订书机组件--护柄压手壳体注塑模具毕业设计说明书
订书机设计说明

南京航空航天大学机电学院工业设计专业课程设计总结报告课程计算机辅助设计与制造设计题目打孔机(标准Ⅱ型)设计学生姓名吴洁学号 05005201指导教师刘苏教授起止日期2003、6、11 —2003、6、27一、产品功能、结构介绍:图1-1结构:大体由底盘(bottom)——软塑料制成,套在金属底座上,有条形凸出条和半圆形凸卡住底座的边缘。
底座(under)——金属材料,一次性冲压做成,上有两个孔,有由打孔柱打孔时完全穿透,还有一个三角形突起,用于固定纸张伸入程度。
支架(hold、hold-)——金属钣金材料,永久固定于底座上,支撑上盖上的轴。
上盖(up)——塑料注模,有很多加强筋,加强强度。
标尺(ruler)——与底盘一样是软塑料制成。
构成。
功能:当给上盖施加一个向下的力,上盖绕支架上的轴旋转的同时把打孔的柱子向下压,穿过纸张和底座,完成打孔任务。
纸屑落入底盘内。
标尺可以自然伸缩,以测量在纸上打孔的位置。
二、产品材料清单:图2-1三、 简介产品组件和主要零件的设计过程:图3-1钣金件—平整图3-2钣金件—折弯图3-3钣金件---从半径创建拉伸壁图3-4打孔完工图3-5图3-6孔和加材料用复制—新参照—不同模型,来复制过去图3-7在草绘里镜像平整钣金截面,余下的与上一个同样。
四、 简介产品主要零件的模具设计过程:开模方法:用分型面和模具体积块来开模。
1、 做模具体积块。
用拉伸命令做模具体积块用来分割整个工件。
体积块以标尺的边缘为参照,拉伸充满整个标尺的空间,再在抽出边缘增加一个稍大的立方体,以便于以后体积块的抽出。
2、做分型面。
由于表面比较凹凸不平,所以使用复制命令来制作分型面。
先复制底面的曲面,再做面延拓到工件的四周,完成分型面的制作。
3、分割体积块。
先用模具体积块分割整个工件,一个模具体积块取暂时名为temp 。
在用分型面分割temp 模具体积块,两个模具体积块,分别为up 和under 。
4、 开始抽取,然后铸模。
论订书机组件护柄压手壳体注塑模具设计

论订书机组件护柄压手壳体注塑模具设计机电工程学院毕业设计说明书设计标题: 订书机组件——护柄压手壳体注塑模具设计先生姓名:XX学号:XXXX专业班级:模具设计与制造0602班指点教员:XXX2020 年6月10 日目录1 塑料的工艺性设计 (2)1.1 注塑模工艺 (2)1.2 化学和物理特征 (2)1.3 塑件的尺寸与公差 (3)2 注射成型机的选择 (4)3 型腔规划与分型面设计 (5)3.1 型腔数目确实定 (5)3.2 型腔的规划 (5)3.3 分型面的设计 (5)4 浇注系统设计 (6)4.1 主流道设计 (6)4.2 主流道衬套的固定 (7)4.3 分流道的设计 (8)4.4 浇口的设计 (10)5 成型零件的设计 (12)5.1 成型零件的结构设计 (13)5.1.1 凹模结构设计 (13)5.1.2型芯结构设计 (14)5.2 成型零件任务尺寸计算 (15)5.2.1 外型尺寸 (16)5.2.2 内腔尺寸 (17)6 合模导向机构设计 (18)6.1 导柱结构 (19)6.2 导套结构 (20)7 脱模机构的设计 (20)7.1 脱模机构的设计的总体原那么 (20)7.2 推杆设计 (21)7.2.1 推杆的外形 (21)7.2.2 推杆的位置与规划 (21)7.3 斜推抽芯机构的设计 (22)7.4 开模行程与推出机构的校核 (22)设计总结 (23)参考文献 (24)1 塑料的工艺性设计1.1 注塑模工艺枯燥处置:无定形料,活动性中等,吸湿大,必需充沛枯燥,外表要求光泽的塑件须长时间预热枯燥80-90度,3小时熔化温度:220~275℃,留意不要超越275℃。
模具温度:50-60度,建议运用50℃。
结晶水平主要由模具温度决议。
注射压力:可大到1800bar。
注射速度:通常,运用高速注塑可以使外部压力减小到最小。
假设制品外表出现了缺陷,那么应运用较高温度下的低速注塑。
流道和浇口:关于冷流道,典型的流道直径范围是4~7mm。
【说明书】手机套注射模具设计说明书

【关键字】说明书课程设计说明书题目手机套注射模具设计姓名专业高分子材料与工程班级指导老师月20 日洛阳理工学院课程设计(论文)任务书填表时间:2012 年12 月20 日年月日手机套注塑模设计随着制造业和计算机软硬件的发展,模具已经得到了快速发展和广泛的应用,因此对各种塑料制品的模具设计具有重要的理论意义和实际应用价值。
此篇论文论述了热塑性材料成型塑件时所用的整套注塑模具的设计过程,包括塑件的成型工艺,分塑面的选择论证,浇注系统的设计、成型零件的尺寸计算、镶块的固定方式、脱模结构、推出机构、冷却系统等的设计。
论证了成型塑件的方式为注塑成型,采用浇注系统推杆推出的方式推出制件的好处,以及整套模具采用标准模架A1形式的好处。
本次设计的制品为诺基亚手机套注射模设计,利用CAD来完成其装配图和零件图。
模具采用了侧抽芯,使侧向的孔能更好的脱模。
模具结构紧凑、工作可靠、操作方便、运转平稳、冷却效果好、劳动强度低、生产效率高、生产的塑件精度高、生产成本低。
本文从型腔数量和布局的确定、注射机选择、流道的设计、模板及其标准件的选用、冷却系统、成型部件的设计等给出了详细的设计过程。
关键词:手机套;注塑模;模具结构高分子材料科学是现代自然科学的结晶、是物质科学中的新科学和增长点。
高分子材料的问世改变了20世纪的物质文明,推动了人类社会的进步。
高分子材料包括塑料、合成塑胶和合成纤维。
作为高分子材料之一的塑料,集原料丰富,制造方便,加工容易、质地优良、轻巧耐用、用途广泛和投资效益显著等众多优点于一身,在现代工业生产领域中占有很重要的地位。
采用模具成型的工艺代替传统的切削加工工艺,可以提高生产效率,保证零件质量,节约材料,降低生产成本,从而取得很高的生产效率。
因此塑料已成为金属的良好代用材料并得到了广泛的应用,出现了金属材料塑料化的趋势。
我国塑料模工业从起步到现在,历经半个多世纪,有了很大发展,模具水平有了较大提高。
成型工艺方面,多材质塑料成型模、高效多色注射模、镶件互换结构和抽芯脱模机构的创新方面也取得较大进展。
注塑模说明书毕业设计
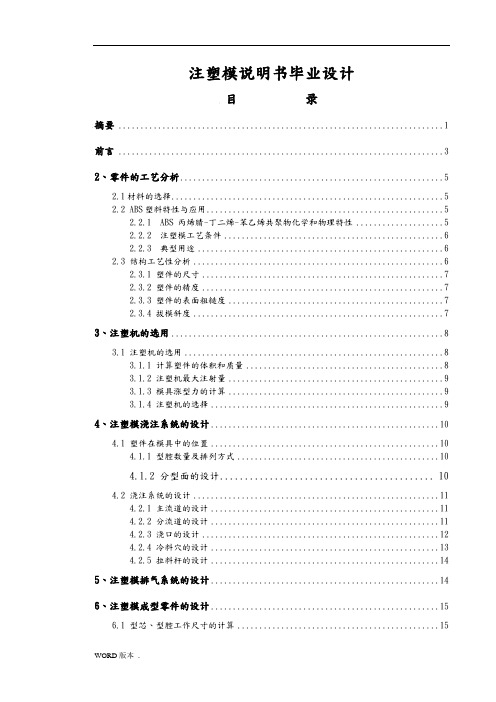
注塑模说明书毕业设计目录摘要 (1)前言 (3)2、零件的工艺分析 (5)2.1材料的选择 (5)2.2 ABS塑料特性与应用 (5)2.2.1 ABS 丙烯腈-丁二烯-苯乙烯共聚物化学和物理特性 (5)2.2.2 注塑模工艺条件 (6)2.2.3 典型用途 (6)2.3 结构工艺性分析 (6)2.3.1 塑件的尺寸 (7)2.3.2 塑件的精度 (7)2.3.3 塑件的表面粗糙度 (7)2.3.4 拔模斜度 (7)3、注塑机的选用 (8)3.1 注塑机的选用 (8)3.1.1 计算塑件的体积和质量 (8)3.1.2 注塑机最大注射量 (9)3.1.3 模具涨型力的计算 (9)3.1.4 注塑机的选择 (9)4、注塑模浇注系统的设计 (10)4.1 塑件在模具中的位置 (10)4.1.1 型腔数量及排列方式 (10)4.1.2 分型面的设计 (10)4.2 浇注系统的设计 (11)4.2.1 主流道的设计 (11)4.2.2 分流道的设计 (11)4.2.3 浇口的设计 (12)4.2.4 冷料穴的设计 (13)4.2.5 拉料杆的设计 (14)5、注塑模排气系统的设计 (14)6、注塑模成型零件的设计 (15)6.1 型芯、型腔工作尺寸的计算 (15)6.1.1 模具成型零件的制造误差 (15)6.1.2 模具安装配合的误差 (15)6.1.3 型芯、型腔工作尺寸的计算 (16)6.2 确定模镶件外形尺寸 (17)6.2.1 确定模镶件的长、宽尺寸 (18)6.2.2 模镶件高度尺寸的确定 (19)6 .2.3 其他设计要点 (19)6.2.4 模镶件配合尺寸与公差 (20)6.2.5 模镶件的型腔表面粗糙度 (20)6.3 成型零件的结构设计 (20)6.3.1 凹模的结构设计 (20)6.3.2 凸模的结构设计 (20)6.3.3 镶件的紧固 (21)7、注塑模结构件的设计 (21)7.1 模架的设计 (21)7.1.1 模架的选用 (21)7.1.2 动、定模板开框尺寸的设计 (21)7.2 浇口套的设计 (22)7.3 模架中其他结构件的设计 (22)7.3.1 撑柱的设计 (22)7.3.2 定位圈 (23)7.3.3 顶棍孔 (23)7.3.4 限位钉 (24)7.3.5 紧固螺钉 (24)8、注塑机脱模系统的设计 (24)8.1 脱模力的计算 (24)8.2 推出机构的设计 (26)8.2.1推杆位置的设计 (26)8.2.2推杆的直径 (26)8.2.3推杆固定形式及装配要求 (26)9、注塑模侧抽芯机构的设计 (27)10、注塑模导向定位系统的设计 (28)10.1 导向系统的设计 (28)10.2 定位系统的设计 (29)11、注塑模温度控制系统的设计 (29)11.1 冷却计算 (30)11.2 冷却系统的确定 (30)11.2.1 冷却系统的设计原则 (30)11.2.2 冷却系统机构的确定 (30)总结 (32)感谢词 (33)参考文献 (34)摘要塑料注塑成型所用的模具称为注塑成型模具,简称注塑模。
注塑模型毕业设计说明书

注塑模型毕业设计说明书
注塑模型毕业设计说明书
设计背景:
注塑模型是一种广泛应用于制造业中的生产工艺,它对于零件原型的制造以及各种产品的批量生产具有重要意义。
本毕业设计的目的就是开发一种高效的注塑模型制造方案,通过对注塑机、注塑模具以及注塑温度等参数的优化设置,实现注塑模型的质量提升和处理效率的提升。
设计方法:
本设计采用了以下几种方法来实现注塑模型的优化制造:
1.优化模具结构。
采用CAD软件进行模具设计,优化模具结构、角度和片数,提高模具运行效率,节约材料成本。
2.优化注塑机设备。
根据注塑模型的特性,选择最适合的注塑机设备,采用高效的注塑技术,确保生产效率。
3.优化注塑温度。
根据不同材料的特性,制定不同的注塑温度方案,减少退火现象,并提高模型质量。
4.生产过程管理。
对于注塑模型的生产过程进行管理,提高生产效率和生产质量,确保模型质量稳定。
设计结果:
通过优化以上设计方法,本毕业设计成功实现了注塑模型的高效制造,提高了生产效率和产品质量。
本设计的成功应用,表明了优化注塑模型生产的重要性和行业应用前景。
同时,本设计也为学术研究和工业生产领域提供了支持和借鉴。
结论:
本毕业设计的目的是通过优化注塑模型制造方案,实现模型质量提升和处理效率的提升,为注塑模型的生产提供优化解决方案。
经过实验验证,本设计成果可以在实际应用中发挥重要作用,具有一定的理论与实践意义,为注塑工艺的研究和优化提供了有价值的参考。
订书机外壳注射模设计

11塑件工艺分析1.1塑件分析如图1所示是订书机外壳,从该塑件的外观可以看出为了要使此塑件的外观光滑,对模具型腔的要求是达到镜面光洁度。
可以利用弯销来实现侧抽芯。
塑件尺寸比较小,但是有较多的内部弯曲的加强肋,考虑到该塑件注射时要有一定的流动性。
从其中的浇口痕迹看,只有一个浇口位置,处于塑件中部。
一端有两个圆柱孔、两个半圆柱也及圆柱孔旁边的浅孔,这些可以通过外侧抽芯来实现。
而内部的凸台可以通过滑块实现内侧抽芯实现成型。
订书机外壳在使用过程中要承受一定的力量,所以塑料应该有足够的刚度、强度、硬度以及抗冲击性等因素,所以选择聚丙烯(PP)做为该订书机外壳的材料。
型腔使用EDM进行最后的精加工,EDM加工时要请注意选择合适的加工工艺,如应用较小的加工电流,保证加工表面粗糙度值较小以方便后续的抛光处理。
如果放电加工工艺选择不当,则可能造成放电白层,抛光时可能没有将该层抛除,就会影响模具的质量。
1.2塑料材料的成型特性分析性能特点:化学稳定性好,耐寒性差,光、氧作用下易降解,机械性能比聚乙烯好。
成型特点:成型时收缩大成型性能好,易变形翘曲,尺寸稳定性好,柔软性好。
有“铰链”特性。
该订书机外壳需要与上盖进行配合,所以对其尺寸稳定性也有要求,而选用聚丙稀能达到此要求。
模具设计的注意事项:因有“铰链”特性,注意浇口位置设计;防缩孔,变形;收缩率为1.0%~3.0%(纯聚丙稀)。
在本设计中选用的收缩率为2%。
使用温度:10℃~120℃,订书机都是在常温下使用,满足使用温度的要求。
主要用途:板、片、透明薄膜、绳、绝缘零件、汽车零件、阀门配件、日用品等。
订书机属于日用品。
1.3 脱模斜度由于制品冷却后产生收缩时会紧紧包在凸模上,或由于黏附作用而紧贴在型腔内。
为了便于脱模,防止制品表面在脱模时划伤、擦毛等,在制品设计时应考虑其表面在合理的脱模斜度。
聚丙烯的脱模斜度是25'~1º之间。
本设计中的脱模斜度采用1º。
注塑模具毕业设计说明书
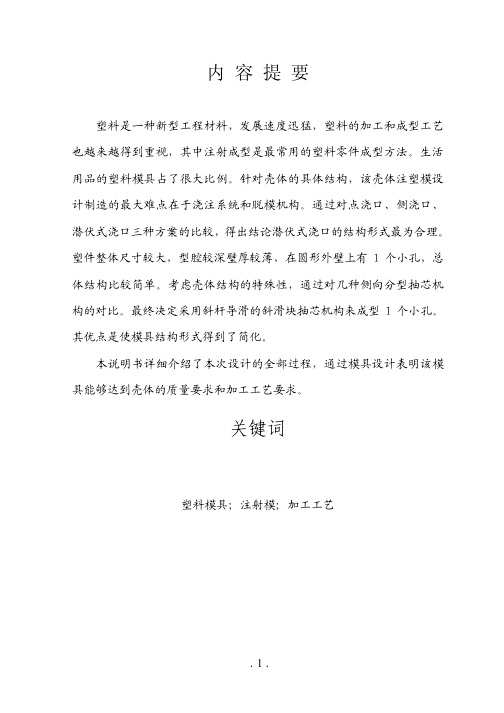
tcartsbA revoC kcaB eht rof dloM noitcejnI fo ngiseD
gniM aiX �rotcurtsnI gnail gnahZ �rehtuA
. 3.
ssecorp erutcafunaM llehS; dloM noitcejnI;dlom citsalp ehT
. 1. 使件塑、求要艺工工加是其尤。 ”柱支大三“的术技型成品制料塑为誉被 �具模的进先和备设的效高、艺工工加的理合�中产生品制料塑代现 。此如是更模料塑型 大�的贵昂分十是用费模制说来 般一�外模易简除�响影的大当相有也 本成件塑对模料塑�次再。响影 的要重有具�度程易难的作操对�性理 合的构结模料塑�中程过工加件 塑在�次其。响影的要重分十着起�等 量质在内与量质观表、小大力应 内、能性理物的件塑及以度精状形度精 寸尺�材型或�品制对均�等定 确的法方型定及以式方模脱、择选臵位 气排与浇进、面型分、度糙粗面 表、寸尺道流、状形腔模�先首。响影 的性定决就�量产与量质品制对 计设具模料塑�后以定确艺工工加及计 设品制、料材料塑在。具模料塑 的应相计设须必品制料塑些这产生了为 。 用应泛广得获面方等活生 常日和防国、 业农、业工在已品制料塑 。题课大重的中域领工加料材子分 高 代 当 是 , 计 设 化 优 模 料 塑 . 模 料 塑称 简 , 具 模 形 成 料 塑 为 称 , 具 模 的 形 成 品 制料塑于用,中域领工加料材子分高在。业行大个一为成已业造制具模以 所�品成制来具模过通是数多中 型成在�件零械机种各和品制的用所活 生常日们人因。等具模璃玻�具 模胶橡�具模铸压属金�具模压冲属金 �具模料塑为分具模将般一�同 不法方型成�同不料原的用采所品制按 � 具工的品制的寸尺和状型 定一有具型成 去状形定特其用利是具模 能功的模料塑 1.1
手机外壳注塑模设计 任务书+开题报告+论文

毕业设计(论文)任务书专业模具设计与制造班级模具072 姓名一、课题名称:手机外壳注塑模设计二、主要技术指标:零件的生产批量为5万件,制品颜色为银灰色,塑件表面为亚光面、平整;塑件表面不允许有缩壁和飞边。
三、工作内容和要求:设计内容:1)、设计产品的三维图;2)、塑件的注塑工艺分析;3)、模具的基本结构和模架的设计;4)、模具结构、尺寸的设计和计算;5)、模具主要零件图和加工工艺规程的设计;6)、完成模具总装配图和模具主要零件图;7)、调整模具的装配及试模;8)、编写计算说明书;9)、进行毕业答辩。
设计要求:1)、模具总装配图1张(1号或2号图纸)。
2)、模具典型零件工作图14-16张。
3)、设计计算说明书一份(8000~10000字)。
四、主要参考文献:[1]齐卫东.塑料模具设计与制造[M].第一版.北京:高等教育出版社,2004[2]陈剑鹤,吴云飞,黄桂林.塑料模具设计图册[M].北京:清华大学出版社,2008[3]史新民.机械设计手册[M].第一版.南京:东南大学出版社,2007[4]张维合.注塑模设计实用教程.第二版.北京:化学工业出版社,2007学生(签名)年月日指导教师(签名)年月日教研室主任(签名)年月日系主任(签名)年月日毕业设计(论文)开题报告目录摘要-----------------------------------------------------------6 前言-----------------------------------------------------------61.塑件的零件图------------------------------------------------72.塑件的注塑工艺分析------------------------------------------8 2.1塑件的材料特性--------------------------------------------8 2.2材料的成型性能分析----------------------------------------8 2.3塑件表面质量要求------------------------------------------8 2.4塑件成型工艺参数------------------------------------------8 2.5塑件的体积和重量------------------------------------------82.6注塑机的选择----------------------------------------------83.模具的结构方案设计-----------------------------------------9 3.1分型面的选择----------------------------------------------9 3.2确定模具总体结构类型-------------------------------------10 3.3成型零件设计---------------------------------------------10 3.4选择标准模架---------------------------------------------11 3.5浇注系统-------------------------------------------------12 3.6推出机构-------------------------------------------------13 3.7冷却系统-------------------------------------------------143.8排气系统-------------------------------------------------154.注射机的校核----------------------------------------------16 4.1注射压力校核---------------------------------------------16 4.2锁模力校核-----------------------------------------------16 4.3安装部分尺寸校核-----------------------------------------16 4.4开模行程校核---------------------------------------------16 4.5推出机构校核---------------------------------------------16 答谢辞--------------------------------------------------------17 参考文献------------------------------------------------------17 附录一------------------------------------------------------------------------------------18 附录二------------------------------------------------------------------------------------19摘要:随着现代塑件制品的使用广泛且形状要求越来越精确,塑料模具的设计的要求也越来越高。
- 1、下载文档前请自行甄别文档内容的完整性,平台不提供额外的编辑、内容补充、找答案等附加服务。
- 2、"仅部分预览"的文档,不可在线预览部分如存在完整性等问题,可反馈申请退款(可完整预览的文档不适用该条件!)。
- 3、如文档侵犯您的权益,请联系客服反馈,我们会尽快为您处理(人工客服工作时间:9:00-18:30)。
机电工程学院毕业设计说明书设计题目: 订书机组件——护柄压手壳体注塑模具设计学生姓名: XX学号: XXXX专业班级:模具设计与制造0602班指导教师: XXX2009 年6月 10 日目录1 塑料的工艺性设计 (2)1.1 注塑模工艺 (2)1.2 化学和物理特征 (2)1.3 塑件的尺寸与公差 (3)2注射成型机的选择 (4)3 型腔布局与分型面设计 (5)3.1 型腔数目的确定 (5)3.2 型腔的布局 (5)3.3 分型面的设计 (5)4 浇注系统设计 (6)4.1 主流道设计 (6)4.2 主流道衬套的固定 (7)4.3 分流道的设计 (8)4.4 浇口的设计 (10)5 成型零件的设计 (12)5.1 成型零件的结构设计 (13)5.1.1 凹模结构设计 (13)5.1.2型芯结构设计 (14)5.2 成型零件工作尺寸计算 (15)5.2.1 外型尺寸 (16)5.2.2 内腔尺寸 (17)6 合模导向机构设计 (18)6.1 导柱结构 (19)6.2 导套结构 (20)7 脱模机构的设计 (20)7.1 脱模机构的设计的总体原则 (20)7.2 推杆设计 (21)7.2.1 推杆的形状 (21)7.2.2 推杆的位置与布局 (21)7.3 斜推抽芯机构的设计 (22)7.4 开模行程与推出机构的校核 (22)设计总结 (23)参考文献 (24)1 塑料的工艺性设计1.1 注塑模工艺干燥处理:无定形料,流动性中等,吸湿大,必须充分干燥,表面要求光泽的塑件须长时间预热干燥80-90度,3小时熔化温度:220~275℃,注意不要超过275℃。
模具温度:50-60度,建议使用50℃。
结晶程度主要由模具温度决定。
注射压力:可大到1800bar。
注射速度:通常,使用高速注塑可以使内部压力减小到最小。
如果制品表面出现了缺陷,那么应使用较高温度下的低速注塑。
流道和浇口:对于冷流道,典型的流道直径范围是4~7mm。
建议使用通体为圆形的注入口和流道。
所有类型的浇口都可以使用。
典型的浇口直径范围是1~1.5mm,但也可以使用小到0.7mm的浇口。
对于边缘浇口,最小的浇口深度应为壁厚的一半;最小的浇口宽度应至少为壁厚的两倍。
ABS材料完全可以使用热流道系统。
成型时间:注射时间 20s~60s高压时间 0s~3s冷却时间 20s~90s总周期 50s~160s1.2 化学和物理特性ABS工程塑料的缺点:热变形温度较低,可燃,耐候性较差。
化学名称:丙烯腈-丁二烯-苯乙烯共聚物英文名称: Butadiene Styrene比重:1.05克/立方厘米成型收缩率:0.4-0.7%成型温度:200-240℃干燥条件:80-90℃ 2小时特点:1、综合性能较好,冲击强度较高,化学稳定性,电性能良好。
2、与372有机玻璃的熔接性良好,制成双色塑件,且可表面镀铬,喷漆处理。
3、有高抗冲、高耐热、阻燃、增强、透明等级别。
4、流动性比HIPS差一点,比PMMA、PC等好,柔韧性好。
用途:适于制作一般机械零件,减磨耐磨零件,传动零件和电讯零件。
成型特性:1.无定形料,流动性中等,吸湿大,必须充分干燥,表面要求光泽的塑件须长时间预热干燥80-90度,3小时。
2.宜取高料温,高模温,但料温过高易分解(分解温度为>270度).对精度较高的塑件,模温宜取50-60度,对高光泽.耐热塑件,模温宜取60-80度。
3、如需解决夹水纹,需提高材料的流动性,采取高料温、高模温,或者改变入水位等方法。
4、如成形耐热级或阻燃级材料,生产3-7天后模具表面会残存塑料分解物,导致模具表面发亮,需对模具及时进行清理,同时模具表面需增加排气位置。
ABS树脂是目前产量最大,应用最广泛的聚合物,它将PS,SAN,BS的各种性能有机地统一起来,兼具韧,硬,刚相均衡的优良力学性能。
ABS是丙烯腈、丁二烯和苯乙烯的三元共聚物,A代表丙烯腈,B代表丁二烯,S代表苯乙烯。
ABS工程塑料一般是不透明的,外观呈浅象牙色、无毒、无味,兼有韧、硬、刚的特性,燃烧缓慢,火焰呈黄色,有黑烟,燃烧后塑料软化、烧焦,发出特殊的肉桂气味,但无熔融滴落现象。
ABS工程塑料具有优良的综合性能,有极好的冲击强度、尺寸稳定性好、电性能、耐磨性、抗化学药品性、染色性,成型加工和机械加工较好。
ABS树脂耐水、无机盐、碱和酸类,不溶于大部分醇类和烃类溶剂,而容易溶于醛、酮、酯和某些氯代烃中。
1.3 塑件的尺寸与公差1.3.1 塑件的尺寸塑件尺寸的大小受制于以下因素:a)取决于用户的使用要求。
b)受制于塑件的流动性。
c)受制于塑料熔体在流动充填过程中所受到的结构阻力。
1.3.2 塑件尺寸公差标准a)影响塑件尺寸精度的因素主要有:塑料材料的收缩率及其波动。
b)塑件结构的复杂程度。
c)模具因素(含模具制造、模具磨损及寿命、模具的装配、模具的合模及模具设计的不合理所可能带来的形位误差等)。
d)成型工艺因素(模塑成型的温度T、压力p、时间t及取向、结晶、成型后处理等)。
e)成型设备的控制精度等。
其中,塑件尺寸精度主要取决于塑料收缩率的波动及模具制造误差。
题中没有公差值,则我们按未注公差的尺寸许偏差计算,查表取MT5。
1.3.3 塑件的表面质量塑件的表面质量包括塑件缺陷、表面光泽性与表面粗糙度,其与模塑成型工艺、塑料的品种、模具成型零件的表面粗糙度、模具的磨损程度等相关。
模具型腔的表面粗糙度通常应比塑件对应部位的表面粗糙度在数值上要低1-2级。
2 注射成型机的选择= 10.105258g估算V塑制品的正面投影面积S= 2534.34mm^2= 9533.26mm^3V公注射机为上海橡塑机厂的XS-ZY-500卧试注塑机。
查表注射压力为104MPa,合模力为350×104N,注射方式为螺杆式,喷嘴球半径R为10mm,喷嘴口直径为4mm(一般工厂的塑胶部都拥有从小到大各种型号的注射机。
中等型号的占大部分,小型和大型的只占一小部分。
所以我们不必过多的考虑注射机型号。
具体到这套模具)。
3 型腔布局与分型面设计3.1 型腔数目的确定型腔数目的确定,应根据塑件的几何形状及尺寸、质量、批量大小、交货长短、注射能力、模具成本等要求来综合考虑。
根据注射机的额定锁模力F 的要求来确定型腔数目n ,即 n 12pA pA F -≤ 式中 F ——注射机额定锁模力(N )P ——型腔内塑料熔体的平均压力(MPa )A 1、A 2——分别为浇注系统和单个塑件在模具分型面上的投影面积(mm 2)大多数小型件常用多型腔注射模,面高精度塑件的型腔数原则上不超过4个,生产中如果交货允许,我们根据上述公式估算,采用一模二腔。
3.2 型腔的布局考虑到模具成型零件和抽芯结构以及出模方式的设计,模具的型腔排列方式如下图所示:图3-1型腔布局3.3 分型面的设计分型面位置选择的总体原则,是能保证塑件的质量、便于塑件脱模及简化模具的结构,分型面受到塑件在模具中的成型位置、浇注系统设计、塑件的结构工艺性及精度、嵌件位置形状以及推出方法、模具的制造、排气、操作工艺等多种因素的影响,因此在选择分型面时应综合分析比较具体可以从以下方面进行选择。
a)分型面应选在塑件外形最大轮廓处。
b)便于塑件顺利脱模,尽量使塑件开模时留在动模一边。
c)保证塑件的精度要求。
d)满足塑件的外观质量要求。
e)便于模具加工制造。
f)对成型面积的影响。
g)对排气效果的影响。
h)对侧向抽芯的影响。
图3-2 分模4 浇注系统设计4.1 主流道设计主流道是一端与注射机喷嘴相接触,可看作是喷嘴的通道在模具中的延续,另一端与分流道相连的一段带有锥度的流动通道。
形状结构如图(3)所示,其设计要点:图4-1 主流道a)主流道设计成圆锥形,其锥角可取2°~6°,流道壁表面粗糙度取Ra=0.63μm,且加工时应沿道轴向抛光。
b)主流道如端凹坑球面半径R2比注射机的、喷嘴球半径R1大1~2 mm;球面凹坑深度3~5mm;主流道始端入口直径d比注射机的喷嘴孔直径大0.5~1mm;一般d=2.5~5mm。
c)主流道末端呈圆无须过渡,圆角半径r=1~3mm。
d)主流道长度L以小于60mm为佳,最长不宜超过95mm。
e)主流道常开设在可拆卸的主流道衬套上;其材料常用T8A,热处理淬火后硬度53~57HRC。
4.2 主流道衬套的固定因为采用的有托唧咀,所以用定位圈配合固定在模具的面板上。
定位圈也是标准件,外径为Φ100mm ,内径Φ35mm 。
具体固定形式如图(4)所示:图4-2 衬套的固定4.3 分流道的设计a) 分流道是脱浇板下水平的流道。
为了便于加工及凝料脱模,分流道大多设置在分型面上,分流道截面形状一般为圆形梯形U 形半圆形及矩形等,工程设计中常采用梯形截面加工工艺性好,且塑料熔体的热量散失流动阻力均不大,一般采用下面的经验公式可确定其截面尺寸:42654.0L m B ⋅=(式1) B H 32= (式2)式中 B ―梯形大底边的宽度(mm )m ―塑件的重量(g )L ―分流道的长度(mm ) H ―梯形的高度(mm )质量大约10.05g ,分流道的长度预计设计成66mm 长,且有2个型腔,所以75.46605.102654.024=⋅⨯=B 取B 为6mm 632⨯=H =4 取H 为4mm根据实践经验,abs 塑料分流道截面直径为4.8~9.5。
所以我们可以选择截面直径为6mm ,H=4mm 。
梯形小底边宽度取8mm ,其侧边与垂直于分型面的方向约成7°。
另外由于使用了水口板(即我们所说的定模板和中间板之间再加的一块板),分流道必须做成梯形截面,便于分流道和主流道凝料脱模。
b) 分流道长度分流道要尽可能短,且少弯折,便于注射成型过程中最经济地使用原料和注射机的能耗,减少压力损失和热量损失。
将分流道设计成直的,总长66mm 。
c) 分流道表面粗糙度由于分流道中与模具接触的外层塑料迅速冷却,只有中心部位的塑料熔体的流动状态较为理想,因面分流道的内表面粗糙度Ra 并不要求很低,一般取1.6μm 左右既可,这样表面稍不光滑,有助于塑料熔体的外层冷却皮层固定,从而与中心部位的熔体之间产生一定的速度差,以保证熔体流动时具有适宜的剪切速率和剪切热。
d) 分流道表面粗糙度分流道在分型面上的布置与前面所述型腔排列密切相关,有多种不同的布置形式,但应遵循两方面原则:即一方面排列紧凑、缩小模具板面尺寸;另一方面流程尽量短、锁模力力求平衡。
4.4 浇口的设计浇口亦称进料口,是连接分流道与型腔的通道,除直接浇口外,它是浇注系统中截面最小的部分,但却是浇注系统的关键部分,浇口的位置、形状及尺寸对塑件性能和质量的影响很大。
a) 浇口的选用它是流道系统和型腔之间的通道,这里我们采用点浇口:✧浇口在成形自动切数断,故有利于自动成形。