中w(C)<0.08%或0.06%。
这类钢高温机械性能好,凝固过程中不存在严重的相变体积变化,内应力及裂纹敏感性小,故通常以较高拉坯速度进行生产,以提高生产率。
基于低碳钢本身的凝固特点和质量要求,设计时主要考虑渣的润滑及消耗。
较高拉速要求尽量增大结晶器热流,加速钢水凝固,防止粘结漏钢,这要求保护渣结晶温度低、凝固温度适中,以确保低碳钢结晶器保护渣在950℃以上处于非晶体状态,使发生粘结漏钢的可能性最小。
在高速浇注时,为使足够的液态保护渣能流入铸流和结晶器内表面之间的区域,确保良好的润滑和足够的消耗,通常保护渣粘度选择较低的范围。
另外,此类钢种初生铁素体坯壳中[P]、[S]偏析小,初生坯壳强度高,铸坯振痕较深,故应使用保温性能较好的保护渣,提高弯月面初生坯壳温度,有利于减轻振痕过深带来的危去。
因此,连铸低碳钢满足以上各要求,就要通过设计具有一定的传热性能、良好的保温性能、良好的非金属吸收、良好的润滑和性能稳定的保护渣来获得。
2、中碳钢中碳钢钢水凝固过程中发生己δ→γ相变,体积强烈收缩,此钢种裂纹敏感性大,容易产生表面裂纹,特别是高拉速时。
避免纵横向裂纹是首要考虑的问题,为此,中碳钢用保护渣设计的重点应放在控制从铸坯传往结晶器的热流上,限制结晶器热通量,希望保护渣具有较大热阻。
因此,应选用凝固温度高、结晶温度也高的保护渣,利用结晶质膜中的“气隙”,使保护渣传热速度减缓,有助于减小铸坯在冷却过程中产生的热应力。
- 1、下载文档前请自行甄别文档内容的完整性,平台不提供额外的编辑、内容补充、找答案等附加服务。
- 2、"仅部分预览"的文档,不可在线预览部分如存在完整性等问题,可反馈申请退款(可完整预览的文档不适用该条件!)。
- 3、如文档侵犯您的权益,请联系客服反馈,我们会尽快为您处理(人工客服工作时间:9:00-18:30)。
不同连铸工艺及品种的保护渣技术特征2标准化文件发布号:(9312-EUATWW-MWUB-WUNN-INNUL-DQQTY-3. 中碳钢板坯连铸保护渣根据钢水凝固特征,国际上通常将钢中[C]≈~%的钢种称为中碳钢,而在我国,则将[C] ≈~%的钢种划入中碳钢之列,但不论怎样划分,中碳钢在我国目前连铸生产品种中所占比例最高,此外,不少中碳低合金钢亦归入此列。
由于中碳钢特殊的凝固特性,铸坯表面容易产生纵裂纹、星状裂纹等典型缺陷,针对这类问题,结晶器保护渣必须采取不同于低碳和超低碳钢的特殊对策,才能保证无缺陷铸坯的工业化生产。
裂纹敏感性包晶钢板坯连铸保护渣对于[C]=~%的钢种,凝固过程中发生包晶反应,结晶器弯月面以下50mm 区域初生坯壳收缩大,晶粒粗大(如图24,图25),初生坯壳生长不均匀,易产生裂纹,这是包晶钢裂纹敏感的主要原因。
为此,许多研究者通过模型计算和实验检测分析了结晶器热流量与铸坯纵裂纹的关系,指出在弯月面下部45mm处,对于低碳钢,当热流密度超过×106W/m2, 对于中碳钢,当热流密度超过×106W/m2时,铸坯表面裂纹指数急剧增大,铸坯易出现表面纵裂纹(见图26)。
因此,在实际生产中一方面减弱结晶器水冷强度,另一方面主要通过采用结晶体状态的保护渣。
国内外目前倾向于采用高碱度保护渣,通过:①减少透明玻璃体达到减少辐射传热;②结晶体内的微孔和界面极大地削弱晶格振动,从而减弱传导传热,达到减缓传热和减少裂纹的目的。
但是,当保护渣碱度过高,析晶温度过高时易严重恶化铸坯润滑状况,导致铸坯粘结和漏钢,连铸生产被迫采用降低拉坯速度的技术路线,这使得连铸机生产率和产能降低20%~30%;如何协调好玻璃体和结晶体的比例,这在国内外许多连铸生产中都还没有得到妥善解决。
为了开发出对中碳钢连铸工艺适应性强的结晶器保护渣,必须针对上述问题,综合分析保护渣主要组份对结晶性能和玻璃化特性的综合影响情况,在此基础上,才能设计保护渣配方。
3.1.1 保护渣组成与结晶性能和玻璃化特性的基本关系为了弄清和明确保护渣组份对其结晶行为的影响规律,本研究首先采用化学纯试剂配制渣样(见表16),采用旋转粘度计测试保护渣在1300℃下的粘度,并在降温条件下测试保护渣粘度--温度曲线关系。
根据粘度--温度曲线,采用回归方法确定保护渣冷却过程中最大粘流活化能变化值max E及其对应的转折温度Tc, 测试粘度后的熔渣注入金属模内自然冷却(所有渣样重量和冷却条件相同),冷凝后的渣样用显微镜观察其断口形貌,测试结晶体和玻璃体比例,并用半球点法测试保护渣熔化温度。
表16 实验研究用渣样基本组成(重量比)渣号 CaO SiO2CaF2Al2O3MgO Na2O R(CaO/SiO2)756636407566No.2364010566a364013566No.2c364016566364019566383875663775667566756675667566表16中各渣样半球点熔化温度为1112~1180℃,1300℃下的粘度为~ , 该参数与许多实际生产中使用的保护渣的熔化温度、粘度值相近,说明在表16所示组成范围内,研究保护渣结晶性能,其结果对实际生产具有参考价值。
(1)连铸保护渣玻璃化特性和结晶性能的概念填充于铸坯坯壳与结晶器壁间隙内的保护渣,主要作为拉坯过程的润滑剂和铸坯向结晶器的传热介质。
为了充分发挥保护渣的润滑功能以减低拉坯阻力, 除采用合理的结晶器振动参数,还要求与铸坯接触的渣膜处于液体状态,通过液体润滑以最大限度地减小铸坯受到的摩擦力。
这不仅要求保护渣在1300℃下具有较低的粘度,而且要求保护渣在冷凝过程中粘度变化缓慢,避免高熔点固相质点析出而使粘度急剧升高。
即希望保护渣粘度随温度的变化关系与玻璃的粘度随温度变化关系相似,这类保护渣冷凝后具有与玻璃相似的非晶态结构。
鉴于此,粘度--温度曲线关系特征和凝固渣样中玻璃体比例,024********120012501300温度,℃粘度,P a .s01234512201240126012801300温度,℃粘度,P a .S(a )玻璃化特性良好的保护渣 (b )结晶性能良好的保护渣图27 保护渣粘度--温度关系曲线即保护渣的玻璃化特性,来表征保护渣的润滑能力。
玻璃性好,意味着保护渣的润滑功能强。
如图22所示,对不同渣样的粘度--温度曲线用阿伦尼乌斯公式进行回归,可得出粘流活化能变化最大值max E 及其对应的粘度--温度曲线转折温度Tc 。
利用max E 和Tc 及凝固渣样中玻璃体比例可分析比较保护渣的玻璃化特性。
与玻璃化过程相反的结构变化行为就是结晶或析出晶体。
结晶性能是保护渣冷凝过程中析出晶体的能力,包括结晶温度和结晶比例。
因为通过保护渣渣膜的传热主要有辐射和导热两种方式,渣膜中结晶体比例增多,不仅透明度降低而减少辐射传热,而且结晶层由于温度梯度而出现微裂纹,可进一步减少传导传热。
因此,通过提高保护渣的结晶性能,可控制或削弱结晶器内初生坯壳的凝固传热强度。
这种功效有助于减少某些钢种的铸坯裂纹缺陷。
显然,通过提高结晶温度虽可提高保护渣的结晶性能,但玻璃性能恶化,不利于高拉速下的铸坯润滑。
只有协调好玻璃化特性和结晶性能之间的矛盾关系,才能满足中碳钢等裂纹敏感类钢种的高速连铸工艺对保护渣的基本要求。
(2)碱度对保护渣玻璃化特性和结晶性能的影响根据化学成分的不同表述形式,通常将连铸保护渣碱度分别表示为二元碱度)(%)(%2SiO wt CaO wt R =和综合碱度)(%])78/56([%22SiO wt CaF CaO wt R +=∑。
从图28可知,随着碱度升高,保护渣冷凝过程中最大粘流活化能变化值不断增大,表明保护渣玻璃化特性减弱,图29结果进一步表明,保护渣冷凝后玻璃体减少,结晶率增大。
当碱度R 大于,保护渣中开始析出晶体;二元碱度R 达到~,综合碱度R 达到时, 保护渣结晶率达到30~60%,最大粘流活化能变化值升高趋势减缓,说明在这种碱度值下保护渣已基本丧失玻璃化特性,从图30可看出,当保护渣碱度大于,保护渣粘度-温度曲线的转折温度超过1200℃,这将出现图2(b)所示的现象,易导致液态渣膜急剧减薄,铸坯得不到充分的润滑,易发生漏钢事故,这在国内外的许多连铸生产中已得到证实。
因此,片面强调提高保护渣碱度以加强结晶能力而控制铸坯凝固传热的方法并不可取。
为协调保证铸坯的润滑和控制传热,0.0E+001.0E+052.0E+053.0E+054.0E+050.80.91 1.11.2碱度 Rm a x ΔE , J /m o l0.0E+001.0E+052.0E+053.0E+054.0E+050.911.11.21.31.4综合碱度 ΣRm a x ΔE , J /m o l(a) 碱度R=CaO/SiO 2 (b) 综合碱度R=[CaO+(56/78)*CaF 2]/SiO 2图28 保护渣碱度与最大粘流活化能变化值的关系(a) 碱度R=CaO/SiO 2 (b) 综合碱度 R=[CaO+(56/78)*CaF 2]/SiO 2图29 保护渣碱度与结晶率的关系204060801000.80.91 1.1 1.2碱 度 R结晶率, %020*********0.901.001.10 1.20 1.301.40综合碱度∑R保护渣结晶率, %在表16所示的组成范围内, 可将二元碱度R 控制在~,综合碱度控制在~的范围内,这种条件下保护渣粘度-—温度曲线的转折温度约1130~1160℃,结晶体比例约30~70%; 根据该结果,要求保护渣碱度变化范围较窄,针对具体的连铸工艺条件所,碱度值允许波动的范围可能更窄,这就要求提高保护渣原材料的稳定性和加强生产工艺的可控性。
(3) CaF 2对保护渣玻璃化特性和结晶性能的影响在二元碱度R 为的渣样基础上,分别外加不同含量的CaF 2,测试结果表明,随CaF 2含量增加,保护渣最大粘流活化能变化值增大(见图31),玻璃化特性减弱。
当CaF 2含量大于13%,渣样冷凝过程中析出晶体(见图32),当CaF 2含量超过15%,粘度-温度曲线转折温度超过1200℃。
因此,在渣样的组成条件下,为了协调保护渣玻璃化特图32 CaF 2含量与保护渣结晶率的关系 图33 CaF 2含量与转折温度的关系性和结晶性能,CaF 2含量只能在13~15%这一较窄的区间内进行调节。
CaF 2含量过高,不仅使Tc 超过1200℃而导致保护渣丧失润滑功能,而且在结晶器钢液面上熔渣层对水口的侵蚀加剧,不利于多炉连浇和连铸生产的顺行。
图31 CaF 2含量与保护渣最大粘流活化能变化值的关系(4) 特殊组份对保护渣玻璃化特性和结晶性能的影响从前述实验结果可知, 仅调节保护渣碱度和CaF2含量, 还不能充分协调保护渣玻璃化特性和结晶性能之间的矛盾以有效发挥保护渣的润滑和控制传热功能。
随着碱度升高和CaF2含量增加, 保护渣结晶性能增强, 玻璃化特性恶化,因此,碱度和CaF2含量只能在一较窄的范围内折中调节,这种限制无疑给保护渣的成分控制和生产增加了难度。
为解决上述弊端,只有在增加保护渣结晶率的同时降低析晶温度和转折温度,才能在保证润滑的前提下加强对铸坯凝固传热的控制。
根据协调保护渣玻璃化特性和结晶性能的上述要求,采用合成方法制得了特殊组分(简称comp)。
随组分comp含量的增加,保护渣结晶体比例增加,粘度—温度曲线的转折温度降低(见图34和图35),当comp含量超过4%后,结晶体比例的增加趋势和转折温度Tc的降低趋势均趋于平缓,由于该组分价格较高,实际应用中可控制保护渣中comp含量为2~4%。
图34 com含量与保护渣结晶率的关系图35 com含量与转折温度的关系3.1.2 保护渣组成与传热特性的关系为了通过保护渣有效控制中碳钢凝固过程中的冷却强度,不仅要了解渣样组成与结晶性能和玻璃化特性的关系,还应综合考虑组成与渣膜传热特性的作用规律,才能正确地设计这类钢种的保护渣。
由于测试保护渣凝固过程中传热特性这一工作在国内其他单位尚无先例,无现成方法和设备装置,因此,本项目结合重庆大学进行的一些前期工作,采用图36所示装置检测保护渣冷凝过程中的导温系数,在此基础上,分析和协调保护渣组份与传热特性的关系。
二硅化钼炉熔渣漏斗上平板下平板熔渣不锈钢容器定位器热电偶调节水平螺钉微型计算机数据采集系统图 36 保护渣导温系数测定装置示意图实验研究除考查了前述碱度、CaF2、comp组份对传热的影响情况外,还进一步分析了TiO2、SiC、CaSi这些外加组份对导温系数的作用规律。
图37和图38表明,在650~1000℃温度范围内,增加碱度和CaF2均使渣膜导温系数缓慢降低,对渣样作矿相分析发现,在碱度和CaF2含量较高时,渣膜中析出Ca4F2Si2O7 Ca2SiO2F2晶体,结晶态渣膜在减弱热传导方面发挥了重要作用。