最新多路数据采集系统方案
多路数据采集系统设计
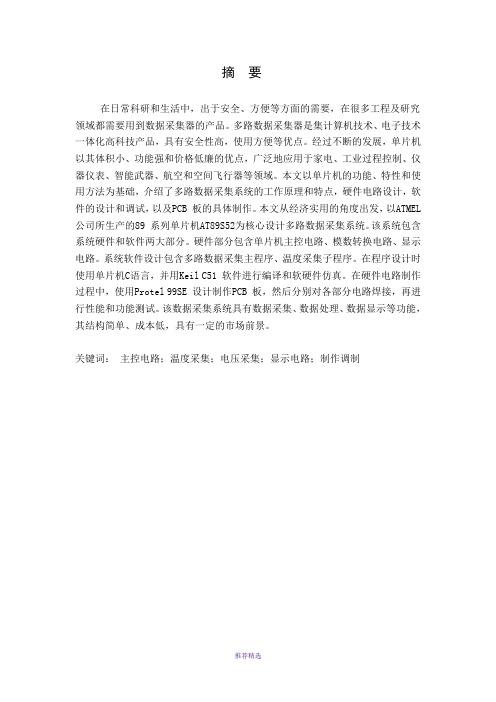
摘要在日常科研和生活中,出于安全、方便等方面的需要,在很多工程及研究领域都需要用到数据采集器的产品。
多路数据采集器是集计算机技术、电子技术一体化高科技产品,具有安全性高,使用方便等优点。
经过不断的发展,单片机以其体积小、功能强和价格低廉的优点,广泛地应用于家电、工业过程控制、仪器仪表、智能武器、航空和空间飞行器等领域。
本文以单片机的功能、特性和使用方法为基础,介绍了多路数据采集系统的工作原理和特点,硬件电路设计,软件的设计和调试,以及PCB 板的具体制作。
本文从经济实用的角度出发,以ATMEL 公司所生产的89 系列单片机AT89S52为核心设计多路数据采集系统。
该系统包含系统硬件和软件两大部分。
硬件部分包含单片机主控电路、模数转换电路、显示电路。
系统软件设计包含多路数据采集主程序、温度采集子程序。
在程序设计时使用单片机C语言,并用Keil C51 软件进行编译和软硬件仿真。
在硬件电路制作过程中,使用Protel 99SE 设计制作PCB 板,然后分别对各部分电路焊接,再进行性能和功能测试。
该数据采集系统具有数据采集、数据处理、数据显示等功能,其结构简单、成本低,具有一定的市场前景。
关键词:主控电路;温度采集;电压采集;显示电路;制作调制AbstractIn daily scientific research and life,Stemming from safe, is convenient and so on the aspect need,All need to use in very many projects and the research area to the data acquisition product。
The multichannel data acquisition is collection computer technology, the electronic technology integration high tech product,Has the security to be high,Merit and so on easy to operate。
《2024年基于单片机和LabVIEW的多路数据采集系统设计》范文

《基于单片机和LabVIEW的多路数据采集系统设计》篇一一、引言在现代化工业和科技应用中,数据采集扮演着举足轻重的角色。
为了满足多路数据的高效、准确采集需求,本文提出了一种基于单片机和LabVIEW的多路数据采集系统设计。
该系统设计旨在实现多通道、高精度的数据采集,为工业自动化、科研实验等领域提供可靠的解决方案。
二、系统设计概述本系统设计以单片机为核心控制器,结合LabVIEW软件进行数据采集、处理和显示。
系统采用模块化设计,包括数据采集模块、数据处理模块、数据传输模块以及LabVIEW上位机显示模块。
通过各模块的协同工作,实现多路数据的实时采集和监控。
三、硬件设计1. 单片机选型及配置系统采用高性能单片机作为核心控制器,具有高速运算、低功耗等特点。
单片机配置包括时钟电路、复位电路、存储器等,以满足系统运行需求。
2. 数据采集模块设计数据采集模块负责从传感器中获取数据。
本系统采用多路复用技术,实现多个传感器数据的并行采集。
同时,采用高精度ADC(模数转换器)对传感器数据进行转换,以保证数据精度。
3. 数据传输模块设计数据传输模块负责将采集到的数据传输至单片机。
本系统采用串口通信或SPI通信等方式进行数据传输,以保证数据传输的稳定性和实时性。
四、软件设计1. 单片机程序设计单片机程序采用C语言编写,实现对传感器数据的采集、处理和传输等功能。
程序采用中断方式接收数据,避免因主程序繁忙而导致的漏采现象。
2. LabVIEW上位机程序设计LabVIEW是一种基于图形化编程的语言,适用于数据采集系统的上位机程序设计。
本系统采用LabVIEW编写上位机程序,实现对数据的实时显示、存储和分析等功能。
同时,LabVIEW程序还具有友好的人机交互界面,方便用户进行操作和监控。
五、系统实现及测试1. 系统实现根据硬件和软件设计,完成多路数据采集系统的搭建和调试。
通过实际测试,验证系统的稳定性和可靠性。
2. 系统测试对系统进行实际测试,包括多路数据采集的准确性、实时性以及系统的稳定性等方面。
多路数据采集系统方案word参考模板

`数据采集系统1、系统方案选择和论证1.1题目要求1.1.1基本要求1.1.2发挥部分1.2系统基本方案1.2.1各模块电路的方案选择及论证1.2.2系统各模块的最终方案2、系统硬件设计与实现2.1系统硬件模块关系2.2 主要单元电路的设计2.2.1正弦信号发生器设计2.2.2F/V变换部分设计2.2.3信号采集部分处理2.2.4通信模块部分设计2.2.5数据地址显示电路设计3、系统软件设计3.1主单片机程序3.1.1主机发送子程序3.1.2主机数据处理子程序3.1.3主机显示子程序3.1.4主机主程序3.2从单片机程序3.2.1数据采集子程序3.2.2从机中断接受子程序3.2.3从机子程序4、系统测试附录1:产品使用说明附录2:元件清单参考文献1. 系统方案选择和论证1.1.1基本要求设计一个八路数据采集系统,系统原理框图如下:主控器能对50米以外的各路数据,通过串行传输线(实验中用1米线代替)进行采集的显示和显示。
具体设计任务是:(1)现场模拟信号产生器。
(2)八路数据采集器。
(3)主控器。
二、设计要求1.基本要求(1)现场模拟信号产生器:自制一正弦波信号发生器,利用可变电阻改变振荡频率,使频率在200Hz~2kHz范围变化,再经频率电压变换后输出相应1~5V直流电压(200Hz对应1V,2kHz对应5V)。
(2)八路数据采集器:数据采集器第1路输入自制1~5V直流电压,第2~7路分别输入来自直流源的5,4,3,2,1,0V直流电压(各路输入可由分压器产生,不要求精度),第8路备用。
将各路模拟信号分别转换成8位二进制数字信号,再经并/串变换电路,用串行码送入传输线路。
(3)主控器:主控器通过串行传输线路对各路数据进行采集和显示。
采集方式包括循环采集(即1路、2路……8路、……1路)和选择采集(任选一路)二种方式。
显示部分能同时显示地址和相应的数据。
2.发挥部分(1)利用电路补偿或其它方法提高可变电阻值变化与输出直流电压变化的线性关系;(2)尽可能减少传输线数目;(3)其它功能的改进(例如:增加传输距离,改善显示功能)。
多路数据采集系统设计
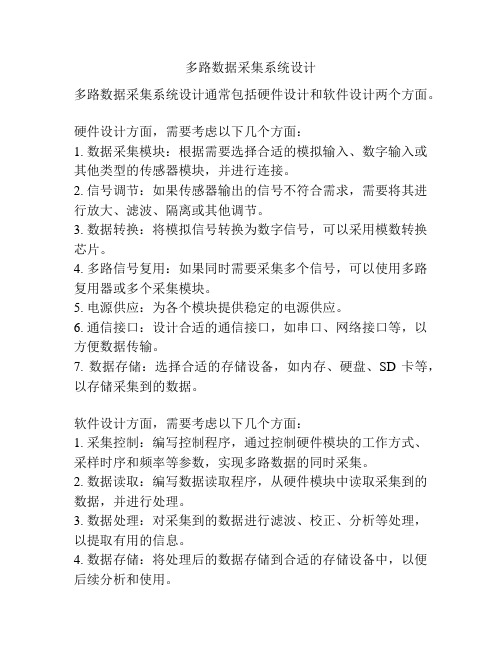
多路数据采集系统设计
多路数据采集系统设计通常包括硬件设计和软件设计两个方面。
硬件设计方面,需要考虑以下几个方面:
1. 数据采集模块:根据需要选择合适的模拟输入、数字输入或其他类型的传感器模块,并进行连接。
2. 信号调节:如果传感器输出的信号不符合需求,需要将其进行放大、滤波、隔离或其他调节。
3. 数据转换:将模拟信号转换为数字信号,可以采用模数转换芯片。
4. 多路信号复用:如果同时需要采集多个信号,可以使用多路复用器或多个采集模块。
5. 电源供应:为各个模块提供稳定的电源供应。
6. 通信接口:设计合适的通信接口,如串口、网络接口等,以方便数据传输。
7. 数据存储:选择合适的存储设备,如内存、硬盘、SD卡等,以存储采集到的数据。
软件设计方面,需要考虑以下几个方面:
1. 采集控制:编写控制程序,通过控制硬件模块的工作方式、采样时序和频率等参数,实现多路数据的同时采集。
2. 数据读取:编写数据读取程序,从硬件模块中读取采集到的数据,并进行处理。
3. 数据处理:对采集到的数据进行滤波、校正、分析等处理,以提取有用的信息。
4. 数据存储:将处理后的数据存储到合适的存储设备中,以便后续分析和使用。
5. 用户接口:设计合适的用户界面,以方便用户对系统进行操作和监视。
综上所述,多路数据采集系统设计需要综合考虑硬件和软件两个方面,确保系统能够稳定、高效地采集和处理多路数据。
基于STC12c5a60s2多路数据采集系统

该模块工作在远距离终端,作为模拟待采样的信号源,产生正弦波。对于该 模块有以下两种方案:
方案一:采用ICL8038集成芯片。构成三角波发生器及正弦整形电路。该IC 电路属于积分型施密特压控多谐振荡器,工作范围0.001HZ~300KHZ,完全可 以达到设计要求。
方案二:LC正弦波振荡器。有电容三点式和电感三点式振荡器以及克拉波和 西勒振荡器
1.2.2 系统各模块的最终方案
根据以上方案,结合器件和实现条件等因素,确定如下方案: (1).利用ICL8038集成芯片来作为正弦波信号的产生器。
(2)F/V变换模块采用LM331频压变换器。 (3).采用双单片机STC12C5A60S2来实完成信号的采集与处理。 (4).单片机之间的通信选取RS-485的通信标准。 (5).显示模块的选用LCD1602液晶显示。 小结:这一部分主要介绍了整个系统的构思,以及各个模块的方案比较与选择。
(5)显示模块 该模块在主控端,用于显示接收到的数据。 方案一:采用数码管显示; 方案二:采用 LCD 液晶显示; 方案一要额外增加锁存器等驱动电路,而且不稳定,调试较为麻烦;而方案
二中LCD则具有功耗小、平面直角显示以及影象稳定不闪烁,可视面积大,画面 效果好,抗干扰能力强等特点。所以选用方案二。
STC12C5A60S2系列单片机ADC(A/D转换器)的结构如下图所示。
A/D 转 换 结 束 后 , 最 终 的 转 换 结 果 保 存 到 ADC 转 换 结 果 寄 存 器 ADC_RES 和 ADC_RESL,同时,置位ADC控制寄存器ADC_CONTR中的A/D转换结束标志位ADC_FLAG, 以供程序查询或发出中断申请。模拟通道的选择控制由ADC控制寄存器ADC_CONTR 中的CHS2 ~ CHS0确定。
多通道数据采集系统的设计与实现

多通道数据采集系统的设计与实现近年来,随着科技的不断发展和数据的迅速增长,对于多通道数据采集系统的需求越来越迫切。
多通道数据采集系统旨在通过多个输入通道同时采集、传输和处理多组数据,以满足大规模数据采集和处理的需求。
本文将详细介绍多通道数据采集系统的设计与实现。
1. 系统需求分析在设计多通道数据采集系统之前,首先要明确系统的需求。
根据具体的应用场景和目标,我们需要确定以下几个方面的需求:1.1 数据采集范围:确定需要采集的数据范围,包括数据类型、数据量和采集频率等。
这将直接影响系统的硬件选择和设计参数。
1.2 数据传输和存储要求:确定数据传输和存储的方式和要求。
例如,是否需要实时传输数据,是否需要数据缓存和压缩等。
1.3 系统的实时性要求:确定系统对数据采集和处理的实时性要求。
根据实际应用场景,可以确定系统对数据延迟和响应时间的要求。
1.4 系统的可扩展性:考虑系统的可扩展性,以满足未来可能的扩展需求。
这包括硬件和软件的可扩展性。
2. 系统设计在需求分析的基础上,我们进行多通道数据采集系统的设计。
系统设计主要包括硬件设计和软件设计两个方面。
2.1 硬件设计根据需求分析中确定的数据采集范围和要求,我们选择合适的硬件设备进行数据采集。
常用的硬件设备包括传感器、模拟信号采集卡和数字信号处理器等。
2.2 传感器选择根据需要采集的数据类型,选择合适的传感器进行数据采集。
不同的传感器适用于不同的数据类型,如温度传感器、压力传感器、光传感器等。
2.3 采集卡设计针对多通道数据采集系统的特点,我们需要选择合适的模拟信号采集卡进行数据采集。
采集卡应具备多个输入通道,并能够同时采集多个通道的数据。
2.4 数字信号处理器设计针对采集到的模拟信号数据,我们需要进行数字信号处理。
选择合适的数字信号处理器进行数据处理,如滤波、采样和转换等。
2.5 软件设计针对系统的需求和硬件的设计,我们需要进行软件设计,以实现数据采集、传输和处理。
多路数据采集系统的设计

C NE J
M 0V M 0V
A ,# 0 0 H S END
A . R6 R6. #F0H
U MP
ORG
0 3H 02 C0M 0 0H 04 S . #7 P 0H I E, #O OH
L MP | J
0RG M AI : M OV N M 0V ANL
A . 21 H
L P:
C R C;1 位A 数据转换成标准数据格式存人 L 2 D
存储单元
M OV A . R2
M OV
M 0V
RRC A M 0V R2. A M OV A . R3
AGAI : M OV N OR L M 0V
和 18 使 接 口 电平 匹 配 。 49
2 电路 框 图 .
模 拟
最
设计 任 务 本 次 设计 的数 据采集 系 统 的任 务是 对 电压 模 拟量进 行采
一
、
集 ,并在P 机上 将采集数据和相应 波形 显示 出 。 C
二 设 计 方案
设计 任务可 以分成两大 部份 ,一 部分是数 据采 集卡的硬件 电路 设计 ,这 里包括 模拟 输入 电路 、时序控 制 、A D 换 、数 /转 据存储 、与P C的接 口和数据交换 等 。另外 一部分是 上位机 的数 据显示 软件设计 ,这 部分包括 接收采集 板 的数 据并将数 据换算 成显示 数据和 现实波形 供采集 人员观察 。下 面我们从这 两部分 进行设计 。
统 ,这 种 系统 的基 本 思想 是 :在采 集 现场 ,将 传 感器 采集 的 制 ,而单片机的最终程序选择可在P 机中进行 。 C 数 据通 讯 :采用串行数据通 讯 口与P 机进行通信 。单片机 c c l 48 串 口将数 据上 传至 P 机 ,在P 机 上进 行分 析处 理并 显示数 据 的串 口电平 与P 机 的串 E 电平不 匹配 ,采用 电平转换 芯片1 8 C C
《2024年基于单片机和LabVIEW的多路数据采集系统设计》范文

《基于单片机和LabVIEW的多路数据采集系统设计》篇一一、引言随着科技的发展,多路数据采集系统在工业、医疗、环境监测等领域的应用越来越广泛。
为了满足多路数据的高效、准确采集需求,本文提出了一种基于单片机和LabVIEW的多路数据采集系统设计。
该系统设计旨在实现多路信号的同时采集、处理及实时监控,以适应复杂多变的应用环境。
二、系统概述本系统采用单片机作为核心控制器,结合LabVIEW软件进行数据采集和处理。
系统由多个传感器模块、单片机控制器、数据传输模块以及上位机软件组成。
传感器模块负责实时监测各种物理量,如温度、湿度、压力等,并将采集到的数据传输给单片机控制器。
单片机控制器对数据进行处理和存储,并通过数据传输模块将数据发送至上位机软件进行进一步的处理和显示。
三、硬件设计1. 传感器模块:传感器模块采用高精度、高稳定性的传感器,如温度传感器、湿度传感器等,实现对物理量的实时监测。
传感器模块的输出为数字信号或模拟信号,方便与单片机进行通信。
2. 单片机控制器:采用具有高速处理能力的单片机作为核心控制器,实现对数据的快速处理和存储。
单片机与传感器模块和数据传输模块进行通信,实现数据的实时采集和传输。
3. 数据传输模块:数据传输模块采用无线或有线的方式,将单片机控制器的数据传输至上位机软件。
无线传输方式具有灵活性高、安装方便等优点,但需要考虑信号干扰和传输距离的问题;有线传输方式则具有传输速度快、稳定性好等优点。
四、软件设计1. 单片机程序设计:单片机程序采用C语言编写,实现对传感器数据的实时采集、处理和存储。
同时,程序还需要与上位机软件进行通信,实现数据的实时传输。
2. LabVIEW程序设计:LabVIEW程序采用图形化编程语言编写,实现对单片机传输的数据进行实时处理和显示。
同时,LabVIEW程序还可以实现对数据的存储、分析和报警等功能。
五、系统实现1. 数据采集:传感器模块实时监测各种物理量,并将采集到的数据传输给单片机控制器。
- 1、下载文档前请自行甄别文档内容的完整性,平台不提供额外的编辑、内容补充、找答案等附加服务。
- 2、"仅部分预览"的文档,不可在线预览部分如存在完整性等问题,可反馈申请退款(可完整预览的文档不适用该条件!)。
- 3、如文档侵犯您的权益,请联系客服反馈,我们会尽快为您处理(人工客服工作时间:9:00-18:30)。
多路数据采集系统方案`数据采集系统1、系统方案选择和论证1.1题目要求1.1.1基本要求1.1.2发挥部分1.2系统基本方案1.2.1各模块电路的方案选择及论证1.2.2系统各模块的最终方案2、系统硬件设计与实现2.1系统硬件模块关系2.2 主要单元电路的设计2.2.1正弦信号发生器设计2.2.2F/V变换部分设计2.2.3信号采集部分处理2.2.4通信模块部分设计2.2.5数据地址显示电路设计3、系统软件设计3.1主单片机程序3.1.1主机发送子程序3.1.2主机数据处理子程序3.1.3主机显示子程序3.1.4主机主程序3.2从单片机程序3.2.1数据采集子程序3.2.2从机中断接受子程序3.2.3从机子程序4、系统测试附录1:产品使用说明附录2:元件清单参考文献1. 系统方案选择和论证1.1.1基本要求设计一个八路数据采集系统,系统原理框图如下:主控器能对50米以外的各路数据,通过串行传输线(实验中用1米线代替)进行采集的显示和显示。
具体设计任务是:(1)现场模拟信号产生器。
(2)(2)八路数据采集器。
(3)(3)主控器。
二、设计要求1.基本要求(1)现场模拟信号产生器:自制一正弦波信号发生器,利用可变电阻改变振荡频率,使频率在200Hz~2kHz范围变化,再经频率电压变换后输出相应1~5V直流电压(200Hz对应1V,2kHz对应5V)。
(2)八路数据采集器:数据采集器第1路输入自制1~5V直流电压,第2~7路分别输入来自直流源的5,4,3,2,1,0V直流电压(各路输入可由分压器产生,不要求精度),第8路备用。
将各路模拟信号分别转换成8位二进制数字信号,再经并/串变换电路,用串行码送入传输线路。
(3)主控器:主控器通过串行传输线路对各路数据进行采集和显示。
采集方式包括循环采集(即1路、2路……8路、……1路)和选择采集(任选一路)二种方式。
显示部分能同时显示地址和相应的数据。
2.发挥部分(1)利用电路补偿或其它方法提高可变电阻值变化与输出直流电压变化的线性关系;(2)尽可能减少传输线数目;(3)其它功能的改进(例如:增加传输距离,改善显示功能)。
1.2系统基本方案根据题目要求系统模块分可以划分为:现场信号发生模块,V/F 变换模块,信号采集处理模块,通信控制模块,显示模块。
系统的框图如图1.2.1 所示。
为实现各模块的功能,分别做了几种不同的设计方案并进行了论证。
下图为系统基本模块图:1.2.1各模块电路的方案选择及论证(1)现场信号发生模块该模块工作在远距离终端,作为模拟待采样的信号源,产生正弦波。
对于该模块有以下两种方案:方案一:采用ICL8038 集成芯片。
构成三角波发生器及正弦整形电路。
该IC 电路属于积分型施密特压控多谐振荡器,工作范围0.001HZ~300KHZ,完全可以达到设计要求。
方案二:由LM358 运放组成的幅值、频率可调的正弦振荡器。
图 1.2.2 所示为由 LM358 组成的正弦波发生器A1 组成的电路相当于比例积分器,A2 所组成的电路相当于比较器。
接通电源后,A2 输出为低电平(0V),而 A1 输出为高电平,由于有电容 C,则这个高电平是逐渐增长的,即随着电容 C经 RW2、R2 去路不断地充电,使 A1 的 1 脚电位逐渐增长。
当其电位增长到高于 Vcc/2 时,A2 输出变为高电平。
A2 的高电平使 A1 反相端为高电平,则 A1 输出力图为低电平,但由于 C 上电压不能突变,其输出端电位只能随电容 C 经 RW2、R2 支路反相充电而下降。
当下降到低于 VCC/2 时,A2 输出又变成低电平。
于是 A1 输出力图为高电平,C 由于上的电压不能突变,其输出端电位只能随 C 的充电逐渐上升……如此工作产生正弦波。
其具体电路图如图 1.2.2 所示。
振荡频率:f=1/2π(RW2+R2)C。
调节 RW2 可改变振荡频率。
频率变化范围为:2.9~5.3KHz。
输出信号的幅度调节通过改变 RW1 来实现。
幅度调节范围为:2~6V。
(2)F/V 变换模块F/V 变换模块采用模拟集成频率--电压变换器 LM331。
LM331 具有精度高、线形度高,温度系数低,功耗低动态范围宽等一系列优点,目前已经广泛应用于数据采集和自动控制中。
(3)信号采集处理模块该模块功能主要是将输入过来的模拟信号转化成数字信号,实现数据的采集与处理。
现在提出以下方案来完成此功能。
A/D 采集模块工作在远程数据采集端,用于将模拟信号转换成数字信号。
计划采用 ADC0809作为模数转换器。
ADC0809 为 CMOS 集成电路,属于逐位逼近比较型的转换器,分辨率为 8 位,转换时间为 100us,数据输出端内部具有三态输出锁存器,可以与单片机直接连接;而界具有 8路模拟开关,可直接连接8 个模拟量,并可程控选择对其中一个模拟量进行转化。
它与单片机连接简单,使用方便。
(4)通信控制模块方案一:由于信号采集处理采用双单片机,即在数据采集的远端、近端均采用单片机控制,远端完成数据的采集、抽样、平滑、发送;近端完成数据的接收、校验、纠错、处理与显示等。
且由于两单片机之间的通讯距离较远,故采用 RS-485 的通信标准。
方案二:可以在信号采集处理模块中采用模拟电路实现信号的串行/并行转换,而只在数据显示时用单片机来控制实现,故此时的通信控制是用单片机的输出控制信号来控制模拟电路的工作的。
(5)显示模块方案一:采用液晶显示屏和通用矩阵键盘。
液晶显示屏(LCD)具有功耗小、轻薄短小无辐射危险,平面直角显示以及影象稳定不闪烁,可视面积大,画面效果好,抗干扰能力强等特点。
但由于只需显示三位温度值,信息量比较少,且由于液晶是以点阵的模式显示各种符号,需要利用控制芯片创建字符库,编程工作量大,控制器资源占用较多,其成本也偏高。
方案二:采用四位 LED 七段数码管分别显示通道地址、电压值。
数码管具有:低能耗、低损耗、低压、寿命长、耐老化,对外界环境要求较低。
同时数码管采用 BCD 编码显示数字,程序编译容易,资源占用较少。
1.2.2 系统各模块的最终方案根据以上方案,结合器件和实现条件等因素,确定如下方案:(1).利用 ICL8038 集成芯片来作为正弦波信号的产生器。
(2).F/V 变换模块采用 LM331 频压变换器。
(3).采用双单片机 MSP430F5529 和 ADC12 来实完成信号的采集与处理。
(4).单片机之间的通信选取 RS-232 的通信标准。
(5).显示模块的实现是选用12864液晶屏动态显示。
2. 硬件设计与实现2.1 系统硬件模块关系图 2.1.1 所示为系统硬件电路单元模块关系图方案一:采用ICL8038-2正弦波信号发生器:方案二:2.2.主要单元电路设计2.2.1 正弦波信号发生器设计方案一:设计中采用ILC8038来产生正弦波。
通过调节RP1来改变频率,其范围值为 20HZ ∽20KHZ ,RP3 用于改善正弦波负向失真。
RP4 改善正弦波正向失真。
其电路图如 2.2.1图 2.2.1 正弦波信号发生电路上图还可以同时产生方波、三角波等信号方案二:采用文氏电路产生频率可调的正弦波信号文氏电路2.2.2 F/V 变换电路设计将正弦信号输入到 F/V 变换电路之前要对正弦信号进行滤波、放大。
其具体的电路变换兔如下。
图 2.2.2 所示为系统 F/V 变换电路图。
F/V 变换模块采用精密且廉价的 F/V 变换器 LM331,此集成电路线形度可达0.06%,该 IC输出电压 Vo 与输出频率的关系为 Vo=fi,而设计要求将 200~2000HZ 的频率变换为 1~5V 的电压,可得到变换式为: V=0.00222f+0.556故应对 F/V 变换的结果进行电位平移。
2.2.3 信号采集处理单元模块设计在此方案采用双单片机,即在数据采集的远端、近端均采用单片机控制,远端完成数据的采集、抽样、平滑、发送;近端完成数据的接收、校验、纠错、处理与显示等。
A/D 转换器是受从单片机的控制的。
2.2.4 通信网络模块设计本系统采用两个单片机来实现系统控制的。
便于改变从单片机的数据采集方式,尽量减小传输线数目。
由于系统采用具有自动控制的单片机,故该系统具有智能话处理能力,可以对不同错误做出处理。
当系统开始运行后,从单片机发出一个选通信号指令选通某路 A/D 转换的指令,并等待接收从单片机返回的信息。
如果主单片机未收到回送的数据或接收到的数据错误,则重发指令。
双单片机之间的通信实际采用 MAX485 构成接口器件,传输速率为 19.2Kbps,在此情况下可以保证两个单片机之间的良好通信。
其电路图如图 2.2.4.1 所示。
2.2.5 数据地址显示电路设计由于题目中要求传送 8 位二进制码,其分辨率达到 1/256 ,显示电压分辨率为5/255=0.0192V,所以电压显示需要 3 位数码管。
显示采用动态扫描的方式,四个七段数码管逐位扫描。
配合通道选择开头,可在 LED 上同时显示一路或多路数据。
数码管分别显示通道地址、电压值。
数码管采用共阴极,由于 AT89C52单片机每个 I/O 的拉电流只有 1—2mA。
所以在位码和段码都加上了同相驱动器。
单片机 XTAL2、XTAL1 接 12MHZ 晶振,提供系统时钟基值。
另 RESET 接复位按键。
3. 系统软件设计系统的软件的设计是采用汇编语言,对单片机进行编程实现各种功能。
程序是在 Windows 2000 环境下采用 WAVE 软件编写的,可以实现对八路数据的采集与处理,并能实现对数据、地址的显示。
主程序主要起到一个导向与决策的功能,决定什么时候采集数据处理数据显示数据。
对于数据的处理的实际功能的实现主要是通过调用具体的子程序。
本系统采用半双工传输,每次需要发送或接收数据时,控制 MAX485 使其成为接收器或发送器。
3.1 主单片机程序主机发送为一字节指令,其高 4 位和低四位均为要采集的通道号,格式为0***0***。
其中***=000~111。
主机发送完成指令后,立即转入接收状态,等待从机回送两字节数据,若在一定时间内未收到数据或收到的两字节数据不一致。
则认为通信有误,转而重发一次指令。
若重发三次均未成功,则点亮线路故障告警灯提醒用户。
3.1.1 主机发送程序流程图如 3.1.1 所示。
3.1.2 主机数据处理子程序图如 3.1.2 所示。
3.1.3 主机显示子程序图如 3.1.3 所示。
3.1.4 主机主程序流程图如 3.1.4 所示。
3.2 从单片机程序为增强数据采集的实时性,从机在为收到指令时,轮流对 8 路模拟信号进行采集变换,并存入相应单元。
从机在接收到主机发送的指令后,回送相应的两字节 8 位 A/D 转换数据。