切边冲孔复合模的设计
冲孔复合模具设计5226

冲孔复合模具设计5226冲孔复合模具设计摘要:垫圈冲孔复合模设计,它的结构的主要特征是有一个既是落料凸模又是冲孔凹模的凹凸模。
这一复合模为倒装式复合模,凹凸模装在下模,落料凹模和冲孔凸模装在上模。
采用刚性推件装置把卡在凹模中的冲件推下,刚性冲件由打杆、推板、连接推杆组成。
冲孔废料直接由冲孔凸模从凸凹模内孔推下,无顶件装置,结构简单,操作方便,主要完成冲孔、落料两道工序。
由打杆顶出制件,橡胶垫驱动的卸料板卸除条料。
由弹性挡料销和导料销定位、导料。
模架为后侧导柱圆形模架,压入式模柄。
由于垫圈的生产为大批量生产,所以在使用模具的前后都应注重模具的保养和修复,防止生产出误差过大的不合格产品。
本次设计使用CATIA绘制零件实体并完成装配,进而生成装配工程图和相关的零件图。
关键词:冲孔复合模具 CATIA 设计1 引言1.1CATIA简介本次设计主要运用了CATIA进行作图设计,下面是关于CATIA的简单介绍。
CATIA具有完备的设计能力和很大的专业覆盖面,它是一套集成的软件应用包,内容覆盖了产品设计的各个方面,包括:计算机辅助设计(CAD),计算机辅助工程分析(CAE)和计算机辅助制造(CAM)。
它既具有各种类型的协同产品设计的必要功能,也可以进行无缝集成完成支持“端到端”的企业流程解决方案,其特有的DMU电子样机模块功能及混合建模技术更使企业竞争力和生产力的提高。
使用CATIA V5版本,可为数字化企业建立一个针对产品整个开发过程的工作环境。
在这个环境中,可以对产品的开发过程进行仿真,实现工人之间的电子通信和产品整个开发过程,包括概念设计、详细设计、工程设计、成品定义和制造乃至成品在整个生命周期中的使用和维护。
总的来说,CATIA具有以下几个方面的特点和应用。
(1)先进的混合建模技术和后期修改性。
设计对象的混合建模:在CATIA V5的设计环境中,无论是实体还是曲面,都做到了真正的互操作。
变量和参数化混合建模:在设计时,用户不必考虑参数化设计目标,CATIA V5提供了变量驱动和后参数化能力。
拉深、翻边、切边和冲底孔复合模具设计探究

拉深、翻边、切边和冲底孔复合模具设计探究摘要随着生产加工的不断进步和发展,对于模具设计的要求也越来越高。
为了提高生产效率,促进企业的长远发展,企业开始研究多功能复合模具的设计。
多功能的复合模具可以满足各种生产需要,但是要想真正发挥复合模具的作用,必须要重视拉深、翻边、切边和冲底孔复合模具的设计。
文中会介绍模具设计中各种参量的确定,分析复合模具设计中要注意的问题,最后重点说明复合模具的设计。
关键词拉深;翻边;切边以及冲底孔;复合模具;设计1 复合模具设计中各种参数的确定1.1 确定模具的拉深次数复合模具的拉深次数直接决定了模具的拉深工作,确定模具的拉深次数要根据不同模具的具体情况来确定。
了解模具的具体情况之后,结合模具的高度、直径、材料的厚度以及毛坯的直径等来计算模具拉深的次数,这样的方式才能很好保证拉深次数的合理性和科学性。
1.2 确定模具的冲压方向模具冲压方向的确定要根据模具的实际工作状态来确定,模具可以根据不同的生产需要灵活地变换冲压方向,冲压方向的改变对于模具本身的形态以及质量没有很大的影响,但是对于模具的翻边工作却有很大的联系,冲压方向细微的变化,都有给翻边带来影响。
如果冲底孔存在瑕疵会造成模具的破损,当翻边方向与冲压方向相反时,可以很好地提高翻边工作的效率和质量。
1.3 确定模具的毛坯直径计算毛坯直径是为了修补模具在工作中造成模具的磨损,准确的毛坯直径能够为下阶段的工作提供依据。
模具在拉深的过程中会受到模具间隙、摩擦力以及模具材料本身的性能等多方面因素的影响,最终出现模具破损的情况。
2 复合模具设计中注意的几点问题2.1 重视模具制件的设计模具制件在整个模具设计中占据十分重要的地位,制件的设计是否合理,很大程度上能够说明整个复合模具的成功与否。
复合模具的制件的形状相对复杂,在实际的设计中要考虑模具各方面的因素,特别是拉深过程中制件变形区的切向压应力与模具的直径大小,两者之间如果存在太大的差异会影响到模具的起皱程度。
端盖冲孔切边复合模设计说明书

端盖冲孔切边复合模设计第一章绪论1.1冲压模具的现状与发展趋势改革开放以来,随着国民经济的高速发展,市场对模具的需求量不断增长。
近年来,模具工业一直以15%左右的增长速度快速发展,模具工业企业的所有制成分也发生了巨大变化,除了国有专业模具厂外,集体、合资、独资和私营也得到了快速发展。
浙江宁波和黄岩地区的“模具之乡”;广东一些大集团公司和迅速崛起的乡镇企业,科龙、美的、康佳等集团纷纷建立了自己的模具制造中心;中外合资和外商独资的模具企业现已有几千家。
随着与国际接轨的脚步不断加快,市场竞争的日益加剧,人们已经越来越认识到产品质量、成本和新产品的开发能力的重要性。
而模具制造是整个链条中最基础的要素之一,模具制造技术现已成为衡量一个国家制造业水平高低的重要标志,并在很大程度上决定企业的生存空间。
近年许多模具企业加大了用于技术进步的投资力度,将技术进步视为企业发展的重要动力。
一些国内模具企业已普及了二维CAD,并陆续开始使用UG、Pro/Engineer、I-DEAS、Euclid-IS等国际通用软件,个别厂家还引进了Moldflow、C-Flow、DYNAFORM、Optris 和MAGMASOFT等CAE软件,并成功应用于冲压模的设计中。
以汽车覆盖件模具为代表的大型冲压模具的制造技术已取得很大进步,东风汽车公司模具厂、一汽模具中心等模具厂家已能生产部分轿车覆盖件模具。
此外,许多研究机构和大专院校开展模具技术的研究和开发。
经过多年的努力,在模具CAD/CAE/CAM技术方面取得了显著进步;在提高模具质量和缩短模具设计制造周期等方面做出了贡献。
例如,吉林大学汽车覆盖件成型技术所独立研制的汽车覆盖件冲压成型分析KMAS软件,华中理工大学模具技术国家重点实验室开发的注塑模、汽车覆盖件模具和级进模CAD/CAE/CAM软件,上海交通大学模具CAD国家工程研究中心开发的冷冲模和精冲研究中心开发的冷冲模和精冲模CAD软件等在国内模具行业拥有不少的用户。
切边冲孔复合模的设计

第一章零件的工艺分析一、零件材料的分析08F钢强度、硬度很低,而塑性、韧性极高,具有良好的冷变形性和焊接性,正火后切削加工性尚可,退火后导磁率较高,剩磁较少,但淬透性、淬硬性极低。
二、零件的结构分析该零件结构简单,尺寸没有公差要求,尺寸均为自由公差,外形对称。
三、零件的工艺性分析该零件是钢料,该零件形状的基本特征是一般的有凹圆的圆筒形件,为圆筒形件底部有一个Φ10孔,内部圆周直径为Φ28,尺寸均为自由公差,因一般情况下,拉深件的尺寸精度应在IT13级以下,不宜高于IT11级。
所以将内部直径改为Φ28+00.3。
高度10+00.2为IT11-IT12级精度。
主要成形方法是冲裁、拉深、切边冲孔和弯曲。
零件的dt/d、h/d都不太大,其拉深工艺性较好。
该零件为大批量生产,零件外形简单对称。
材料为08F钢,采用冲压加工经济性较好。
零件如图:t=1mm其余R=0.4第二章确定冲压工艺方案冲压工艺方案的确定是制定冲压工艺过程的主要内容,需要综合考虑各方面的因素,有的还需要进行必要的工艺计算,因此,实际确定时通常先提出几种可能的方案。
再在此基础上进行分析、比较和择优。
从零件的结构和形状可知,所需基本工序为落料、拉深、冲孔、弯曲四种。
但工序模具生产效率低难以满足大批量生产的要求,为了提高生产效率主要采用复合冲裁或级进冲裁两种方式。
若采用级进模虽然生产效率很高,但模具的结构比较复杂,对制造精度要求较高,一般生产周期长,成本高维护也比较困难。
采用复合冲裁时,冲出的零件精度和平直度较好,生产效率也较高,模具结构较级进模简单生产成本也比级进模的低。
第一节零件毛坯的尺寸计算(1)弯曲毛坯尺寸的确定对于r<0.5t的弯曲件毛坯长度的计算公式Lz=5+4+5+0.6t=5+5+4+0.6×1=14.6(2)拉深次数的确定及尺寸计算因板料厚度t为1mm故按厚度中线尺寸计算,如图所示。
2.1.1计算坯料尺寸D=(d22+4d2H-1.72rd2-0.56r2)½=(29*29+4*29*10.5-1.72*2.5*29-0.56*2.5*2.5)½=43.94mmL1=Lz+2*2.5=19.6mmL=L1+D=63.54mm图2-12.1.2 确定拉深次数根据坯料的相对厚度t/D=1/43.94=2.28%拉伸系数m=d/D=29/43.94=0.66大于极限拉深系数[m],所以一次拉深成形。
冲孔切边模具设计

冲孔切边模具设计绪 论模具是提高产品质量和市场竞争力的重要手段,已经越来越受到各工业部门的 重视。
可以减少材料的消耗提高生产的效率。
我国已经成为世界上净出产模具最 多的国家。
但是大型多位级进模,精密冲压模具.大型汽车覆盖件模具等虽然已经 可以生产,但总体技术还不高,与国外还有很大差距。
模具是机械、汽车、电子、通讯、家电等工业产品的基础工艺装备,属于高新 技术产品。
作为基础工业,模具的质量、精度、寿命对其他工业的发展起着十分。
近十年来,随着国民经济的快速发展, 重要的作用,在国际上称为“工业之母”作为工业品基础的模具行业,也得到了蓬勃发展,已成为国民经济建设中的重要 产业。
据统计,我国(未包括台湾、香港、澳门)现有模具厂已超过1700家,从 业人员达60多万人。
模具分为冲压模具、热锻模具、塑料模具、铸造模具、橡胶模具和玻璃模具 等。
其中,冷冲压模具历史悠久、用途广、技术成熟,在各种模具中所占比重最 多。
汽车、摩托车、家电行业是模具最大的市场,占整个市场的60%以上。
例如, 一种车型的轿车共需模具 4000 套,价值达 2 亿元`到 3 亿元;单台电冰箱需要模 具生产的零件约 150 个,共需模具约 350 套,价值约 400 万元;单台彩电大约有 150个零件需用模具生产,共需模具约140套,价值达700万元。
其中所需模具大 部分为冷冲压模具。
冲压是在室温下。
利用安装在压力机上的模具对材料施加压 力,使其产生分离或塑性变形,从而获得所需零件的一种压力加工方法。
也叫冷 冲压.在冲压过程中,将材料加工成零件的一种特殊工艺装配,称为冲压模具。
冲 模是在实现冲压加工中必不可少的工艺装配,与冲压件是“一模一样”的关系, 若没有符合要求的冲模,就不能生产出合格的冲压件:没有先进的模具,先进的 冲压成型工艺就无法实现。
在冲压零件的生产中,合理的成形工艺、先进的模具、高效的冲压设备是比不可少的三要素。
与切削加工相比,冷冲压靠模具和设备完成加工过程,所以具有生产效率高、加 工成本低、材料利用率高 、产品一致性好、操作简单、便于实现机械化与自动化 等一系列优点。
五速轮 锻模和切边冲孔复合模设计
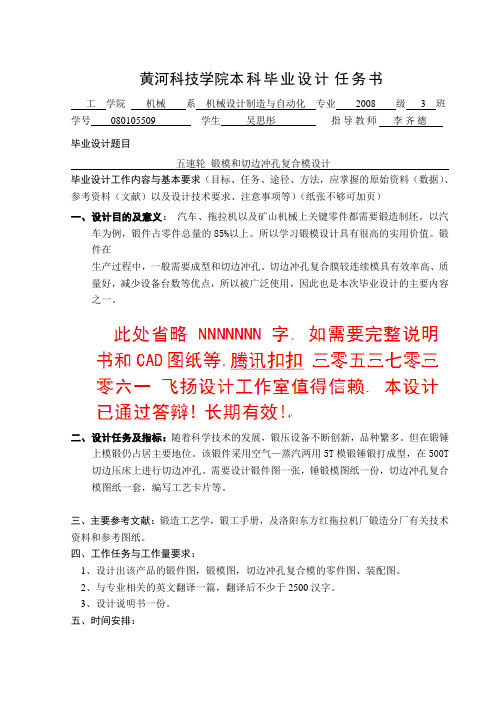
黄河科技学院本科毕业设计任务书工学院机械系机械设计制造与自动化专业2008 级 3 班学号080105509 学生吴思彤指导教师李齐德毕业设计题目五速轮锻模和切边冲孔复合模设计毕业设计工作内容与基本要求(目标、任务、途径、方法,应掌握的原始资料(数据)、参考资料(文献)以及设计技术要求、注意事项等)(纸张不够可加页)一、设计目的及意义:汽车、拖拉机以及矿山机械上关键零件都需要锻造制坯。
以汽车为例,锻件占零件总量的85%以上。
所以学习锻模设计具有很高的实用价值。
锻件在生产过程中,一般需要成型和切边冲孔。
切边冲孔复合膜较连续模具有效率高、质量好,减少设备台数等优点,所以被广泛使用,因此也是本次毕业设计的主要内容之一。
二、设计任务及指标:随着科学技术的发展,锻压设备不断创新,品种繁多。
但在锻锤上模锻仍占居主要地位。
该锻件采用空气—蒸汽两用5T模锻锤锻打成型,在500T 切边压床上进行切边冲孔。
需要设计锻件图一张,锤锻模图纸一份,切边冲孔复合模图纸一套,编写工艺卡片等。
三、主要参考文献:锻造工艺学,锻工手册,及洛阳东方红拖拉机厂锻造分厂有关技术资料和参考图纸。
四、工作任务与工作量要求:1、设计出该产品的锻件图,锻模图,切边冲孔复合模的零件图、装配图。
2、与专业相关的英文翻译一篇,翻译后不少于2500汉字。
3、设计说明书一份。
五、时间安排:1周——2周收集设计资料并画出锻件图和工艺卡。
3周——4周完成英文资料翻译。
5周——6周进行锻模设计。
7周——10周绘制切边冲孔复合模的零件图和装配图11周修改整理,准备答辩。
毕业设计(论文)时间:2012年 2 月13 日至2012 年 5 月15 日计划答辩时间:2012 年 5 月19日专业(教研室)审批意见:审批人签名:。
惰轮锻模和切边冲孔复合膜设计

惰轮锻模和切边冲孔复合模设计摘要模具是机械制造业中技术先进、影响深远的重要工艺装备,具有生产效率高、材料利用率高、制件质量优良、工艺适应性好等特点,被广泛应用于汽车、机械、航天、航空、轻工、电子、电器、仪表等行业。
随着我国汽车工业的迅猛发展,汽车性能不断提高,汽车零部件中对高精度、形状复杂锻件的需求量越来越大,锻造新工艺、省材、节能工艺等技术的开发对于新型汽车零件的生产尤为重要。
我国冲压模具无论在数量上,还是在质量、技术和能力等方面都已有了很大发展,但与国民经济需求和世界先进水平相比,差距仍很大,一些大型、精密、复杂、长寿命的高档模具每年仍大量进口,特别是中高档轿车的覆盖件模具,目前仍主要依靠进口。
本文主要是以惰轮锻件的生产,加工工艺等,设计制造了,一些模具,包括,堕轮锻件的镦粗,终锻,以及切边冲孔等后期加工模具。
首先介绍了,模具的一些简单情况,模具的分类,发展现状和趋势等,其次介绍了,零件的工艺性,毛坯的制定,镦粗,终锻模膛的设计,包括飞边槽的设计,再次介绍了,切边冲孔复合模的设计。
关键词:模具,终锻模膛,飞边槽,钳口,镦粗,切边,冲孔An inert wheel forging the design specificationAuthor:Zhang Zong MingTutor:Li Qi DeAbstractMold is mechanical manufacturing technology advanced, profoundly important technical equipment,High production efficiency, material with high efficiency and good quality, technology parts good adaptability etc. Characteristics.Widely used in motor vehicles, machinery, aerospace, aviation, light industry, electronics, electric appliances, instruments and other industries.With the rapid development of China's automobile industry,The car's performance to improve, Auto parts of high precision, complicated shape of forging an increasing demand for,Forging new craft, material, energy saving technology province technology development for new type of car parts production is especially important.Our country stamping die in the number no matter, or in quality, technology and ability are already has great development,But with the national economy needs and the advanced world level, compared to a gap still, Some large, sophisticated, complex, the long life of high-grade die every year in the importation of large still, Especially in high-grade car covering mould, at present still mainly rely on imports.The paper is an inert round of forging production, Processing techniques, Design and manufacturing, some mould, including, fall round of forgings upsetting, eventually forging, and trimming punching production processing mould.Firstly introduces, die some simple case, the classification of mould, development situation and trends,Secondly introduces, the technology of parts, blank the formulation, the upsetting, and the design of the chamber forging die,Including flash slots of design, Introduced again, trimming punching the design of the composite film.Key words:Mould,Finally bore, Flash tank,Clamp mouth,Upsetting,Trimming, punching目录1.绪论 (1)1.1模具工业简介 (1)1.2模具分类 (1)1.3热锻的目的有三方面: (2)1.4我国锻造模具发展现状和趋势 (2)2.课题的分析拟定 (3)2.1零件的工艺性分析 (3)2.1.1制件的技术要求 (4)2.1.2确定工艺方案 (4)3.制定锻件图 (5)3.1确定分型面 (5)3.2确定加工余量和公差 (6)3.3估算锻件质量m (7)3.4计算加工余量公差 (7)3.5技术条件 (7)3.6模锻斜度 (8)4.冲孔连皮设计 (8)5.设计终锻模膛 (9)5.1绘制齿轮热锻件图 (9)5.2确定飞边槽的尺寸 (10)5.2.1飞边槽形式 (10)5.2.2飞边槽的作用: (11)5.2.3飞边槽的尺寸确定方法: (11)5.3钳口的确定 (12)6.制坯模膛的设计 (14)6.1确定终锻模设备吨位 (15)6.2设计制坯模锻 (15)6.3制坯工步的确定 (16)6.4确定坯料长度 (17)7.锻模结构设计 (17)7.1模膛布置 (17)7.2镦粗台的设计 (17)7.3模块尺寸及要求 (18)7.4模块材料 (19)7.5燕尾槽尺寸 (19)8.模锻工艺流程 (19)9.切边冲孔复合模的设计 (19)9.1切边冲孔方式及模具类型 (19)9.2切边模 (20)9.3切边冲头的设计和固定方法 (21)9.4切边模其他部分设计 (23)9.5模具的工作过程 (23)10.锻模模具材料及其热处理的确定 (24)10.1锻锤模及切边模模具材料的确定 (24)10.2模具材料热处理的硬度要求 (25)11.热锻模的失效形式 (25)结论 (26)致谢 (27)参考文献: (28)1.绪论1.1模具工业简介模具工业是国民经济的重要基础工业之一。
带法兰圆筒拉深冲孔复合模的设计方案

零件图工件名称:带法兰圆筒件;生产批量:10万件/年;冲压材料:08F,厚度t=2mm。
带法兰圆筒拉深冲孔复合模的设计摘要模具工业是国民经济的重要基础工业之一。
模具是工业生产中的基础工艺装备,是一种高附加值的高精密集型的产品,也是高新技术产业化的重要领域,其技术水平的高低已经成为衡量一个国家制造业水平的重要标志。
而复合模生产效率较高,适合大规模的工业生产。
本次设计对典型的复合模中包含的四种冲压工序落料、拉深、冲孔与切边变形特性进行了分析,并从模具结构的角度对各工序变形影响因素进行了讨论。
运用大学期间所学的专业课程知识、理论和毕业实习中学到的实践知识,正确地解决复合模设计中工艺分析、方案论证等模具结构设计等问题,充分利用与本复合模设计有关的各种资料,做到科学合理地熟练应用。
同时提高自己绘图能力,通过对带法兰圆筒拉深冲孔复合模的设计,巩固对模具理论的掌握,增强动手的能力,培养严谨科学态度,并且也达到理论与实际相结合的目的。
关键词:复合模;落料;拉深;冲孔;切边DESIGNOFDRAWING-PUNCHING COMPOUND DIEFORTHEFLANGE CYLINDERABSTRACTMouldindustryis oneoftheimportantbasicindustriesofnationaleconomy.Moldis the basictechnologyofindustrialproductionequipment,akindofhighvalueoflabor-intensive products,also theimportantfieldshigh-techindustrialization,whose technicallevelhas becometomeasureacountry'simportantsymbol ofthelevelsofmanufacturing.The productionefficiencyofcompositemoldishigherthanothers,therefore,itissuitablefor large-scaleindustrialproduction.The typical composite modulus containing four punching process: blanking, deep drawing,punchingand trimmingdeformation characteristicsareanalyzedin thisdesign,and thefactorsofvariousprocessesdeformationwerediscussedfrom theangleofthemould inguniversitymajorknowledgeandknowledgefromtheory andgraduation practicecorrectlysolvetheproblemofprocessanalysis,plandemonistincompoundmolddesign.Theutilizationofmaterial related thecompositemodulusdesignmakereasonably scientificskilledapplication.Throughthedesignof drawingpunchingcompounddieforthe flangedcylinder,wecanimprovecartography ability,consolidatethemasterofmouldtheory, strengthen practice ability, cultivate the rigorous scientific attitude, and also attain the objectiveof integratingtheorywiththepractice.Keywords:compounddie。
- 1、下载文档前请自行甄别文档内容的完整性,平台不提供额外的编辑、内容补充、找答案等附加服务。
- 2、"仅部分预览"的文档,不可在线预览部分如存在完整性等问题,可反馈申请退款(可完整预览的文档不适用该条件!)。
- 3、如文档侵犯您的权益,请联系客服反馈,我们会尽快为您处理(人工客服工作时间:9:00-18:30)。
第一章零件的工艺分析一、零件材料的分析08F钢强度、硬度很低,而塑性、韧性极高,具有良好的冷变形性和焊接性,正火后切削加工性尚可,退火后导磁率较高,剩磁较少,但淬透性、淬硬性极低。
二、零件的结构分析该零件结构简单,尺寸没有公差要求,尺寸均为自由公差,外形对称。
三、零件的工艺性分析该零件是钢料,该零件形状的基本特征是一般的有凹圆的圆筒形件,为圆筒形件底部有一个Φ10孔,内部圆周直径为Φ28,尺寸均为自由公差,因一般情况下,拉深件的尺寸精度应在IT13级以下,不宜高于IT11级。
所以将内部直径改为Φ28+00.3。
高度10+00.2为IT11-IT12级精度。
主要成形方法是冲裁、拉深、切边冲孔和弯曲。
零件的dt/d、h/d都不太大,其拉深工艺性较好。
该零件为大批量生产,零件外形简单对称。
材料为08F钢,采用冲压加工经济性较好。
零件如图:t=1mm其余R=0.4图1-1 零件图第二章确定冲压工艺方案冲压工艺方案的确定是制定冲压工艺过程的主要内容,需要综合考虑各方面的因素,有的还需要进行必要的工艺计算,因此,实际确定时通常先提出几种可能的方案。
再在此基础上进行分析、比较和择优。
从零件的结构和形状可知,所需基本工序为落料、拉深、冲孔、弯曲四种。
但工序模具生产效率低难以满足大批量生产的要求,为了提高生产效率主要采用复合冲裁或级进冲裁两种方式。
若采用级进模虽然生产效率很高,但模具的结构比较复杂,对制造精度要求较高,一般生产周期长,成本高维护也比较困难。
采用复合冲裁时,冲出的零件精度和平直度较好,生产效率也较高,模具结构较级进模简单生产成本也比级进模的低。
第一节零件毛坯的尺寸计算(1)弯曲毛坯尺寸的确定对于r<0.5t的弯曲件毛坯长度的计算公式Lz=5+4+5+0.6t=5+5+4+0.6×1=14.6(2)拉深次数的确定及尺寸计算因板料厚度t为1mm故按厚度中线尺寸计算,如图所示。
2.1.1计算坯料尺寸D=(d22+4d2H-1.72rd2-0.56r2)½=(29*29+4*29*10.5-1.72*2.5*29-0.56*2.5*2.5)½=43.94mmL1=Lz+2*2.5=19.6mmL=L1+D=63.54mm图2-12.1.2 确定拉深次数根据坯料的相对厚度t/D=1/43.94=2.28%拉伸系数m=d/D=29/43.94=0.66大于极限拉深系数[m],所以一次拉深成形。
第二节拟定冲压工艺方案根据以上的分析计算,该零件的冲压加工需以下基本工序:落料、拉深、冲Φ10mm的孔、切边、弯曲。
根据以上基本工序,拟定一下冲压工艺方案。
方案一:落料与拉深复合→其余按基本工序。
方案二:落料与拉深复合→冲孔与切边复合→弯曲。
方案一工序组合程度较低,生产率较低。
不过各工序模具结构简单,制造费用低,对中小批量生产是合适的。
方案二制作出的零件尺寸精度高,需要两个复合模具,可获得高的生产率,而且操作方便。
模具的结构复杂,制作周期长,生产成本高。
因此,只在大批量生产中才较适宜。
此次生产就是大批量生产故决定采用方案二的冲压工艺方案。
冲压工艺方案为:落料与拉深复合→冲孔与切边复合→弯曲第三章模具总体结构方案在冲压工艺方案确定以后,根据零件的形状特点、生产批量、模具制造条件、操作与安全要求、以及利用现有设备的可能,确定每道工序所用模具的总体结构方案。
模具总体结构方案的确定包括以下内容:(1)模具类型模具类型主要是指单工序模、复合模、和级进模三种,模具类型应根据生产批量、冲件形状与尺寸等因素确定。
及根据冲压工艺方案确定采用复合模。
(2)操作与定位方式根据生产批量确定采用手工操作、半自动操作或自动化操作;根据坯料或工序件的形状、冲件精度要求、材料厚度、模具类型、操作方式等确定采用坯料的送进导向与送料定距方式或工序件的定位方式。
虽然此零件的生产批量较大但合理的安排生产可用手工送料方式能够达到批量要求,且能降低模具成本,因此采用手工送料。
为了便于操作和保证零件的精度且零件不太小所以采用挡料销、导料销作为定位方式。
(3)卸料与出件方式根据材料的厚度、尺寸与质量要求、冲压工艺性质以及模具类型等,确定卸料选用弹性卸料装置,出件选用刚性顶件装置。
(4)模架类型及精度根据冲压件尺寸与精度,材料厚度、模具类型、送料与操作等因素确定,由于零件厚度薄,冲裁间隙较小且零件为对称的回转体拉深件,则冲裁时一般不会承受大的偏心载荷又是复合模,因此选用中间导柱圆形模架。
考虑到零件的精度要求不高但冲裁间隙较小,所以采用错误!未找到引用源。
级模架精度。
第四章主要工艺参数的计算第一节确定排样与裁板方案板料规格拟选用1×900×1800mm( 08F钢板)因为坯料长L=63.54mm、宽b=43.94mm,不算太小考虑到操作方便采用条料单排,取搭边值a=1.8mm a1=1.5mm,则进距:S=b+a1=43.94+1.5=45.44mm条料宽度:B=L+2a=63.54+2×1.8=67.14mm4.1.1 采用纵裁每板条料数:n1=900÷67.14≈13条余27.18mm每条零件数:n2=(1800-1.5)/45.44≈39件余26.34mm每板零件数:n1×n2=13×39=507件材料利用率:η=(507×1725.5456)/900×1800=54%4.1.2 采用横裁每板条料数:n1=1800÷67.14≈26条余54.36mm每条零件数:n2=(900-1.5)/45.44≈19件余42.10mm每板零件数:n1×n2=26×19=494件材料利用率:η=(494×1725.5456)/900×1800=52%由此可件,纵裁有较高的材料利用率,且该零件没有纤维方向行的。
故决定采用纵裁法。
图4-1 排样图现对切边冲孔复合模进行设计与加工第二节计算该工序的冲压力及选择设备毛坯如图所示:1、冲压力计算切边力:F1=Ltσb=135.7×1×304×1.3=53628.64N卸料力:Fx=KxF1=0.05×53628.64=2681.432N推件力:F T=K T F1=0.055×53628.64=2949.58N冲孔力:F3= LtσB=10π×2×395=24806NF1——冲裁力(N)L——冲件周边长度(mm)t ——材料厚度(mm)σb——材料抗拉强度(MPa)Kx——卸料力系数,数值可查表2、压力机标称压力的确定标称压力是指滑块在工作行程内允许承受的最大负荷,而滑块必须在到达下止点前某一特定距离内允许承受标称压力。
标称压力是压力机的主要技术参数。
对于冲裁工序,压力机的标称压力应大于或等于冲裁时总冲压力的1.1~1.3倍,即Fg≥(1.1~1.3)×FΣ冲压工艺总力:FΣ= F1+ Fx + F T + F3=84065.652N标称压力Fg≥1.3×FΣ= 110KN因为本工序是切边冲孔复合,因此压力机标称压力时应考虑压力机的许用压力曲线,本工序可选用开式双柱可倾式压力机J23-16压力机。
J23-16压力机的主要技术规格为:公称压力:160 KN滑块行程:55 mm滑块行程次数:120次/min最大封闭高度:220 mm封闭高度调节量:45 mm垫块尺寸:40 mm模柄孔尺寸:直径40 mm 深度60 mm第四节 弹性卸料装置的选用弹性卸料装置由卸料板、卸料螺钉和弹性元件(弹簧和橡胶)组成。
本设计选用弹性元件是橡胶。
弹性卸料板的平面外形尺寸等于或稍大于凹模板的尺寸,厚度取凹模厚度的0.6~0.8倍。
卸料板与凸模的双边间隙根据冲件料厚确定,一般取0.1~0.3 mm (料厚时取大值,料薄时取小值)。
为了便于可靠卸料,在模具开启状态下卸料板工作表面应高出凸模刃口端面0.3~0.5 mm 。
卸料螺钉一般采用标准的阶梯形螺钉,取数量按卸料板形状与大小确定。
卸料螺钉的直径根据模具大小可选用8~12 mm ,各卸料螺钉的长度应一致,以保证装配后卸料板水平和均匀卸料。
考虑到模具的结构,选用6个圆筒形的聚氨酯橡胶,则每个橡胶所承受的顶件力为Fy= F x /n=2681.432/6≈447N确定橡胶的横截面积A:取h y =10%h 0,查表的p=1.1MPa ,则 A=Fy/p=447N/1.1N/ mm 2 ≈406.4 mm 2确定橡胶的截面尺寸:选用直径为10 mm 的卸料螺钉,取橡胶上螺钉过孔直径d=12 mm ,则橡胶外径D 根据π(D 2 -d 2)/4=A 求得 D= (d 2 +4A/π)½ =(122 +4×44)½≈18mm为了保证足够卸料力,可取D=20mm 。
卸料板为圆形的常选用3-4个,但由于卸料力比较大经计算选用6个。
卸料螺钉的直径根据模具选用10 mm 。
第五节 出件装置出件装置的作用是从把零件从模具内卸出来。
把装在上模内的出件装置称为推件装置,装在下模内的称为顶件装置。
因本设计的模具装在下模内所以称之为顶件装置。
此模具选用的是刚性出件装置利用推件板和推杆把零件从模内推出。
在顶件装置中,推件板与凹模空口配合并作相对运动,对它的要求是模具处于闭合状态时,其背后应有一定的空间,以备修模和调整的需要.第五章模具工作部分尺寸的计算第一节切边冲孔凸、凹模计算查表的Z min=0.100,Z max=0.140。
因为为自由尺寸可按IT14级精度处理查得Δ=0.36 mm Z max - Z min =0.040 mm 系数x=0.55.1.1切边δp=0.020δd =0.0305.1.2冲孔(Ф10 mm)x=0.5 δp =0.02 δd =0.02校核间隙:因为δp+δd=0.02+0.02=0.04 mm < Z min-Z max=0.114 mm 所以符合δp+δd≤Z min-Z maxd p=(d min+xΔ) -0δp = (10+0.5×0.84)-00.02=10.42 -00.02d d=(d p+Z min) +0δd =(10.42+0.246) +00.02=10.67 +00.02d d、dp——落料凸、凹模刃口尺寸x——磨损系数,差表冲件精度为IT14时,x=0.5d max——落料件的最小极限尺寸Δ——冲件的制造公差(mm)δp、δd——凸、凹模制造公差(mm)Z min——最小合理间隙(mm)第三节凹模轮廓尺寸的确定凹模轮廓尺寸包括凹模板的平面尺寸及厚度尺寸。