自乳化水性环氧树脂的研究
环氧树脂的水性化技术与分析研究进展

环氧树脂的水性化技术与研究进展摘要:本文主要对环氧树脂的水性化技术的原理及方法进行了系统的分类及论述;对不同水性化技术方法的特点进行了综述评论。
总结了环氧树脂水性化技术的研究进展及其发展趋势。
关键词:环氧树脂;水性化Abstract:This article focusing on the principles and methods of the technology of waterborne epoxy resin makes a systematic classification and discussion and has summaries and comments of technology and methods of different characteristics of waterborne .It summarizes the research progress of technology of waterborne epoxy resin and its development trend .Keywords: epoxy resins; waterborne0 前言近年来,环境保护日益受到人们的重视, 许多国家相继颁布了控制挥发性有机化合物( VOC)的法规,执行标准愈加严格。
涂料向高固体分和水性化方向发展已成为涂料界的共识, 其中水性涂料由于其高度环保而倍受亲睐。
环氧树脂具有优良的工艺性能、力学性能和物理性能,广泛地应用于胶粘剂、涂料、机械、电子等领域[1]。
常用的环氧树脂大多数为黏稠的液体或固体, 不溶于水, 溶于有机溶剂。
而大多数有机溶剂易挥发、易燃易爆、有毒,随着对环境保护的要求日益迫切和严格,使环氧树脂的应用受到了一定限制。
以水为分散介质的环氧树脂体系,与传统的环氧树脂体系相比,避免了因使用有机溶剂而造成的环境污染和资源浪费,并可在室温和潮湿环境下固化,操作性大大改善。
水性环氧树脂
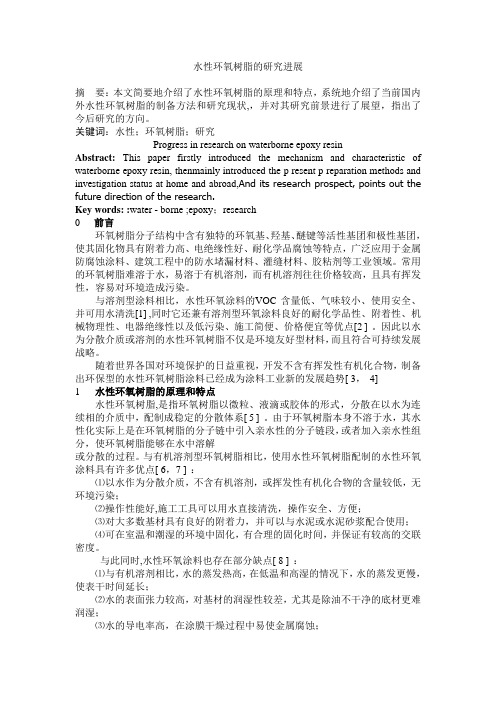
水性环氧树脂的研究进展摘要:本文简要地介绍了水性环氧树脂的原理和特点,系统地介绍了当前国内外水性环氧树脂的制备方法和研究现状,,并对其研究前景进行了展望,指出了今后研究的方向。
关键词:水性;环氧树脂;研究Progress in research on waterborne epoxy resinAbstract: This paper firstly introduced the mechanism and characteristic of waterborne epoxy resin, thenmainly introduced the p resent p reparation methods and investigation status at home and abroad,And its research prospect, points out the future direction of the research.Key words: :water - borne ;epoxy;research0 前言环氧树脂分子结构中含有独特的环氧基、羟基、醚键等活性基团和极性基团,使其固化物具有附着力高、电绝缘性好、耐化学品腐蚀等特点,广泛应用于金属防腐蚀涂料、建筑工程中的防水堵漏材料、灌缝材料、胶粘剂等工业领域。
常用的环氧树脂难溶于水,易溶于有机溶剂,而有机溶剂往往价格较高,且具有挥发性,容易对环境造成污染。
与溶剂型涂料相比,水性环氧涂料的VOC 含量低、气味较小、使用安全、并可用水清洗[1] ,同时它还兼有溶剂型环氧涂料良好的耐化学品性、附着性、机械物理性、电器绝缘性以及低污染、施工简便、价格便宜等优点[2 ] 。
因此以水为分散介质或溶剂的水性环氧树脂不仅是环境友好型材料,而且符合可持续发展战略。
随着世界各国对环境保护的日益重视,开发不含有挥发性有机化合物,制备出环保型的水性环氧树脂涂料已经成为涂料工业新的发展趋势[ 3,4]1水性环氧树脂的原理和特点水性环氧树脂,是指环氧树脂以微粒、液滴或胶体的形式,分散在以水为连续相的介质中,配制成稳定的分散体系[ 5 ] 。
水性环氧树脂的研究与进展[1]
![水性环氧树脂的研究与进展[1]](https://img.taocdn.com/s3/m/9875b115cec789eb172ded630b1c59eef8c79ae5.png)
水性环氧树脂的研究与进展[1]
水性环氧树脂的研究与进展[1]
摘要:
水性环氧树脂是一种在涂料、油墨、油墨油墨辊涂、汽车涂料、油漆、印花印刷涂料、水性哑光涂料及热固性塑料等产品中广泛应用的重要通用
有机物质。
环氧树脂的有效改性和功能改善,决定着环氧树脂在现代行业
中的重要性。
本文重点介绍了水性环氧树脂的研究历史、基本概念、合成
方法和性能评价,以及有关水性环氧树脂的研究进展情况,总结了未来水
性环氧树脂的研究前景及应用方向。
关键词:水性环氧树脂;合成;功能改性;研究进展
1绪论
环氧树脂是一种现代化工产品,它可以用于多种行业。
它有优异的耐
热性、耐湿性、耐老化性和机械性能,是众多行业中重要的基础材料。
根
据不同性能需求,改性剂可以加入到环氧树脂中,以调节、改善树脂的性能,使环氧树脂具有更完善的性能[2]。
由于水性环氧树脂具有环保、耐
腐蚀、低毒性和可持续发展等特点,因此,近年来,水性环氧树脂这一新
型高性能树脂在涂料、油墨、印刷油墨辊涂、汽车涂料、油漆、印花印刷
涂料、水性哑光涂料及热固性塑料等行业得到广泛应用,成为涂料领域当
今最热门的研究课题。
环保节能型水性环氧树脂性能改良的研究
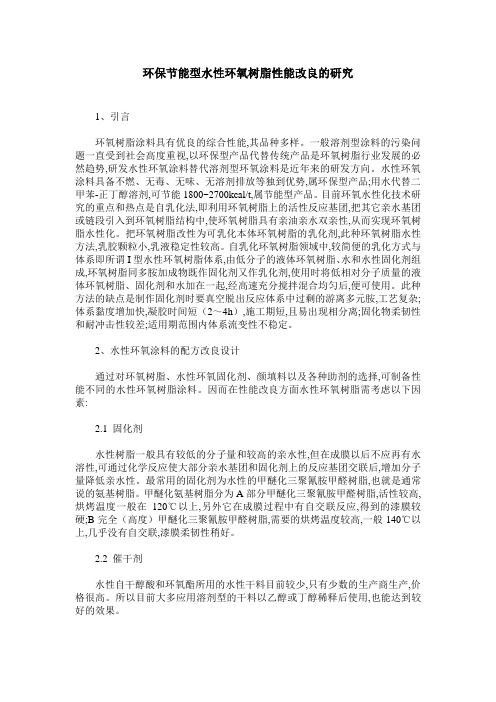
环保节能型水性环氧树脂性能改良的研究1、引言环氧树脂涂料具有优良的综合性能,其品种多样。
一般溶剂型涂料的污染问题一直受到社会高度重视,以环保型产品代替传统产品是环氧树脂行业发展的必然趋势,研发水性环氧涂料替代溶剂型环氧涂料是近年来的研发方向。
水性环氧涂料具备不燃、无毒、无味、无溶剂排放等独到优势,属环保型产品;用水代替二甲苯-正丁醇溶剂,可节能1800~2700kcal/t,属节能型产品。
目前环氧水性化技术研究的重点和热点是自乳化法,即利用环氧树脂上的活性反应基团,把其它亲水基团或链段引入到环氧树脂结构中,使环氧树脂具有亲油亲水双亲性,从而实现环氧树脂水性化。
把环氧树脂改性为可乳化本体环氧树脂的乳化剂,此种环氧树脂水性方法,乳胶颗粒小,乳液稳定性较高。
自乳化环氧树脂领域中,较简便的乳化方式与体系即所谓I型水性环氧树脂体系,由低分子的液体环氧树脂、水和水性固化剂组成,环氧树脂同多胺加成物既作固化剂又作乳化剂,使用时将低相对分子质量的液体环氧树脂、固化剂和水加在一起,经高速充分搅拌混合均匀后,便可使用。
此种方法的缺点是制作固化剂时要真空脱出反应体系中过剩的游离多元胺,工艺复杂;体系黏度增加快,凝胶时间短(2~4h),施工期短,且易出现相分离;固化物柔韧性和耐冲击性较差;适用期范围内体系流变性不稳定。
2、水性环氧涂料的配方改良设计通过对环氧树脂、水性环氧固化剂、颜填料以及各种助剂的选择,可制备性能不同的水性环氧树脂涂料。
因而在性能改良方面水性环氧树脂需考虑以下因素:2.1 固化剂水性树脂一般具有较低的分子量和较高的亲水性,但在成膜以后不应再有水溶性,可通过化学反应使大部分亲水基团和固化剂上的反应基团交联后,增加分子量降低亲水性。
最常用的固化剂为水性的甲醚化三聚氰胺甲醛树脂,也就是通常说的氨基树脂。
甲醚化氨基树脂分为A部分甲醚化三聚氰胺甲醛树脂,活性较高,烘烤温度一般在120℃以上,另外它在成膜过程中有自交联反应,得到的漆膜较硬;B完全(高度)甲醚化三聚氰胺甲醛树脂,需要的烘烤温度较高,一般140℃以上,几乎没有自交联,漆膜柔韧性稍好。
自乳化水性环氧树脂乳液的制备与性能

水性环氧树脂的研究
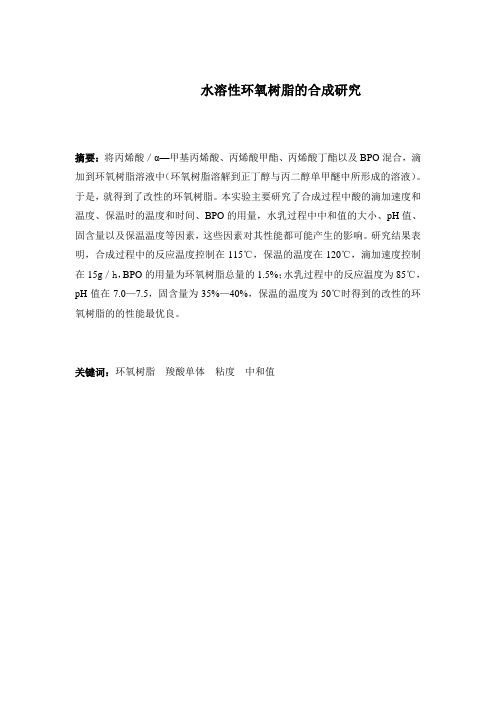
水溶性环氧树脂的合成研究摘要:将丙烯酸/α—甲基丙烯酸、丙烯酸甲酯、丙烯酸丁酯以及BPO混合,滴加到环氧树脂溶液中(环氧树脂溶解到正丁醇与丙二醇单甲醚中所形成的溶液)。
于是,就得到了改性的环氧树脂。
本实验主要研究了合成过程中酸的滴加速度和温度、保温时的温度和时间、BPO的用量,水乳过程中中和值的大小、pH值、固含量以及保温温度等因素,这些因素对其性能都可能产生的影响。
研究结果表明,合成过程中的反应温度控制在115℃,保温的温度在120℃,滴加速度控制在15g/h,BPO的用量为环氧树脂总量的1.5%;水乳过程中的反应温度为85℃,pH值在7.0—7.5,固含量为35%—40%,保温的温度为50℃时得到的改性的环氧树脂的的性能最优良。
关键词:环氧树脂羧酸单体粘度中和值1 引言1.1 环氧树脂简介环氧树脂是泛指分子中含有两个或两个以上环氧基的有机高分子化合物,除个别外,它们的相对分子质量都不。
环氧树脂的分子结构是以分子链中含有的活泼的环氧基团为其特征,环氧基团可以位于分子链的末端、中间或称环状结构。
由于分子结构中还有活泼的环氧基团,使它们可与多种类型的固化剂发生交联反应而形成不溶、不熔的具有三项网状结构的高聚物。
1.2 环氧树脂的应用特点1)具有极大的配方设计灵活性和多样性。
能按不同的使用性能和工艺性能要求,设计出针对性很强的最佳配方。
这是环氧树脂应用中的一大特点和优点。
2)不同的环氧树脂固化体系分别能在低温、室温、中温或高温固化,能在潮湿表面甚至在水中固化,能快速固化、也能缓慢固化,所以它对施工和制造工艺要求的适应性很强。
环氧树脂可低压成型或接触压成型,因此可降低对成型设备和模具的要求,减少投资,降低成本。
3)在三大通用型热固性树脂中,环氧树脂的价格偏高,从而在应用上受到一定的影响。
但是,由于它的性能优异,所以主要用于对使用性能要求高的场合,尤其是对综合性能要求高的领域。
1.3 环氧树脂固化环氧树脂固化剂是环氧树脂应用技术范畴中极其重要的材料,是决定产品工艺技术和特性的关键组分。
水性环氧涂料固化剂的研究进展
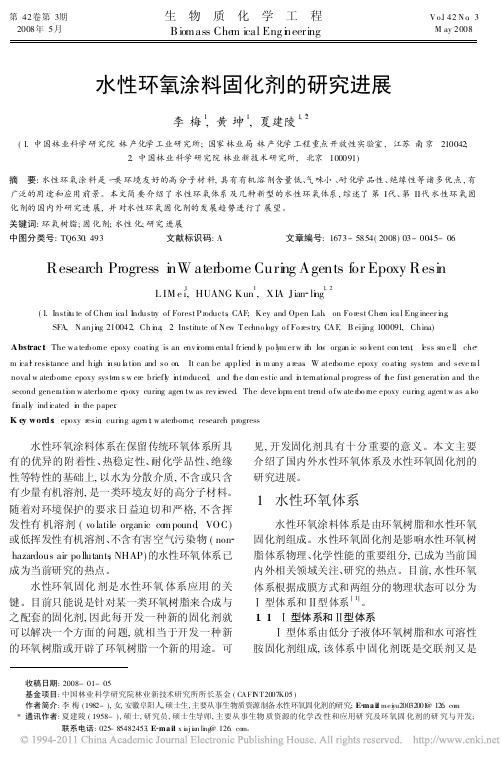
型水性环氧固化剂自开发以来取得了很大 进展, 由最早的经过部分成盐的改性脂肪胺水溶 性固化剂发展到后来的不需要采用有机酸成盐的 水性环氧固化剂。经过部分成盐的改性脂肪胺水 溶性固化剂是通过加有机酸成盐来降低反应活性 和增加水溶性、稳定性, 多余的乙酸对钢铁有一定 的腐蚀作用, 因此不宜用于钢铁构件上。为解决 水性环氧涂料耐腐蚀问题, 开发了一些新型固化 剂, 这类固化剂多不需要采用有机酸成盐, 主要是 通过引入聚氧乙烯链, 使其分散在水中, 常采用的 亲水链段有: 聚乙二醇、聚氧乙烯胺、聚氧乙烯二 醇二缩水甘油醚等, 同时利用含有聚氧乙烯链段
Shim p等 [ 7] 采用低分子质量环氧树脂与多乙 烯多胺反应生成多胺-环氧加成物, 再经单环氧 化合物将其封端, 并用醋酸中和部分的仲胺, 以调 节固化剂的 HLB, 以降低固化剂的反应活性, 延 长适用期。
陶永忠 等 [ 8] 则 将 低分 子 量 液 体 环 氧 树 脂
( E51) 与聚乙二醇反应生成端环氧化合物, 然后 与三乙烯四胺反应生成端胺基环氧- 胺加 成物, 再用单环氧化合物封端, 最后用醋酸中和成盐, 制 得 I型水性环氧固化剂。由于长链聚乙二醇的引 入降低了交联密度, 提高了涂膜的柔韧性。
环氧富锌用自乳化环氧树脂合成及其性能研究

环氧富锌用自乳化环氧树脂合成及其性能研究******************绵阳 622000摘要:自制自乳化环氧树脂,该水性环氧树脂的制备无需外加乳化剂,经过对油溶性环氧树脂的改性,配合水溶型固化剂可实现流畅的相反转,不发生破乳、絮凝、分层。
对颜填料包裹性好,作为环氧富锌涂料主剂对锌粉的分散性、稳定性、防沉等方面表现优秀,漆膜初期耐水、耐盐雾和拉开附着力佳。
自乳化环氧树脂以聚乙二醇为扩链剂,并在环氧树脂上引入亲水基团,从而实现环氧树脂的自乳化,研究得出选用环氧树脂E20,E51,聚乙二醇8000,三氟化硼-乙醚为原料,采用两步法制备的自乳化环氧树脂性能最佳。
重点探讨了反应时间、反应温度、反应摩尔比对自乳化环氧树脂的影响。
0前言富锌涂料由于具有优异的防腐性能而被广泛应用于工业防腐领域,按照树脂基料可以分为无机富锌涂料、有机富锌涂料、有机-无机相结合富锌涂料。
我国重点工程的重防腐涂料配套设计中,以环氧富锌涂料、水性自固化无机富锌涂料和醇溶性无机富锌涂料种为主[1]。
水性性环氧富锌涂料的发展历程大致可分为 3 个阶段。
第一阶段:由水性化的环氧乳液、水性环氧固化剂、锌粉 3 个组分组成。
第二阶段:在水性环氧固化剂中引入亲水性物质,但产品形式不加水。
加入锌粉、助剂,作为涂料的主剂 A 组分(不含水),B 组分为水性化后的环氧乳液(含水)。
第三阶段:环氧树脂中引入亲水性物质,但产品形式不加水。
加入锌粉、助剂等作为涂料的主剂 A 组分(不含水),水性环氧固化剂作为 B 组分(含水)。
第一阶段的产品,由 3 组分构成的水性环氧富锌涂料体系,因配漆工艺繁琐,搅拌时间长,黏度大,消泡难,现场锌尘大等问题,已逐渐淡出市场。
目前水性环氧富锌涂料以第二阶段、第三阶段产品为主流体系。
在第三阶段产品中,自乳化环氧树脂是70-75%丙二醇甲醚溶液,树脂液无水且呈中性。
自乳化环氧树脂的水性化为关键技术,为保证在配漆时使用低剪切力即能发生流畅的相反转,其引入的相同亲水物质含量比普通环氧乳液要多。
- 1、下载文档前请自行甄别文档内容的完整性,平台不提供额外的编辑、内容补充、找答案等附加服务。
- 2、"仅部分预览"的文档,不可在线预览部分如存在完整性等问题,可反馈申请退款(可完整预览的文档不适用该条件!)。
- 3、如文档侵犯您的权益,请联系客服反馈,我们会尽快为您处理(人工客服工作时间:9:00-18:30)。
自乳化水性环氧树脂的研究1前言1.1环氧树脂环氧树脂(Epoxy Resin)泛指含有两个或两个以上环氧基()的那一类有机高分子化合物,除个别外,他们的相对分子质量都不高[1]。
多以脂肪族、脂环族或芳香族等有机化合物为骨架,分子链中含有活泼的环氧集团为特征,可位于分子链的中间、末端或成环状结构,并能由于分子链中活泼的环氧基团可反应形成有用的热固性产物的高分子低聚体(01igolner)。
环氧树脂是一种从液态到黏稠态、固态多种形态的物质。
它几乎没有单独的使用价值,只有和固化剂反应生成三维网状结构的不溶不熔聚合物才有应用价值,因此环氧树脂归属于热固性树脂。
属于网络聚合物范畴。
1.2环氧树脂的性能和特性在热固性树脂中,环氧树脂、酚醛树脂和不饱和聚酯树脂合称三大通用性热固性树脂,使用量大、应用范围广。
与其他各类热固性树脂相比,环氧树脂因其特有的环氧基,及分子链上的羟基、醚键等活性集团和极性集团,使环氧树脂具有不同种类和牌号的性能各异的优质树脂。
环氧树脂固化剂种类众多,加上众多的促进剂、改性剂、添加剂等,可以进行多种多样的组合和组配。
从而能获得各种各样性能优异的、各具特色的环氧固化体系和固化物。
几乎能适应和满足各种不同使用性能和工艺性能的要求。
环氧树脂及其固化物的性能特点:(1)力学性能高。
(2)粘接性能优异。
(3)固化收缩率小。
(4)工艺性好,固化方便。
(5)电性能好。
(6)化学稳定性好。
(7)环氧固化物的耐热性好。
(8)品种多,形式多样。
(9)在热固性树脂中,环氧树脂及其固化物的综合性能最好。
1.3环氧树脂发展简史环氧树脂的发明曾经历了相当长的时期。
早在1891年,德国的Lindmann用对苯二酚与环氧氯丙烷反应,缩聚成树脂并用酸酐使之固化,但并未研究其应用价值。
1930年,瑞士的Pierre Castan 和美国的S.O.Greenlee进一步进行研究,用有机多元胺使上述树脂固化,显示出很高粘接强度,引起了人们的重视。
大约在20世纪20年代中期已经报导了双酚A与环氧氯丙烷反应产物,15年后首创了不稳定的环氧化脂肪胺中间产物的生产技术。
在此后的近三十年,由双酚A制得的环氧树脂热固性制品、涂料树脂陆续研制成功,并凭借其良好的产品性能,开始了工业化生产和集中性的应用开发。
在1955~1965年期间,环氧树脂质量明显提高,双酚A环氧树脂已有所有的平均相对分子质量等级的牌号。
酚醛环氧确立了明显的耐高温应用的优级性能。
1957 年有关环氧树脂的合成工艺的专利问世,是由Shell Developmet co.申请的,该专利研究了固化剂和填加剂的应用工艺方法,揭示了环氧树脂固化物的应用。
过醋酸法合成的环氧树脂最初是1956年由美国联合碳化物公司推出,1964年转卖给联碳塑料。
中国研制环氧树脂始于1956年,在沈阳、上海两地首先获得了成功。
1958年上海、无锡开始了工业化生产。
20世纪60年代中期开始研究一些新型的脂环族环氧:酚醛环氧树脂、聚丁二烯环氧树脂、缩水甘油酯环氧树脂、缩水甘油胺环氧树脂等,到70年代末期中国已形成了从单体、树脂、辅助材料,从科研、生产到应用的完整的工业体系。
2环氧树脂的水性化方法环氧树脂的水性化实际上是指以水为主要分散剂或溶剂,按树脂分散粒子大小不同而制得的以水乳液、水溶胶及水溶液等不同形式的稳定的分散体系。
环氧树脂的水性化技术经历了从外加乳化剂法到自乳化法的发展过程[2]。
2.1外加乳化剂外乳化法就是借助于外加的乳化剂,将液体或磨碎的固体环氧树脂通过机械搅拌分散于水中,形成稳定的水包油乳液体系[3],实施方法有机械法和相反转法。
2.1.1机械法图1 环氧树脂水分散体系的机械法制备工艺机械法又称直接乳化法,如图1所示,将环氧树脂用球磨机、胶体磨、均氏器等磨碎,加入乳化剂,激烈搅拌即得环氧树脂分散体。
机械法制备水性环氧树脂乳液的优点是工艺简单、成本低廉,所需乳化剂的用量较少,但乳液中环氧树脂分散相微粒的尺寸较大,约10μm 左右,粒子形状不规则且粒度分布较宽,所配得的乳液稳定性差,并且乳液的成膜性能也不是很好,且非离子表面活性剂的存在,影响涂膜的外观和防腐性能[4]。
2.1.2相反转法图2 相反转技术制备高分子树脂微粒化水基化体系的乳化过程“相反转”原指小分子乳液体系中的连续相从油相变为水相(或从水相变为油相)的过程,如图2所示。
通过改变水相的体积,将聚合物从油包水(W/O)状态转变成水包油(O/W)状态[5]。
是一种制备高分子树脂乳液较为有效的方法,几乎可将所有的高分子树脂借助于外加乳化剂的作用并通过物理乳化的方法制得相应的乳液。
相反转法即相反转原指多组分体系中的连续相在一定条件下相互转化的过程,如在油/水/乳化剂体系中,当连续相由水相向油相(或从油相向水相)转变时,在连续相转变区,体系的界面张力最低,因而分散相的尺寸最小。
通过相反转法将高分子树脂乳化为乳液,其分散相的平均粒径一般为1~2/m。
用相反转法制备水性环氧树脂乳液的具体过程是在高速剪切作用下缓慢地向体系中加入蒸馏水,随着加水量的增加,整个体系逐步由油包水向水包油转变,形成稳定的水可稀释体系。
在这一过程中,水性环氧树脂乳液的许多性质会发生改变,如体系的黏度、导电性和表面张力等,通过测定体系乳化过程中的电导率和黏度的变化就可判断相反转是否完全。
该乳化过程可在室温环境下进行,对于固体环氧树脂,则需要借助于少量有机溶剂或进行加热来降低环氧树脂的本体黏度,然后再进行乳化。
用于高分子乳液的制备效果较好,但一般需要添加适量的溶剂以降低固体高分子材料的初始黏度,且操作相对复杂。
杨振忠等人[6]用双酚A环氧树脂E-51或E-20(EP)与聚乙二醇(PEG)600、10000等反应,合成多嵌段共聚物PEG-(EP-PEG)3-EP-PEG,并用它作为乳化剂采用相反转法制得环氧树脂乳液。
总之,外加乳化剂法制备的水乳液容易破乳,不能满足稳定性的需求;另外,该法在环氧树脂体系中添加了不含活性基团(环氧基)的物质,会对环氧树脂的固化过程和固化物的性质带来一定的影响。
2.2自乳化自乳化法也称为化学改性法,是利用环氧树脂的环氧基、仲羟基及次甲基上的氢等活性反应基团,将其他的亲水性基团或链段(氨基、羧基、酯基)引入到环氧树脂分子结构中,使环氧树脂具有亲水、亲油两亲性,改善其水分散性能[2]。
采用自乳化法合成的水性环氧树脂,根据树脂的极性可分为离子型(包括阳离子型、阴离子型)和非离子型两类;根据反应类型分可分为醚化反应型、酯化反应型和接枝反应型三类;根据环氧树脂参与反应的活性基团可分为环氧基反应型、仲羟基反应型和次甲基氢反应型3类。
2.3固化剂乳化法除上述方法外还可采用改性固化剂乳化法,它不需要先将环氧树脂改性和乳化,而在配制使用前与改性固化剂棍合乳化[7],这种固化剂一般由多元胺固化剂进行加成扩链、接枝、成盐而制得,非极性及具有表面活性的基团和链段的引人,不仅改善了与其环氧树脂的相容性,而且对低分子质量液体树脂有良好乳化作用,这种乳化剂既是固化剂又有乳化剂的功能[8]。
此法主要用于乳化中低相对分子质量的环氧树脂。
目前我们研究的乳化剂型固化剂性能优越,涂膜具有透明的外观和良好的机械性能,是一种很有应用前景的乳化方式。
周继亮、涂伟萍等人采用聚醚多元醇二缩水甘油醚(DGEPG)、三乙烯四胺(TETA)及液体环氧树脂(EPON828)为原料,采用2步扩链法合成的非离子型水性环氧固化剂具有良好的乳化液体环氧树脂的功能[9]。
3自乳化水性环氧树脂根据改性剂与树脂的反应类型可将离子型水性环氧树脂的合成方法分为醚化反应型、酯化反应型和接枝反应型等三种类型。
3.1醚化反应型醚化反应型均是亲核剂直接进攻环氧环上的C原子。
醚化型水性化环氧树脂中没有可水解的化学键,具有很好的稳定性。
如图3、图4所示。
(a)将环氧树脂与非离子低聚物如聚氧化乙烯二醇、多元酚,在催化剂作用下发生醚化反应,然后与多异氰酸酯作用可得分散体。
(b)也可将环氧树脂与强亲水性胺(如二乙醇胺、2-氨基乙基-2-羧基甲烷、N-氨乙基哌啶等)反应,生成环氧-胺加成物,再用酸(如乙酸、乳酸等)中和成盐,即可制成水溶液或水乳液。
图3 醚化反应型阳离子基改性环氧树脂图4 醚化反应型阴离子基改性环氧树脂张肇英等[10]采用此法将环氧树脂改性,探索出制备改性产物乳液的条件,成功地制得稳定的水乳液,并对制备机理和影响乳液稳定性的因素进行了研究。
以改性产物为原料,制备水性乳液,所制得的漆膜性能优良[11]。
美国杜邦公司[12]利用醚化反应研制了一种环氧树脂水分散体系,特别适用于汽车涂料或工业涂料的底漆。
3.2酯化反应型酯化反应型与醚化型不同的是氢离子先将环氧环极化,酸根离子再进攻环氧环,使其开环。
如图5所示。
图5 酯化反应型离子基改性环氧树脂通过适当的方法在环氧树脂分子链中引入羧酸、磺酸等功能基团,中和成盐后环氧树脂就具备了水分散的性质。
最常用的方法是功能性单体扩链法,即利用环氧树脂与一些低分子扩链剂如氨基酸、氨基苯甲酸等化合物上的氨基反应,在环氧树脂分子链上引入羧酸、磺酸基团,中和成盐得水分散体。
用羧基聚合物酯化环氧树脂也可制备水分散环氧树脂体系。
目前水性化改性环氧树脂的酯化反应类型主要有:(a)最常用的方法是由不饱和脂肪酸与环氧树脂进行酯化生成环氧酯。
加入不饱和二元酸(酐)及引发剂进行加成反应,在大分子上引入羧基,再用碱(醇胺或氨水)中和成盐[13]。
佩德森W R [14]等人就用此法发明了一种水分散性聚合物和含该聚合物的乳液组合物,该乳液组合物固化后显示了优良的柔性、粘合力、耐化学性和耐腐蚀性。
美国瓦尔斯巴公司[15]发明了一种新的方法,即环氧树脂与羧基聚合物在酯化催化剂作用下反应,并在酯化反应完成前抑制反应混合物而制备水分散乳液组分。
范一波[16]等用马来酸酐与双酚A型环氧树脂主链上的仲羟基进行醇解反应,在环氧树脂主链上引入亲水性—COOH基团,制得水性环氧树脂。
(b)环氧树脂与丙烯酸树脂发生酯转移反应,或环氧树脂与丙烯酸单体溶液反应,丙烯酸通过酯键接枝于环氧树脂上,这2种改性方法所得的水乳体系,大量用作罐头内表涂料。
(c)环氧树脂的环氧基和羟基,或环氧丙烯酸酯的羟基与浓磷酸进行酯化反应,生成环氧磷酸酯,再用碱中和,即可制成不易水解的较稳定水分散体系。
KLEIN等[17]用环氧树脂与磷酸类化合物及含羟基的调节剂反应合成了磷酸酯,以此产物配制的水性热固化涂料可与目前市售涂料相媲美,特别是耐化学品腐蚀性能显著。
台湾省中油公司[18]用环氧树脂与二元酸酐反应制备一种可发生双交联反应的水性树脂分散体。
M.J.Husbands[19]等将环氧树脂的环氧基或羟基与磷酸反应生成环氧磷酸酯,用胺中和得较稳定的水分散体。