铅冶炼工艺流程
铅冶炼工艺流程

铅冶炼工艺流程铅冶炼是一种将铅矿石进行处理,提纯铅金属的工艺过程。
下面将介绍一种常见的铅冶炼工艺流程。
首先,矿石破碎。
将铅矿石经过破碎机进行初步破碎,使得矿石颗粒尺寸减小,便于后续的处理。
然后,矿石选矿。
使用选矿设备将破碎后的矿石进行分离,将其中的铅矿石和其他杂质分开。
常用的选矿设备有浮选机、重选机等。
接下来,矿石浸出。
将选矿后的矿石送入浸矿槽中,加入一定浓度的化学药剂,使得铅矿石的铅物质溶解出来,形成含有铅的浸出液。
然后,浸出液净化。
通过沉淀、过滤等工艺将浸出液中的杂质去除,得到纯净的含铅浸出液。
接下来,浸出液还原。
将含铅浸出液经过还原反应,加入一定的还原剂,使得溶解在液体中的铅物质还原成金属铅。
然后,铅浸出液电解。
将还原后的浸出液放入电解槽中,通过电流作用,使得铅离子在阳极处析出,沉积在阴极上,最终得到纯净的铅金属。
最后,铅金属精炼。
将电解得到的铅金属进行精炼,去除其中的杂质,提高铅金属的纯度。
常用的精炼方法有蒸馏炉法、火法等。
整个铅冶炼工艺流程中,涉及到了破碎、选矿、浸出、净化、还原、电解和精炼等多个环节。
每个环节都有相应的设备和工艺要求,以确保铅金属的提纯和生产效率。
在实际生产中,还需要考虑环保和安全等因素。
铅冶炼会产生一定的废水和废气,需要经过处理才能排放。
此外,还需要进行安全操作,避免铅矿石和化学药剂对人员和环境产生危害。
总之,铅冶炼工艺流程是一个复杂的过程,需要经过多个环节处理和各种设备的协同作用。
随着科技的发展,铅冶炼工艺也在不断改进,以提高生产效率和资源利用率。
铅冶炼工艺流程范文

铅冶炼工艺流程范文铅冶炼是将含铅矿石经过一系列的工艺流程进行提纯和精炼,最终得到纯度较高的铅金属的过程。
下面是介绍铅冶炼工艺流程的详细步骤。
1.矿石破碎和磨矿:首先,将含铅矿石进行破碎和磨矿,使其颗粒度适合进一步的处理。
这一步通常使用颚式破碎机和球磨机进行。
2.浮选分离:将磨碎后的矿石与水混合并加入气泡剂,通过浮选机进行浮选分离。
由于铅矿与气泡剂的亲和力不同,可以使含铅矿石浮在液体表面,而其他矿石沉在底部,实现分离。
3.精选:将浮选分离得到的含铅矿石进一步进行精选,以去除杂质。
通常采用重力浮选、电选和磁选等方法,根据矿石的特性选择合适的方法。
4.煅烧:经过精选的含铅矿石进行煅烧处理。
煅烧是指将矿石放入高温炉中进行加热,使矿石中的硫分子脱离矿石,转化为氧化硫气体,然后从矿石中释放出来。
这样可以降低矿石中的硫含量。
5.炼铅炉:煅烧后的矿石被输送到炼铅炉中进行进一步处理。
炼铅炉通常采用反射炉或旋风炉。
矿石通过炉内的矿石料层不断降低,同时加入煤和石灰石,形成熔融的炼渣和金属铅。
6.溶炼:金属铅被输送到溶炼炉中,进行进一步的提纯和精炼。
通常采用低温脱硫、半球炉和精炼炉等工艺方法,去除金属铅中的杂质,提高纯度。
7.铸造和冷却:铅液经过精炼后,通过铅水道进入铸造机中,进行铅块的铸造。
铸造后的铅块需要经过冷却处理,使其快速冷却至室温。
8.检测和包装:冷却的铅块经过外观检查、化学成分分析和物理性能测试等检测,确保铅块达到规定的质量标准。
合格的铅块经过包装处理,储存和运输到使用地点。
以上是铅冶炼的一般工艺流程,具体的步骤和工艺参数会根据矿石的品位和工艺要求有所差异。
另外,为了保护环境和减少对人体的危害,现代铅冶炼工艺还需要配备污染治理设备,如烟气净化系统和废水处理设备,以满足环境保护的要求。
湿法炼铅工艺流程

湿法炼铅工艺流程
湿法炼铅是一种冶金技术,它通过化学浸出和电解过程从铅精矿中提取金属铅。
以下是该工艺的基本流程:
1. 浸出过程:在这一步骤中,铅精矿与盐类或碱溶液接触,通过化学反应将铅从固态矿物中转移到溶液中。
这个过程通常在较低的温度下进行,与火法冶金相比,能耗较低。
2. 电解过程:经过浸出的溶液中含有铅离子,将这些溶液送入电解槽中,通过电解作用,铅离子在阴极上还原成金属铅沉积下来。
这样可以得到纯度较高的铅金属。
3. 后处理:电解产出的金属铅可能需要进一步的精炼和纯化,以达到工业使用的标准。
总的来说,湿法冶金技术的优点包括操作温度低、能耗相对较低、环境污染小,并且可以处理一些火法冶金难以处理的物料。
然而,湿法炼铅在工业应用上还面临着一定的挑战,比如技术成熟度、经济效益等方面的考量。
炼铅工艺技术
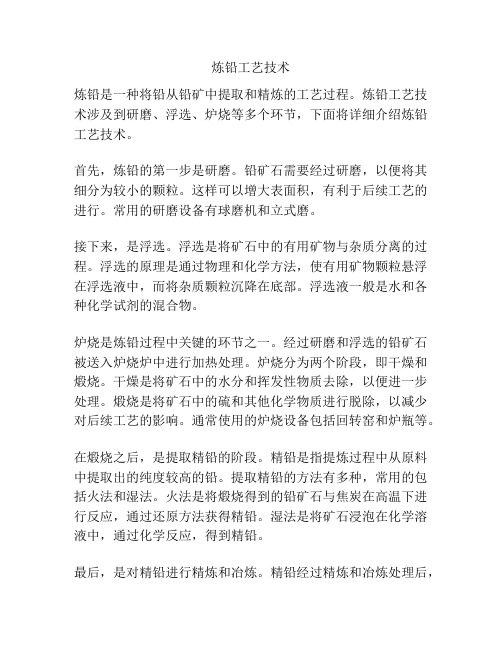
炼铅工艺技术炼铅是一种将铅从铅矿中提取和精炼的工艺过程。
炼铅工艺技术涉及到研磨、浮选、炉烧等多个环节,下面将详细介绍炼铅工艺技术。
首先,炼铅的第一步是研磨。
铅矿石需要经过研磨,以便将其细分为较小的颗粒。
这样可以增大表面积,有利于后续工艺的进行。
常用的研磨设备有球磨机和立式磨。
接下来,是浮选。
浮选是将矿石中的有用矿物与杂质分离的过程。
浮选的原理是通过物理和化学方法,使有用矿物颗粒悬浮在浮选液中,而将杂质颗粒沉降在底部。
浮选液一般是水和各种化学试剂的混合物。
炉烧是炼铅过程中关键的环节之一。
经过研磨和浮选的铅矿石被送入炉烧炉中进行加热处理。
炉烧分为两个阶段,即干燥和煅烧。
干燥是将矿石中的水分和挥发性物质去除,以便进一步处理。
煅烧是将矿石中的硫和其他化学物质进行脱除,以减少对后续工艺的影响。
通常使用的炉烧设备包括回转窑和炉瓶等。
在煅烧之后,是提取精铅的阶段。
精铅是指提炼过程中从原料中提取出的纯度较高的铅。
提取精铅的方法有多种,常用的包括火法和湿法。
火法是将煅烧得到的铅矿石与焦炭在高温下进行反应,通过还原方法获得精铅。
湿法是将矿石浸泡在化学溶液中,通过化学反应,得到精铅。
最后,是对精铅进行精炼和冶炼。
精铅经过精炼和冶炼处理后,可以得到高纯度的铅。
精炼是将精铅与其他杂质进行分离的过程,常用的方法是电解和蒸馏。
电解是将精铅溶解在电解液中,通过电流作用将杂质从铅中分离出来。
蒸馏是将精铅加热蒸馏,使不同沸点的杂质得到分离。
炼铅工艺技术的发展使得铅的提取和精炼变得更加高效和环保。
炼铅过程中严格控制各个环节的操作参数,可以有效降低能耗和减少污染物排放。
同时,炼铅技术还可以通过回收和再利用铅资源,减少矿石开采的需要,达到可持续发展的目标。
总之,炼铅工艺技术涉及到研磨、浮选、炉烧、提取精铅和精炼冶炼等多个环节。
通过优化每个环节的操作和技术手段,可以实现高效、环保的铅炼制过程,为社会经济发展做出贡献。
废铅冶炼工艺流程

废铅冶炼工艺流程废铅冶炼工艺流程废铅冶炼是利用废旧铅酸蓄电池、废旧电子产品等中含有的铅进行冶炼,从中提取出铅金属,并进行再利用的过程。
废铅冶炼的工艺流程包括以下几个步骤:废旧物料收集、破碎、焙烧、熔炼、精炼、铅锭铸造等。
首先,进行废旧物料收集。
废旧铅酸蓄电池、废旧电子产品中含有铅,这些废旧物料是废铅冶炼的原料。
在进行废旧物料收集时,需要将不同种类的废旧物料进行分类,提高废铅冶炼的转化率。
接下来,对收集到的废旧物料进行破碎处理。
废铅冶炼的原料通常是废旧物料或者废弃物,需要先对其进行破碎处理,使其颗粒大小适合后续焙烧和熔炼的要求。
然后,对破碎后的废旧物料进行焙烧。
焙烧是将废旧物料在高温条件下进行加热处理,使其产生化学反应和物理变化,进一步分解和分离杂质。
通过焙烧可以将有机物质燃烧掉,提高铅金属的含量。
随后,进行熔炼。
将经过焙烧处理的废旧物料放入熔炉中进行熔化,通过加热使废旧物料中的铅金属熔化出来,形成熔融态的铅液。
在熔炼过程中,可以通过加入适量的矿渣、辅助熔剂等控制温度、去除杂质等。
接着,对熔融态的铅液进行精炼处理。
精炼是指通过物理和化学方法分离铅液中的杂质,提高铅金属的纯度。
常见的精炼方法包括真空蒸馏法、电子束加热法等,可以去除铅液中的氧化铅、硫、锑等杂质。
最后,将精炼后的铅液铸造成铅锭。
将精炼后的铅液倒入铅锭模具中,冷却凝固后取出,即可得到铅锭。
铅锭的形状和重量可以根据实际需要进行设计,一般为长方体或圆柱形。
废铅冶炼工艺流程中的每一步都至关重要,各个环节的控制和优化可以进一步提高废铅冶炼的效率和质量。
同时,在整个冶炼过程中需要严格控制废铅产生的废气、废水和固体废弃物的排放,确保环境污染最小化。
废铅冶炼的再利用,不仅有助于资源的循环利用,还可以减少废旧物料对环境的污染。
火法炼铅工艺

火法炼铅工艺火法炼铅工艺是一种常用的金属冶炼工艺,主要用于铅矿石的冶炼。
本文将介绍火法炼铅的工艺流程、设备及对环境的影响。
一、工艺流程:火法炼铅工艺的主要步骤包括碎矿、浮选、烧结、还原、脱硫、炼出等环节。
1. 碎矿:将铅矿石经过破碎和磨矿处理,使其颗粒度适宜进一步处理。
2. 浮选:利用浮选法选别矿石中的杂质,以提高铅的品位。
经过浮选处理,矿石中的硫化铅和杂质被分离,得到精矿。
3. 烧结:将浮选得到的铅精矿与焦炭混合,添加适量的草木灰等助熔剂,经过烧结的高温煅烧处理,使精矿颗粒熔结成为烧结块。
4. 还原:将烧结块放入高温还原炉中,加入石灰和焦炭作为还原剂,将精矿中的氧化铅还原为金属铅。
在还原的过程中,金属铅被蒸发出来,通过冷凝收集。
5. 脱硫:通过向还原炉中加入适量的空气氧化剂,将还原反应中形成的二氧化硫气体进行氧化反应,以除去气体中的硫化物。
6. 炼出:将经过还原和脱硫处理的金属铅熔融炼制,去除其中的杂质和不溶性物质。
经过过滤、离心、冷却等处理,获得纯净的铅液。
二、设备:火法炼铅工艺需要使用的主要设备有碎矿机、浮选机、烧结机、还原炉等。
其中,还原炉是整个工艺中最重要的设备,需要具备高温煅烧和还原铅精矿的能力。
三、环境影响:火法炼铅工艺对环境产生的影响主要有以下几个方面:1. 废气排放:火法炼铅过程中产生大量的废气,主要包括二氧化硫气体。
这些废气中的二氧化硫是一种有害气体,对环境和人体健康都有较大的危害。
2. 废水排放:在火法炼铅过程中,会产生大量的废水,其中含有金属离子和酸性物质。
这些废水需要经过处理后才能排放,否则会对水源和周围的土壤产生污染。
3. 固体废弃物处理:火法炼铅过程中产生的固体废弃物包括矿渣、烟尘等。
这些固体废弃物需要进行妥善处理,以防止对土地和水源造成污染。
为了减少火法炼铅工艺对环境的影响,需要采取相应的环保措施,如加装废气处理设备、建立废水处理系统、合理处置固体废弃物等。
同时,还需要加强监管和管理,确保生产过程中的废物排放符合环境保护要求。
粗铅火法精炼的工艺流程

粗铅火法精炼的工艺流程以粗铅火法精炼的工艺流程为标题,写一篇文章。
粗铅火法精炼是一种常见的铅冶炼工艺,用于提取和精炼铅金属。
下面将介绍粗铅火法精炼的工艺流程。
一、铅矿破碎和磨矿将原料铅矿进行破碎和磨矿处理,将其细化成粉末。
这一步骤旨在增大铅矿的表面积,便于后续的矿石浸取和反应过程。
二、矿石浸取将磨碎后的铅矿与稀硫酸等酸性溶液进行反应浸取。
这一步骤的目的是将铅矿中的铅物质溶解出来,形成铅离子溶液。
三、铅离子还原将铅离子溶液进行还原反应,使铅离子还原为金属铅。
通常采用焙烧法或碳还原法进行。
焙烧法是指将铅离子溶液与还原剂一起加热,使还原剂与铅离子反应生成金属铅。
碳还原法是指将铅离子溶液与炭粉混合后加热,使炭粉与铅离子反应生成金属铅。
四、铅金属精炼经过还原反应后,得到的金属铅中可能还含有杂质。
为了提高铅金属的纯度,需要进行精炼。
精炼通常采用火法精炼或电解精炼。
火法精炼是指将金属铅加热至一定温度,使其中的杂质氧化并形成气体,然后通过冷却和凝固将杂质分离出去。
电解精炼是指将金属铅作为阳极,在电解槽中进行电解,使杂质被电解掉,从而提高铅金属的纯度。
五、铅金属浇铸经过精炼后,得到的铅金属可以进行浇铸成型。
浇铸可以根据需要选择不同的形状和尺寸,用于制造各种铅制品,如铅板、铅管、铅合金等。
六、废渣处理在粗铅火法精炼的过程中,会产生一定的废渣。
这些废渣中可能含有一些有害物质,需要进行安全处理。
废渣处理通常包括固化、中和、焚烧等步骤,以将有害物质固化、中和或破坏,降低对环境的影响。
总结:粗铅火法精炼是一种常见的铅冶炼工艺,通过铅矿破碎和磨矿、矿石浸取、铅离子还原、铅金属精炼、铅金属浇铸和废渣处理等步骤,可以提取和精炼铅金属,并制造各种铅制品。
在整个过程中,需要注意安全环保,对废渣进行正确处理,以减少对环境的污染。
经过粗铅火法精炼,可以获得高纯度的铅金属,为各种应用提供优质的原材料。
铅矿冶炼技术及工艺流程

铅矿冶炼技术及工艺流程
一、铅矿冶炼技术
1、铅矿冶炼技术
2、冶炼原料
铅矿冶炼原料可以由多种不同的铅矿获得,如铅滩矿、铅锌碱活矿、
红土矿和褐矿等。
3、消耗材料
冶炼过程中需要消耗化学药剂,主要有烯醇、氧化铅、酸化剂和活性
炭等,以及烟煤等燃料。
4、冶炼设备
冶炼设备主要有烧结炉、熔炼炉、精炼炉、合金炉、快冷炉、粉碎机、磨粉机等。
二、铅矿冶炼工艺流程
1、烧结
将原料加入到烧结炉中,加入一定量的化学药剂,加热至一定温度,
使矿石中的铅和其他有机物质熔融,形成新的物质,并将杂质固定在熔炉
内的冰壁上,减少熔炉内熔炉熔渣的产量。
2、熔炼
烧结后的矿石经过粉碎后,进入熔炼炉进行熔炼,加热至一定温度后,将熔矿产物进行熔融,形成铅金属液,并将杂质沉淀在底部,形成熔渣。
3、浸出精炼
将熔炼后的铅金属液浸入特殊的溶液中,使其中的金属元素溶解。
- 1、下载文档前请自行甄别文档内容的完整性,平台不提供额外的编辑、内容补充、找答案等附加服务。
- 2、"仅部分预览"的文档,不可在线预览部分如存在完整性等问题,可反馈申请退款(可完整预览的文档不适用该条件!)。
- 3、如文档侵犯您的权益,请联系客服反馈,我们会尽快为您处理(人工客服工作时间:9:00-18:30)。
铅冶炼工艺流程选择氧气底吹熔炼—鼓风炉还原法和浸没式顶吹(ISA或Ausmelt)熔炼—鼓风炉还原法在工艺上都是将冶炼的氧化和还原过程分开,在不同的反应器上完成,即在熔炼炉内主要完成氧化反应以脱除硫,同时产出一部分粗铅和高铅渣。
高铅渣均是通过铸渣机铸成块状再送入鼓风炉进行还原熔炼,产出的粗铅送往精炼车间电解,产出的炉渣流至电热前床贮存保温,前床的熔渣流入渣包或通过溜槽进入烟化炉提锌。
随着我国对节能减排和清洁生产政策的不断贯彻落实,上述工艺的弊端也显现出来,鼓风炉还原高铅渣块,液态高铅渣的潜热得不到利用,还要消耗大量的焦炭,随着焦炭价格的提升,炼铅成本居高不下。
电热前床消耗大量的电能和石墨材料,也增加了冶炼成本,同时需要占用大量的土地和投资。
为了适应环保、低炭、节能降耗的需求,新的技术不断出现,目前在河南省济源豫光金铅,金利公司、万洋集团各自采用的液态高铅渣直接还原的三种炉型代表了我国铅冶炼发展的最高水平。
一、豫光金铅底吹还原工艺:取消鼓风炉,不用冶金焦,实现液态渣直接还原,与原有富氧底吹炉氧化段一起,形成完整的液态渣直接还原工业化生产系统。
具体技术方案为:铅精矿、石灰石、石英砂等进行配料混合后,送入氧气底吹炉熔炼,产出粗铅、液态渣和含尘烟气。
液态高铅渣直接进入卧式还原炉内,底部喷枪送入天然气和氧气,上部设加料口,加煤粒和石子,采用间断进放渣作业方式。
天然气和煤粒部分氧化燃烧放热,维持还原反应所需温度,气体搅拌传质下,实现高铅渣的还原。
工艺流程如图1。
图1 豫光炼铅法的工艺流程图生产实践效果8万t/a熔池熔炼直接炼铅环保治理工程主要包括以豫光炼铅法为主的粗铅熔炼系统、大极板电解精炼系统和余热蒸汽回收利用系统等。
项目09年2月正式开工,09年8月进行设备安装,2010年元月开始空车调试,3月28日熔炼系统氧化炉点火烘炉。
目前氧化炉、还原炉、烟化炉、硫酸及制氧系统均正常生产,经几个月的生产检验,各项环保指标优于国标,技经指标达设计水平。
豫光炼铅新技术的主要特点(1)流程短:工艺省去了铸渣工序,淘汰了鼓风炉,减少了二次污染和烟尘率(国际同类技术的烟尘率一般在15%左右,而豫光炼铅法的烟尘率仅为7~8%)。
(2)自动化水平高:工艺可在氧化、还原等关键工序中设置3000多个数据控制点,实现全系统的DCS集中自动控制,用工大幅减少,系统生产更安全稳定性。
(3)低能耗:该工艺不仅利用了渣和铅的潜热,熔池熔炼时传热传质效率高,能耗大大降低。
粗铅能耗比氧气底吹-鼓风炉炼铅低25%左右,比传统工艺低约50%。
(4)低排放:采用天然气、煤粒替代焦炭,达到清洁生产的目标,SO2排放浓度和远低于国家标准,仅为氧气底吹-鼓风炉炼铅中鼓风炉排放量的10%,同时CO2排放量仅为氧气底吹-鼓风炉炼铅工艺的22%。
(5)清洁化生产:密闭性好的熔炼设备缩短了工艺流程,减少了无组织排放量,实现了铅清洁化生产。
终渣含铅指标比国际同类工艺低2%左右,资源利用率提高。
二、金利侧吹还原工艺:熔炼炉产出的高铅渣定期的由排放口放出,熔融状态下通过溜槽加入到侧吹还原炉中、侧吹还原炉设有热渣加入口和冷料加入口。
还原粒煤、熔剂经配料由冷料口加入。
还原炉两侧设煤气、工业氧喷枪为还原炉提供热源,还原炉下部侧墙设铅虹吸放出口,还原铅由虹吸口连续排出转送精炼车间,还原炉端墙下部设有排渣口,当虹吸排铅停止时,即为一个周期的终点。
排渣口放渣,为进一步回收渣中的锌,此渣经前床贮存后送烟化炉处理。
侧吹还原烟气通过余热锅炉回收余热,表面冷却器降温,布袋收尘器收尘后,是否经尾气处理,依煤粒含硫而定。
图2 金利侧吹炉工艺流程图金利液态高铅渣还原炉工业性试验装置工程的设计和建设于2008年底完工,包括一座8m2的侧吹还原炉、相应的烟气处理系统、冷料配料、上料系统及供气系统。
2009年初进入试运行阶段。
工业性试验共分三个阶段,其内容包括装置的适应性、渣型的选择、工况、供气、还原粒煤与还原周期调整等试验。
其间对设施进行了必要的维护和修改:炉子下部面积扩大为13m2,试验工作于2009年8月底完成,达到了与底吹熔炼炉放渣制度相适应的稳定运行。
各项技术条件和指标较稳定。
2009年9月初即转入示范性生产。
停止了高铅渣的铸块和鼓风炉的生产。
还原炉第一炉期共进行了5个月,2010年3月20号更换炉衬,2010年3月底第二炉期开始运行.金利新技术的工艺技术特点(1)侧吹还原炉能耗低,产出烟气量和二氧化硫排放量远低于鼓风炉,同等规模的烟气量为鼓风炉的30%,二氧化硫排放量约为10%。
流程短捷,扬尘点少,易于密闭通风除尘,有效的防治了铅尘的弥散,经测定,操作岗位铅含量小于m3,卫生通风除尘后的排放铅尘浓度6mg/m3。
(2)经金利公司生产10个月的冶炼数据核算,侧吹还原炉焦炉煤气和无烟粒煤消耗折合标煤为197kgce/t-pb,比鼓风炉纯铅能耗380kg,折合标煤369 kgce/t-pb的指标大幅降低。
(3)侧吹还原炉渣含铅小于2%,而鼓风炉渣含铅3—4%,侧吹还原炉铅回收率为%,鼓风炉铅回收率%。
(4)过程简单,工序少,作业稳定,易操作,可实现DCS控制和管理,提高了劳动生产率。
(5)经金利公司统计计算,粗铅单位或成本为550元左右,比鼓风炉单位成本840元明显降低。
(6)侧吹还原炉、烟化炉与熔炼炉放置在一个厂房内,省略了鼓风炉上料、热渣铸造系统,建筑面积显著减少。
三、万洋三连炉工艺:万洋公司与豫北金铅公司、中联公司于2009年合作开发“三连炉”炼铅新工艺,采用氧化炉—还原炉—烟化炉三炉相连,热渣直流,三台熔池熔炼炉由两道连接溜槽串接在一起组成一整体;两连接溜槽分别连接在前一台熔池熔炼炉的出渣口和后一台熔池熔炼炉的熔融渣加料口之间,充分利用液态高铅渣和还原炉渣的潜热,紧凑的布置使得流程短占地很少,工人劳动强度小,环保效果好,实现了铅冶炼生产的低碳模式。
“三连炉”炼铅工艺流程图见图3。
图3 万洋“三连炉”炼铅工艺流程图如图3所示,“三连炉”中氧化炉可以是氧气底吹炉,也可以是奥斯麦特(Ausmelt)炉、艾萨(ISA)炉、氧气侧吹炉等,还原炉为氧气侧吹还原炉,烟化炉增加渗铅装置改进。
生产系统具体为硫化物精矿、石灰石、石英砂、含铅烟尘物料进入氧化炉熔炼炉内充分混合、迅速熔化和氧化,生成一次粗铅、高铅渣和烟气。
粗铅送到下道工序进行电解精炼。
氧化炉产生的液态高铅渣通过溜槽直接流入氧气侧吹还原炉,高铅渣与煤、熔剂,经鼓入的富氧空气强烈搅拌而激烈反应,产出的粗铅经虹吸道流出,含有微量SO2气体经锅炉回收余热后进入脱硫塔处理排空。
还原炉产出的炉渣通过直接流入烟化炉提锌。
与氧气底吹熔炼—鼓风炉还原工艺相比,三炉通过溜槽直接相连,液态高铅渣直接流入侧吹还原炉内,充分利用了高铅渣的潜热,取消了铸渣机,避免了高铅渣块产生的烟尘飞扬现象;还原炉热渣直接流入烟化炉内,潜热也得到了充分利用,进入烟化炉内不需要提温期,可以直接喷入粉煤还原提锌,降低了煤耗,缩短了烟化提锌时间,提高了生产效率;同时取消了电热前床和热渣吊运过程,既节省了设备投资,也降低了生产电耗以及避免了渣包运输带来的环境问题。
万洋公司氧气侧吹炉在新乡中联公司多次试验的基础上,于2011年3月10日一次性开炉成功,运行半年来,生产稳定连续,各项技术经济指标达到了预期目标值。
前期氧化段底吹炉为Φ×,110~120min放一次渣,产出液态高铅渣量为28~35t/炉,渣含铅43~50%,此次设计的氧气侧吹炉为,高铅渣在一个还原周期内完全可以降至1%以下。
为了考虑后面烟化炉的生产,使熔池内的锌尽可能的保留在渣中,生产中控制渣含铅不大于2%。
万洋、豫北“三连炉”工艺特点与氧气底吹熔炼—鼓风炉还原法和浸没式顶吹(ISA或Ausmelt)熔炼—鼓风炉还原法相比,“三连炉”工艺具有以下的优势:(1)取消了铸渣机,避免了高铅渣冷却铸块过程中水汽迷漫、碎沫飞扬的现象,生产环境进一步改善,也省下了铸渣机的设备投资。
(2)高铅渣在熔融液态下直接还原,充分利用了高铅渣熔体的潜热,节省了大量的燃料,使吨铅生产能耗下降。
(3)侧吹还原炉的高温炉渣直接流入烟化炉,不需要电热前床保温,烟化炉省略提温阶段,充分利用了熔渣的热能,可直接进入还原提锌,节省了粉煤,也提高了生产效率,同时氧化锌品质更好。
(4)高铅渣还原只采用单一的煤作为燃料和还原剂,起到加热和还原的作用。
与鼓风炉相比煤比焦炭价格低廉,与国内其他的还原炉相比不需要天然气或煤气作为燃料,使不具有天然气或煤气的厂家也可采用此种工艺,对建厂条件的适应性更好,推广前景更广。
(5)侧吹还原炉床能率很高,时间上可以与底吹炉、烟化炉相匹配,取消了电热前床,节省大量的电能及石墨电极,使能耗降低。
(6)侧吹还原炉熔池熔炼反应激烈,还原程度彻底,为了保证锌的回收,渣含铅控制不大于2%。
(7)烟化炉采用渗铅改进,既增加了铅的回收率,也提高了氧化锌的品位。
(8)三炉相连,热渣直流,占地很少,节省投资。
(9)生产操作简单,指标易于控制,工人劳动强度小,生产操作环境好。
四、几种工艺技术参数的比较:表1 几种工艺的技术经济指标对比项目豫光底吹-液态渣还原工艺金利底吹-液态渣还原工艺万洋、豫北“三连炉”工艺工艺流程短短短工作环境扬尘点较少,环境好扬尘点少,环境更好扬尘点少,环境更好生产效率高:1)氧化段产出部分粗铅;2)采用富氧熔炼,反应速度较快;3)氧化段生成的液态高铅渣直接流入还原炉,流程紧凑,效率高。
高:1)氧化段产出部分粗铅;2)采用富氧熔炼,反应速度较快;3)氧化段生成的液态高铅渣直接流入还原炉,流程紧凑,效率高。
高:1)氧化段产出部分粗铅;2)采用富氧熔炼,反应速度较快;3)氧化段生成的液态高铅渣直接流入还原炉,流程紧凑,效率高。
原料适应性原料适应性广原料适应性广原料适应性广粗铅品位98-99%98-99%98-99%烟气SO2浓度及收率SO2浓度:8~10%SO2收率:98%SO2浓度:8~10%SO2收率:98%SO2浓度:8~10%SO2收率:98%铅总收率~98%97~98%97~98%脱硫率98%98%98%烟尘率氧化段:12~14%,还原段:12~13%氧化段:12~14%,还原段:~10%氧化段:12~14%,还原段:~10%熔剂率氧化段:3%,还原段:2~3%氧化段:3%,还原段:2~3%氧化段:3%,还原段:2~3%氧气单耗360m3/t360 m3/t320~330 m3/t电耗100kWh/t80~96 kwh/t68~80 kwh/tjn煤耗150kg/t69 kg/t131 kg/t天然气耗75Nm3/t t——混合矿含铅45~65%45~65%43~47%混合矿含硫14~18%16~18%16~18%还原炉床能力————50~80 t/(m2·日)终渣含铅<3%≤2%≤2%综合能耗(注)276 kgce/t230 kgce/t230 kgce/t投资额大较大小注:以上技术经济指标均来自相关厂的报道。