塑性加工中的数值模拟
第五章刚塑性有限元法基本理论与模拟方法

塑性成形过程 计算机数值模拟
第五章 刚塑性有限元法基本理论与模拟方法
❖ 从数学的角度来讲,有限元法是解微分方程的一种数值方法。它的 基本思想是:在整个求解区域内要解某一微分方程很困难(即求出 原函数)时,先用适当的单元将求解区域进行离散化,在单元内假 定一个满足微分方程的简单函数作为解,求出单元内各点的解;然 后,再考虑各单元间的相互影响,最后求出整个区域的场量。
两个或一个事先得到满足,而将其余的一个或两个,通过拉格朗日
乘子引入泛函中,组成新的泛函,真实解使泛函取驻值,这就是不
完全广义变分原理。
❖ 在选择速度场时应变速率与速度的关系(1)式和速度边界条(3)式容 易满足,而体积不可压缩条件(2)式难于满足。因此,可以把体积 不可压缩条件用拉格朗日乘子入引入到泛函中,得到新泛函:
够的工程精度的前提下,可提高计算效率。
塑性成形过程 计算机数值模拟
第五章 刚塑性有限元法基本理论与模拟方法
❖ 由于刚塑性有限元法采用率方程表示,材料变形后的构形可通 过在离散空间对速度的积分而获得,从而避开了应变与位移之 间的几何非线性问题。
❖ 由于忽略了弹性变形,刚塑性有限元法仅适合于塑性变形区的 分析,不能直接分析弹性区的变形和应力状态,也无法处理卸 载和计算残余应力与变形。
在满足: (1) 速度-应变速率关系
ij
1 2
ui, j
u j,i
(2) 体积不可压缩条件 (3) 速度边界条件
V kk 0
ui ui
(在 Su 上)
的一切动可容场
ui*j
,
塑性加工过程有限元法模拟的现状和困难
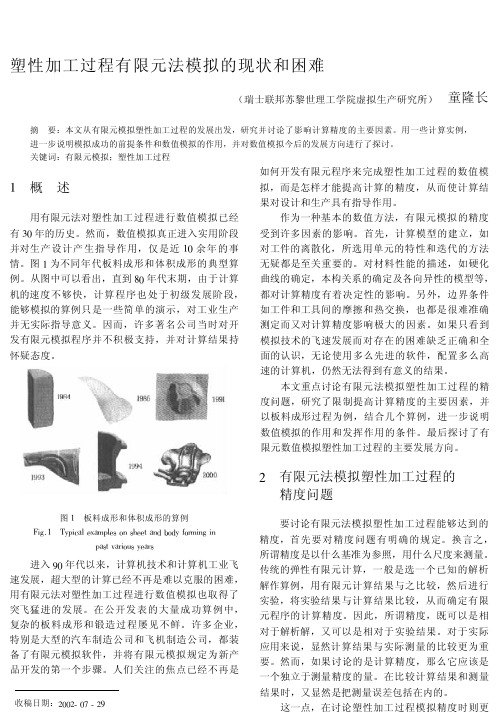
图& *+,-&
主要的材料参数
")硬化曲线; ()屈服轨迹; ))屈服轨迹强化
.%/ 0"1"2%#%13 45 2"#%1+"6
7)图 &" 为材料的硬化曲线。由于用简单的拉 伸试验一般只能获得 89:’9: 的应变,而塑性 成形 过程中,工件中的应变量经常在 799: 以上。用压 缩或扭转试验虽然能得到较大的变形量,但由于试 件中的变形不是均匀的,很难将试验数据合理地转 化为硬化曲线。由图 &" 可看出,用不同的数学模型 处理试验数据,尽管曲线与试验数据吻合很好,当 应变增大后,不同的曲线类型之间的差异不断增大。 硬化曲线不仅影响变形力的计算,对材料的失效判 据也有至关重要的影响。 8)图 &( 为材料屈服轨迹的描述。在计算材料 本构关系时,基本的原理是应变增量垂直于屈服轨 迹,即正交法则。不同的屈服轨迹将导致不同的应 力—应变增量关系,因此直接影响计算结果。在板 料成形中,一般引入各向异性参数 ! 。按照 ;+66 的 模型,屈服轨迹与 ! 和指数系数 " 有关。实验证 明,参数 ! 在变形过程中并不是常数,也就是说屈 服轨迹的形状在变形过程中会变化。至今尚未见到 任何研究结果可以描述 ! 随应变的变化。用 ! 为常 数的假设进行计算,对许多合金材料是不符合实际 的。 ’)图 &) 为屈服轨迹的强化模型。众 所 周 知, 材料变形时流动应力随应变而增加,屈服轨迹也将 改变。采用 <+3%3 流动判据,屈服表面为一圆柱面。 随着变形增加,圆柱面的半径将增大。按各向同性 强化理论,圆柱面沿所有方向按比例扩大,其轴线
塑性加工过程有限元法模拟的现状和困难
金属塑性成形过程韧性断裂的准则及其数值模拟
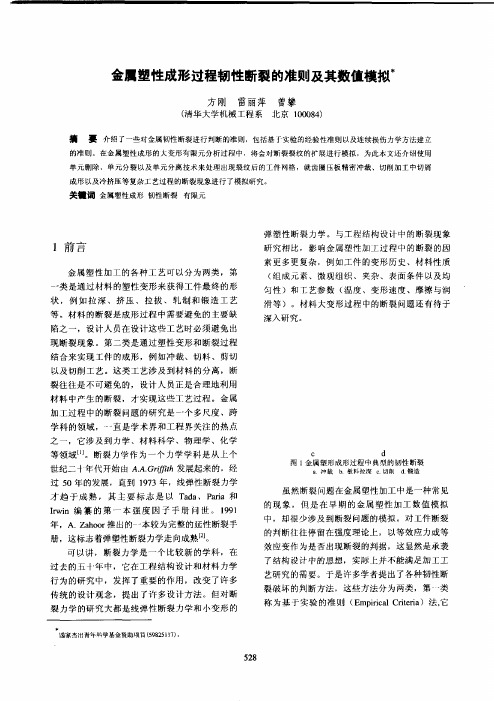
R e r y在1 9 es 9 年提出了三向应力作 i 和Tc l 6 c a ]
用下材料的韧性断裂准则为:
的应用。最后介绍作者对几个典型工艺模拟的结
果。
1 .
2韧性断裂准则
金属在加工过程中发生的断裂大多是韧性断 裂,很少发生脆性断裂。一般认为,金属中的韧
Kc nv 1 8 a a 在 9 年首先提出的另一种分析方 ho 5
法。这种研究方法主要是从细观 ( e s l m s ce oa) 的角度进行研究,对空洞的萌生和扩展角度进
行预测,建立空洞萌生准则。因为韧性断裂的
调整,局部调整还包括单元删除 ( e tn D l o)、 e i
50 3
截
国家杰出青年科学基金资助项目( 851) 5 21 . 9 7
58 2
主要是通过标准的常规实验来获取材料的实验数 据,然后用于对材料成形过程中的韧性断裂的判 断上,它还分二种,即应力、应变和应变能准 则,这类准则的代表是 C cr t a a 准则。 ok fLt m o- h 从所分析的尺度和方法上讲,它属于宏观断裂力 学的范畴。这种方法的缺陷是简单的力学实验条
申
虽然断裂问题在金属塑性加工中是一种常见 的现象,但是在早期的金属塑性加工数值模拟 中,却很少涉及到断裂问题的模拟。对工件断裂 的判断往往停留在强度理论上,以等效应力或等 效应变作为是否出现断裂的判据,这显然是承袭 了结构设计中的思想,实际上并不能满足加工工 艺研究的需要。于是许多学者提出了各种韧性断 裂破坏的判断方法,这些方法分为两类,第 类 称为基于实验的准则 (m i a Cir ) 它 E pi l ea 法, r c r i t
世纪二十年代开始由A .r h .G咖t发展起来的, A 经
刚塑性有限元数值模拟中产生误差的原因及改进方法(精)

刚塑性有限元数值模拟中产生误差的原因及改进方法1 引言塑性加工过程的有限元数值模拟,可以获得金属变形的详细规律,如网格变形、速度场、应力和应变场的分布规律,以及载荷-行程曲线。
通过对模拟结果的可视化分析,可以在现有的模具设计上预测金属的流动规律,包括缺陷的产生(如角部充不满、折叠、回流和断裂等)。
利用得到的力边界条件对模具进行结构分析,从而改进模具设计,提高模具设计的合理性和模具的使用寿命,减少模具重新试制的次数。
在制造技术飞速发展、市场竞争日益加剧的今天,塑性加工过程的计算机模拟可在模具虚拟设计、制造阶段就能充分检验模具设计的合理性,减少新产品模具的开发研制时间,对用户需求做出快速响应,提高市场竞争能力。
由此可见,金属成型过程的有限元模拟已是模具计算机集成制造系统中必不可少的模具设计检验环节。
金属成形工艺分体积成形和板料成形两大类,相应地,用于分析其流动规律的有限元法也分为两类,即:刚塑性、刚粘塑性有限元和弹塑性有限元。
体积成形中的挤压成形和锻造成形在实际生产中应用很广,中外学者在这方面进行了很多研究,其中二维模拟技术已相当成熟,三维模拟是目前的世界研究热点。
刚塑性、刚粘塑性有限元模拟能否对模具设计的合理性做出可靠校验,取决于模拟的精度和效率。
作者结合从事二维塑性有限元模拟的经验和当前的三维塑性有限元模拟系统开发的实践,对刚塑性、刚粘塑性有限元模拟过程中产生误差的原因进行了全面的详细分析,并提出相应的解决方法,同时以具体实例说明。
2 刚塑性、刚粘塑性有限元模拟中产生误差的原因及改进方法2.1 刚塑性有限元法求解的数学基础刚塑性有限元法是假设材料具有刚塑性的特点,把实际的加工过程定义为边值问题,从刚塑性材料的变分原理或上界定理出发,接有限元模式把能耗率表示为节点速度的非线性函数,利用数学上的最优化原理,在给定变形体某些表面的力边界条件和速度边界条件的情况下,求满足平衡方程、本构方程和体积不变条件的速度场和应力场。
金属塑性加工过程有限元数值模拟及软件应用(梅瑞斌编著)PPT模板
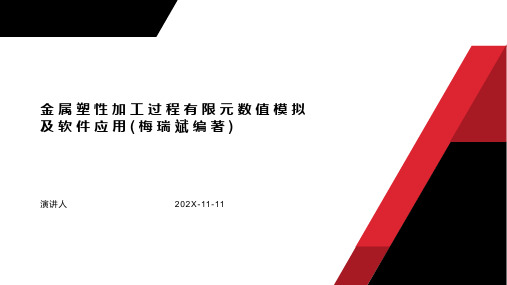
演讲人
2 0 2 X - 11 - 11
目 录
0 1 前言
0 2 第1章绪论
0 3 第2章塑性力学及有限元理论基础
04
第3章不同软件及方法求解圆柱体等温压缩过程
0 5 第4章温度场ANSYS有限元数值模拟求解实例
0 6 第5章塑性加工过程变形ANSYS求解实例
2.1应力与应变
2.1.1点的应 力状态
2.1.2应力分 析
2.1.3应变分 析
第2章塑性力学及 有限元理论基础
2.2平衡微分方程与屈服准 则
2.2.1平衡 微分方程
1
2.2.2屈服 准则
2
第2章塑性力学及有限元理论基础
2.3变形抗力与条件简化
2.3.1变形 抗力模型
1
2.3.2平面 问题
2
2.3.3轴对 称问题
06 参考文献
第4章温度场ANSYS有限元数值模拟求解实例
4.1板坯空冷过程温度场求解实例
4.1.1问题提 出
4.1.2ANSYS 软件求解
4.1.3温度振 荡问题与分析
第4章温度场ANSYS有 限元数值模拟求解实例
4.2试样多阶段热处理过程温度场 求解实例
4.2.1问题 提出
1
4.2.2ANSY S软件求解
有第
限 元 理 论 基 础
章 塑 性 力 学 及
2
01
2.1应力与 应变
04
2.4弹塑性 有限元变刚
度法
02
2.2平衡微 分方程与屈
服准则
05
2.5刚塑性 有限元法
03
2.3变形抗 力与条件简
塑性成形过程的数值模拟
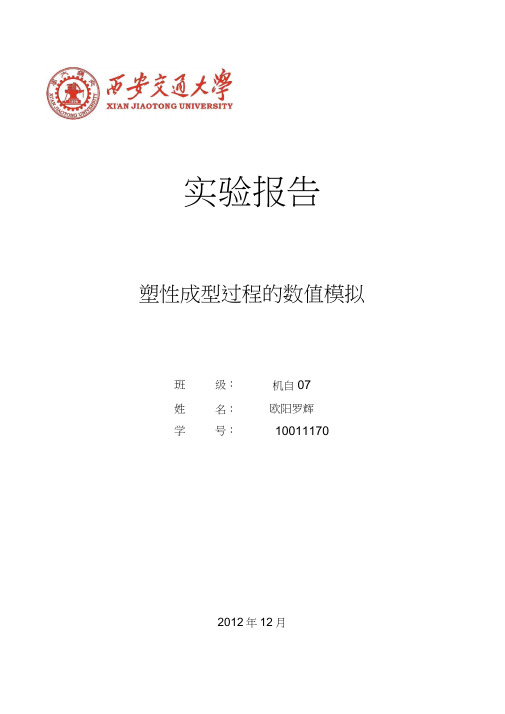
实验报告塑性成型过程的数值模拟班级:机自07姓名:欧阳罗辉学号:100111702012年12月一、实验目的:通过本实验的教学,使学生基本掌握有限元技术在板料塑性成形领域的应用情况,拓宽学生的知识面,开阔视野,使学生对塑性成形过程的数值模拟技术有深刻的理解,预测板料弯曲成形的性能。
二、教学基本要求:学会使用Dynaform数值模拟软件进行板料弯曲成形过程的仿真模拟,对模拟结果具有一定的分析和处理能力。
三、实验内容提要:掌握前处理的关键参数设置,如零件定义、网格划分、模型检查、工具定义、坯料定义、工具定位和移动、工具动画、运行分析。
了解后处理模块对模拟结果的分析,如读入d3plot 文件、动画显示变形和生成动画文件、成形极限图分析、坯料厚度变化分析等。
四、软件操作过程:1.导入压边圈、板料、下模板、上模板图形文件点击File —Import,出现Import File 对话框,找到“ L型弯曲零件图”选中binder.igs,点击Import,如此,依次导入四个模型文件,最后点击“确定”确认四个模型导入后,结果如图Fite- Parts- Pre§)rocE3B DFE 単E5eiLp SCF Toob Qplxxt UUM IH Yew Analyss FtosIProceH Het□fea 呦越超曲.i 制倒翅制则④朋叫面h 1回哦间谢佃创初斜划’•2. 重命名文件点击PartLEdit ,出现Edit Part 对话框,这里便要依次更改文件名。
cOOIvOOO 1 ”,在上面的 Name 对话框中输入 binder ,然后点击 Modify ,以此类推输入 banker 、die 、punch 。
Edit Part3. 对各图形文件划分有限元网格1. Binder 零件网格划分rshrtik rNEfmairHfldtnrFilCakw首先选用红色文件名“ rjgmeID ColorDeletePROCESSING OEPENDENT RECORDS 13PHOCES3r4G IM3EPEf<DENT RECORDS F Lfifrs P Suriacrs-匸Tfl/DYWAFDRnpimchigslSMPaHTED 引□点击 □图标,出现 Part Turn 。
材料加工中的数值模拟技术

材料加工中的数值模拟技术近年来,随着科技的不断进步和发展,材料加工中的数值模拟技术正在得到越来越广泛的应用。
数值模拟技术可以模拟材料加工过程中的各种因素,从而对生产过程进行优化,提高产品的质量和生产效率。
本文将从数值模拟技术在材料加工中的应用、数值模拟技术的分类以及数值模拟技术的发展趋势等方面对其进行探讨。
一、数值模拟技术在材料加工中的应用材料加工是指通过加工方法将原材料加工成符合要求的零部件、工件、产品等。
常见的材料加工方法包括钣金加工、铸造加工、焊接加工、铣削加工等。
而数值模拟技术是指利用计算机模拟材料加工过程中的各种因素,从而对生产过程进行优化、改进和控制的一种技术。
数值模拟技术可以模拟材料的受力情况、材料变形情况、温度变化情况等因素,从而能够准确地预测材料加工过程中的各种物理效应以及产品的性能。
这不仅能够提高产品的质量和生产效率,还能够降低生产成本,并且减少生产事故的发生。
二、数值模拟技术的分类数值模拟技术在材料加工中的应用是十分广泛的,而基于不同的模拟对象,数值模拟技术可以分为多种类型。
主要包括流体力学模拟、热传导模拟、结构力学模拟、材料塑性变形模拟等。
流体力学模拟是指对材料加工过程中的液体流动情况进行模拟。
如液态金属的流动、塑料挤出等。
热传导模拟是指对材料加工过程中的温度变化情况进行模拟。
如钢件的热处理、焊接熔池的温度分布等。
结构力学模拟是指对材料加工过程中的结构力学情况进行模拟。
如机械零件的承载能力、机器的振动稳定性等。
材料塑性变形模拟则是针对材料加工过程中的塑性工艺进行模拟。
如钣金成形过程、有限元法等。
三、数值模拟技术的发展趋势随着科学技术的发展,数值模拟技术也在不断地演变和创新。
在材料加工中,数值模拟技术已经成为了一个越来越重要的工具。
未来,数值模拟技术的发展趋势主要集中在以下几个方面。
1. 多物理场模拟的综合性应用在材料加工过程中,常常需要考虑到多个因素共同影响下的加工情况,如温度、应力、变形等。
数值模拟在冲压过程中的应用

数值模拟在冲压过程中的应用对材料加工进行成型是在重工业领域中的重要手段之一。
随着社会日新月异的发展和人们对生产生活要求的全面提高,塑性加工也不断发展。
在塑性加工过程中充分利用计算机的快速、精确计算等优点已得到广泛的应用。
利用计算机的数值模拟制造已成为了新研究方法,可以对产品性能、质量进行分析,降低消耗和成本,提高产品开发效率如汽车外形、冲压模具、坯料,揭示各种成型规律并且进行优化工艺过程预报组织性能。
塑性成型的数值模拟方法主要有三种:上限法、边界元法和有限元法。
上限法主要用于分析较为简单的准稳态变形问题,边界元法主要用于模具设计分析和温度计算,而有限元法(FEM)主要用于大变形的体积成形和板料成型,变形过程呈现非稳态,材料的几何形状、边界、材料的性质等都会发生很大的变化。
有限元法将具有无限个自由度的连续体看成只具有有限个自由度的单元集合体。
单元之间只在指定节点处相互铰接,并在节点处引入等效相互作用以代替单元之间的实际相互作用。
对每个单元选择一个函数来近似描述其物理量,并依据一定的原理建立各物理量之间的关系。
最后将各个单元建立起来的关系式加以集成,就可得到一个与有限个离散点相关的总体方程,由此求得各个离散点上的未知量,得到整个问题的解。
它对问题的性质、物体的形状和材料的性质几乎没有特殊的要求,只要能构成与有限个离散点相关的总体方程就可以按照有限元的方法求解。
有限元法能考虑多种外界因素对变形的影响,如温度、摩擦、工具形状、材料性质不均匀等。
除边界条件和材料的热力学模型外,有限元的求解精度从理论上看一般只取决于有限元网格的疏密。
利用有限元进行数值分析可以获得成形过程多方面的信息,如成形力、应力分布、应变分布、变形速率、温度分布和金属的流动方向等[1]。
金属板料冲压成形是金属材料塑性成形的一种重要方法。
有限元法在板料成形领域的应用始于20世纪70年代,自此,在这一领域的研究逐渐发展起来[2]。
在机械制造业中有着广泛的应用,例如:汽车的车身、底盘、油箱、散热器片、锅炉的汽包、电动机等都是采用了板料冲压工艺加工成形。
- 1、下载文档前请自行甄别文档内容的完整性,平台不提供额外的编辑、内容补充、找答案等附加服务。
- 2、"仅部分预览"的文档,不可在线预览部分如存在完整性等问题,可反馈申请退款(可完整预览的文档不适用该条件!)。
- 3、如文档侵犯您的权益,请联系客服反馈,我们会尽快为您处理(人工客服工作时间:9:00-18:30)。
铝合金挤压过程的数值模拟
铝合金可以被视为一种粘性不可压缩非牛顿流体。
目前流体运动的描述方法可以分为拉格朗日描述(Lagrangian description)方法、欧拉描述(Eulerian description)方法和任意拉格朗日-欧拉描述(Arbitrary Lagrangian-Eulerian description)方法三种。
数值模拟计算方法中,根据离散方法的不同,主要可以分为有限差分方法(FDM)、有限元法(FEM)、有限体积法(FVM)等。
几十年来,有限元和有限体积法等数值模拟方法已被广泛应用于铝合金挤压过程的数值分析中。
众多的研究者利用数值方法对铝合金挤压过程进行了模拟研究,其中有限元法应用最为广泛,而有限体积法因其解决大变形问题的优势,也逐渐被引入到塑性成形领域。
1、6063铝合金半固态反挤压数值模拟
利用有限元模拟技术,研究材料在半固态成形过程中的流场、温度场、应力应变场等分布规律,预测6063铝合金在成形过程中的充型行为、可能产生的缺陷和最佳工艺参数等信息,可为实际生产提供理论依据。
6063铝合金具有极佳的加工性能,是典型的挤压合金,被广泛应用于建筑型材等。
获得6063铝合金不同温度和应变速率下的应力-应变曲线后,采用有限元软件DEFORM-3D对合金半固态反挤压成形过程进行数值模拟,对主要工艺参数进行优化。
半固态反挤压过程的有限元力学模型见图1,变形体为圆柱体。
实验中所用的坯料、凸模和凹模均为轴对称,取其1/4进行模拟分析。
采用刚-粘塑性有限元法,采用图1有限元力学模型对半固态6063合金在不同工艺条件下的反挤压过程进行有限元模拟。
图1 反挤压力学模型及特征点位置
数值模拟结果分析:
(1)坯料变形过程及坯料成形中的速度场分布
挤压模拟时取工件内部不同位置的5个点作为特征点跟踪,特征点位置见图
1。
挤压过程中特征点位置坯料流动速度随时间的变化见图2。
在挤压变形过程中,材料受三向压应力作用,发生塑性变形的金属主要集中在坯料端部的外侧,且靠近上模型腔入口处的金属变形量为最大。
变形初期P 1、P 2处于大变形区内,坯料流动速度变化剧烈。
速度的大小和方向变化都比较明显,随凸模压下量的增大,变形后期特征点P 1的材料作刚性平移,此时材料的流动方向由沿径向向外流动逐渐变为沿凸凹模间隙向上流动。
靠近坯料中心部位的材料P 3,挤压初期获得较大流速,在之后挤压过程中整体向下均匀流动,其速度大小不变。
当变形达到一定程度,凸模端面下的材料(如特征点P 4和P 5)相对于P 3位置径向外流的趋势更大,且随凸模压下量的继续增大,金属由径向外流逐渐变为沿凸凹模间隙向上流动。
(2)凸模速度的影响
图3为变形温度620℃,摩擦因数为0.25,凸模压下量为12.7mm 时,凸模速度对工件内不同特征点处等效应力和等效应变的影响。
结果表明,反挤压大变形区和应力较大的区域都集中在工作带附近,可以看出在5个特征点处,凸模速度对等效应变的影响不如对等效应力的影响显著,随凸模速度的升高,
等效应力变化图2 特征点位置坯料流动速度随时间的变化
明显而等效应变基本不变。
图3 凸模速度对特征点等效应变和等效应力的影响
(3)变形温度的影响
图4为凸模速度取12.7mm/s,摩擦因数为0.25,凸模压下量12.7mm时,变形温度对工件内不同特征点处等效应变和等效应力的影响。
随着变形温度的升高,处于大变形区内的材料等效应变明显增大,而材料各点的等效应力均有所减小。
图4 变形温度对特征点等效应变和等效应力的影响
(4)摩擦因数的影响
在材料的成形过程中,摩擦条件是不容忽视的。
变形温度为620℃,凸模速度为12.7mm/s,凸模压下量为12.7mm时,摩擦因数对工件内不同特征点处等效应变和等效应力的影响见图5。
可见,随着摩擦因子的改变,工件内部等效应力与等效应变稍有变化,但整体上摩擦对等效应力和应变的影响不显著。
这是由于材料在半固态下,液相对固相有一定的润滑作用,使得摩擦条件对变形的影响不显著。
该课题研究结果表明,随着变形程度增大,处于大变形区内的材料流动速度与方向变化明显,小变形区也逐渐参与变形,变形的不均匀性更加明显。
随着凸模速度的增大,坯料流动速度加快,整个变形的不均匀性加剧,对成形不利。
随着变形温度的升高,处于大变形区内的材料等效应变明显增大,而材料各点的等效应力均有所减小。
摩擦条件对材料变形的影响不显著。
2、铝合金挤压成形过程及模具负载的数值模拟
本文结合MSC.SuperForge 和MSC.Marc 计算平台,分别对铝合金挤压成形过程和挤压模具的应力负载过程进行了数值模拟研究。
对30mm ×30mm 的方管型材进行分析,探讨数值模拟进行模具设计及修模调整的方法。
计算的CAD 模型和有限元模型如图6所示。
图5 摩擦因素对不同特征点等效应变和等效应力的影响
图6 型材截面及模具模型
结果分析:
(1)金属变形
图7所示为挤压过程中金属的变形过程。
从图7(b )可见,在挤压刚进入分流孔的位置,金属的应力负载较大,在进入分流孔后,如图7(c )和图7(d ),在进入模腔最前方的金属塑性停止,该部分金属的应力负载值开始减少,而分流孔入口处的金属应力负载仍然最大。
当变形金属进入焊合腔与模具焊合室底面相互接触后,如图7(e )和图7(f ),在最前端的金属受到焊合室的阻碍,开始产生横向的流动,并开始焊合,如图7(g )所示。
在金属焊合的过程中,焊合室内金属的应变分布先上升,再下降。
金属在模具工作带部位,金属的应力值最大。
而挤出型材产品后,应力负载下降,如图7(h )所示。
而图8所示是对应8个不同时刻变形金属的等效塑性应变速率的结果。
可以发现,在分流孔的入口部位以及金属在焊合室完全焊合前,金属的等效塑性应变速率急剧增大。
同样的情况发生在金属进入工作带后挤出模孔的位置。
可见,等效应变速率的变化与金属成形的应力变化分布有较大的关联。
当金属变形产生突变时,应变速率急剧增大,对应位置金属的应力也增加。
图7 坯料变形过程的等效应力分布(MPa )
图8 坯料变形过程的等效塑性应变分布(s -1)
(2)模具应力
图9所示是挤压时间t=3.9s 时模具的应力负载分布。
从结果分析可以得到:(a )在模具入料方向的分流孔圆角位置,模具的应力负载达到最大值1440MPa 。
可见圆角部位设计不合理,导致了应力集中,大大的影响了模具寿命。
(b )在上模不同截面位置模具的应力大小数值不同,但模具应力整体的变化趋势大致相同。
(c )在模桥位置的应力负载值比模芯位置大。
(d )本套模具的入料面截面的应力负载比其他界面的应力负载大。
(e )模具除分流孔圆角外,其他各部位应力负载分布较均匀,且在安全范围之内。
再对挤压不同时刻对应的模具应力负载进行分析,发现:(a )当坯料到达下模焊合室时,模具应力负载有一定幅度的下降;(b )金属在焊合室时,模具的应力负载开始明显上升;在金属开始挤出模孔时,应力负载上升幅度增大。
3、铝合金挤压非正交网格有限体积法数值模拟
利用非正交网格,将铝合金挤压金属流动区域离散成不规则六面体有限体积控制单元,充分考虑网格非正交性对铝合金挤压金属流动控制方程离散过程的影响,研究了非正交网格下铝合金挤压有限体积法模拟关键技术。
建立了基于非正交网格的铝合金挤压过程有限体积法数值模拟模型,并编制了相应的分析程序。
对典型铝合金挤压过程进行了模拟,并与有限元分析软件Deform-3D 模拟结果进行了分析比较。
分析结果验证了本文铝合金挤压有限体积模拟模型的正确性。
参考文献:
[1] 王姣姣,路贵民,尚淑珍,等.6063铝合金半固态反挤压数值模拟[J].特种铸造及有
色合金,2010,30(8):714-717.
[2] 李淼林.铝合金挤压成形过程及模具负载的数值模拟[J].金属铸锻焊技术,2010,(7):
110-113.
[3] 娄淑梅,张建中,袁建军.铝合金挤压非正交网格有限体积法数值模拟[J].金属铸锻
焊接技术,2010,(4):74-76.
图9 t=3.9s 的模具等效应力分布(MPa )。