钛渣冶炼炉新工艺介绍
高钛渣生产工艺资料
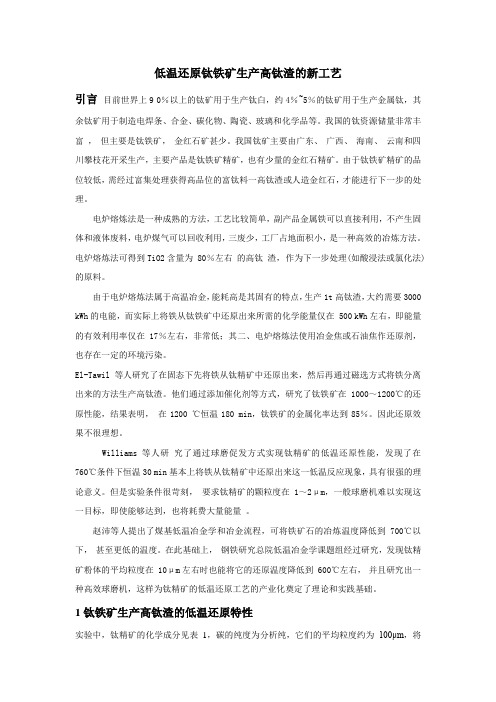
低温还原钛铁矿生产高钛渣的新工艺引言目前世界上9 0%以上的钛矿用于生产钛白,约4%~5%的钛矿用于生产金属钛,其余钛矿用于制造电焊条、合金、碳化物、陶瓷、玻璃和化学品等。
我国的钛资源储量非常丰富,但主要是钛铁矿,金红石矿甚少。
我国钛矿主要由广东、广西、海南、云南和四川攀枝花开采生产,主要产品是钛铁矿精矿,也有少量的金红石精矿。
由于钛铁矿精矿的品位较低,需经过富集处理获得高品位的富钛料一高钛渣或人造金红石,才能进行下一步的处理。
电炉熔炼法是一种成熟的方法,工艺比较简单,副产品金属铁可以直接利用,不产生固体和液体废料,电炉煤气可以回收利用,三废少,工厂占地面积小,是一种高效的冶炼方法。
电炉熔炼法可得到TiO2含量为 80%左右的高钛渣,作为下一步处理(如酸浸法或氯化法) 的原料。
由于电炉熔炼法属于高温冶金,能耗高是其固有的特点,生产1t高钛渣,大约需要3000 kWh的电能,而实际上将铁从钛铁矿中还原出来所需的化学能量仅在 500 kWh左右,即能量的有效利用率仅在17%左右,非常低;其二、电炉熔炼法使用冶金焦或石油焦作还原剂,也存在一定的环境污染。
El-Tawil等人研究了在固态下先将铁从钛精矿中还原出来,然后再通过磁选方式将铁分离出来的方法生产高钛渣。
他们通过添加催化剂等方式,研究了钛铁矿在1000~1200℃的还原性能,结果表明,在1200 ℃恒温180 min,钛铁矿的金属化率达到85%。
因此还原效果不很理想。
Williams等人研究了通过球磨促发方式实现钛精矿的低温还原性能,发现了在760℃条件下恒温30 min基本上将铁从钛精矿中还原出来这一低温反应现象,具有很强的理论意义。
但是实验条件很苛刻,要求钛精矿的颗粒度在1~2μm,一般球磨机难以实现这一目标,即使能够达到,也将耗费大量能量。
赵沛等人提出了煤基低温冶金学和冶金流程,可将铁矿石的冶炼温度降低到700℃以下,甚至更低的温度。
在此基础上,钢铁研究总院低温冶金学课题组经过研究,发现钛精矿粉体的平均粒度在10μm左右时也能将它的还原温度降低到600℃左右,并且研究出一种高效球磨机,这样为钛精矿的低温还原工艺的产业化奠定了理论和实践基础。
钛渣炉在钒钛磁铁矿冶炼新工艺流程中的应用

2 )技术参数 新工艺流程 中单座钛渣炉的技术参数,见表 5 。
表 5 单座钛渣炉的技术参数
参数 名称
炉 型 变压 器容 量/ A MV
2 钛渣炉在常规 冶炼工艺流程 中的功能及参数
在 常规冶炼 工艺流程 中,钛渣炉 内主要发生还 原反
数值
半 封 闭型 1. 25
应,通过控制合 理的生产工艺 制度,将 钛精矿 中铁 的氧 化 物选择性地 还原为金 属铁,而钛 的氧化物被 富集在 炉 渣 中,经 渣铁分离获得 钛渣和少量 的副产品金属铁| 1 ] 。
铁精 矿 5 .5 1 8 0 6 I 2 . 1 5 5
50 .1
48 . 0
3 7 . 6
13 . 5
由于钒钛磁 铁矿为 共生矿 ,在选矿 阶段很难将矿 石 中的钒 、钛 、铁分离,经选矿后,铁精矿 中w T 2 (i ) 0 仍然较 高。目前在传统工艺 中,对于含钛量很高 ( (i2≥4 %) w TO) 5 的矿石 采用钛渣炉冶炼 ,其他铁精 矿都 采用高炉冶 炼钒 钛磁铁矿的技术,常规工艺流程见 图 1 。
钒 钛 磁铁 矿
磨 矿 、 选 矿
2 )技术参数 该厂使用 的单座钛渣炉的技术参数,见 表 3 。
表 3 单座钛渣炉的技术参数
参 数名 称
炉 型
弃尾矿场H 尾矿l 钛 ̄ (( O) 4% I l wT 5 ) i ≥ I铁精矿
垡塞 卜—— ——一 厂 丽
弃 I I 渣场
LI W e Y OU ing m i N i, X a —
(. ’nEetc u ae ntue o L d 1 Xia lc i F r c stt C . t. ’n 7 0 6 ,C ia r n I i ,Xia 10 1 hn ;
钛渣的冶炼原理
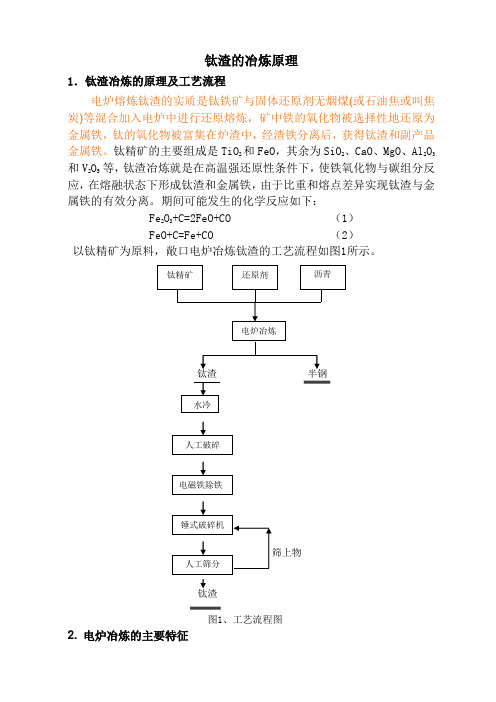
钛渣的冶炼原理1.钛渣冶炼的原理及工艺流程电炉熔炼钛渣的实质是钛铁矿与固体还原剂无烟煤(或石油焦或叫焦炭)等混合加入电炉中进行还原熔炼,矿中铁的氧化物被选择性地还原为金属铁,钛的氧化物被富集在炉渣中,经渣铁分离后,获得钛渣和副产品金属铁。
钛精矿的主要组成是TiO2和FeO,其余为SiO2、CaO、MgO、Al2O3和V2O5 等,钛渣冶炼就是在高温强还原性条件下,使铁氧化物与碳组分反应,在熔融状态下形成钛渣和金属铁,由于比重和熔点差异实现钛渣与金属铁的有效分离。
期间可能发生的化学反应如下:Fe2O3+C=2FeO+CO (1)FeO+C=Fe+CO (2)以钛精矿为原料,敞口电炉冶炼钛渣的工艺流程如图1所示。
钛渣图1、工艺流程图2. 电炉冶炼的主要特征钛渣是一种高熔点的炉渣,钛渣熔体具有强的腐蚀性、高导电性和其粘度在接近熔点温度时而剧增的特性,而且这些性能在熔炼过程中随其组成的变化而发生剧烈的变化。
2.1钛渣的高电导率和熔炼钛渣的开弧熔炼特征2.1.1钛渣的高电导率钛铁矿在熔化状态具有较大的电导率,在1500℃时为2.0~2.5ks/m,在1800℃为5.5~6.0ks/m,随着还原熔炼钛铁矿过程的进行,熔体组成发生变化,FeO含量减少,而TiO2和低价钛氧化物的含量增加,因此其电导率迅速上升,如加拿大索雷尔钛渣在1750℃电导率为15~20ks/m,而一般的炉渣在1750℃电导率为100s/m,可见钛渣的电导率比普通冶金炉渣的电导率高数十倍甚至几百倍,比普通离子型电解质(如Nacl液体在900℃时的电导率约为400s/m)的电导率都高很多,且温度变化对钛渣电导率影响不大,这些都说明钛渣具有电子型导电体的特征。
2.1.2熔炼钛渣电炉的开弧熔炼特征钛渣的高电导率决定了熔炼钛渣电炉的开弧熔炼特征,即熔炼钛渣的热量来源主要依靠电极末端至熔池表面间的电弧热,这就是所谓的“开弧冶炼”,而在高电阻炉渣的情况下,电极埋入炉渣,熔炼过程的热量来源主要是渣阻热,即所谓的“埋弧熔炼”。
钛渣的冶炼原理

钛渣的冶炼原理1.钛渣冶炼的原理及工艺流程电炉熔炼钛渣的实质是钛铁矿与固体还原剂无烟煤(或石油焦或叫焦炭)等混合加入电炉中进行还原熔炼,矿中铁的氧化物被选择性地还原为金属铁,钛的氧化物被富集在炉渣中,经渣铁分离后,获得钛渣和副产品金属铁。
钛精矿的主要组成是TiO2和FeO,其余为SiO2、CaO、MgO、Al2O3和V2O5 等,钛渣冶炼就是在高温强还原性条件下,使铁氧化物与碳组分反应,在熔融状态下形成钛渣和金属铁,由于比重和熔点差异实现钛渣与金属铁的有效分离。
期间可能发生的化学反应如下:Fe2O3+C=2FeO+CO (1)FeO+C=Fe+CO (2)以钛精矿为原料,敞口电炉冶炼钛渣的工艺流程如图1所示。
钛渣图1、工艺流程图2. 电炉冶炼的主要特征钛渣是一种高熔点的炉渣,钛渣熔体具有强的腐蚀性、高导电性和其粘度在接近熔点温度时而剧增的特性,而且这些性能在熔炼过程中随其组成的变化而发生剧烈的变化。
2.1钛渣的高电导率和熔炼钛渣的开弧熔炼特征2.1.1钛渣的高电导率钛铁矿在熔化状态具有较大的电导率,在1500℃时为2.0~2.5ks/m,在1800℃为5.5~6.0ks/m,随着还原熔炼钛铁矿过程的进行,熔体组成发生变化,FeO含量减少,而TiO2和低价钛氧化物的含量增加,因此其电导率迅速上升,如加拿大索雷尔钛渣在1750℃电导率为15~20ks/m,而一般的炉渣在1750℃电导率为100s/m,可见钛渣的电导率比普通冶金炉渣的电导率高数十倍甚至几百倍,比普通离子型电解质(如Nacl液体在900℃时的电导率约为400s/m)的电导率都高很多,且温度变化对钛渣电导率影响不大,这些都说明钛渣具有电子型导电体的特征。
2.1.2熔炼钛渣电炉的开弧熔炼特征钛渣的高电导率决定了熔炼钛渣电炉的开弧熔炼特征,即熔炼钛渣的热量来源主要依靠电极末端至熔池表面间的电弧热,这就是所谓的“开弧冶炼”,而在高电阻炉渣的情况下,电极埋入炉渣,熔炼过程的热量来源主要是渣阻热,即所谓的“埋弧熔炼”。
钛渣冶炼炉新工艺介绍

关于钛渣冶炼炉的新工艺介绍目前,发达国家中的钛渣炉,容量都比较大,多采用全封闭,湿法除尘和回收煤气,并向干法除尘转变。
这些大型电炉采用计算机进行控制,从原料准备到产品出炉全过程自动化,生产效率高,产品质量稳定,环保设施完善,有利于资源的综合利用,也是中国钛渣生产发展的方向。
国内某企业从南非引进的3万kVA全密闭直流高钛渣炉,已经将高钛渣的吨产电耗从国内普遍的3500kwh/t~4500 kwh/t降至2600kwh/t~ 2800kwh/t,大大降低了生产成本(注:由于该企业对引进技术吸收消化严重不足,加之过份神秘化的保密隔绝,导致试生产周期特长,生产时断时续。
不久前,此高钛渣炉炉底熔穿目前正停产维修。
该企业的负责人在接待国家工信部考察人员时介绍说:技术指标是非常先进的,政治上丰收,经济效益趋于零)。
国内钛渣冶炼通常采用三相交流敞口电炉或半密闭电炉,一次性加料生产工艺,污染严重、热辐射高、操作环境恶劣。
炉膛热量直接从炉口或烟道散出,电炉热损失大,容易造成除尘器布袋的烧蚀。
三相交流电炉的三根电极之间的电流为平面流动形式,由于炉料的导电性,而不能选用较高的二次电压,否则会出现电极不能深插,炉底温度低的现象,使得SiC沉积造成炉底上涨。
交流电炉炉膛的深、径比小,每次排渣或出铁水后,炉内温度下降快,当下一炉的生料加入后,需要焙烧一段时间以提高炉温,增大了耗电量。
综合上述几个原因,使得国内钛渣、工业硅、铁合金及电石等冶炼成本居高不下,市场竞争力低。
目前世界上最为先进的冶炼方法,是密闭直流电炉空心电极连续加料冶炼方式。
密闭直流电炉空心电极粉料连续入炉冶炼工艺具有如下优点:⑴炉膛密闭,无外部空气进入,烟气量小,除尘设备负担小。
⑵密闭电炉无外部空气进入,冶炼操作在密闭的高还原性气氛下进行,降低了电极的高温氧化和还原剂的氧化烧损。
可以节省电极消耗达50%以上。
⑶富含一氧化碳的高温烟气,显热直接用来干燥矿粉,降低矿粉中的水分,充分利用烟气的热量,比半密闭/敞口炉的潮矿入炉减少了电能消耗。
钛的冶炼技术

钛在地壳中的含量十分丰富,按丰度值算占第九位。
解放前,我国的钛锆铪冶炼工业是空白,虽然资源丰富,但未得到利用。
解放后,开始建立我国的钛锆铪冶炼和加工工业,适应了我国尖端技术和相关工业部门对这些金属和化合物的需要。
现在,我国的钛锆铪工业都在积极发展中。
化学性质钛位于元素周期表中第四周期第IV副族,原子序数为22。
钛的化学性质相当活泼,可与很多元素反应或形成固溶体。
主要物理性质,熔点;钛的熔点为1660℃。
沸点钛的沸点为3302℃。
超导性,耐蚀性:不锈钢;机械性质纯钛的机械强度比铁大一倍,比铝大5倍。
钛具有可塑性,钛合金在航天航空工业上的应用,钛具有质轻、强度高,耐热、耐低温性能。
钛合金在化工、冶金上的应用:钛的耐蚀性能好,日常生活领域,钛和钛合金具有质轻、强度高、耐腐蚀并兼有外观漂亮等综合性能。
人造关节,假肢。
超导材料,钛镍合金具有形状记忆功能,在镍含量x Ni为49.5%~51.5%的组成范围内,x Ni每变化0.01,相变温度约变化10℃。
钛镍合金还具有超弹性,它的耐磨性能也很优异。
钛铁合金具有储氢功能,FeTi合金的吸放氢气可在接近常温﹑常压条件下进行,而且,储氢容量也很大。
钛铌合金具有超导性,钾和镁。
钛属于典型的亲岩石元素,存在于所有的岩浆岩中。
钛的分布极广,遍布于岩石、砂土、粘土、海水、动植物,甚至存在于月球和陨石中。
钛的化学活性很强,所以自然界中没有钛的单质存在,总是和氧结合在一起。
在矿物中,钛以氧化物(金红石)形式和钛酸盐形式存在,钛还经常与铁共生(钛铁矿)。
金红石是一种黄色至红棕色的矿物,其主要成分是TiO2,还含有一定量的铁、铌和钽。
铁是由于它与钛铁矿共生的结果。
由于Ti4+与Ni+、Ta5+ 离子的相似性,铌和钽常伴生在钛矿石中。
93%~98%,钛铁矿理论分子式为FeTiO3,其中TiO2理论含量为52.63%。
但钛铁矿的实际组成是与其成矿原因和经历的自然条件有关。
可以把自然界的钛铁矿看成是FeO-TiO2和其他杂质氧化物组成的固溶体。
钛渣冶炼电炉炉体制作、安装工艺
钛渣冶炼电炉炉体制作、安装工艺摘要:电炉炉体为电炉的电热反应场所,其内部可存储一定容量的铁水和渣液,是整个电炉系统的核心设备和基础。
电炉炉壳由锅炉钢板焊接而成,分为上、中、下3层。
炉壳的中、下层各瓣之间通过膨胀补偿连接板(缓冲板)连接在一起,用以补偿炉衬的热膨胀。
关键词:加工工艺,整体组装,应力消除一.概述:钛渣冶炼电炉炉体要求与炉底板、悬臂梁、炉盖之间绝缘,绝缘值>5 KΩ;电炉炉体在冶炼过程中会因为炉底板不平及垂直中心偏差过大产生飘移现象,严重影响设备的正常运行。
故要求电炉砼基础平台水平差≤5㎜,电炉底板水平差≤10㎜;电炉冶炼采用多点布料、极心圆可调工艺;并具有配料、加料的自动操作,电极升降、压放、炉压自动控制,实时监控配料、加料、电炉冶炼、冷却系统、液压系统的主要工艺参数等自控功能,故对电炉炉体设备制作、安装质量提出了很高的要求。
二、电炉炉体制作工艺:①、样板制作炉壳卡样板(检查用样板),采用δ=2mm冷轧钢板制作,采用内圆卡样板,卡样板外弧R为每带炉壳检查处设计尺寸(因炉壳制作加工过程中考虑了焊接收缩因素,其R 值应与计算值相一致,检查位置一般为离炉壳上下口50mm处),卡样板弧长不得小于2m,偏差不大于1mm。
根据数控切割机要求,可先利用CAD 软件画出炉壳下料及开孔切割轮廓线,并按数控切割机的操作要求进行图形转换。
在进行炉壳切割时,要求预留出下料切割余量及焊接收缩余量,以保证炉壳切割后和焊接收缩完尺寸能满足设计要求。
②、下料前的计算按图纸设计尺寸进行,其中环缝每带考虑焊接收缩余量2mm;每块炉皮竖缝考虑焊接收缩余量4mm,每带环缝(6块)共考虑焊接收缩余量24mm,重新计算每块炉皮实际下料尺寸。
③、炉壳下料在计算机上进行绘图,通过专用程序(FastCAM软件),将图形转化为数控切割机所能识别的图形。
按计算尺寸在钢板上作好炉壳展开图形,然后严格校对上下弦长、弧长、弧弦距、对角线、炉壳立缝边长等是否与设计尺寸符合,所有尺寸偏差要求不大于±1 ㎜;炉壳表面应作出标记或十字中心线,在拆开的接头处或上下圈之间,应用油漆作出明显的对位标志。
空心电极密闭直流高钛渣炉简介
密闭直流电炉空心电极连续加料高钛渣生产工艺一、概述高钛渣(High Titania Slag)是经过物理生产过程而形成的钛矿富集物俗称,通过电炉加热熔化钛矿,使钛矿中二氧化钛和铁熔化分离,从而得到二氧化钛高含量的富集物。
高钛渣既不是废渣,也不是副产物,而是生产四氯化钛、钛白粉和海绵钛产品的优质原料。
二、应用领域1. TiO2含量大于90%的高钛渣可以作为氯化法钛白的生产原料。
2. TiO2含量小于90%的高钛渣是硫酸法钛白生产的优质原料。
三、国内高钛渣技术发展概况我国钛资源比较丰富,除少量钛铁砂矿外,主要以钛铁岩矿为主,国内钛铁岩矿的缺点是品位低,杂质含量高,不能直接满足氯化法钛白对原料的要求,仅适宜作硫酸法钛白的原料。
由于硫酸法钛白生产过程中产生大量难以治理、污染环境的“三废”,近年来全球硫酸法钛白产能急剧萎缩。
随着我国氯化法钛白以及海锦钛工业的快速发展,对高品位富钛料的需求日益增加。
因此,寻求经济合理的钛原料处理方法,将我国丰富的钛铁矿资源加工成富钛料是我国钛白和钛材产业发展的当务之急。
国内钛渣生产自50年代起,至今已有半个世纪,原主要生产厂家是遵义钛厂、阜新冶炼厂,厦门冶炼厂以及宣化冶炼厂等。
近年来云南武定、禄丰、富民、楚雄以及攀枝花地区陆续建设了许多中小钛渣冶炼厂,其中多数钛渣厂的电炉由铁合金炉和电石炉改建而成。
我国钛渣整体生产技术落后,冶炼设备的特点是小型炉子多,大型炉子少,没有特大型炉子。
炉型以敞口式电弧炉为主,渣和铁从同一出口排出,生铁不经处理即出售。
原料选用钛精矿直接入炉冶炼,人工捣炉,间断加料,间断出炉,煤气点火排空。
变压器功率介于400~7000kV A之间。
国内钛渣冶炼工艺水平决定了钛渣生产规模小、效率低、能耗高、环境差、冶炼操作不稳定。
目前国内大多数钛渣生产厂采用的是敞口电炉一次加料冶炼工艺。
这种冶炼工艺存在着炉况不稳、翻渣结壳、经常塌料、电流波动大、劳动条件差、粉尘飞扬、物料损失严重、收率低等缺点,与国外钛渣生产工艺相比,无论在规模、产量、质量方面都有很大差距。
预处理——电炉联合冶炼高钛渣新工艺
预处理——电炉联合冶炼高钛渣新工艺王祥丁;郑汝宁;王青【摘要】文章在总结分析现有富钛料生产技术的基础上,提出一种利用改造回转窑预还原钛精矿的新工艺.此工艺既可以直接生产钛含量低的钛铁产品,也可以联合电炉生产高钛渣,从而改善电炉炉况,并以较低的改造成本提升高钛渣产能.【期刊名称】《有色金属设计》【年(卷),期】2018(045)002【总页数】4页(P82-85)【关键词】钛精矿;高钛渣;预还原;电炉;回转窑【作者】王祥丁;郑汝宁;王青【作者单位】昆明有色冶金设计研究院股份公司,云南昆明650051;昆明有色冶金设计研究院股份公司,云南昆明650051;昆明有色冶金设计研究院股份公司,云南昆明650051【正文语种】中文【中图分类】TD8530 引言钛金属因其具有的一系列优异特性而被用于众多领域,人们将其称为“21世纪金属”。
我国的钛资源居世界首位,国内外已发现钛资源总储量近20亿t,我国约占48 %[1]。
全国有20个省市自治区有钛矿,其中98.9 %是钛铁矿。
富钛料一般指TiO2含量不小于85 %的电炉冶炼钛渣或人造金红石,而且富钛料也是氯化法生产高档金红石型钛白粉和海绵钛的重要原料。
生产富钛料常用的方法是盐酸浸出法、硫酸浸出法、还原锈蚀法、电炉熔炼法等,鉴于我国钛矿资源的实际情况,电炉熔炼钛渣在我国生产的富钛料中占重要地位[2]。
结合近几年电炉熔炼钛渣生产中出现的原料适应性弱、产品品质波动大等问题,文章提出一种预还原-电炉联合冶炼高钛渣新工艺。
1 现有富钛料生产工艺特点生产富钛料常用的方法是盐酸浸出法、硫酸浸出法、还原锈蚀法、电炉熔炼法等[9]。
结合目前均有工业生产实践,以上方法各有优缺点,存在可提升改进空间。
1.1 盐酸浸出法生产特点[2,6]盐酸浸出法的工艺多种多样,既有稀盐酸的美国BCA 法,又有浓盐酸的华昌法,稀酸浸出法又分为常压浸出法和高压浸出法。
尽管方法多种多样,但其基本原理是相同的。
钛渣电炉布料及精准加料工艺的探讨
钛渣电炉布料及精准加料工艺的探讨发布时间:2022-02-25T10:23:33.508Z 来源:《中国科技信息》2021年11月中32期作者:杨斌[导读] 由于钛渣冶炼电炉的布料方式具有多样性,因此,选择一种合理的方式对电炉生产极为重要。
钛渣电炉炉料主要通过炉顶料仓和料管输送到炉膛内,采用多点布料、连续加料、连续冶炼的方式相比批量加料、间断冶炼的布料方式优点较多。
新疆湘和新材料科技有限公司杨斌新疆哈密摘要:由于钛渣冶炼电炉的布料方式具有多样性,因此,选择一种合理的方式对电炉生产极为重要。
钛渣电炉炉料主要通过炉顶料仓和料管输送到炉膛内,采用多点布料、连续加料、连续冶炼的方式相比批量加料、间断冶炼的布料方式优点较多。
关键字:多点布料;连续加料;连续冶炼1 前言钛具有密度小、耐腐蚀、耐高温等优异性能,是重要的轻型耐腐蚀结构、功能和生物工程材料,是一种仅次于铁、铝正在崛起的“第三金属”,被广泛应用于航空、航天、化工、石油、冶金和日常生活器具等工业生产中,它被誉为现代金属。
生产钛的原料主要为天然金红石、人造金红石和富钛料,而随着天然金红石资源的不断减少,其价格也不断增加,富钛料成为制作钛材的优质原料,价格低且产量大。
目前国内钛渣生产已经有50多年的历史,但至今任然采用半密闭电炉、批量加料、间歇式操作,在冶炼过程中,经常发生塌料现象,产生大的泡沫渣,导致炉况不稳定,电流波动较大,操作难度较高。
不仅对操作人员和设备存在较大的安全隐患,而且不能实现连续生产连续冶炼,导致电炉生产率和变压器效率较低,电能消耗大,生产成本大大增加。
因此,选择一种合理的加料方式对电炉生产极为重要。
2、电炉冶炼法生产钛渣的现状及存在问题2.1钛渣冶炼原理电炉熔炼钛铁矿生产钛渣,是使用还原剂将钛铁矿中铁的氧化物选择性的还原成金属铁,从而预先富集钛的火法冶金过程。
其主要工艺过程是使用无烟煤、石油焦或兰炭作为还原剂,与钛精矿配料后加入到钛渣电炉内,在1600~1800℃的高温条件下进行熔炼,根据生铁与钛渣比重和磁性的不同,把钛氧化物和铁分离,从而得到TiO2品位为74%-95%的钛渣。
- 1、下载文档前请自行甄别文档内容的完整性,平台不提供额外的编辑、内容补充、找答案等附加服务。
- 2、"仅部分预览"的文档,不可在线预览部分如存在完整性等问题,可反馈申请退款(可完整预览的文档不适用该条件!)。
- 3、如文档侵犯您的权益,请联系客服反馈,我们会尽快为您处理(人工客服工作时间:9:00-18:30)。
钛渣冶炼炉新工艺介绍关于钛渣冶炼炉的新工艺介绍前言本方案瞄准国际先进技术,借鉴国内引进的成败实例,结合我团队自主研发并已成熟应用的成果而制定。
本方案所采用的各种“非常规”措施,最终将体现为:1.节能,比常规交流电炉耗电低25%~35%,真正实现低成本运行;2.生产环境优良,低噪音、全密闭,突显“人性化”,尾气排放可满足新国标;由于工艺上的改革,使除尘器过滤面积、烟管面积、风机及功率,与传统工艺的除尘器相比,≦1/8,并且通过新工艺,使被过滤的烟气温度有效、可靠地控制在200℃以下,促使滤袋寿命成倍地延长。
3.生产过程简化,实行计算机控制,在原编制上可大幅削减冶炼工人;4.电炉设计上,倾向于多功能——满足冶炼多种产品(随意可调的宽幅电压);5.产品生产的质量特别稳定、易控。
6.电炉本体故障率特低,平时只需巡视和加注润滑等基本保养。
本方案其它特点:1.独创的底电极结构,从根本上杜绝了铜质针刺因高温频繁烧蚀的断电事故,彻底保障了导电可靠性。
2.电炉功率因数高(只考虑动力补偿);同时,在电气设计上已消除了谐波危害。
3.采用可控硅整流方式,能很方便地化解凝炉(非正常停电)、因SiC沉积造成的炉底上涨现象。
4.原料连续入炉、大容量电炉可实现产品连续出炉。
5.利用电炉产生的高温烟气烘干原料及煤气回收发电技术。
烟气进入原料干燥装置降温后,再进除尘器除尘,由煤气风机送至煤气发电车间,全程安全可控。
根据国家对铁合金、电石等冶炼行业的准入限制,为适应国家可能出台的新政策,综合考虑钛渣炉性价比,建议钛渣炉的单台容量≧2万kVA。
工信部规定,容量在6300KVA以下的交流矿热炉逐步淘汰,新上的交流矿热炉容量必须≥25000KVA,直流炉容量≥12500KVA。
内蒙、贵州及四川攀枝花等地已经在落实。
一台2万KVA空心电极直流密闭炉,可年产主产品钛渣67000吨左右,副产品半钢5000吨左右。
与传统冶炼方式相比,生产一吨主产品可节省电能1200~1800度。
建造一台生产钛渣的2万KVA空心电极直流密闭炉,约需人民币6000~7000万元。
投产后1~2年即可收回投资。
直流密闭炉节能效果显著,为国内首创。
建设单位可以向国家工信部申报节能减排项目,寻求国家奖励或资助。
贵州兴义某企业计划新建4台30000万KVA半密闭直流铁合金炉,已获得当地政府3亿元的贴息贷款扶植。
内蒙古卓资县一铁合金企业新建一台16500KVA全密闭直流铁合金炉,已获得当地政府4百万元资助,正在向工信部申请立项。
目前,发达国家中的钛渣炉,容量都比较大,多采用全封闭,湿法除尘和回收煤气,并向干法除尘转变。
这些大型电炉采用计算机进行控制,从原料准备到产品出炉全过程自动化,生产效率高,产品质量稳定,环保设施完善,有利于资源的综合利用,也是中国钛渣生产发展的方向。
国内某企业从南非引进的3万kVA全密闭直流高钛渣炉,已经将高钛渣的吨产电耗从国内普遍的3500kwh/t~4500 kwh/t降至2600kwh/t~ 2800kwh/t,大大降低了生产成本(注:由于该企业对引进技术吸收消化严重不足,加之过份神秘化的保密隔绝,导致试生产周期特长,生产时断时续。
不久前,此高钛渣炉炉底熔穿目前正停产维修。
该企业的负责人在接待国家工信部考察人员时介绍说:技术指标是非常先进的,政治上丰收,经济效益趋于零)。
国内钛渣冶炼通常采用三相交流敞口电炉或半密闭电炉,一次性加料生产工艺,污染严重、热辐射高、操作环境恶劣。
炉膛热量直接从炉口或烟道散出,电炉热损失大,容易造成除尘器布袋的烧蚀。
三相交流电炉的三根电极之间的电流为平面流动形式,由于炉料的导电性,而不能选用较高的二次电压,否则会出现电极不能深插,炉底温度低的现象,使得SiC沉积造成炉底上涨。
交流电炉炉膛的深、径比小,每次排渣或出铁水后,炉内温度下降快,当下一炉的生料加入后,需要焙烧一段时间以提高炉温,增大了耗电量。
综合上述几个原因,使得国内钛渣、工业硅、铁合金及电石等冶炼成本居高不下,市场竞争力低。
目前世界上最为先进的冶炼方法,是密闭直流电炉空心电极连续加料冶炼方式。
密闭直流电炉空心电极粉料连续入炉冶炼工艺具有如下优点:⑴炉膛密闭,无外部空气进入,烟气量小,除尘设备负担小。
⑵密闭电炉无外部空气进入,冶炼操作在密闭的高还原性气氛下进行,降低了电极的高温氧化和还原剂的氧化烧损。
可以节省电极消耗达50%以上。
⑶富含一氧化碳的高温烟气,显热直接用来干燥矿粉,降低矿粉中的水分,充分利用烟气的热量,比半密闭/敞口炉的潮矿入炉减少了电能消耗。
降温除尘后的一氧化碳气体可以用来驱动燃气发电机发电,能源得到综合利用。
⑷粉料连续入炉,原料和还原剂均为粉末,物料反应的表面积增大。
物料直接进入熔池,在液态下进行还原反应,还原反应充分、速度快——“瞬间还原”。
⑸粉料连续入炉,省去繁重的捣炉作业,减轻了劳动强度,改善了工作环境。
⑹直流电炉炉膛的深/径比大于交流电炉的深/径比,即相同容量直流电炉的炉膛比交流电炉深,直径比交流电炉小,热量集中,热损失小。
⑺直流电炉炉膛深/径比大,炉膛表面积小,比交流电炉节省炉衬材料。
⑻直流电炉炉底作为导电电极,使电弧引向炉底,直流电流对熔池具有上下运动的电磁搅拌作用,使熔池上下层温度均匀,大大改善金属氧化物高温还原反应的热力学和动力学条件,消除了炉底上涨的可能。
⑼直流电炉的顶电极位于炉膛中心,产生的电弧对炉衬的高温辐射烧损小,故炉衬材料的消耗降低,使用寿命延长。
⑽直流电炉二次侧短网和熔池内无感抗影响,且无电流集肤效应和邻近效应,电网供给的交流电通过24脉整流,电压脉动系数减少,产生的高次谐波极弱,对电网干扰小,功率因数高。
⑾直流电炉,炉盖只有一个电极孔,易于密封和除尘。
⑿直流电弧无电流过零息弧,噪音小,电弧稳定。
⒀直流电炉在炉膛内为垂直导电方式,不受炉料电阻率的影响,易于实现高电压长弧冶炼操作,提高冶炼速度。
仅直流供电一项即可比交流电炉节电10%以上。
⒁停炉、修炉后起弧方便,易于操作。
密闭直流电炉与半密闭交流电炉性能对比见表1。
高钛渣冶炼过程中烟气带走的热量(包括可燃性气体的化学能)几乎相当于输入炉内的电能转化的热量。
因此,充分利用此能源是钛渣生产降耗的出路之一。
利用密闭电炉的高浓度CO气体进行发电,同时,适当增加投资,亦可回收利用液态铁水的显热等,都是二次能源利用。
密闭直流电炉空心电极粉料连续入炉生产工艺能够利用密闭炉气的显热来干燥炉料,降温、除尘、净化后的炉气,用来驱动燃气发电机产生电力,反馈为电炉电能的补充,使得电能的消耗大大降低。
仅此一项即可节能15%~20%。
综合起来,密闭直流电炉空心电极粉料连续入炉生产工艺综合节电效果可以达到25 %~35%。
表1直流密闭空心电极电炉与交流半密闭/敞口电炉性能对比序号项目交流敞口/半密闭电炉直流密闭空心电极电炉1 电耗% 100 ~703 电极消耗% 100 ~554 还原剂消耗% 100 ~805 功率因数(未补偿)0.55~0.85 ﹥0.96 产能% 100 105~1287 炉料形状球团、块料粉末8 加料形式间断连续9 物料还原反应状态固相液相10 炉膛空间气氛空气、二氧化碳一氧化碳(80%)11 噪音大微12 车间粉尘多很少13 炉况不稳定,需要捣炉稳定,不需要捣炉14 电炉煤气无法回收利用回收利用15 环保除尘运行费用% 100 40~50高钛渣冶炼工艺流程以钛精矿为主要原料、炭为还原剂,密闭直流电炉空心电极粉料连续入炉,生产工艺流程图如图一所示。
经粉碎后符合粒度要求的粉状原料经装载机分别倒运装入配料站的各储料仓。
根据冶炼制度确定炉料的组成及其配比。
各种符合粒度要求的粉状原料经电子秤精确称量混合后经矿粉预热干燥机送至炉顶料仓,再由气力给料机通过空心电极直接将混合后的粉料加入电炉,被输入到炉内的电能冶炼,连续发生一系列物化反应后生成液态的钛渣和半钢,积于炉底并利用其密度差异自动分离,俗称“熔分”。
每隔约4~6小时,打开一次出渣口和出铁口,将渣和铁分别放出,熔状钛渣经水喷射后成为水淬渣(便于破碎时的渣铁分离,提高产品质量),在鳞板输送机上利用自身余热干燥,再破碎、除铁、筛分、均化、钛渣产品包装;铁水包运到浇铸间浇入锭模内,或由出铁咀直接流入铸铁机,凝固后脱模,经过精整运入成品库。
炉中产生的高温炉气,温度在1000℃以上,CO含量高达80%。
高温炉气经隔热烟道送至余热锅炉第一次降温。
余热锅炉产生的蒸汽动力,驱动汽轮发电机发电。
经余热锅炉降温后炉气,送至矿粉预热干燥机第二次降温、计算机控喷雾(确保收尘布袋不结露)炉气温度可降至200℃以下。
最后经过脱硫除尘,富含CO的低温洁净炉气送至燃气发电机发电。
直流电炉车间主要设备特点直流电炉车间的电炉采用空心单电极密闭式炉型。
可把生产中产生的废气(主要成分是一氧化碳)回收利用。
冶炼过程全封闭微正压操作,煤气发生过程连续稳定,煤气体积只有敞口电炉烟气体积的10~20%。
因此煤气净化设备小,组合简单,净化操作便利。
密闭炉的炉盖为混合式结构,采用水冷骨架,其间打结耐火混凝土或铺以水冷盖板,在水冷盖板内侧打结耐火混凝土。
骨架使用钢管制作以减少焊缝,靠近电极处采用防磁材料制作,以减少涡流和磁滞损失。
炉盖呈锥台形,中部的水平面装有电极密封孔和料管密封孔,侧壁装有带防爆盖的密封炉门,用以取出折断的电极头和进行炉内检修,还装设1~2个烟囱以引导炉气排入除尘系统或大气中。
为便于操作检修,并保证安全运行,封闭电炉炉盖上设置若干个带盖的窥视、检修和防爆孔。
炉内底部炉衬设置安装数只热电偶,信号进入计算机,实时监控、报警,确保生产安全。
电炉结构形式直流电炉为全封闭矿热炉的结构形式为:全封闭、空心单电极、固定式圆形炉体。
电炉装备除烟罩使用全封闭式和气封系统使用氮气外均与交流炉类似。
2万KVA (单台)钛渣炉主要技术经济指标 编制:沈阳东大科技有限责任公司 佟玉鹏 戴小平江苏百斯特热能工程有限公司 单总工程师(重庆分公司经理) 2015-03-20附: 沈阳东大科技、直流炉优势、百斯特能源回收简 介沈阳东大科技有限责任公司成立于2000年,依托东北大学在冶金领域雄厚的科研、实验背景,成果突出。
一. 沈阳东大科技有限责任公司名 称 单位 数量 备 注1 钛精矿(原料) 2.2t/(t 高钛渣)按46%品位计2 碳粉 (原料) 0.26 t/(t 高钛渣) 兰碳(脱硫)3 氮气 (原料)3000m 3/天 纯度:≧99.5% 4氧气1m 3/t 高钛渣 5 1/2吋焊管(吹氧管) 2kg/t 高钛渣6生产用水 ≦150m 3/天 仅考虑补充蒸发量7生产用电(以高钛渣产品计,综合电耗) ≦2800kwh/吨高钛渣未计生活、办公、照明、机修,未计回收发电≦2300kwh/吨高钛渣未计生活、办公、照明、机修,已计回收发电 8 高钛渣 (主产品) 64000~69000t/年 Ti O 2品位:≧90% 9 半钢(副产品 王八铁) 48000~52000t/天10全年生产时间330天 11 电炉设备连续使用率 ≧95%12 设备建造安装费用6000~7000万元不含土建、厂房13投资回收期约1年总经理:佟玉鹏教授(2013年6月退休于东北大学)。