钛渣的冶炼原理
高钛渣生产工艺资料
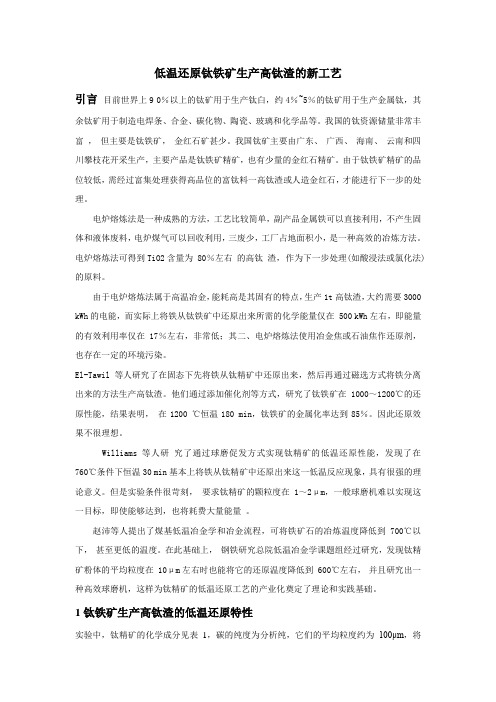
低温还原钛铁矿生产高钛渣的新工艺引言目前世界上9 0%以上的钛矿用于生产钛白,约4%~5%的钛矿用于生产金属钛,其余钛矿用于制造电焊条、合金、碳化物、陶瓷、玻璃和化学品等。
我国的钛资源储量非常丰富,但主要是钛铁矿,金红石矿甚少。
我国钛矿主要由广东、广西、海南、云南和四川攀枝花开采生产,主要产品是钛铁矿精矿,也有少量的金红石精矿。
由于钛铁矿精矿的品位较低,需经过富集处理获得高品位的富钛料一高钛渣或人造金红石,才能进行下一步的处理。
电炉熔炼法是一种成熟的方法,工艺比较简单,副产品金属铁可以直接利用,不产生固体和液体废料,电炉煤气可以回收利用,三废少,工厂占地面积小,是一种高效的冶炼方法。
电炉熔炼法可得到TiO2含量为 80%左右的高钛渣,作为下一步处理(如酸浸法或氯化法) 的原料。
由于电炉熔炼法属于高温冶金,能耗高是其固有的特点,生产1t高钛渣,大约需要3000 kWh的电能,而实际上将铁从钛铁矿中还原出来所需的化学能量仅在 500 kWh左右,即能量的有效利用率仅在17%左右,非常低;其二、电炉熔炼法使用冶金焦或石油焦作还原剂,也存在一定的环境污染。
El-Tawil等人研究了在固态下先将铁从钛精矿中还原出来,然后再通过磁选方式将铁分离出来的方法生产高钛渣。
他们通过添加催化剂等方式,研究了钛铁矿在1000~1200℃的还原性能,结果表明,在1200 ℃恒温180 min,钛铁矿的金属化率达到85%。
因此还原效果不很理想。
Williams等人研究了通过球磨促发方式实现钛精矿的低温还原性能,发现了在760℃条件下恒温30 min基本上将铁从钛精矿中还原出来这一低温反应现象,具有很强的理论意义。
但是实验条件很苛刻,要求钛精矿的颗粒度在1~2μm,一般球磨机难以实现这一目标,即使能够达到,也将耗费大量能量。
赵沛等人提出了煤基低温冶金学和冶金流程,可将铁矿石的冶炼温度降低到700℃以下,甚至更低的温度。
在此基础上,钢铁研究总院低温冶金学课题组经过研究,发现钛精矿粉体的平均粒度在10μm左右时也能将它的还原温度降低到600℃左右,并且研究出一种高效球磨机,这样为钛精矿的低温还原工艺的产业化奠定了理论和实践基础。
钛的冶炼
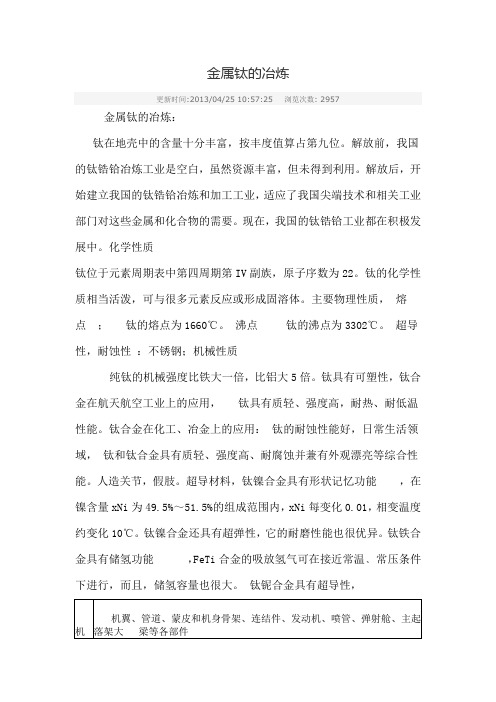
金属钛的冶炼更新时间:2013/04/25 10:57:25 浏览次数: 2957金属钛的冶炼:钛在地壳中的含量十分丰富,按丰度值算占第九位。
解放前,我国的钛锆铪冶炼工业是空白,虽然资源丰富,但未得到利用。
解放后,开始建立我国的钛锆铪冶炼和加工工业,适应了我国尖端技术和相关工业部门对这些金属和化合物的需要。
现在,我国的钛锆铪工业都在积极发展中。
化学性质钛位于元素周期表中第四周期第IV副族,原子序数为22。
钛的化学性质相当活泼,可与很多元素反应或形成固溶体。
主要物理性质,熔点;钛的熔点为1660℃。
沸点钛的沸点为3302℃。
超导性,耐蚀性:不锈钢;机械性质纯钛的机械强度比铁大一倍,比铝大5倍。
钛具有可塑性,钛合金在航天航空工业上的应用,钛具有质轻、强度高,耐热、耐低温性能。
钛合金在化工、冶金上的应用:钛的耐蚀性能好,日常生活领域,钛和钛合金具有质轻、强度高、耐腐蚀并兼有外观漂亮等综合性能。
人造关节,假肢。
超导材料,钛镍合金具有形状记忆功能,在镍含量xNi为49.5%~51.5%的组成范围内,xNi每变化0.01,相变温度约变化10℃。
钛镍合金还具有超弹性,它的耐磨性能也很优异。
钛铁合金具有储氢功能,FeTi合金的吸放氢气可在接近常温﹑常压条件下进行,而且,储氢容量也很大。
钛铌合金具有超导性,钛在地壳中的丰度为0.56%,按元素丰度排列居第九位,仅次于氧、硅、铝、铁、钙、钠、钾和镁。
钛属于典型的亲岩石元素,存在于所有的岩浆岩中。
钛的分布极广,遍布于岩石、砂土、粘土、海水、动植物,甚至存在于月球和陨石中。
钛的化学活性很强,所以自然界中没有钛的单质存在,总是和氧结合在一起。
在矿物中,钛以氧化物(金红石)形式和钛酸盐形式存在,钛还经常与铁共生(钛铁矿)。
金红石是一种黄色至红棕色的矿物,其主要成分是TiO2,还含有一定量的铁、铌和钽。
铁是由于它与钛铁矿共生的结果。
由于Ti4+与Ni+、Ta5+ 离子的相似性,铌和钽常伴生在钛矿石中。
钛渣的冶炼原理

钛渣的冶炼原理1.钛渣冶炼的原理及工艺流程电炉熔炼钛渣的实质是钛铁矿与固体还原剂无烟煤(或石油焦或叫焦炭)等混合加入电炉中进行还原熔炼,矿中铁的氧化物被选择性地还原为金属铁,钛的氧化物被富集在炉渣中,经渣铁分离后,获得钛渣和副产品金属铁。
钛精矿的主要组成是TiO2和FeO,其余为SiO2、CaO、MgO、Al2O3和V2O5 等,钛渣冶炼就是在高温强还原性条件下,使铁氧化物与碳组分反应,在熔融状态下形成钛渣和金属铁,由于比重和熔点差异实现钛渣与金属铁的有效分离。
期间可能发生的化学反应如下:Fe2O3+C=2FeO+CO (1)FeO+C=Fe+CO (2)以钛精矿为原料,敞口电炉冶炼钛渣的工艺流程如图1所示。
钛渣图1、工艺流程图2. 电炉冶炼的主要特征钛渣是一种高熔点的炉渣,钛渣熔体具有强的腐蚀性、高导电性和其粘度在接近熔点温度时而剧增的特性,而且这些性能在熔炼过程中随其组成的变化而发生剧烈的变化。
2.1钛渣的高电导率和熔炼钛渣的开弧熔炼特征2.1.1钛渣的高电导率钛铁矿在熔化状态具有较大的电导率,在1500℃时为2.0~2.5ks/m,在1800℃为5.5~6.0ks/m,随着还原熔炼钛铁矿过程的进行,熔体组成发生变化,FeO含量减少,而TiO2和低价钛氧化物的含量增加,因此其电导率迅速上升,如加拿大索雷尔钛渣在1750℃电导率为15~20ks/m,而一般的炉渣在1750℃电导率为100s/m,可见钛渣的电导率比普通冶金炉渣的电导率高数十倍甚至几百倍,比普通离子型电解质(如Nacl液体在900℃时的电导率约为400s/m)的电导率都高很多,且温度变化对钛渣电导率影响不大,这些都说明钛渣具有电子型导电体的特征。
2.1.2熔炼钛渣电炉的开弧熔炼特征钛渣的高电导率决定了熔炼钛渣电炉的开弧熔炼特征,即熔炼钛渣的热量来源主要依靠电极末端至熔池表面间的电弧热,这就是所谓的“开弧冶炼”,而在高电阻炉渣的情况下,电极埋入炉渣,熔炼过程的热量来源主要是渣阻热,即所谓的“埋弧熔炼”。
金属钛的制取方法术(三篇)

金属钛的制取方法术钛及其合金具有密度小耐腐蚀、耐高温等优异性能。
世界钛工业正经历着以航空航天为主要市场的单一模式,向冶金、能源、交通、化工、生物医药等民用领域为重点发展的多元模式过渡。
目前世界上能进行钛工业化生产的国家只有美国、日本、俄罗斯、中国等少数国家,钛的世界年总产量仅有几万吨。
但是由于钛的重大战略价值和在国民经济中的地位,钛将成为继铁、铝之后崛起的“第三金属”,21世纪将是钛的世纪。
当前钛的生产方法当前钛的生产采用金属热还原法,其是指利用金属还原剂(R)与金属氧化物或氯化物(Mx)的反应制备金属M。
已经实现工业化生产的钛冶金方法为镁热还原法(Kroll法)和钠热还原法(Hunter法)。
因为Hunter法比Kroll法生产成本高,所以目前在工业中广泛应用的方法只有Kroll法。
Kroll法从1948年开发当初就因其成本高、还原效率低而受到批评。
半个世纪过去了,该工艺并没有根本的改变,仍然是间歇式生产,未能实现生产的连续化。
金属钛生产方法的新动向世界钛工业经过几十年的发展,尽管对Kroll法和Hunter法进行了一系列的改进,但它们均是间歇操作,小的改进并不能大幅度降低钛的价格。
因此应开发新的、低成本的连续化工艺才能从根本上解决高生产成本这一问题。
为此,研究人员进行了大量的实验和研究。
当前研究的重点有以下几种方法:电化学还原法为了降低成本,人们对金属钛直接除氧进行了研究。
国外有人用电化学的方法使钛中固溶氧的浓度降低到检出界限(500ppm)以下。
他们认为在电化学除氧的过程中,除氧剂钙在电解氯化钙熔盐时产生,O2-在阳极以CO2或CO的形式析出。
这种新型高纯化方法,不仅用于钛的脱氧,而且适用于钇、钕等稀土金属,并且可使氧含量降低到10ppm。
电化学的方法的工业化实验的流程是:首先将二氧化钛粉末用浇注或压力成形,烧结后作阴极,以石墨为阳极,以CaCl2为熔盐,在石墨或钛坩埚中进行电解。
所加电压2.8V~3.2V,低于CaCl2的分解电压(3.2V~3.3V)。
钛的基本知识

熔炼钛渣基本知识钛是一种金属元素,钛有13种同位素,其中稳定同位素5个,其余8个为不稳定的微量同位素,钛的最高氧化钛通常是正四价。
钛广泛应用于航空航天、化工、冶金、电力、船舶和日常生活中。
由于钛的化学活性很强,所以自然界中没有单质存在,总是和氧结合在一起。
在矿中钛主要以TiO2和钛酸盐形式存在。
FeO、Fe2O3、TiO2三者可形成无限固溶体。
钛铁矿是一种以偏钛酸铁晶格为基础的多组分复杂固溶体,熔点是1470ºC。
理论分子式为Fe TiO3(FeO·TiO2),分岩矿和砂矿,岩矿储量大,FeO/ Fe2O3高,结构致密,不易将TiO2与其他成分分离。
砂矿储量小,FeO/ Fe2O3小,结构疏松,易将TiO2与其他成分分离。
世界上90%以上钛矿用于生产钛白。
钛的氧化物中主要是TiO2,此外还有许多低价氧化物,如TiO、Ti2O3、Ti3O5。
高价氧化物,如TiO3、Ti2O7等,它们彼此可形成固溶体。
TiO2在自然界中存在三种同素异型钛态,即金红石型、锐钛型和板钛型。
金红石型TiO2是最稳定的一种,即使在高温下也不发生转化和分解。
锐钛型TiO2仅在低温下稳定,610ºC便开始缓慢转化为金红石型,915ºC可完全转化为金红石型。
板钛型TiO2是不稳定化合物,加温高于650ºC则转化为金红石型。
TiO2是一种白色粉末。
是两性化合物。
钛渣是由钛铁矿经火法冶金处理后获得的含钛品位较高的物料,含TiO2一般大于72%的富钛料。
钛渣分酸溶性钛渣(TiO2为72~85%,主要用于硫酸法生产钛白)和高钛渣(TiO2≥85%,主要用于氯化法生产钛白和金属钛)。
酸溶性钛渣应含有适量的助熔杂质(主要是FeO 和MgO)和一定量的Ti2O3,使钛的氧化物尽可能赋存于黑钛石(Mg Ti2O5)固溶体中,并在工艺上尽量采取措施避免生成金红石型TiO2。
钛渣是一种高熔点的炉渣,钛渣熔体具有强的腐蚀性、高导电性和其粘度在接近熔点温度时而剧增的特性。
钛渣生产新技术—中国钒钛之都的生产、市场与产业的知识元素

钛渣生产新技术—中国钒钛之都的生产、市场与产业的知识元素原创邹建新等近年钛渣生产技术的发展方向体现在三方面,一是合理发展大型密闭矩形电炉,二是采用大型圆形密闭电炉,三是针对现有的圆形电炉进行局部各环节的改进。
比如,近年云南新立公司引进了南非、德国及乌克兰的大型直流空心电极电弧炉技术,并进行了优化改进,运行效果较好。
近年具有代表性的钛渣生产新技术如下。
(1)高杂质钛铁矿精矿制取富钛料的方法中国地质科学院矿产综合利用研究所提出了一种高杂质钛铁矿精矿制取富钛料的方法,涉及富钛料的制取方法技术领域,其技术路线为:原矿—磁选—铁精矿—尾矿—浮选—钛铁矿精矿—焙烧—磁选—还原熔炼—钛渣—提纯—富钛料,该法集电炉熔炼法和酸浸法之优势,克服了两法之不足,既能处理高杂质含量的岩矿型钛铁矿精矿,又能生产高质量的钛渣产品。
(2)一种环形炉或转底炉冶炼钛渣的方法攀钢提供了一种冶炼钛渣的方法,该方法包括下述步骤:将钛精矿、粘结剂和碳质还原剂的混合物制成球团矿或压团矿;将球团矿或压团矿烘干;使用环形炉或转底炉预还原球团矿或压团矿,从而制得金属化球团或金属化压团;将金属化球团或金属化压团装入电炉进行熔化分离,得到半钢和钛渣,其中,使用球团矿或压团矿的预还原产生的烟气为球团矿或压团矿的烘干提供热量,并使用熔化分离过程中产生的烟气为球团矿或压团矿的预还原提供热量。
(3)利用钒钛铁精矿融态还原冶炼酸溶性钛渣的方法攀钢提供了一种利用钒钛铁精矿融态还原冶炼酸溶性钛渣的方法。
包括步骤:将钒钛铁精矿与钛精矿混合,加入碳质还原剂和粘结剂,形成混合料;对所述混合料进行还原,然后进行渣铁分离处理,以得到半钢和钛渣;对经渣铁分离处理得到钛渣的表面进行喷水,以使钛渣的温度在降温过程中迅速跨越600℃~850℃温度区间,形成酸溶性钛渣。
该方法能够高效利用钒钛铁精矿中的Fe和TiO且具有融态还原过程反应平稳、熔化分离过程效果好、炉况稳定、冶炼周期2短、电耗水平低和生产成本低等优点。
钛冶炼中的炉渣处理与利用
碱处理法
用碱溶解炉渣中的有价值 矿物,再通过沉淀、结晶 等方法将其从溶液中分离 出来。
还原处理法
通过加入还原剂将炉渣中 的有价值矿物还原成易分 离的形态。
生物处理法
微生物浸出法
利用微生物的代谢产物将炉渣中的有价值矿物溶解出来,再通过提取、沉淀等 方法将其回收。
微生物吸附法
利用微生物的吸附作用将有价值矿物从炉渣中吸附出来,再通过分离、回收的 方法进行处理。
复合材料。
增强材料性能
02
通过添加钛渣作为填料,可以改善复合材料的物理和机械性能
,如强度、耐磨性等。
拓宽应用领域
03
钛渣复合材料在航空航天、汽车、化工等领域具有广泛的应用
前景,有助于推动相关产业的发展。
04
案例分析
某钛业公司的炉渣处理方案
方案概述
该方案主要采用高温熔融技术, 将炉渣进行高温处理,提取其中 的有价金属,同时将废渣进行环
02
炉渣处理技术
物理处理法
01
02
03
磁选法
利用不同矿物之间的磁性 差异,通过磁场分离出有 价值的矿物。
重力分选法
根据炉渣中不同矿物密度 的差异,通过重力作用将 其分离。
浮选法
通过向炉渣中加入特定的 化学药剂,使有价值矿物 附着在气泡上,再将其分 离。
化学处理法
酸处理法
用酸溶解炉渣中的有价值 矿物,再通过沉淀、结晶 等方法将其从溶液中分离 出来。
加强钛渣资源循环利用研究,提高资 源利用率,降低对原生资源的依赖。
智能化发展
利用信息技术和自动化技术,实现钛 渣冶炼过程的智能化控制和管理,提 高生产效率和产品质量。
新材料应用
探索新型的钛渣冶炼材料和技术,提 高冶炼效果和产品质量,推动钛工业 的可持续发展。
钛渣介绍
钛渣介绍1概述高钛渣(High Titanium Slag)是经过物理生产过程而形成的钛矿富集物俗称,通过电炉加热熔化钛矿,使钛矿中二氧化钛和铁熔化分离后得到的二氧化钛高含量的富集物。
高钛渣既不是废渣,也不是副产物,而是生产四氯化钛、钛白粉和海绵钛产品的优质原料。
钛渣是由钛精矿(ILMEnite)冶炼而成。
2 应用领域1.TiO2含量大于90%的高钛渣可以作为氯化法钛白的生产原料2.TiO2小于90%的高钛渣是硫酸法钛白生产的优质原料3 成份标准4 状态颜色一般状态粉状,黑色。
粒度在40-200目(Mesh)5 发展概况1、我国钛资源比较丰富,除少量钛铁砂矿外,主要以钛铁岩矿为主,国内钛铁岩矿的缺点是品位低,杂质含量高,不能直接满足氯化法钛白对原料的要求,仅适宜作硫酸法钛白的原料。
由于硫酸法钛白生产过程中产生大量难以治理、污染环境的“三废”,近年来全球硫酸法钛白产能急剧萎缩。
随着我国氯化法钛白以及海锦钛工业的快速发展,对高品位富钛料的需求日益增加。
因此,寻求经济合理的钛原料处理方法,将我国丰富的钛铁矿资源加工成富钛料是我国钛白和钛材产业发展的当务之急。
国内从上世纪50年代就开始对电炉冶炼钛渣的生产工艺进行研究开发,经过近50年的发展,目前全国钛渣生产能力仍很小,约15万吨/年,仅占世界年生产能力的5%。
如果加上攀钢正在建设的年产6万吨钛渣厂和承德年产3.3万吨的高钛渣厂,全国总生产能力也仅占世界的8.1%,与我国丰富的钛资源和全球第二大钛白生产国的地位极不相称。
因此,必须加快我国钛渣产业的发展,为钛白和钛材业提供更多的优质原料,减轻钛白行业环保压力,促进我国钛白和钛材工业整体水平的全面提高。
2、国内钛渣技术发展现状国内钛铁矿一般直接供硫酸法钛白生产作原料,少量加工成富钛料,供氯化法钛白、四氯化钛、海绵钛和电焊条工业使用。
随着海绵钛和氯化钛白工业的迅速发展,对钛渣等富钛料的需求越来越大,国内钛渣产量逐年增加。
钛渣生产原理
钛渣生产原理原创邹建新等钛渣的生产方法主要是电炉熔炼法。
这种方法是使用还原剂,将钛精矿中的铁氧化物还原成金属铁分离出去的选择性除铁,从而富集钛的火法冶金过程。
以无烟煤或石油焦为还原剂,与钛精矿经过配料、制团后,加入矿热式电弧炉内,于1600~1800℃高温下还原熔炼,所得凝聚态产物为生铁和钛渣,根据生铁和钛渣的比重和磁性差别,使钛氧化物与铁分离,从而得到含TiO272%~95%的钛渣。
冶炼钛渣的原料:钛精矿,焦炭(无烟煤)。
冶炼钛渣的产品:酸溶性钛渣或氯化钛渣、生铁。
冶炼钛渣的工艺:电炉熔炼法。
冶炼钛渣的设备:矿热式电弧炉(密闭式、半密闭式、敞口式、圆形、矩形、直流、交流)。
钛渣产品和电弧炉分别如图4.2.1和图4.2.2所示。
图4.2.1 粒状钛渣产品图4.2.2 电弧炉外观钛精矿原料典型化学成分和酸溶性钛渣产品典型化学成分分别如表4.2.1和表4.2.2所示。
表4.2.1 攀钢主流程钛精矿产品典型化学成分,%成分 TiO 2 ΣFe FeO Fe 2O 3 SiO 2 S P MgO Al 2O 3 含量 >47 30.58 34.27 5.55 <3.0 <0.19 <0.0049 6.12 1.34成分 MnO V 2O 5 Cu Co NiCrAsCaO 含量 0.650.0950.00520.00130.0087 <0.005 <0.00770.75表4.2.2 酸溶性钛渣典型化学成分,%成分ΣTiO 2 Ti 2O 3 ΣFe FeO Fe SiO 2 CaO V 2O 5 MgO Al 2O 3 含量 77.2226.46.241.533.771.360.077.621.76生产钛渣的电炉是介于电弧炉与矿热炉之间的一种特殊炉型,有敞开式、半密闭式和密闭式三种,熔炼温度一般为1600~1700℃,最高温度可达1800℃。
高温主反应为:FeTiO3+C=Fe+TiO2+CO ΔG=190900-161T (298~1700K)高温副反应为(生成低价钛):3/4 FeTiO3+C=1/4 Ti3O5+3/4 Fe+CO ΔG=209000-168T (298~1700K)2 FeTiO3+3C=2Fe+Ti2O3+3CO ΔG=213000-171T (298~1700K)FeTiO3+2C=Fe+TiO+2CO ΔG=252600-177T (298~1700K)另有赤铁矿被还原:Fe2O3+3C=2Fe+3CO ΔG=164000-176T (298~1700K)在2000K以下温度,主要是铁和TiO2被还原,伴有低价钛生成。
钛渣生产流程
薛工:现将几个问题的意见写给你,供参考1.钛渣在钛产业链中的地位1.1钛产业链目前的大致走向钛精矿---硫酸法制钛白粉钛精矿---酸溶性钛渣---硫酸法钛白钛精矿---高钛渣---四氯化钛---氯化法钛白钛精矿---高钛渣---四氯化钛---海绵钛---钛合金钛精矿---钛铁钛精矿---钢结碳氮化钛---超硬材料用钛精矿直接生产钛白时,铁在酸溶时生成硫酸铁,为脱Fe,需加铁粉将其还原成硫酸亚铁,再冷冻结晶后,从钛酸液中沉淀出来。
才能保证钛白质量。
因这一路线的酸耗大,流程长,逐渐被钛渣制钛白粉代替。
用酸溶性钛渣生产钛白,因大部分铁已在冶炼中脱出,酸溶时耗酸少,并可减少硫酸铁还原和硫酸亚铁结晶工序,可降低成本,近年来发展很快。
酸溶钛渣和高钛渣的区别在于钛品位高低,钛渣的酸溶性好坏取决于物相,在以Ti3O5为基,溶解FeO、MgO等组成的黑钛石相酸溶性最好。
因此酸溶性钛渣需保存一定的FeO量,MgO存在是有益的。
TiO2的还原程度也不能高。
通常用指标Ti2O3/ TiO2的比值衡量。
而高钛渣是做四氯化钛的原料,TiO2与氯气反应,要求Mg,Ca,Fe含量少,钛高。
对钛的价位没有特别要求。
2.两段法生产钛渣,因在固相还原时,铁的金属化率可控,TiO2的还原成低价钛也可控。
因此这种工艺生产的钛渣容易满足不同用户的要求。
3.由钛精矿富集成富钛料有人造金红石法,钛渣法等,钛渣的优点是钛和铁都能应用。
特别是高铁,低钛原料,铁的回收是一个重要的利润来源。
将铁只作为渣铁回收是最差的方法,只有在设计对将铁的处理一并考虑,将熔分的铁水处理成带合金元素的金属料,是提高附加值的重要方法。
4.钛铁矿固相还原的原理①钛铁矿的组成TiO2●FeO②在液态还原时其中的反应FeO●TiO2→FeO+ TiO2FeO→FeTiO2→Ti3O5→Ti2O3→TiO→Ti→TiCN③钛渣一段法生产时,铁与钛的还原都能进行,铁在低温下完成还原,但要保证渣的流动性,须提高炉温。
- 1、下载文档前请自行甄别文档内容的完整性,平台不提供额外的编辑、内容补充、找答案等附加服务。
- 2、"仅部分预览"的文档,不可在线预览部分如存在完整性等问题,可反馈申请退款(可完整预览的文档不适用该条件!)。
- 3、如文档侵犯您的权益,请联系客服反馈,我们会尽快为您处理(人工客服工作时间:9:00-18:30)。
钛渣的冶炼原理1.钛渣冶炼的原理及工艺流程电炉熔炼钛渣的实质是钛铁矿与固体还原剂无烟煤(或石油焦或叫焦炭)等混合加入电炉中进行还原熔炼,矿中铁的氧化物被选择性地还原为金属铁,钛的氧化物被富集在炉渣中,经渣铁分离后,获得钛渣和副产品金属铁。
钛精矿的主要组成是TiO2和FeO,其余为SiO2、CaO、MgO、Al2O3和V2O5 等,钛渣冶炼就是在高温强还原性条件下,使铁氧化物与碳组分反应,在熔融状态下形成钛渣和金属铁,由于比重和熔点差异实现钛渣与金属铁的有效分离。
期间可能发生的化学反应如下:Fe2O3+C=2FeO+CO (1)FeO+C=Fe+CO (2)以钛精矿为原料,敞口电炉冶炼钛渣的工艺流程如图1所示。
钛渣图1、工艺流程图2. 电炉冶炼的主要特征钛渣是一种高熔点的炉渣,钛渣熔体具有强的腐蚀性、高导电性和其粘度在接近熔点温度时而剧增的特性,而且这些性能在熔炼过程中随其组成的变化而发生剧烈的变化。
2.1钛渣的高电导率和熔炼钛渣的开弧熔炼特征2.1.1钛渣的高电导率钛铁矿在熔化状态具有较大的电导率,在1500℃时为2.0~2.5ks/m,在1800℃为5.5~6.0ks/m,随着还原熔炼钛铁矿过程的进行,熔体组成发生变化,FeO含量减少,而TiO2和低价钛氧化物的含量增加,因此其电导率迅速上升,如加拿大索雷尔钛渣在1750℃电导率为15~20ks/m,而一般的炉渣在1750℃电导率为100s/m,可见钛渣的电导率比普通冶金炉渣的电导率高数十倍甚至几百倍,比普通离子型电解质(如Nacl液体在900℃时的电导率约为400s/m)的电导率都高很多,且温度变化对钛渣电导率影响不大,这些都说明钛渣具有电子型导电体的特征。
2.1.2熔炼钛渣电炉的开弧熔炼特征钛渣的高电导率决定了熔炼钛渣电炉的开弧熔炼特征,即熔炼钛渣的热量来源主要依靠电极末端至熔池表面间的电弧热,这就是所谓的“开弧冶炼”,而在高电阻炉渣的情况下,电极埋入炉渣,熔炼过程的热量来源主要是渣阻热,即所谓的“埋弧熔炼”。
在敞口电炉熔炼钛渣的初期具有短期的矿热炉埋弧冶炼的特征,随着熔炼过程的深入进行,开弧冶炼的电弧特征越来越明显。
熔炼过程超过1小时后,电弧热所占比例可达90%,熔炼过程的后期电弧热所占比例可达97%。
2.2.钛渣熔点和粘度特性对熔炼过程的影响2.2.1钛渣熔点对熔炼过程的影响钛氧化物中的钛-氧键很牢固,它们的熔点很高。
钛渣主要是由钛的氧化物组成,因此它的熔点很高,按其组成其熔点在1580~1700℃之间,钛渣的熔点随其中TiO2含量的增加而升高,熔炼钛渣要在高温下进行,这就要求热量必须高度集中在还原熔炼区。
2.2.2钛渣粘度对熔炼过程的影响钛渣具有短渣的特性,在温度高于熔点处于完全熔化的钛渣熔体具有很低的粘度,但当渣温接近其熔点时,其粘点急剧增加。
这是因为钛渣的结晶温度范围很窄,温度接近熔点时少量结晶固体析出悬浮在熔体中,使熔体变得十分粘稠,造成渣流动性变坏,出炉时困难。
2.3钛渣熔体的高化学活性对电炉的影响钛渣的主要成分是TiO2 ,但还含相当数量的低价钛氧化物,因而具有极高的化学活性,几乎能与所有的金属和非金属材料发生作用。
事实上钛渣熔体能很快的腐蚀普通的耐火材料,所以钛渣的还原熔炼是在炉衬上挂上一层钛渣用于保护炉体。
2.4钛渣熔体的沸腾对熔炼过程的影响钛铁矿的还原反应主要在熔体的表面,但当固体炉料突然陷落到熔体中,或者由于表面还原反应生成的高碳铁经熔体下降,都可能在熔体中或金属铁与熔渣介面上发生瞬间激烈反应,生成的大量的CO气体经熔渣逸出,使熔渣沸腾和喷溅,熔渣的沸腾会把电极淹没,使电炉的瞬间电流增大,造成短路,引起钛渣熔炼不稳定。
在一次加料的间歇式熔炼工艺中,钛渣会经常发生沸腾,造成炉况不稳定,只有通过连续加料和密闭冶炼方式可以避免和减少钛渣的沸腾,使熔炼过程炉况稳定。
2.5杂质元素对钛渣熔体的影响钛渣的熔点随其中TiO2含量的增加而升高,而影响钛渣熔点的另一个因素是它的还原度,即渣中钛渣含有的Ti2O3与TiO2的比值。
当O/Ti =1.76时系统具有最低共熔点,随着O/Ti比值的降低(还原度的增大),系统熔点升高,当O/Ti比值=1.67时达到一个较高的熔点,可见熔炼钛渣的终点最好在O/Ti=1.76左右。
钛原料中的杂质元素如FeO、MgO、CaO、MnO和Al2O3都分别可与TiO2形成二元化合物和低共熔点,在它们一定含量范围内,都起降低钛渣熔点的作用,可见这些杂质元素是一种很好的造渣剂,但杂质元素过高会降低钛渣的品位。
3.钛渣的试验情况集团公司和钛业公司先后在武定和陆良开展了大规模的冶炼钛渣试验,其试验情况如下:3.1武定钛渣试验试验是以云南武定钛渣冶炼厂现有条件,不作任何改变的情况下进行,即敞口电炉,自焙电极,电炉炉底用400×400的碳砖砌筑,炉壁用一般的耐火砖砌筑,出炉口正对1#电极。
3.1.1主要工艺条件及操作配碳量:以矿中全部Fe2O3转化为FeO,96%FeO还原成金属铁,30%TiO2还原成Ti3O5,熔池中铁的渗碳按2%计算理论配碳量为加矿量的7.98%,折合成焦粉为加矿量的9.85%,而实际配碳约12%。
电参数:在该电炉及变压器不配套的情况下,几乎没有调节的余地,加之试验炉次较少,就以现行操作的100V,作为二次电压进行冶炼。
冶炼操作:每炉投入钛精矿1.49吨,其中0.78吨作为配沥青、焦粉的混合料一次性加入炉内并捣实,0.71吨的钛精矿是作为附加矿,在冶炼过程中间断式地从电极孔逐渐加入炉内,作为调节品位,避免翻渣、结壳、喷溅的一种手段。
每出炉一次算一个炉号,每炉冶炼180分钟,波动在150~240分钟,出炉时不断电,用氧气烧穿炉口,渣、铁混出,排入渣盘内,渣盘的侧面沿底部设有φ100mm的孔,出炉5~8分钟,待钛渣凝结后,抽开渣盘侧面小孔,铁水注入沙盘成80~90kg的铁锭。
出炉完毕堵上出炉口,沿三个电极孔分别加入约60kg矿,7kg焦粉后,捣炉,加料,并用铁锤夯实,放电极,合闸送电,冶炼下一炉,从出炉到第二炉送电时间约10~20分钟。
3.1.2试验概况及结果试验于7月26日19:40时开始,至7月29日24:00时结束,冶炼时间为76小时20分,共冶炼23炉,平均每炉间隔时间20分钟,投入攀枝花钛精矿30吨,冶金焦粉2.98吨,沥青1.296吨(7.2%),产钛渣18.425吨,半钢7.8吨。
其中过渡钛渣3.375吨,成品渣15.05吨,洗炉渣及钛渣(TiO2)品位分别为79.52%、76.65%。
4~20炉的17炉连续稳定试验,钛渣平均电耗2201KWh/t渣,TiO2收率92.88%。
电极消耗55kg/t渣。
整个冶炼期间冶炼平稳、炉况顺行,没有因翻渣喷溅而被迫停电或跳闸现象,达到了预期效果。
3.1.3结论1.经过这次工业试验,再一次证明了敞口电炉用攀枝花钛矿(TiO2在47%以上)冶炼76%左右的酸溶性钛渣的可行性。
根据出炉渣的粉化情况看,钛渣品位超过78%以上,粉化现象严重,而品位低于74%的钛渣,冶炼炉温低、产量低。
因此,我们认为用攀枝花钛矿冶炼酸溶性钛渣的适宜品位在74%~77%之间。
2.敞口电炉、自焙电极冶炼钛渣,用约50%的矿拌焦、沥青,一次加入炉内捣实,50%的粉矿逐渐从电极孔加入,即类似密闭电炉连续加料的工艺,可以解决我国传统冶炼的翻渣、结壳、喷溅、电极串动跳闸、变压器功率不能充分发挥的问题。
3.该冶炼方法使用自焙电极,钛渣电耗达2200KWh/t渣,TiO2品位76.65%,钛渣含硫0.091%,半钢含硫0.171%,可使钛渣成本较大幅度降低,产品钛渣、半钢质量得到提高,有利于半钢处理利用。
4.该冶炼方法不能解决钛渣冶炼环境恶劣,工人劳动强度大,煤气不能利用的问题,有待进一步研究解决。
3.2陆良钛渣试验3.2.1主要操作制度3.2.1.1配碳量以矿中Fe2O3全部转化为FeO,90%~96%FeO还原成金属铁,30%TiO2还原成Ti3O5,熔池中铁的渗碳按2%计算理论配碳量,折合成还原剂的加入量。
3.2.1.2电参数120V。
3.2.1.3送电制度。
通过控制电流大小作为敞口电炉钛渣冶炼控制炉况的手段。
3.2.1.4冶炼操作将沥青、焦粉和钛精矿按照一定比例混合均匀,加入炉内并捣实,每炉加入混合矿约3.0吨。
在冶炼过程中,间断式地从电极孔人工加入少量钛精矿作为调节品位,避免翻渣、结壳、喷溅的一种手段。
每炉冶炼时间控制在150min左右。
出炉时不断电,用氧气烧穿炉口,渣铁混出,渣车侧面沿底部设有φ100mm的出铁孔,待钛渣凝结后,通开出铁孔,铁水浇注成80~90kg的铁锭。
铁水放完后,立即用水管对钛渣进行表面喷水冷却,至钛渣表面变暗为止。
用葫芦吊将其吊入简易水池(长×宽×高=5000×3000×800mm,用5mm厚的钢板制成的)中,水池中严禁装水。
等钛渣冷却后将其破碎得钛渣成品。
出炉完毕后堵上出炉口,进行捣炉作业,开始下一炉冶炼,出炉间隔20~30min。
3.2.2试验概况及结果3.2.2.1攀枝花钛矿与云南钛矿各50%的混矿试验(1)冶炼TiO279±2%的钛渣试验配料比混合钛矿∶焦碳∶沥青=100∶11∶7进行冶炼。
在条件试验阶段,测得出炉渣铁温度较高,达1800℃以上,比所冶炼钛渣的熔点1700℃左右高很多。
虽然较高的炉温对提高碳还原钛精矿中铁氧化物的反应速度有利,但温度过高,渣中低价钛大量出现会影响钛渣的质量,既冶炼时间在90min至120min时,将电极电流稳定控制在120A左右,而冶炼时间达到120min至150min时,逐渐降低电极电流到100A。
表4:攀钛矿与云南钛矿各50%生产79%±2渣化学成分 %SiO2 Al2O3CaO MgO P V2O5TiO2TFe FeO Ti2O34.45 2.19 1.605.37 <0.005 0.232 79.996.107.85 12.08 (2)冶炼TiO275±2%的钛渣试验配料比调整为:混钛矿∶还原剂∶沥青=100∶10(20%细冶金焦粉灰+80%无烟煤) ∶8,送电制度延用了冶炼79±2%钛渣时的送电制度。
试验共产出品位为75±2%的成品钛渣100.95吨,其典型化学全分析见表10。
通过试验确定用混合矿生产TiO275±2%钛渣的合理的配料比是:混钛矿∶无烟煤∶沥青=100∶9∶7.5 ,或者混钛矿∶还原剂∶沥青=100∶10(20%细冶金焦粉灰+80%无烟煤) ∶8;合理的送电制度见图2。
表5:攀钛矿与云南钛矿各50%生产75±2%渣化学成分 %SiO2 Al2O3CaO MgO P V2O5TiO2TFe FeO Ti2O34.39 2.05 1.60 4.16 <0.005 0.413 76.09 10.25 13.19 9.03 3.2.2.2全云南钛矿试验(1)冶炼TiO282±2%的钛渣试验配料比为:云南矿∶无烟煤∶沥青=100∶9∶8。